Have you ever wondered why some metal parts are strong yet light? Or why do some products last longer than others? These questions are crucial for manufacturers who want to make high-quality products. Aluminum casting is a popular method for creating strong and lightweight parts. But what exactly is aluminum casting, and how can it solve common problems manufacturers face?
In today’s competitive world, manufacturers are pressured to produce parts that meet high standards quickly and cost-effectively. This blog explores aluminum casting, its processes, and how it can help manufacturers overcome their challenges.
Aluminum Alloy Selection
The first step in aluminum casting is choosing the right aluminum alloy. Aluminum alloys come in different types, each with unique properties.
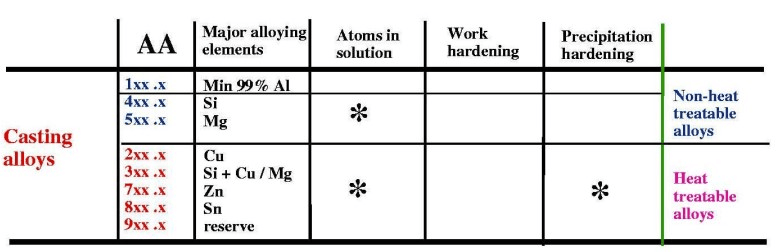
Properties of Aluminum Alloys
Different alloys have different strengths, flexibility, and resistance to corrosion. The properties of aluminum alloys are largely determined by their chemical composition and microstructure. Here are some common alloys used in aluminum casting:
- 6061 Alloy – This alloy contains magnesium and silicon. It is known for its good mechanical properties and weldability. It has a tensile strength of about 290 MPa and is often used in structural applications, such as frames and supports.
- 356 Alloy—This silicon and magnesium alloy is known for its excellent casting characteristics. It has good fluidity, which helps it fill molds accurately, and a tensile strength of about 240 MPa. It is widely used in automotive and aerospace components.
- 413 Alloy – This alloy is particularly suited for high-temperature applications. It maintains strength at elevated temperatures, making it ideal for engine components. It has a tensile strength of about 310 MPa.
Understanding these properties is vital because they affect the material’s performance in the final product. Making the right choice can lead to better product performance and lower production costs.
Alloy Designation Systems
The Aluminum Association uses a numbering system to identify aluminum alloys. The first digit of the alloy number indicates the main alloying element. For example, 1 indicates a pure aluminum alloy, while 2 indicates an alloy primarily composed of copper. The second digit indicates the specific alloy within that group.
Understanding this system helps manufacturers communicate effectively and use the correct materials for their applications.
Impact of Alloy Selection on Casting Performance
The choice of alloy significantly affects the casting process. Different alloys have varying melting points and fluidity levels. For instance, an alloy with low fluidity may not fill the mold properly, leading to defects like incomplete casting or porosity. Therefore, manufacturers must balance strength, weight, and casting characteristics when selecting an alloy.
For example, 356 alloy is preferred for intricate castings due to its excellent fluidity, while 6061 alloy might be selected for structural components due to its higher strength and weldability.
Casting Process Methodologies
Once the alloy is selected, the next step is choosing a casting method. Different methods have advantages and disadvantages, and selecting the right one can impact production efficiency and product quality.

Die Casting
It is a fast and efficient method commonly used in aluminum casting. There are following two main types of die casting:
- Cold Chamber Die Casting – This method suits high melting point alloys. In this process, the molten aluminum is poured into a chamber before being injected into the mold. It minimizes contamination and is ideal for alloys like 356. This process allows for better control over the metal flow and is used for parts requiring higher strength.
- Hot Chamber Die Casting – This method is used for alloys with lower melting points, like some zinc alloys. In this casting, the molten metal is held in a chamber attached to the mold, allowing for faster production cycles. However, this method can lead to contamination due to the metal’s exposure to the environment.
Die casting is ideal for mass production because it offers high precision & can produce complex shapes. However, the initial cost of creating molds can be high, which might be a barrier for small production runs.
Sand Casting
It is one of the oldest and most versatile aluminum casting methods. In this process, a mold is made from sand. The two main types of sand used are:
- Green Sand is a mixture of sand, clay, and water. It is easy to mold and provides good flexibility, but it may lead to a lower surface finish and dimensional accuracy.
- Resin-Bonded Sand – This option uses resin to bind sand particles together, creating a more durable mold. It can produce finer details and better surface finishes than green sand, making it suitable for complex shapes.
Sand casting is cost-effective for small production runs and offers flexibility in design. However, it may not achieve the same precision as die casting, which can be a downside for manufacturers seeking high-tolerance parts.
Investment Casting
It is also known as lost-wax casting and is known for its high precision. A wax pattern is created and covered in a ceramic shell. The shell is then heated, causing the wax to melt away and leaving mold for the molten aluminum.
This method is excellent for producing intricate designs and thin-walled parts. Due to the high level of detail achievable through this process, the final products often require less machining. However, it can be more time-consuming and expensive than other methods, making it more suitable for low-volume, high-value components.
Quality Control and Defect Management
Quality control is critical in aluminum casting. Defects can lead to product failures and unhappy customers.
Common Defects in Aluminum Casting
Common defects in aluminum casting include:
- Porosity occurs when air pockets are trapped inside the metal during the cooling process. Porosity weakens the part and can lead to failure under stress.
- Inclusions – These are foreign materials mixed with aluminum, which can create weaknesses in the final product. Inclusions can come from sand, slag, or other contaminants.
- Warping—Warping happens when the shape of the part changes during cooling. It can occur if the cooling rate is uneven or if the mold design is not optimal.
Understanding these defects is essential for manufacturers as it helps them take proactive steps to prevent them.
Inspection Techniques
To ensure quality, manufacturers can use non-destructive testing (NDT) methods. NDT techniques include:
- Ultrasonic Testing – It uses sound waves to detect internal flaws. By sending sound waves through the material, technicians can identify areas of weakness or voids.
- Radiography – It uses X-rays to visualize the internal structure of the casting. It can reveal porosity and other internal defects.
- Dye Penetrant Testing – Involves applying a dye to the surface of the casting. The dye seeps into cracks or voids, making them visible for inspection.
These inspection methods help identify defects early, saving time and resources while ensuring high product quality.
Statistical Process Control (SPC)
Statistical Process Control (SPC) is a method for monitoring and controlling the casting process. It involves using statistical techniques to analyze data and identify trends. These are used to track variations in the casting process. They help manufacturers determine if the process is stable and if it remains within specified limits.
Using SPC can lead to fewer defects and higher-quality products by providing a systematic approach to quality management.
Process Optimization Techniques
Optimizing the casting process is essential for efficiency and quality.
Thermal Analysis
Thermal analysis helps manufacturers understand how aluminum solidifies. They can adjust the casting process to minimize defects by studying cooling curves and solidification times. Manufacturers can adjust parameters to prevent defects like warping or cracking by monitoring how quickly a casting cools. If a part cools too quickly, it may create internal stress leading to deformation.
Understanding thermal dynamics can significantly improve product quality. For example, a cooling rate that is too rapid can result in porosity or other defects, while an optimal cooling rate can help achieve a uniform microstructure.
Mold Design and Simulation
Advanced simulation software can help manufacturers design molds effectively. Software like MAGMASOFT or ProCAST allows them to visualize the casting process before production.
- Identifying Potential Defects—Simulation helps identify potential defects in the mold design and allows adjustments to optimize the flow of molten metal.
- Optimizing Gate and Runner Systems – The design of gates and runners influences how well the molten aluminum fills the mold. Proper design can reduce turbulence and improve the filling process, leading to higher-quality parts.
Good mold design reduces the risk of defects and improves production efficiency.
Process Parameter Optimization
Key parameters like injection speed, temperature control, and cooling rates can significantly impact the final product.
- Injection Speed: The speed at which molten aluminum is injected into the mold can affect how well it fills the cavity. Too fast can lead to turbulence, while too slow can cause incomplete filling.
- Temperature Control: It is crucial to maintain the correct temperature of the molten aluminum. If the metal is too cool, it may not flow properly, and if it’s it’s, it can degrade its properties.
By conducting experiments (Design of Experiments, or DOE), manufacturers can find the best settings for their processes. For instance, adjusting the injection speed can help minimize porosity and improve the overall quality of the cast parts.
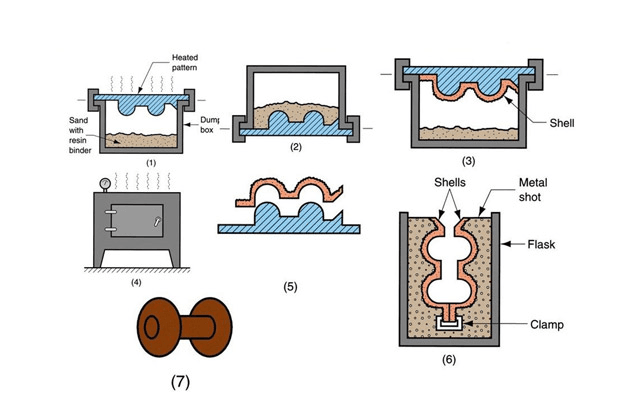
Environmental and Regulatory Compliance
Manufacturers must consider the environment and regulations in their casting processes.
Environmental Impact of Aluminum Casting
Aluminum casting can produce emissions and waste, so manufacturers should aim to reduce their environmental footprint. Aluminum is highly recyclable and can be reprocessed many times without losing quality, reducing the need for raw materials and minimizing waste. According to the Aluminum Association, recycling aluminum saves 90% of the energy required to produce new aluminum from ore.
Implementing effective waste management practices can help reduce pollution. This includes proper disposal of sand, scrap aluminum, and other byproducts from the casting process.
Compliance with Industry Standards
Manufacturers must adhere to industry standards like ISO 9001 and ASTM. These standards ensure quality and consistency in production. Compliance is vital for maintaining customer trust and market competitiveness.
For example, ASTM B108 provides specifications for aluminum alloy castings, ensuring that the materials used meet specific performance criteria.
Conclusion
Aluminum casting is a powerful process for creating strong and lightweight parts. Manufacturers can overcome common challenges by understanding the technical aspects of alloy selection, casting methods, quality control, and process optimization. Leveraging technology, optimizing processes, and building strong supplier relationships can lead to success in manufacturing.
By focusing on the right materials, methods, and partnerships, manufacturers can produce the best aluminum parts for their applications. Let Frigate be your partner in navigating the complexities of aluminum casting.