Custom Hydroforming Services
Frigate provides precise Custom Hydroforming with tight tolerances for complex metal shapes. Our process ensures uniform wall thickness and high strength across diverse geometries.
Get Your Quote Now
- Instant Quotation
- On-Time Delivery
- Affordable Cost
Precision Custom Hydroforming Services
Frigate’s Custom Hydroforming Services craft complex, high-strength metal forms using high-pressure hydraulic fluids. This process minimizes welding, achieving structural integrity and consistent quality across large volumes. Hydroforming delivers uniform wall thickness and supports intricate geometries, ideal for aerospace, automotive, and industrial applications. Materials like aluminum, stainless steel, titanium, etc., offer durability and corrosion resistance, with precise tolerances reducing the need for additional finishing.
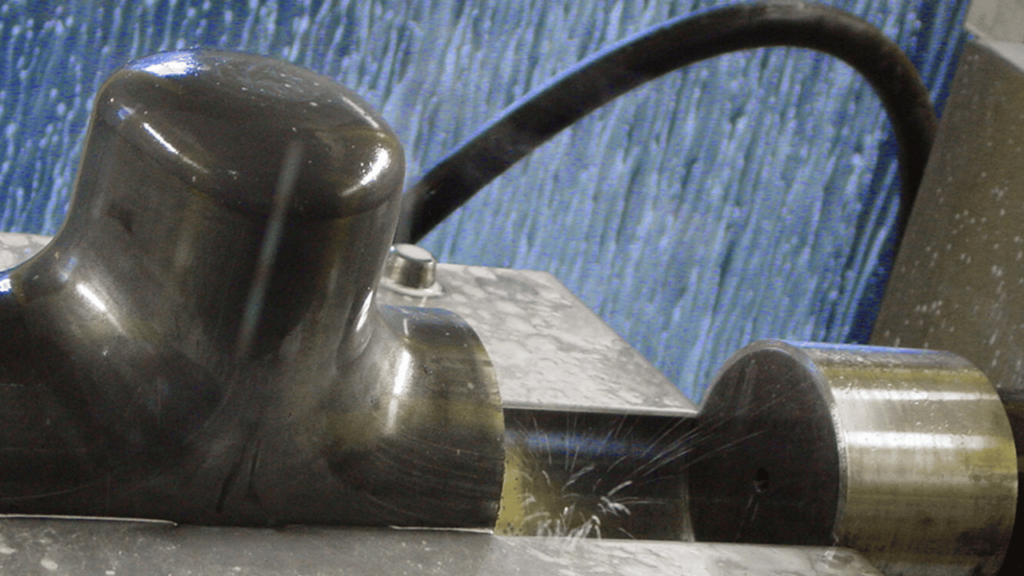
Streamlining the Creation of Complex Geometries
High-pressure hydroforming shapes complex parts in one step, preserving design precision and integrity without additional processes.
Frigate’s hydroforming supports deep draws, which is essential for producing enhanced depth components while retaining material strength.
Hydroforming reduces or eliminates the need for welding by forming shapes directly, resulting in cleaner, structurally stronger parts.
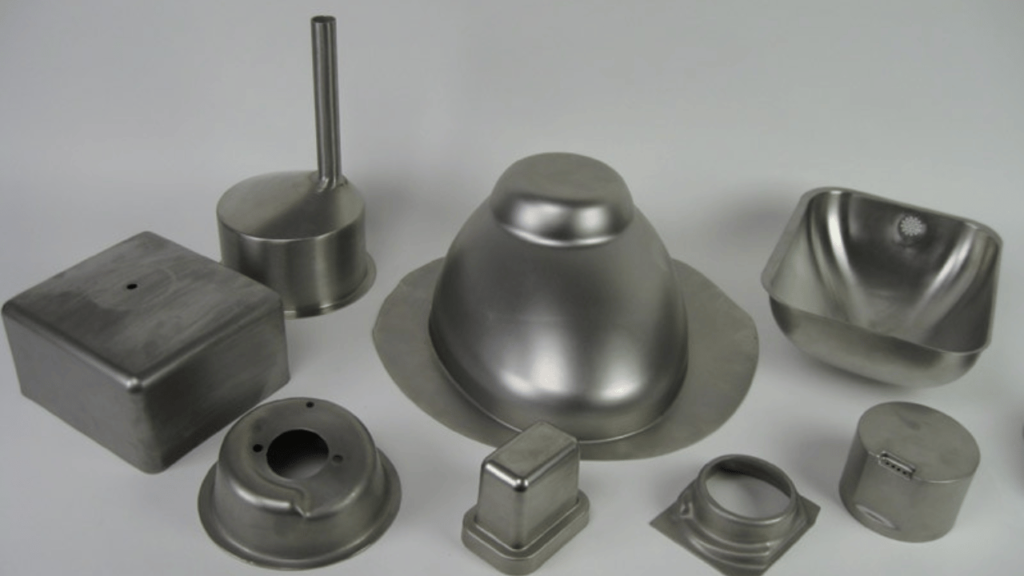
Ensuring Consistent Wall Thickness and Tolerances
Advanced pressure controls ensure even thickness throughout each component, which is essential for durability and consistent performance.
Frigate’s hydroforming maintains tight tolerances across all parts, reducing the need for further machining and enhancing part uniformity.
Consistent wall thickness and tight tolerances help minimize secondary operations, streamlining production and ensuring higher-quality parts.
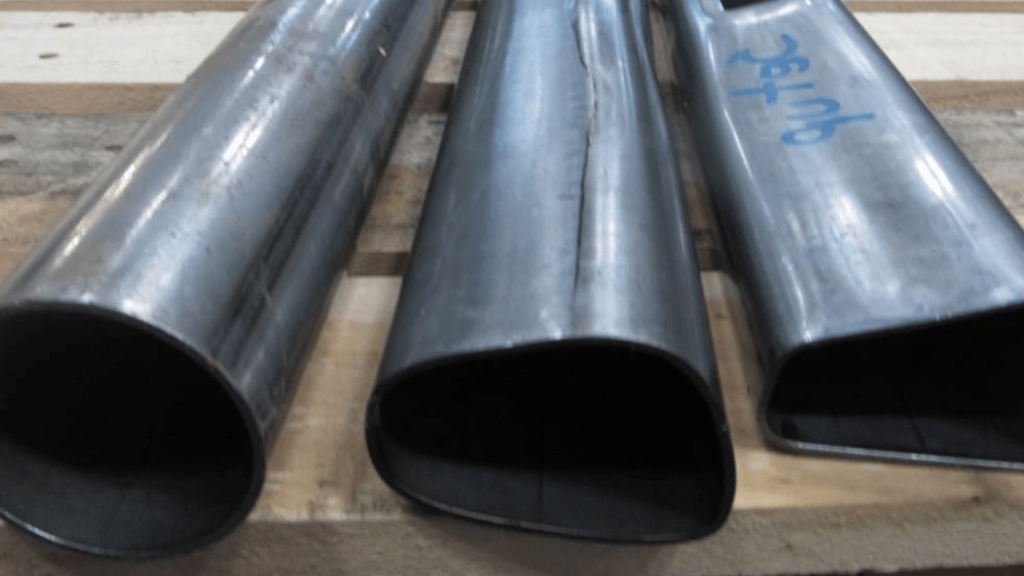
Maximizing Material Versatility for Diverse Applications
Frigate’s hydroforming accommodates metals like titanium, stainless steel, and aluminum, meeting diverse industry requirements.
This service offers materials with specific properties ideal for sectors needing durability, corrosion resistance, or lightweight strength.
The versatility of materials supports compliance with stringent standards in aerospace, medical, and automotive applications.
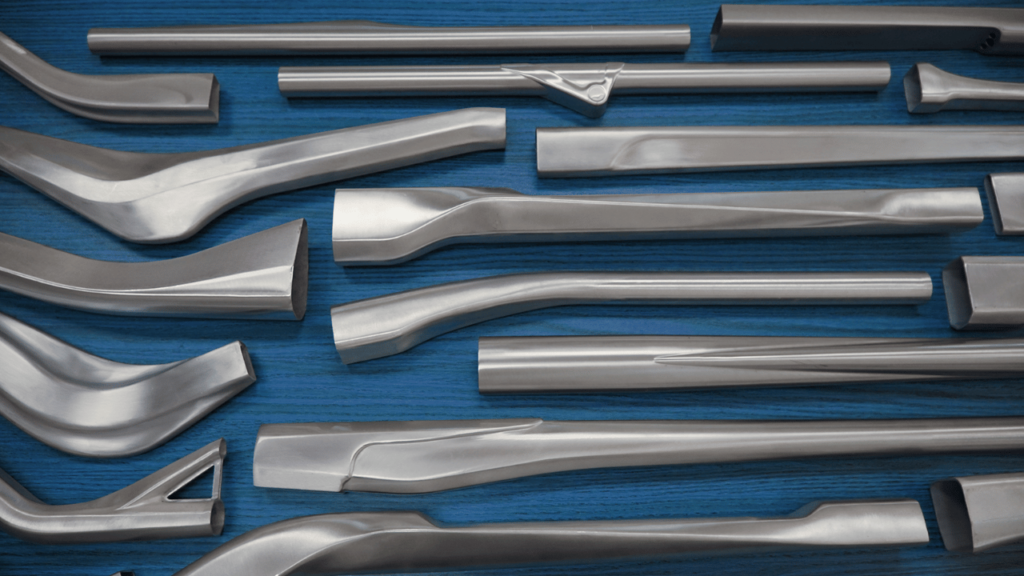
Custom Hydroforming Materials
Custom hydroforming is a precision manufacturing process using high-pressure hydraulic fluid. This method shapes metals into complex geometries with uniform thickness and accuracy.
It is lightweight and offers excellent corrosion resistance. It is ideal for applications requiring high strength-to-weight ratios. Frigate utilizes various aluminum grades, including 6061 and 5052, which are known for their good formability and weldability.
Stainless steel offers superior strength and resistance to corrosion. Common grades used in hydroforming include 304 and 316. These materials are suitable for applications in harsh environments, such as automotive and industrial components.
Titanium alloys are recognized for their high strength and low weight, making them ideal for aerospace and medical applications. Frigate works with various titanium grades, including Ti-6Al-4V, which is known for its excellent mechanical properties and corrosion resistance.
Copper alloys, including brass and bronze, offer good thermal and electrical conductivity. These materials are often used in applications requiring conductivity and corrosion resistance, making them suitable for electrical and plumbing components.
High-strength steel offers enhanced mechanical properties, allowing thinner sections without compromising strength. Frigate uses advanced high-strength steels (AHSS) for automotive applications, where weight reduction is critical.
Nickel alloys exhibit excellent corrosion resistance and high-temperature strength. They are suitable for demanding applications in aerospace and chemical processing. Frigate employs alloys like Inconel for components requiring high performance in extreme environments.
Improving Equipment Functionality and Pressure Regulation
Hydroforming requires precise control of hydraulic pressures to achieve desired shapes in metal forming. Pressure variation can lead to defects such as wrinkling, thinning, or incomplete forming. Equipment regular calibration is essential for consistent pressure application. Frigate employs advanced hydraulic systems with real-time monitoring to maintain optimal pressure levels, ensuring uniform part quality.
Effective pressure management is crucial for achieving required geometries while preserving material integrity. Fluctuations in pressure can impact the mechanical properties of final components. Frigate minimizes pressure-related issues by utilizing robust equipment and sophisticated control systems, enhancing production efficiency and ensuring compliance with stringent quality standards.
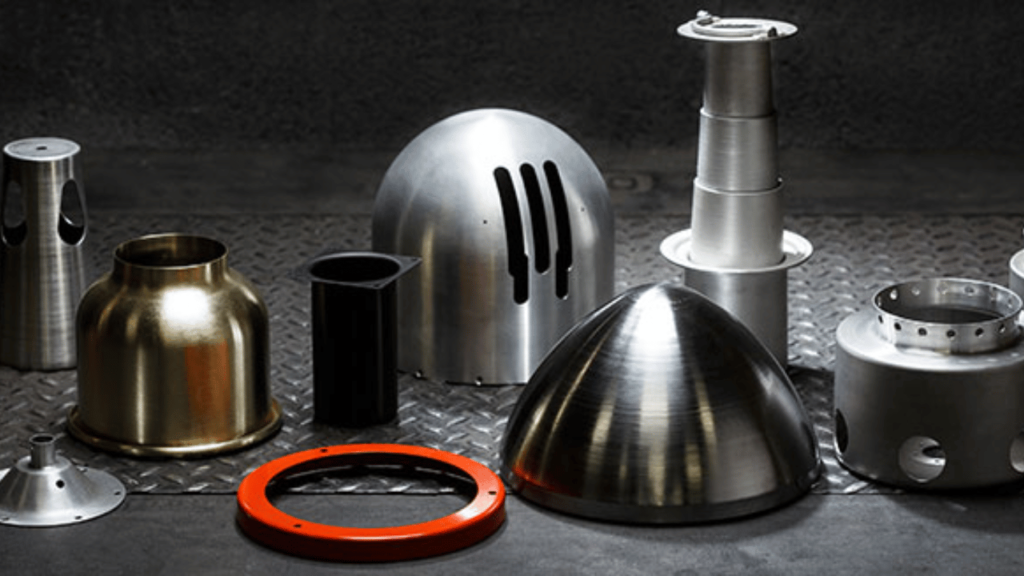
What Our Customers Say about Frigate
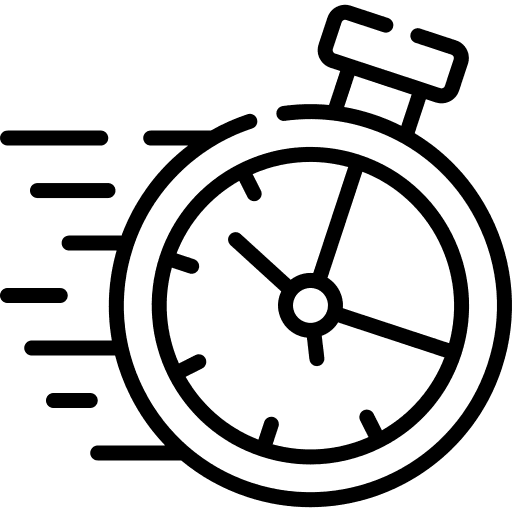
21%
Faster Manufacturing
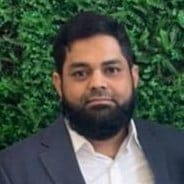
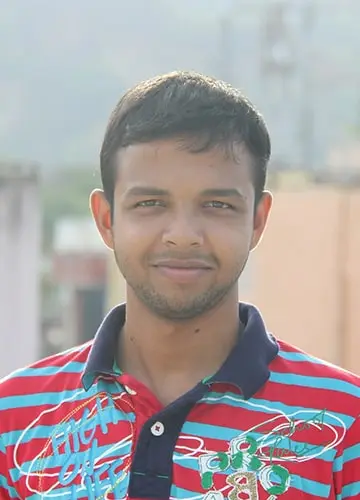

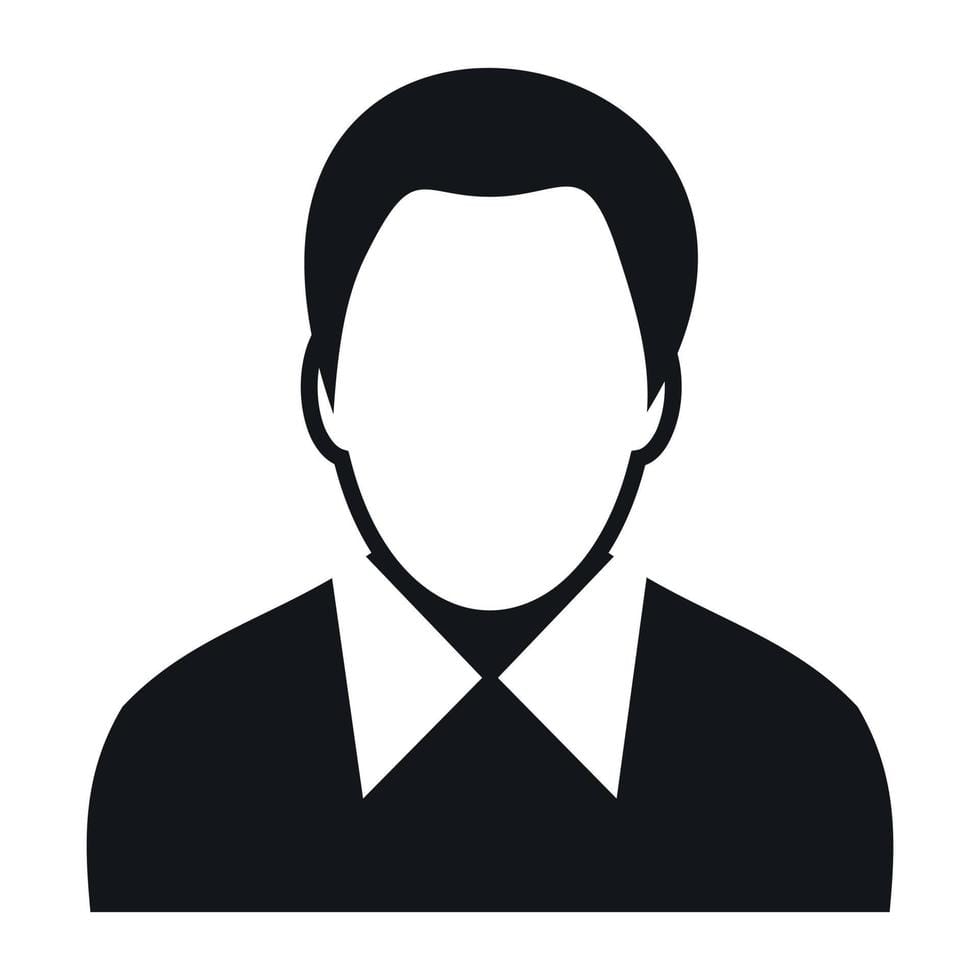
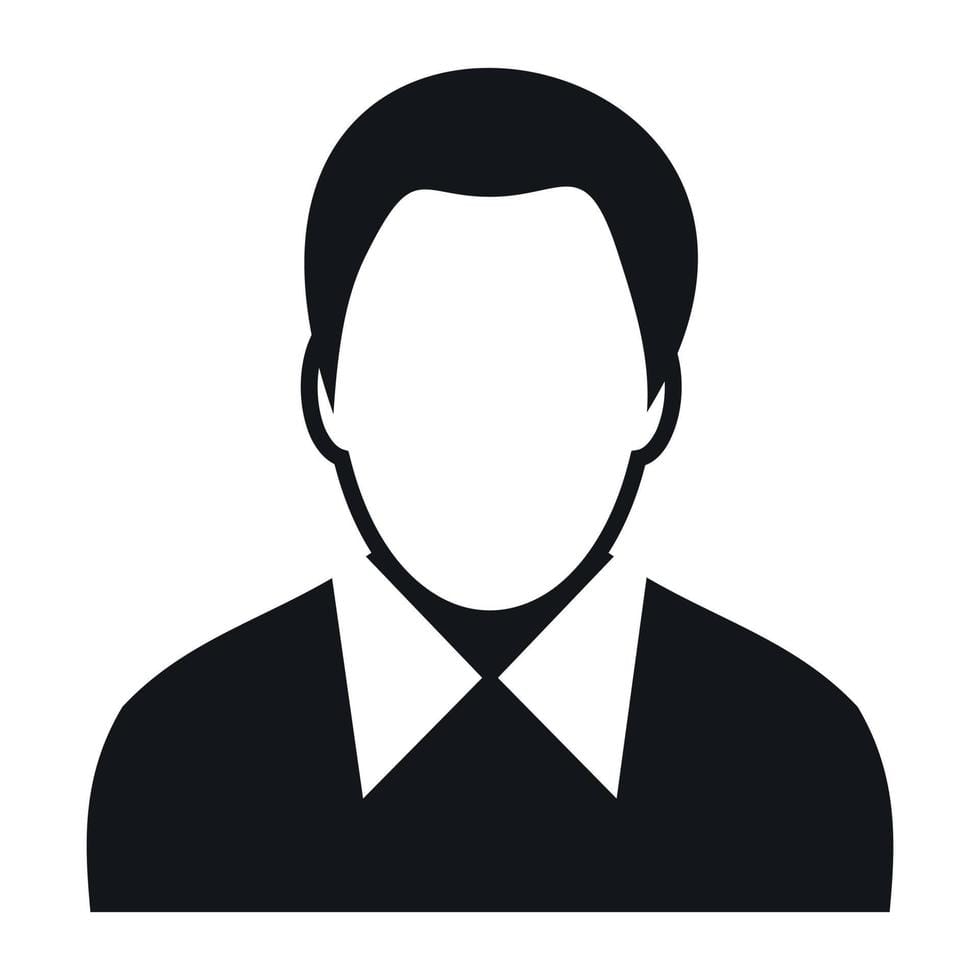
Having Doubts? Our FAQ
Check all our Frequently Asked Question
Material selection is influenced by the required mechanical properties, formability, and complexity of the shapes. Frigate evaluates the specific application needs to ensure optimal material compatibility for hydroforming.
Frigate employs advanced hydraulic systems with real-time pressure monitoring to ensure consistent pressure application. This technology helps prevent defects such as thinning or wrinkling, maintaining high-quality standards throughout production.
Frigate uses precise calibration and advanced tooling to achieve desired shapes while controlling hydraulic pressures. This meticulous approach reduces the risk of defects and enhances the overall integrity of complex parts.
Frigate implements strict quality control measures, including continuous pressure and temperature monitoring during forming. These practices help maintain tight tolerances and ensure that each component meets the specified dimensions and performance requirements.
While hydroforming minimizes the need for secondary operations, some parts may require finishing processes. Frigate assesses each component's needs and employs efficient post-processing techniques to ensure that all parts meet industry standards and customer specifications.
Manufacturing Capability/Capacity
Ferrous casting
Mold size(max): 1m X 1m
Weight Range: 1 KG ~ 30 KGS
Mold size(max): 1.5m X 1.5m
Weight Range: 30 KG ~ 150 KGS
Mold size(max): 3m X 3m
Weight Range: 100 KG ~ 1000 KGS
Mold size(max): 500 MM X 500 MM
Weight Range: 0.250 KG ~ 20 KGS
Mold size(max): 500 MM X 500 MM
Weight Range: 0.100 KG X 20 KGS
Non-ferrous casting
Capacity: 5000 MT/a
Range of weight: 100 gm to 20 KGS
Mold size(max): 1 M X 1 M
Weight Range: 0.5 KG X 50 KGS
Mold size(max): 1 M X 1 M
Weight Range: 0.5 KG X 50 KGS
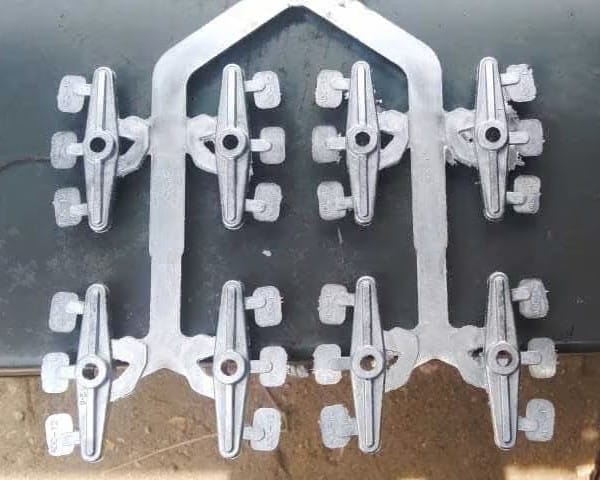
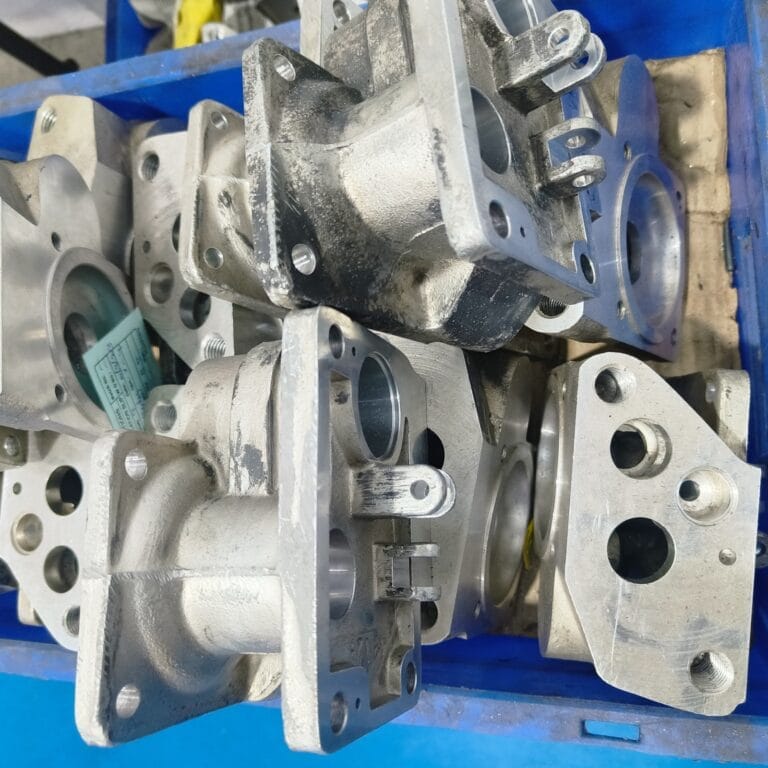
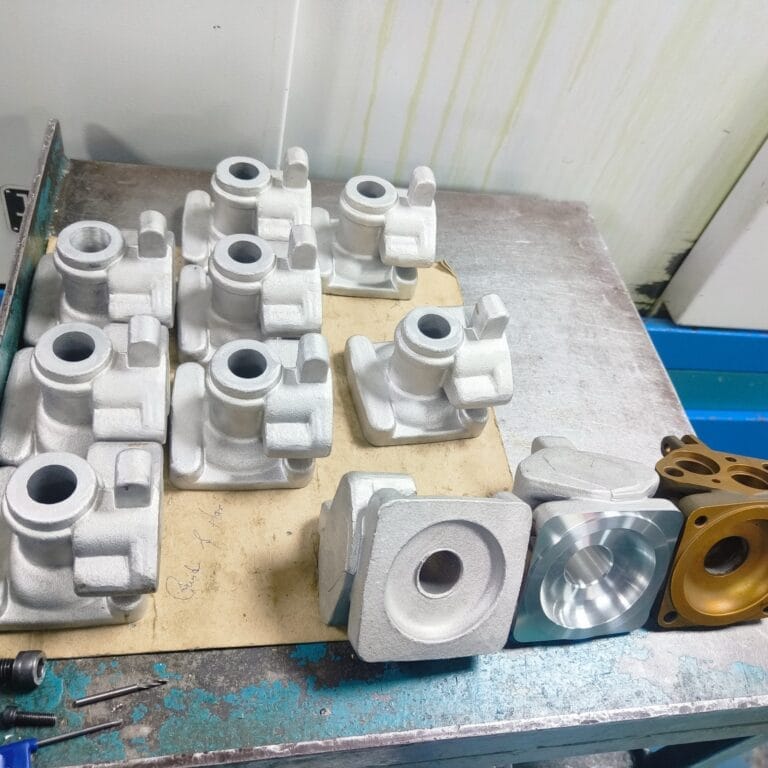
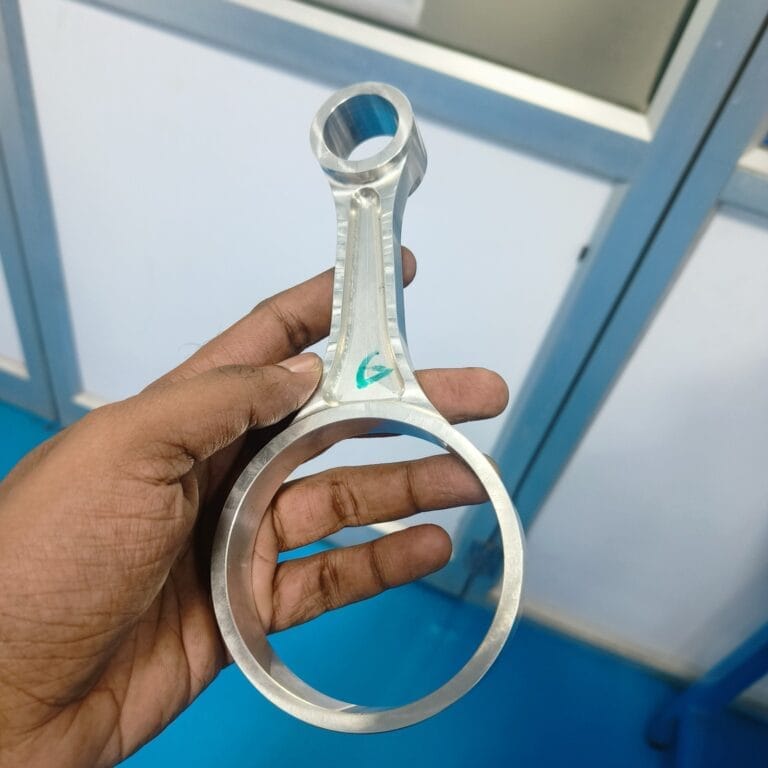
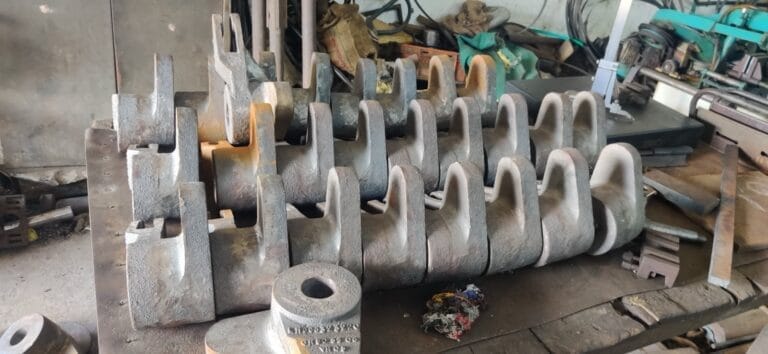
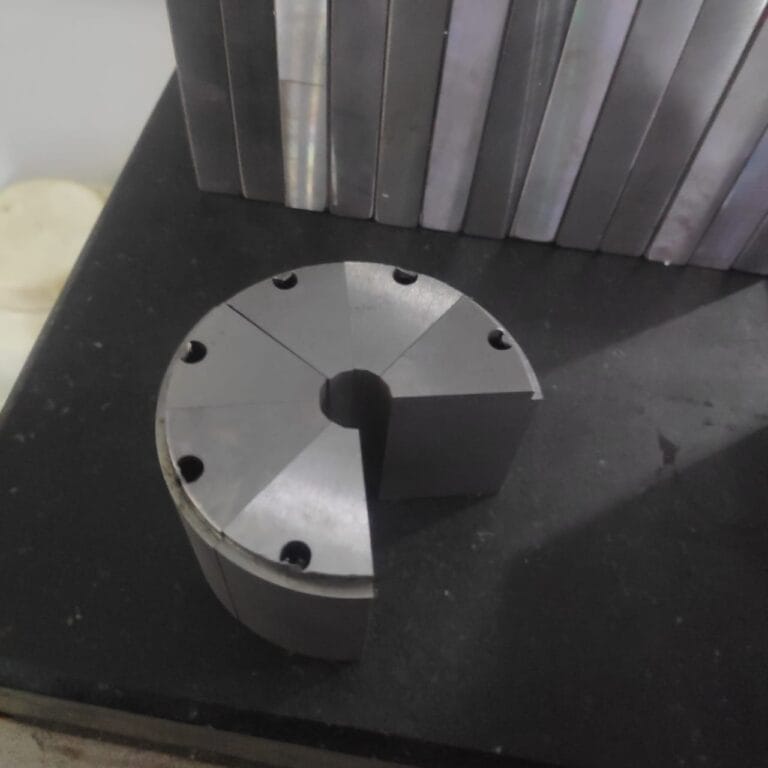
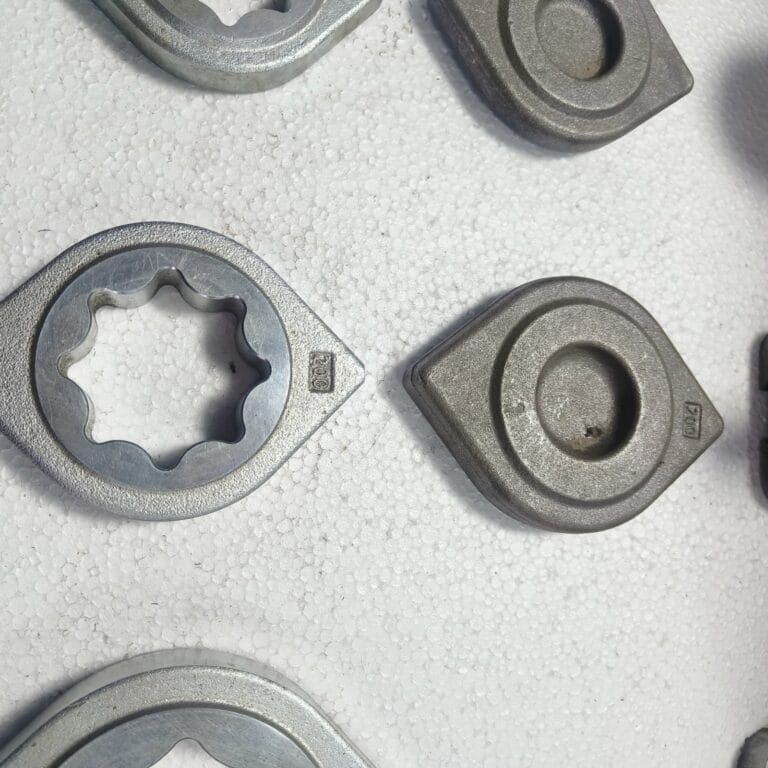
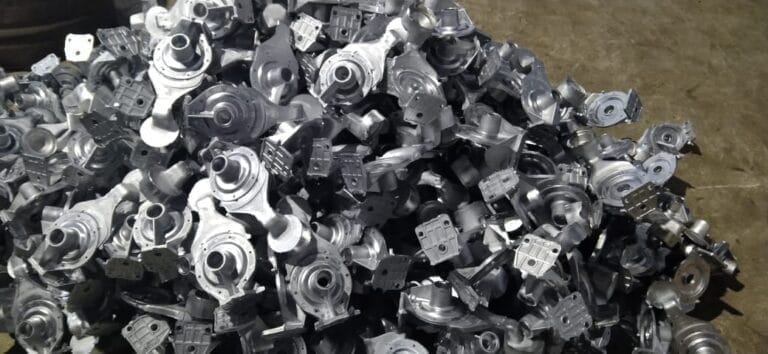
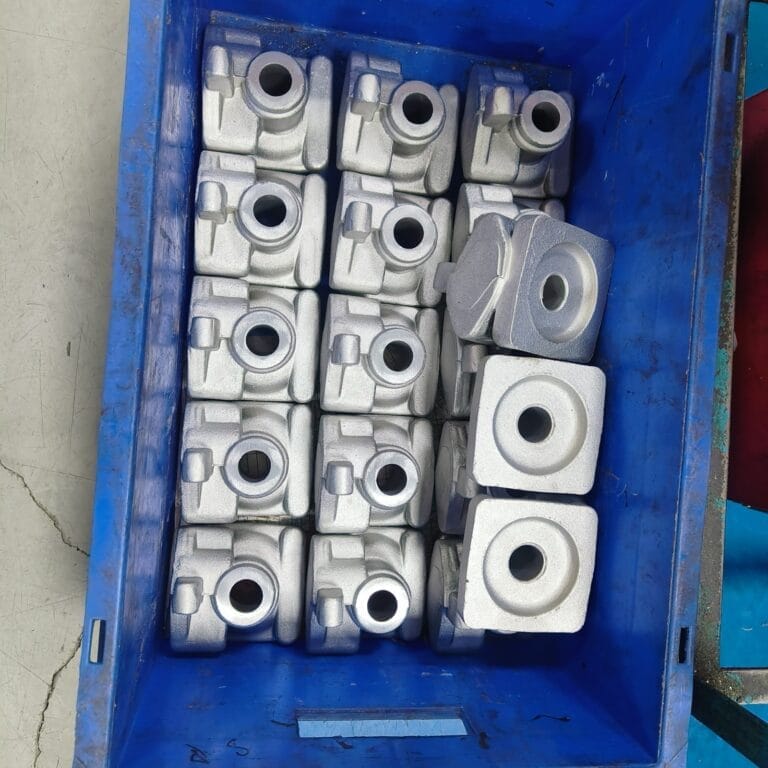
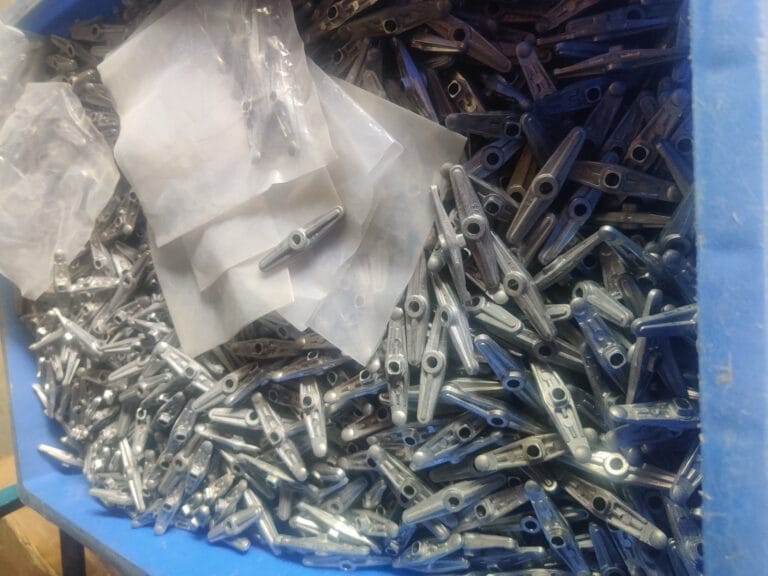
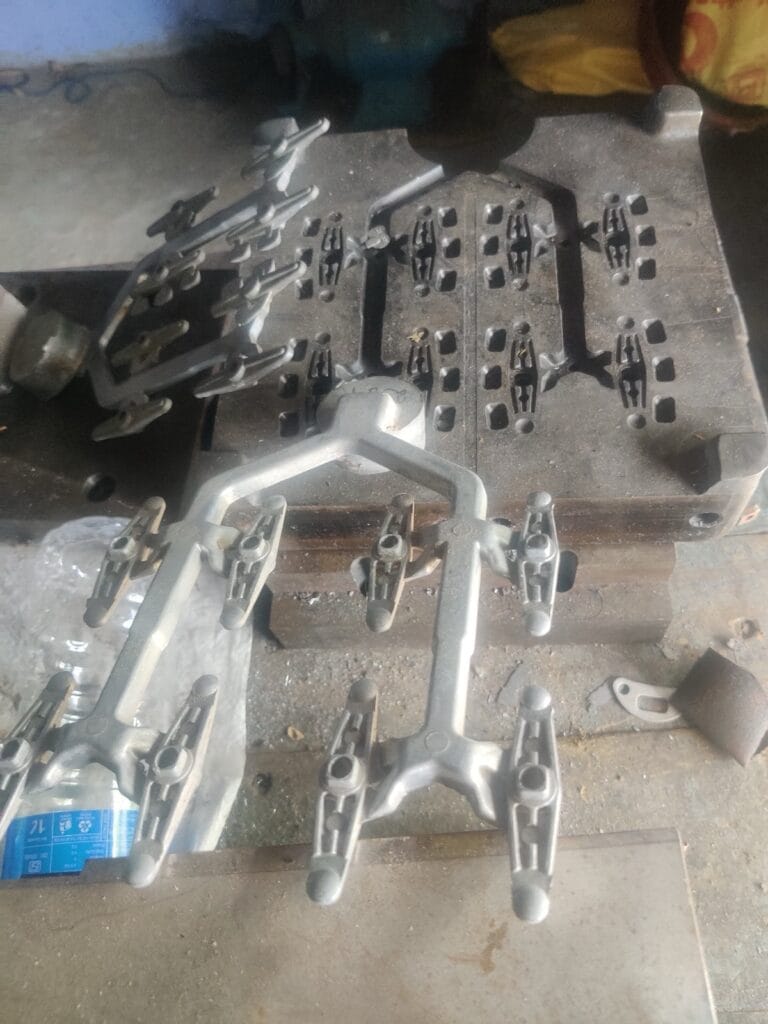
Forging
Capacity: 20,000 Tons per Annum
Range of weight: 300 KG to 1 Ton
Hammering: 5 Ton
Range of weight: 0.2 KG to 200 KGS
Hammering: 1600 Ton Hydraulic press
Ring size: 350 MM OD to 3000 MM OD
Range of weight: 15 KGS to 3200 KGS
Materials
Carbon Steel, Stainless Steel (AUSTENITE), Alloy Steel, Stainless Steel (MARTENSITE), etc.
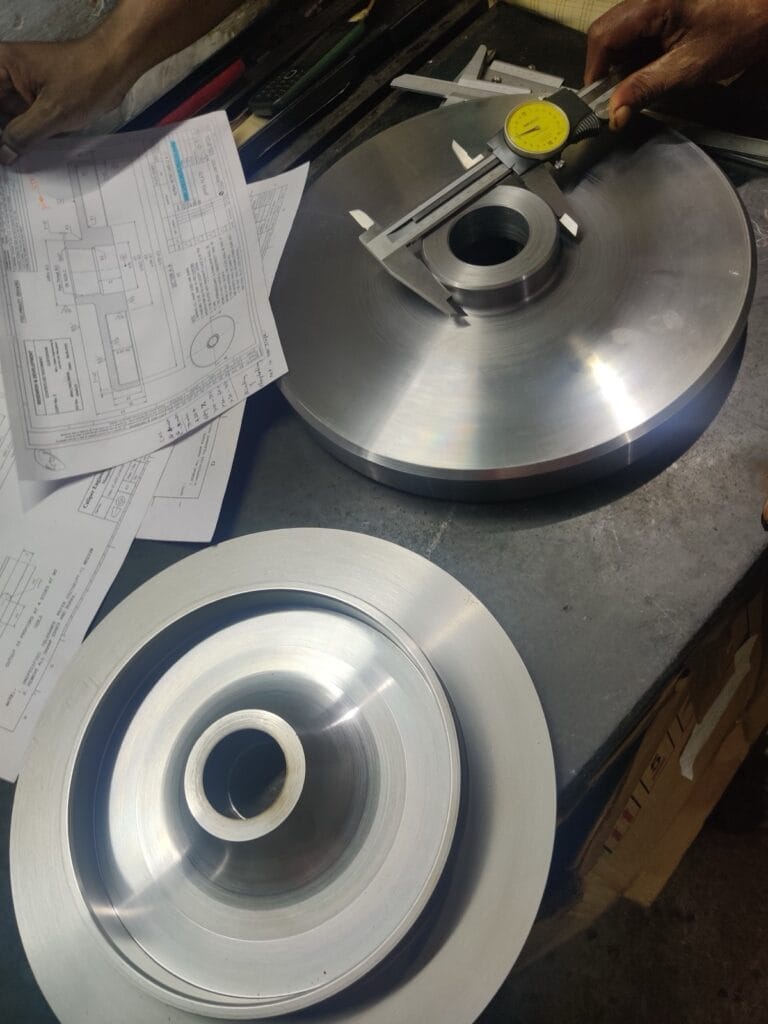
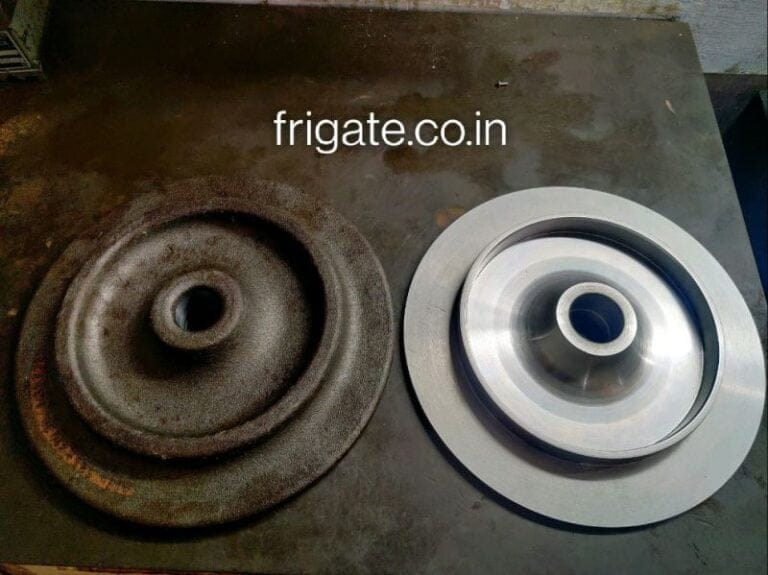
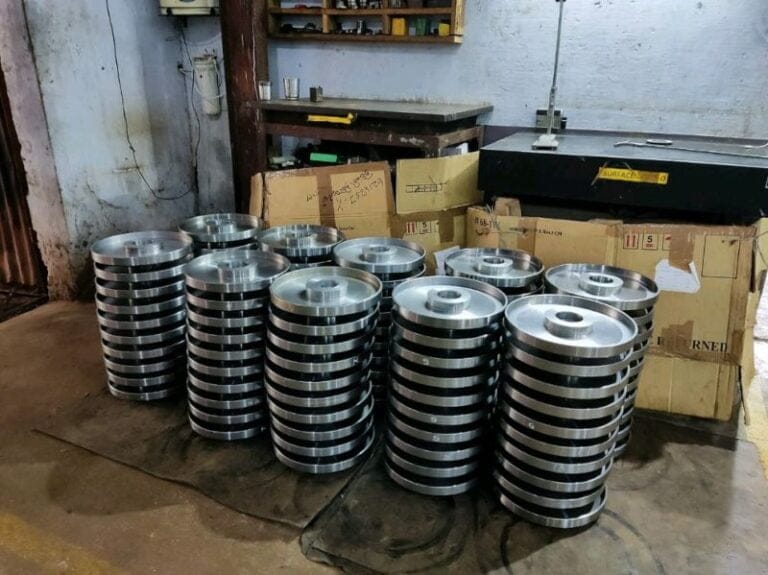
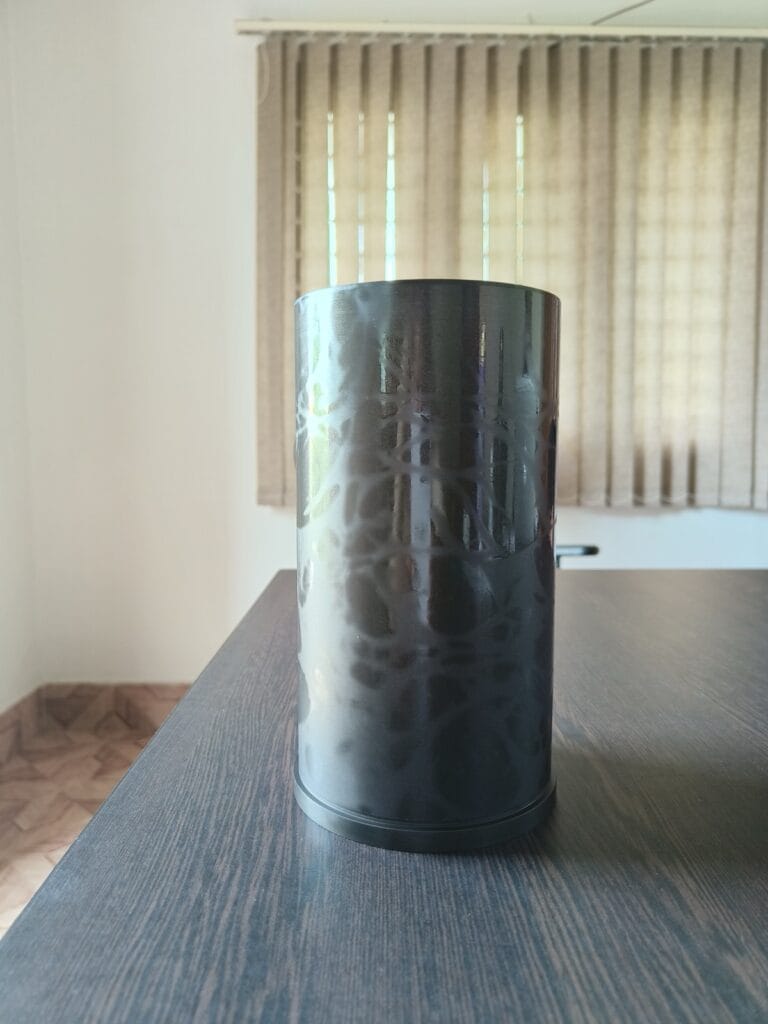
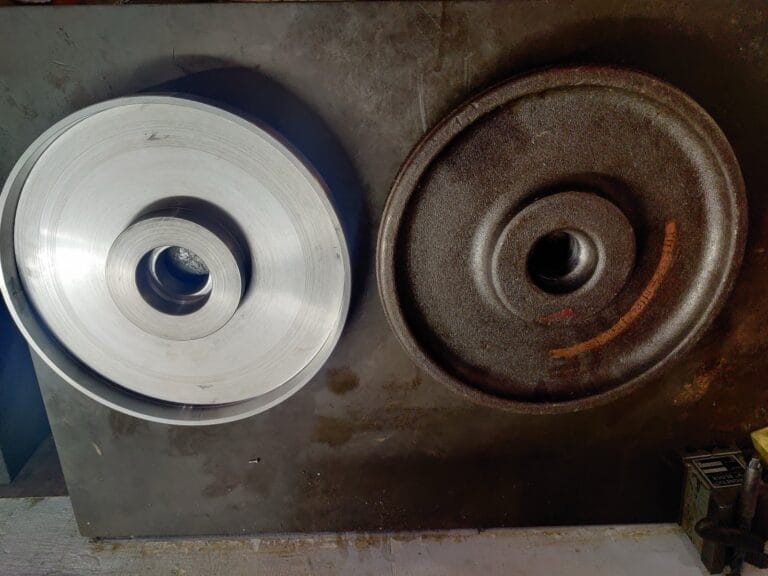
Machining
1 to 1000 MM
1 to 1000 MM
1 to 1000 MM
Materials
Steel, Aluminum, Brass, Copper, Titanium, Nickel Alloys, Tungsten Carbide, etc.
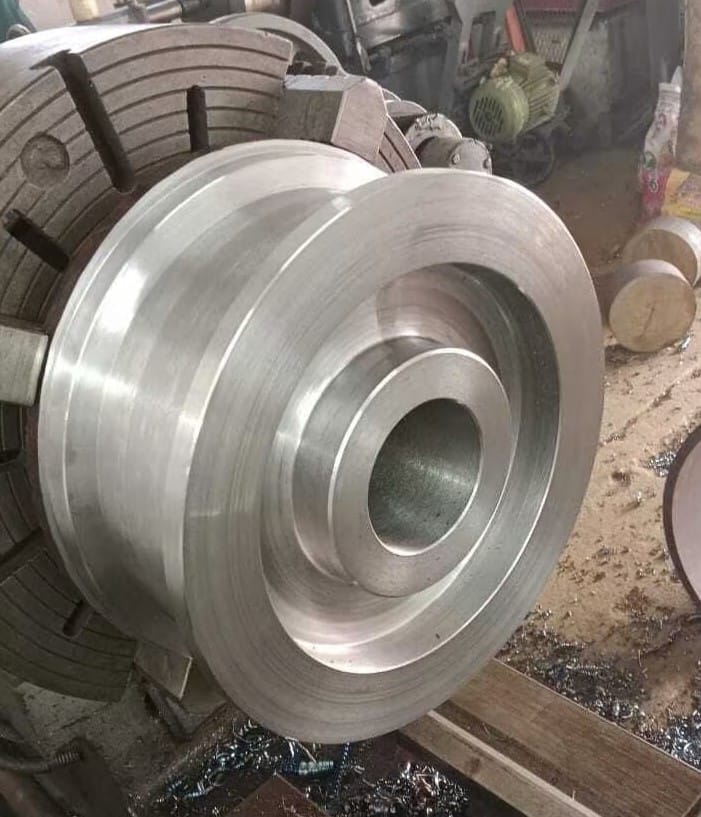
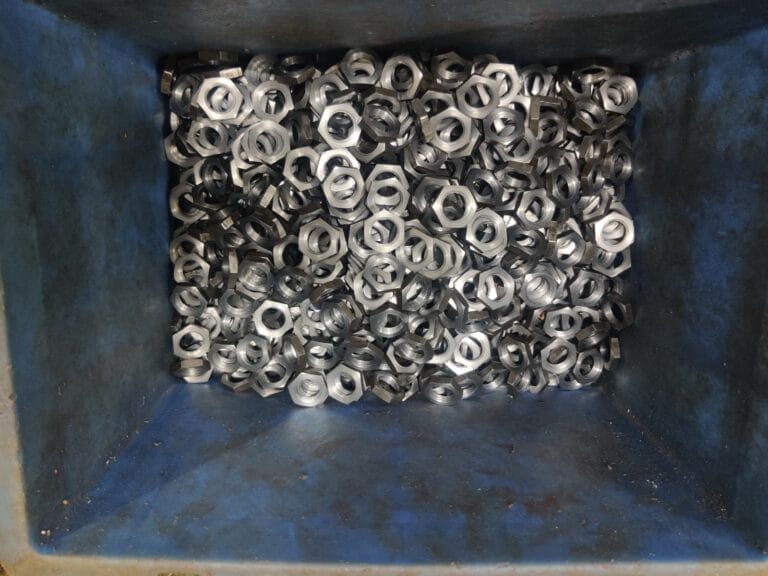
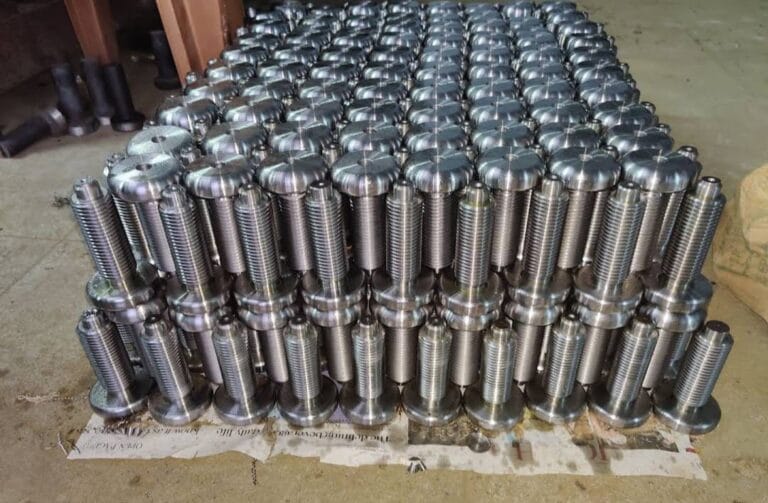
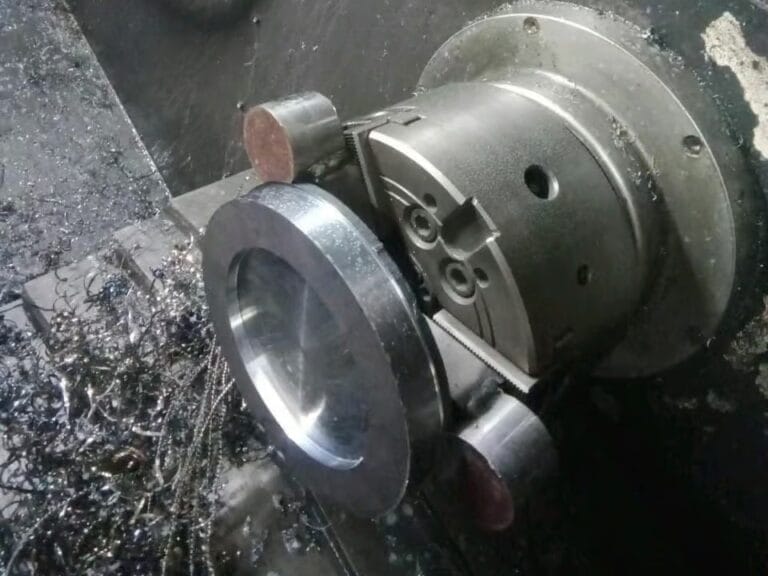
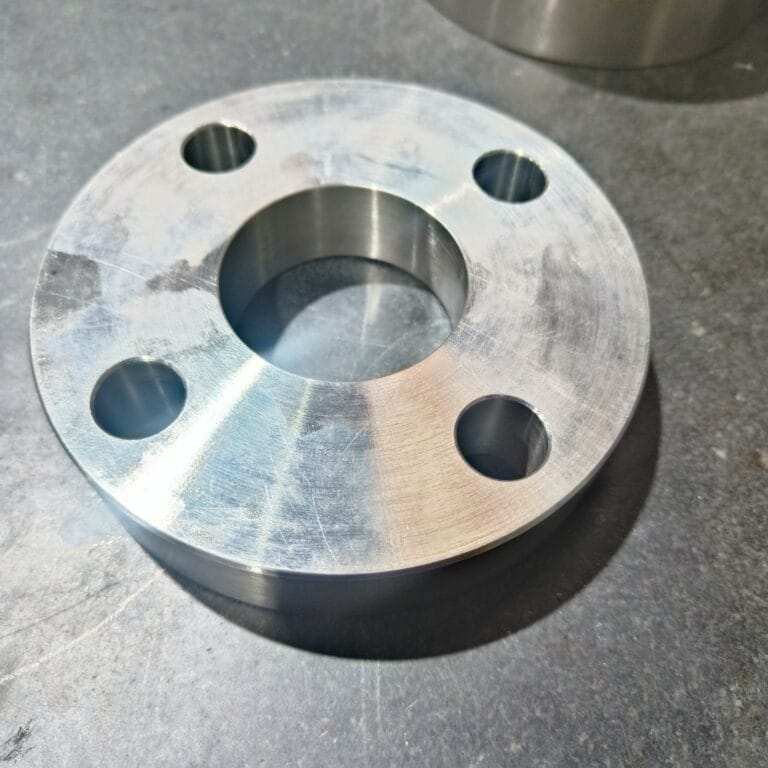
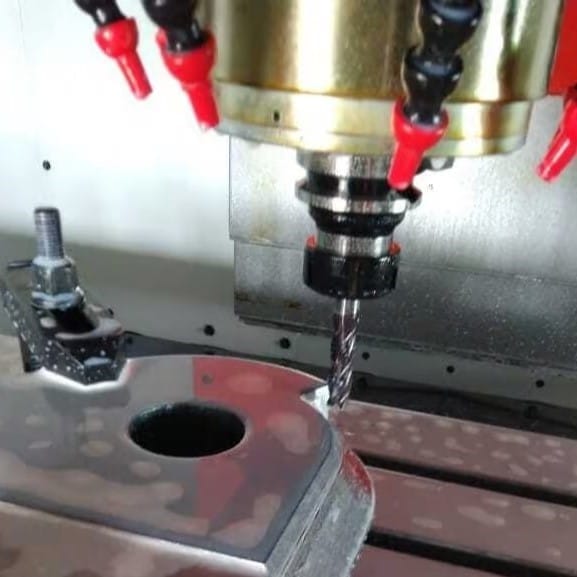
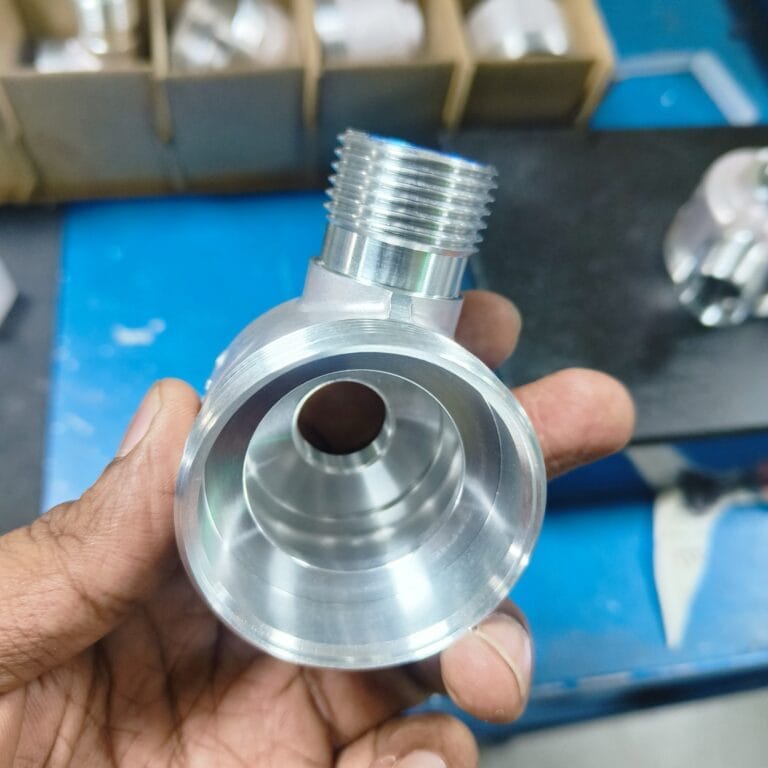
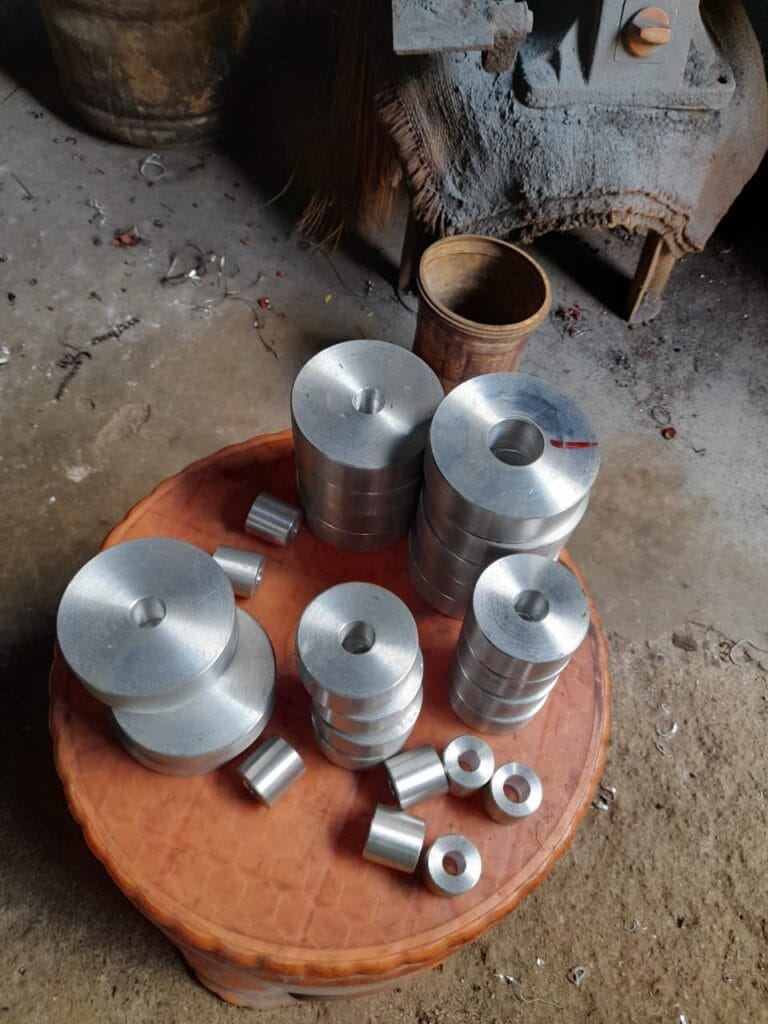
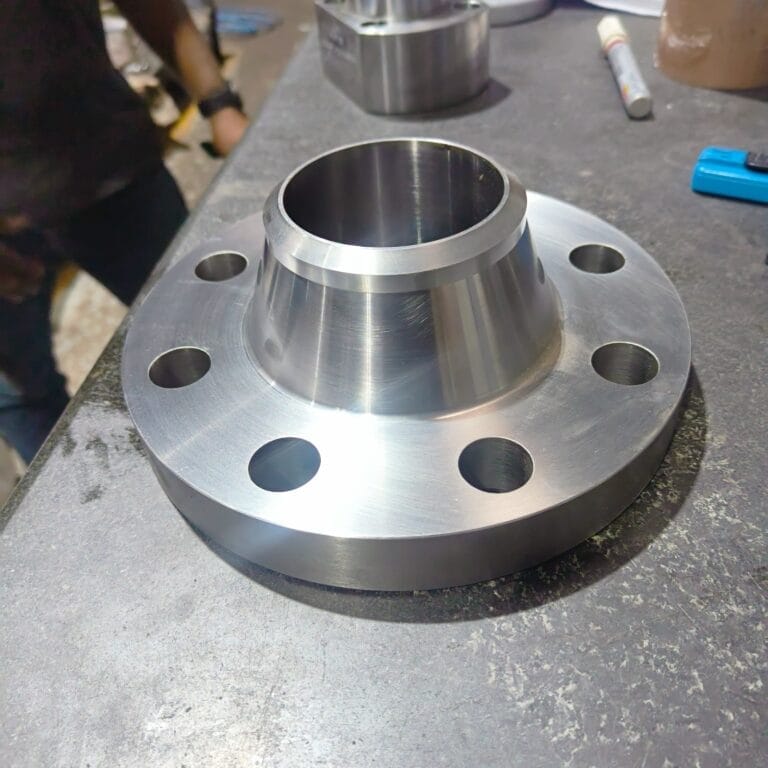
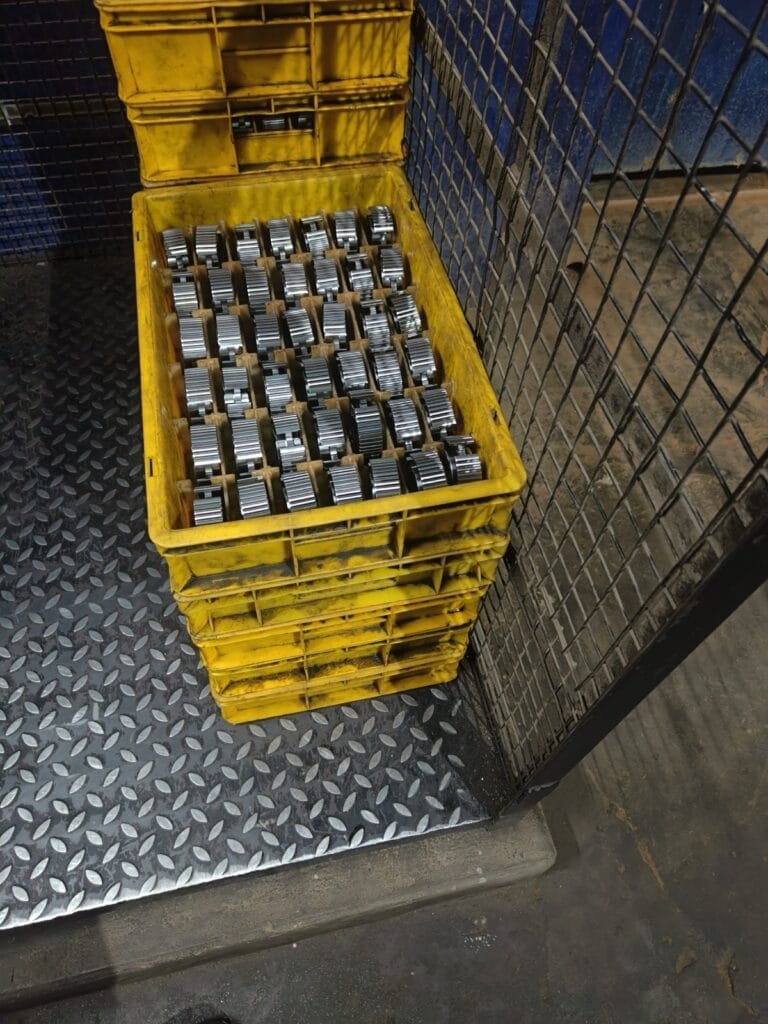
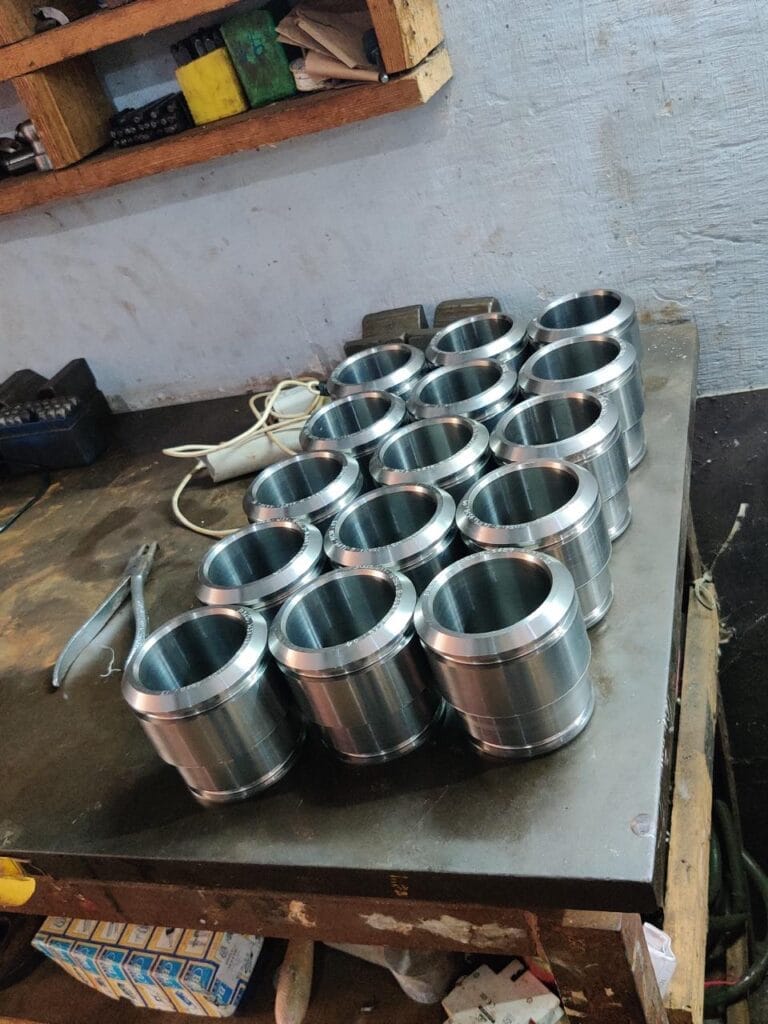
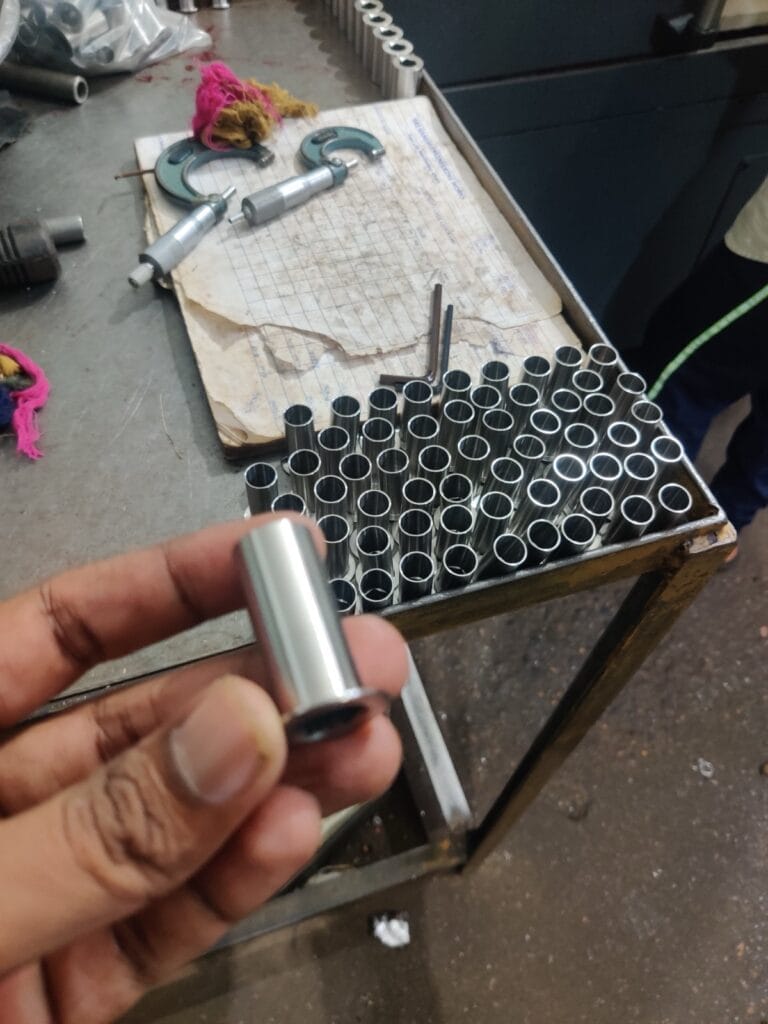
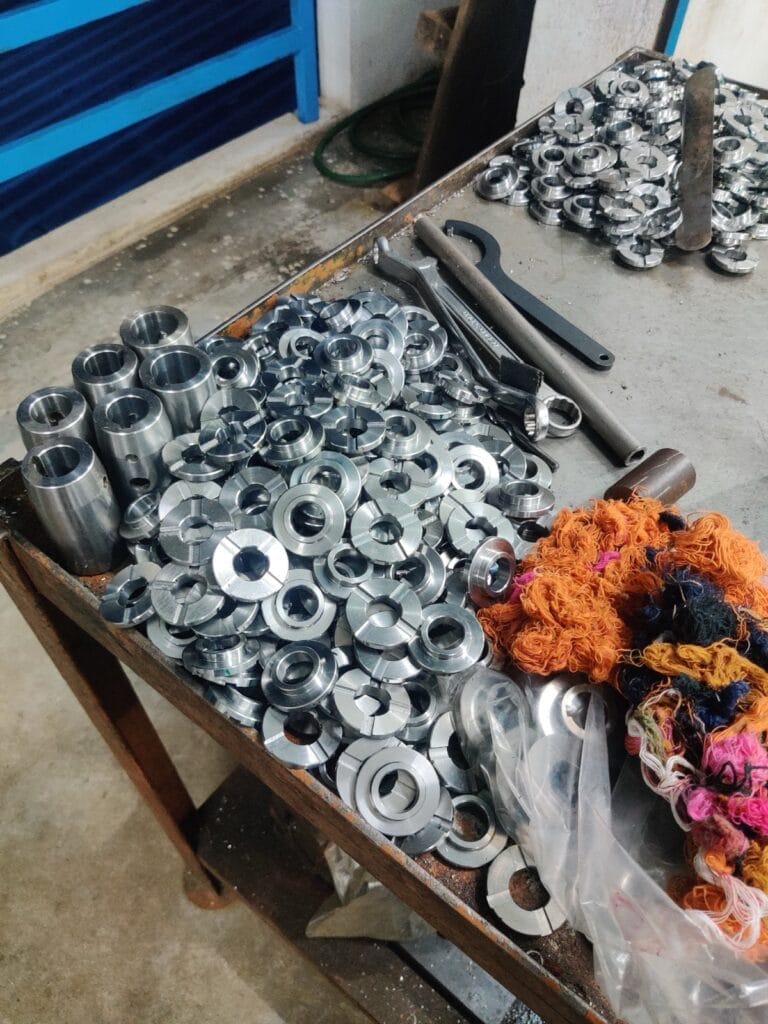
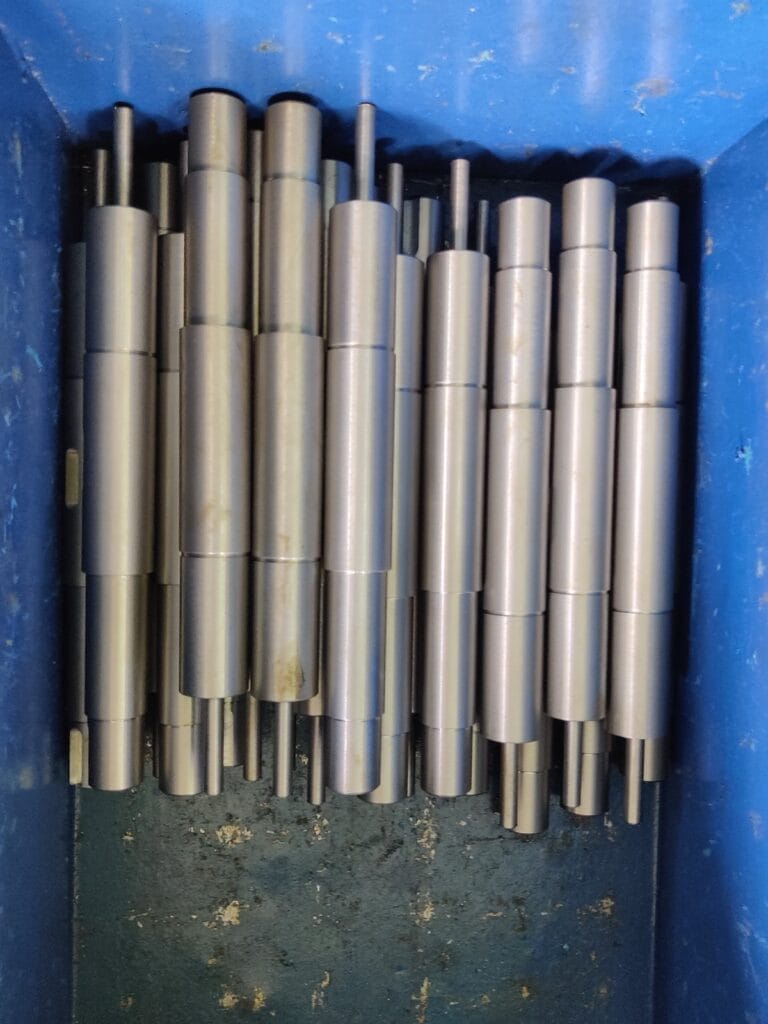
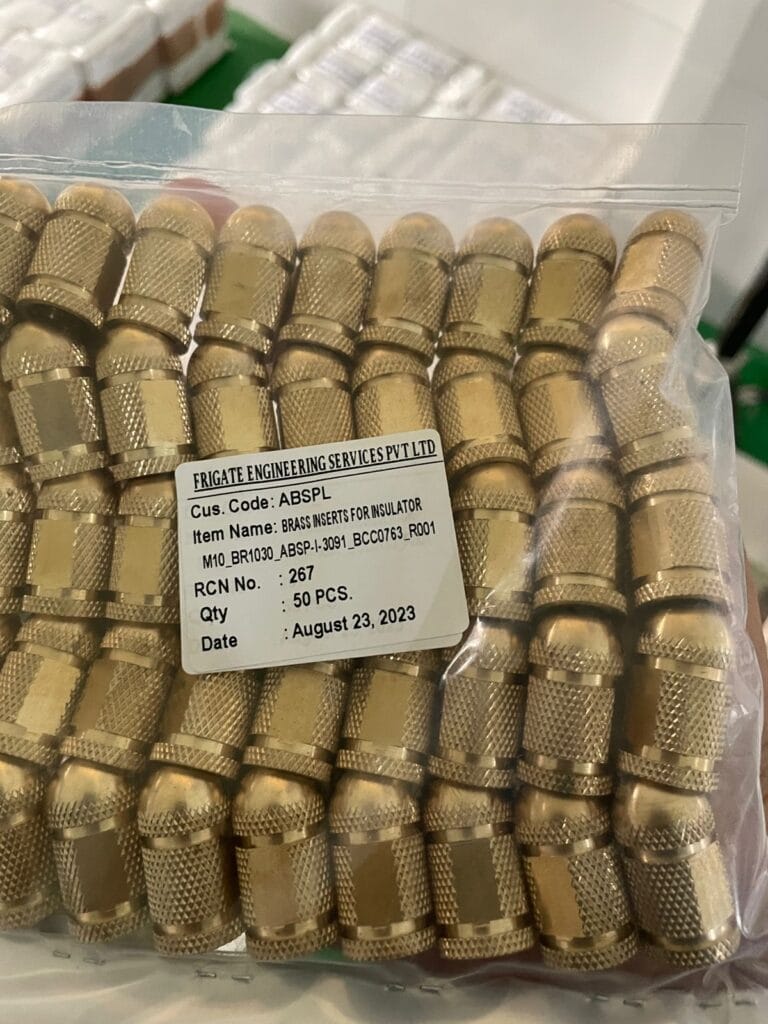
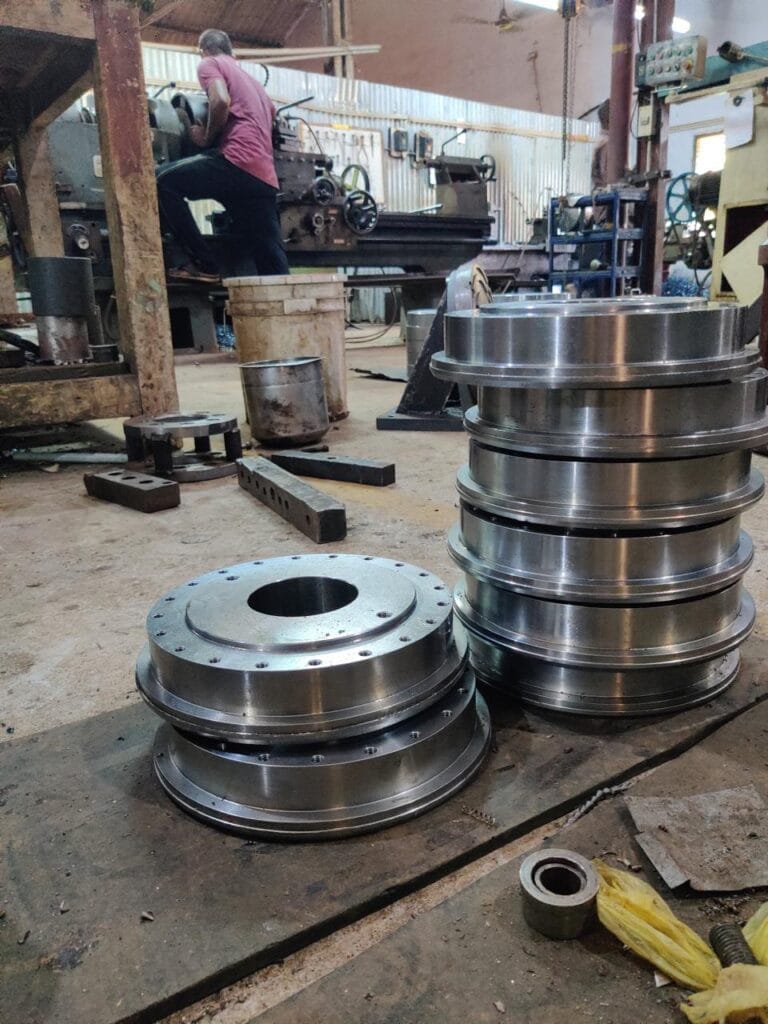
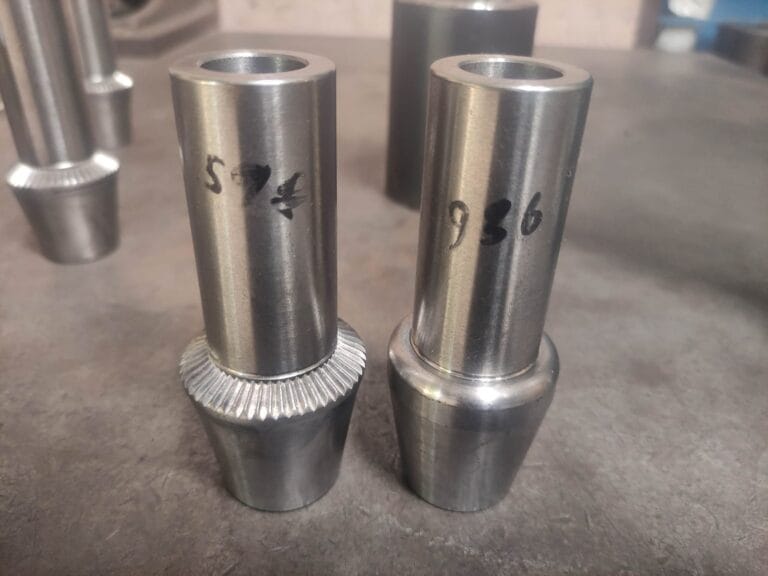
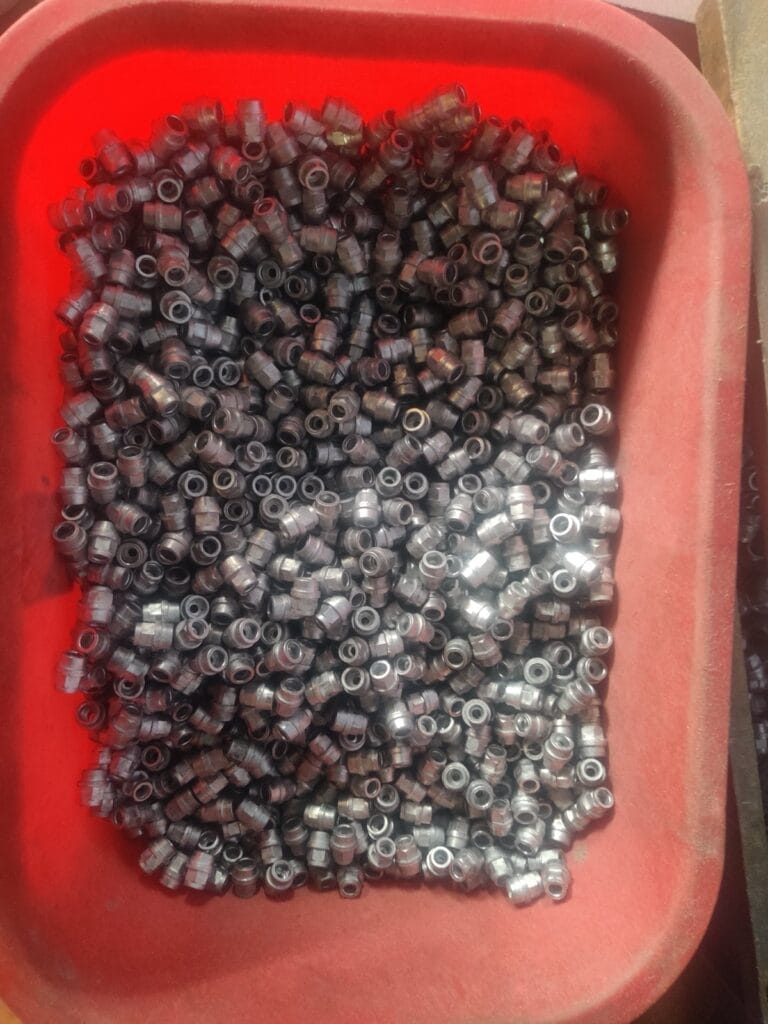
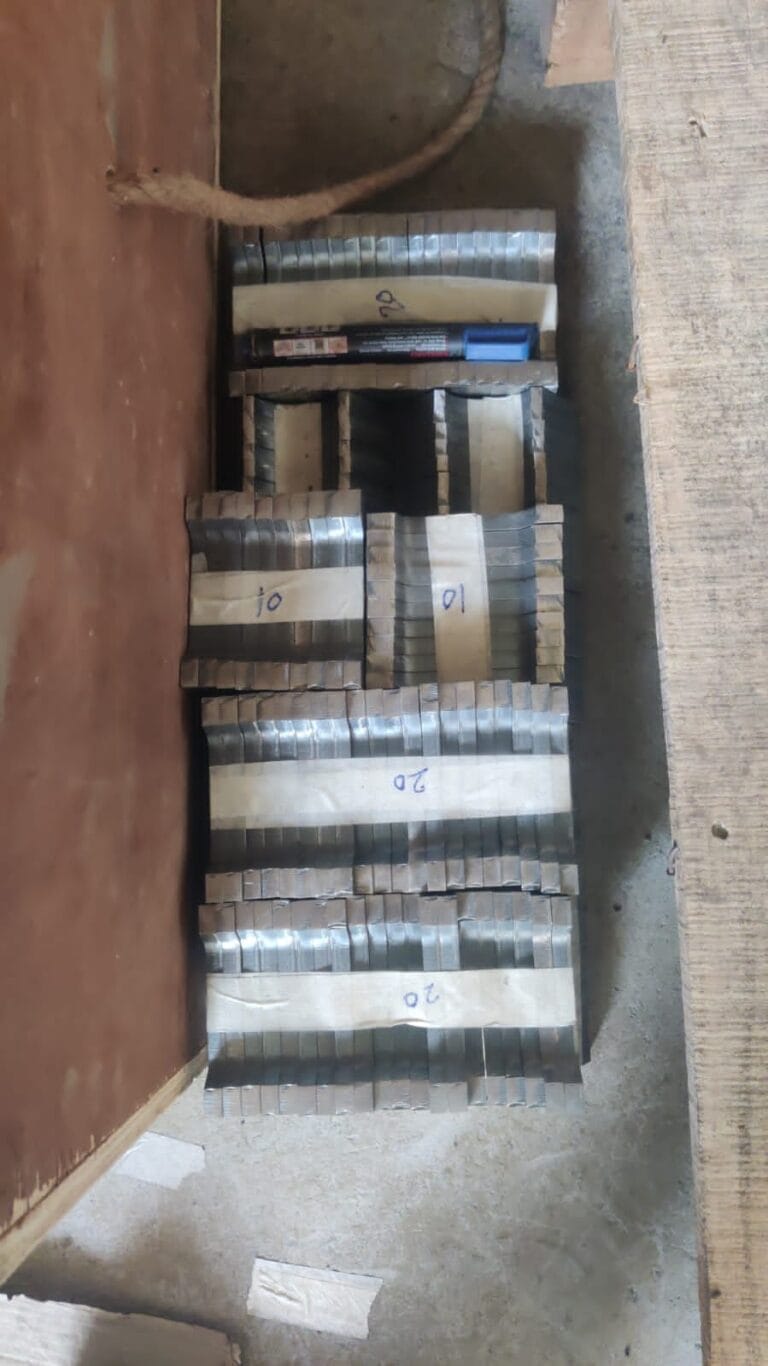
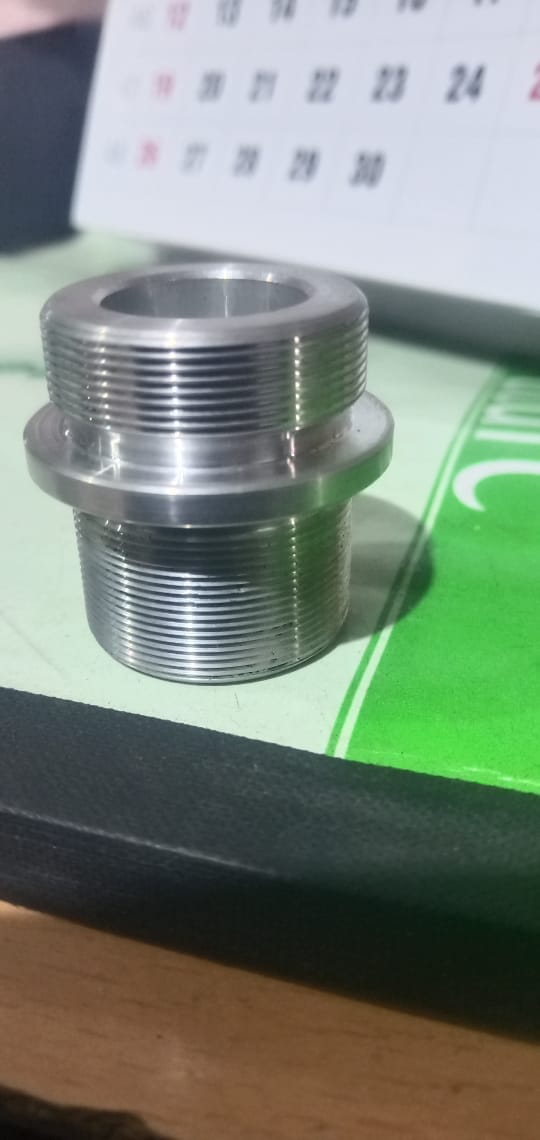
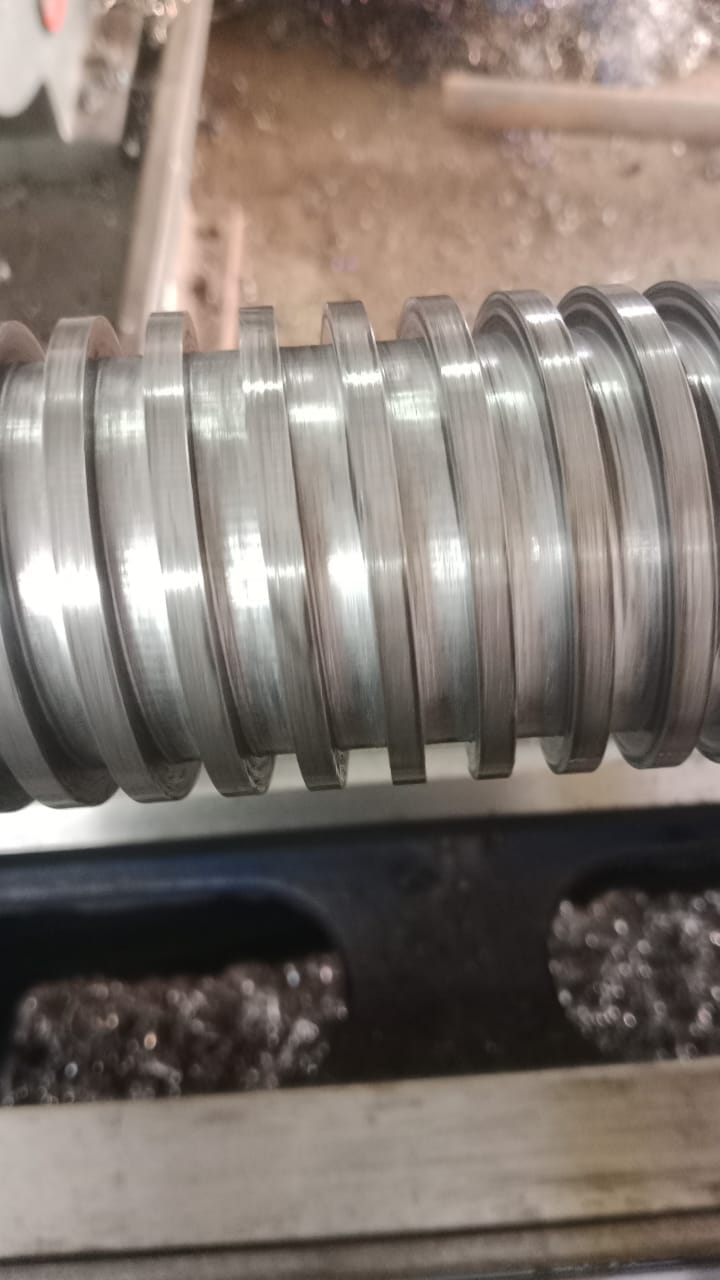
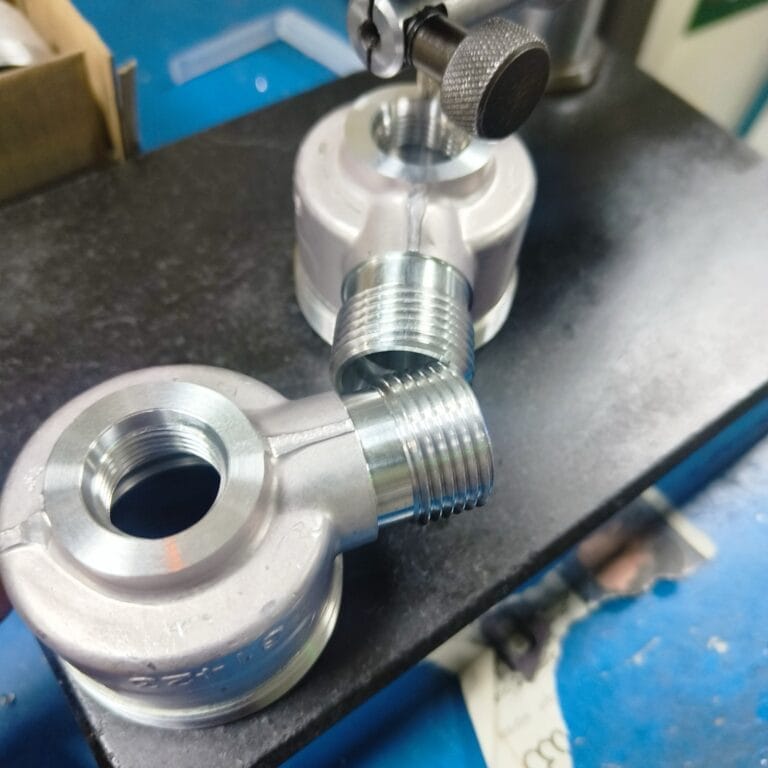
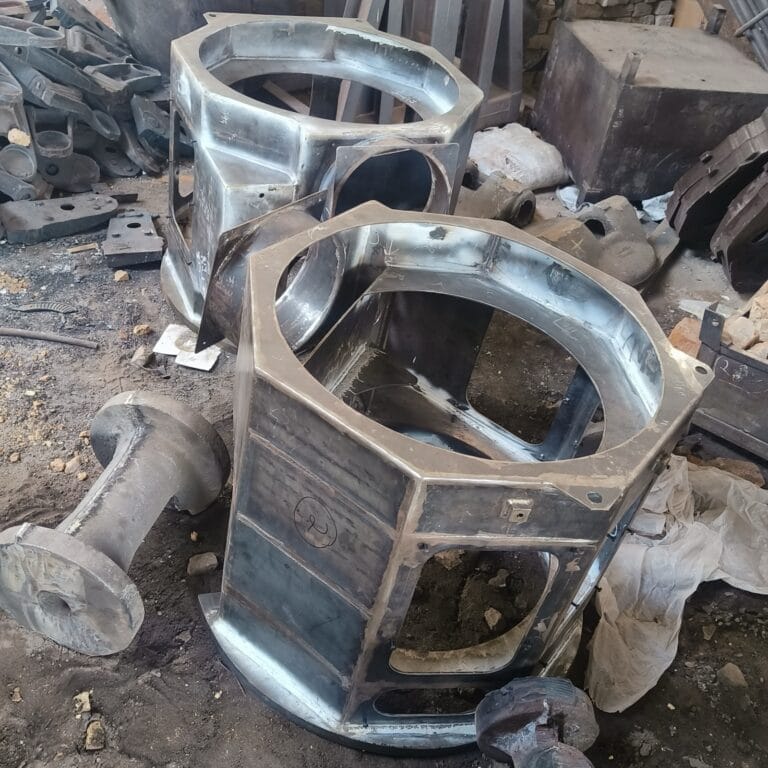
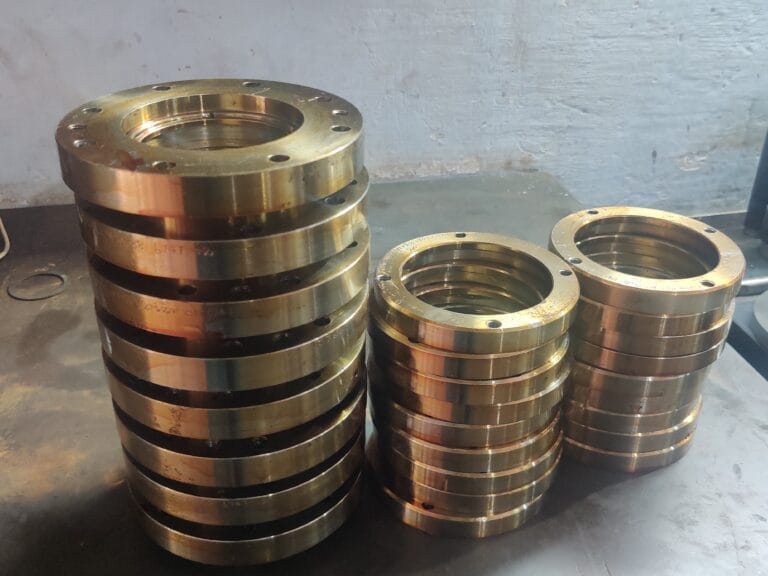
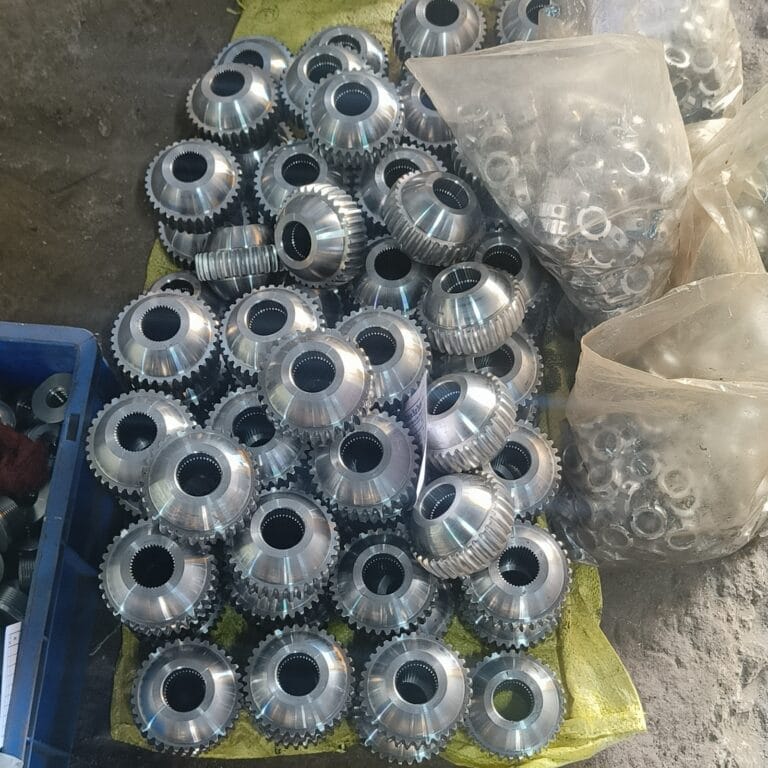
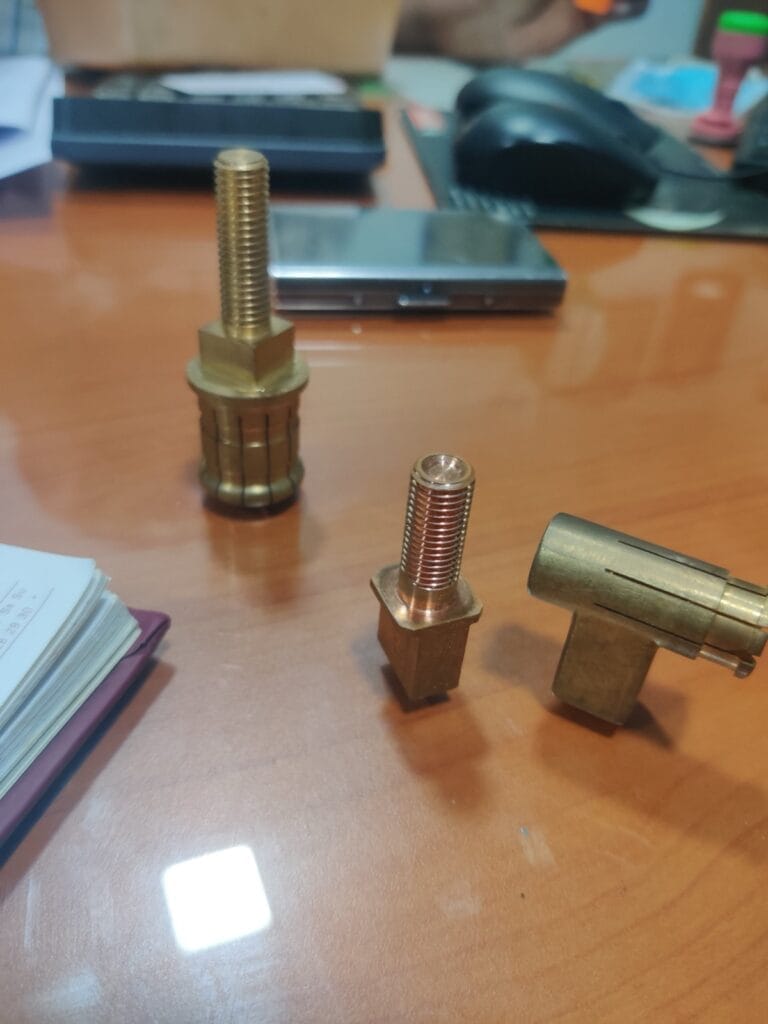
Plastics
Materials
1250 X 1250 MM
Within 10 microns
Engineering Plastics, Polyethylene, Polypropylene, Polyvinyl chloride, Polyethylene terephthalate, Bioplastics, etc.
Rubber
Materials
Natural rubber, Styrene-Butadiene Rubber, Nitrile Butadiene Rubber, Silicone Rubber, Fluorocarbon Rubber, Recycled Rubber, etc.
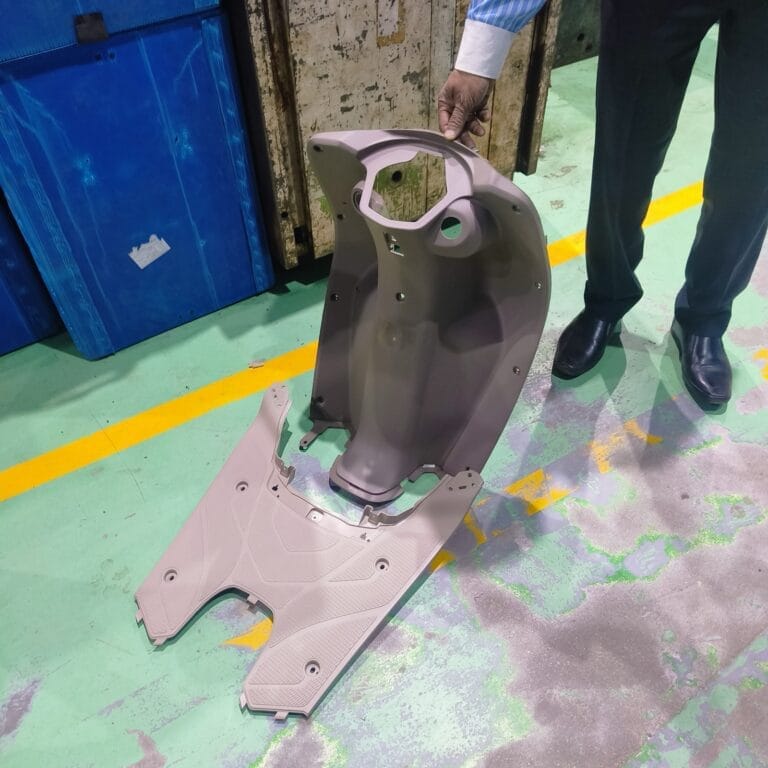
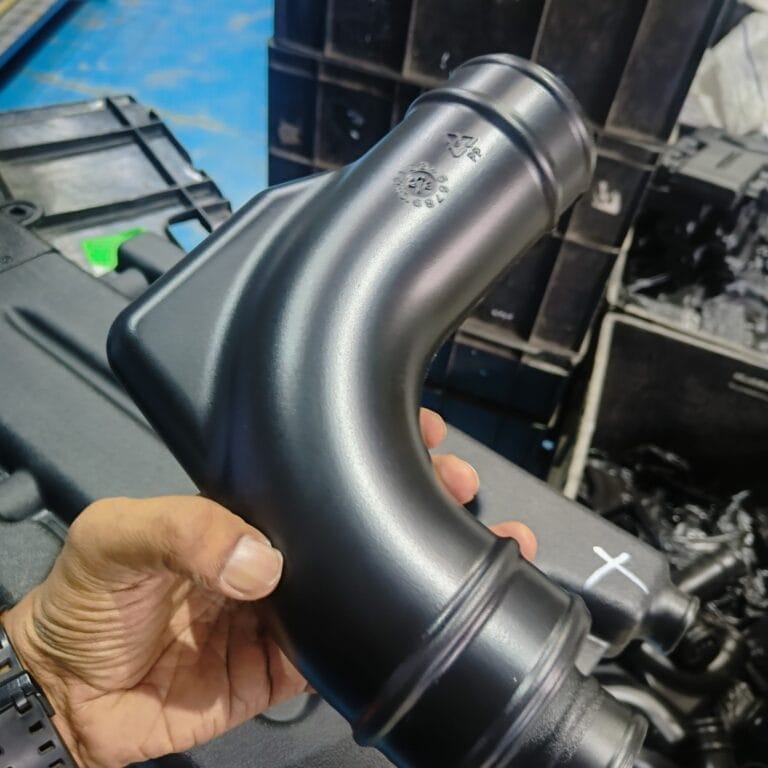
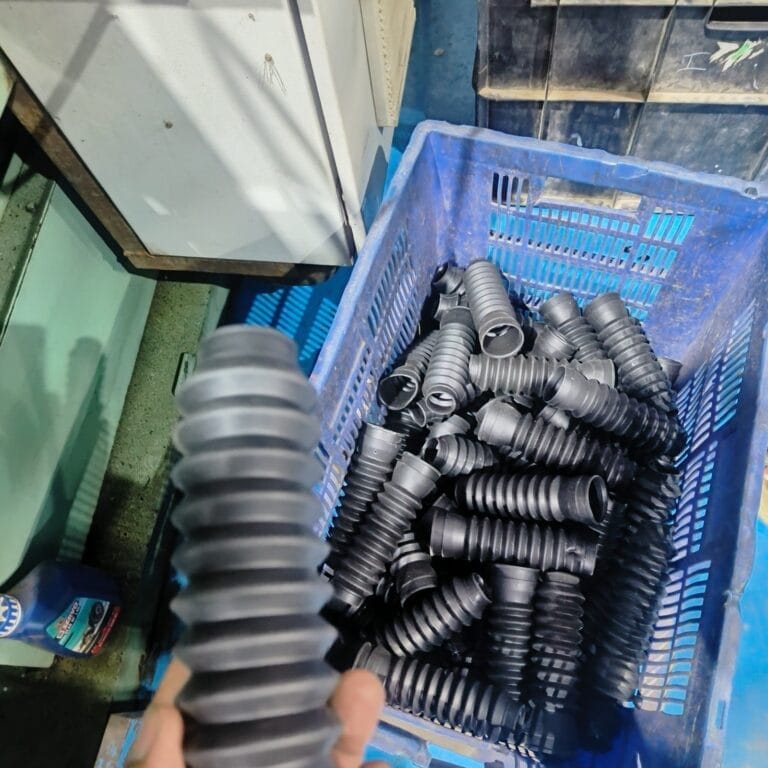
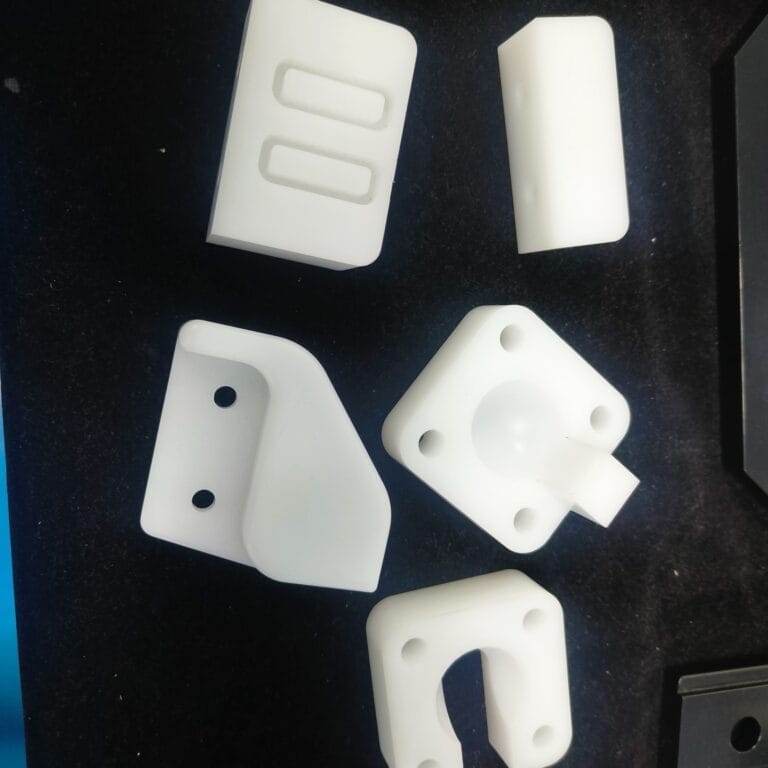
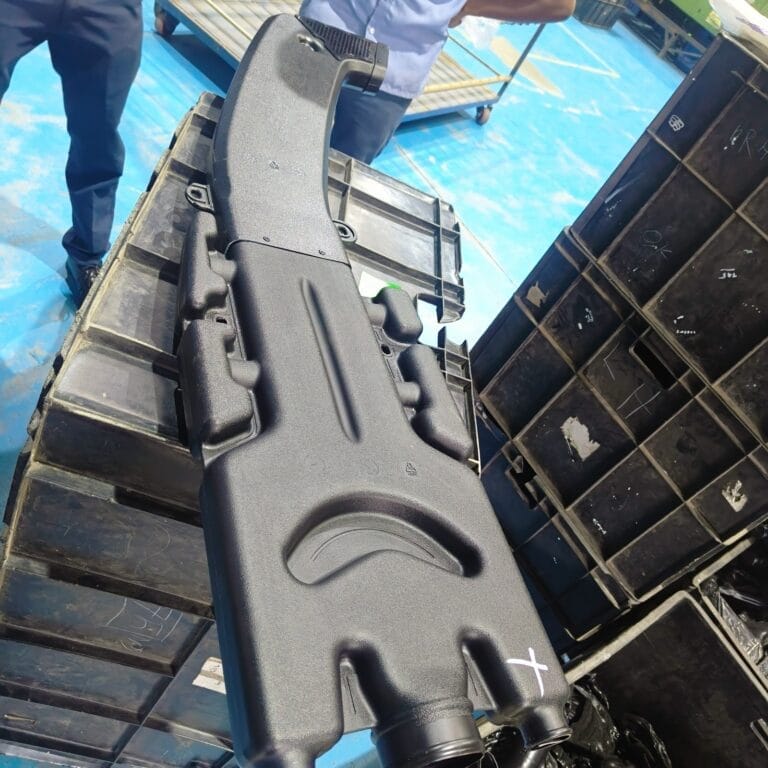
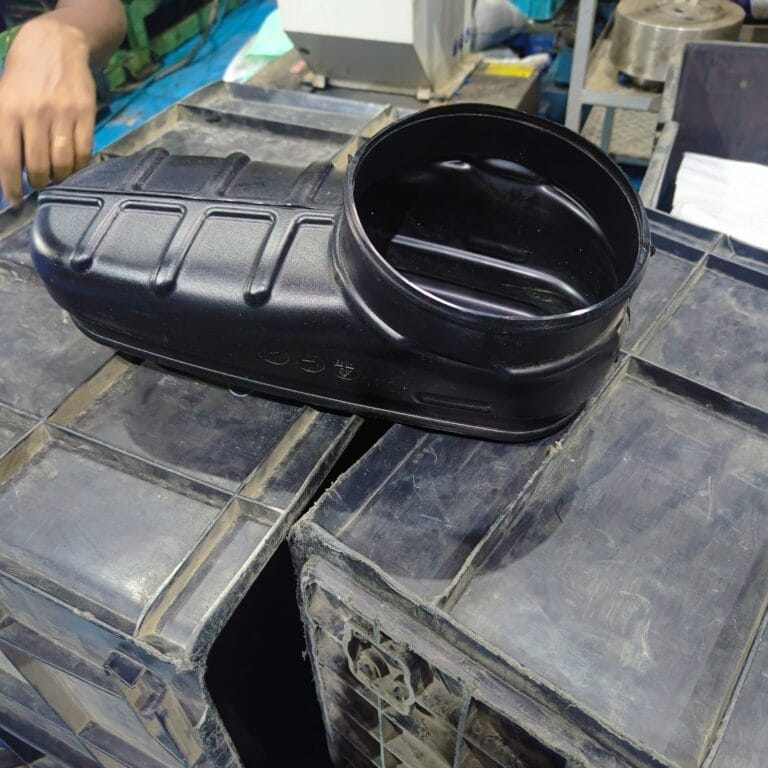
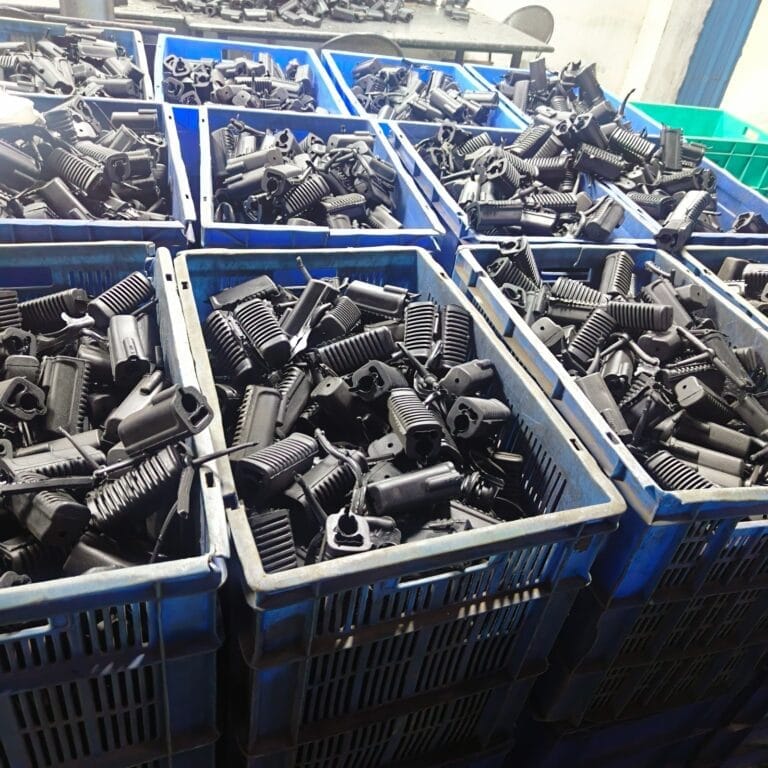
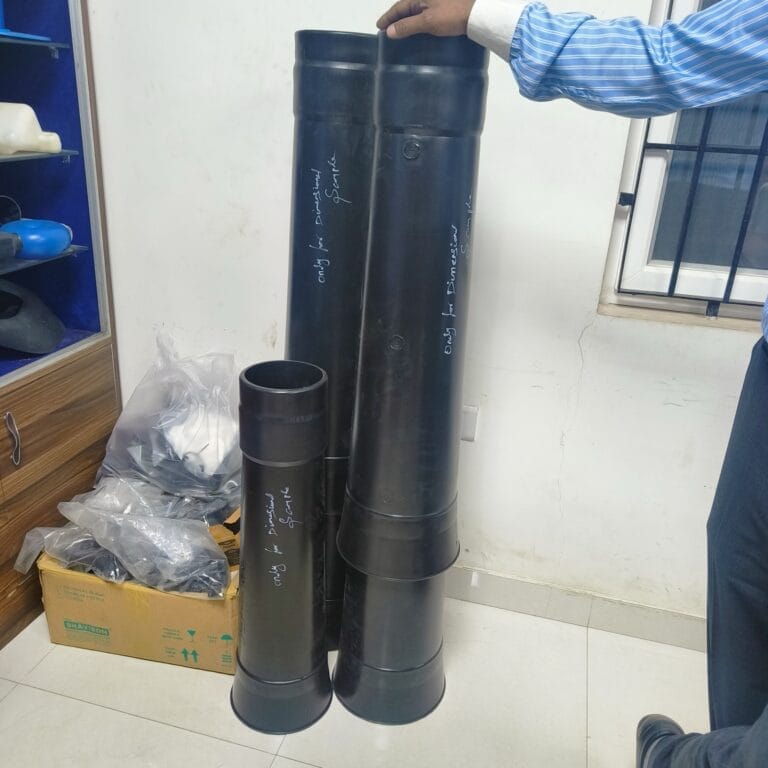
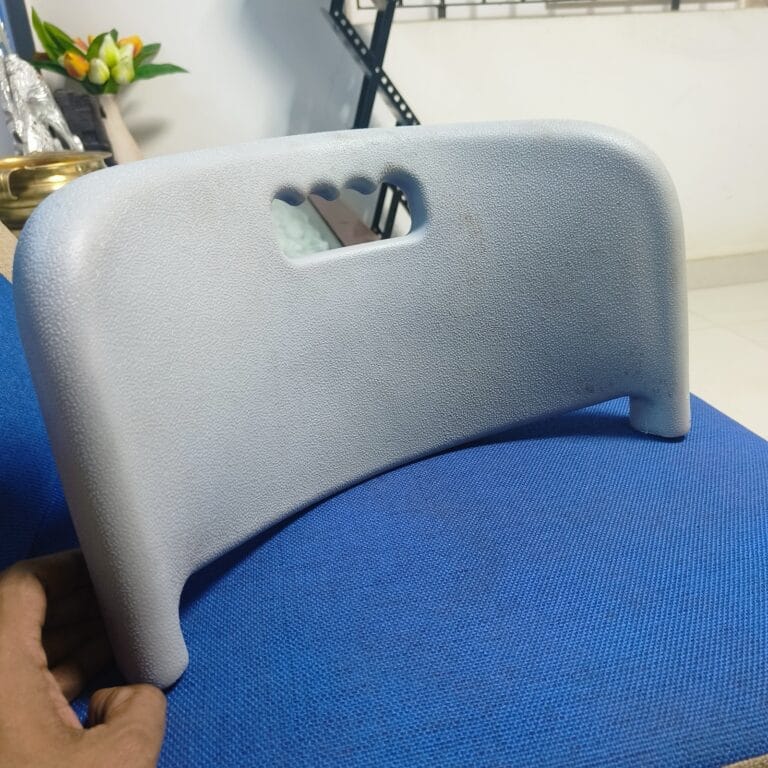
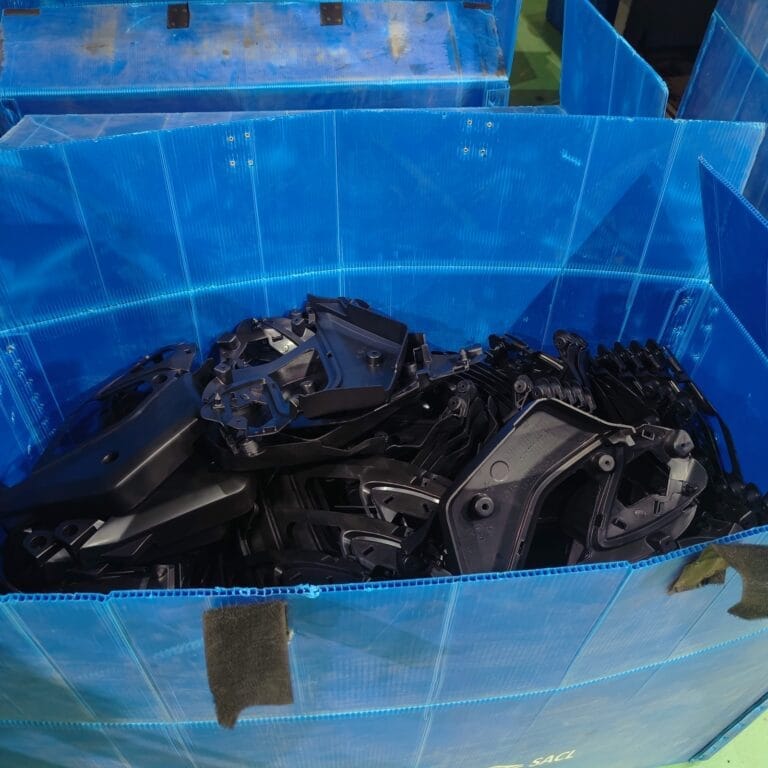
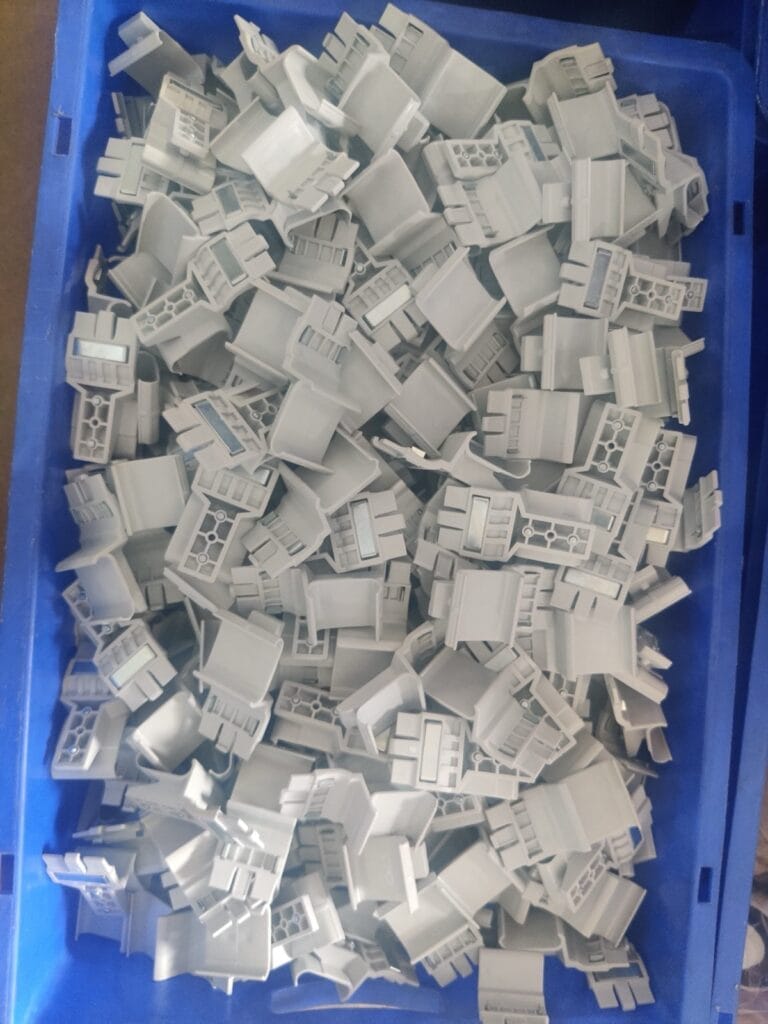
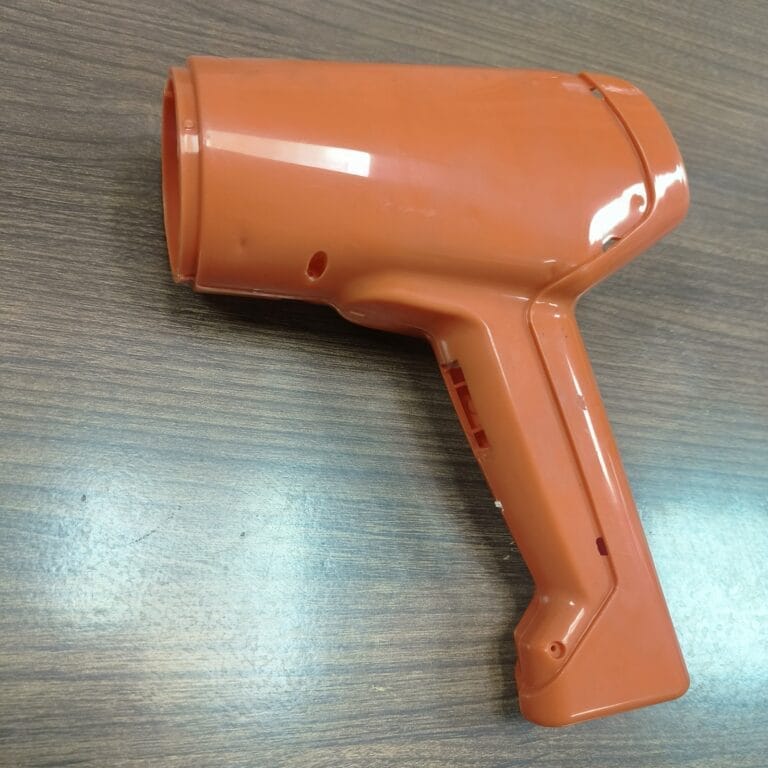
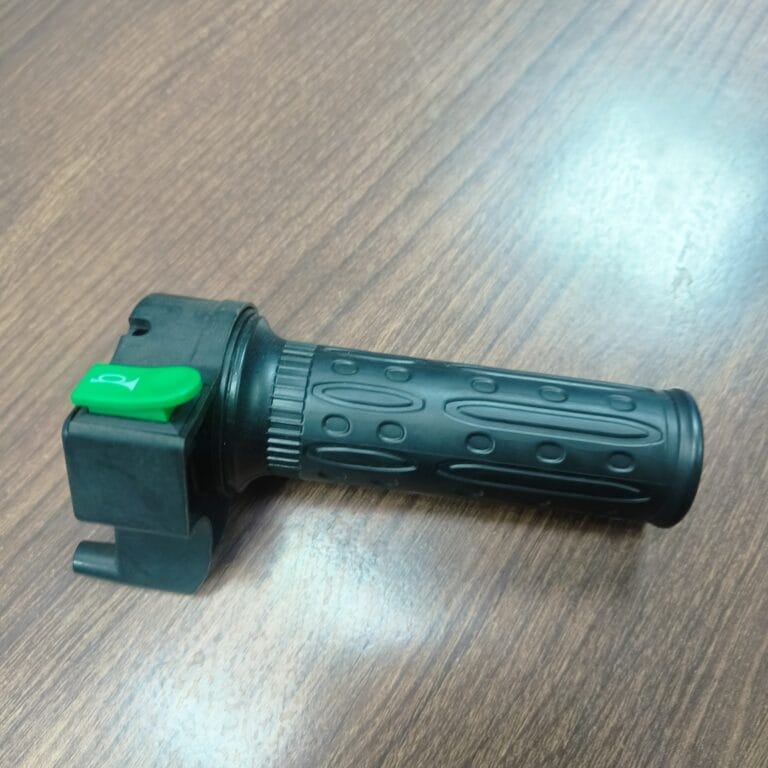
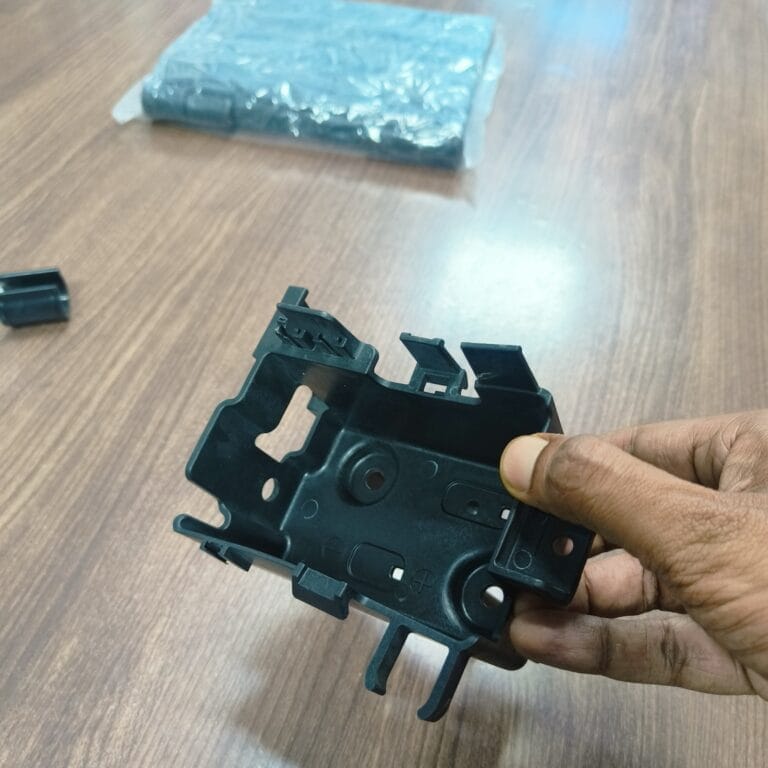
Heavy Fabrication
24000 MT/a
Materials
CS / MS, Alloy steel, Stainless Steel, etc.
Sheet Metal Fabrication
0.8 to 25 mm
Materials
Mild Steel, Stainless Steel, Aluminum, Brass, Copper, etc.
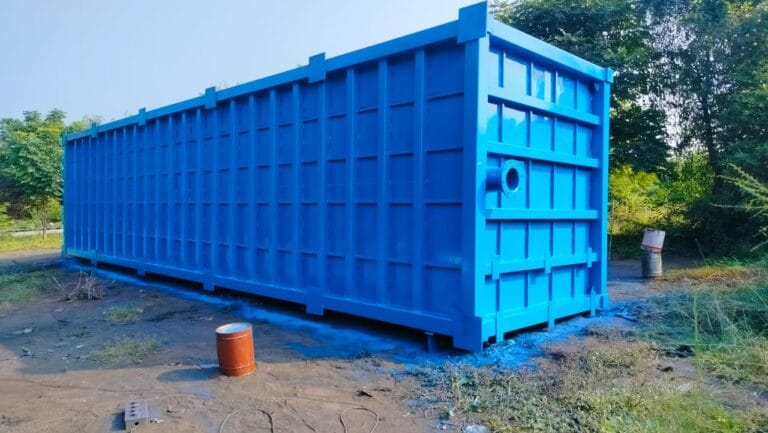
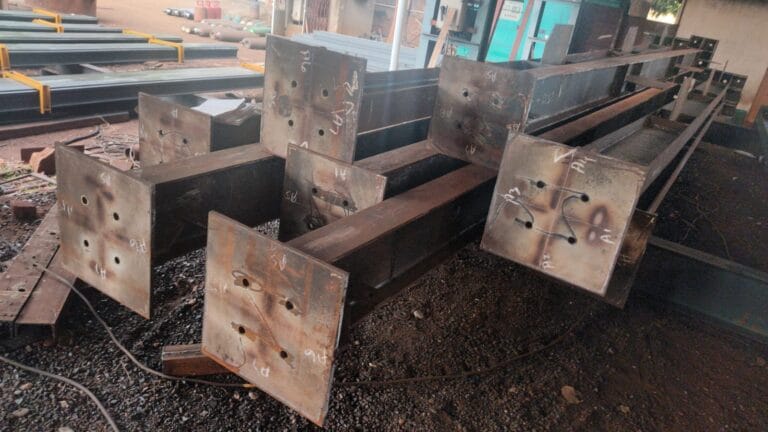
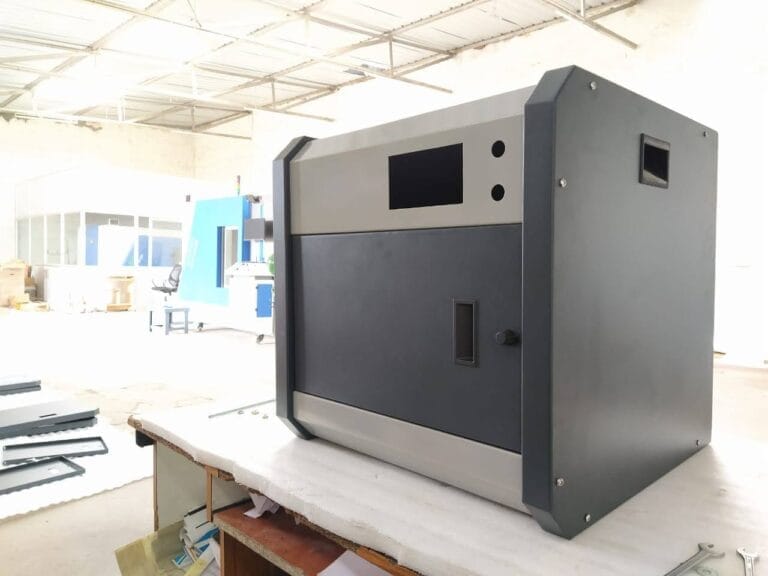
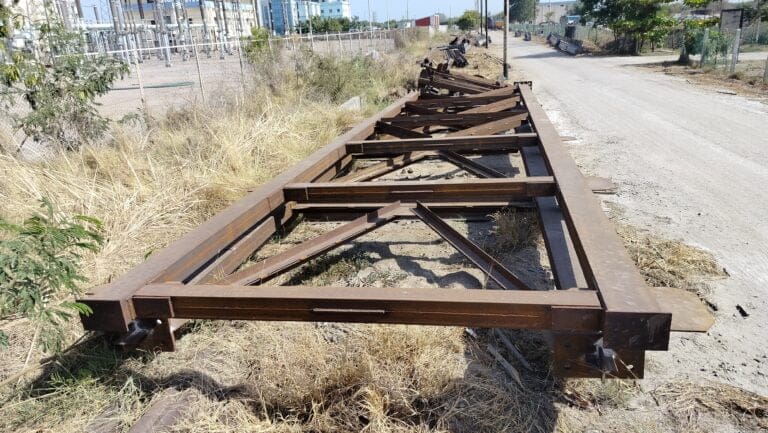
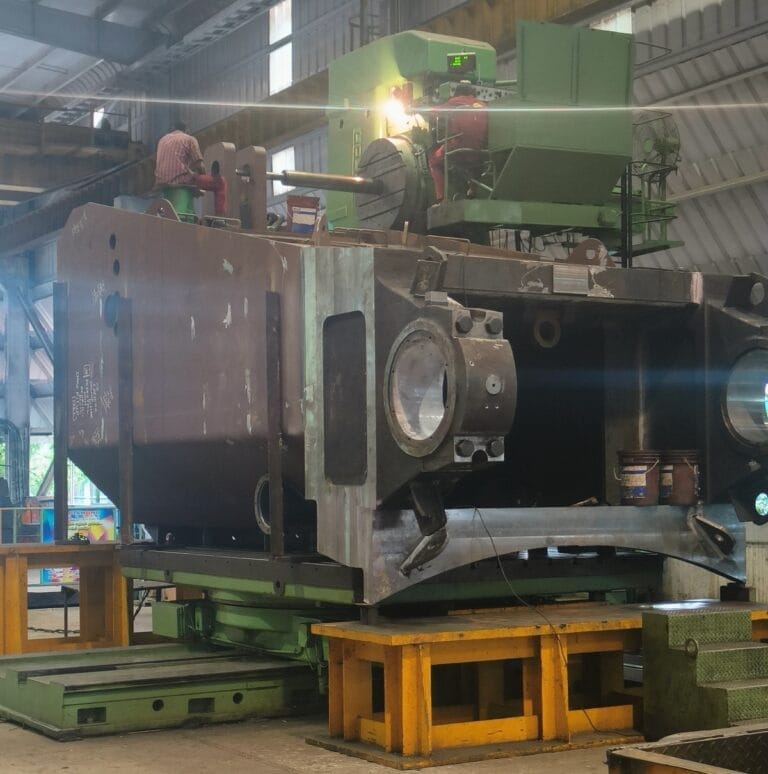
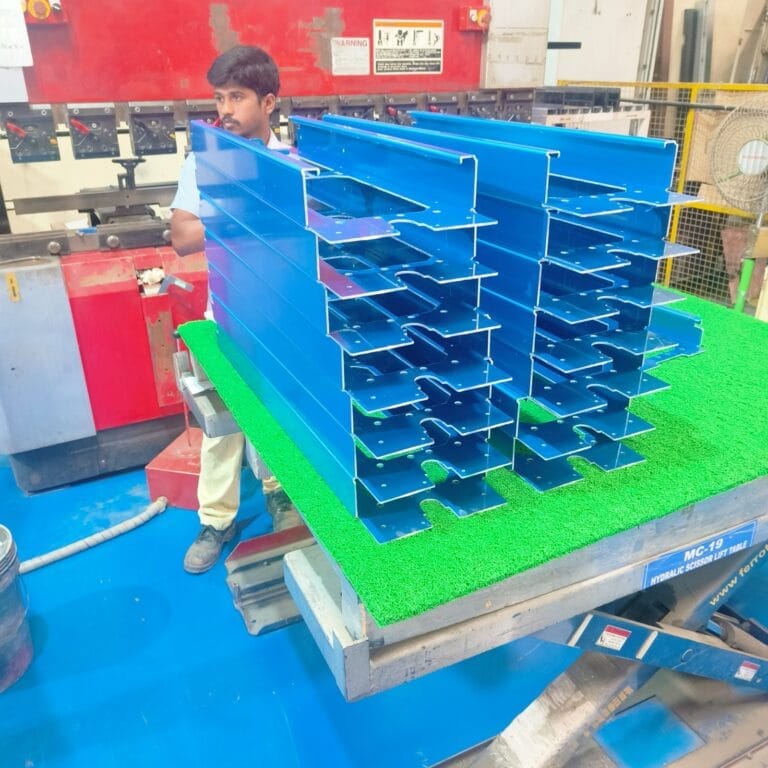
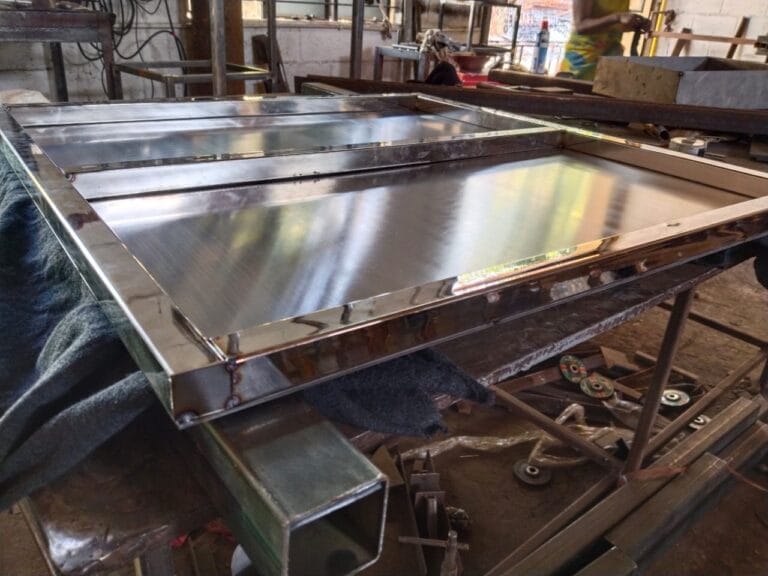
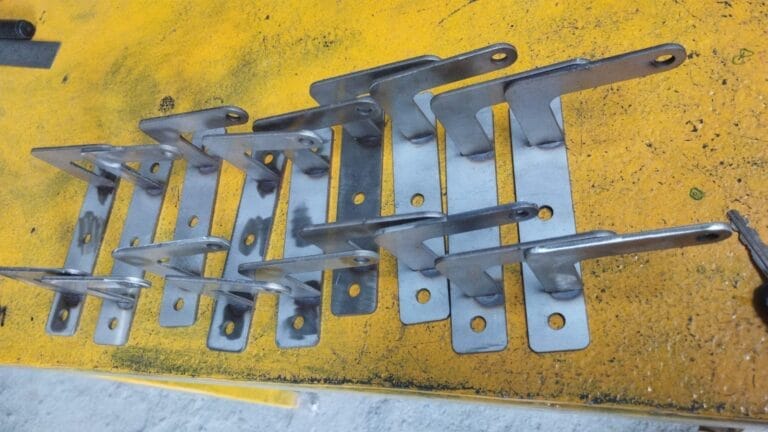
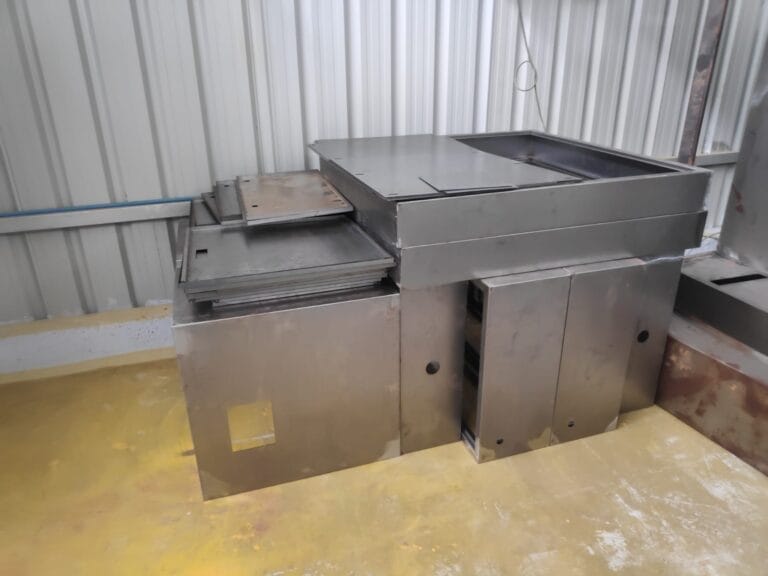
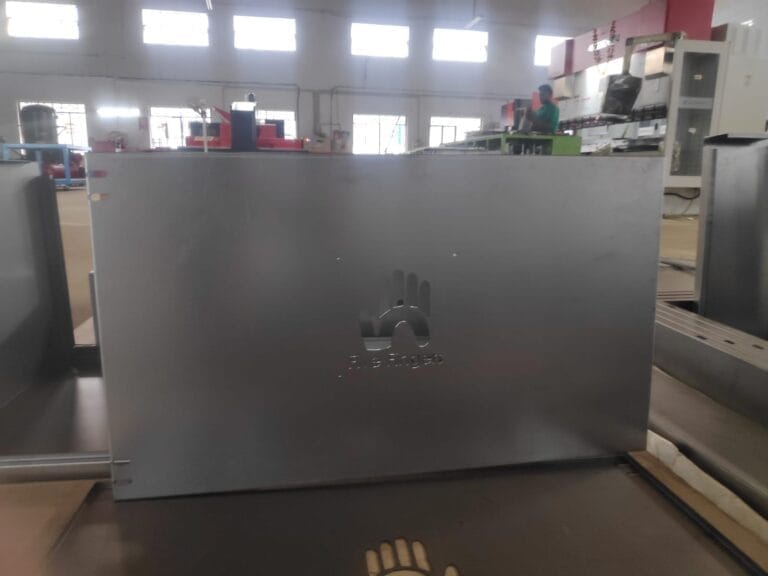
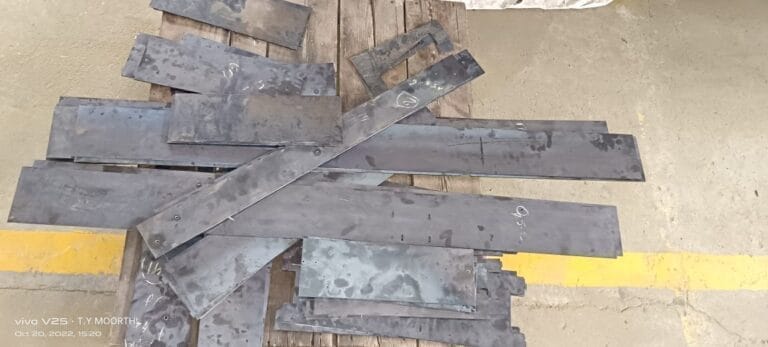
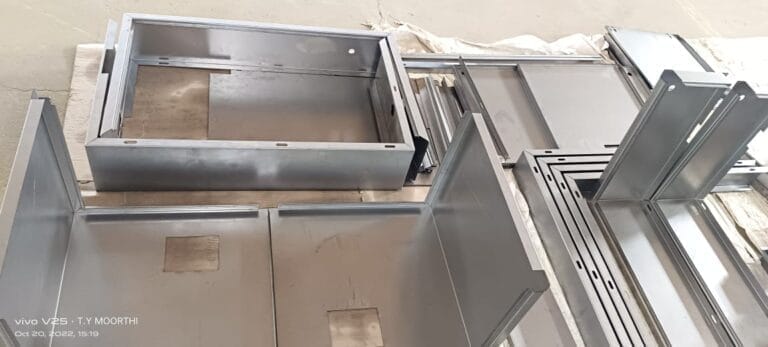
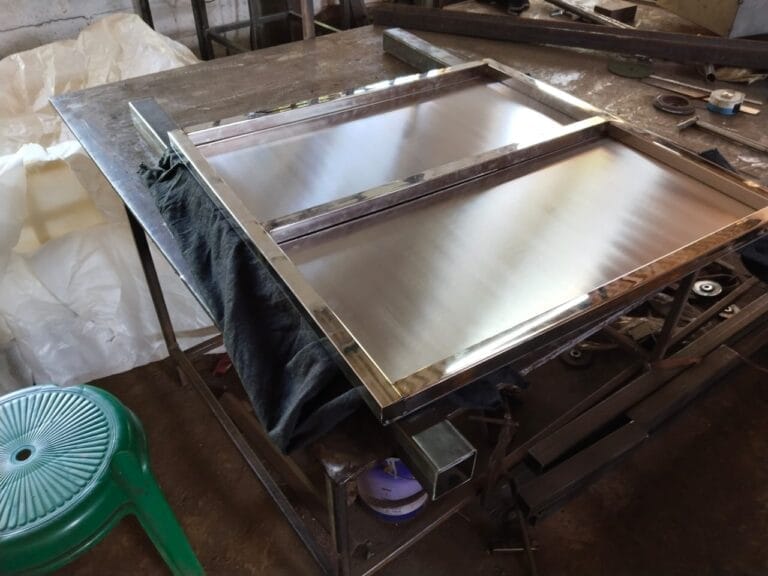
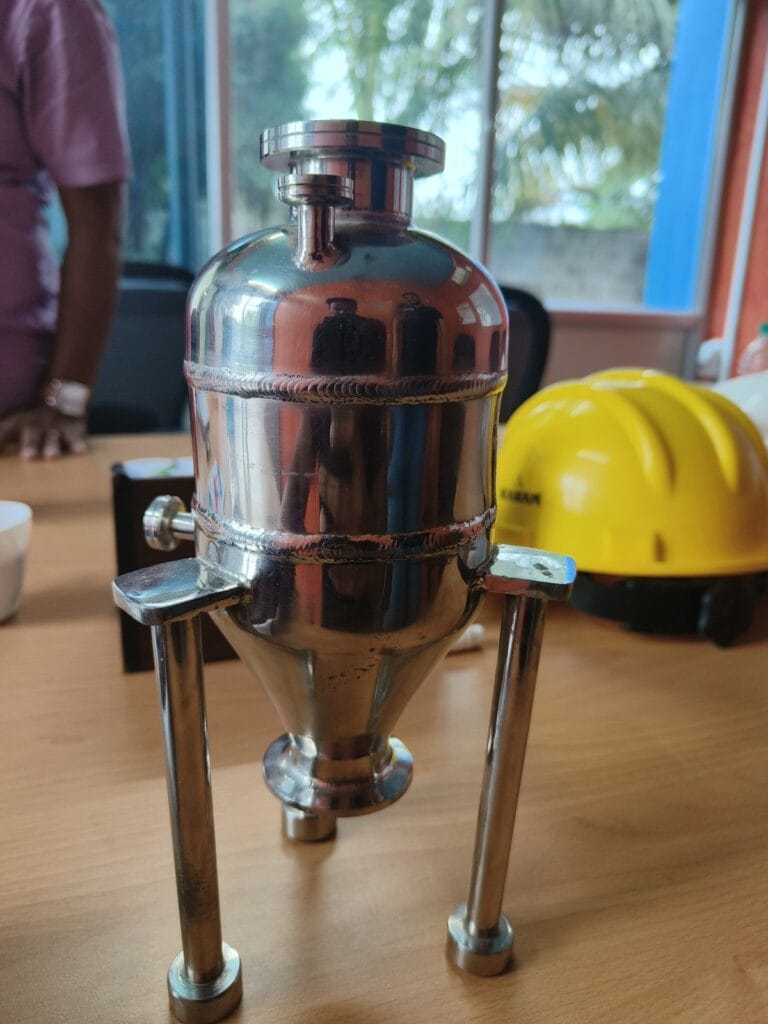
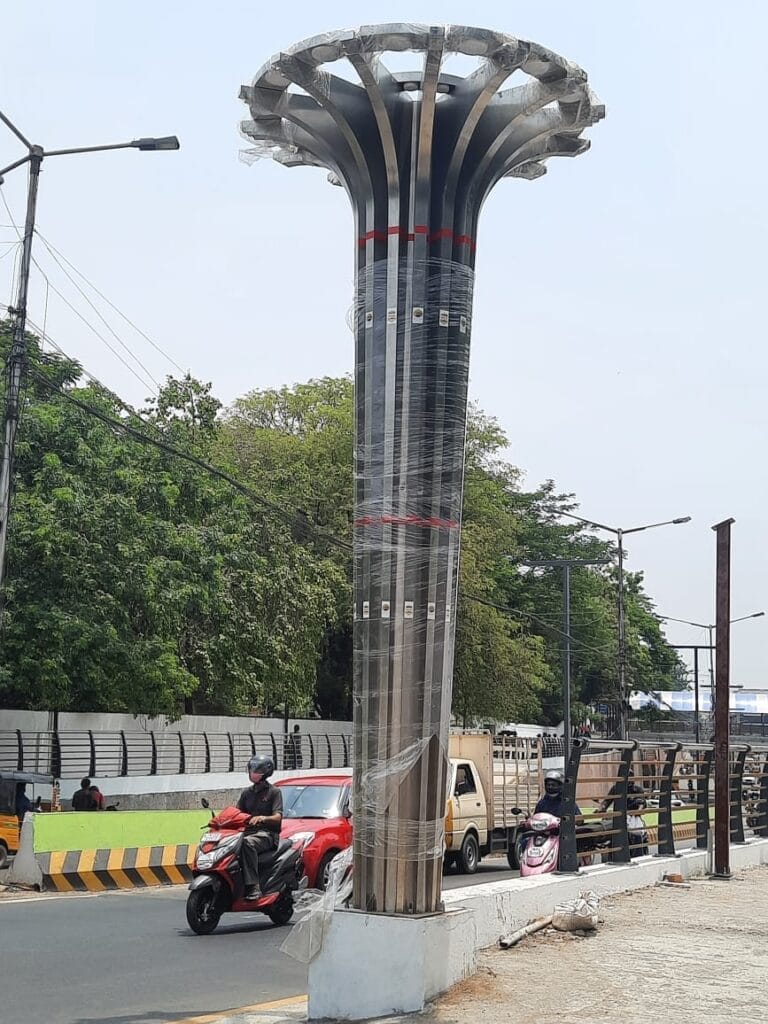
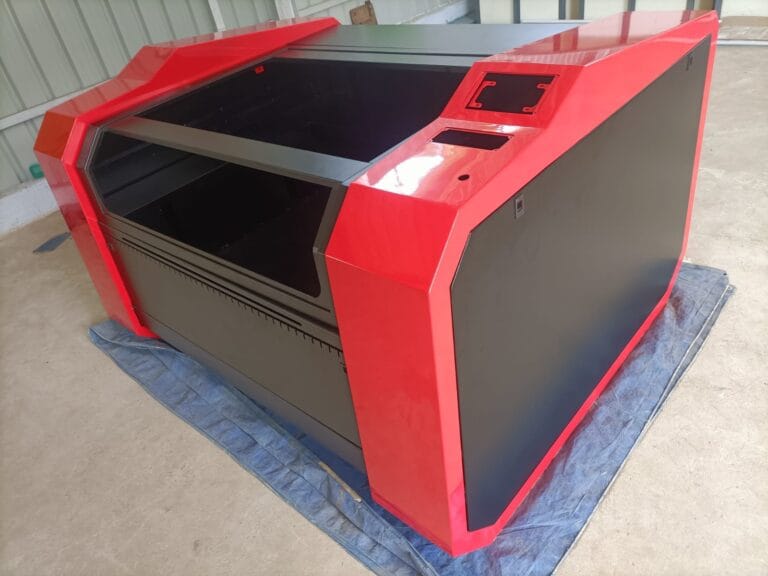
We'd love to Manufacture for you!
Submit the form below and our representative will be in touch shortly.
LOCATIONS
Global Sales Office
818, Preakness lane, Coppell, Texas, USA – 75019
Registered Office
23, 6th West Street, Balaji Nagar, Kattur, Pappakuruchi, Tiruchirappalli-620019, Tamil Nadu, India.
Operations Office
9/1, Poonthottam Nagar, Ramanandha Nagar, Saravanampatti, Coimbatore-641035, Tamil Nadu, India. ㅤ