Are precision, speed, and cost-efficiency achievable simultaneously in forging? This question resonates with industries facing the challenge of balancing multiple demands precision in component design, speed in production, and cost-effectiveness. Industries like aerospace and automotive require highly complex forged components, but traditional forging methods often fail to ensure that these components meet high-scale standards. Problems like scrap, extended production cycles, and high tooling costs often delay production and reduce profitability.
Forging simulation solves these issues by creating virtual models of the forging process. Simulation allows manufacturers to test designs digitally, predict material behavior, and optimize the forging process before investing in physical production. This leads to fewer defects, reduced time-to-market, and improved cost-effectiveness.
Challenges Impacting the Efficiency of Advanced Forging
Forging is crucial for making strong, durable parts. However, as materials and designs become more complex, manufacturers face challenges. Issues like unpredictable material flow, high tooling costs, and design limitations can slow production and lead to defects. This section explores the key challenges in advanced forging and how overcoming them can improve efficiency and quality.
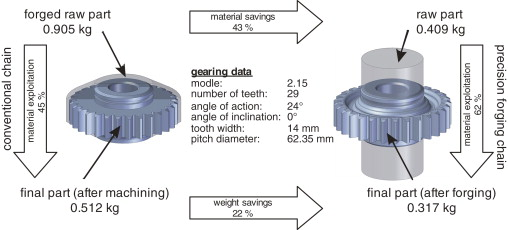
Lack of Predictability in Material Flow
In forging, the material flow must be controlled precisely to ensure it fills the die properly and retains the desired shape. Any misstep in material flow can cause defects such as voids or cracks, compromising the component’s strength and functionality.
Predicting the flow of material through the die becomes even more difficult in complex shapes, especially when forging high-strength alloys or intricate geometries. An incorrect prediction can result in waste, rework, or scrap, increasing production costs.
Forging simulation overcomes this challenge by simulating how the material behaves under extreme pressure and temperature conditions. By analyzing how materials flow and fill the die, manufacturers can identify potential areas of weakness, adjust die designs accordingly, and ensure that the material flows evenly and without defects.
High Costs in Tool Design
Forging dies is one of the most significant costs. They must be designed and manufactured to withstand extreme pressures, temperatures, and forces. A miscalculated die design can result in defects, inefficiency, or premature die failure, requiring costly rework or replacement. Each die iteration often involves months of design and testing, contributing to long lead times and increased expenses.
Simulation helps by allowing manufacturers to test die designs virtually before physical production. By simulating material deformation and die stress, manufacturers can optimize die-shapes, improve wear resistance, and reduce the number of iterations needed, saving significant time and cost.
Difficulty in Adopting Complex Materials
Complex materials, such as high-temperature alloys, titanium, and advanced steels, are increasingly used in industries like aerospace and energy. These materials exhibit unique behaviors during forging, including differences in thermal conductivity, flow characteristics, and deformation under pressure. Understanding and predicting how these materials behave is difficult without trial-and-error testing.
Forging simulation is crucial here. By using precise thermomechanical modeling, manufacturers can predict how these complex materials behave under different conditions. This insight allows manufacturers to optimize their forging processes, avoid cracking or excessive wear, and ensure that the final component meets performance and safety standards.
Balancing Speed with Quality
Manufacturers often sacrifice quality for speed as market pressures demand faster production cycles. This manifests as potential defects like incomplete fill or overheating in forging, leading to dimensional inaccuracies, weak points, or defects.
Simulation allows manufacturers to strike a balance between speed and quality. By simulating the entire forging process—considering variables like material behavior, die design, and heat distribution—manufacturers can fine-tune the speed of the process. This ensures that components are produced faster without compromising the integrity and quality of the final part.
Environmental and Sustainability Concerns
The forging process is energy-intensive and typically generates significant waste, a growing concern in today’s eco-conscious market. Many manufacturers are pressured to reduce energy consumption, minimize waste, and lower their environmental impact.
Simulation provides the tools to design processes that minimize waste and energy use. Manufacturers can reduce energy consumption and scrap rates by accurately predicting the required material sizes, die designs, and heating needs. Optimizing material usage and predicting how much material is required also helps to minimize waste, contributing to more sustainable operations.
How Forging Simulation Enhances Advanced Forging Techniques
Advanced forging techniques aim for precision, efficiency, and high material performance. However, achieving these goals without effective tools is tough. Forging simulation helps by predicting and optimizing the forging process before production starts. This section will show how forging simulation improves material flow, die design, defect detection, and overall process efficiency.
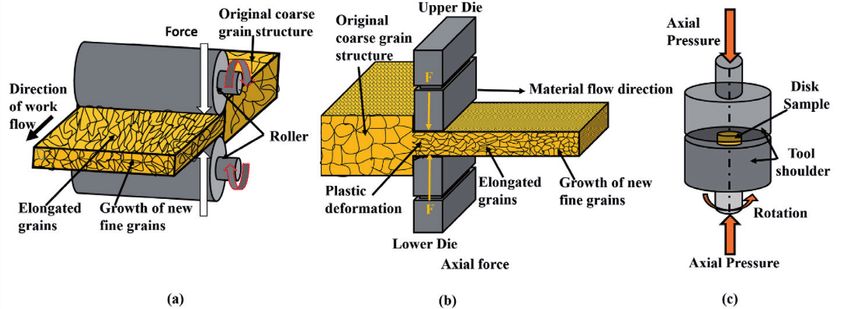
Predictive Analysis for Material Behavior
Simulation helps manufacturers predict how the material will behave under forging conditions. Using tools like Finite Element Analysis (FEA), simulation can model the deformation, material flow, and heat distribution across the workpiece. This allows manufacturers to identify areas that may experience too much stress, where cracks could form, or where material flow might be uneven.
With accurate predictions of material behavior, manufacturers can adjust the parameters such as temperature, pressure, or die design before the actual forging process begins. This ensures the final forged component is defects-free and meets the necessary specifications.
Optimized Die Design
Die design is a critical aspect of forging, and optimizing the design is essential to ensure efficiency and durability. Simulation tools allow manufacturers to analyze the stresses and strains on dies during forging. The virtual models can identify areas where the die may experience excessive wear, thermal fatigue, or deformation.
This allows manufacturers to modify the die design before production to optimize die life, improve material flow, and prevent premature die failure. Simulation significantly cuts tooling costs by reducing the number of physical die prototypes required.
Enhanced Defect Detection
Simulation allows for early identification of potential defects that could arise during the forging process. It can predict issues like –
- Cavities caused by incomplete filling of the die.
- Hot tears or cracks due to uneven material cooling or stress during forging.
- Distortion is caused by uneven force distribution.
By analyzing the simulation results, manufacturers can identify defects before starting the actual forging process, leading to a reduction in scrap rates, rework, and costly production delays.
Improved Process Efficiency
Simulation allows manufacturers to optimize the entire forging process by adjusting parameters such as material temperature, tool force, and billet positioning. These optimizations can significantly enhance production efficiency by –
- Reducing cycle times.
- Ensuring that material is used efficiently.
- Reducing energy consumption.
Simulation-driven improvements can lead to up to 30% reductions in cycle time and material usage, resulting in higher throughput and better overall profitability.
Sustainability Gains
Simulation aids manufacturers in reducing material waste and energy consumption, directly contributing to sustainability. By predicting the exact amount of material required for each part and optimizing energy usage in the heating and cooling stages, manufacturers can cut down on scrap and reduce the carbon footprint of their operations.
Simulation has led some manufacturers to report a reduction in material waste by up to 20%, contributing to profitability and environmentally friendly operations.
How are Emerging Technologies Shaping Forging Simulation?
New technologies are rapidly evolving forging simulation. Tools like Finite Element Analysis (FEA), AI, and digital twins enhance simulation capabilities and improve accuracy, efficiency, and scalability. In this section, we’ll examine how these technologies drive forging simulation and improve product quality, reduce costs, and streamline operations.
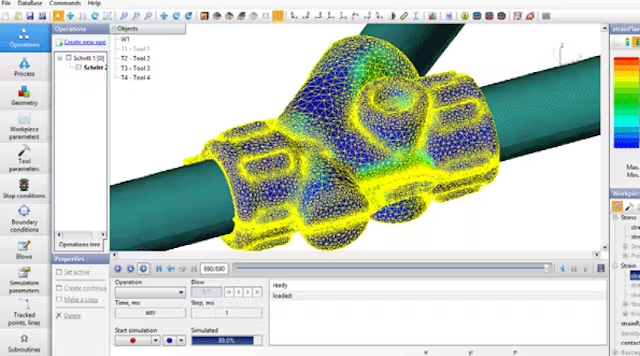
Finite Element Analysis (FEA)
FEA is a computational tool that breaks down complex physical processes into smaller, manageable elements. Forging simulates how the material behaves under stress, strain, and temperature. This analysis gives manufacturers precise data on deformation, flow, and thermal profiles, helping fine-tune the forging process.
Digital Twin Integration
A digital twin creates a virtual replica of the entire forging operation. This allows manufacturers to monitor real-time production data, adjust processes dynamically, and predict equipment failures. By linking simulation data with real-time sensor data, manufacturers can make informed decisions and continuously optimize production.
Artificial Intelligence and Machine Learning
AI and machine learning enable manufacturers to predict and optimize the forging process by analyzing vast data. These technologies can identify patterns that might not be immediately obvious to engineers, continuously improving the simulation’s accuracy and ensuring even better results as more data is collected.
High-Performance Computing (HPC)
The complexity of forging simulations, particularly when dealing with large or highly detailed parts, requires significant computational power. High-performance computing accelerates the simulation process, enabling faster analysis and more detailed predictions. HPC is especially valuable for industries requiring quick design cycles and rapid production adjustments.
Frigate’s Expertise in Revolutionizing Forging Processes
Frigate is at the forefront of leveraging forging simulation and advanced forging techniques. Frigate can model and optimize the forging process for various industries, including aerospace, automotive, and energy, through its cutting-edge simulation capabilities.
Frigate utilizes FEA, digital twins, and AI-driven models to optimize material flow, die design, and production cycles, ensuring maximum efficiency and minimum waste. Additionally, Frigate’s commitment to sustainability is evident in its focus on reducing energy consumption and waste, all while producing high-quality, defect-free forged components.
Conclusion
Integrating forging simulation and advanced techniques transforms the manufacturing process, enabling companies to meet higher quality standards while reducing costs and time-to-market. As industries demand greater precision, speed, and sustainability, forging simulation provides the tools to stay ahead.
Frigate’s expertise in forging simulation ensures that each component is produced with optimal material flow, precise die design, and reduced waste. Contact Frigate today to experience the benefits of advanced forging techniques and simulation-driven precision in your manufacturing operations.