- Seamless Profiles
Extruded Pipes, Tubes & Rods
Frigate delivers extruded pipes, tubes, and rods, featuring smooth, uniform finishes straight from the extrusion process. Whether matte, glossy, or textured, our parts meet functional and aesthetic requirements, eliminating extra finishing steps and streamlining your operations.

Our Clients
Trusted by Engineers and Purchasing Leaders
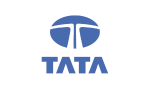
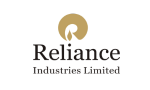


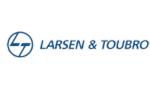
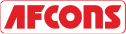


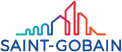

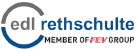

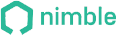
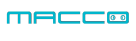









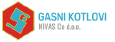
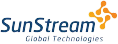

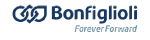


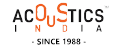
- Versatile Offerings
Our Extruded Pipes, Tubes & Rods Products
Explore our range of high-quality Extruded Pipes, Tubes & Rods today.
- Real Impact
Words from Clients
See how global OEMs and sourcing heads describe their experience with our scalable execution.
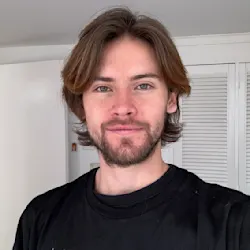
“Quick turnaround and solid quality.”
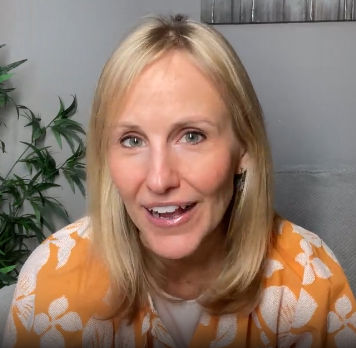
“The instant quote tool saved us time, and the parts were spot-on. Highly recommend Frigate!”
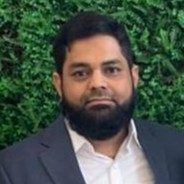
“I would strongly recommend Frigate to anyone who wants to do Rapid Prototyping, and take their ideas to manufacturing. One firm doing all kinds of Product Development!”
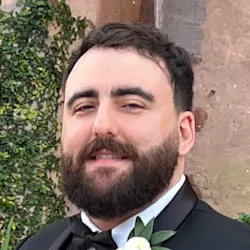
“Great service, fair price, and the parts worked perfectly in our assembly.”
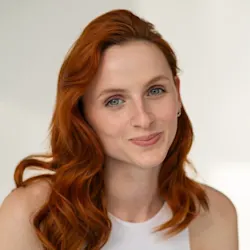
“Top-notch machining and fast shipping. Very satisfied with the results.”
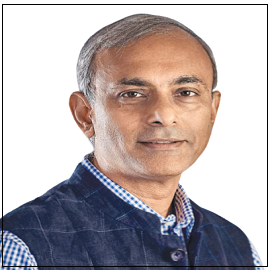
“The next disruption is happening in Prototyping & Manufacturing on-demand and Frigate is leading the way! I personally believe the Frigate's way of IIOT enabled cloud platform with Al.”
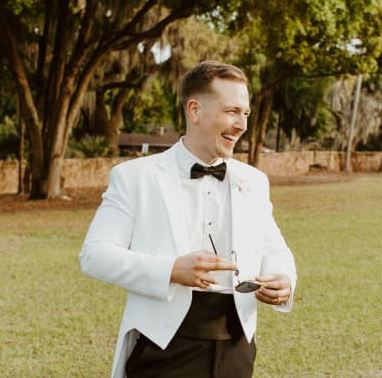
“Frigate delivered high-quality parts at a competitive price. The instant quote tool is a huge plus for us!”

“We appreciate the precision and quality of the machined components in the recent delivery—they meet our specifications perfectly and demonstrate Frigate’s capability for excellent workmanship.”
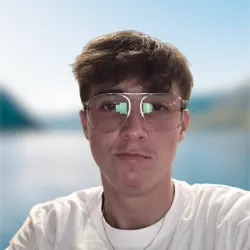
“Flawless execution from quote to delivery.”

“I am absolutely happy to work with supplier like Frigate who were quite proactive & result oriented . Frigate has high willingness team who has strong know how & their passion towards the products & process were absolutely thrilling.”
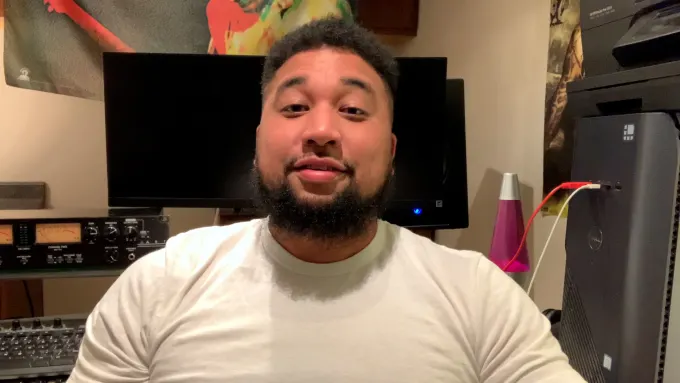
“The precision on these parts is impressive, and they arrived ahead of schedule. Frigate’s process really stands out!”
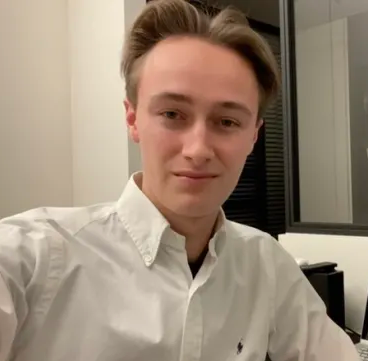
“Parts were exactly as spec’d, and the instant quote made budgeting a breeze.”
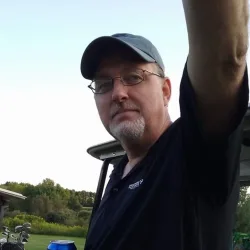
“Good value for the money.”
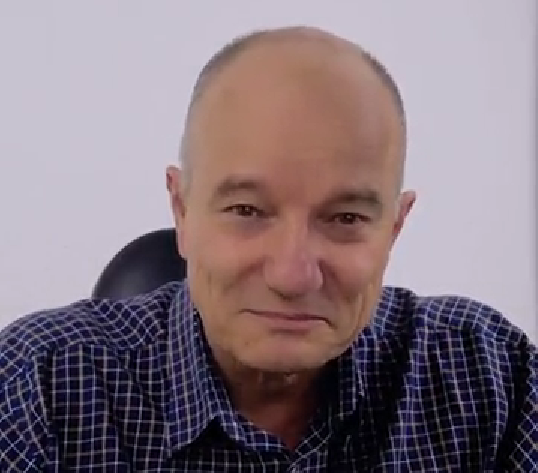
“The finish was perfect, and the team was easy to work with.”

“Working with Frigate has been great. Their proactive, results-driven approach and expertise shine through in every project. It's been a pleasure collaborating with them.”

"We are highly satisfied with the timely delivery and quality of the MIG Welding Cable from Frigate. Their attention to detail, secure packaging, and quick responsiveness stood out. We confidently recommend Frigate Engineering Services Pvt. Ltd. as a reliable manufacturing partner."
We export to 10+ countries
Frigate’s Global Presence
Frigate takes pride in facilitating “Make in India for the globe“. As our global network of Frigaters provides virtually limitless capacity, and through our IoT enabled platform your parts go directly into production. By digitally and technologically enabling “the silent pillars of the economy” MSME and SME manufacturing industries, we are able to tap the huge potential for manufacturing to bring the best results for our clients.

100,000+
Parts Manufactured
250+
Frigaters
2000+
Machines
450+
Materials
25+
Manufacturing Process
Industry Applications
Used in heat exchanger systems for efficient thermal transfer between fluids in HVAC, power plants, and industrial processes.
Serve as conduits for high-pressure fluids in hydraulic machinery, ensuring structural integrity and minimal flow resistance.
Protect and route electrical wiring in industrial, commercial, and residential infrastructure, offering mechanical protection and insulation.
Utilized in fuel delivery systems for precise tolerance, chemical resistance, and long-term durability under thermal cycling.
Transmit compressed air in control systems requiring consistent internal diameters for accurate flow and response times.
Form structural parts in diagnostic and therapeutic equipment, offering biocompatibility and precision in fluid delivery paths.




- Engineered Alloys
Customized Alloys for Optimal Performance
We specialize in creating custom alloys tailored to your unique application needs. Whether you require higher tensile strength, superior electrical conductivity, or enhanced wear resistance, we provide precise solutions to improve performance and ensure reliability. Our advanced alloy formulations offer the flexibility and durability you need for demanding environments.
- Achieve tensile strengths up to 700 MPa for high-stress applications.
- Customize electrical conductivity from 60% to 100% IACS for electrical components.
- Improve wear resistance by up to 30% over standard materials.
- Enhance corrosion resistance for use in harsh, high-temperature environments.
- Tailor chemical composition for specific industry needs, such as aerospace and automotive.
The maximum tolerance for dimensional accuracy in extrusions depends on the material and size of the product. Typically, tolerances of ±0.1mm are achievable for small diameters, while larger extrusions may have tolerances up to ±0.5mm. Precision can be further enhanced with specialized processes such as multi-stage extrusion or high-precision tooling.
The extrusion process significantly influences material properties. For example, the high-pressure environment in extrusion can increase tensile strength by aligning the material's grain structure. Additionally, the cooling rate after extrusion can affect hardness, with faster cooling generally resulting in a harder product. Adjusting the alloy composition and heat treatment processes can further optimize these properties.
Wall thickness plays a crucial role in the extrusion process, as thinner walls are more challenging to extrude consistently and may result in defects such as warping or surface cracks. However, precise control over the extrusion speed and cooling rates can help maintain the integrity of thinner-walled products. In applications requiring high strength, thicker walls may be necessary to ensure structural reliability under stress.
Materials such as stainless steel, titanium alloys, and high-temperature alloys like Inconel or Hastelloy are often used for high-temperature applications. These materials offer excellent thermal stability and resistance to oxidation, ensuring the extruded components retain their strength and dimensional stability even in environments exceeding 500°C.
Extrusion speed has a direct impact on both the surface finish and the internal consistency of the product. Faster extrusion speeds can result in uneven cooling, leading to surface imperfections or internal voids. Slower extrusion rates allow for more controlled cooling, improving the surface finish and ensuring the material is homogenous throughout, reducing the risk of defects like porosity or inclusions.
We'd love to Manufacture for you!
Submit the form below and our representative will be in touch shortly.
LOCATIONS
Registered Office
10-A, First Floor, V.V Complex, Prakash Nagar, Thiruverumbur, Trichy-620013, Tamil Nadu, India.
Operations Office
9/1, Poonthottam Nagar, Ramanandha Nagar, Saravanampatti, Coimbatore-641035, Tamil Nadu, India. ㅤ
Other Locations
- Bhilai
- Chennai
- USA
- Germany