Have you ever wondered why some plastic parts fit perfectly while others don’t? This difference often comes down to injection molding tolerances, which are the specific limits set during the manufacturing process. If the tolerances aren’t just right, parts can fail. Imagine buying a toy that doesn’t fit together properly or a car part that doesn’t work. For businesses, this means unhappy customers and wasted money. Understanding injection molding tolerances can help prevent these problems.
In this blog, we will explore injection molding tolerances, why they matter, and how they impact different industries. We will look at real-world examples and case studies to illustrate the importance of getting tolerances right.
Understanding Injection Molding Tolerances
Injection molding is a popular manufacturing process. To generate a precise shape, molten plastic is injected into a mold. The permissible bounds for these forms’ dimensions are called tolerances. Here are the different types of tolerances:
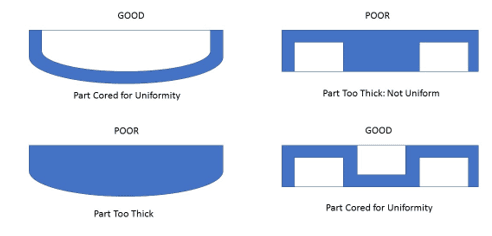
- Dimensional Tolerances: These are limits on a part’s size. For example, if a part should be 10 mm long, a dimensional tolerance might allow it to be anywhere from 9.8 mm to 10.2 mm long. This small variation can make a big difference, especially in applications where precision is crucial. For instance, even a fraction of a millimeter in electronic housings can affect how well components fit together and function.
- Geometric Tolerances: These go beyond just size and ensure that the shape of the part is correct. They check how parts fit together. Geometric tolerances include:
- Form Tolerances: These control the shape of features, such as flatness and roundness. For example, a hole that needs to be perfectly round may have a tolerance that allows for a slight deviation, but too much deviation can lead to assembly issues.
- Orientation Tolerances address the angles and alignment of features. For example, if a part has holes that must align with other components, the orientation tolerance ensures that those holes are not skewed.
- Location Tolerances: These specify where features must be placed on a part. If a hole is supposed to be positioned at a specific point, the location tolerance will dictate how far off it can be. This is critical for assembled parts, as misalignment can lead to assembly failure.
Impact of Tolerance on Product Quality
Understanding the impact of injection molding tolerances on product quality is vital for manufacturers. Tolerances influence how well parts fit together, affect the durability of the final product, and can even determine whether a product passes quality control checks. When tolerances are too loose, parts may not fit properly, leading to assembly issues and product failures. Conversely, overly tight tolerances can increase production costs and time without providing additional benefits.
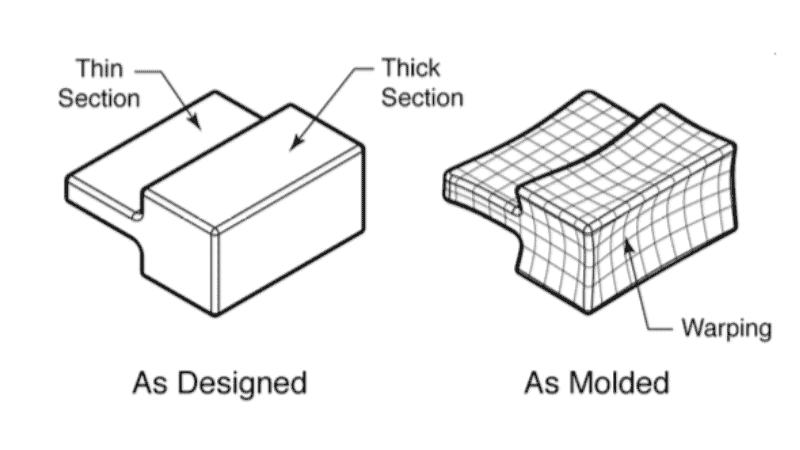
Material Selection
The type of material chosen affects tolerances. Different plastics shrink differently when cooling, impacting the final dimensions of the molded part. For example:
- ABS (Acrylonitrile Butadiene Styrene): It holds tolerances well due to its relatively low shrinkage rate. This characteristic makes it a preferred material for consumer goods like toys and electronic housings, where precise dimensions are necessary for proper fit and function.
- Nylon: While it has higher strength and impact resistance, nylon tends to shrink more during cooling, which can lead to larger variations in tolerances. This variability might pose challenges in applications with critical dimensional accuracy, such as automotive components.
Mold Design Considerations
The design of the mold is crucial for achieving tolerances. If the mold is poorly designed, parts can warp or not fit together properly. Key factors include:
- Gate Locations: Where the plastic enters the mold affects the flow and cooling of the molten material. Poor gate placement can lead to uneven filling, causing defects in the final product.
- Cooling Channels: Proper cooling is essential to prevent uneven shrinkage. If one part of the mold cools faster than another, it can lead to warping and dimensional discrepancies. An optimized cooling system ensures uniform temperature distribution, which helps maintain tight tolerances.
Tolerances in Different Industries
Different industries have unique requirements regarding injection molding tolerances. Understanding these differences is crucial for manufacturers. Each sector has its specific tolerance standards based on the performance requirements of the end products.
Automotive Industry
In the automotive world, precision is vital. Parts must fit together perfectly for safety and performance. Tolerances for certain components can be as tight as ±0.1 mm. If a component doesn’t fit right, it can lead to failures or accidents.
Case Study: A manufacturer produced a batch of injection-molded brackets for a new car model. They found that the brackets were off by 0.5 mm. This small error led to assembly issues, causing delays and additional costs. After thoroughly reviewing their processes, they improved their tolerance checks and implemented stricter controls, which helped prevent future issues and improved overall product quality.
Aerospace Industry
The aerospace industry has some of the strictest tolerance requirements. Parts must be lightweight yet strong, and tolerances can be as tight as ±0.05 mm. Because aircraft components must resist harsh environments, the smallest error can cause major issues.
Case Study: An airplane manufacturer used injection molding for a component in their fuselage. They set strict tolerances and utilized advanced testing methods to ensure compliance. This attention to detail ensured that the part met safety standards, performed well during tests, and ultimately contributed to the overall reliability of the aircraft.
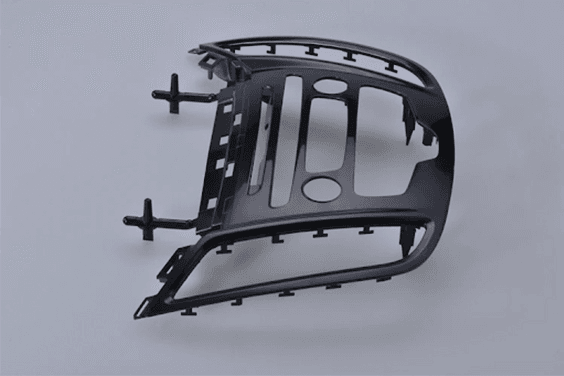
Consumer Electronics
Products in consumer electronics are getting smaller and more complex. Precision is crucial for components to fit together and work correctly. Tolerances in this field can range from ±0.1 mm to ±0.3 mm. The tight fit is essential for both functionality and aesthetics.
Case Study: A smartphone maker faced issues with cases that didn’t fit well due to poor tolerance controls. After analyzing their injection molding process, they discovered the tolerances were too loose. By tightening the tolerances and improving their quality control measures, they enhanced product quality, reduced returns, and increased customer satisfaction.
Measuring and Maintaining Tolerances
For manufacturers, measuring and maintaining tolerances is critical. Accurate measurement ensures that parts meet specifications, while effective maintenance helps avoid deviations over time.
Measurement Techniques
To ensure injection molding tolerances are met, manufacturers use various measurement techniques. Here are some common methods:
- CMM (Coordinate Measuring Machine): This machine measures a part’s physical geometrical characteristics. It uses a probe that touches the part and collects data to determine whether it meets the specified tolerances. This technology is crucial for high-precision applications where accuracy is paramount.
- Laser Scanning: This non-contact method provides quick and accurate measurements of complex geometries. It creates a 3D part model, allowing engineers to identify deviations from the intended design. Laser scanning is especially useful for large-scale manufacturing, where traditional measurement methods may be time-consuming.
Quality Control Practices
Maintaining tolerances is essential for consistent quality. Statistical Process Control (SPC) helps manufacturers monitor and control their processes. By analyzing data collected during production, they can identify trends and adjust before issues arise.
Case Study: A factory implemented SPC to track its injection molding process. They discovered that a specific machine produced parts out of tolerance more frequently than others. With this knowledge, they adjusted the machine settings and implemented regular maintenance checks, which improved overall product quality and reduced waste.
Challenges and Solutions in Achieving Tolerances
While achieving the right tolerances is essential, manufacturers often face challenges. Identifying these challenges and implementing effective solutions is key to maintaining product quality.
Common Challenges
Achieving the right tolerances can be tricky. Here are some common challenges that manufacturers face:
- Warping: Parts can bend or change shape as they cool. Warping can result from uneven cooling, improper mold design, or material properties. This distortion can lead to significant deviations from the intended dimensions.
- Shrinkage: Different materials shrink at different rates when cooling, which can cause size variations. Understanding the shrinkage characteristics of each material is crucial for designing molds that account for these changes.
- Tooling Errors: A mistake in the mold design can result in inaccurate parts. Errors can occur during the design phase or manufacturing of the molds, leading to costly rework and delays.
Innovative Solutions
To overcome these challenges, manufacturers are adopting innovative solutions:
- Mold Flow Analysis: This technique helps predict how the plastic will flow within the mold. By simulating the injection process, engineers can identify potential issues before the mold is even built. This analysis can save time and resources by minimizing trial and error during production.
- Advanced Materials: Using materials with lower shrinkage rates or specific properties can improve tolerance control. For example, using glass-filled nylon can reduce shrinkage and improve dimensional stability.
- Regular Maintenance: It is crucial to keep molds in good condition. Regular maintenance can help identify wear and tear and ensure that molds continue to produce parts within the specified tolerances.
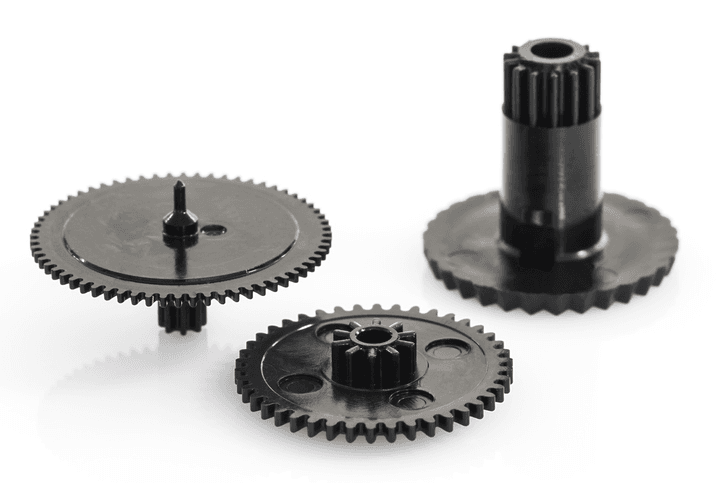
Conclusion
Understanding injection molding tolerances is crucial for achieving precision in manufacturing. Tolerances directly impact product quality and customer satisfaction across automotive, aerospace, and consumer electronics industries. Manufacturers can meet essential specifications by selecting the right materials, designing effective molds, and implementing robust quality control practices.
At Frigate Die Casting Services, we prioritize precision in our injection molding solutions. Our expert team and advanced technology ensure that every part meets your tolerances. Trust us to deliver reliable components that enhance your product’s performance.
Contact us today to discover how our services can elevate your manufacturing processes!