The world of metalworking offers a vast array of options for creating the components you need. Casting, machining, and 3D printing are all valuable techniques, each with its own strengths and limitations. But when it comes to forging a time-tested and versatile process, Frigate stands out as the ideal partner for your next forging project.
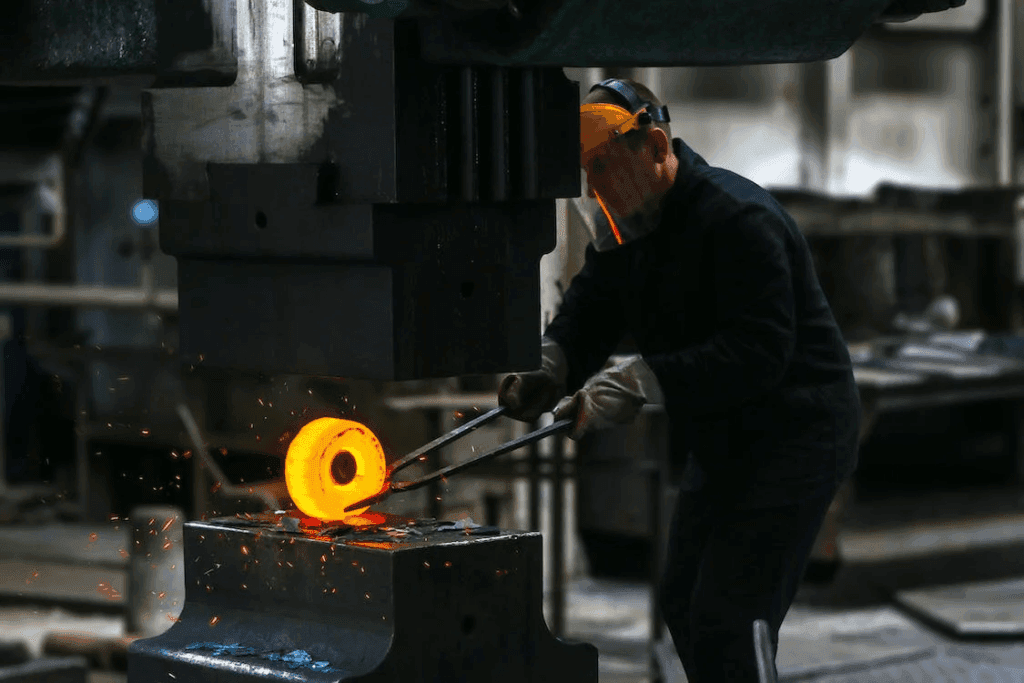
Forging involves shaping metal through compressive force. This method offers several advantages over other techniques, making it perfect for a wide range of applications. For instance, forging excels at producing high-strength components due to the refined grain structure created during the forming process. This translates to parts that can withstand significant loads and stresses, making them ideal for demanding applications in industries like aerospace, automotive, and construction.
Furthermore, forging allows for a remarkable degree of design flexibility. Unlike casting, which is limited by the flow of molten metal, or 3D printing, which can struggle with creating certain features, forging can create intricate shapes and complex geometries – all while maintaining exceptional strength. This design freedom opens a world of possibilities for engineers and designers, allowing them to bring their most innovative concepts to life.
Frigate – Your Complete Solution for High-Precision Forged Metal Components
At Frigate, we aren’t just a metalworking company; we’re your one-stop shop for everything related to precision-forged components. We possess the expertise, resources, and passion to transform your vision into reality. Whether you need a single, intricate prototype for a groundbreaking invention or require high-volume production of mission-critical parts for your established product line, Frigate has the capabilities to handle it all.
Our team of experienced engineers and specialists will collaborate closely with you throughout every stage of the process. From initial design consultation to material selection, tooling development, and final production, we ensure clear communication and meticulous attention to detail. This collaborative approach guarantees that your unique design translates perfectly into a flawless forged component that meets your exact specifications and exceeds your expectations.
Here are just a few reasons why Frigate should be your trusted partner for your next forging project-
- Design Flexibility- Forging allows for a remarkable degree of design flexibility. Unlike other methods limited by material flow, forging can create intricate shapes and complex geometries – all while maintaining exceptional strength. Our team of engineers will work closely with you to ensure your design translates perfectly into a forged component.
- High-Precision Results- At Frigate, precision is paramount. We utilize state-of-the-art equipment and a skilled workforce to deliver consistently high-precision forged components. This translates to parts that meet your exact specifications, reducing the need for post-processing and ensuring a seamless assembly process.
- Cost-Effective Solutions- While forging may seem like a complex process, it can often be a more cost-effective solution in the long run. Forged components boast superior strength and durability, leading to less frequent replacements and lower maintenance costs. Additionally, Frigate’s efficient production processes help us offer competitive pricing.
- Industry Expertise- Our team at Frigate has extensive experience working across various industries. We understand the unique challenges and requirements of each sector, allowing us to tailor our forging solutions to your specific needs. Whether you’re in the automotive, aerospace, or any other industry that relies on high-performance metal components, we have the expertise to deliver exceptional results.
- Rapid Prototyping- Need a prototype quickly to validate your design? Frigate excels in rapid prototyping using the forging process. This allows you to test functionality and form before committing to a full production run, saving you valuable time and resources.
- High-Volume Production Runs- Frigate is equally adept at handling large-scale production runs. Our facilities are equipped to efficiently manufacture a high volume of forged components while maintaining consistent quality and meeting tight deadlines.
The Frigate Advantage- Beyond the Basics
Our commitment to excellence goes beyond the core benefits of forging. Here’s what truly sets Frigate apart-
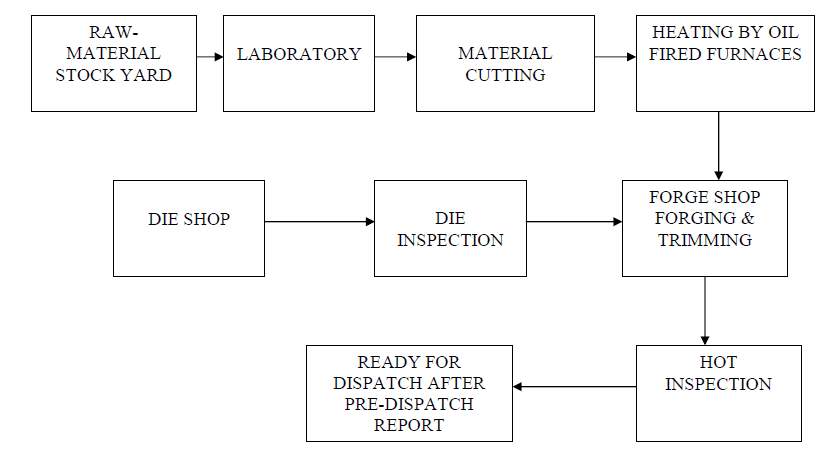
- Unparalleled Quality Control- At Frigate, quality is not a compromise; it’s our priority. We have a rigorous quality control process in place, ensuring every forged component meets the strictest standards. This commitment to quality gives you peace of mind, knowing you’re receiving parts that are built to last.
- Reduced Lead Times- In today’s fast-paced world, time is of the essence. We understand the importance of getting your forging project completed on schedule. Frigate works diligently to streamline processes and optimize production, resulting in reduced lead times for your forging needs.
- Exceptional Customer Service- We believe in building strong partnerships with our clients. Our dedicated team is here to provide exceptional customer service throughout the entire forging process. From initial consultation to final delivery, we’ll be there to answer your questions, address your concerns, and ensure your complete satisfaction.
Forge Your Path to Success with Frigate
If you’re looking for a reliable partner to deliver high-quality, precision-forged metal components, look no further than Frigate. We offer a winning combination of design flexibility, cost-effective solutions, industry expertise, and exceptional customer service.
Beyond forging, we see ourselves as an extension of your team. Our collaborative approach ensures clear communication and a deep understanding of your forging project goals. We’ll work closely with you to identify the optimal forging process for your specific needs, considering factors like material selection, complexity, and production volume. This ensures you receive not just a perfectly forged component but a solution that maximizes efficiency and minimizes overall forging project costs.
Contact Frigate today to discuss your forging project needs and learn how we can help you achieve success in your next forging project. Let’s forge a path to a brighter future together!