Radial forging, a specialized metalworking process, has emerged in the manufacturing of complex components. From aerospace to automotive industries, the demand for intricate parts with high precision and durability continues to grow. However, achieving such complexity while maintaining tight tolerances and structural integrity poses significant challenges.
Traditional forging methods often fall short when it comes to producing components with intricate geometries, thin walls, or asymmetrical designs. This is where radial forging steps in offering unparalleled precision, efficiency, and versatility. For manufacturers striving to meet the demands of modern engineering, understanding the advantages of radial forging is not just beneficial; it’s essential.
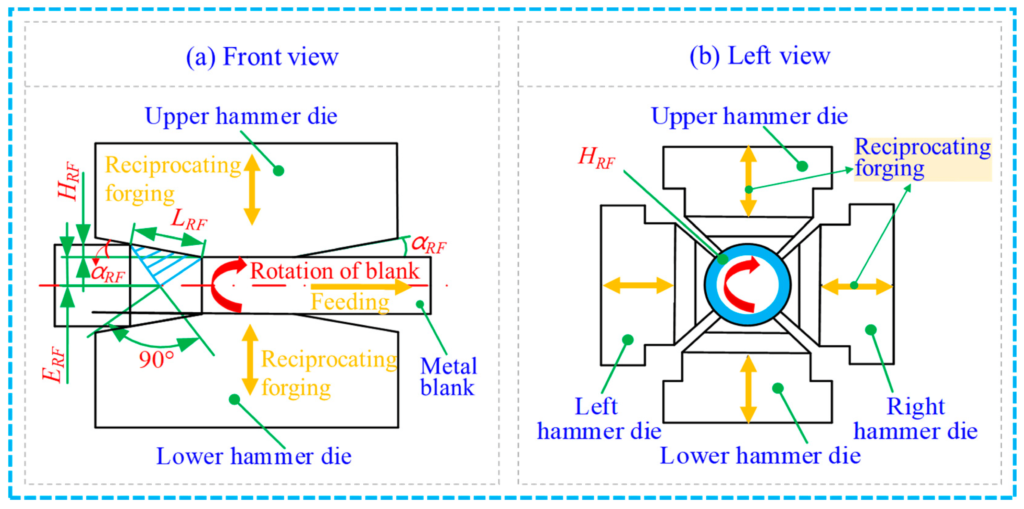
The Unique Advantages of Radial Forging
Radial forging stands out due to its ability to deliver exceptional dimensional accuracy, material efficiency, and adaptability to complex geometries. Let’s explore why this process is ideal for manufacturing intricate parts.
Precision in Every Stroke
Radial forging employs multiple synchronized hammers that strike the workpiece radially, ensuring uniform deformation and precise control over dimensions. This method achieves tolerances as tight as ±0.001 inches, making it suitable for applications where even minor deviations can compromise performance.
For example, in the production of turbine shafts for jet engines, radial forging ensures that the internal bore and external surfaces align perfectly. Such precision reduces the need for secondary machining, saving both time and costs. According to industry data, manufacturers adopting radial forging have reported a 25% reduction in post-forging machining requirements.
Material Efficiency and Structural Integrity
One of the standout features of radial forging is its ability to optimize material usage. Unlike traditional methods that generate significant waste, it minimizes excess material by precisely shaping the workpiece. This is particularly advantageous when working with expensive alloys like titanium or nickel-based superalloys.
Moreover, the controlled deformation process enhances the mechanical properties of the material. Grain refinement during radial forging improves strength and fatigue resistance, which is critical for components operating under extreme conditions. Studies show that parts forged using radial techniques exhibit up to 30% higher fatigue life compared to conventionally forged counterparts.
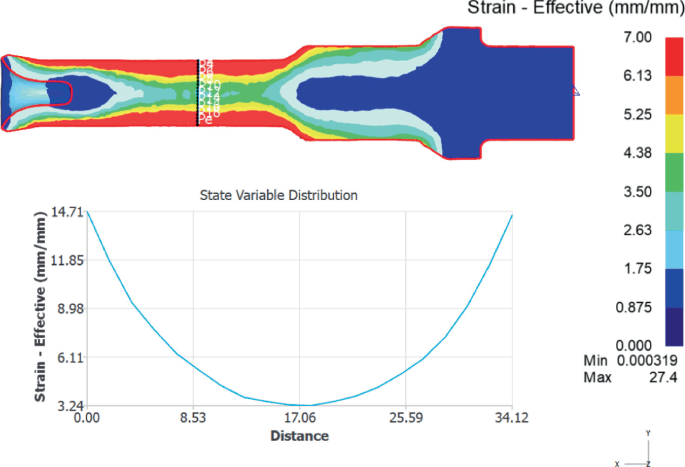
Versatility Across Complex Geometries
Radial forging excels in producing parts with complex geometries, including stepped shafts, hollow tubes, and asymmetrical profiles. The process accommodates varying cross-sections along the length of the component, enabling the creation of intricate designs in a single operation.
For instance, in the medical device industry, radial forging is used to manufacture surgical instruments with tapered handles and fine tips. These components require not only precision but also smooth surface finishes to meet stringent hygiene standards. Radial forging achieves these specifications consistently, ensuring compliance with regulatory requirements.
Addressing Key Challenges in Complex Part Manufacturing
While the benefits of radial forging are clear, it’s important to address the pain points manufacturers face when producing complex parts.
Overcoming Tooling Limitations
Traditional forging methods often struggle with tool wear, especially when working with hard materials or intricate shapes. Radial forging mitigates this issue through advanced tooling technologies. Techniques like Physical Vapor Deposition (PVD) coatings extend die life by up to 40%, reducing downtime and maintenance costs.
Additionally, real-time monitoring systems integrated into radial forging equipment detect tool wear patterns early. Laser scanning and thermal imaging ensure that tools remain in optimal condition throughout the production cycle.
Managing Material Variability
Inconsistent raw material properties can lead to variations in forgeability and final dimensions. Radial forging addresses this challenge by leveraging predictive analytics and digital twins. These technologies simulate material behavior under different conditions, allowing engineers to adjust parameters dynamically and maintain consistent tolerances.
For example, a manufacturer producing hydraulic cylinders used digital twin simulations to predict material flow during radial forging. This approach reduced prototyping time by 25% and ensured dimensional accuracy across all batches.
Scaling Production Without Compromising Quality
As production scales, maintaining tight tolerances becomes increasingly difficult. Radial forging solves this problem through closed-loop control systems. Embedded sensors monitor critical parameters like pressure distribution and temperature gradients, enabling mid-process adjustments. This ensures batch-to-batch consistency, even in high-volume production environments.
Industry-Specific Applications of Radial Forging
The versatility of radial forging makes it indispensable across various industries. Let’s examine how it meets the unique demands of each sector.
Aerospace
In aerospace, where safety and performance are paramount, radial forging produces components like landing gear struts and engine shafts with exceptional precision. The process ensures tolerances within ±0.0005 inches, meeting the rigorous standards of regulatory bodies like the FAA.
Automotive
Automotive manufacturers rely on radial forging for producing drivetrain components such as axles and gears. The process delivers repeatability and dimensional accuracy, ensuring seamless integration into automated assembly lines.
Energy
In the energy sector, radial forging is used to manufacture components for wind turbines and nuclear reactors. The ability to produce large, hollow parts with uniform wall thickness enhances energy efficiency and operational reliability.
Business Impact of Radial Forging
Adopting radial forging translates into tangible business benefits, from cost savings to enhanced market competitiveness.
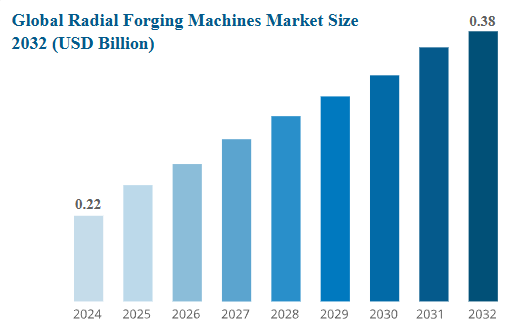
Revenue Growth
Manufacturers achieving tight tolerances with radial forging gain access to premium markets. For example, a supplier producing medical implants with tolerances of ±0.0002 inches secured a 30% increase in market share.
Cost Reduction
By minimizing material waste and eliminating secondary machining, radial forging reduces production costs significantly. One automotive supplier reported annual savings of $2 million after switching to radial forging.
Supply Chain Optimization
Consistent tolerances simplify downstream processes like assembly and quality checks, ensuring timely deliveries and strengthening client relationships.
How Radial Forging Excellence is Delivered by Frigate
At Frigate, we take pride in delivering components that meet the most stringent requirements for precision, durability, and performance. Our expertise in radial forging is built on decades of experience, deep material knowledge, and a relentless focus on quality. Here’s how we ensure excellence in every project –
Advanced Material Expertise
Our team specializes in working with high-performance materials such as titanium, nickel-based superalloys, and high-strength steels, which are often challenging to forge due to their unique properties. By leveraging metallurgical techniques like grain structure analysis and thermal deformation modeling, we ensure optimal material behavior during the forging process.
For instance, in aerospace applications, we engineer specialized alloys that maintain dimensional stability under extreme temperatures and mechanical stresses. This ensures tolerances as tight as ±0.0005 inches, even for components operating in demanding environments. Our ability to address material complexities at the microstructural level guarantees consistent performance and long-term reliability.
Process Optimization Through Experience
We understand that achieving tight tolerances requires more than just advanced machinery it demands a deep understanding of the forging process. Our engineers meticulously optimize every step, from die design to post-forging treatments, ensuring uniform deformation and dimensional accuracy.
Key highlights include –
- Die Design Expertise – Our dies are engineered to minimize material displacement errors, ensuring consistent results across high-volume production runs.
- Post-Forging Treatments – Techniques like controlled cooling and stress-relief annealing enhance dimensional stability, reducing the risk of thermal contraction or warping.
- Tool Maintenance Protocols – Regular inspections and refurbishments of forging tools prevent wear-related deviations, maintaining tolerances within ±0.001 inches.
These measures collectively ensure that our components meet the tightest tolerances while minimizing waste and rework.
Collaborative Engineering for Customized Solutions
We believe that the best outcomes result from close collaboration with our clients. By involving our engineering team early in the design phase, we help optimize component designs for manufacturability and performance.
- Design for Manufacturability (DFM) – We analyze client designs to identify potential challenges and suggest modifications that improve tolerance control without compromising functionality.
- Prototyping and Validation – Before full-scale production, we create prototypes to validate designs under real-world conditions. This ensures that each component meets performance expectations and tolerance requirements.
This collaborative approach not only reduces development time but also minimizes costly redesigns, making it ideal for industries like medical devices and automotive manufacturing where precision is critical.
Rigorous Quality Assurance
Quality is non-negotiable at Frigate. Our multi-layered inspection protocols ensure that every component meets the highest standards of dimensional accuracy and structural integrity.
- Precision Measurement Tools – We use tools like Coordinate Measuring Machines (CMMs) to verify dimensions at sub-micron levels, ensuring compliance with even the tightest tolerances.
- Non-Destructive Testing (NDT) – Techniques like ultrasonic testing and magnetic particle inspection detect internal defects without damaging the component, ensuring reliability in critical applications.
- Statistical Process Control (SPC) – Real-time data analysis monitors production consistency, enabling immediate corrective actions when deviations occur.
This meticulous attention to detail ensures tolerances as tight as ±0.0005 inches, reducing costly rework and strengthening client confidence in our solutions.
Conclusion
Radial forging represents the pinnacle of precision and efficiency in complex part manufacturing. Its ability to deliver tight tolerances, optimize material usage, and accommodate intricate geometries makes it an invaluable asset for industries demanding high-performance components. By investing in these technologies, manufacturers can overcome traditional limitations, reduce costs, and unlock new opportunities in competitive markets.
At Frigate, we specialize in delivering cutting-edge solutions customized to meet the most stringent tolerance requirements. With our metallurgical expertise, real-time process monitoring, and collaborative engineering approach, we ensure your components achieve unmatched precision and performance. Contact us now to learn how our radial forging expertise can transform your business.