Ceramic Mold Casting Services
Frigate’s Ceramic Mold Casting Services provides high precision and excellent surface finish. We use advanced ceramic shell techniques to ensure optimal strength and thermal resistance.
Our Clients





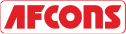

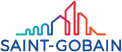


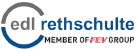

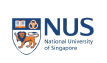
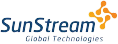

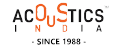




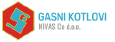
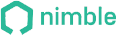
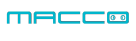












Advantages of Ceramic Mold Casting Services
Complex Core Formation
Ceramic mold casting can integrate complex internal cores, producing hollow and intricate structures without additional assembly.
High Reproducibility
Once the mold is made, ceramic mold casting ensures consistent quality and repeatability in production, even for large volumes of parts.
Thermal Resistance
Ceramic molds withstand extreme temperatures, making them ideal for casting materials like superalloys in aerospace and high-performance applications.
Complex Geometries
This method enables the creation of intricate designs and thin-walled structures, offering design flexibility for advanced industrial applications.
Custom Ceramic Mold Casting Services
Custom ceramic mold casting services high precision and accuracy for complex geometries. It is ideal for producing intricate parts with tight tolerances. The process supports various materials, including superalloys, ensuring suitability for demanding aerospace and automotive applications. With exceptional thermal resistance, ceramic molds perform well under extreme temperatures. The smooth surface finish reduces post-processing requirements, improving efficiency. This method also offers design flexibility, enabling the creation of complex internal structures and thin-walled components.

Get Your Quote Now
- Instant Quotation
- On-Time Delivery
- Affordable Cost
Our Ceramic Mold Casting Process






A precise pattern of the component is made from a material like wax, which mimics the final product's shape. This pattern is created using methods such as 3D printing or machining.
The pattern is coated with a fine ceramic material to form a shell. This process involves multiple layers of ceramic slurry and sand, followed by drying between each layer to build strength.
After the ceramic shell has been built, it is dried and fired in a kiln. This removes any moisture and hardens the shell to withstand the high temperatures of molten metal.
The shell is then heated to a temperature where the wax pattern inside melts and is drained away, leaving a hollow ceramic shell. This process is often called "lost wax" casting.
Once the shell is ready, molten metal or alloy is poured into the cavity left by the removed pattern. The material fills the shell, taking the shape of the original pattern.
The metal cools and solidifies inside the ceramic shell. Once cooled, the ceramic shell is broken away, revealing the cast component, which is then cleaned, inspected, and finished as required.
Post Processing Services in Cold Chamber Casting
Cold chamber casting produces high-strength, complex metal parts, but post-processing is essential to enhance quality, durability, and functionality. Various techniques refine surface finish, improve mechanical properties, and ensure corrosion resistance.
Aerospace (turbine blades), Automotive (engine components), Industrial (valves, pumps)
Aerospace (turbine components, structural parts), Medical (implants), Automotive (brake discs)
Aerospace (high-strength alloys), Automotive (high-performance engine parts), Oil & Gas (drill bits)
EDM: 0.05 - 0.1 mm precision, up to 5-axis milling
Aerospace (precision engine parts), Automotive (gears, shafts), Medical (surgical instruments)
Aerospace (high-temp resistant parts), Electronics (heat sinks), Automotive (cylinder heads)
Aerospace (critical components), Medical (bio-compatible implants), Jewelry (luxury items)
Aerospace (critical castings), Automotive (safety parts), Medical (implant verification)
Laser repair: 50 - 100 W, Brazing: 600 - 700°C
Aerospace (repair of cracked turbine blades), Automotive (defective castings), Industrial (tool repairs)
Aerospace (cleaning of complex parts), Medical (implant sterilization), Automotive (engine parts)
Deburring: 0.1 - 0.5 mm tolerance
Automotive (chassis parts, trim components), Aerospace (fuel systems), Industrial (tooling, fittings)
Methoding in Ceramic Mold Casting
Aerospace (turbine blades), Automotive (engine blocks), Energy (turbine nozzles)
Aerospace (engine parts), Oil & Gas (valve components), Automotive (brake parts)
Aerospace (high-precision components), Automotive (engine pistons), Energy (valve bodies)
Aerospace (turbine blades), Automotive (engine parts), Industrial (pump bodies)
Aerospace (high-precision castings), Automotive (engine components), Medical (surgical tools)
Aerospace (engine components), Automotive (structural parts), Industrial (machinery components)
Aerospace (turbine blades), Automotive (precision gears), Energy (turbine components)
Aerospace (casting integrity), Automotive (engine components), Oil & Gas (pressure vessels)
Aerospace (turbine parts), Automotive (complex components), Medical (custom implants)
Aerospace (engine components), Automotive (brake parts), Industrial (custom tooling parts)
Aerospace (high-performance parts), Automotive (engine blocks), Industrial (tooling molds)
Aerospace (high-value components), Automotive (brake pads), Energy (valve bodies)

Ceramic Mold Casting Materials
Ceramic mold casting services offers precise replication of complex shapes and features. The process is used for high-performance components requiring exceptional strength and accuracy.
Stainless Steel offers high corrosion resistance and strength at elevated temperatures. It is ideal for casting components such as valves, pumps, and turbine parts, where durability and resistance to oxidation are critical.
These alloys provide excellent high-temperature strength and oxidation resistance. They are commonly used in aerospace, gas turbines, and heat exchangers, where components endure extreme thermal conditions.
Cobalt-based alloys like Stellite offer outstanding wear resistance and high hardness. They are typically used for components exposed to extreme wear, such as cutting tools and wear-resistant surfaces.
Known for their high strength-to-weight ratio and excellent corrosion resistance, titanium alloys are used in aerospace, medical implants, and marine applications, where lightweight and high-performance materials are needed.
Aluminum-based alloys, such as 2024 or 7075, are lightweight and provide good strength and corrosion resistance. They are commonly used in aerospace and automotive components, where reducing weight without compromising strength is essential.
Copper alloys like bronze and brass offer superior thermal and electrical conductivity. They are typically used in electrical connectors, heat exchangers, and marine components.
These high-performance alloys are designed to maintain strength and stability at extreme temperatures. Superalloys are widely used in aerospace turbine blades, requiring high thermal fatigue and creep resistance.
Efficient Solutions for Managing Longer Production Cycles
Ceramic mold casting services involves multiple steps, including mold drying, firing, and shell building, which can extend the overall production time. Each step is crucial for ensuring the mold’s strength and precision. Frigate optimizes these stages by employing advanced techniques and strict process control, reducing delays while maintaining the integrity of the final part. Efficient planning and careful monitoring ensure that production timelines are adhered to, even when complex geometries are required.

Compliance for Ceramic Mold Casting Services
We ensure all ceramic casting processes comply with stringent industry standards and certifications, ensuring precision and reliability. Adhering to specific regulatory frameworks allows the company to provide high-quality, durable, and safe ceramic components for the aerospace, automotive, and medical industries. The team ensures strict oversight, meets safety and environmental requirements and operates with the latest technology to achieve exceptional results.
Compliance for Ceramic Casting Services
Standard Specification for Ceramic Materials for Thermal Insulation.
Quality Management Systems certification ensuring consistent quality in production.
Environmental Management Systems to ensure sustainable practices.
Environmental testing standard for military applications.
Certification ensuring compliance with restrictions on hazardous substances in electronic devices.
Occupational Safety and Health Administration standards for workplace safety.
Certification for quality management systems in the medical device industry.
Aerospace (turbine blades), Automotive (large engine parts), Industrial (heavy machinery components)
Aerospace (engine components), Automotive (structural parts), Oil & Gas (pressure vessels)
Aerospace (precision castings), Automotive (engine blocks), Energy (turbine blades)
Aerospace (high-precision components), Automotive (engine parts), Industrial (pump bodies)
Aerospace (turbine parts), Automotive (brake components), Energy (heat exchangers)
Aerospace (high-performance parts), Automotive (precision gears), Medical (implants)
Aerospace (complex geometry components), Automotive (brake rotors), Medical (surgical instruments)
Aerospace (turbine components), Automotive (engine parts), Industrial (custom parts)
Automotive (mass production engine parts), Aerospace (brackets), Industrial (tooling parts)
Aerospace (high-value components), Automotive (lightweight parts), Energy (precision castings)
Tonnage/Capacity in Ceramic Mold Casting
Tonnage and capacity are critical factors in ceramic mold casting, impacting the size, precision, and production efficiency of components. From mold size to casting weight, and injection pressure, these parameters define the capabilities of casting operations.
Dimensions in Ceramic Mold Casting
Dimensions play a crucial role in ceramic mold casting, affecting the size, shape, and precision of cast components. These parameters determine the feasibility of producing complex and high-performance parts across various industries.
Aerospace (turbine blades), Automotive (engine blocks), Industrial (heavy machinery components)
Aerospace (structural components), Automotive (engine components), Medical (implants)
Aerospace (high-strength components), Automotive (brake pads), Industrial (casting molds)
Aerospace (turbine blades), Automotive (precision gears), Energy (turbine components)
Aerospace (fan blades), Automotive (transmission shafts), Industrial (piping components)
Aerospace (critical components), Automotive (steering systems), Industrial (heat exchangers)
Aerospace (engine housings), Automotive (chassis), Medical (surgical tools)
Aerospace (turbine blade cooling holes), Automotive (engine parts), Industrial (valves)
Aerospace (complex aerospace parts), Automotive (detailed automotive components), Medical (implants)
Aerospace (turbine blades), Automotive (engine parts), Energy (valve bodies)

Tolerance for Ceramic Mold Casting Services
Precision in the overall size and shape of the casting, essential for fit and function.
Variation in wall thickness to ensure structural integrity and consistency.
Surface roughness specified by the average height of surface irregularities (Ra).
Tolerance in the flatness of the part, critical for alignment in assemblies.
Deviation from a perfect 90° angle between surfaces, important for geometric precision.
Deviation from true circular shape, essential for function in rotating or mating parts.
Tolerance for weight variation, depending on part size, material, and application.
Maximum allowable porosity, critical for maintaining mechanical strength and durability.
Deviation from the intended roundness, affecting the fit of rotating components.
Variability in thickness throughout the part to maintain uniform strength distribution.
Shrinkage tolerance during cooling, important for ensuring final dimensions match specifications.
Tolerance for internal and external diameters, critical for tight-fitting components.
Deviation in angular dimensions, particularly for complex geometries in technical applications.
Allowable variance in the tensile strength of the ceramic material, ensuring required performance.
Hardness variation to ensure appropriate wear resistance for specific applications.
Deviation in thermal conductivity, critical for thermal management in specific industries.
Precision control of cavity depths in complex casting geometries.
Max allowable moisture content in the ceramic, important for firing and sintering processes.

Quality Testing Standards for Ceramic Mold Casting Services
Measuring the rate at which heat passes through the ceramic material, essential for thermal management applications.
Testing the material's expansion or contraction with changes in temperature.
Evaluation of a ceramic material's ability to resist crack propagation under stress.
Measuring the ceramic's ability to withstand compressive forces without failure.
Testing for deformation under a constant load over an extended period at high temperatures.
Measurement of the material’s stiffness under bending stress.
Testing the ceramic’s ability to withstand repeated loading cycles without failure.
Measuring the material's ability to absorb energy from an impact without breaking.
Measurement of the ceramic's electrical conductivity, permittivity, and resistivity.
Detecting high-frequency stress waves to monitor crack formation or growth.
Measuring the ability of ceramic material to absorb and dampen vibrational energy.
Evaluating the ceramic's resistance to wear under continuous friction.
Evaluating changes in the material’s microstructure during the sintering process.
Measuring dimensional changes during drying, firing, and cooling to ensure proper final size.
Evaluating the strength of bonds between ceramic layers or between ceramic and other materials.
Quantifying the size and distribution of pores in the ceramic to assess quality and integrity.
Measuring the flow of gases through the ceramic to evaluate its density and pore structure.
Determining the density after sintering to confirm that the part has reached the desired structural properties.
Measuring the material’s resistance to deformation under tensile stress.
Measuring the material’s transparency or light transmission for optical applications.
Testing the amount of moisture absorbed by the ceramic material under controlled conditions.
Inspection Techniques in Ceramic Mold Casting
Value/Range - 0.1 - 5 mm
Aerospace (turbine blades), Automotive (engine blocks), Medical (implants)
Value/Range - 2 - 500 mm
Aerospace (aircraft engine components), Automotive (suspension parts), Industrial (pressure vessels)
Value/Range - 0.1 - 10 mm
Aerospace (turbine blades), Automotive (precision gears), Energy (turbine components)
Value/Range - 0.1 - 5 mm
Aerospace (engine casings), Automotive (brake components), Oil & Gas (drill bits)
Value/Range - 0.1 - 2 mm
Aerospace (turbine blades), Automotive (casting integrity), Medical (surgical tools)
Value/Range - 0.2 - 10 mm
Aerospace (engine parts), Automotive (brake pads), Industrial (valve bodies)
Value/Range - 0.1 - 50 mm
Aerospace (complex geometries), Automotive (precision parts), Medical (implants)
Value/Range - 2 - 500 mm
Aerospace (high-precision components), Automotive (engine parts), Industrial (machinery components)
Value/Range - 50 - 60 HRC
Aerospace (engine components), Automotive (brake pads), Industrial (tooling parts)
Value/Range - 0.1 - 5 µm
Aerospace (turbine blades), Automotive (engine components), Medical (surgical instruments)
Value/Range - 200 - 1500 MPa
Aerospace (structural components), Automotive (engine parts), Industrial (machine components)


Industry Applications of Ceramic Mold Casting
Turbine blades, heat shields, nozzle components, jet engine housings
Cylinder heads, turbocharger parts, exhaust manifolds, engine pistons
Heart valves, orthopedic implants, surgical instruments, dental crowns
Gas turbine components, reactor vessels, steam nozzles, valve seats
Drill rigs, subsea components, downhole tools, pipeline valves
Armor plating, radar housing, gun parts, missile components
Pump casings, valve bodies, manufacturing jigs, industrial seals
Circuit boards, connectors, battery cases, sensor housings
Propellers, marine engine components, ship hull fittings, valve parts
Microwave components, antenna housing, base station parts
Semiconductor molds, wafer supports, process chambers
Food processing machinery, pump components, conveyor parts
Crusher parts, mining drill components, excavator parts
Concrete molds, bridge components, construction machinery parts
Advancing Medical Component Manufacturing with Ceramic Mold Casting
Precision and reliability are critical in medical component manufacturing, especially for complex parts like surgical instruments, implants, and device housings. Traditional casting methods often face difficulties in achieving tight tolerances and intricate designs. Ceramic mold casting addresses these issues by offering exceptional dimensional accuracy, smooth surface finishes, and the ability to create detailed internal geometries. This process ensures that medical components meet strict quality standards, reducing the need for extensive post-processing and delivering high-performance, reliable parts tailored to the demands of the medical field.






Industries We Serve
- Solid Progress
Our Manufacturing Metrics
Frigate brings stability, control, and predictable performance to your sourcing operations through a structured multi-vendor system.
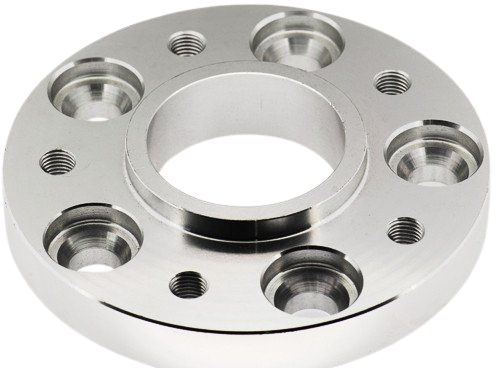
2.8X
Sourcing Cycle Speed
Frigate’s pre-qualified network shortens decision time between RFQ and PO placement.
94%
On-Time Delivery Rate
Structured planning windows and logistics-linked schedules improve project-level delivery reliability.
4X
Multi-Part Consolidation
We enable part family batching across suppliers to reduce fragmentation.
22%
Quality Rejection Rate
Multi-level quality checks and fixed inspection plans lower non-conformities.
30%
Procurement Costs
Optimized supplier negotiations and bulk order strategies reduce your overall sourcing expenses.
20%
Manual Processing Time
Automation of sourcing and supplier management significantly reduces time spent on manual tasks.
Scalable Options for High-Volume Production Runs
Although ceramic mold casting is ideal for producing complex, low-volume parts, scaling up for large production runs can be challenging due to the labor-intensive nature of the process. Frigate addresses this by strategically evaluating the most efficient use of ceramic molds based on part complexity and production volume. Alternative methods, such as die casting or sand casting, may be considered for high-volume needs, ensuring the most cost-effective and timely solution is chosen while maintaining high-quality standards.

Get Clarity with Our Manufacturing Insights
- Real Impact
Words from Clients
See how global OEMs and sourcing heads describe their experience with our scalable execution.
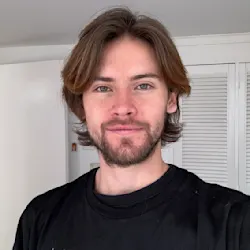
“Quick turnaround and solid quality.”
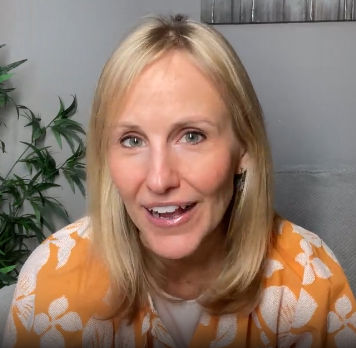
“The instant quote tool saved us time, and the parts were spot-on. Highly recommend Frigate!”
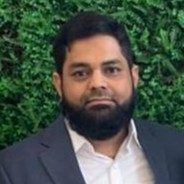
“I would strongly recommend Frigate to anyone who wants to do Rapid Prototyping, and take their ideas to manufacturing. One firm doing all kinds of Product Development!”
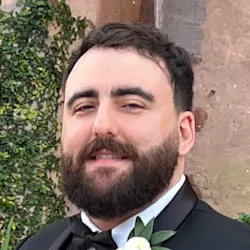
“Great service, fair price, and the parts worked perfectly in our assembly.”
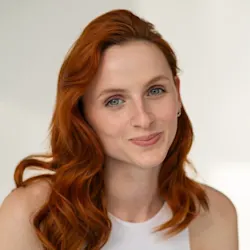
“Top-notch machining and fast shipping. Very satisfied with the results.”
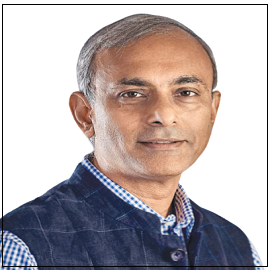
“The next disruption is happening in Prototyping & Manufacturing on-demand and Frigate is leading the way! I personally believe the Frigate's way of IIOT enabled cloud platform with Al.”
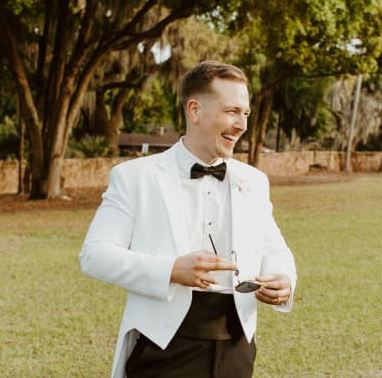
“Frigate delivered high-quality parts at a competitive price. The instant quote tool is a huge plus for us!”

“We appreciate the precision and quality of the machined components in the recent delivery—they meet our specifications perfectly and demonstrate Frigate’s capability for excellent workmanship.”
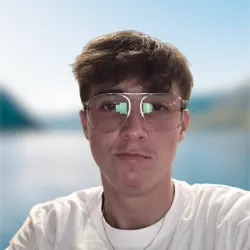
“Flawless execution from quote to delivery.”

“I am absolutely happy to work with supplier like Frigate who were quite proactive & result oriented . Frigate has high willingness team who has strong know how & their passion towards the products & process were absolutely thrilling.”
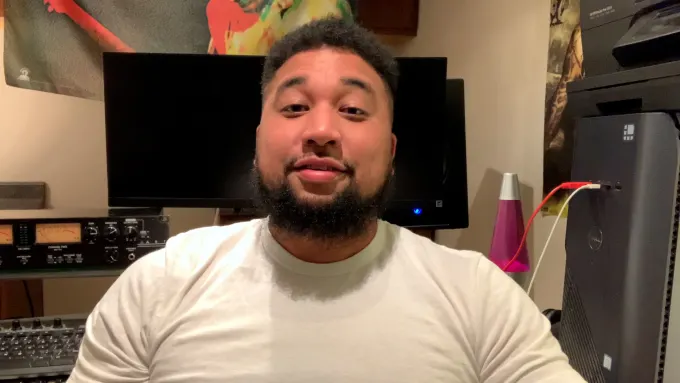
“The precision on these parts is impressive, and they arrived ahead of schedule. Frigate’s process really stands out!”
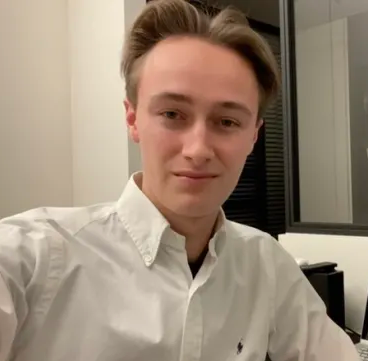
“Parts were exactly as spec’d, and the instant quote made budgeting a breeze.”
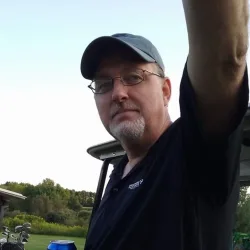
“Good value for the money.”
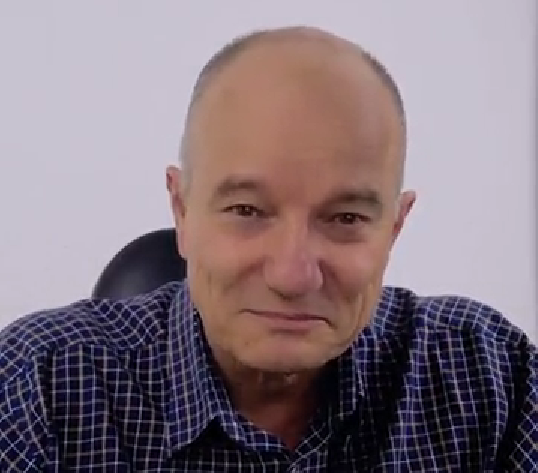
“The finish was perfect, and the team was easy to work with.”

“Working with Frigate has been great. Their proactive, results-driven approach and expertise shine through in every project. It's been a pleasure collaborating with them.”

"We are highly satisfied with the timely delivery and quality of the MIG Welding Cable from Frigate. Their attention to detail, secure packaging, and quick responsiveness stood out. We confidently recommend Frigate Engineering Services Pvt. Ltd. as a reliable manufacturing partner."
Having Doubts? Our FAQ
Check all our Frequently Asked Question
Ceramic molds are designed to withstand extreme temperatures, preventing thermal shock or deformation during the casting of high-temperature alloys and ensuring the structural integrity of parts under severe operating conditions.
The ceramic shell's thickness directly influences mold strength and dimensional accuracy. A thicker shell increases strength, but excessive thickness can lead to challenges in achieving fine detail and precision.
Ceramic mold casting controls the cooling rate to prevent thermal stresses, ensuring uniform cooling, which optimizes material properties like tensile strength and fatigue resistance, especially in critical components such as turbine blades.
Yes, ceramic mold casting can handle high-viscosity alloys like titanium and zirconium by utilizing advanced shell materials and heating techniques that ensure proper flow into complex molds and prevent solidification before complete filling.
Ceramic molds provide a superior surface finish with minimal porosity, reducing the need for extensive post-processing. This allows for tighter tolerances and reduces the need for secondary machining compared to metal molds.
We'd love to Manufacture for you!
Submit the form below and our representative will be in touch shortly.
LOCATIONS
Registered Office
10-A, First Floor, V.V Complex, Prakash Nagar, Thiruverumbur, Trichy-620013, Tamil Nadu, India.
Operations Office
9/1, Poonthottam Nagar, Ramanandha Nagar, Saravanampatti, Coimbatore-641035, Tamil Nadu, India. ㅤ
Other Locations
- Bhilai
- Chennai
- USA
- Germany