Vacuum Casting Services
Frigate employs vacuum casting for precise, high-quality prototypes and low-volume production. We achieve optimal material consistency, minimized porosity, and tight dimensional tolerances.
Our Clients
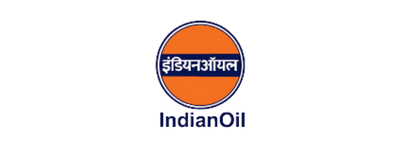
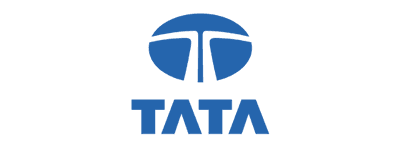
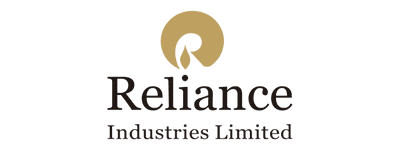

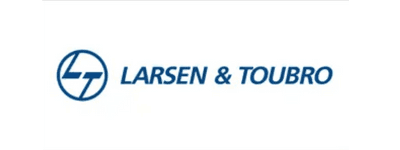
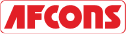

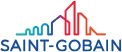
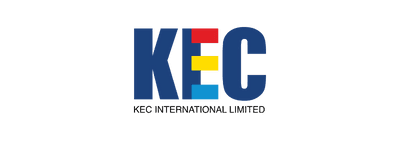

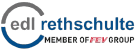

Advantages of Vacuum Casting Services
Enhanced Surface Finish
The process delivers parts with smooth, high-quality surfaces, reducing the need for additional finishing and improving visual appeal.
Faster Turnaround Time
Vacuum casting offers quick production cycles, enabling faster delivery of prototypes and low-volume parts, shortening development timelines.
Material Property Replication
Vacuum casting closely mimics the properties of final production materials, ensuring prototypes function similarly to their mass-produced counterparts.
Low-Volume Production Capability
Ideal for small production runs, vacuum casting provides a flexible solution for manufacturing limited quantities without costly molds or tooling.
Custom Vacuum Casting Services for Precision and Reliability
Custom vacuum casting provides high-precision prototypes and low-volume production with minimal porosity and tight dimensional tolerances. This method accurately replicates complex geometries and fine details, ensuring parts meet design specifications. It supports a variety of materials, including metals, plastics, and elastomers, offering flexibility for diverse applications. Vacuum casting enables rapid production, reducing lead times and accelerating development cycles. With excellent material property replication, parts produced through this process closely resemble their final production counterparts, ensuring functionality and durability in real-world applications.
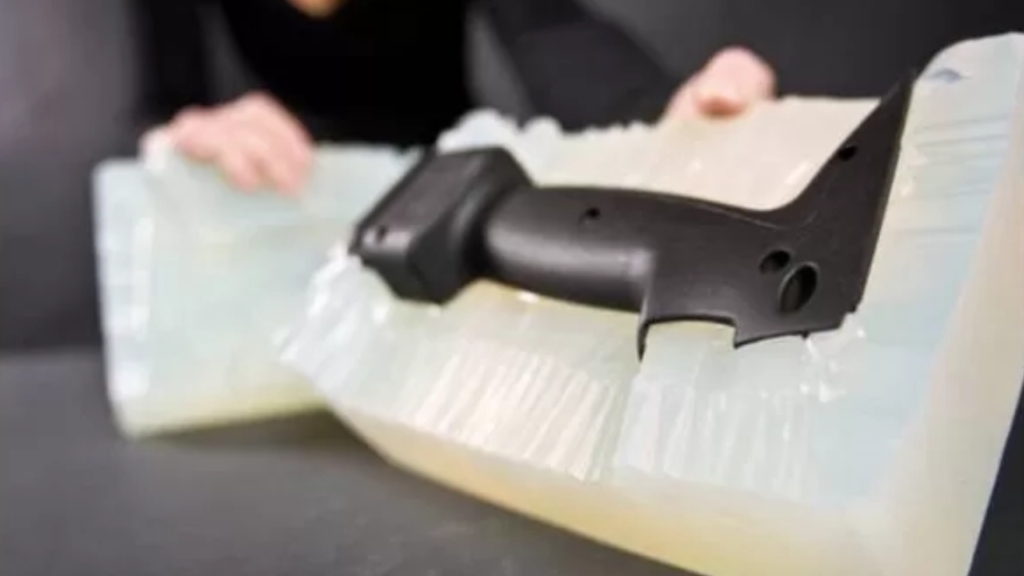
Get Your Quote Now
- Instant Quotation
- On-Time Delivery
- Affordable Cost
Our Vacuum Casting Process
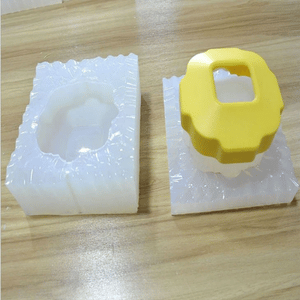
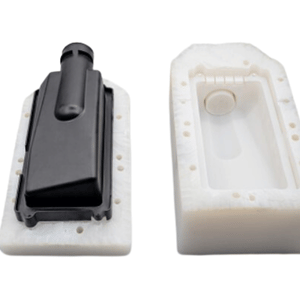
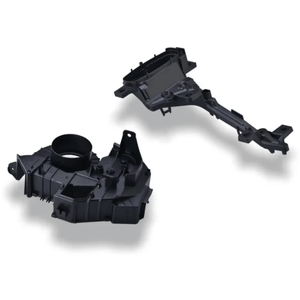
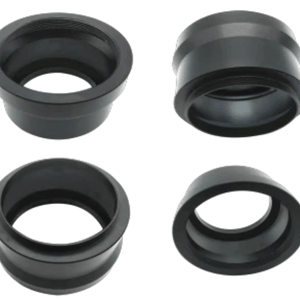
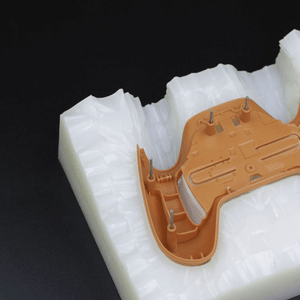
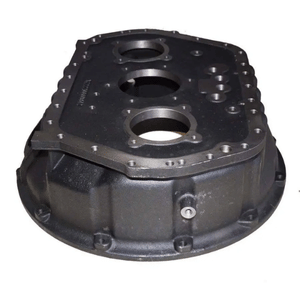
To capture the exact design details, a master pattern of the part is made, typically using 3D printing or CNC machining.
The master pattern is placed in a mold box, covered with silicone rubber, and then cured to form the mold.
The silicone mold is placed in a vacuum chamber, and the air is removed to prevent air pockets or bubbles in the mold.
The chosen material, often resin or metal, is heated and poured into the vacuum mold under low pressure, ensuring even flow and minimal defects.
The cast material can cure and solidify in the mold, accurately replicating the pattern’s shape and features.
Once cooled, the cast part is removed from the mold, and any finishing touches, such as sanding or polishing, are applied to achieve the desired surface finish.
Post-Processing Services in Vacuum Casting
Post-processing in vacuum casting enhances component quality and performance for various industries. These services refine surfaces, improve durability, and meet specific technical needs.
Gloss Level: 10 - 90%
Automotive (dashboard panels), Consumer Electronics (casings)
Hardness (Rockwell): 60-80
Medical (device housings), Consumer Goods (custom enclosures)
Hardness (Vickers): 150-300
Aerospace (interior components), Luxury Goods (decorative parts)
Hardness: 200-500 HV
Automotive (grilles, trims), Electronics (connectors)
Color Stability: ≥5 years
Consumer Electronics (buttons, covers), Fashion (accessories)
Time: 1 - 3 hours
Automotive (heat-resistant components), Industrial Equipment
Surface Finish: Ra 0.4 - 1.6 µm
Aerospace (fittings), Medical (precise instrument parts)
Electronics (sensor housings), Marine (control panels)
Laser Power: 20 - 200 W
Branding (logos, serial numbers), Consumer Goods (custom textures)
Assembly Tolerance: ±0.1 mm
Medical (multi-part devices), Automotive (complex assemblies)
Methoding in Vacuum Casting
Automotive (high-strength parts), Aerospace (complex geometries)
Aerospace (thermal-resistant components), Automotive (engine parts)
Automotive (engine blocks), Medical (housings)
Aerospace (defect-free casting), Electronics (smooth finishes)
Automotive (heat-resistant components), Medical (custom devices)
Aerospace (structural parts), Consumer Electronics (casing)
Consumer Electronics (lightweight components), Automotive (heavy-duty parts)
Medical (precision devices), Industrial Equipment (gears, housings)
Automotive (high-volume parts), Aerospace (high-precision components)
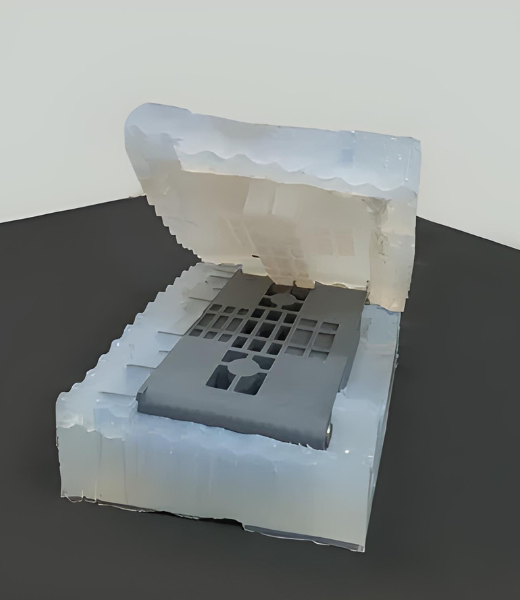
Vacuum Casting Materials
Vacuum casting provides high-precision, low-volume production with excellent detail replication. This process ensures tight tolerances and smooth surfaces for functional prototypes.
Polyurethane Resins are ideal for creating durable, high-fidelity prototypes with excellent surface finish. They are available in various hardness levels, from soft to rigid, offering versatility for both functional and aesthetic parts.
Silicone rubber is used for producing flexible components. It has high tear resistance and can endure extreme temperatures. It’s commonly chosen for parts that require elasticity, such as seals, gaskets, and soft-touch products.
Epoxies are known for their high mechanical strength, low shrinkage, and superior adhesion. They are suitable for parts requiring dimensional stability and resistance to wear and are often used in aerospace, automotive, and industrial applications.
Aluminum-based alloys provide lightweight, high-strength parts with excellent thermal conductivity. Vacuum casting with aluminum alloys is ideal for producing components that need good corrosion resistance and heat dissipation, and it is often used in automotive and aerospace.
Zinc alloys offer good casting fluidity, high strength, and resistance to corrosion. They are commonly used for precision parts requiring tight tolerances and are frequently employed in electronics, automotive, and hardware applications.
Copper-based alloys, such as bronze and brass, are selected for their high thermal and electrical conductivity. They are often used in parts that handle electrical currents or high temperatures, such as connectors, heatsinks, and industrial components.
These transparent materials provide high-impact resistance and optical clarity. Polycarbonates, in particular, offer superior strength and heat resistance, making them ideal for components used in lighting, displays, and protective covers.
Cost-Effective Solution for Small-Batch Production
Vacuum casting provides a precise and cost-effective solution for small-batch production. Unlike traditional methods that require costly tooling for low-volume runs, this technique efficiently produces high-quality parts in smaller quantities. Frigate’s vacuum casting services utilize quick-turnaround silicone molds, significantly reducing setup costs and lead times. This makes it ideal for prototypes, short production runs, and customized components while maintaining high precision and performance.
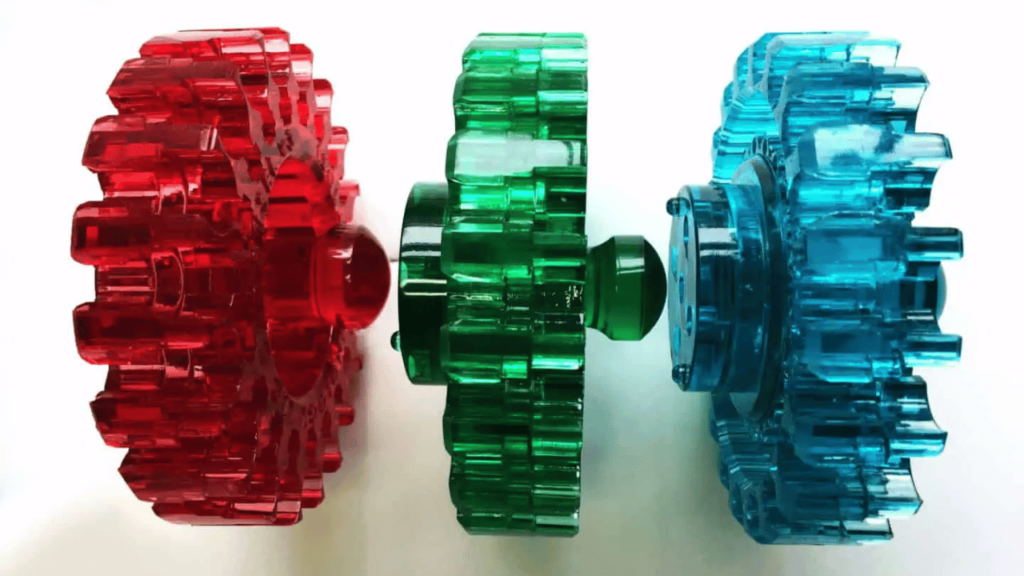
Compliance for Vacuum Casting Services
Frigate adheres to stringent industry standards for Vacuum Casting services, ensuring high precision, safety, and environmental compliance. We follow rigorous protocols to guarantee the highest product quality. Our processes align with global regulations, ensuring reliable and consistent results. Each component is manufactured with strict attention to detail, meeting performance and safety benchmarks.
Quality management system ensuring product consistency and continuous process improvement.
Environmental management system focusing on sustainable practices and reducing ecological impact.
Restriction of hazardous substances, ensuring components are free from dangerous materials.
European regulation for the safe use of chemicals, ensuring chemical safety in materials.
Aerospace standard ensuring the highest quality control and traceability for critical aerospace components.
Medical device regulation ensuring compliance with safety and performance requirements for medical-grade components.
Tonnage / Capacity in Vacuum Casting
Tonnage and capacity are critical factors in vacuum casting, influencing the precision, speed, and quality of the final components. The right parameters ensure that parts are produced efficiently, with optimal material properties and minimal defects.
Automotive (large moldings), Aerospace (high-strength parts)
Consumer Electronics (small components), Industrial Equipment (medium parts)
Medical Devices (precise parts), Aerospace (complex geometries)
Automotive (high-volume production), Consumer Goods (small enclosures)
Automotive (lightweight parts), Electronics (fine detail parts)
Aerospace (high-temperature resistant parts), Automotive (thermal components)
Medical (soft-touch components), Consumer Electronics (high-precision molds)
Aerospace (defect-free casting), Electronics (smooth finishes)
Dimensions in Vacuum Casting
Dimensions play a crucial role in vacuum casting, affecting the precision and functionality of the final components. Accurate dimensional control ensures that parts meet strict design specifications, with minimal deviations.
Aerospace (fittings), Automotive (precision parts)
Automotive (exterior trims), Consumer Electronics (buttons)
Medical Devices (housing), Industrial Equipment (components)
Electronics (small enclosures), Aerospace (thin-walled parts)
Automotive (interior parts), Consumer Electronics (housing)
Aerospace (structural components), Automotive (complex shapes)
Consumer Electronics (lightweight parts), Automotive (heavy components)
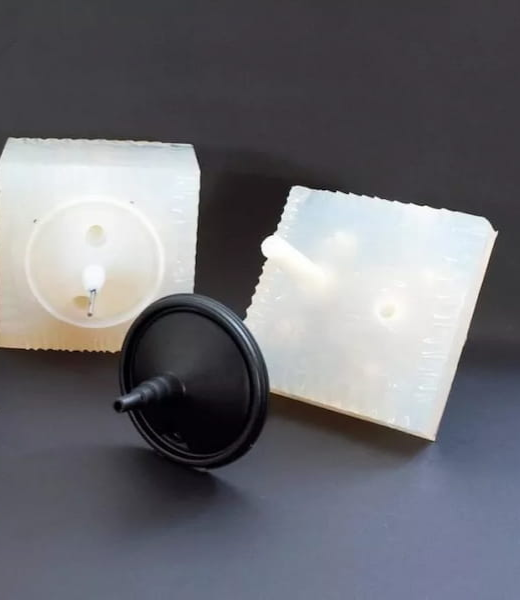
Tolerance for Vacuum Casting Services
Tolerance on the uniformity of part wall thickness.
Deviation from a perfect circle on cylindrical features.
Deviation between a surface and a reference surface, ensuring 90° angles.
Tolerance on the location of features relative to other features.
Deviation from a perfect circular cross-section in round features.
Tolerance on the location of holes, slots, and features.
Variation in thickness across the surface or wall of the part.
Deviation in angles between surfaces or features.
Deviation in the parallelism between two reference faces.
Deviation from the design model, ensuring the part matches the CAD file closely.
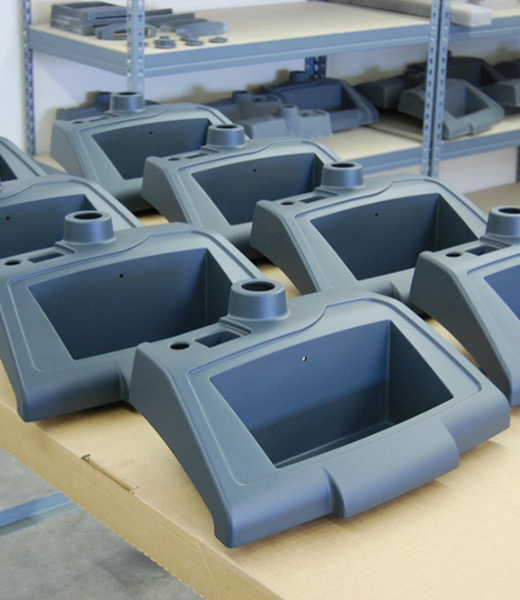
Quality Testing Standards for Vacuum Casting Services
Measures the part’s dimensions with high precision against CAD specifications.
Inspects surface for defects such as cracks, voids, or inconsistencies in texture.
Assesses the material's strength under tension and its ability to deform before breaking.
Evaluates material hardness to ensure durability and wear resistance.
Detects internal voids or bubbles that can affect part integrity and strength.
Measures heat flow and phase transitions to determine material stability at different temperatures.
Evaluates the material’s resistance to cyclic loading and its lifespan under stress.
Analyzes material to ensure compliance with alloy specifications and regulatory standards.
Determines the material’s ability to absorb impact energy without fracturing.
Determines the material's density and checks for internal voids or inconsistencies.
Measures how material dimensions change under temperature fluctuations, ensuring stability in varying environments.
Ensures the component maintains its structural integrity under pressure or vacuum conditions, without leaks.
Inspection Techniques in Vacuum Casting
Surface roughness (Ra): 0.1 - 2 µm
Gloss: 10 - 90%
Aerospace (interior panels), Automotive (exterior parts)
Tolerance: ±0.05 mm to ±0.2 mm
Medical Devices (housings), Industrial Equipment (brackets)
Resolution: 0.1 - 1 mm
Penetration Depth: 20 - 50 mm
Aerospace (structural components), Automotive (engine parts)
Frequency: 0.5 - 10 MHz
Thickness: 1 - 50 mm
Medical (implantable devices), Aerospace (critical components)
Accuracy: ±0.01 mm
Range: 500 x 500 x 500 mm
Automotive (complex geometries), Electronics (connectors)
Temperature Range: -20°C to 500°C
Electronics (power components), Aerospace (insulation parts)
Hardness (Rockwell): 60 - 80, Vickers: 150-300 HV
Automotive (machinery components), Aerospace (wear-resistant parts)
Pressure: 1 - 10 bar
Time: 1 - 10 minutes
Medical (airtight enclosures), Automotive (sensor housings)
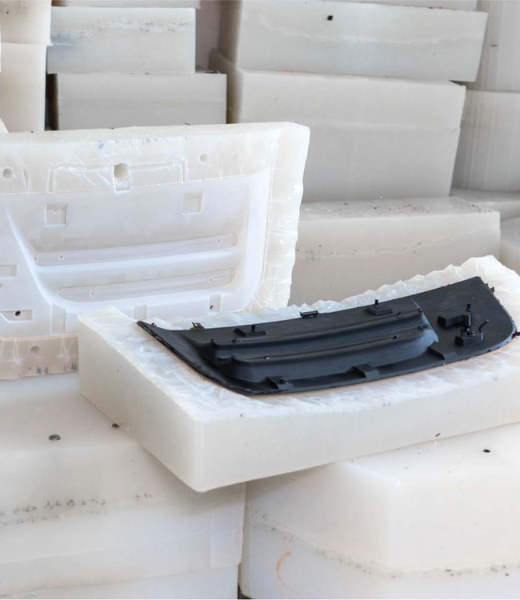
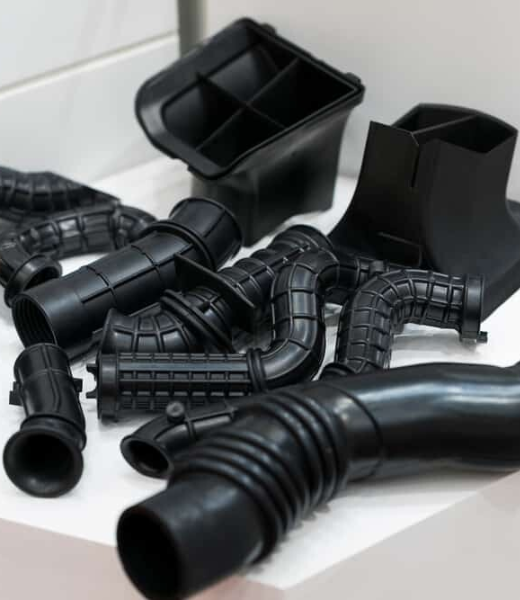
Industry Applications of Vacuum Casting
Engine blocks, Turbocharger components, Lighting housings
Aircraft brackets, Landing gear parts, Engine housings
Smartphone casings, Wearable device components, Remote controls
Prosthetic parts, Diagnostic devices, Implantable components
Hydraulic parts, Valve bodies, Pump components
Watch cases, Eyewear frames, Belt buckles
Boat fittings, Marine electronics, Hull components
Armor plating, Tactical equipment housings, Sensor covers
Wind turbine components, Generator housings, Battery casings
Robotic arms, Precision gears, Actuators
Antenna casings, Signal boosters, Base station housings
Optimizing Consumer Product Manufacturing with Vacuum Casting Technology
Balancing production efficiency and part quality can challenge consumer product manufacturing. Vacuum casting eliminates this issue by enabling the precise, low-volume production of complex components with reduced lead times. This process allows for creating detailed and accurate prototypes that simulate real-world performance, reducing the need for time-consuming post-processing. With the ability to handle a wide variety of materials, vacuum casting ensures that every component produced meets both functional and aesthetic requirements.
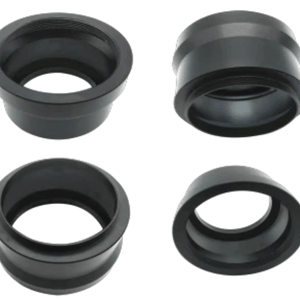
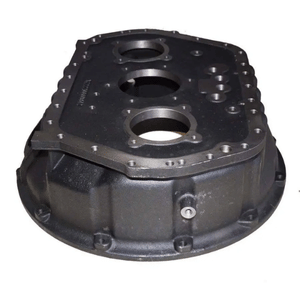
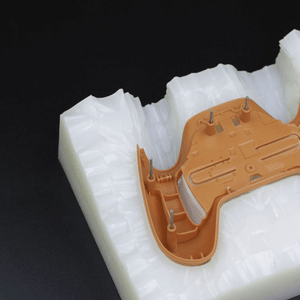
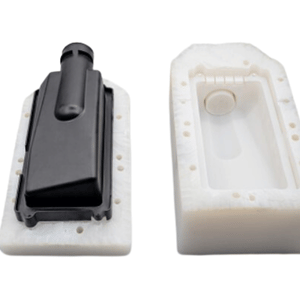
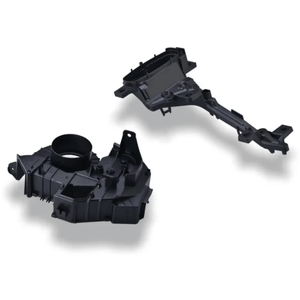
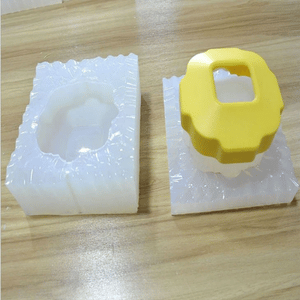
Industries We Serve
- Solid Progress
What You Gain with Us
We make your profitability and operations easier with practical approach.
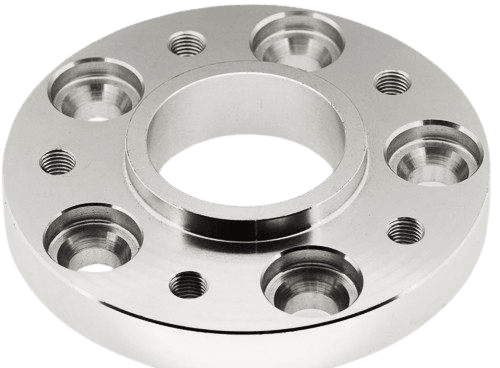
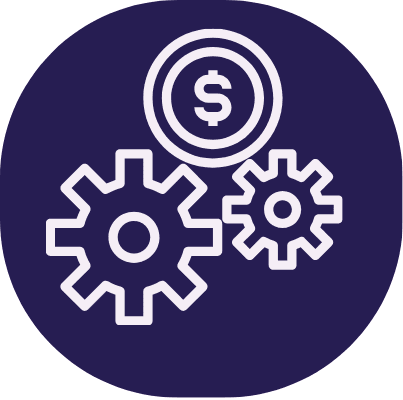
↓ 7-8%
OPS COST
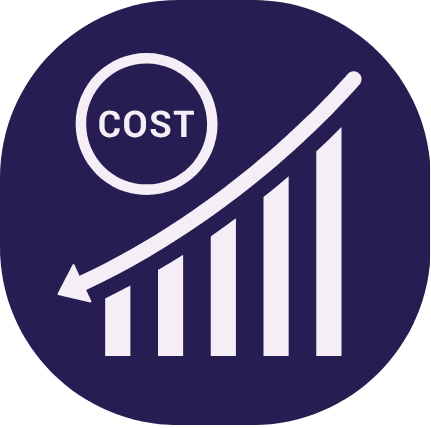
↓ 2-3%
COGM
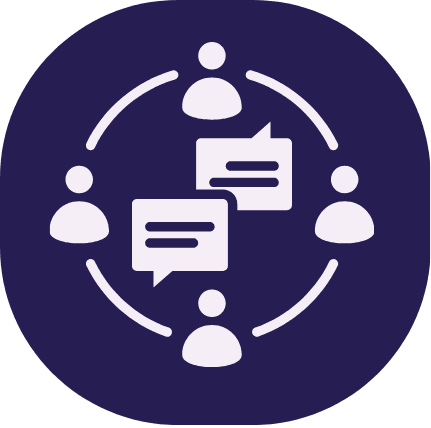
3X
Aggregation
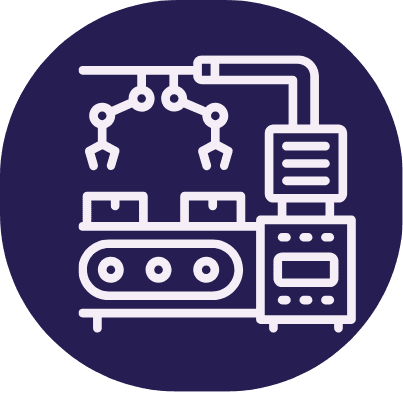
↑ 25%
Machinery Utilisation
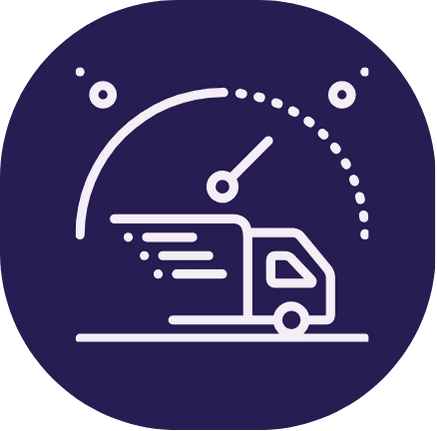
↓ 50%
Expedition
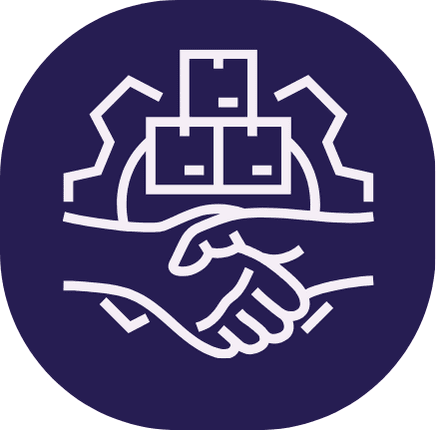
↑ 30%
Frigater Revenue
- Solid Progress
Our Manufacturing metrics
Frigate brings stability, control, and predictable performance to your sourcing operations through a structured multi-vendor system.
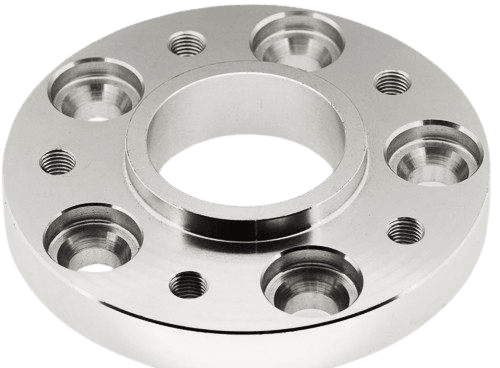
2.8X
Sourcing Cycle Speed
Frigate’s pre-qualified network shortens decision time between RFQ and PO placement.
94%
On-Time Delivery Rate
Structured planning windows and logistics-linked schedules improve project-level delivery reliability.
4X
Multi-Part Consolidation
We enable part family batching across suppliers to reduce fragmentation.
22%
Quality Rejection Rate
Multi-level quality checks and fixed inspection plans lower non-conformities.
30%
Procurement Costs
Optimized supplier negotiations and bulk order strategies reduce your overall sourcing expenses.
20%
Manual Processing Time
Automation of sourcing and supplier management significantly reduces time spent on manual tasks.
Achieving Consistent, High-Quality Surface Finishes
Achieving consistent surface quality without extensive post-processing is a common challenge with conventional casting. Vacuum casting, however, delivers superior surface finishes due to the controlled vacuum environment that eliminates air bubbles and other defects. This results in parts with minimal surface imperfections, reducing the need for additional finishing work. Frigate’s vacuum casting process ensures high-quality surfaces, even for complex geometries, allowing parts to meet exacting standards with minimal additional effort or time spent on post-production.
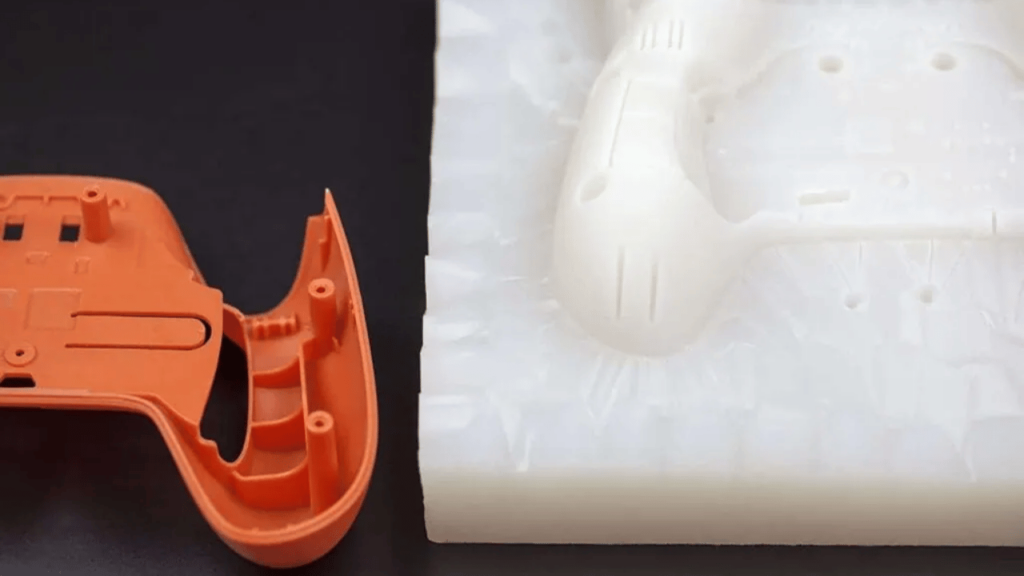
Get Clarity with our Manufacturing Insights
- Satisfied Customers
Excellence You Can Trust
Trusted by Fortune 500 companies for high-precision CNC machining, tight tolerances, and superior quality.
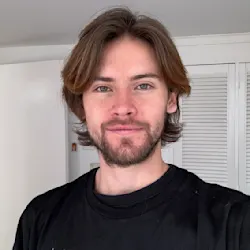
“Quick turnaround and solid quality.”
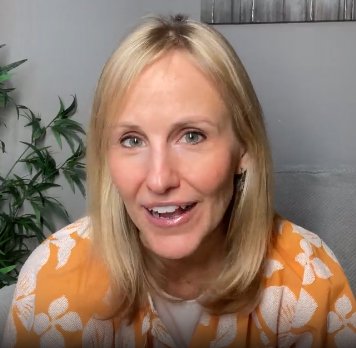
“The instant quote tool saved us time, and the parts were spot-on. Highly recommend Frigate!”
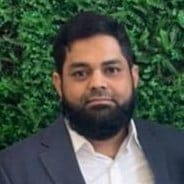
“I would strongly recommend Frigate to anyone who wants to do Rapid Prototyping, and take their ideas to manufacturing. One firm doing all kinds of Product Development!”

“Great service, fair price, and the parts worked perfectly in our assembly.”
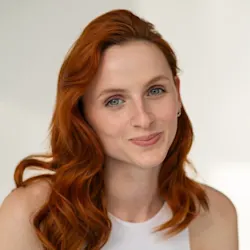
“Top-notch machining and fast shipping. Very satisfied with the results.”

“The next disruption is happening in Prototyping & Manufacturing on-demand and Frigate is leading the way!I personally believe the Frigate's way of IIOT enabled cloud platform with Al.”
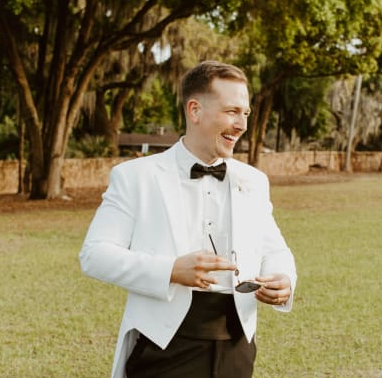
“Frigate delivered high-quality parts at a competitive price. The instant quote tool is a huge plus for us!”
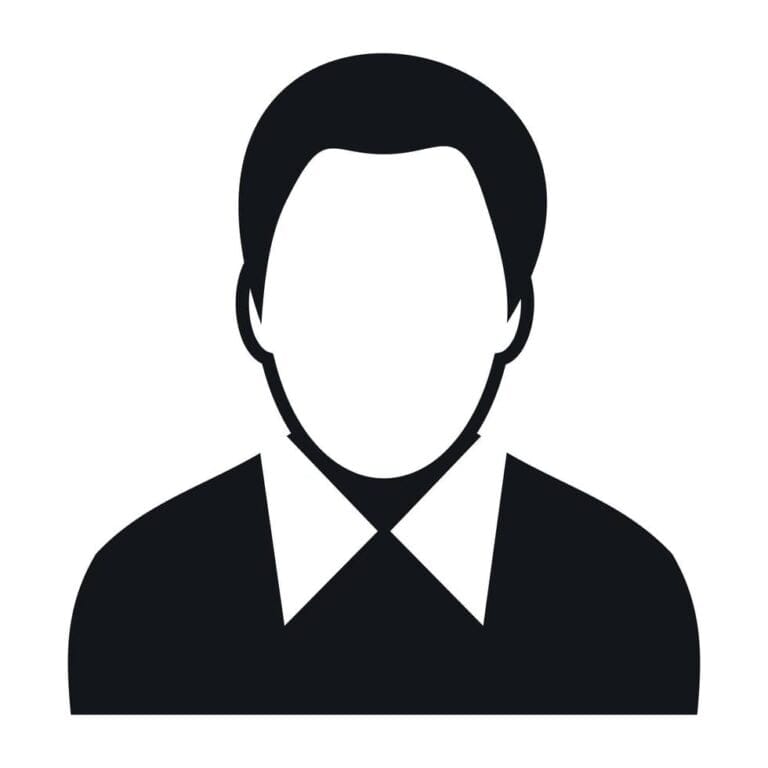
“We appreciate the precision and quality of the machined components in the recent delivery—they meet our specifications perfectly and demonstrate Frigate’s capability for excellent workmanship.”
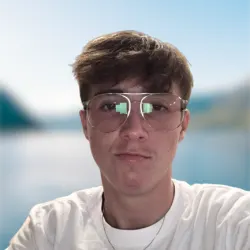
“Flawless execution from quote to delivery.”
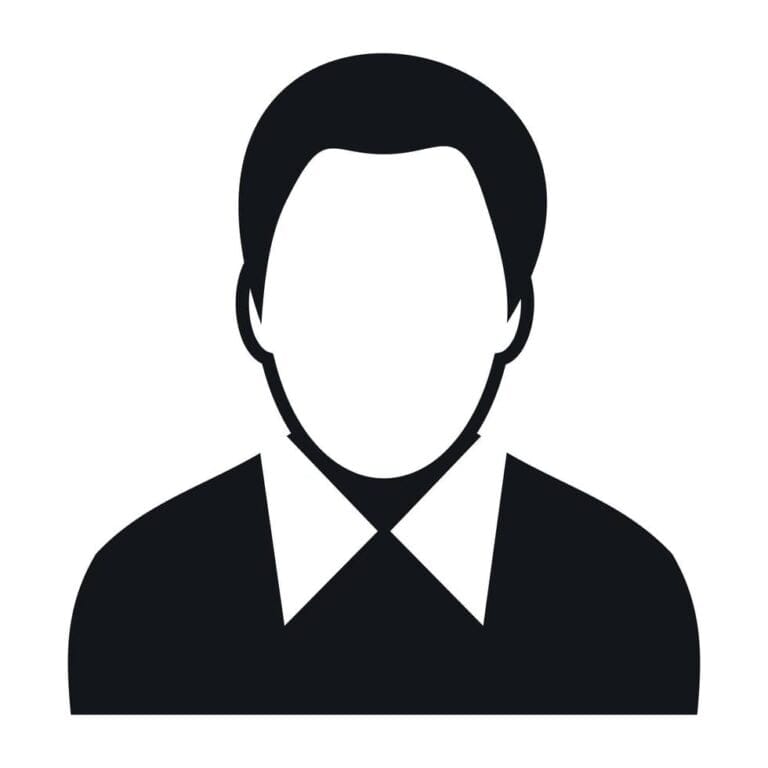
“I am absolutely happy to work with supplier like Frigate who were quite proactive & result oriented . Frigate has high willingness team who has strong know how & their passion towards the products & process were absolutely thrilling.”
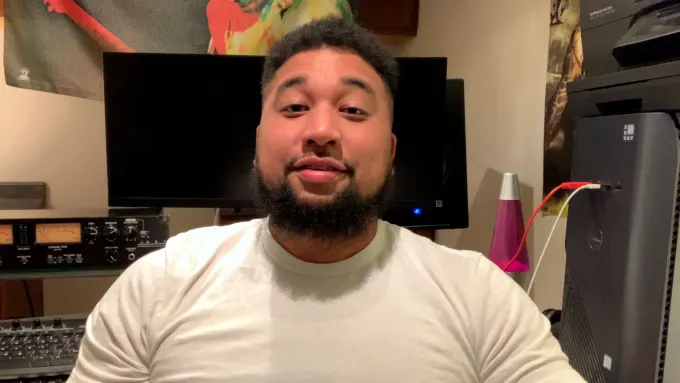
“The precision on these parts is impressive, and they arrived ahead of schedule. Frigate’s process really stands out!”
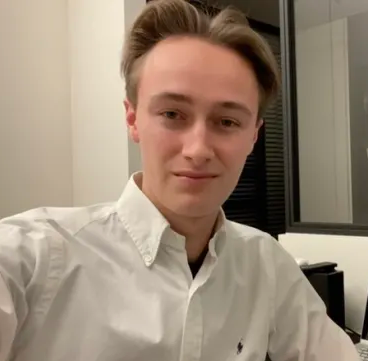
“Parts were exactly as spec’d, and the instant quote made budgeting a breeze.”
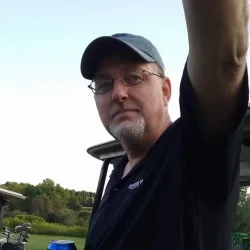
“Good value for the money.”

“The finish was perfect, and the team was easy to work with.”
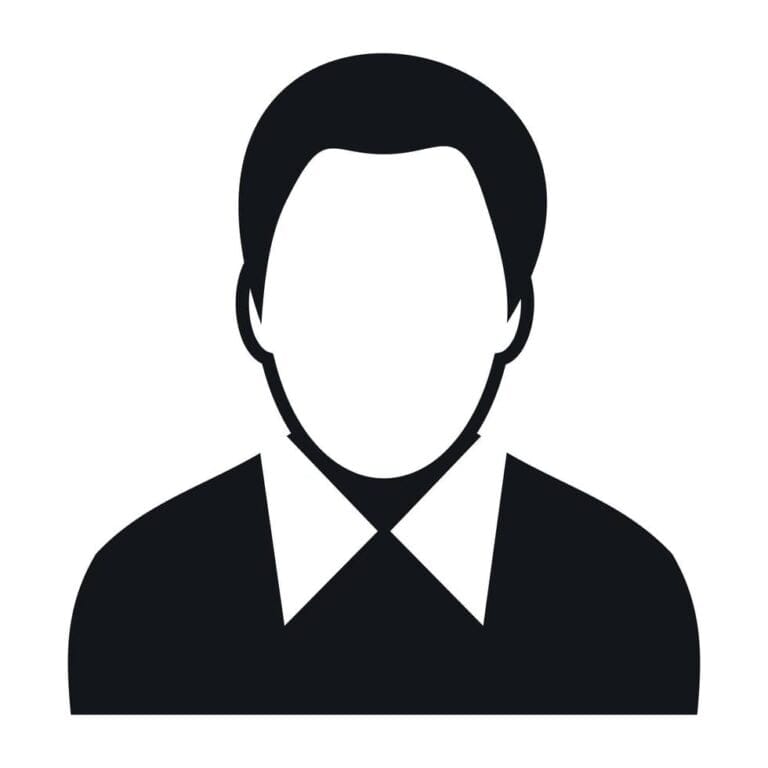
“Working with Frigate has been great. Their proactive, results-driven approach and expertise shine through in every project. It's been a pleasure collaborating with them.”
Having Doubts? Our FAQ
Check all our Frequently Asked Question
Vacuum casting maintains consistent material properties using precise temperature control during material pouring and curing. The vacuum environment eliminates air pockets, ensuring uniform density and mechanical characteristics in each batch.
The vacuum environment removes trapped gases, leading to denser, stronger materials with enhanced mechanical properties. This results in improved tensile strength, impact resistance, and reduced brittleness, which is critical for parts subjected to stress.
Yes, vacuum casting can closely replicate metal properties using specialized resins or metal-filled materials. For metals like aluminum or zinc, casting can achieve near-identical strength and thermal conductivity, making prototypes functionally representative of final production parts.
Combining the vacuum chamber and controlled curing ensures minimal shrinkage and precise mold formation. This results in tight tolerances (often within ±0.1mm), making vacuum casting ideal for parts that require perfect fit and functionality.
Material selection is crucial in vacuum casting, directly influencing the part’s strength, flexibility, and durability. Advanced resins and alloys are chosen based on their specific mechanical properties, ensuring the final part meets the performance criteria for each unique application.
We'd love to Manufacture for you!
Submit the form below and our representative will be in touch shortly.
LOCATIONS
Global Sales Office
818, Preakness lane, Coppell, Texas, USA – 75019
Registered Office
10-A, First Floor, V.V Complex, Prakash Nagar, Thiruverumbur, Trichy-620013, Tamil Nadu, India.
Operations Office
9/1, Poonthottam Nagar, Ramanandha Nagar, Saravanampatti, Coimbatore-641035, Tamil Nadu, India. ㅤ
Other Locations
- Bhilai
- Chennai
- Texas, USA