The automotive industry is constantly evolving, with a relentless push for lighter vehicles, improved fuel efficiency, and innovative designs. In this competitive world, manufacturers require production methods that are efficient, cost-effective, and deliver high-quality components. That’s why we use pressure die casting, a game-changing technology that has become an indispensable tool for automotive success.
What is Pressure Die Casting?
Pressure die casting (PDC) is a manufacturing process that involves injecting molten metal under high pressure into a reusable steel mold (die). This rapid injection process, followed by rapid solidification, creates precise and complex metal parts. PDC is a form of high-pressure die casting, typically using aluminum alloys due to their high melting points.
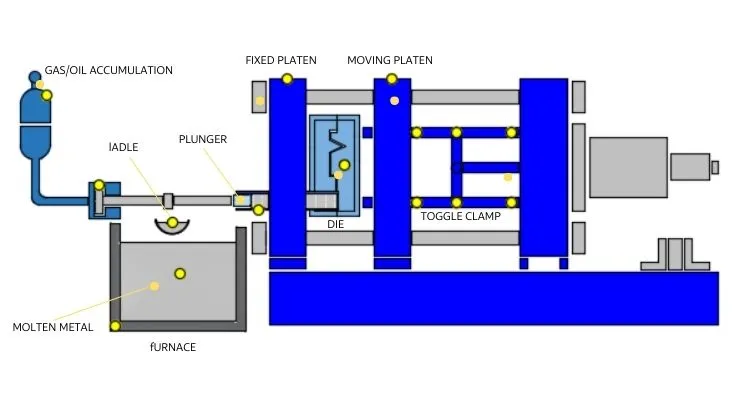
Why is Pressure Die Casting Perfect for the Automotive Industry?
There are several reasons why pressure die casting has become the perfect method for producing a wide range of automotive components,
High Volume Production – Pressure die casting excels at high volume production. The entire process is automated, allowing for the rapid creation of identical parts, ideal for vehicles manufactured on a large scale.
Lightweight Parts – The automotive industry is constantly striving to reduce vehicle weight for better fuel efficiency and performance. Aluminum alloys, the primary material used in pressure die casting, are lightweight compared to other metals like steel. This translates to lighter vehicles without compromising on part strength.
Complex Geometry – Pressure die casting accommodates complex geometry with intricate details. The high pressure forces the molten metal to fill even the most minute sections of the die, resulting in near-net-shaped parts that require minimal machining.
Dimensional Accuracy – Pressure die casting is renowned for its dimensional accuracy. The robust steel dies maintain their shape throughout the casting process, ensuring parts are produced with consistent dimensions and tolerances. This reduces the need for extensive post-processing and streamlined assembly.
Rapid Solidification – The high pressure in pressure die casting leads to rapid solidification of the molten metal. This rapid solidification creates a fine-grained structure in the cast parts, enhancing their strength and durability are crucial qualities for components used in automobiles.
How do we use pressure die casting to produce high-quality parts for the automotive industry?
Have you ever looked under the hood of a car and wondered at the complex parts that make it run? Many of those components are produced as the result of a precise manufacturing process called pressure die casting. Here at Frigate, we use this technique to craft high-quality parts for the automotive industry. But how exactly does it work?
The Power of Pressure
The liquid metal is being injected into a mold under high pressure. That’s the essence of pressure die casting. We use powerful machines (800, 600, and 400 ton) to force molten metal into precisely crafted steel dies. This creates complex shapes with excellent mechanical properties which is perfect for the demanding needs of the automotive world.
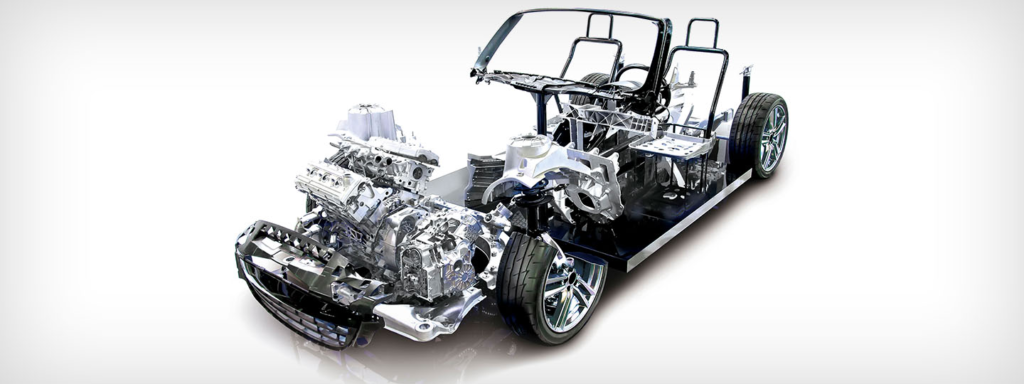
A Recipe for Success
But creating these parts is more than just brutal force. It’s a carefully executed process:
- Melter’s Touch – First, we start with high-quality raw metal. Our melting furnaces (ranging from 1500 to 500 lbs) heat the metal to the perfect temperature, ensuring a smooth pour.
- Precision Dosing – Dosing furnaces (600, 400, and 200 lbs) keep the molten metal at the optimal temperature for casting, guaranteeing consistent results.
- Automated Delivery – Auto Ladle & Spray systems (with capacities matching our dosing furnaces) efficiently transfer the molten metal to the die casting machines, minimizing waste and maximizing efficiency.
From Casting to Assembly
We get near-net-shape parts once the metal cools and hardens in the mold. But the journey isn’t over yet. Here’s what happens,
- Trimming the Excess – Trimming machines (4, 3, and 2 tons) remove any extra material left behind from the casting process.
- Surface Prep – Shot blasting machines (with capacities of 400, 300, and 150 cu ft) clean and prepare the surface of the castings, ensuring a smooth finish.
- Building Blocks – Assembly stations (we have 38 of them!) bring various components together to create the final parts.
- A Finishing Touch – Paint booths (in 300, 200, and 100 sq ft sizes) give the parts a polished look and protect them from wear and tear.
Quality is everything
At every stage, quality control is a key factor. Our team of skilled inspectors examine each part using advanced tools like hardness testers, tensile testers, and metallographic microscopes. This ensures every component meets the demanding specifications of the automotive industry.
The Human Touch Matters
While our machinery is impressive, it’s our skilled workforce that truly sets us apart. From our machine operators and supervisors to our quality inspectors and support staff, their dedication and expertise are what make Frigate a leader in pressure die casting for automotive applications.
Frigate’s Executed Pressure Die Cast Parts in Automobiles
A wide variety of automotive components are now manufactured using pressure die casting. Here are some prominent examples,
The Future of Pressure Die Casting in Automotive
As the automotive industry pushes the boundaries of design and lightweight, pressure die casting is expected to play an even greater role. Advancements in die design and materials are allowing for the creation of even larger and more complex die-cast parts. This could revolutionize car body construction, potentially leading to single-piece castings for entire sections of a vehicle.
Looking for Pressure die-casting solutions?
If you’re looking for a reliable and efficient way to produce high-quality, lightweight parts with complex geometry for your industry, then look no other than Frigate. We have the expertise and technology to help you achieve success through the power of pressure die casting.
Frigate is a leader in producing complex, high-quality parts for the automotive and transportation industries by combining advanced machinery, skilled labor, and rigorous quality control processes. Our commitment to innovation and precision drives us forward, ensuring that our customers receive nothing but the best.
Contact us today to discuss how we can meet your specific needs and elevate your projects to new heights of success.