Have you ever struggled to find components that can handle extreme conditions without breaking down? Or do you face delays because the parts you need aren’t ready on time? High-strength forging services can be the solution. But how do you ensure the parts you choose meet strict quality standards while staying within budget? These are common challenges in manufacturing today. This blog will explore how high-strength forging services address these pain points and why they are critical for industries demanding durable and customized solutions.
Understanding the Pain Points in High-Strength Forging
The stakes are high in manufacturing. Companies often face stringent quality demands, tight schedules, and the need for custom components. High-strength forging services directly target these issues, ensuring the durability and reliability of critical parts. Let’s explore the main pain points that companies encounter and how forging can address them effectively.
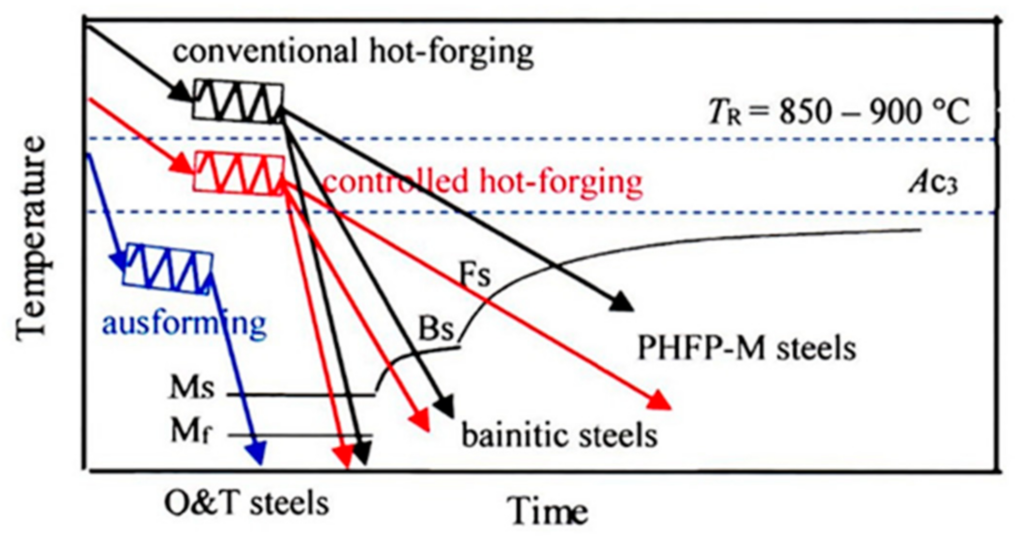
Material Quality & Consistency
Inconsistent material quality can lead to performance failures. If materials don’t have uniform properties, they might not withstand the pressures and stresses they face. Forging with high-strength materials ensures consistency. Unlike casting, where molten metal is poured into a mold, forging involves shaping solid metal with compressive forces. This process aligns the grain structure, which improves the strength and durability of the material. For example, forged aluminum can be up to 300% stronger than cast aluminum due to better grain structure.
Cost Efficiency & Lead Times
High-strength forging services is often perceived as costly. But what if you could combine strength and cost efficiency? The forging process is faster than many machining methods. According to industry data, forging can reduce manufacturing costs by 20-30% compared to other methods due to lower waste. Shorter lead times are another advantage. Components can be produced in weeks rather than months, even for complex designs.
Customization & Flexibility
Many manufacturers struggle with finding suppliers that provide custom solutions. Customization is crucial, especially when your requirements are unique. High-strength forging services offer flexibility. Components can be tailored to exact dimensions and specifications. From choosing the right alloy to designing precise shapes, the forging process accommodates special requests, making it ideal for niche industries.
Technical Specifications & Compliance
How do you ensure that a component meets industry standards? This is often a top concern. Technical specifications, like exact tolerances and surface finishes, are critical in industries like aerospace and automotive. Forging is known for its ability to achieve tight tolerances. Components forged with high-strength materials often exceed compliance requirements, offering safety and reliability in high-stress environments. For example, forged parts can easily meet standards such as ASTM, ISO, and DIN.
Performance Under Extreme Conditions
In sectors like oil and gas, parts need to endure extreme heat, pressure, and corrosive environments. High-strength forging services offer components specifically designed to handle these challenges. For example, forged steel has higher fatigue resistance than other methods, making it suitable for high-impact applications. In the automotive industry, forged crankshafts can last up to 50% longer than machined alternatives, reducing the risk of part failure.
Key Considerations for Selecting a High-Strength Forging Provider
Choosing the right forging provider is crucial for maintaining product quality and meeting production goals. With many options available, knowing what factors will make the difference in your decision is essential. Here’s what to look for when selecting a provider for high-strength forging services.
Advanced Forging Techniques
High-strength forging services employ various advanced techniques, including closed-die and open-die forging. Closed-die forging involves compressing metal between two dies, shaping it precisely. This method is ideal for complex shapes that need high accuracy. On the other hand, open-die forging is used for larger parts and allows for greater flexibility in shaping. Modern advancements, like precision forging, ensure that components are manufactured with minimal material loss and maximum strength.
Material Expertise
Selecting the right material is essential. Different applications require different metals. For instance, aerospace components often use titanium or high-strength aluminum alloys because they are light and strong. Automotive parts might rely on steel for its durability. High-strength forging services offer expertise in a wide range of materials. Forging specialists know how to select and process the right alloys to match the application, ensuring each component performs as expected.
Production Capacity & Scalability
A common challenge is ensuring suppliers can handle small and large orders. Whether you need a batch of 100 parts or 10,000, the provider’s production capacity matters. High-strength forging services are scalable. They can adapt to different production volumes without compromising quality, which is crucial in industries that experience fluctuations in demand.
Quality Assurance & Testing
Ensuring product quality is non-negotiable. High-strength forging services include rigorous quality checks. Standard protocols include non-destructive testing (NDT), hardness tests, and tensile strength measurements. Forged components often undergo ultrasonic or X-ray inspections to detect internal flaws. According to data, components tested under such stringent conditions have a defect rate of less than 1%, far lower than traditional methods.
Sustainability & Waste Reduction
Sustainability is becoming a priority. Forging is inherently efficient, reducing material waste. Advanced forging processes can minimize scrap rates by 25-50% compared to traditional machining. This reduction not only saves costs but also aligns with sustainable manufacturing goals. Many forging providers adopt eco-friendly practices, such as using recycled materials and energy-efficient machinery.
Benefits of Custom Solutions in High-Strength Forging
One size rarely fits all in demanding industries. Custom solutions in high-strength forging services cater to specific needs, allowing for enhanced performance and cost-effectiveness. Here’s why custom solutions are invaluable for manufacturers seeking high-quality forged components.
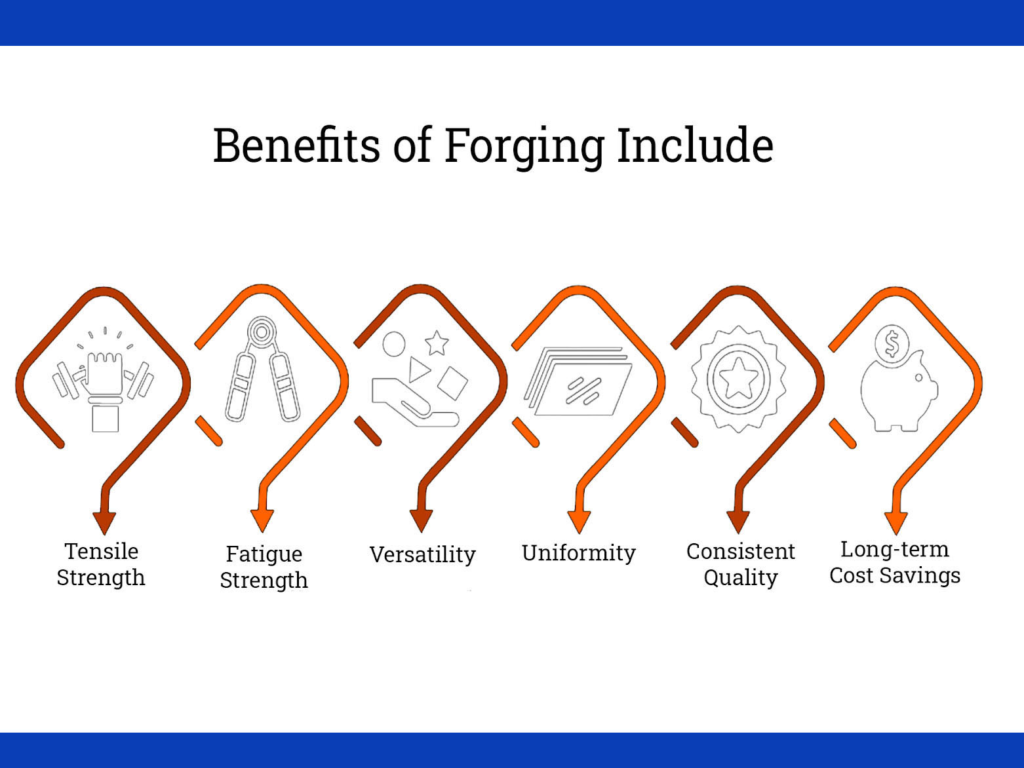
Optimized Component Design
Tailored solutions ensure that components are designed to fit specific needs. Custom designs can reduce unnecessary material, lowering overall weight without sacrificing strength. A study showed that optimized forged designs could lead to a 15% increase in component efficiency. This optimization is particularly useful in weight-sensitive industries like aerospace, where every gram counts.
Improved Supply Chain Management
Supply chain disruptions are a major concern. High-strength forging services can streamline your supply chain. With a single reliable supplier, inventory management becomes simpler. Components can be delivered on time, reducing lead times and avoiding costly delays. This streamlined process is especially valuable in industries like construction, where tight schedules are critical.
Reduced Maintenance & Lifecycle Costs
Forged components are known for their durability. Components manufactured using high-strength forging services often have a longer lifespan. For example, in heavy machinery, forged gears have shown up to 40% longer service life than non-forged alternatives. This increased durability means fewer replacements and lower maintenance costs over time.
Frigate’s Capabilities in High-Strength Forging
Regarding custom solutions, Frigate stands out as a leader in high-strength forging services. They have built a reputation for delivering high-quality, customized components across various industries. Here’s what sets Frigate apart from the competition.
Custom Solutions for Demanding Manufacturing Requirements
Frigate specializes in creating custom forging solutions. They understand that every industry has unique demands. From automotive to energy, they tailor their services to meet specific requirements. Whether it’s a small part for precision equipment or a large, heavy-duty component, Frigate can handle it.
Material Versatility & Advanced Alloy Selection
Frigate offers a broad range of materials. They have expertise in metals like stainless steel, brass, titanium, and aluminum. Each material is chosen based on the specific application. Their advanced alloy selection ensures that every component has the right properties, be it corrosion resistance or high tensile strength.
Cutting-Edge Forging Technology
Using state-of-the-art equipment, Frigate delivers precision. They employ modern closed-die and open-die forging techniques, ensuring tight tolerances and superior surface finishes. Their technology investment means they can produce parts faster and with higher accuracy than many competitors.
Rigorous Quality Assurance & Testing Protocols
Quality is a top priority at Frigate. Every component undergoes a series of tests to verify strength, hardness, and durability. Advanced testing methods, such as ultrasonic and dye-penetrant inspections, detect even the smallest defects. This attention to detail means reliable components every time.
Short Lead Times & High Production Efficiency
Time is money in manufacturing. Frigate’s streamlined processes allow for rapid production. Thanks to their efficient workflows, they can handle high volumes with short lead times. This capability is especially crucial for industries where downtime can be costly.
Industries That Benefit from High-Strength Forging
High-strength forging services cater to various industries, each with its unique demands. For example, in energy transportation, forged components are critical in maintaining performance and safety. Here’s a closer look at the sectors that benefit most.
Aerospace & Defense
Forged components are lightweight and strong, perfect for aerospace. They handle stress well and are resistant to fatigue. For example, aircraft parts made from forged aluminum can reduce overall weight by up to 30%.
Automotive & Heavy Equipment
In the automotive industry, high-strength forging is used for critical parts like crankshafts and connecting rods. Forged parts are more durable and perform better under stress. Forged steel is favored for toughness in heavy equipment.
Energy & Oil & Gas
Components in the energy sector face extreme conditions. Forged parts can withstand high pressure and temperature. For instance, valves and fittings made from forged materials offer better performance in oil extraction.
Construction & Infrastructure
Construction relies on durable components that won’t fail. Forged steel parts provide the necessary strength for construction equipment and reduce the risk of failure in high-load situations, making them ideal for cranes and loaders.
Conclusion
High-strength forging services are essential for industries requiring reliable, durable, customized components. These services address pain points like material consistency, cost efficiency, and compliance with strict standards. Choosing the right forging provider can make all the difference in aerospace, automotive, or energy.
Contact Frigate for all your high-strength forging needs. They offer custom solutions, advanced technology, and rapid lead times that meet the most demanding manufacturing requirements. Choose a partner who understands your needs and delivers quality every time.
Get in touch with Frigate today!