Rapid Prototyping Services
Frigate’s rapid prototyping uses CNC and 3D printing for high-precision models. We ensure swift iteration cycles with accurate designs for rigorous testing stages.
Get Your Quote Now
- Instant Quotation
- On-Time Delivery
- Affordable Cost
Custom Rapid Prototyping Services for Precision and Performance
Frigate offers custom rapid prototyping services using advanced CNC machining and 3D printing. Each prototype achieves exacting tolerances for precise fit, finish, and functionality. The process starts with detailed CAD models, transforming designs into high-accuracy physical models. High-strength materials ensure durability, making prototypes suitable for functional testing. Multistage inspections verify accuracy at each phase, meeting strict dimensional standards. Rapid iteration cycles allow quick adjustments and modifications, refining the prototype for optimal performance.
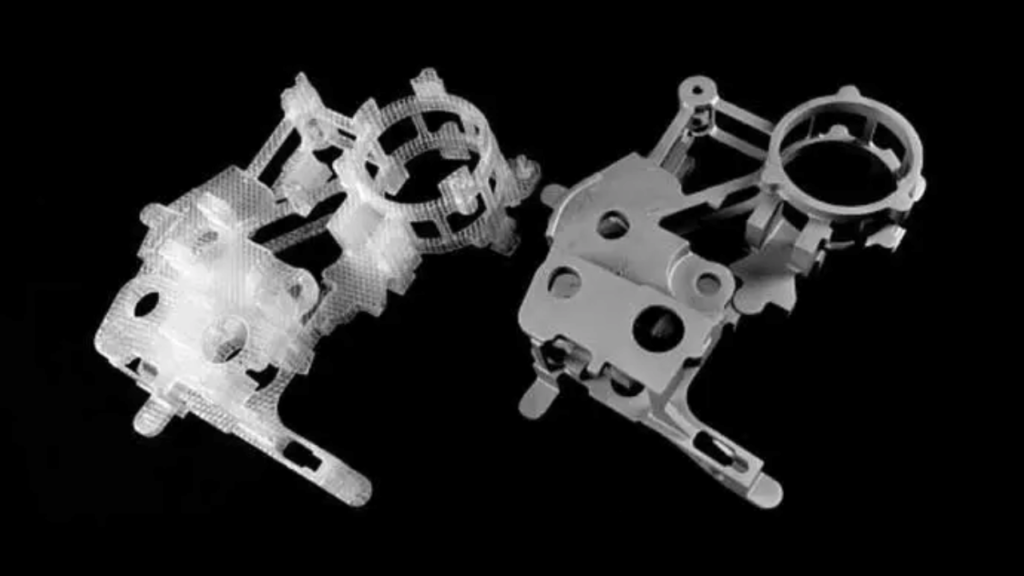
Improving Surface Finish Quality
Utilizing specialized finishing processes ensures smooth surfaces, enhancing both aesthetics and functionality.
Employing high-precision CNC machining and 3D printing technologies minimizes surface imperfections and achieves desired finishes.
Implementing rigorous quality control measures throughout production guarantees uniformity in surface quality across all prototypes.
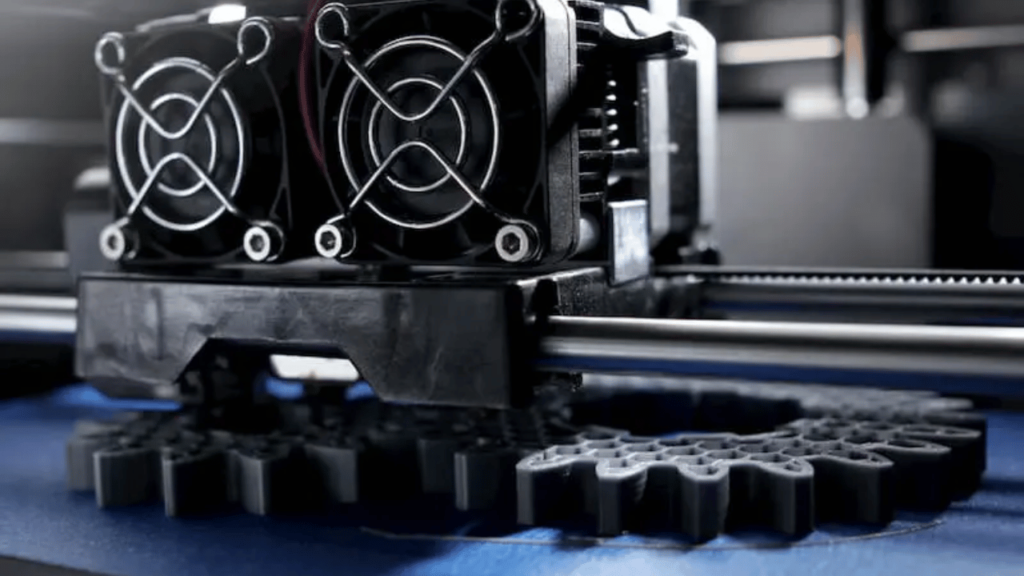
Enhancing Scalability for Design Evolution
Offering a range of prototyping methods allows for easy adaptation as design specifications change.
Integrating prototyping and manufacturing processes streamlines scaling efforts, reducing time and complexity during the transition.
Encouraging ongoing communication during the prototyping phase enables quick adjustments, ensuring the final product meets evolving requirements.
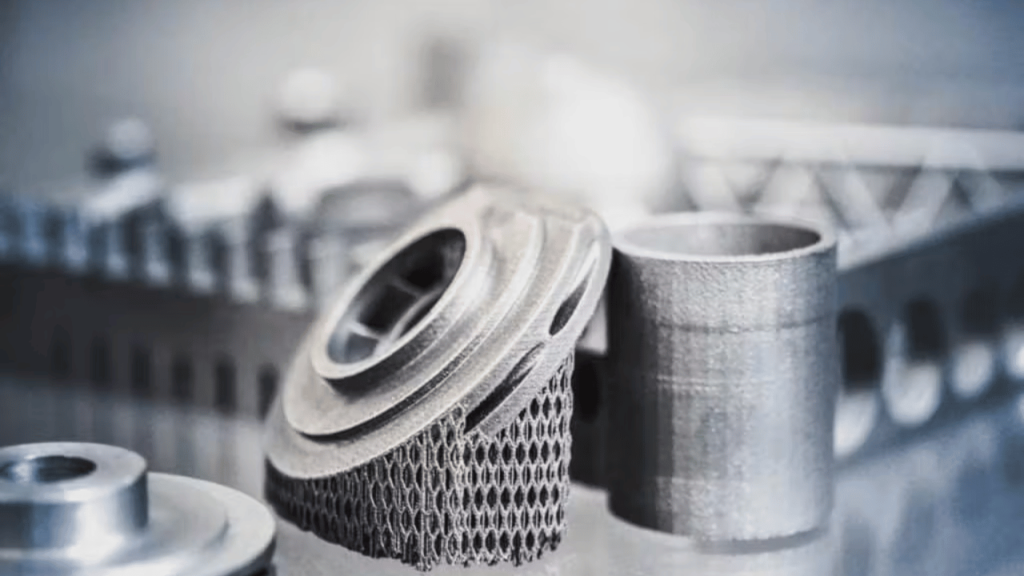
Reducing Long Lead Times for Prototyping
Streamlining production workflows improves efficiency and significantly reduces lead times for prototype delivery.
Leveraging advanced CNC machining and 3D printing technologies allows quicker turnaround times without sacrificing quality.
Assigning dedicated project managers ensures timely updates and accountability throughout the prototyping process, facilitating faster completion.
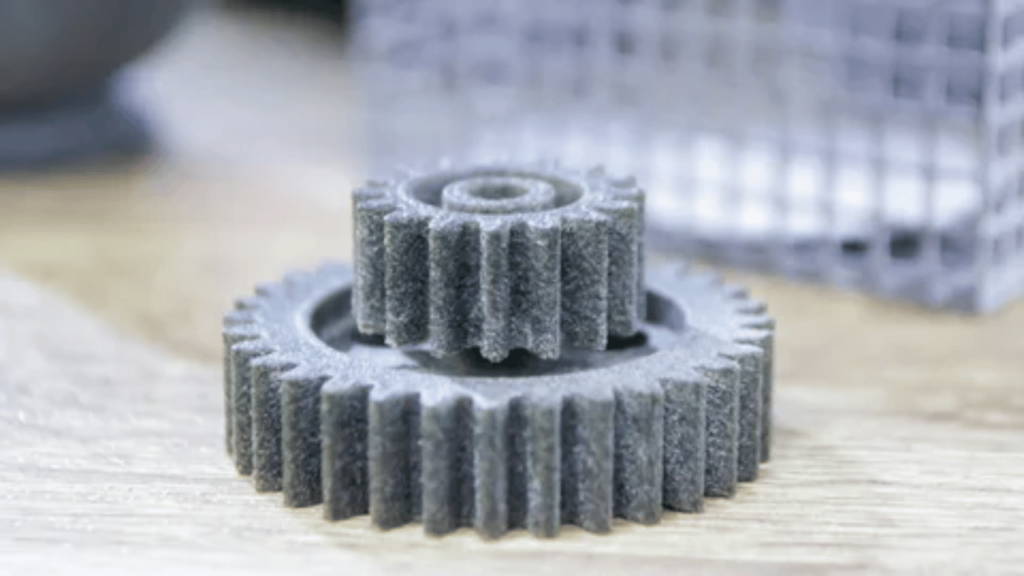
Rapid Prototyping Materials
Rapid prototyping services accelerate the product development process and design iterations. These services enable the creation of high-fidelity prototypes for testing and evaluation.
Commonly used plastics include ABS, PLA, and Nylon. These materials offer versatility in flexibility, strength, and ease of printing. They are suitable for functional prototypes and visual models.
Metals such as aluminum, stainless steel, and titanium are used for prototypes requiring high strength and durability. Metal prototyping supports more rigorous testing and real-world applications, making it ideal for components subjected to stress.
Composite materials, like carbon fiber-reinforced plastics, combine lightweight properties with high strength. These materials provide enhanced performance in demanding applications, making them suitable for the aerospace and automotive industries.
Various resins, including standard, tough, and flexible options, are utilized in 3D printing processes like stereolithography (SLA) and digital light processing (DLP). Resins allow for high-detail prototypes and are often used for intricate designs that require smooth finishes.
Ceramic materials are employed for prototypes with high heat resistance and chemical stability. They are ideal for applications in industries such as electronics and aerospace, where thermal properties are critical.
Flexible materials like TPU (thermoplastic polyurethane) are used to create prototypes that require stretch and flexibility. Elastomers are particularly useful for parts like seals, gaskets, and soft-touch features.
Effectively Managing Costs in Prototype Development
The expenses incurred from multiple prototype iterations can pose significant challenges for customers. Each modification typically requires additional resources, including materials and labor, which can accumulate quickly. When rapid adjustments are necessary to resolve design flaws or functionality issues, these costs can escalate beyond initial project budgets.
Frigate addresses this concern by implementing efficient prototyping processes that minimize waste and optimize resource use. Advanced technologies and streamlined workflows help reduce costs associated with iterative prototyping, allowing for effective design validation without compromising financial constraints.
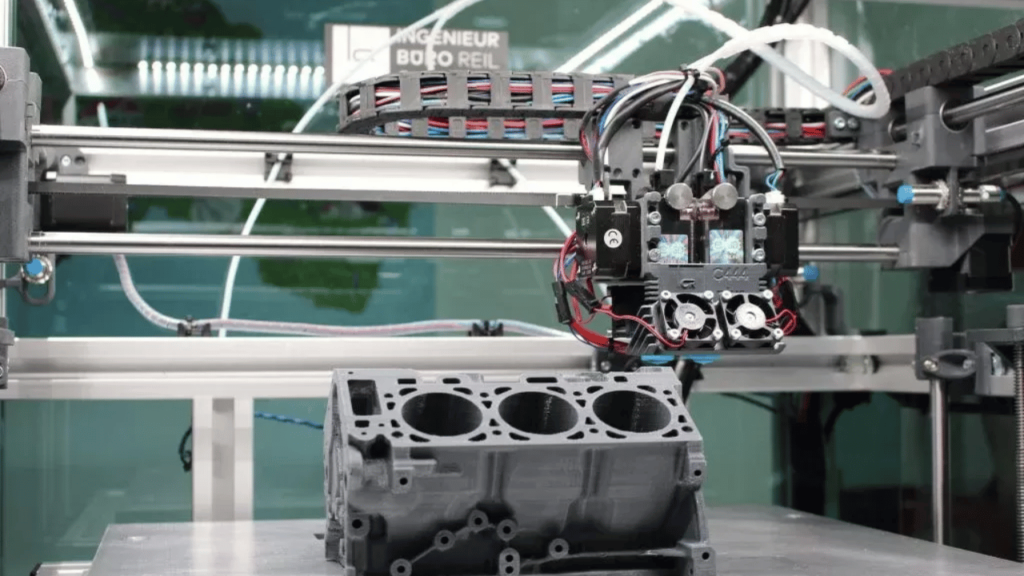
- Real Impact
Words from Clients
See how global OEMs and sourcing heads describe their experience with our scalable execution.
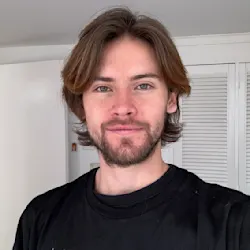
“Quick turnaround and solid quality.”
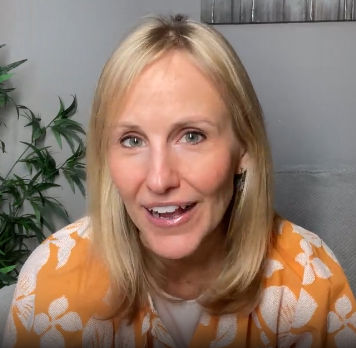
“The instant quote tool saved us time, and the parts were spot-on. Highly recommend Frigate!”
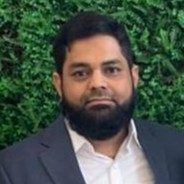
“I would strongly recommend Frigate to anyone who wants to do Rapid Prototyping, and take their ideas to manufacturing. One firm doing all kinds of Product Development!”
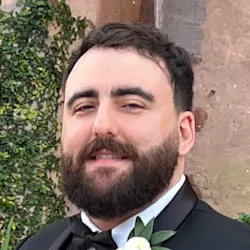
“Great service, fair price, and the parts worked perfectly in our assembly.”
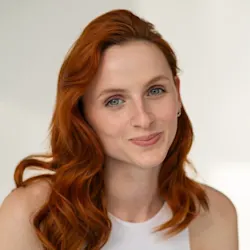
“Top-notch machining and fast shipping. Very satisfied with the results.”
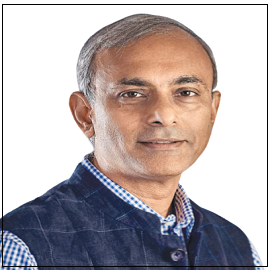
“The next disruption is happening in Prototyping & Manufacturing on-demand and Frigate is leading the way! I personally believe the Frigate's way of IIOT enabled cloud platform with Al.”
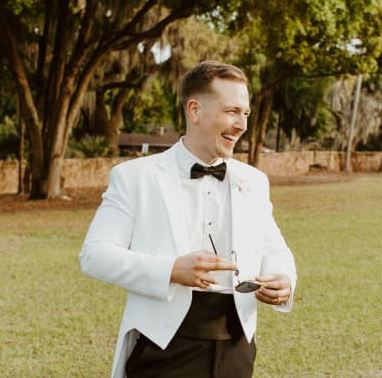
“Frigate delivered high-quality parts at a competitive price. The instant quote tool is a huge plus for us!”

“We appreciate the precision and quality of the machined components in the recent delivery—they meet our specifications perfectly and demonstrate Frigate’s capability for excellent workmanship.”
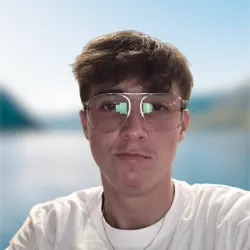
“Flawless execution from quote to delivery.”

“I am absolutely happy to work with supplier like Frigate who were quite proactive & result oriented . Frigate has high willingness team who has strong know how & their passion towards the products & process were absolutely thrilling.”
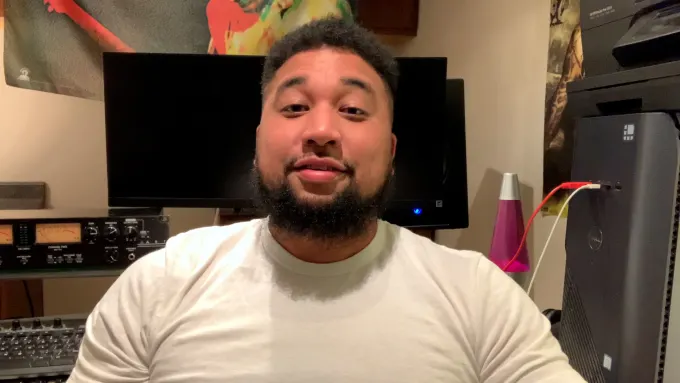
“The precision on these parts is impressive, and they arrived ahead of schedule. Frigate’s process really stands out!”
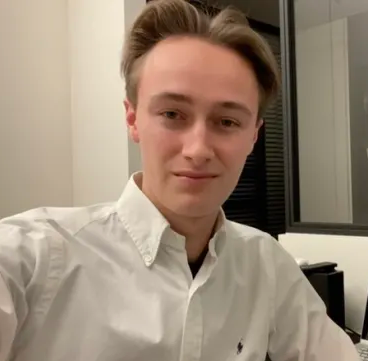
“Parts were exactly as spec’d, and the instant quote made budgeting a breeze.”
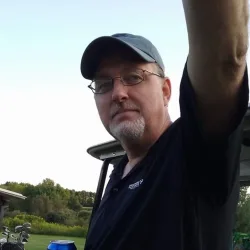
“Good value for the money.”
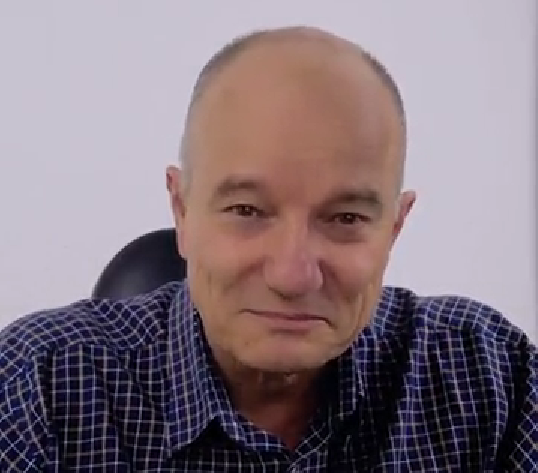
“The finish was perfect, and the team was easy to work with.”

“Working with Frigate has been great. Their proactive, results-driven approach and expertise shine through in every project. It's been a pleasure collaborating with them.”

"We are highly satisfied with the timely delivery and quality of the MIG Welding Cable from Frigate. Their attention to detail, secure packaging, and quick responsiveness stood out. We confidently recommend Frigate Engineering Services Pvt. Ltd. as a reliable manufacturing partner."
Having Doubts? Our FAQ
Check all our Frequently Asked Question
Frigate employs advanced CAD modeling and precision manufacturing techniques to produce prototypes with complex geometries. These methods allow for precise replication of design specifications, ensuring that intricate features are accurately represented in the final prototype.
Frigate utilizes optimized production workflows and advanced printing techniques to reduce material waste. By carefully analyzing design files and employing efficient layer strategies, excess material is minimized, resulting in lower costs and improved sustainability.
Frigate offers rapid prototyping services that leverage cost-effective materials and efficient processes. This approach allows for quick iterations and modifications, helping control expenses while ensuring design flaws are identified and addressed promptly.
Frigate enables functionality testing through various materials and methods tailored to specific applications. Prototypes can be produced using materials that closely mimic the final product, allowing customers to assess performance under real-world conditions.
Frigate maintains a flexible prototyping approach that accommodates rapid design changes. Close collaboration with customers during the prototyping phase allows for quick adaptations, ensuring that evolving requirements are met efficiently and effectively.
Manufacturing Capability/Capacity
Ferrous casting
Mold size(max): 1m X 1m
Weight Range: 1 KG ~ 30 KGS
Mold size(max): 1.5m X 1.5m
Weight Range: 30 KG ~ 150 KGS
Mold size(max): 3m X 3m
Weight Range: 100 KG ~ 1000 KGS
Mold size(max): 500 MM X 500 MM
Weight Range: 0.250 KG ~ 20 KGS
Mold size(max): 500 MM X 500 MM
Weight Range: 0.100 KG X 20 KGS
Non-ferrous casting
Capacity: 5000 MT/a
Range of weight: 100 gm to 20 KGS
Mold size(max): 1 M X 1 M
Weight Range: 0.5 KG X 50 KGS
Mold size(max): 1 M X 1 M
Weight Range: 0.5 KG X 50 KGS
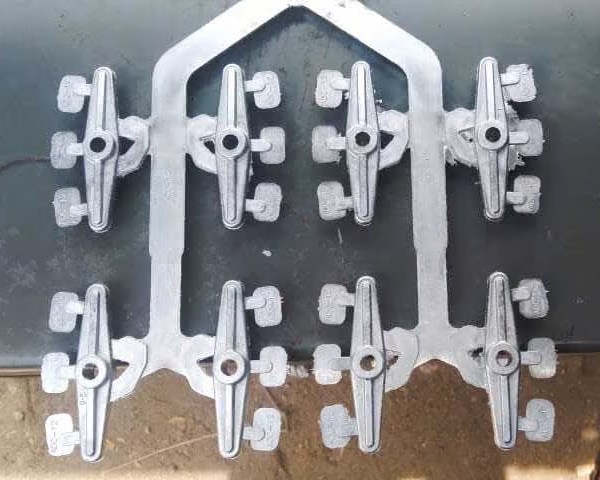
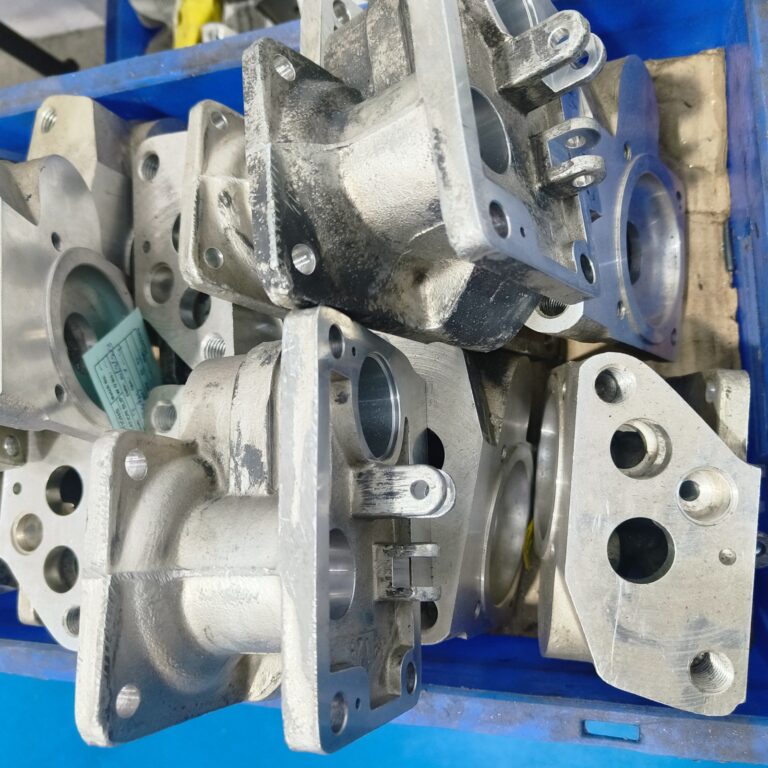
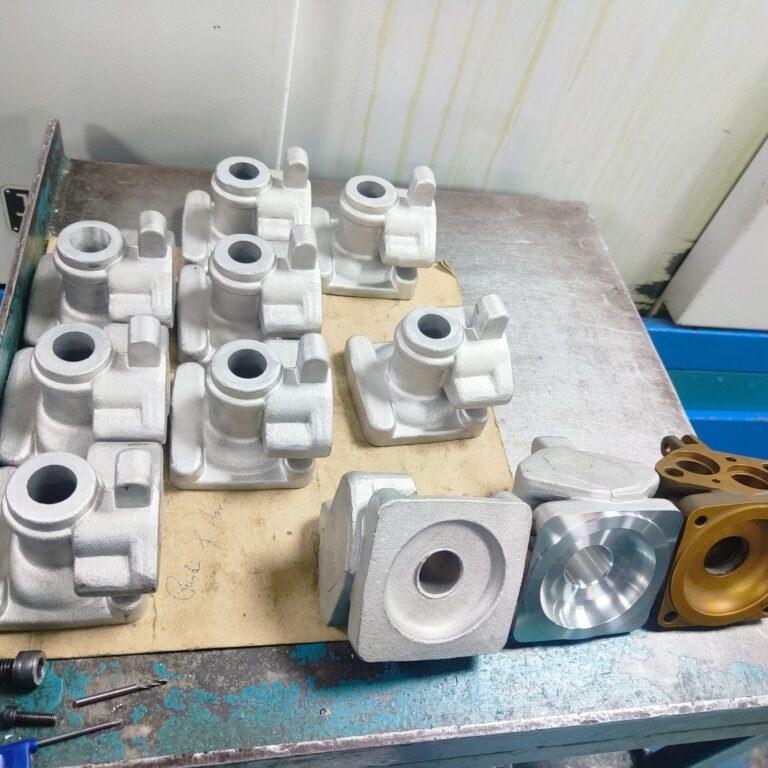
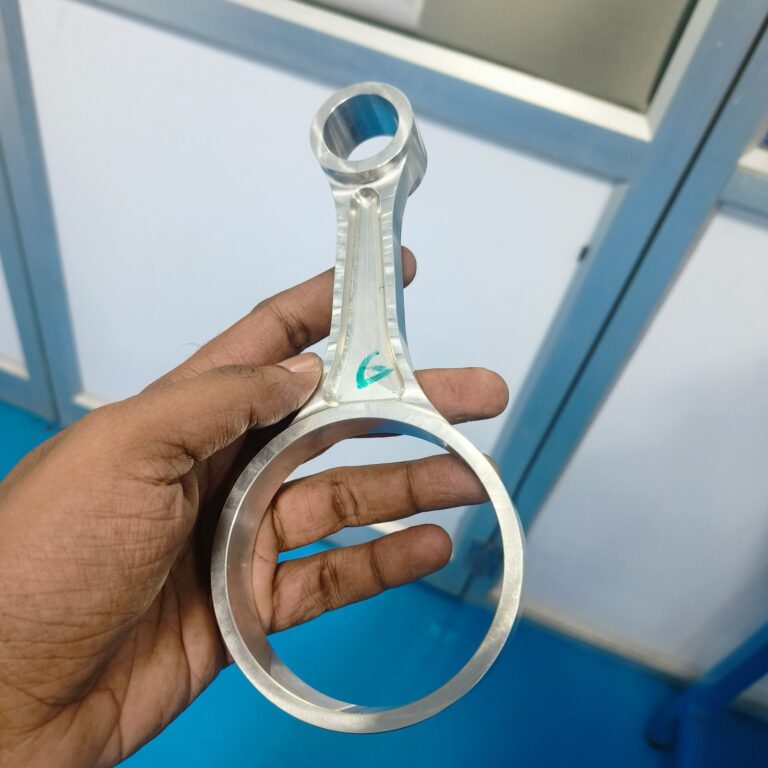
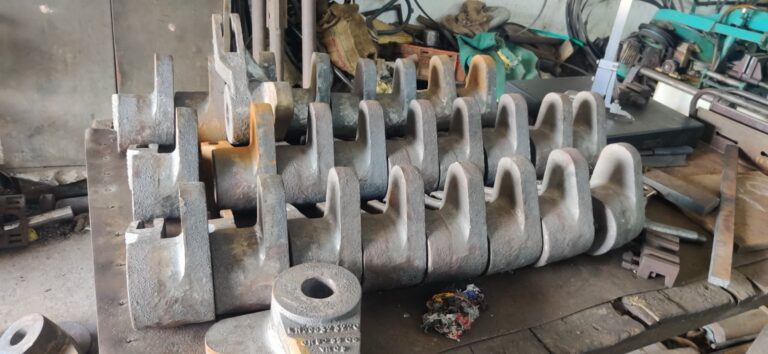
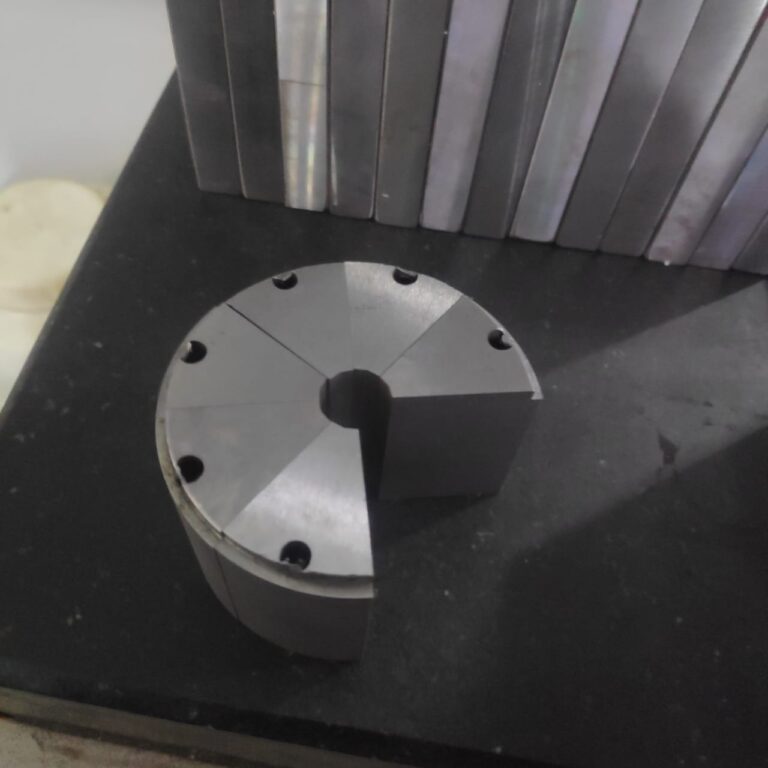
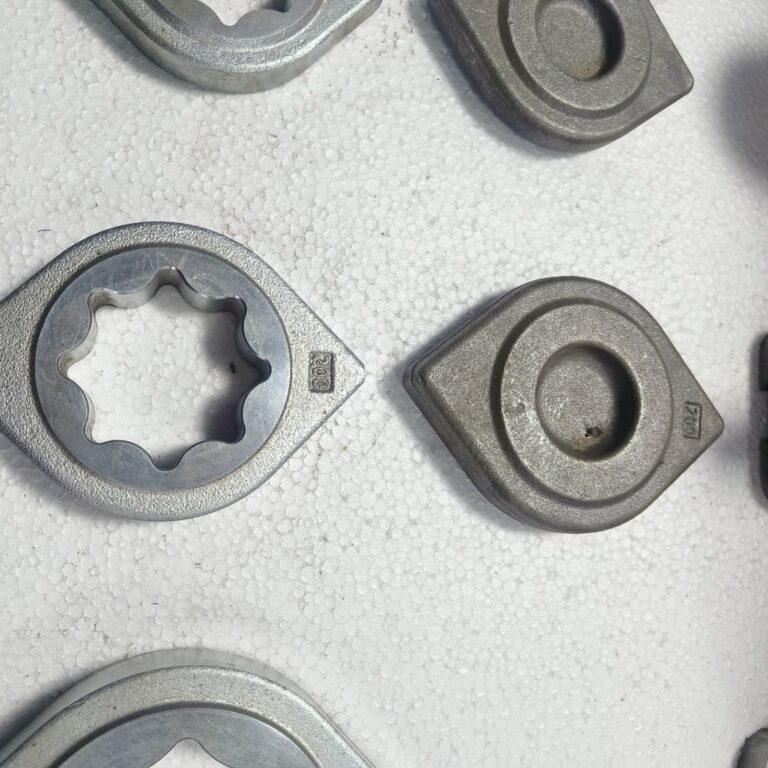
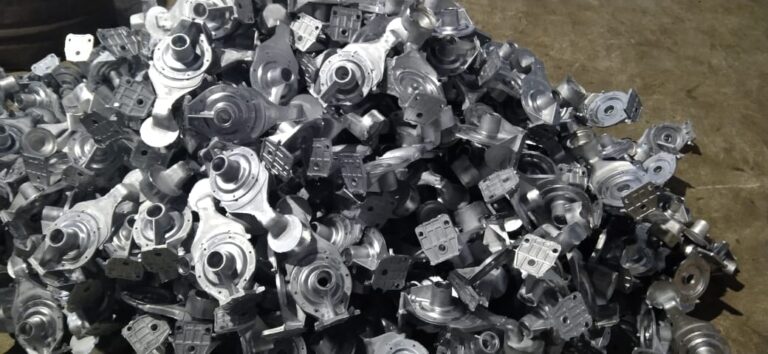
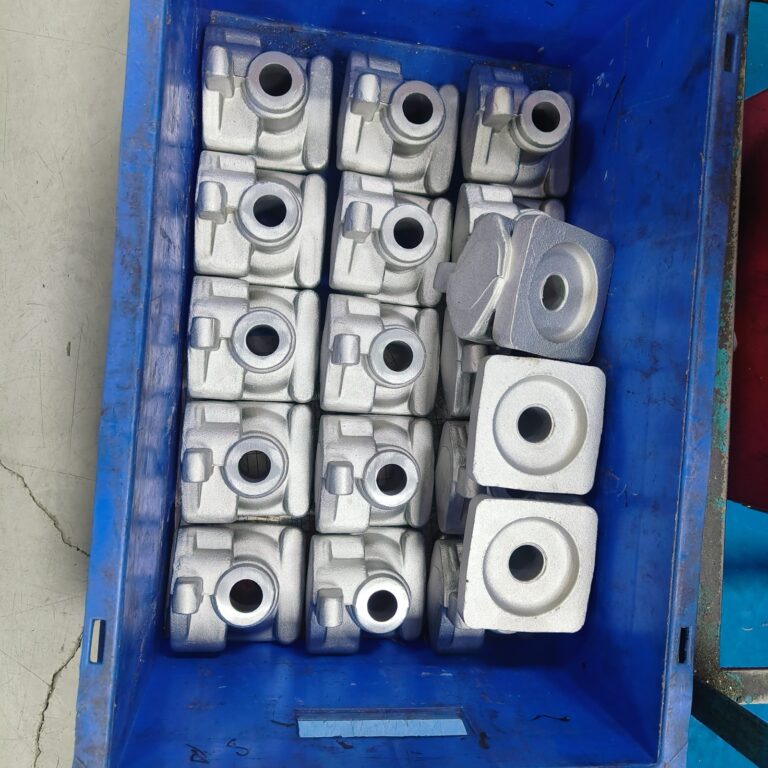
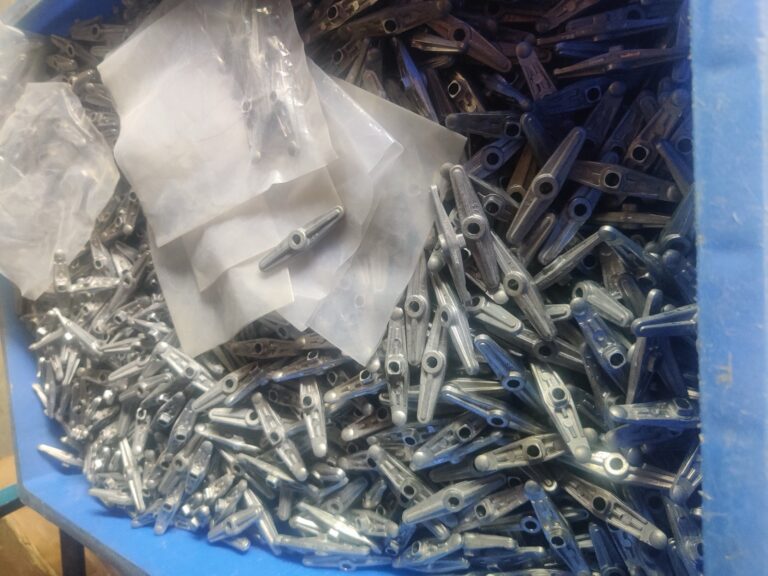
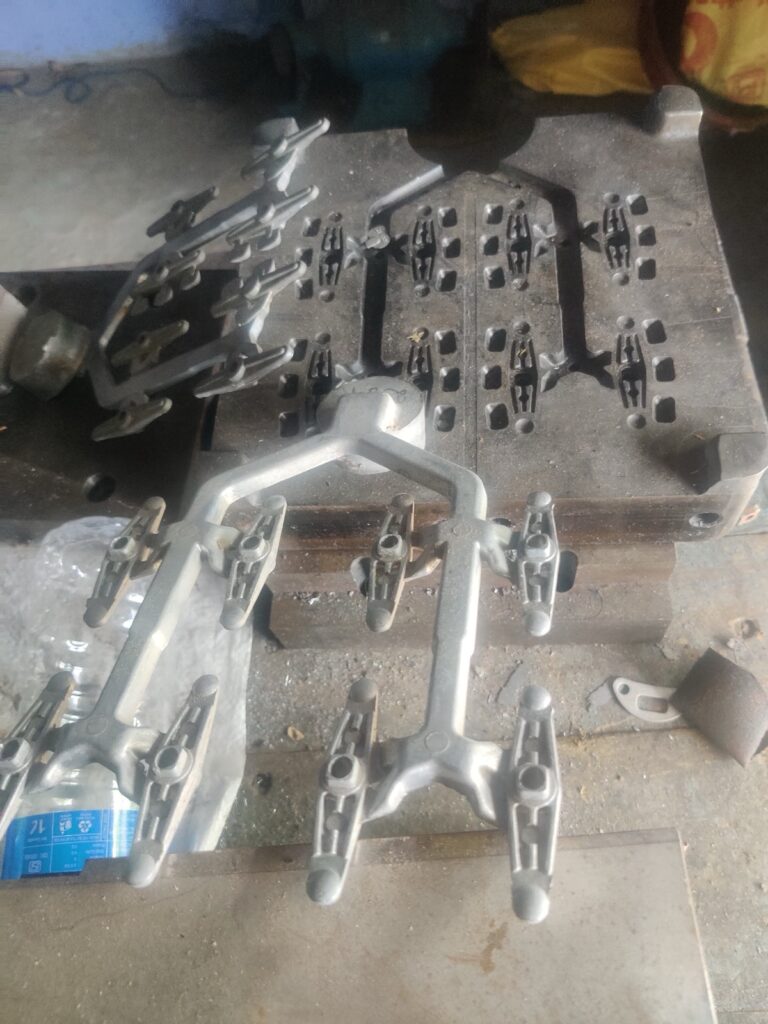
Forging
Capacity: 20,000 Tons per Annum
Range of weight: 300 KG to 1 Ton
Hammering: 5 Ton
Range of weight: 0.2 KG to 200 KGS
Hammering: 1600 Ton Hydraulic press
Ring size: 350 MM OD to 3000 MM OD
Range of weight: 15 KGS to 3200 KGS
Materials
Carbon Steel, Stainless Steel (AUSTENITE), Alloy Steel, Stainless Steel (MARTENSITE), etc.
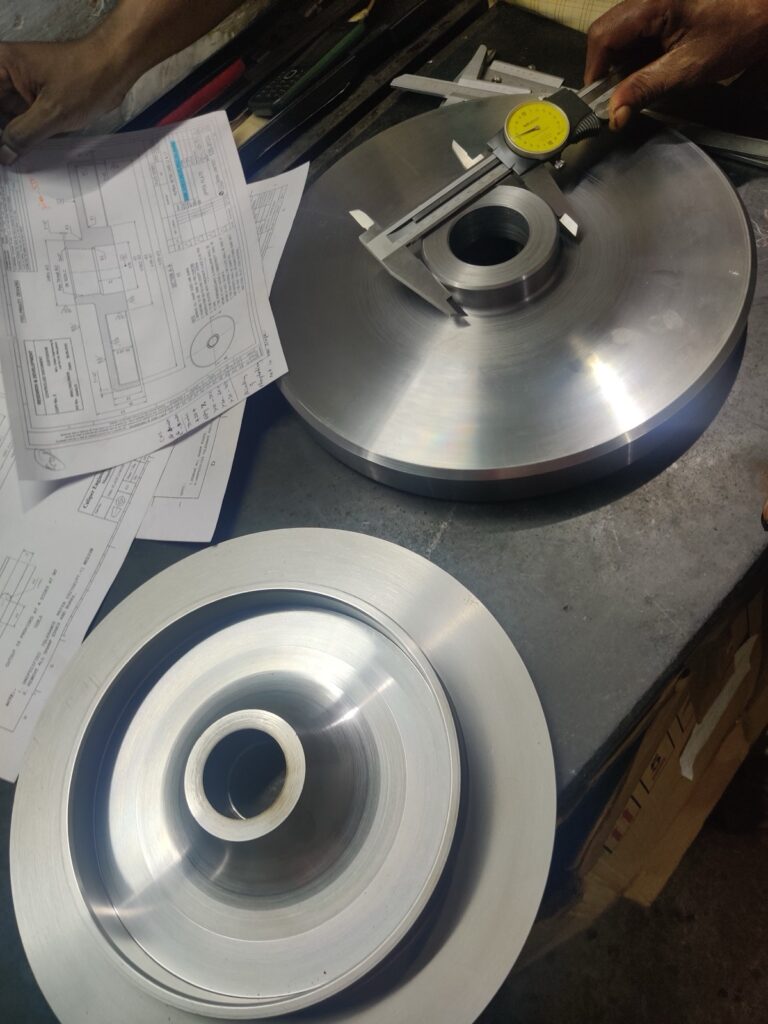
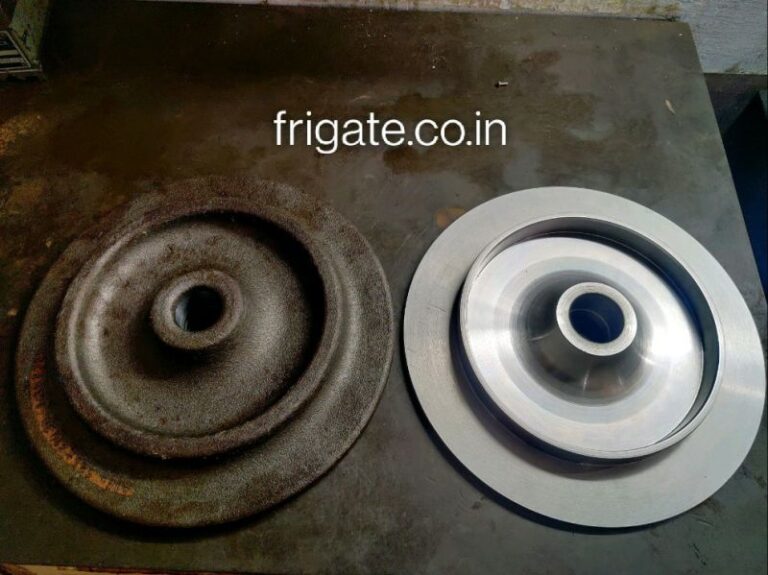
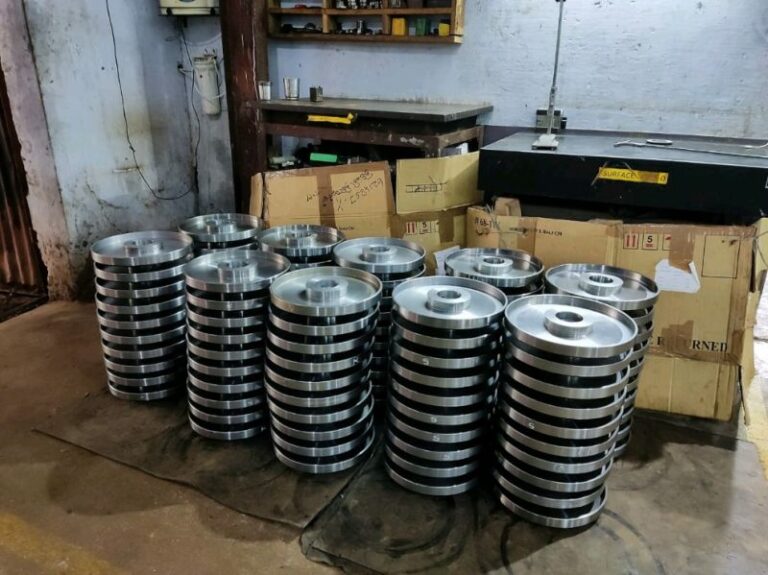
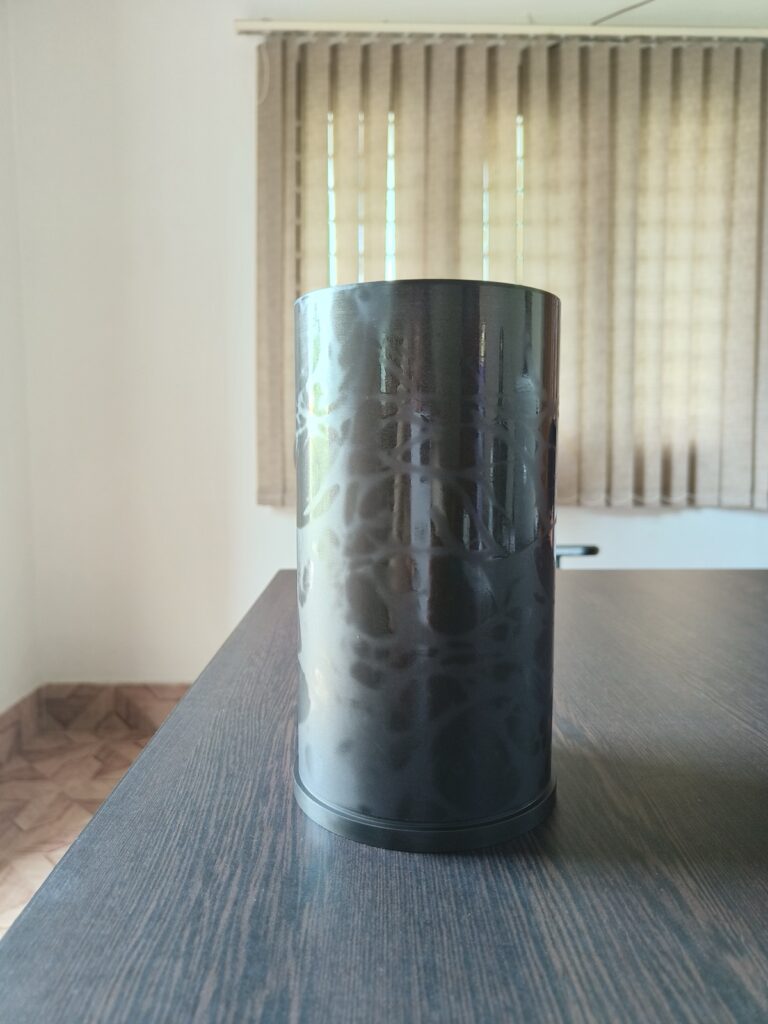
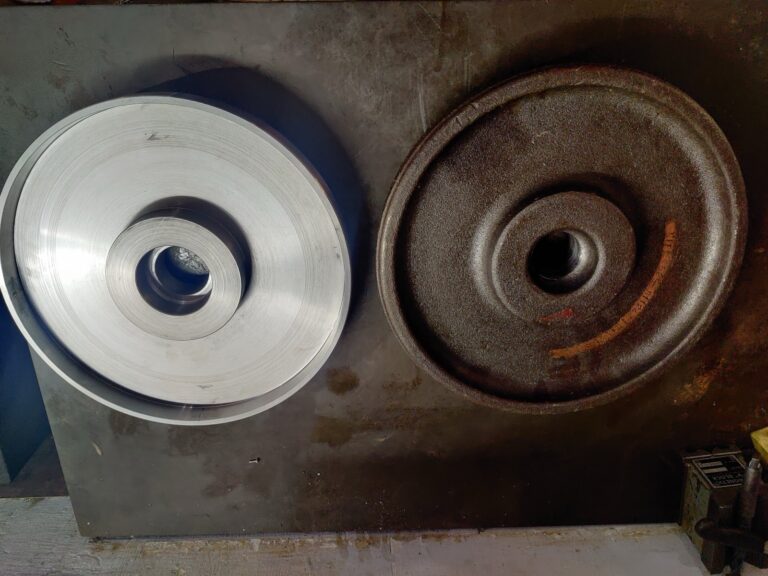
Machining
1 to 1000 MM
1 to 1000 MM
1 to 1000 MM
Materials
Steel, Aluminum, Brass, Copper, Titanium, Nickel Alloys, Tungsten Carbide, etc.
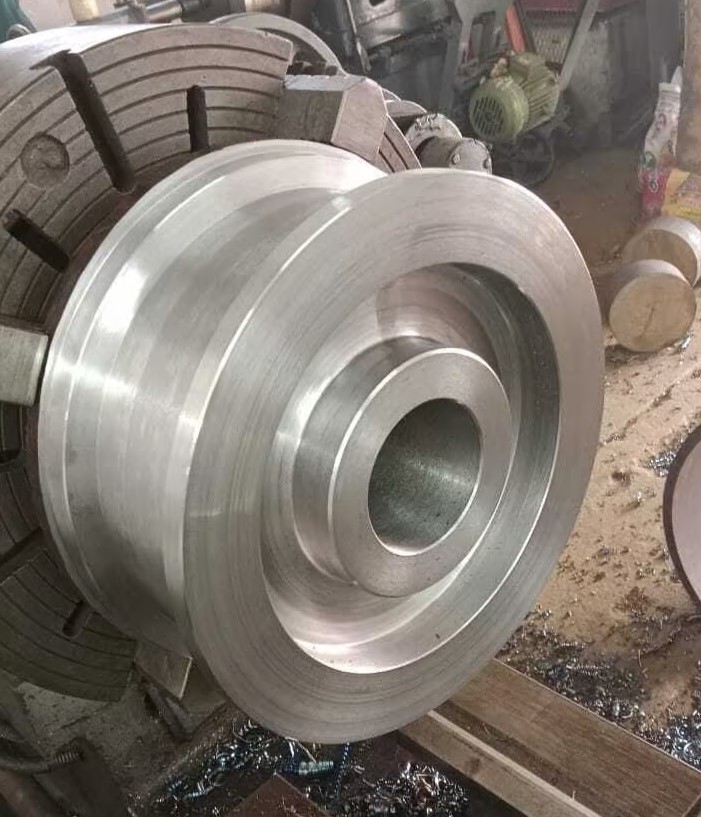
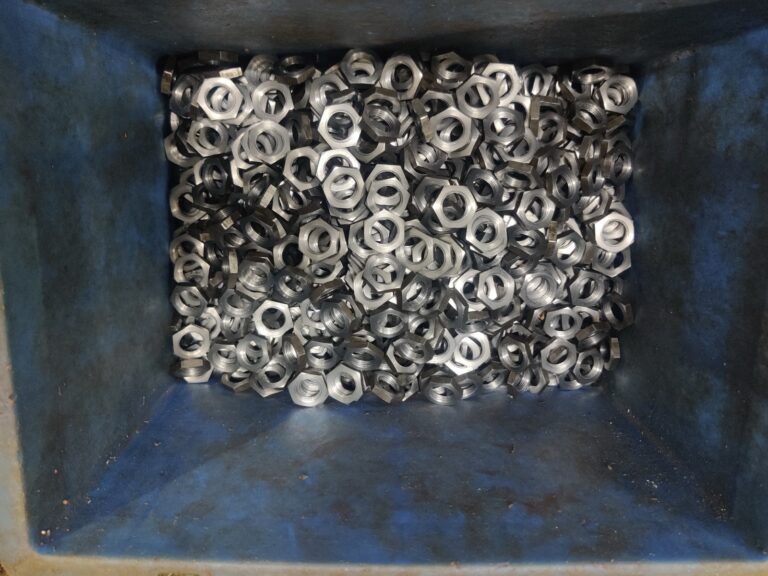
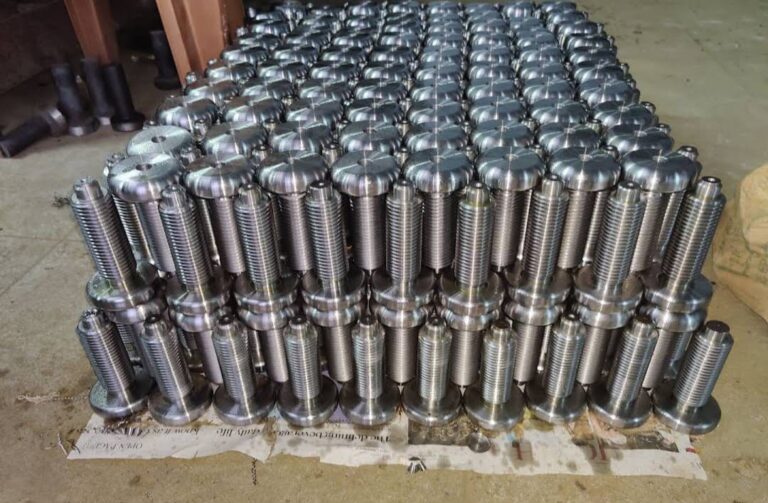
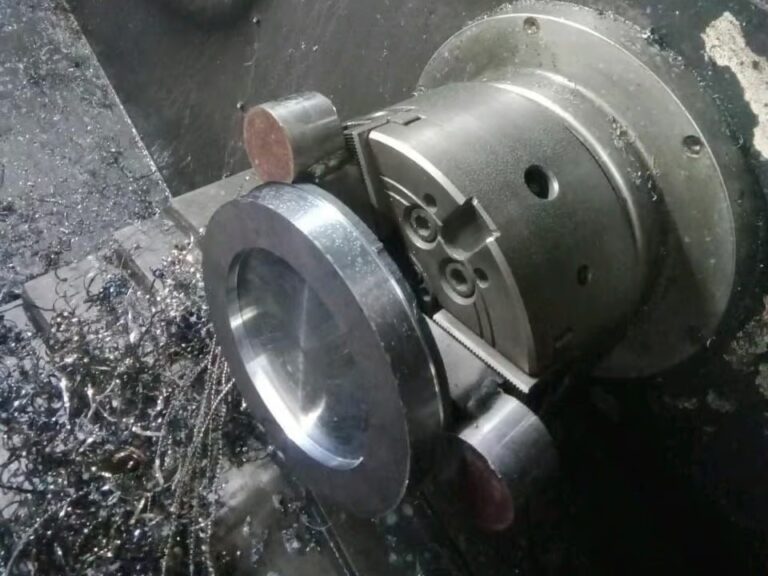
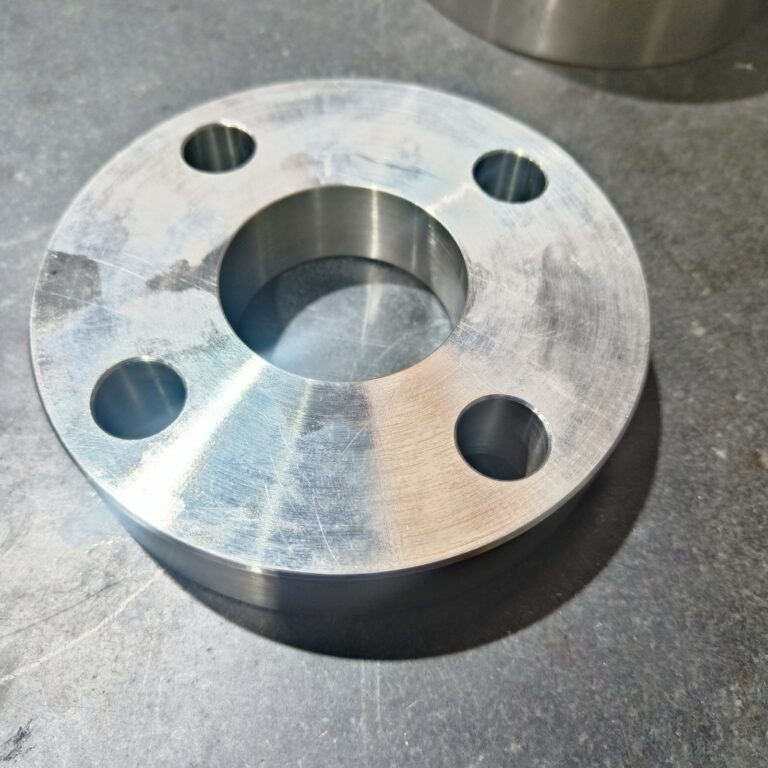
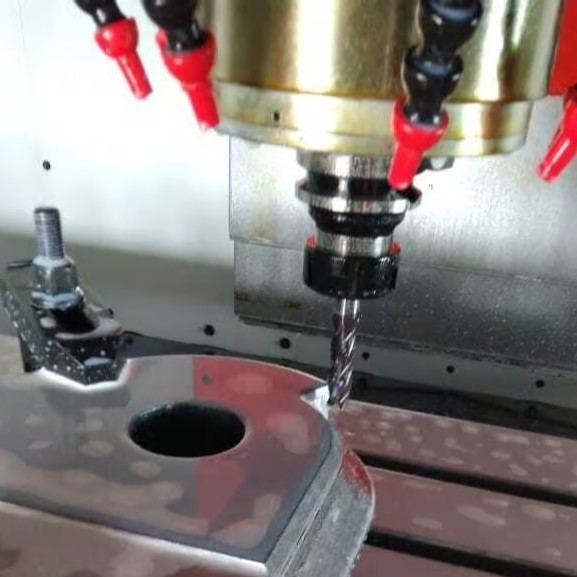
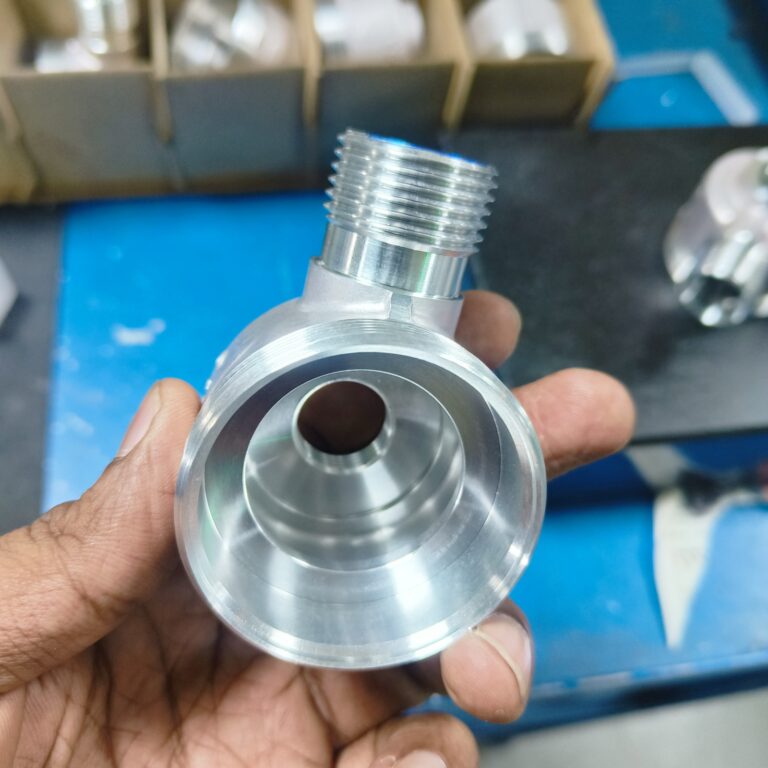
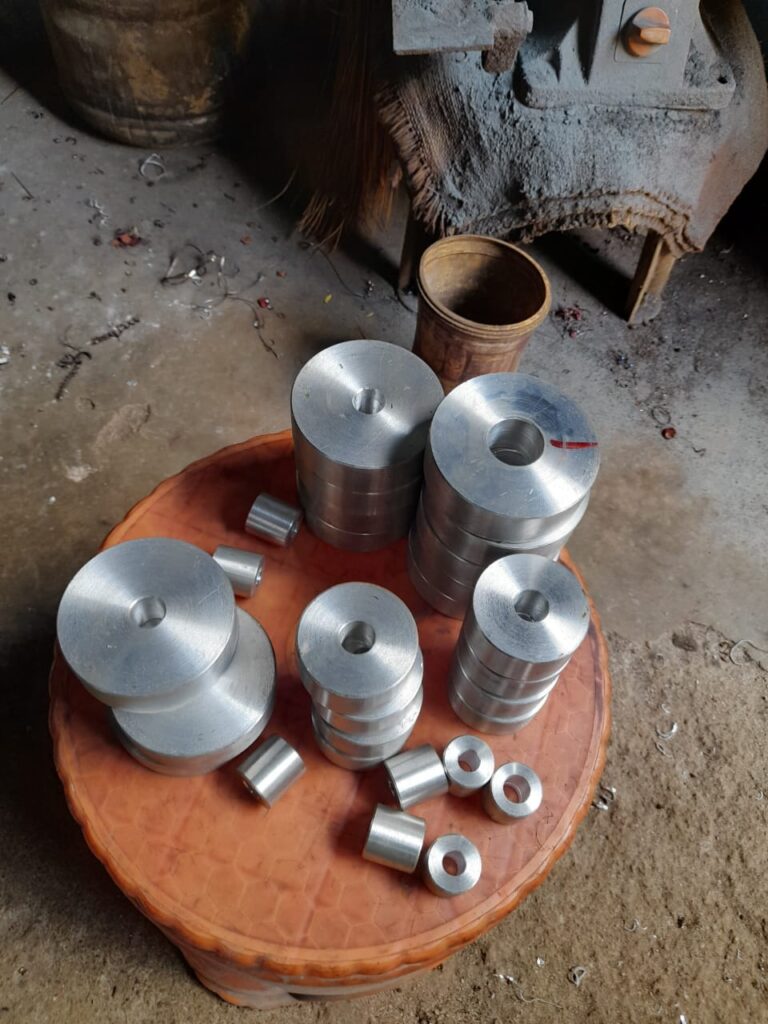
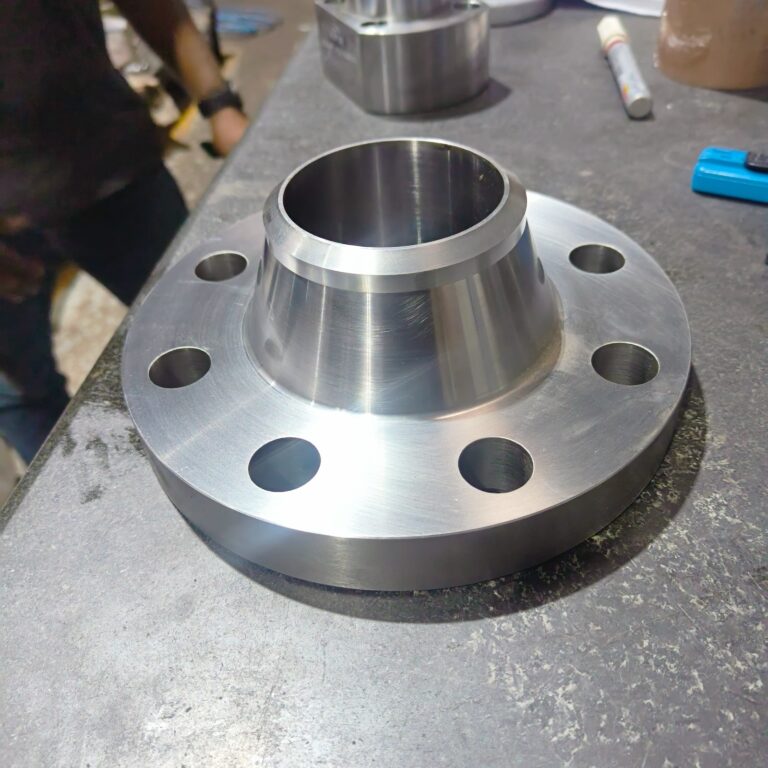
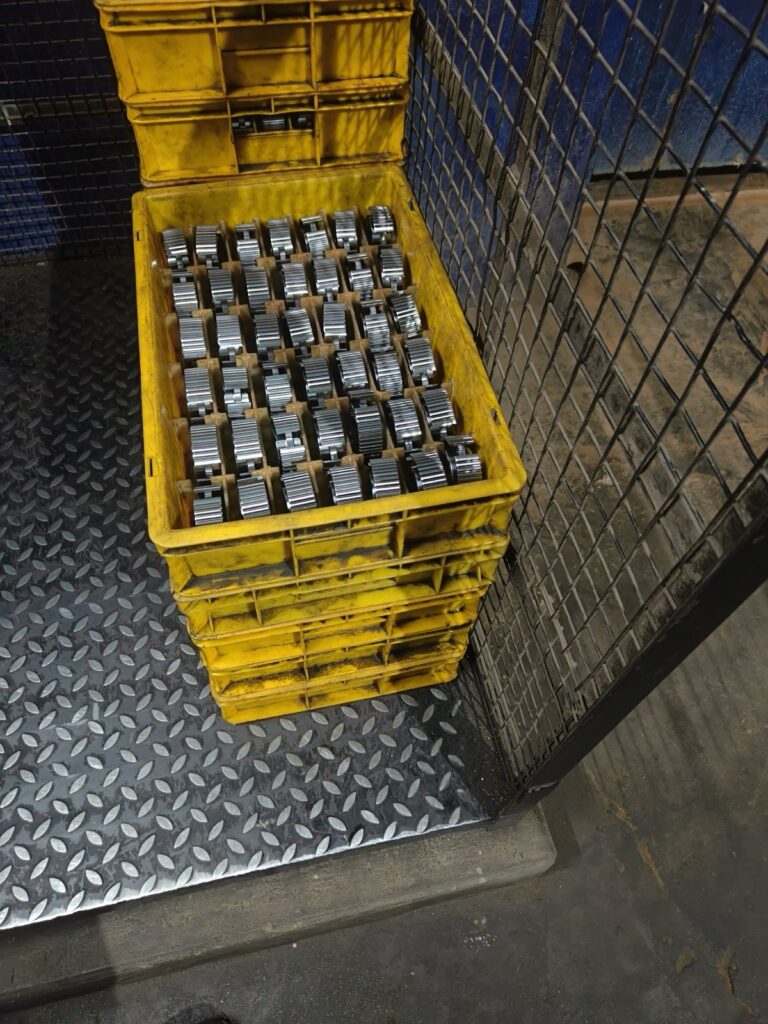
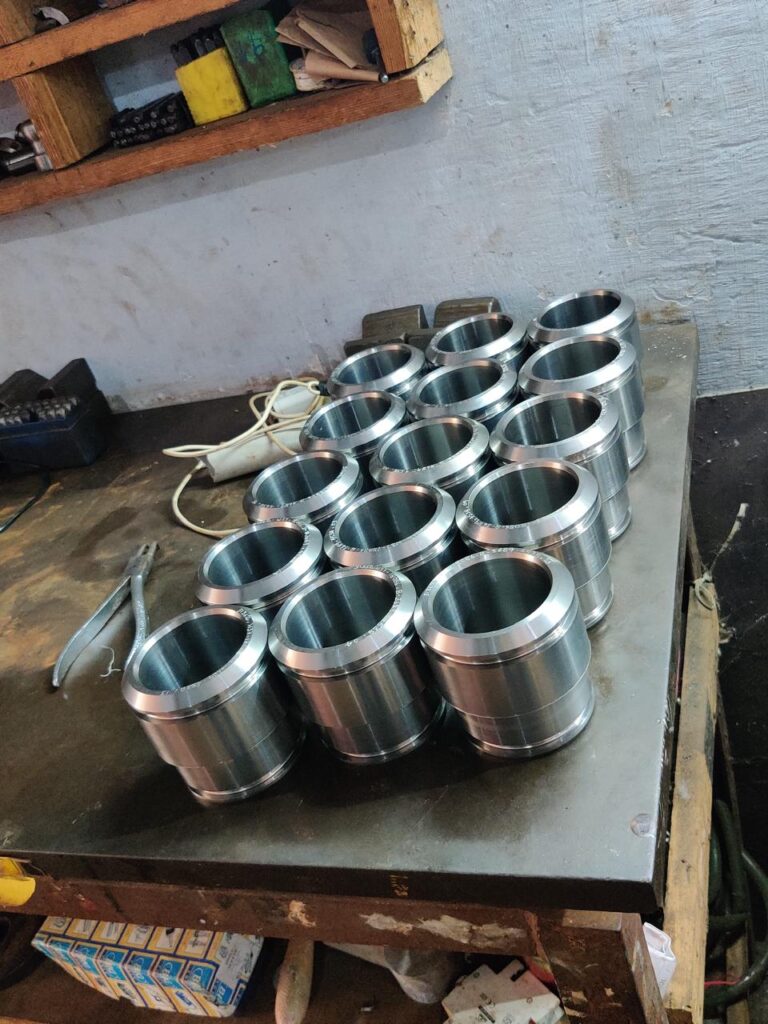
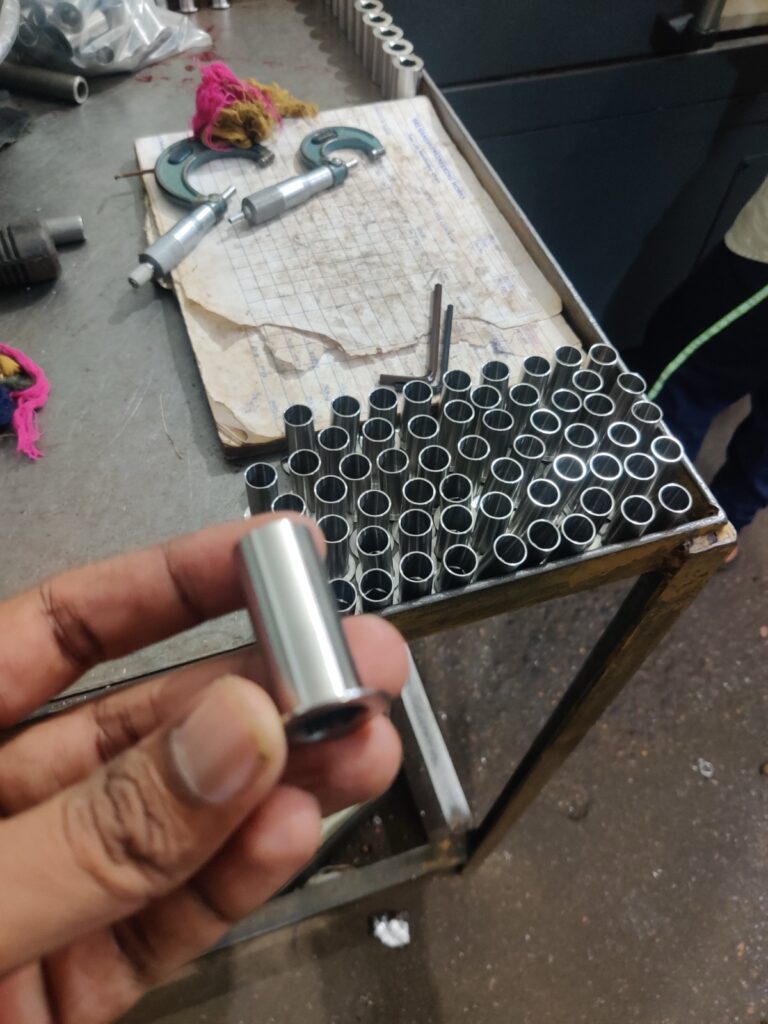
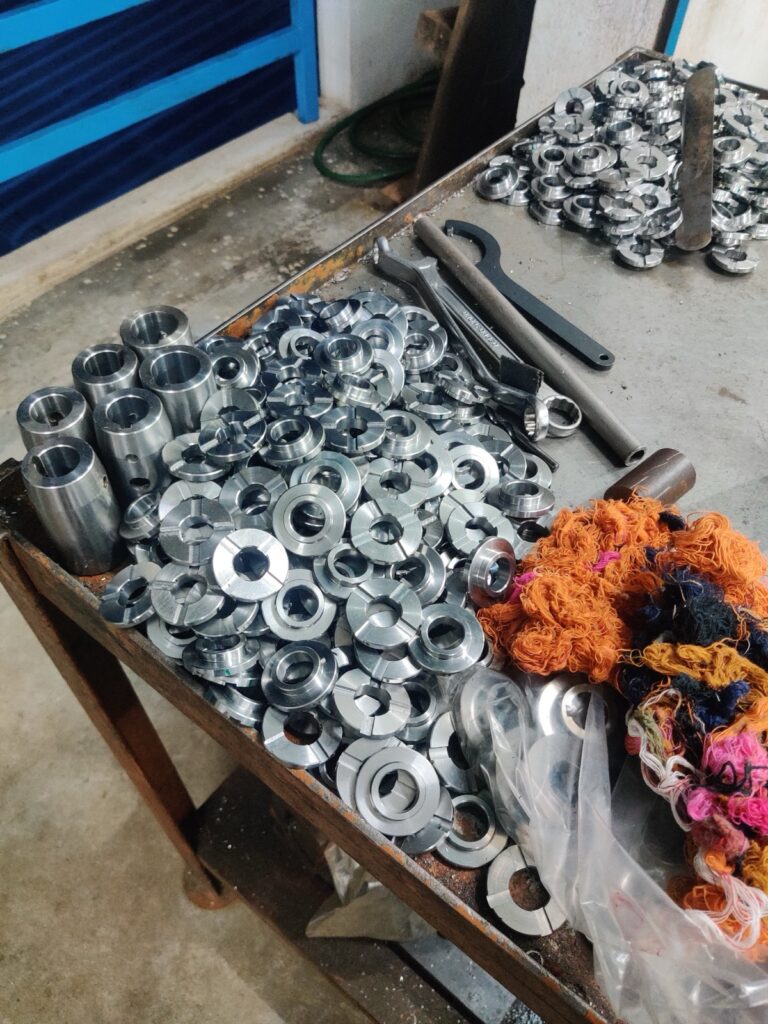
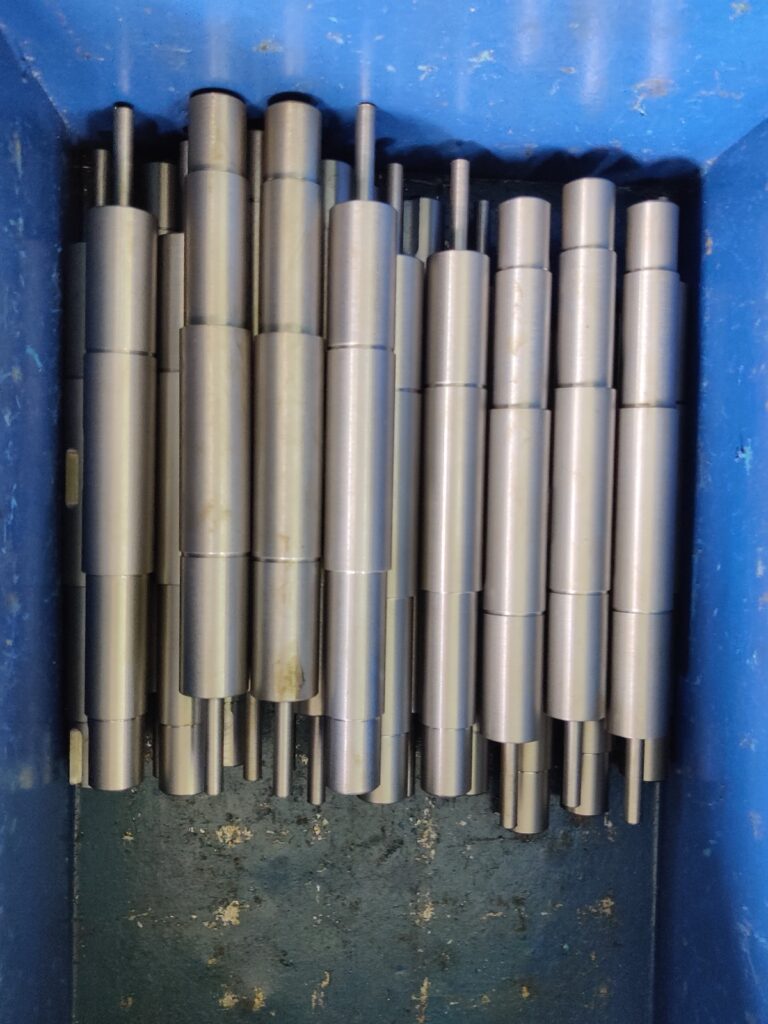
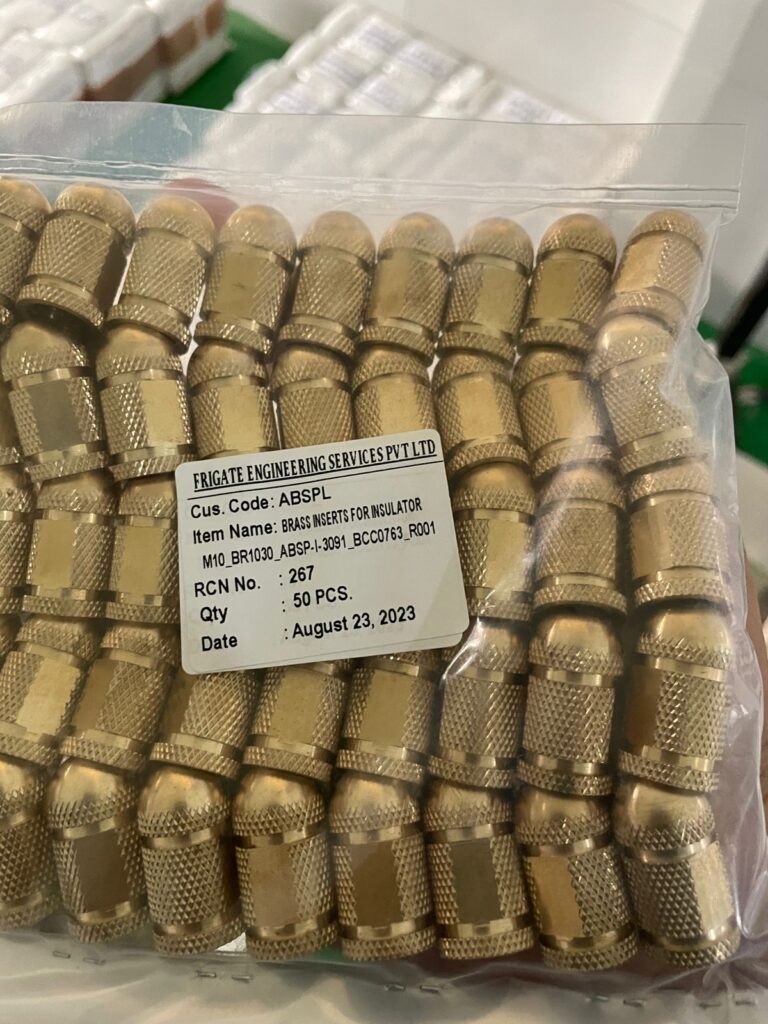
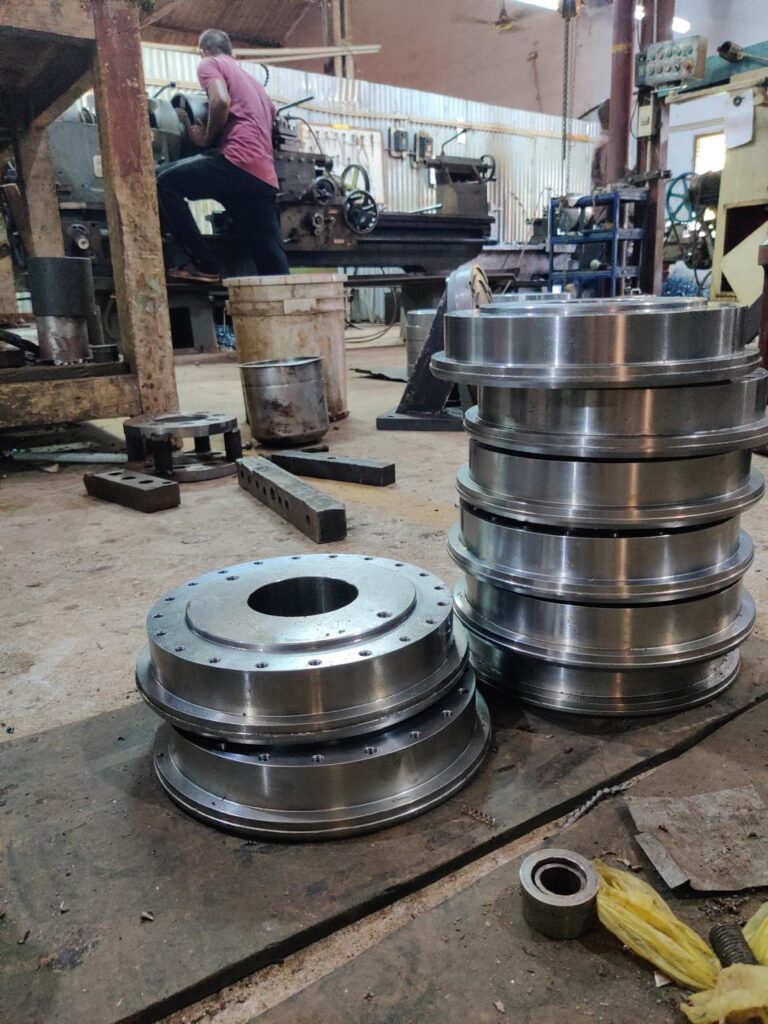
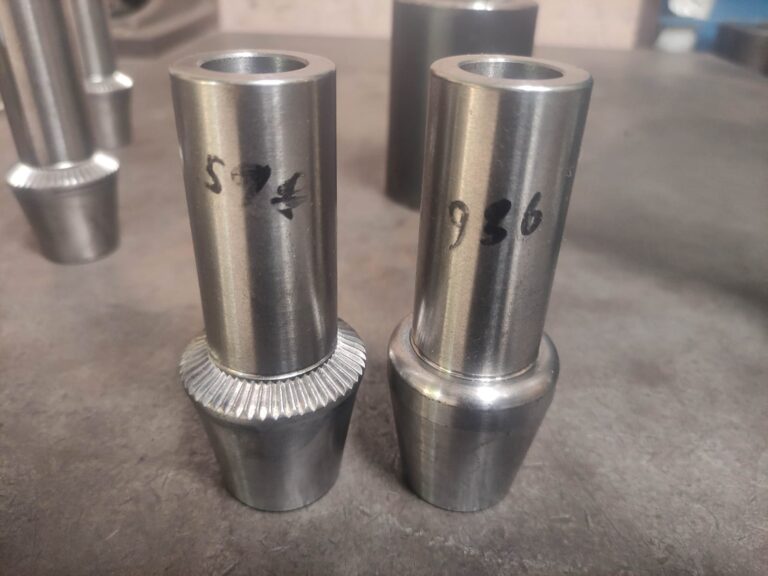
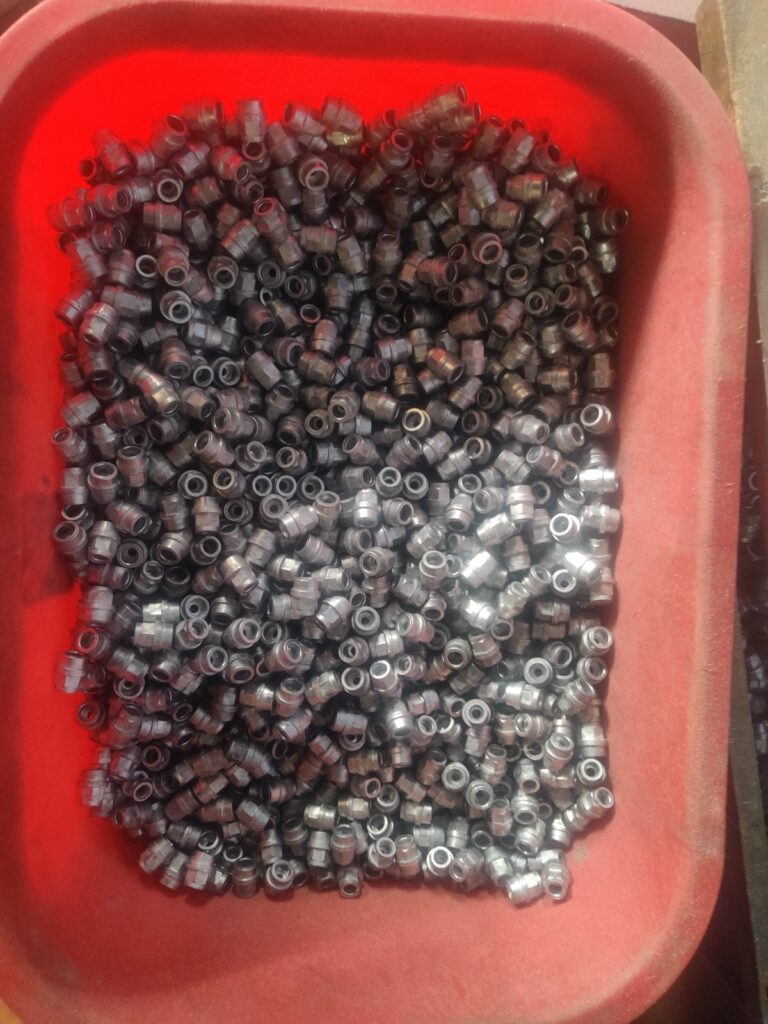
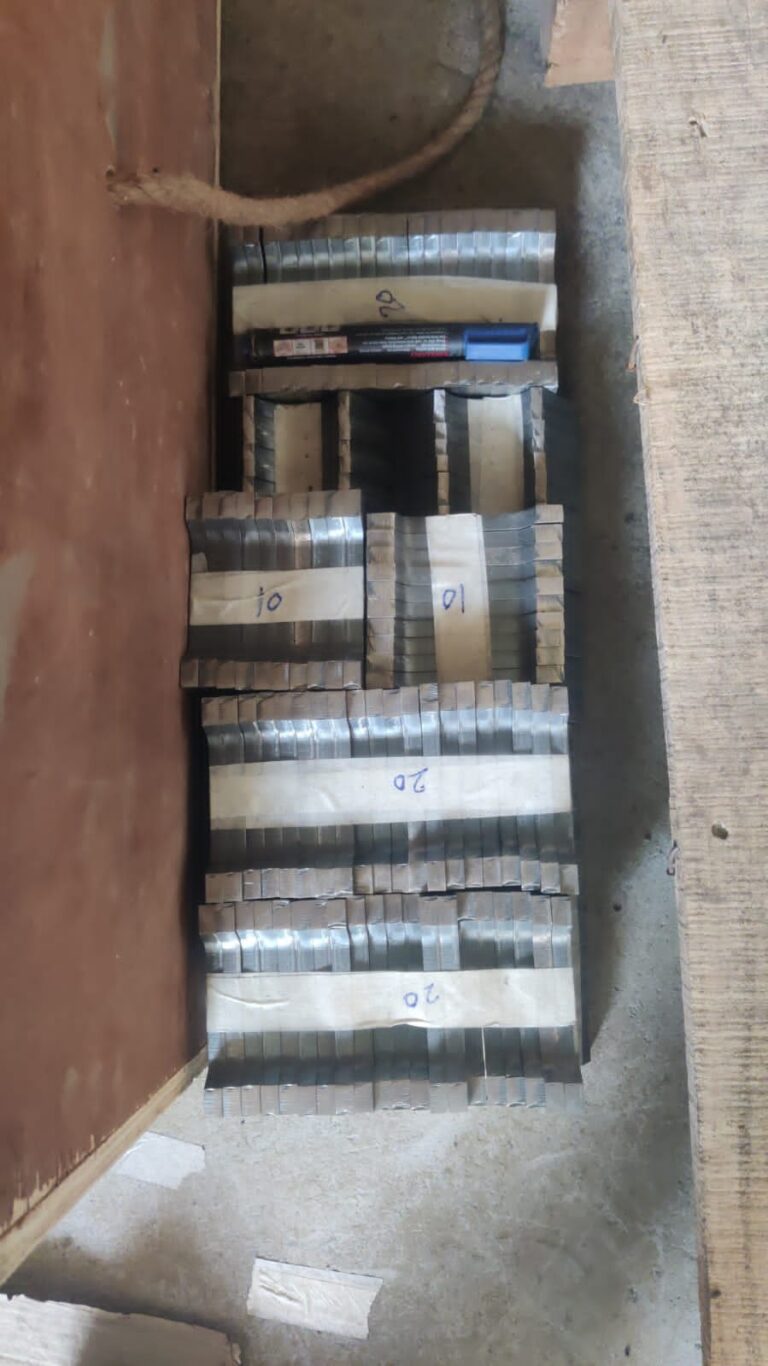
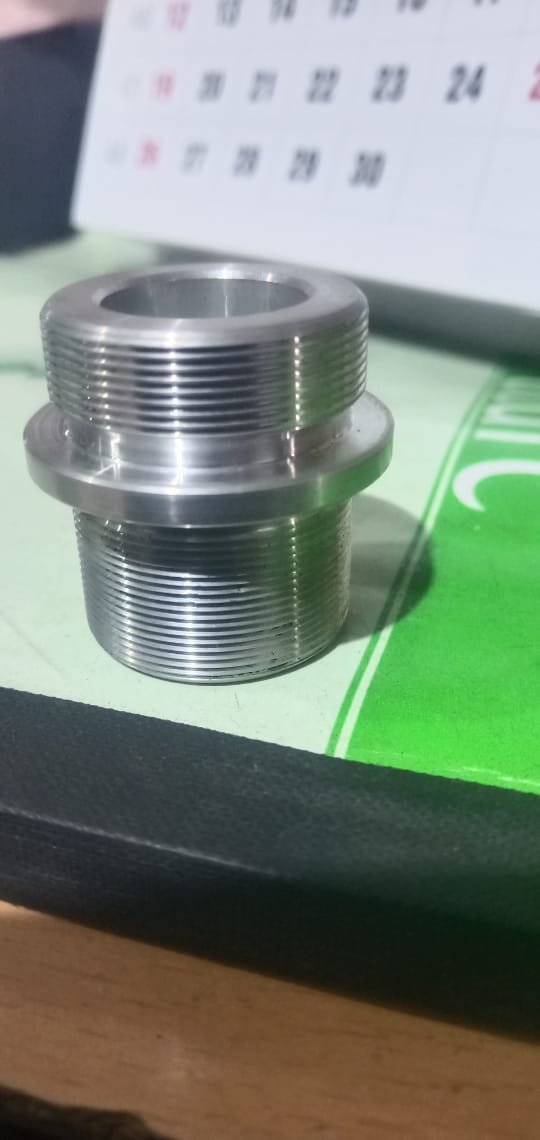
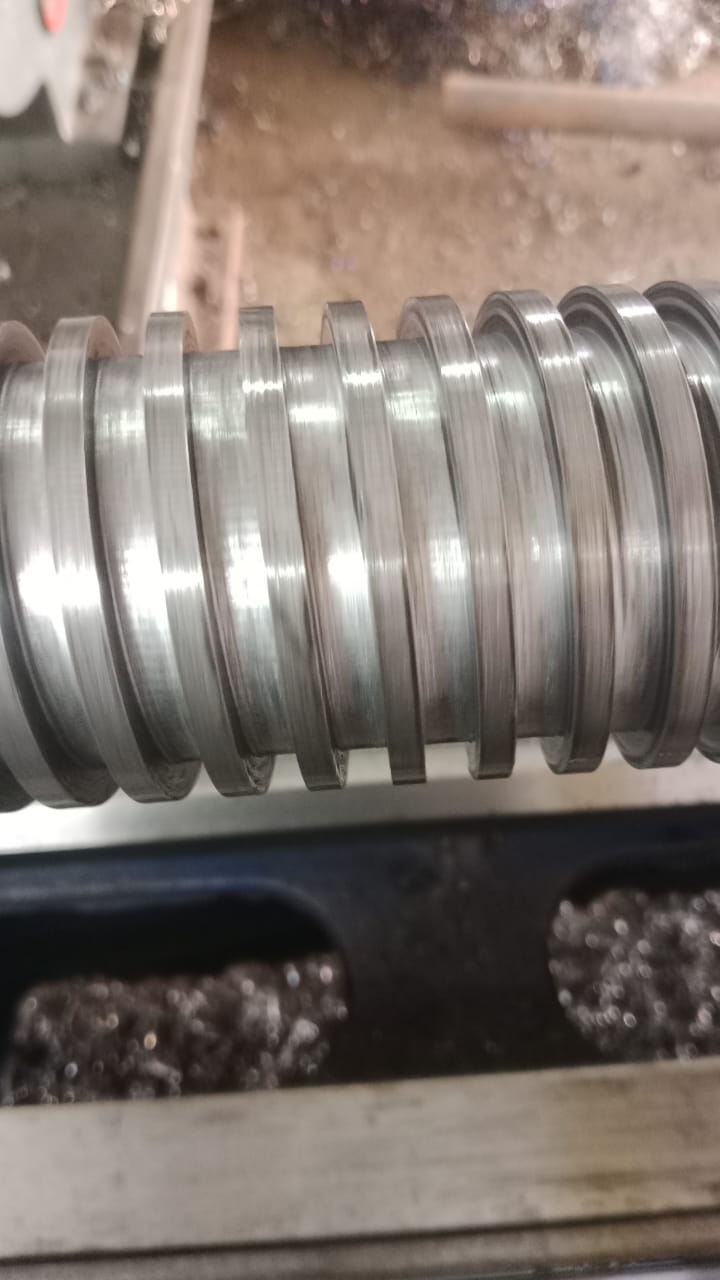
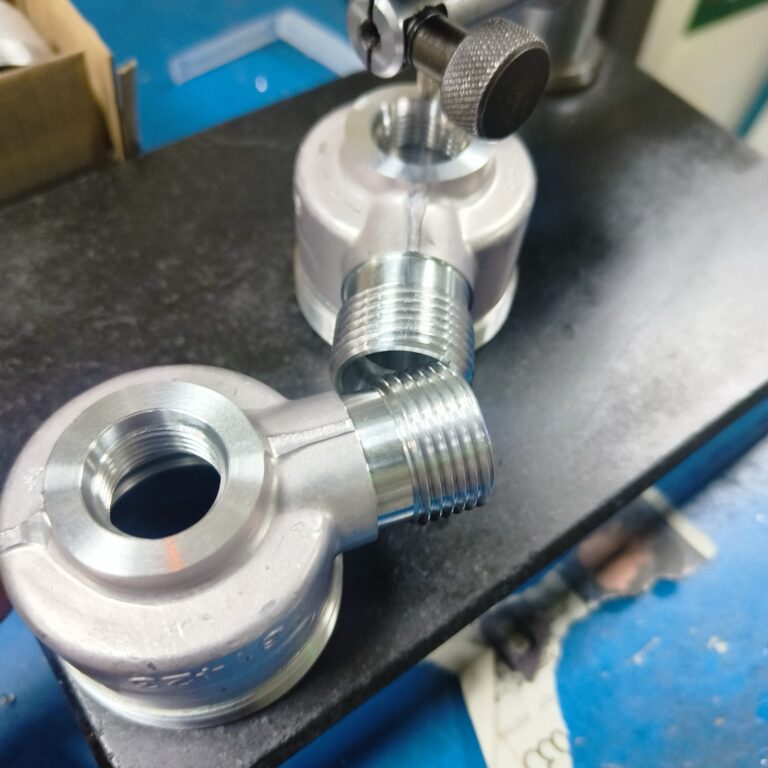
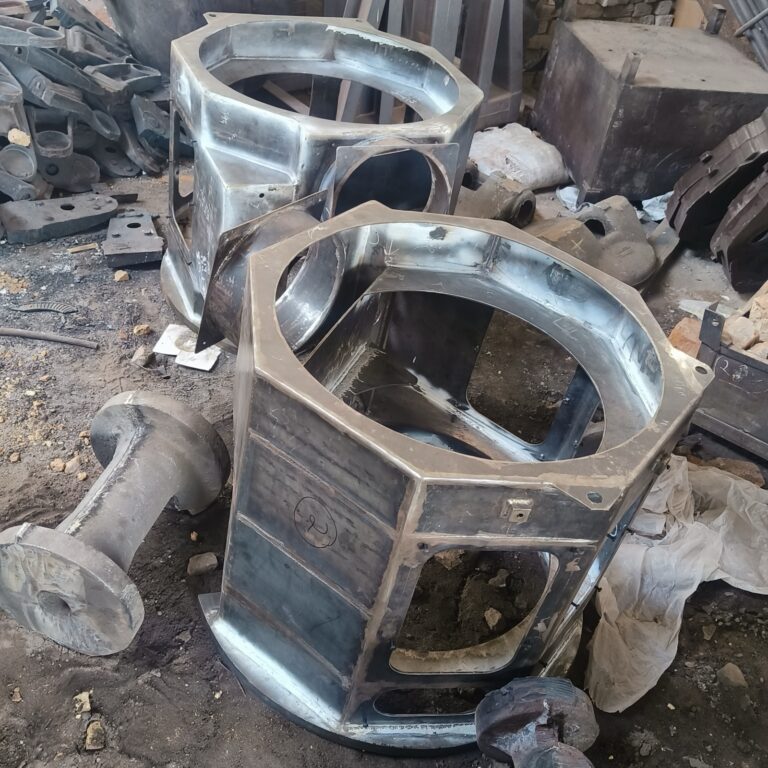
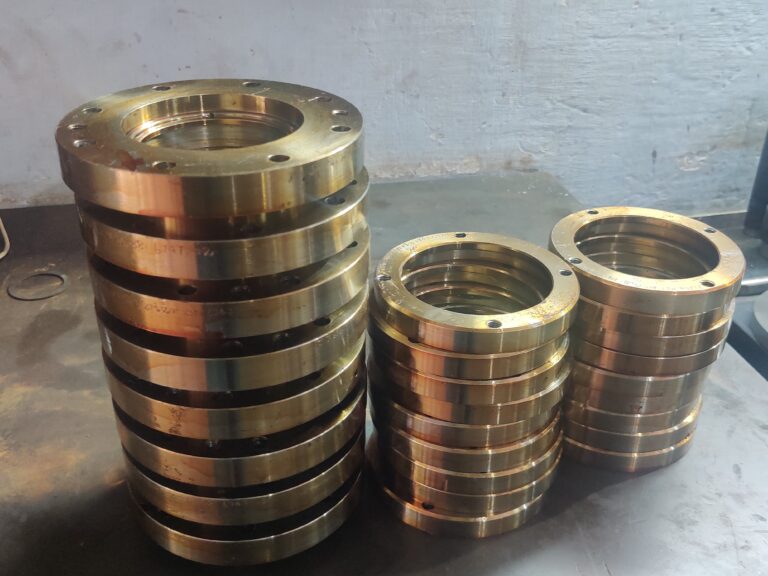
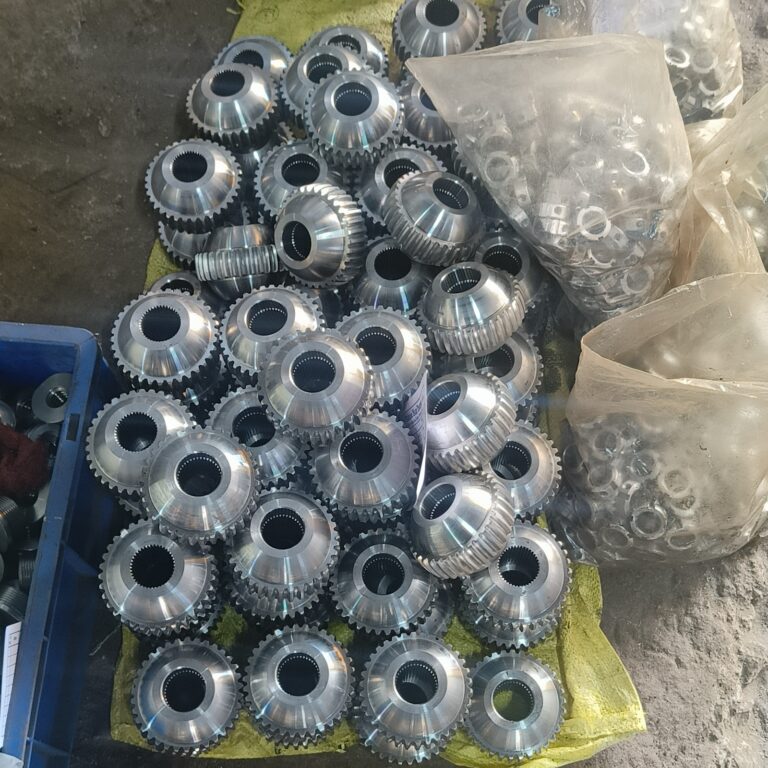
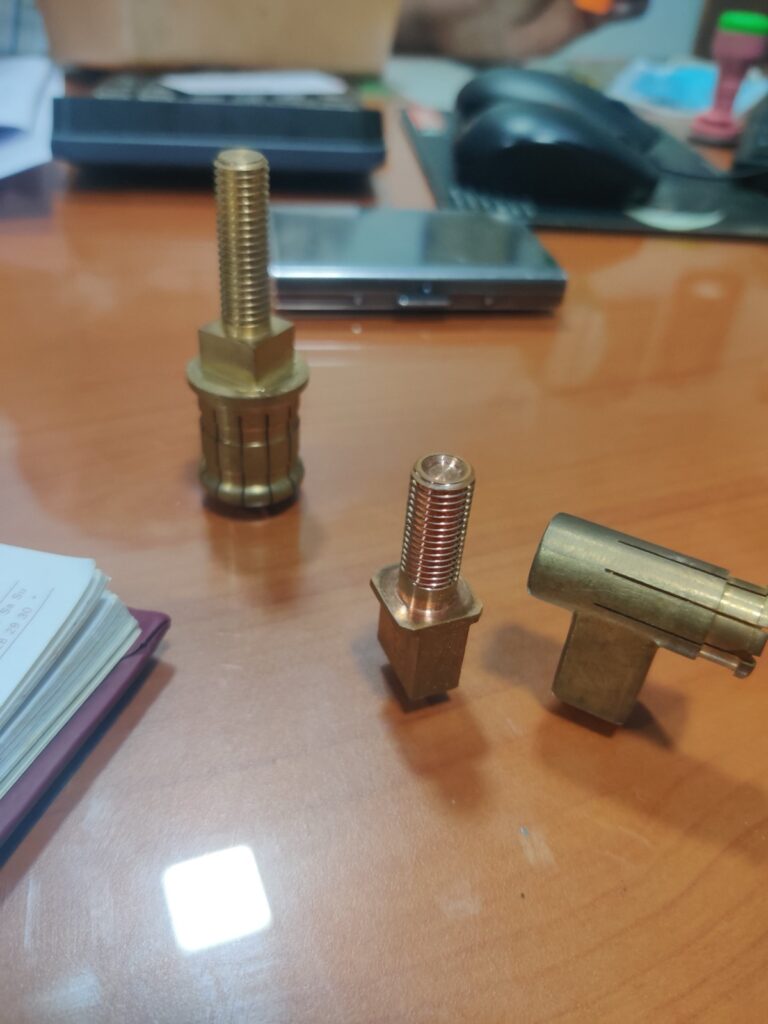
Plastics
Materials
1250 X 1250 MM
Within 10 microns
Engineering Plastics, Polyethylene, Polypropylene, Polyvinyl chloride, Polyethylene terephthalate, Bioplastics, etc.
Rubber
Materials
Natural rubber, Styrene-Butadiene Rubber, Nitrile Butadiene Rubber, Silicone Rubber, Fluorocarbon Rubber, Recycled Rubber, etc.
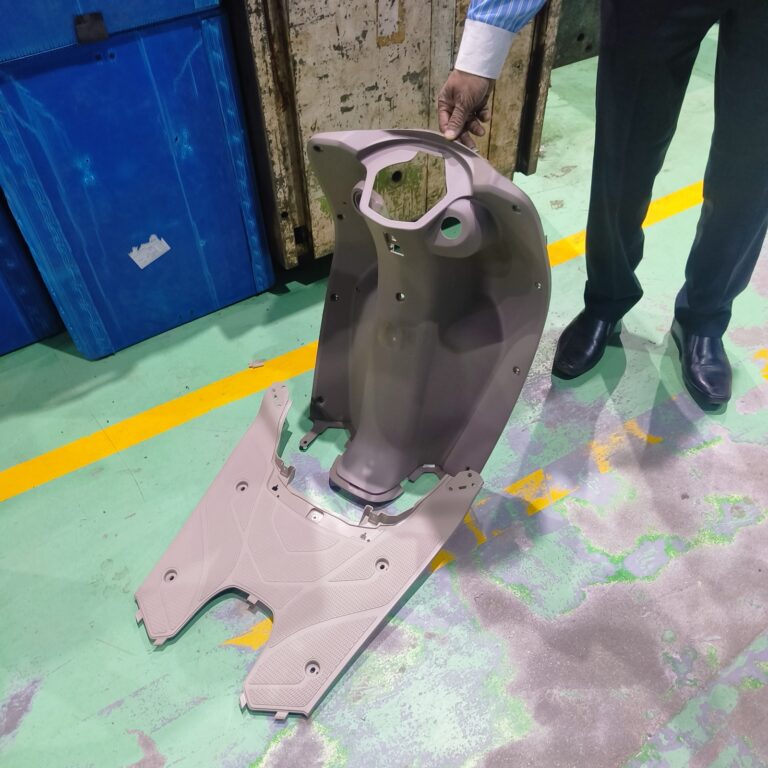
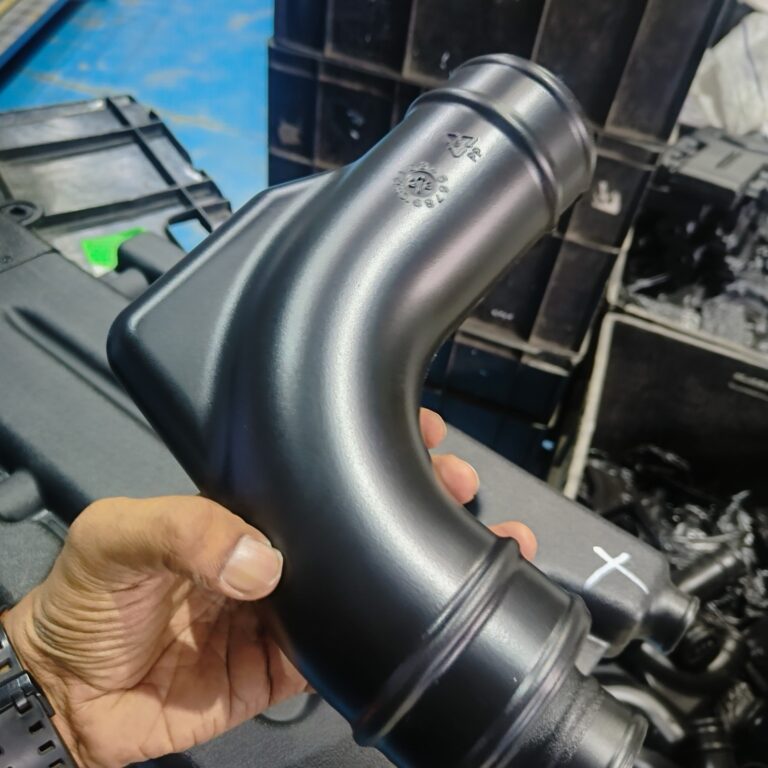
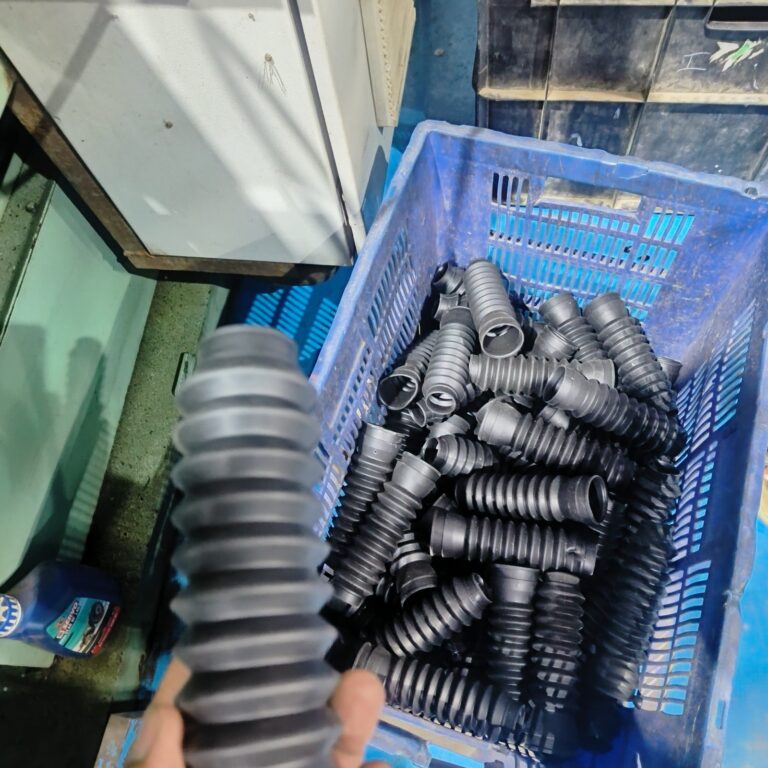
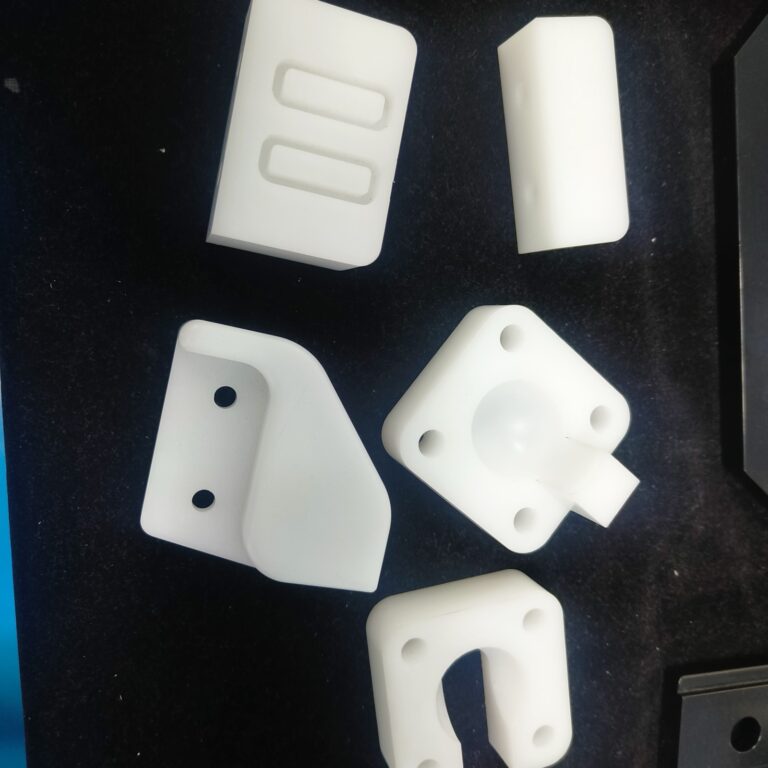
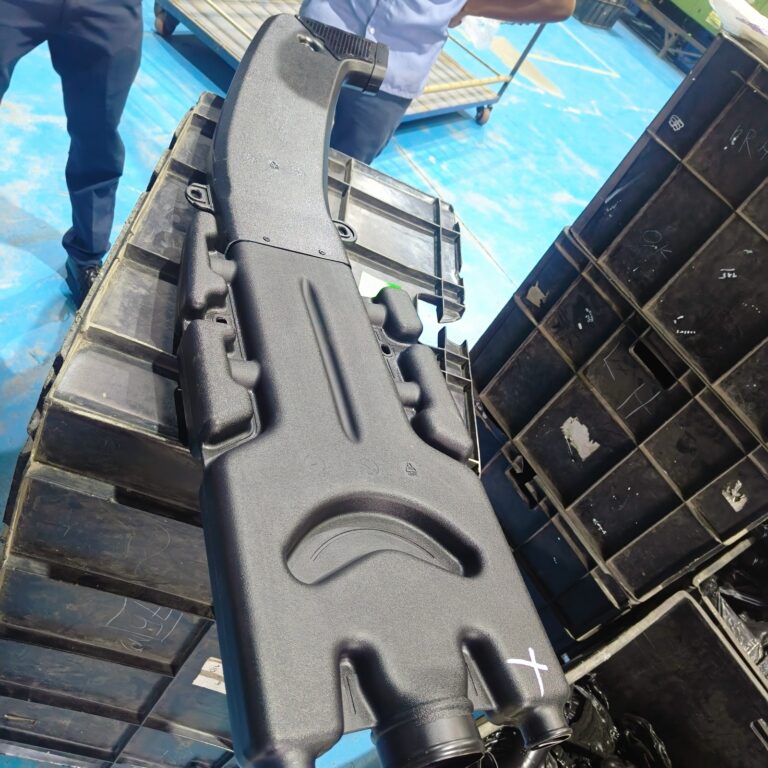
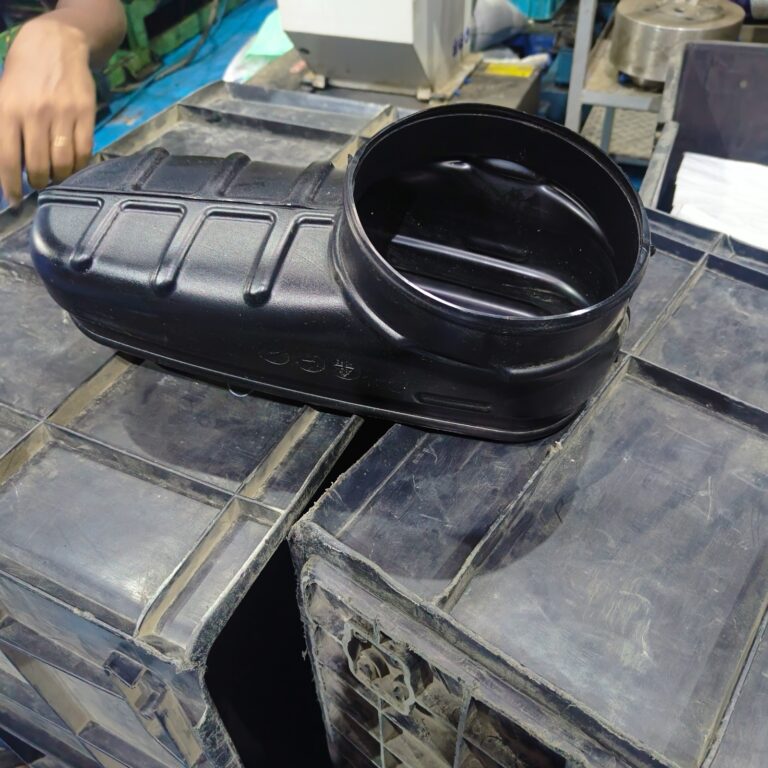
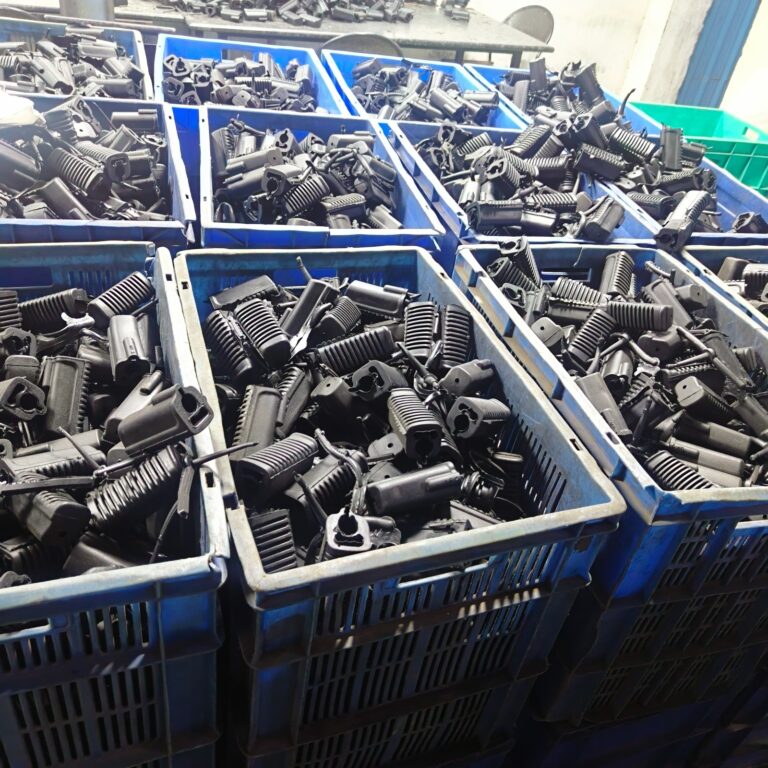
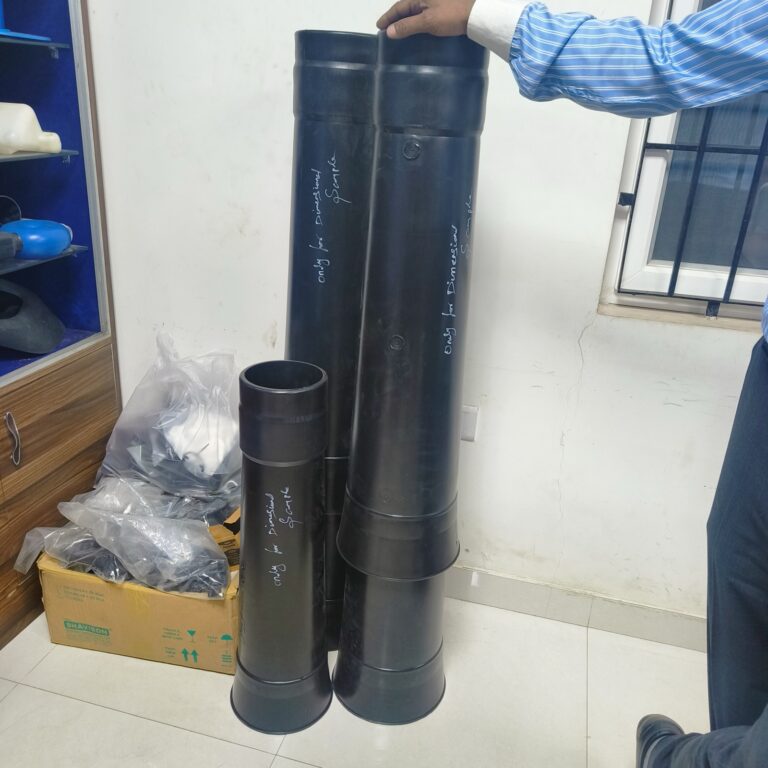
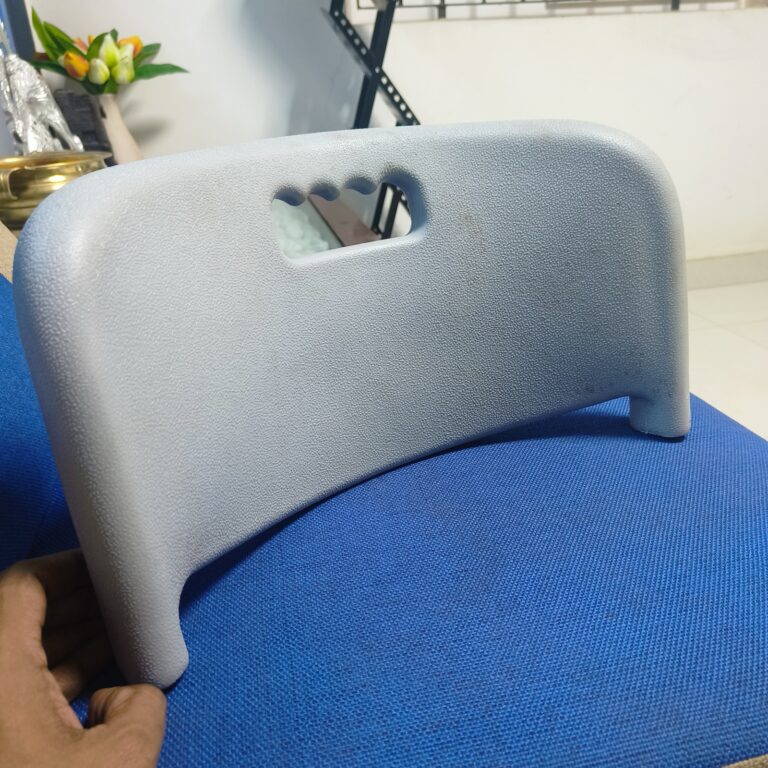
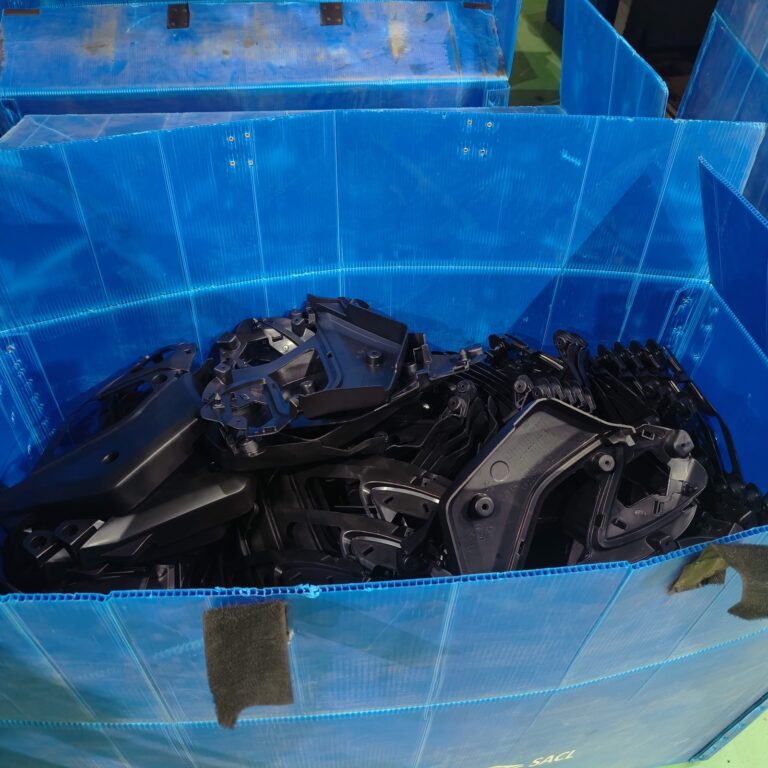
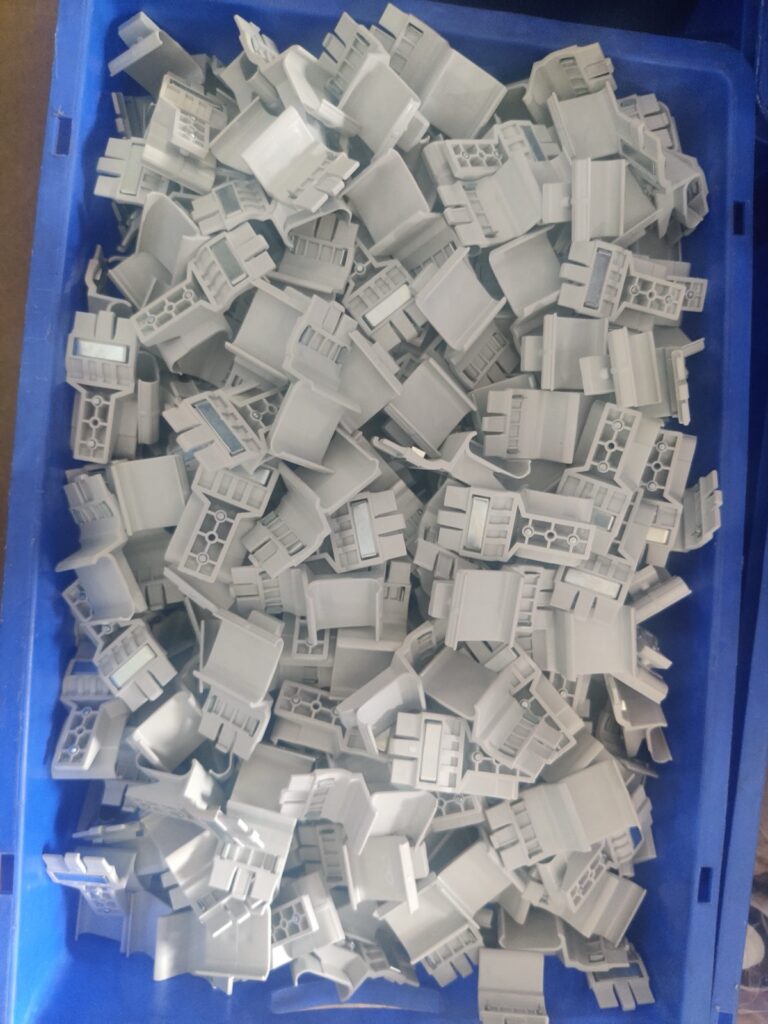
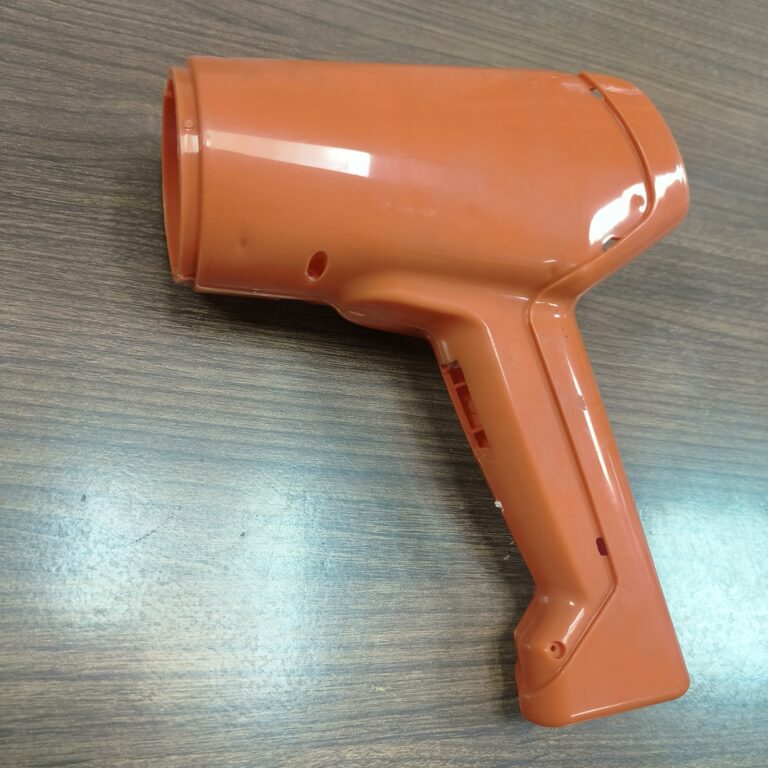
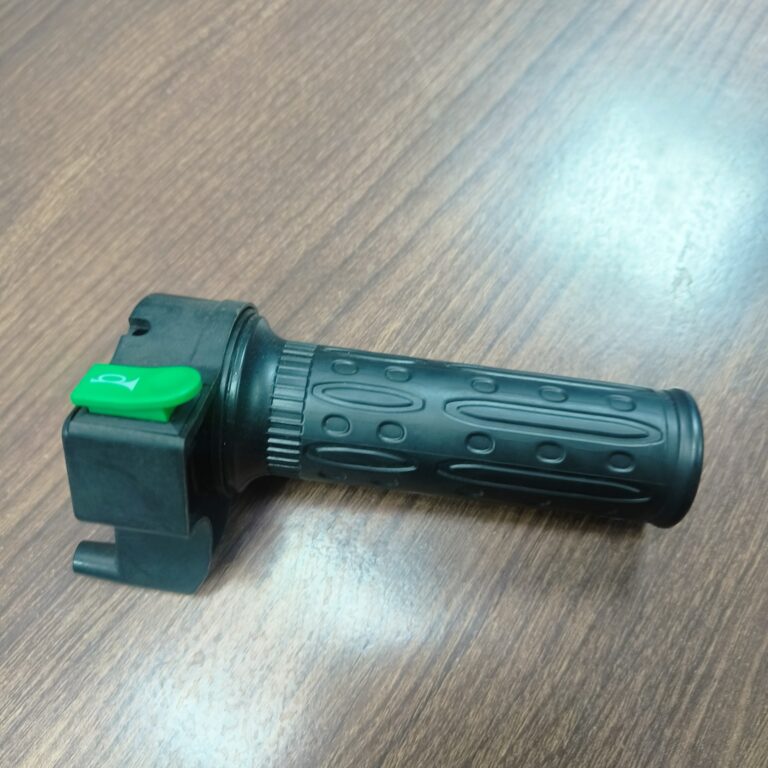
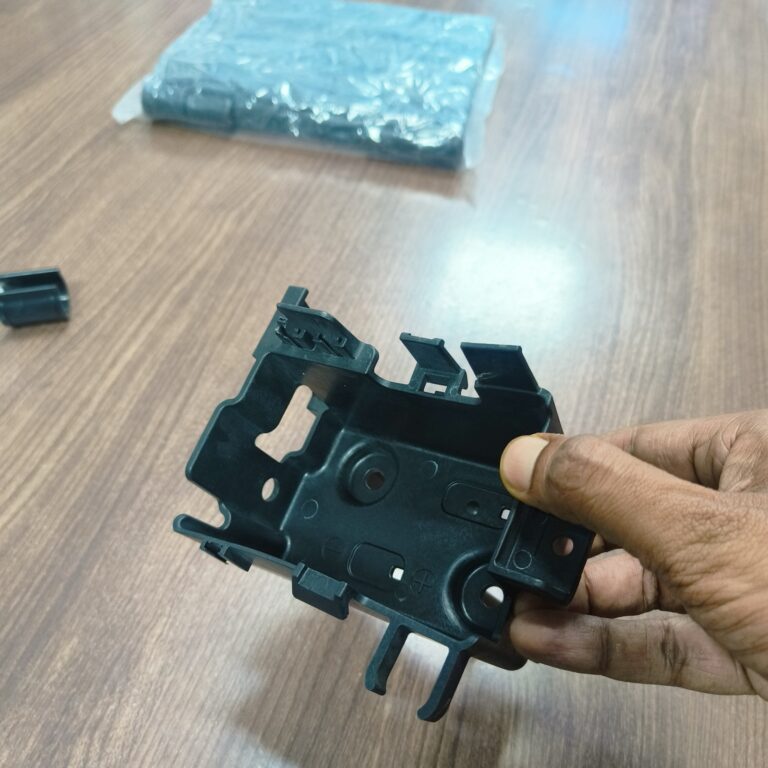
Heavy Fabrication
24000 MT/a
Materials
CS / MS, Alloy steel, Stainless Steel, etc.
Sheet Metal Fabrication
0.8 to 25 mm
Materials
Mild Steel, Stainless Steel, Aluminum, Brass, Copper, etc.


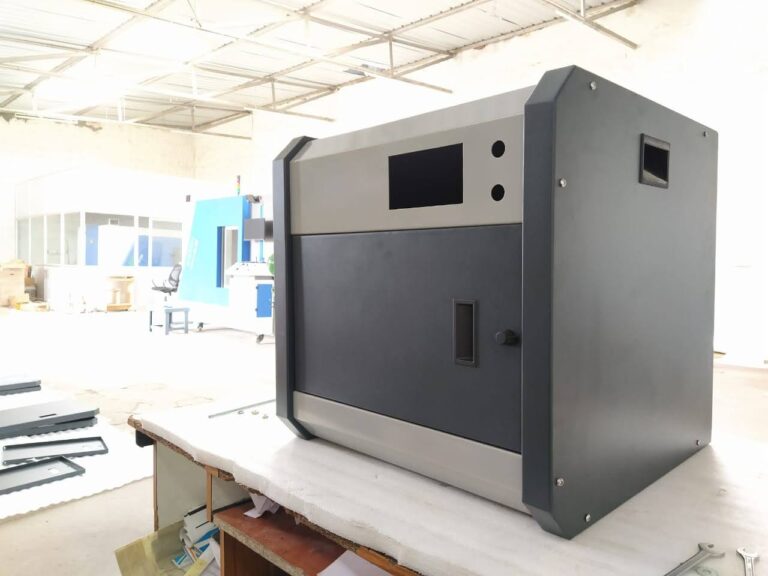


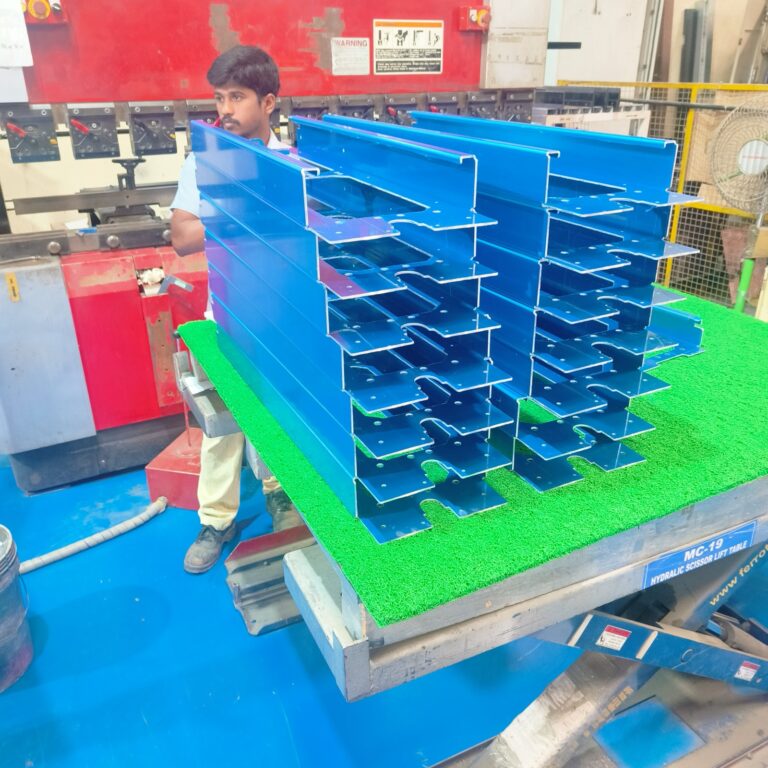
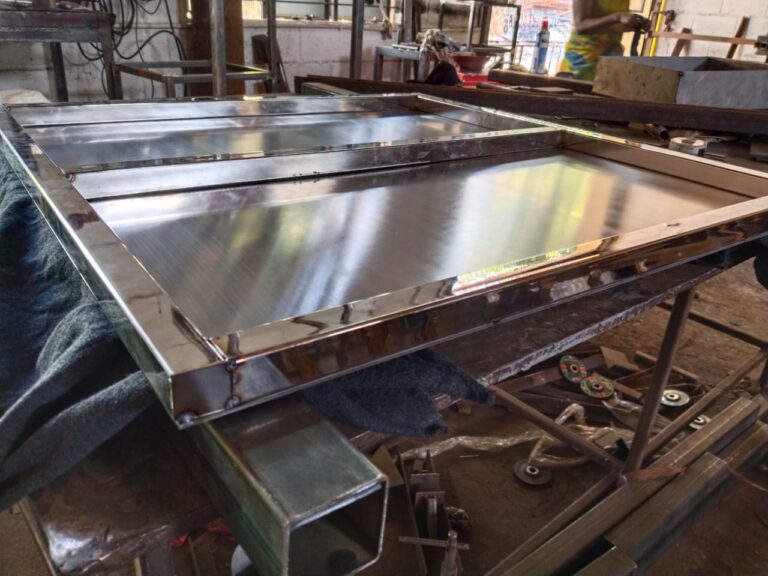
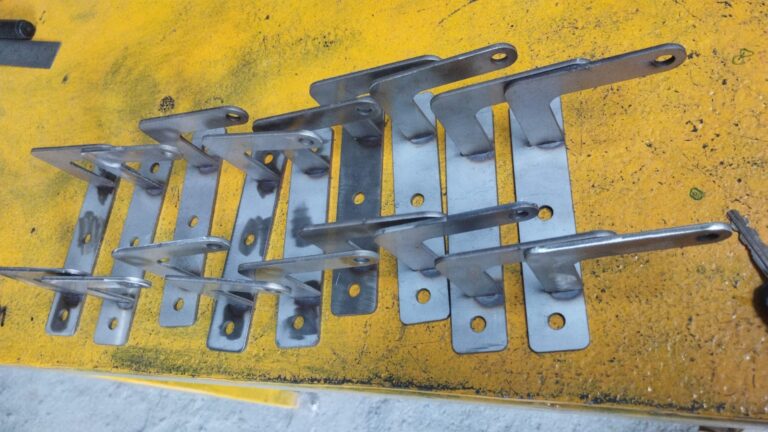
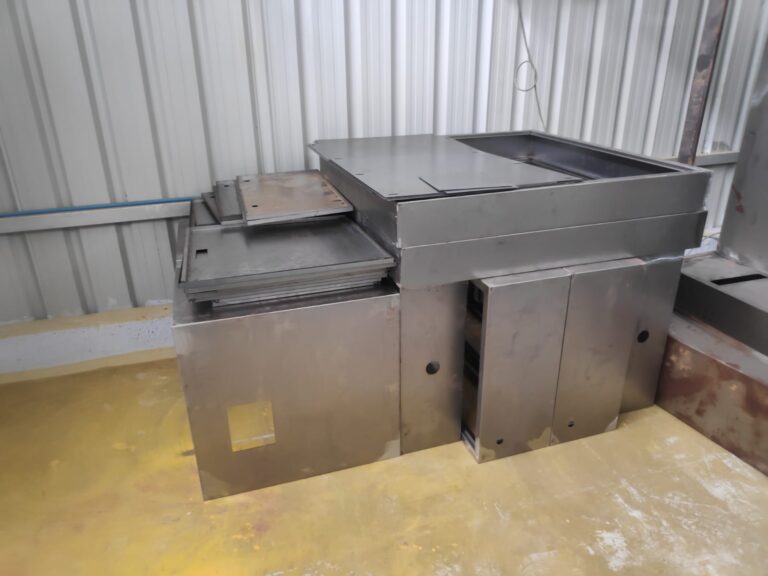
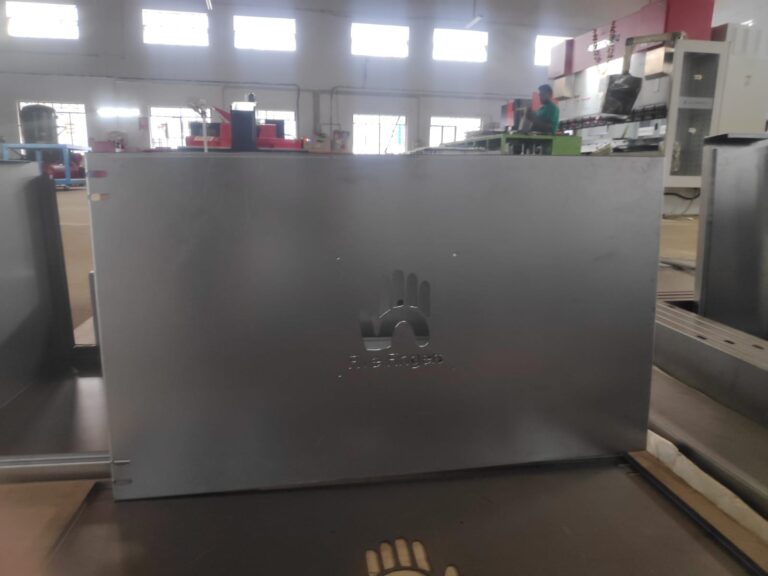
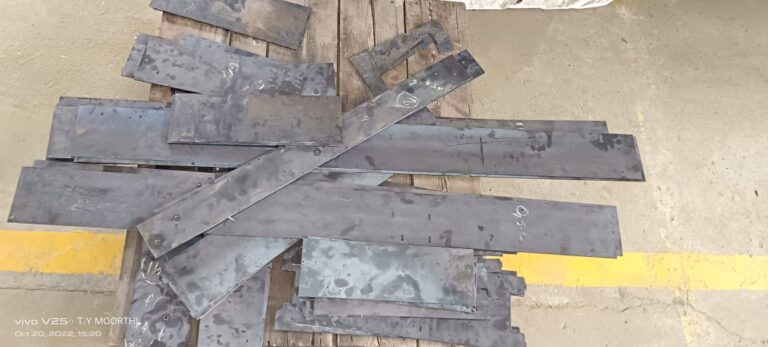
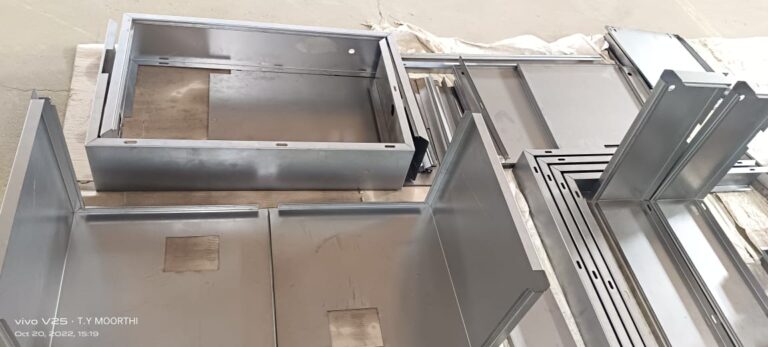
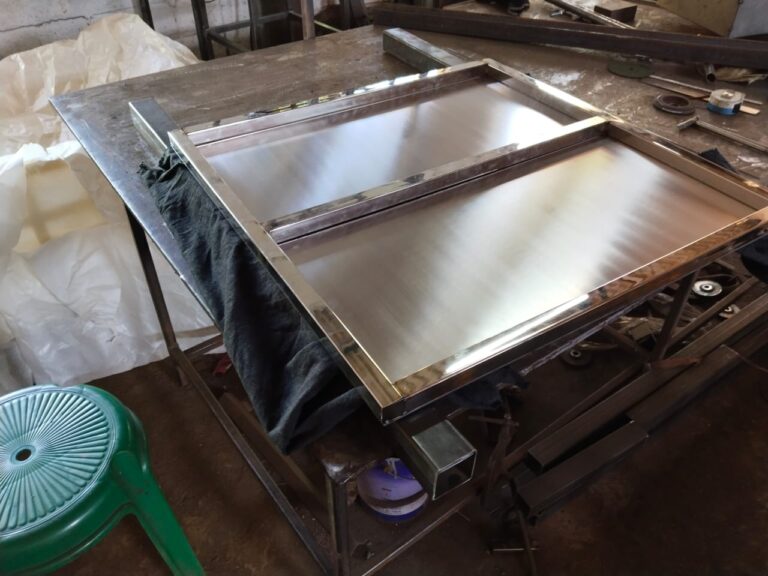
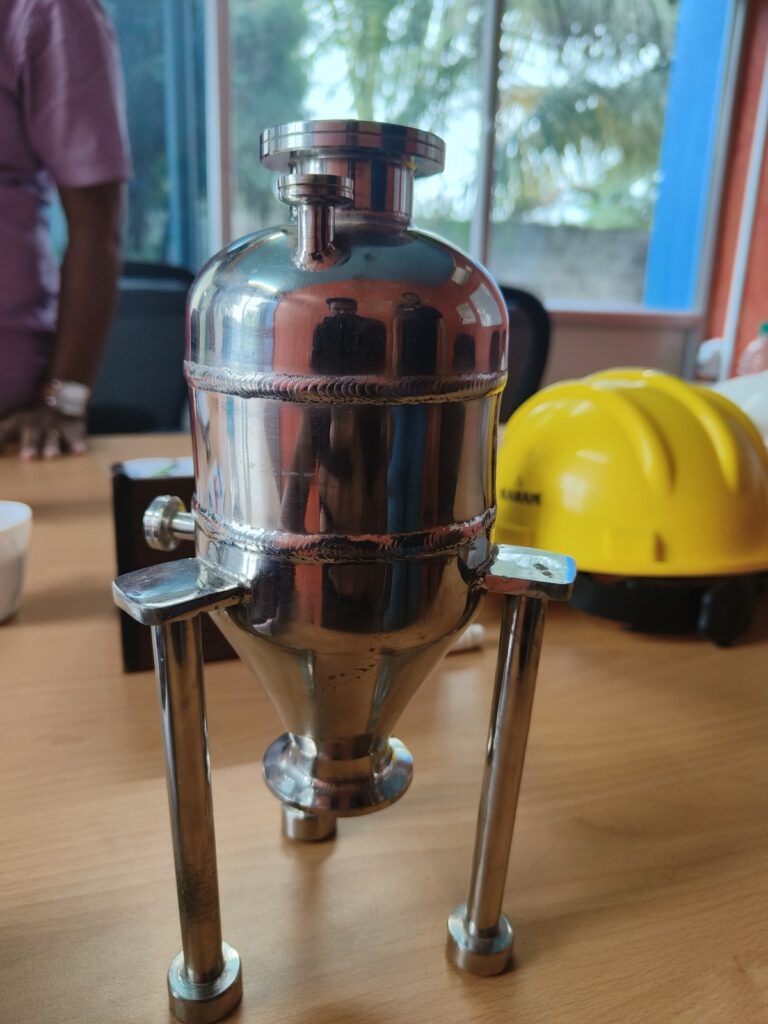
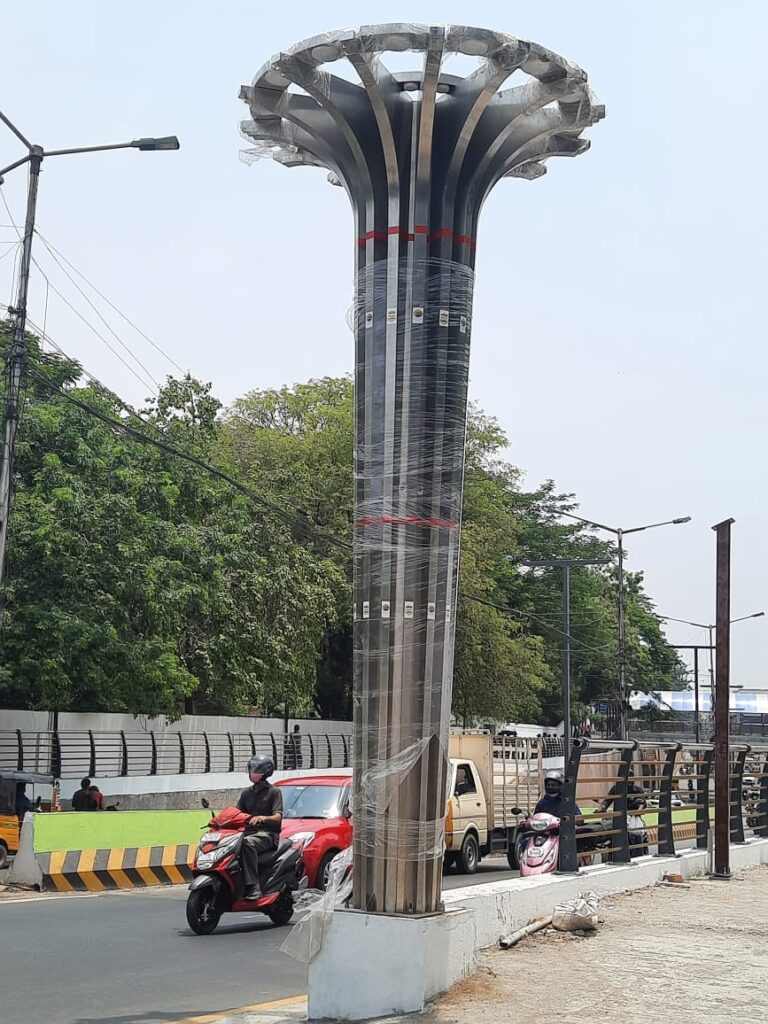
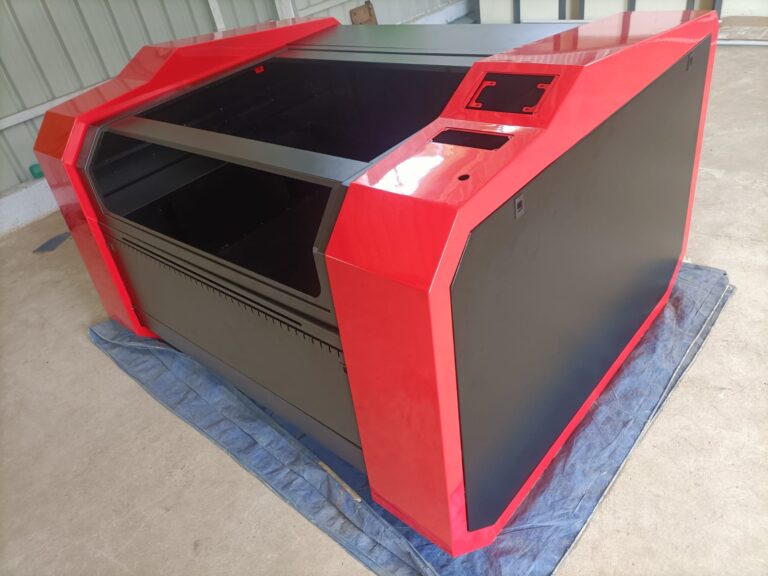
We'd love to Manufacture for you!
Submit the form below and our representative will be in touch shortly.
LOCATIONS
Registered Office
10-A, First Floor, V.V Complex, Prakash Nagar, Thiruverumbur, Trichy-620013, Tamil Nadu, India.
Operations Office
9/1, Poonthottam Nagar, Ramanandha Nagar, Saravanampatti, Coimbatore-641035, Tamil Nadu, India. ㅤ
Other Locations
- Bhilai
- Chennai
- USA
- Germany