Plastic 3D Printing Services
Frigate’s Plastic 3D Printing Services uses advanced additive manufacturing techniques. We offer a range of thermoplastics for optimized material properties and designs.
Get Your Quote Now
- Instant Quotation
- On-Time Delivery
- Affordable Cost
Effective Plastic 3D Printing for Custom Parts
Frigate’s Plastic 3D Printing Services are fast and cost-effective. They are ideal for designing, prototyping, and producing custom parts. Unlike subtractive manufacturing, which removes material, 3D printing builds designs layer by layer. The process starts with a three-dimensional digital design file, a CAD file. Once you provide a CAD file, several 3D printing methods can create your parts. Frigate uses industrial additive manufacturing to print components. We work with various engineered polymers, from transparent prototypes to flame-retardant plastics for aerospace applications.

Ensuring Quality and Accuracy in 3D Printed Parts
Implement rigorous quality control processes to ensure compliance with specified tolerances. Use advanced inspection techniques to verify dimensional accuracy and overall component quality.
Conduct thorough material testing to assess performance characteristics. This ensures that selected materials meet the required strength, durability, and functionality standards.
Utilize advanced inspection tools and technologies to monitor production quality. Employ non-destructive testing methods to identify potential defects without compromising the integrity of parts.
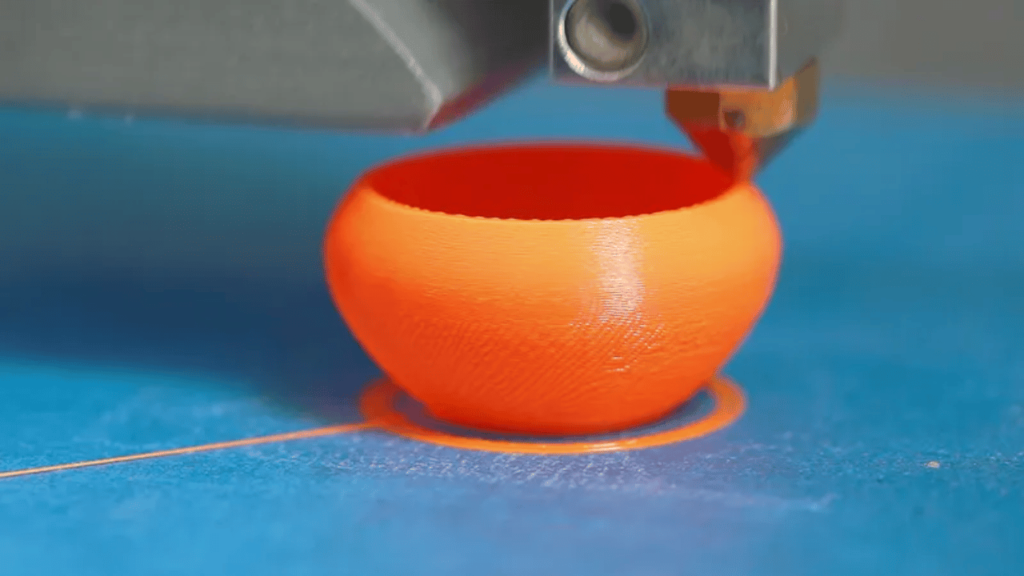
Streamlining Production for Speed and Scalability
Streamline production workflows to reduce setup times and enhance efficiency. Adopt best practices that facilitate quicker transitions between different print jobs.
Leverage a variety of 3D printing technologies to accommodate diverse production needs. This flexibility allows for rapid adjustments in response to changing project requirements or volume demands.
Enhance capacity to manage large production runs without compromising quality. Establish scalable processes that enable timely delivery of high volumes while maintaining consistent output.
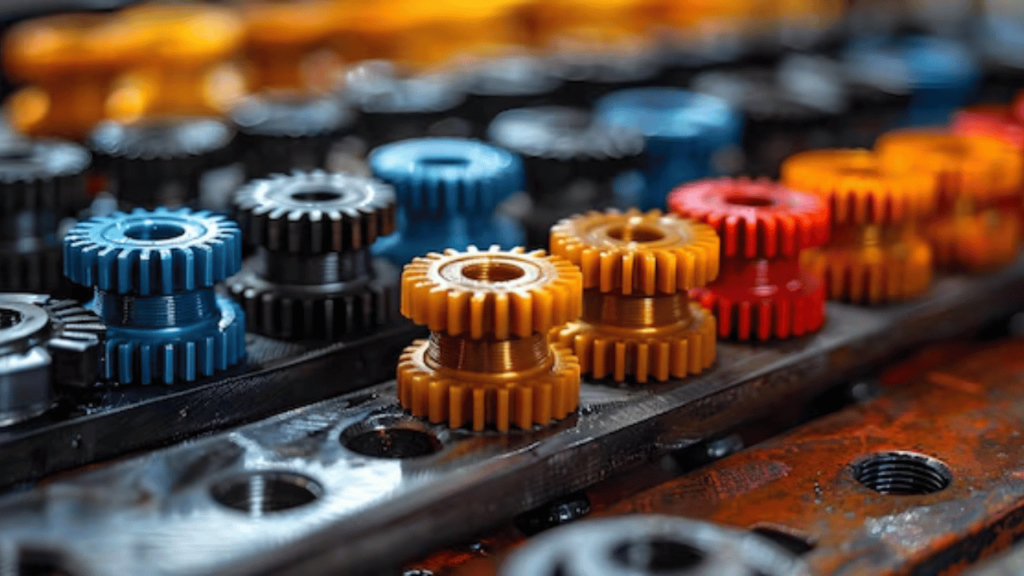
Enabling Innovative Design Solutions
Offering specialized support throughout the design and production phases ensures customer needs are met accurately. This dedicated approach minimizes misunderstandings and production errors.
Providing consistent communication on project progress keeps customers informed. This allows for timely adjustments and fosters a collaborative relationship.
Delivering detailed documentation on processes and specifications ensures clarity. This comprehensive approach helps customers understand all aspects of the extrusion process, enhancing confidence in the final product.
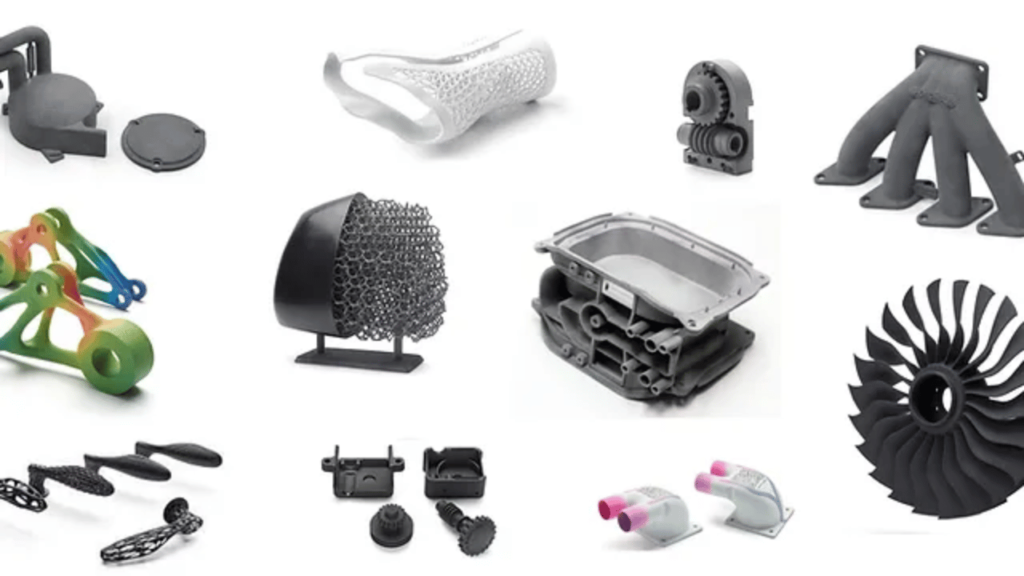
Plastic 3D Printing Materials
Plastic 3D printing enables the precise production of complex components through additive manufacturing. This technology allows rapid prototyping for various applications across multiple industries.
ABS is a widely used thermoplastic known for its strength and durability. It offers good impact resistance and can withstand higher temperatures than other plastics. Frigate utilizes ABS to produce robust prototypes and functional parts.
PLA is a biodegradable thermoplastic derived from renewable resources like corn starch. It is easy to print and provides an excellent surface finish. Frigate employs PLA for applications requiring high detail and low warping.
Nylon is a versatile engineering thermoplastic with high strength and flexibility. It exhibits excellent wear resistance and is suitable for functional prototypes and end-use parts. Frigate uses Nylon for applications demanding durability and flexibility.
Polycarbonate is a high-performance thermoplastic known for its exceptional impact resistance and optical clarity. It can withstand extreme temperatures and is suitable for demanding applications. Frigate employs polycarbonate for parts requiring high strength and thermal stability.
TPEs combine the properties of rubber and plastic, providing flexibility and resilience. They are suitable for applications that require soft-touch surfaces and excellent grip. Frigate uses TPE to produce flexible components and custom designs.
PEEK (Polyether Ether Ketone) and Ultem (Polyetherimide) are used for applications requiring high thermal stability and chemical resistance. These materials maintain their properties at elevated temperatures, making them ideal for aerospace and automotive components. Frigate incorporates high-temperature plastics for specialized applications.
PETG is a glycol-modified version of PET, known for its clarity and toughness. It combines the benefits of PLA and ABS, offering good impact resistance and ease of printing. Frigate uses PETG for functional prototypes and parts needing transparency and strength.
ASA is similar to ABS but offers improved weather resistance and UV stability. It is suitable for outdoor applications where exposure to sunlight is a concern. Frigate employs ASA for durable parts intended for exterior use.
Enhancing Consistency and Reducing Lead Time Variability
Reliability in production lead times is essential for project success. Frigate utilizes robust scheduling and workflow management systems to optimize efficiency and ensure timely delivery. Continuous monitoring of production processes allows for the early identification of potential bottlenecks, enabling proactive solutions to prevent delays. Frigate promptly addresses any timeline changes, ensuring that project plans remain on track and minimizing disruptions to operations.
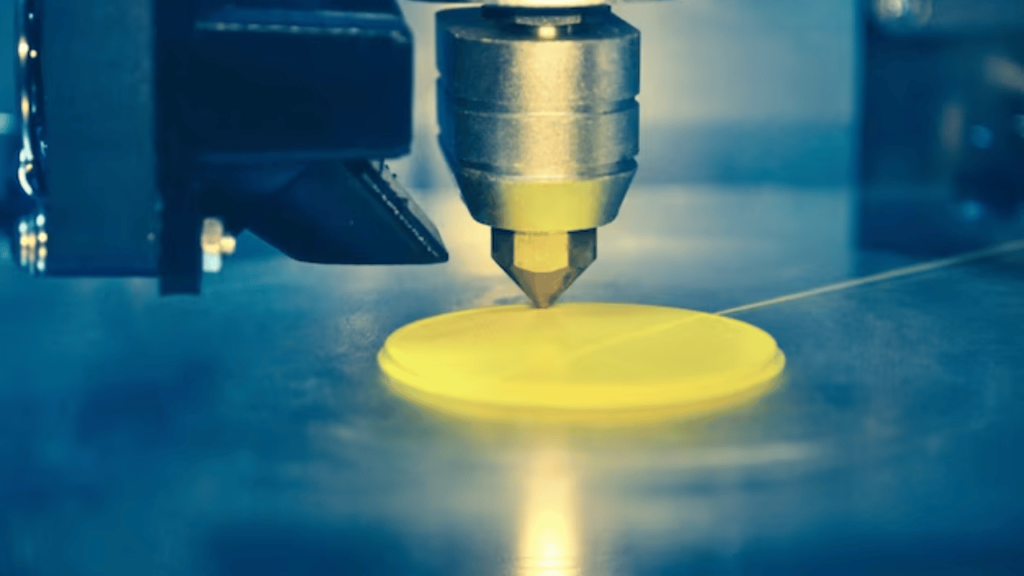
What Our Customers Say about Frigate
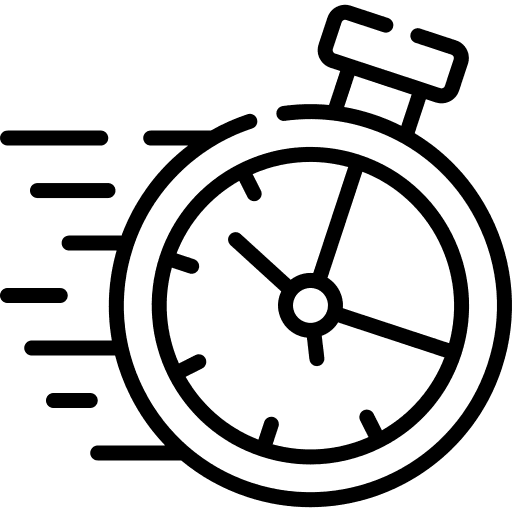
21%
Faster Manufacturing
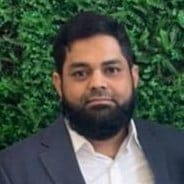

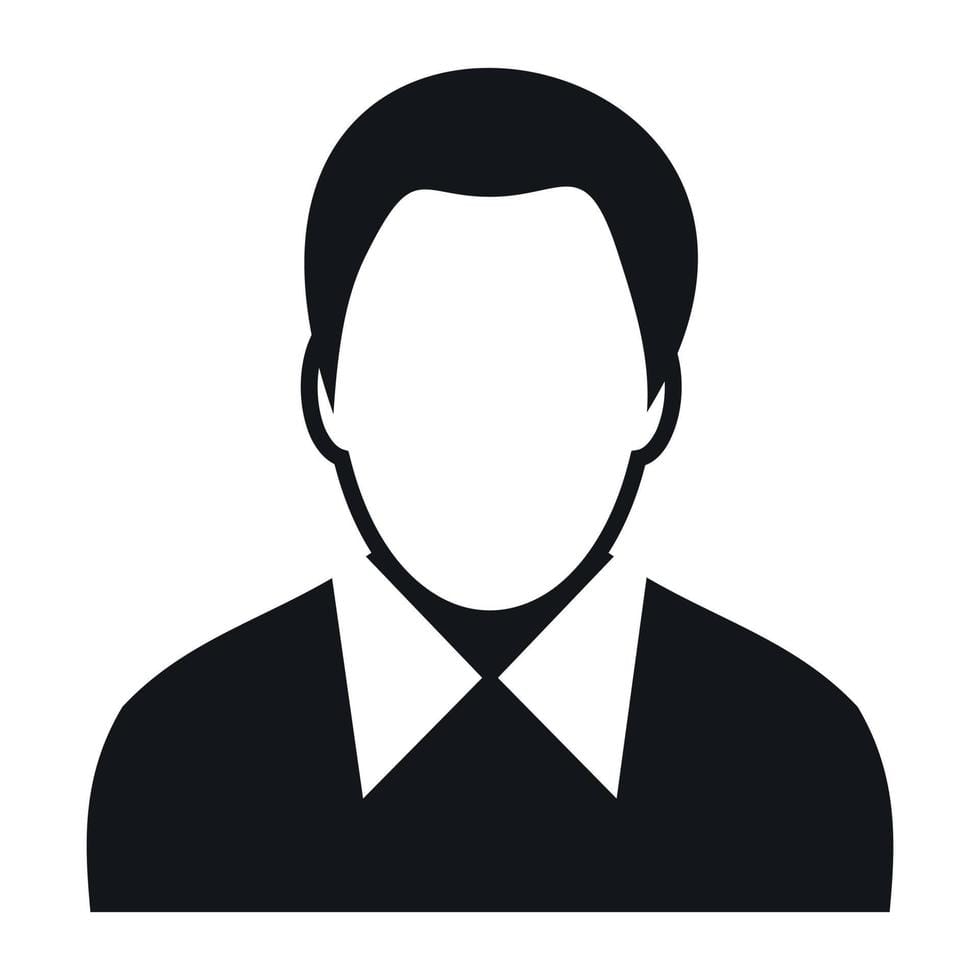
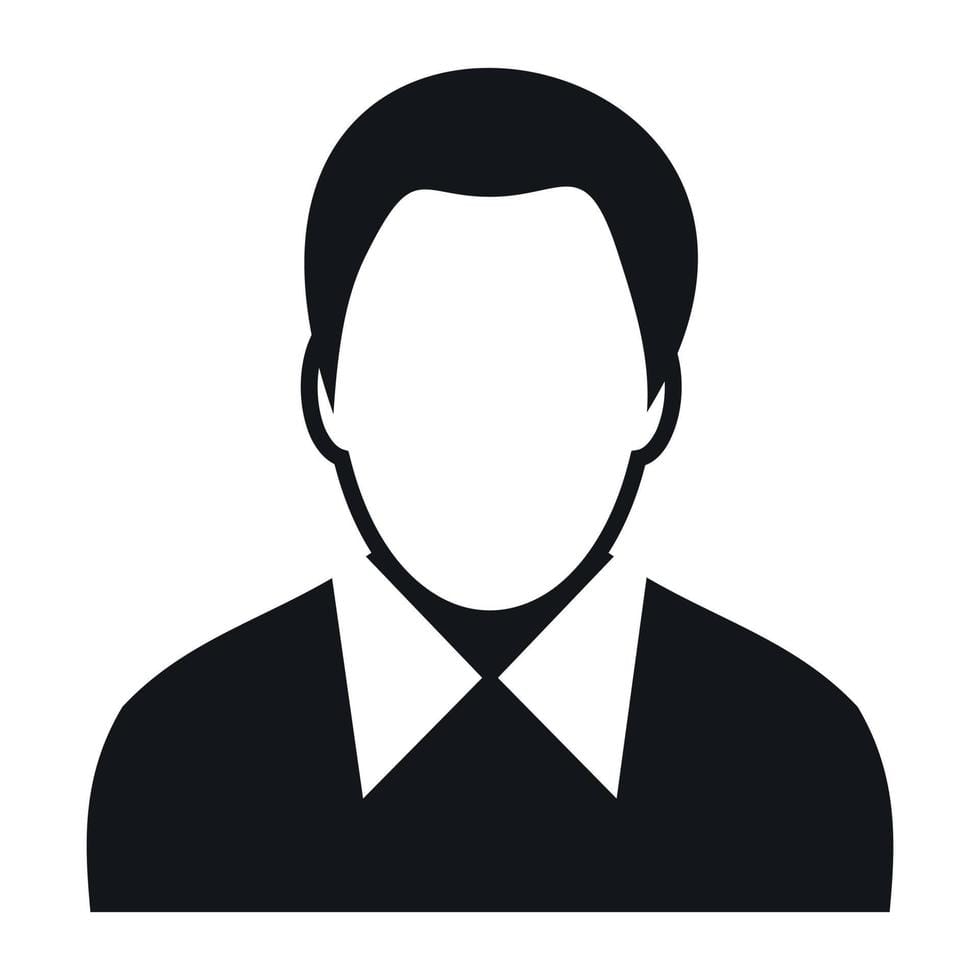
Having Doubts? Our FAQ
Check all our Frequently Asked Question
Frigate employs advanced quality control techniques, including precision calibration of 3D printers and regular inspection of produced parts. This ensures that each component meets specified tolerances and maintains high dimensional accuracy, minimizing discrepancies in critical applications.
Frigate offers a range of materials tailored to various performance requirements. The team selects appropriate materials by analyzing project specifications and intended use, considering strength, flexibility, and thermal stability, ensuring optimal results for each application.
Frigate optimizes production workflows through efficient scheduling and resource allocation. Continuous monitoring of printing and post-processing stages allows for quick identification of potential delays, enabling timely interventions to meet project deadlines without sacrificing quality.
Frigate supports an iterative design approach, allowing for adjustments throughout printing. The team can quickly incorporate design changes by maintaining open communication with clients, ensuring that final products align with customer expectations and requirements.
Frigate utilizes various post-processing techniques, such as sanding, polishing, and chemical smoothing, to improve the surface finish of printed components. These methods enhance aesthetics and ensure that parts meet functional requirements, particularly in applications where surface quality is critical.
Manufacturing Capability/Capacity
Ferrous casting
Mold size(max): 1m X 1m
Weight Range: 1 KG ~ 30 KGS
Mold size(max): 1.5m X 1.5m
Weight Range: 30 KG ~ 150 KGS
Mold size(max): 3m X 3m
Weight Range: 100 KG ~ 1000 KGS
Mold size(max): 500 MM X 500 MM
Weight Range: 0.250 KG ~ 20 KGS
Mold size(max): 500 MM X 500 MM
Weight Range: 0.100 KG X 20 KGS
Non-ferrous casting
Capacity: 5000 MT/a
Range of weight: 100 gm to 20 KGS
Mold size(max): 1 M X 1 M
Weight Range: 0.5 KG X 50 KGS
Mold size(max): 1 M X 1 M
Weight Range: 0.5 KG X 50 KGS
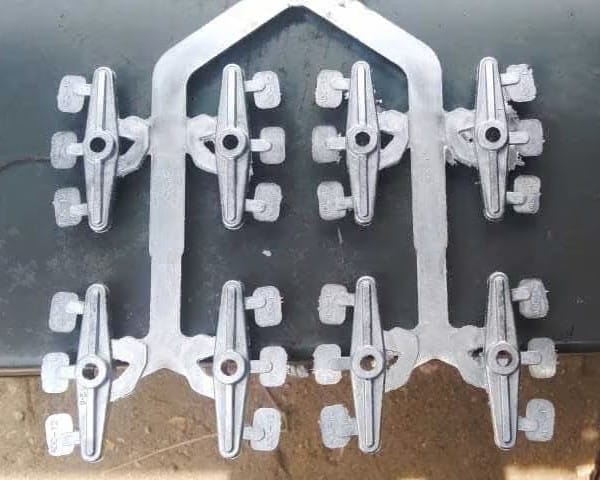
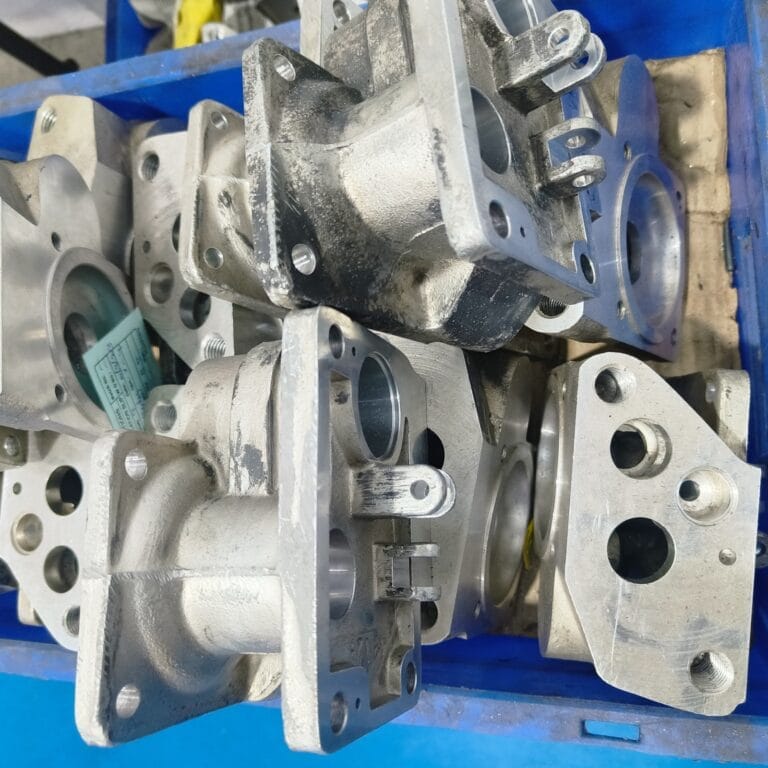
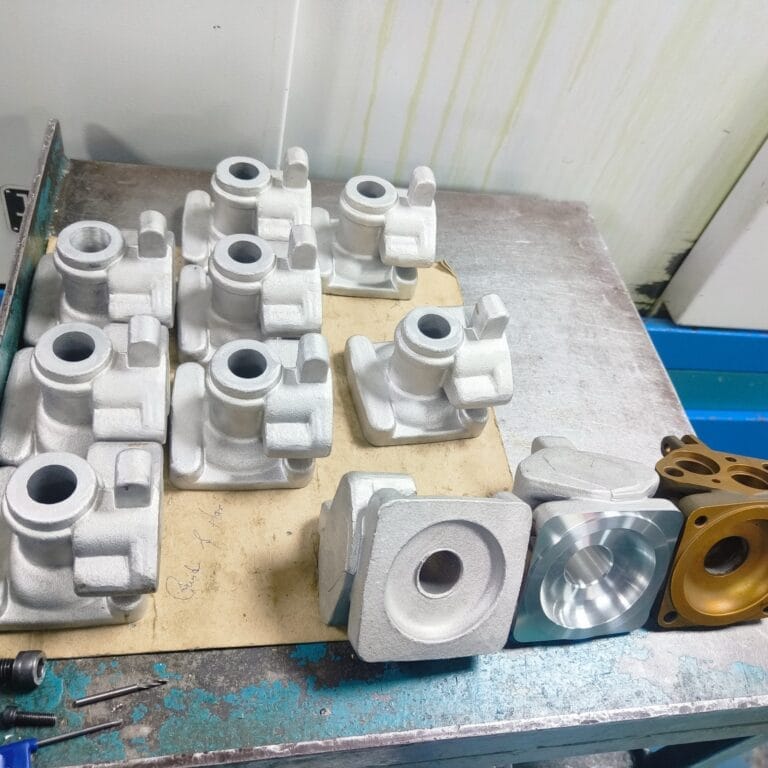
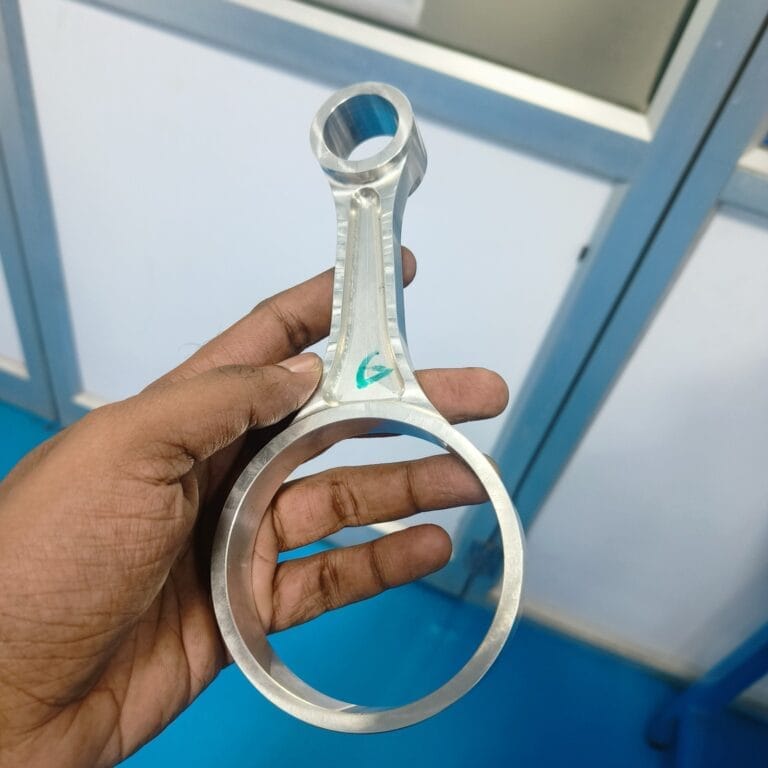
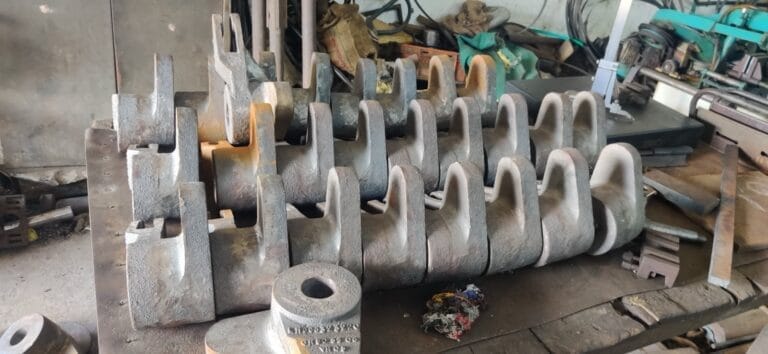
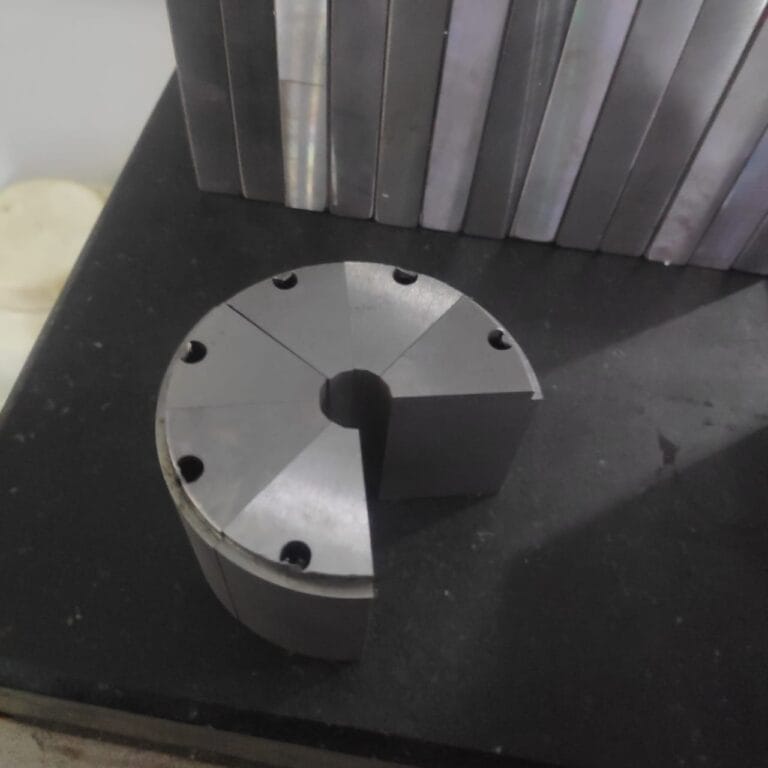
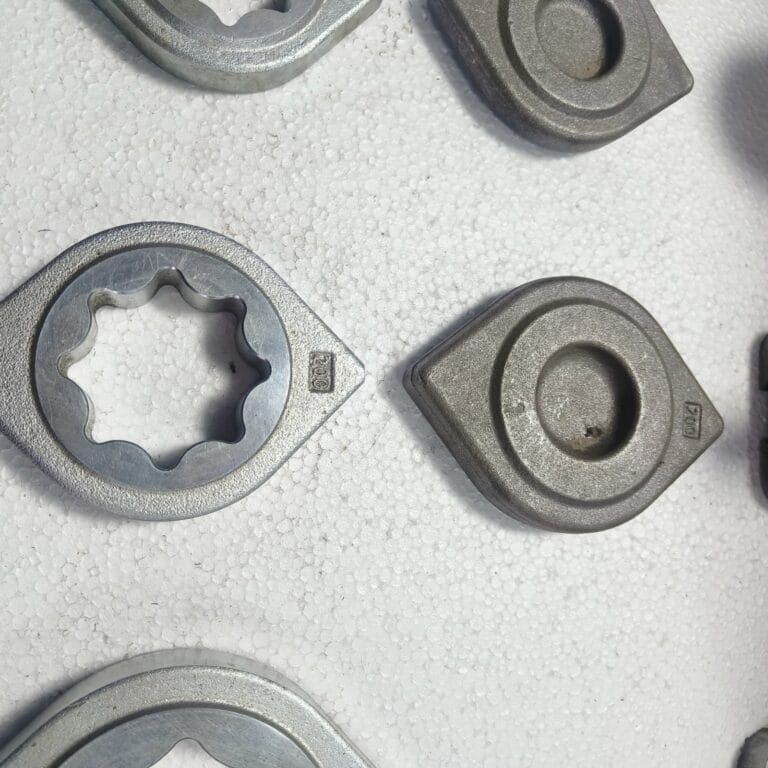
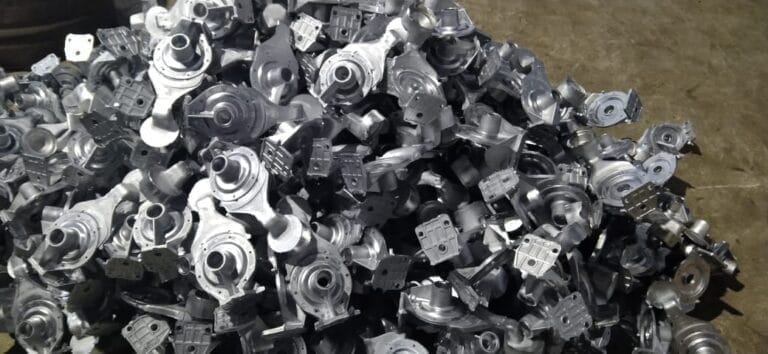
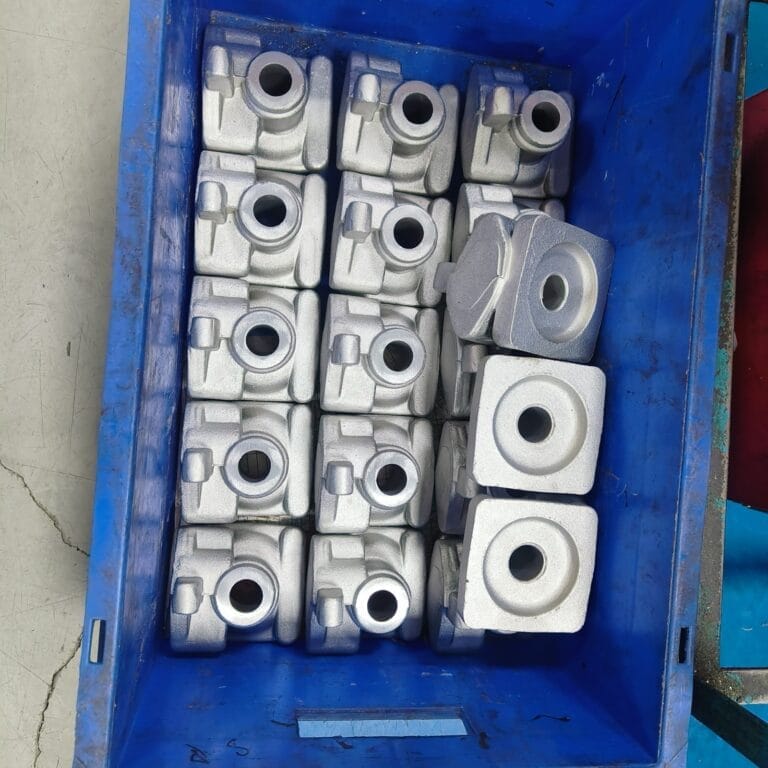
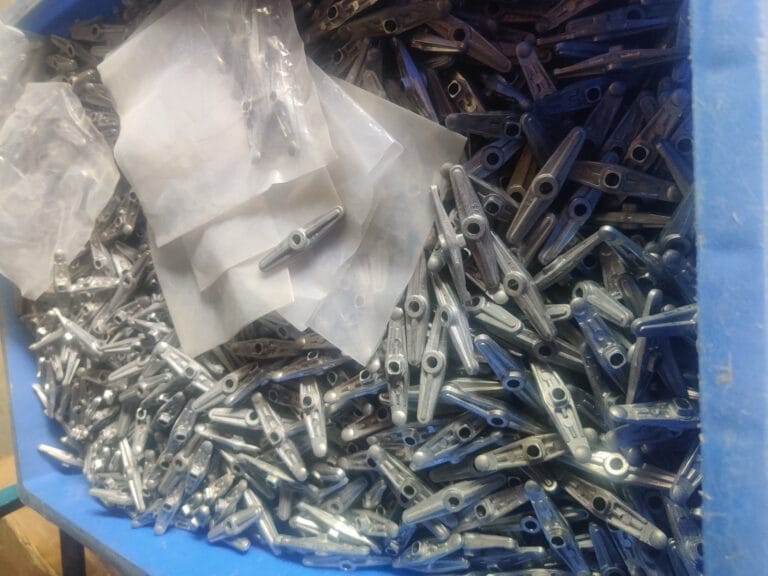
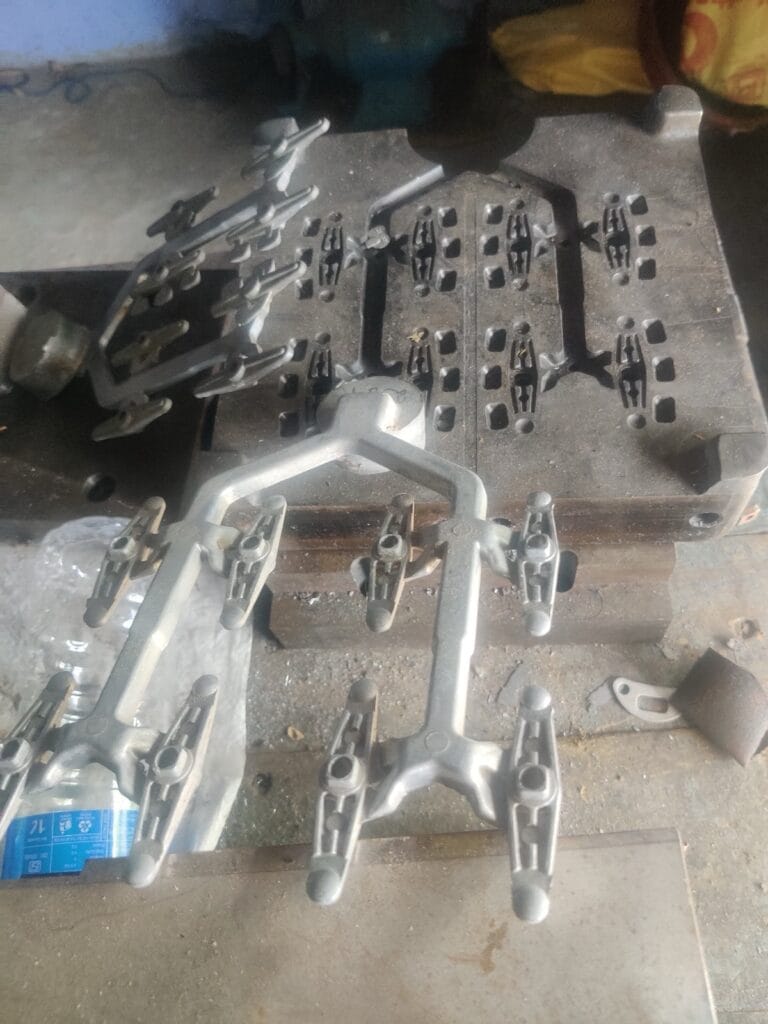
Forging
Capacity: 20,000 Tons per Annum
Range of weight: 300 KG to 1 Ton
Hammering: 5 Ton
Range of weight: 0.2 KG to 200 KGS
Hammering: 1600 Ton Hydraulic press
Ring size: 350 MM OD to 3000 MM OD
Range of weight: 15 KGS to 3200 KGS
Materials
Carbon Steel, Stainless Steel (AUSTENITE), Alloy Steel, Stainless Steel (MARTENSITE), etc.
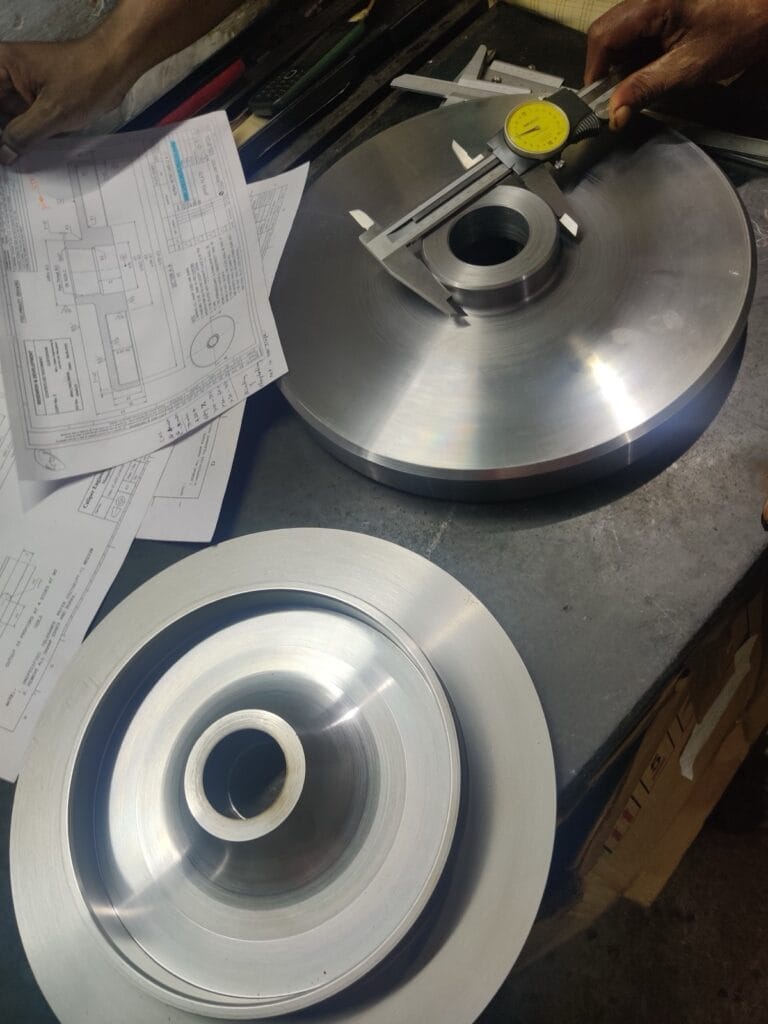
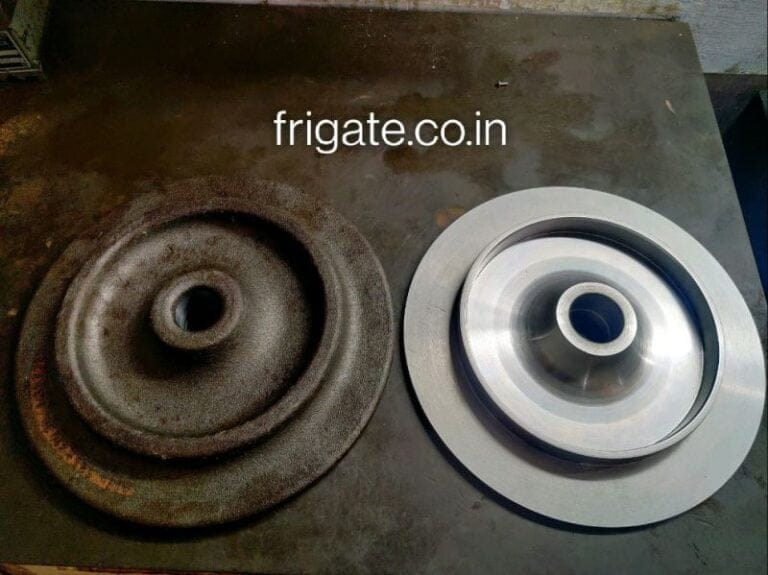
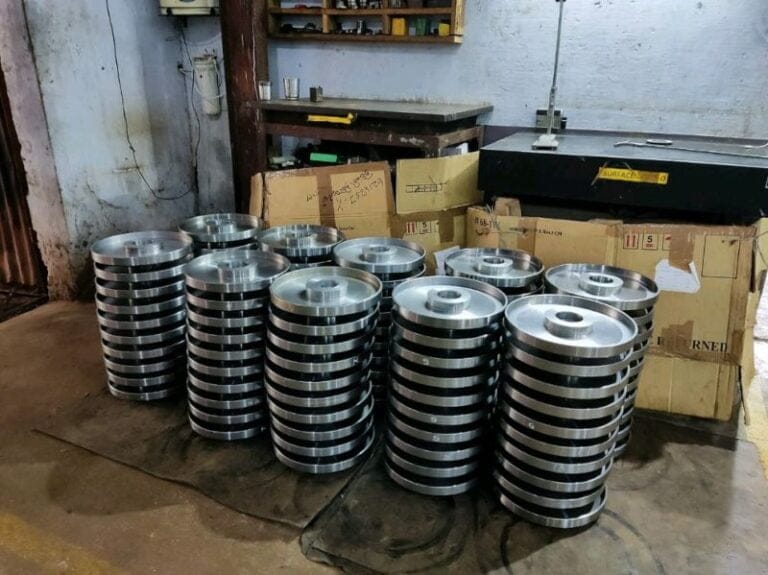
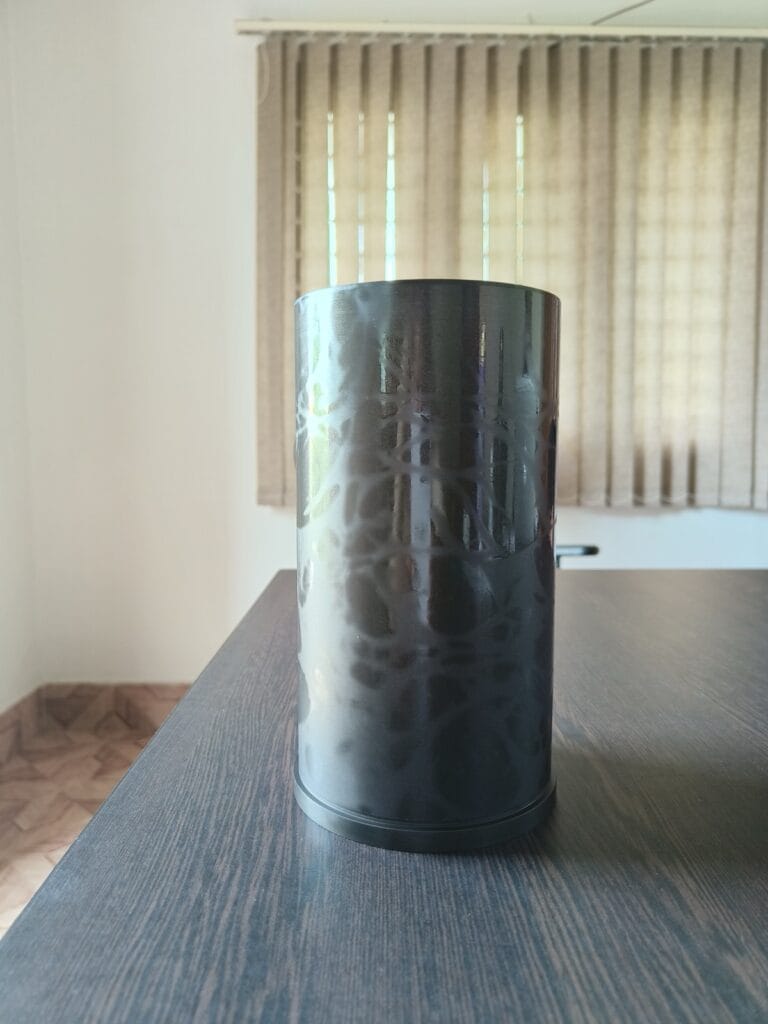
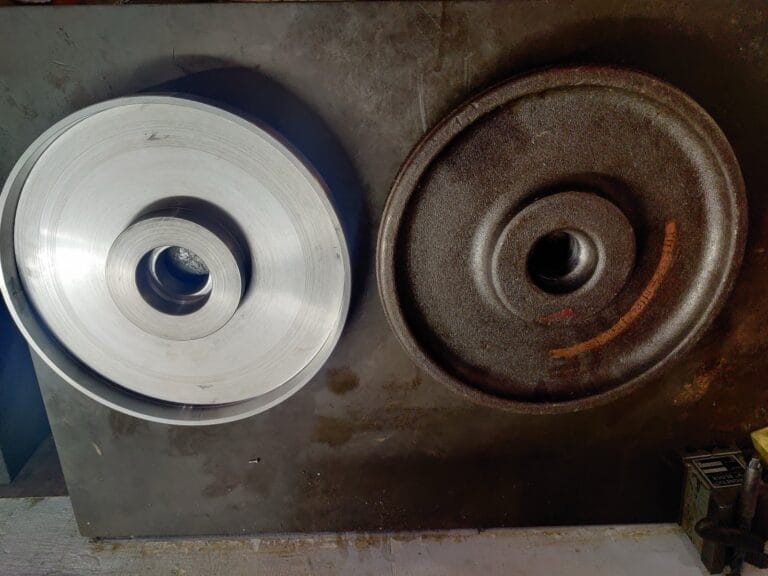
Machining
1 to 1000 MM
1 to 1000 MM
1 to 1000 MM
Materials
Steel, Aluminum, Brass, Copper, Titanium, Nickel Alloys, Tungsten Carbide, etc.
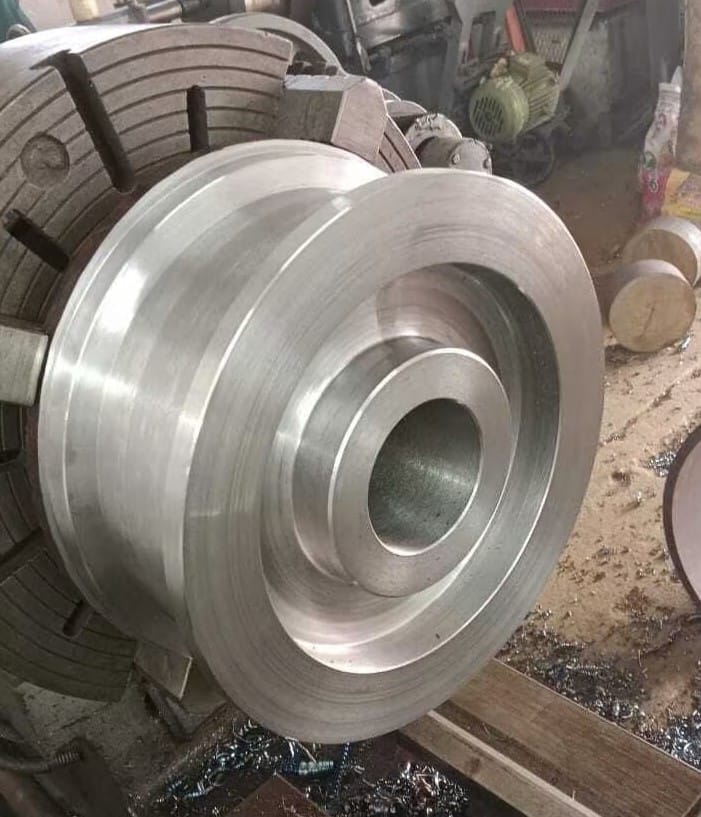
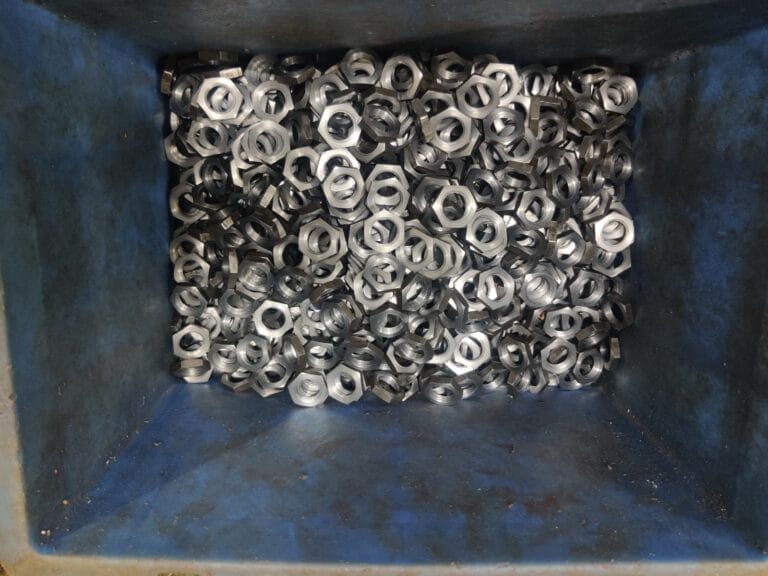
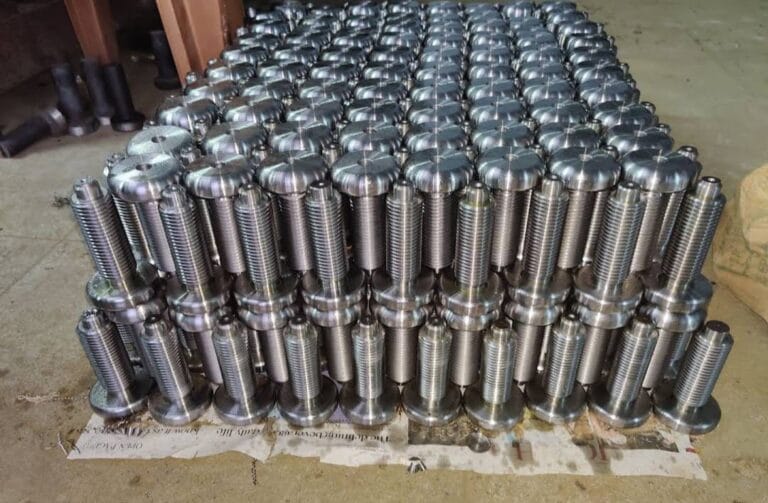
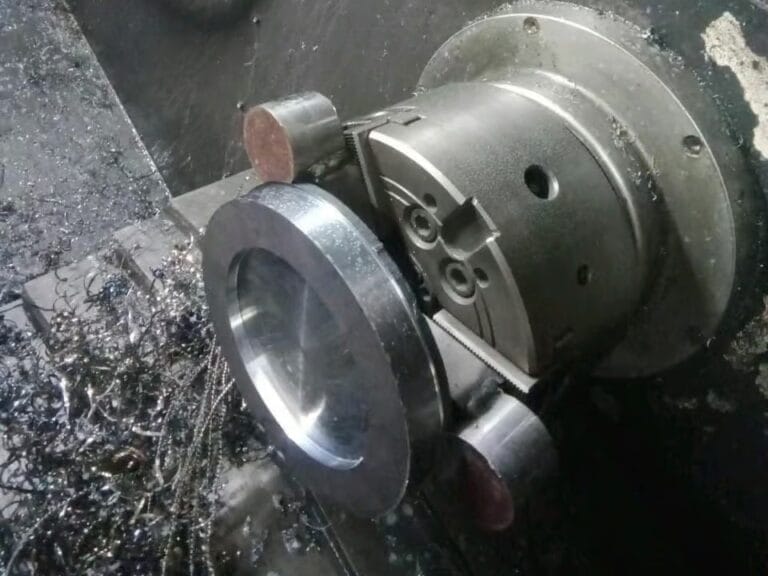
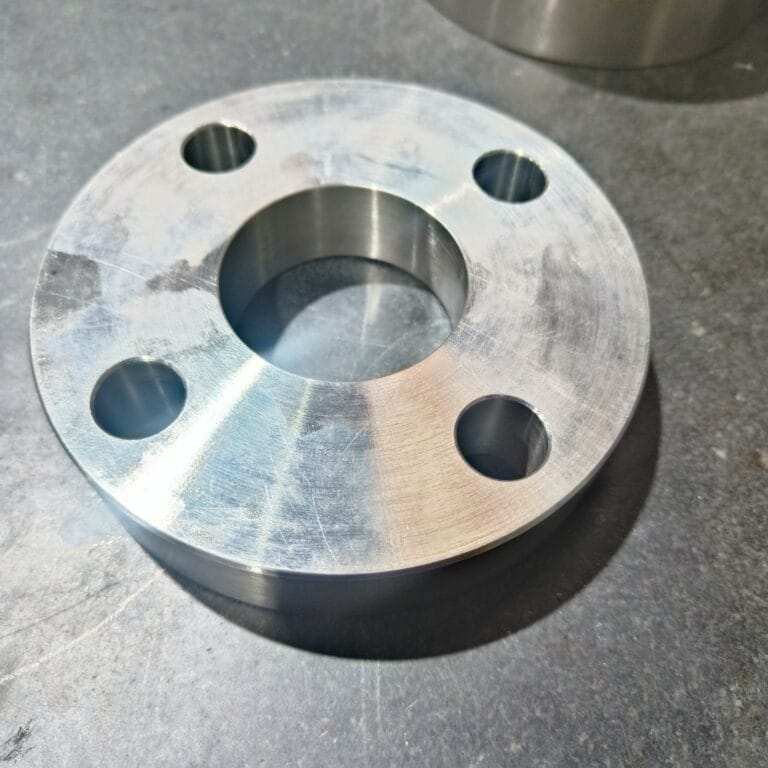
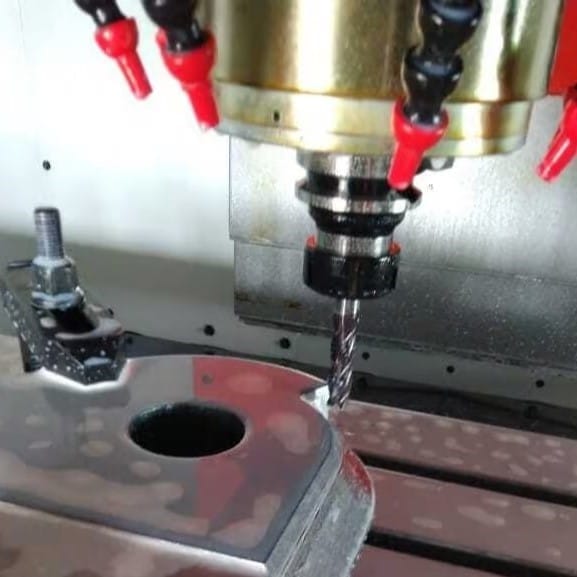
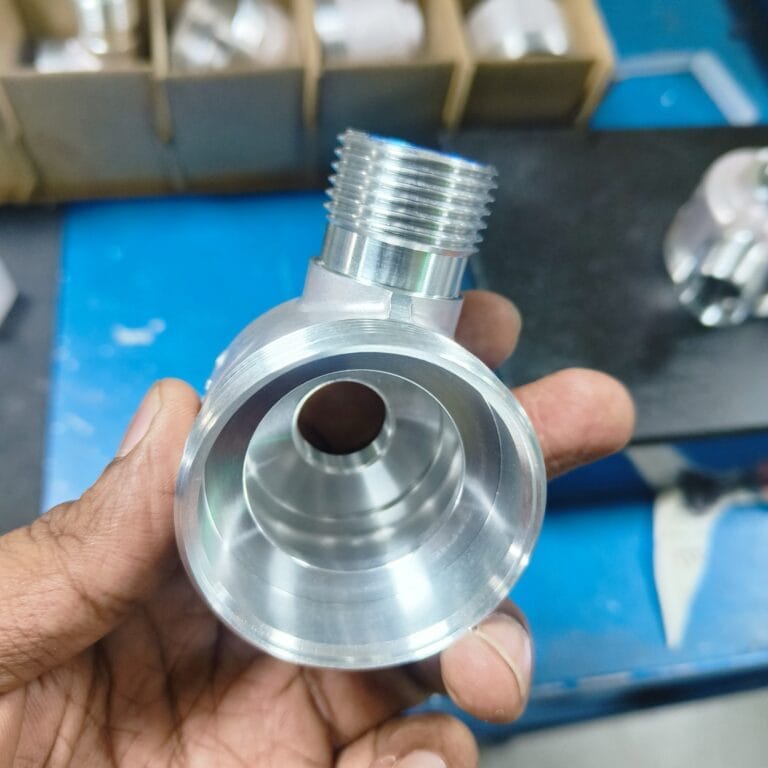
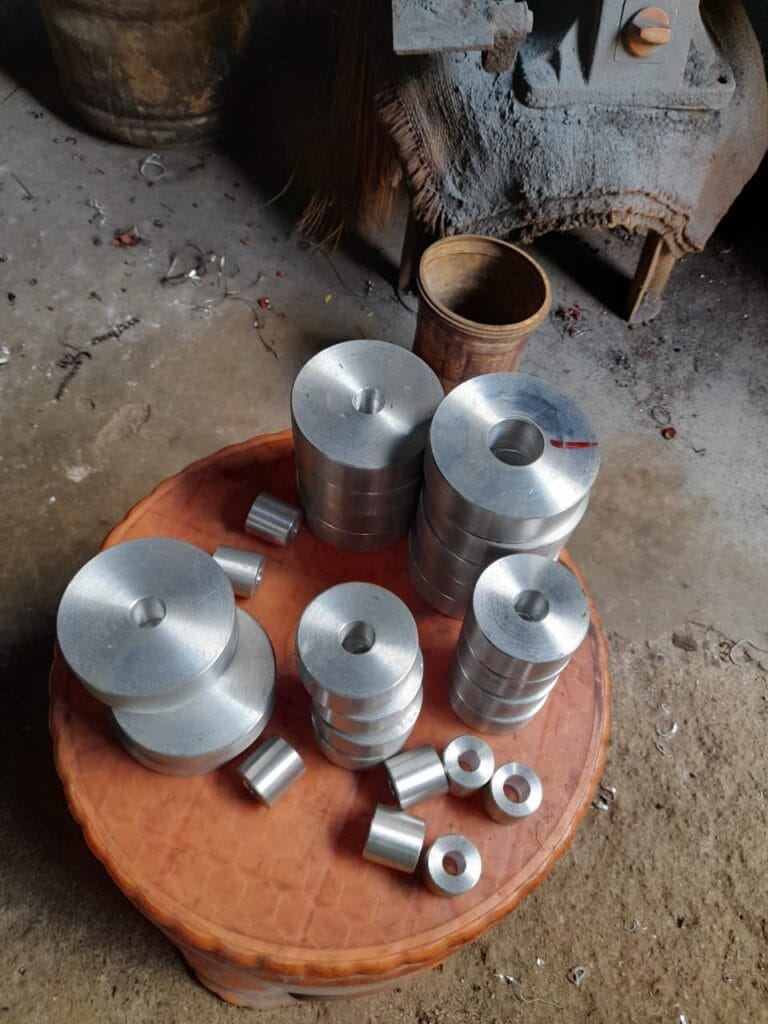
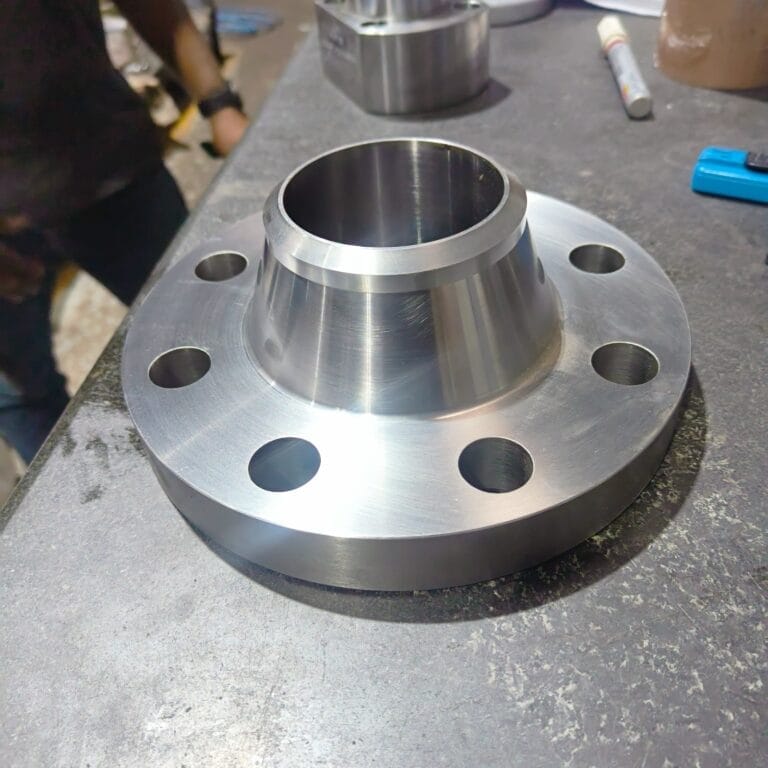
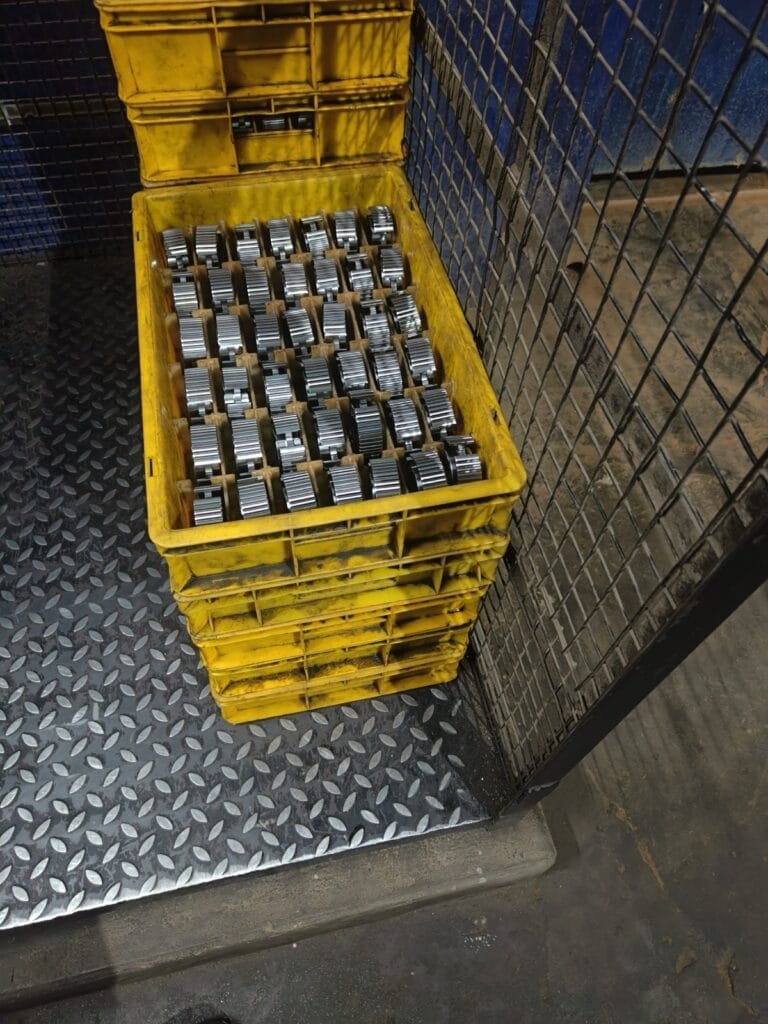
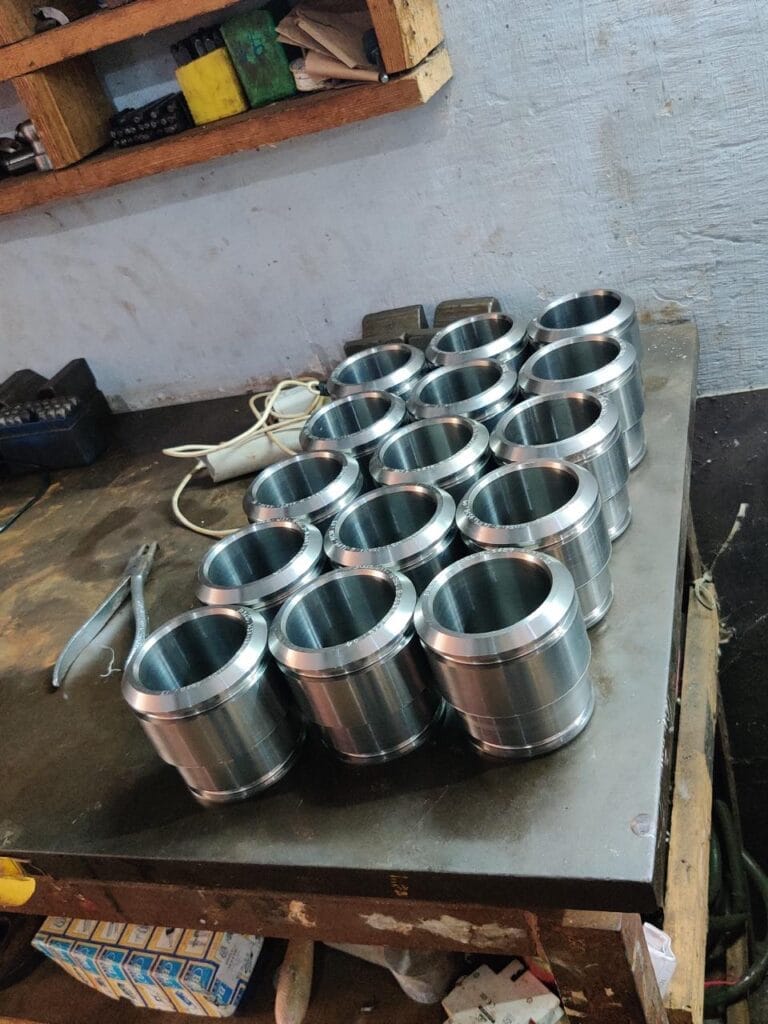
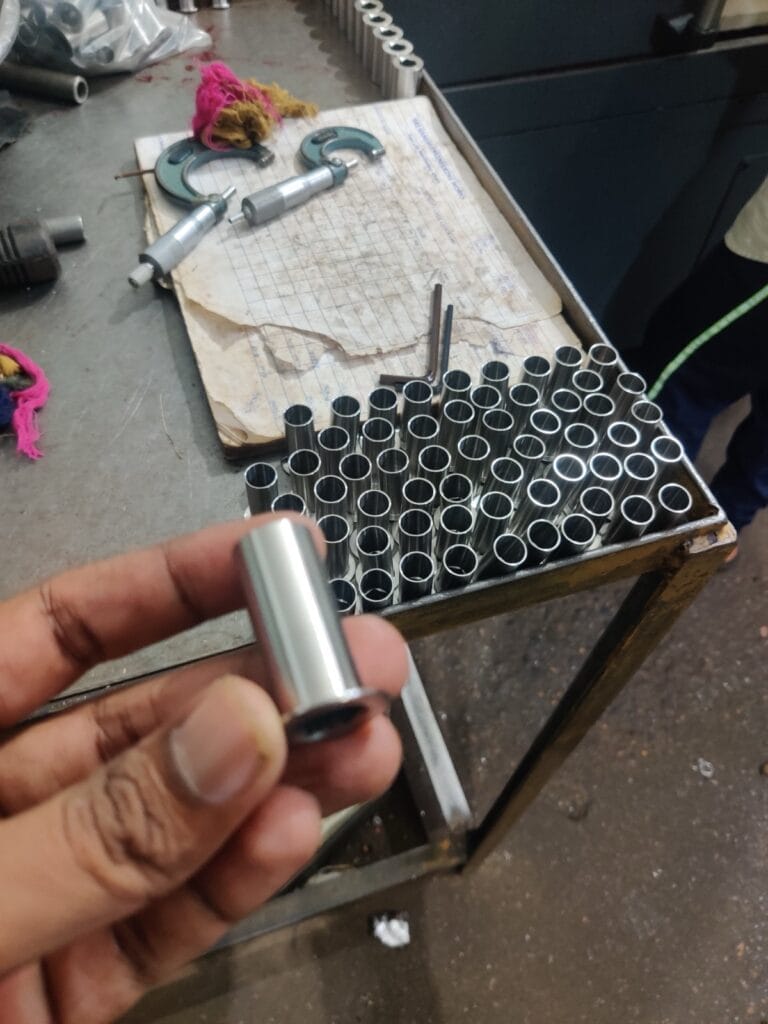
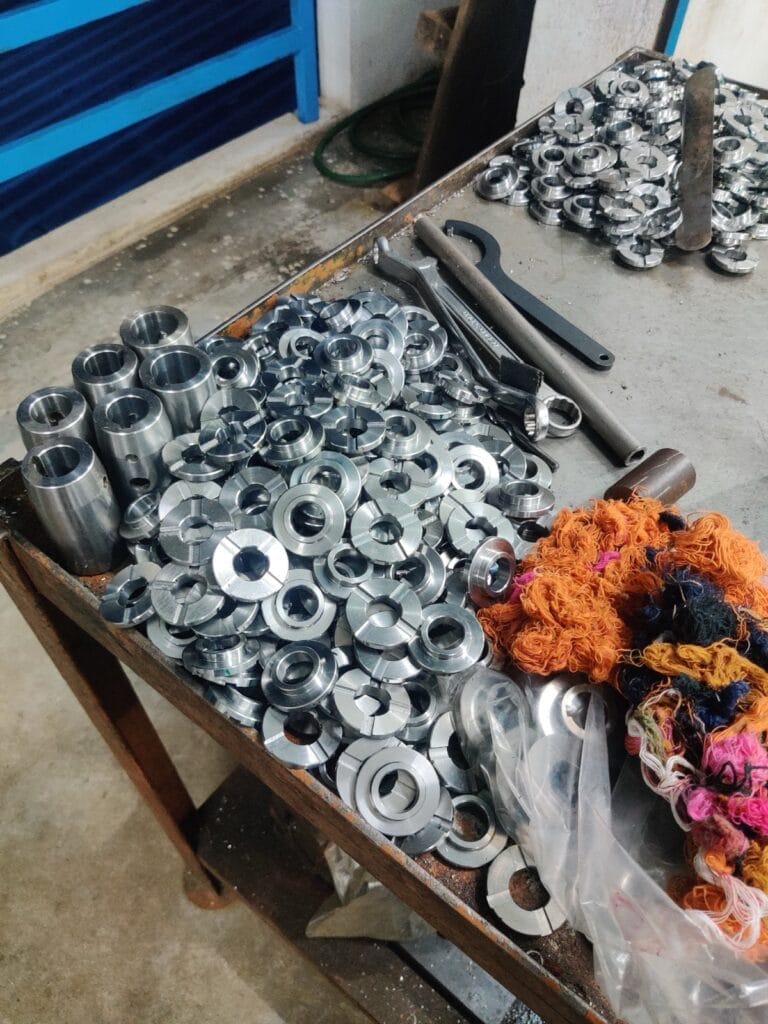
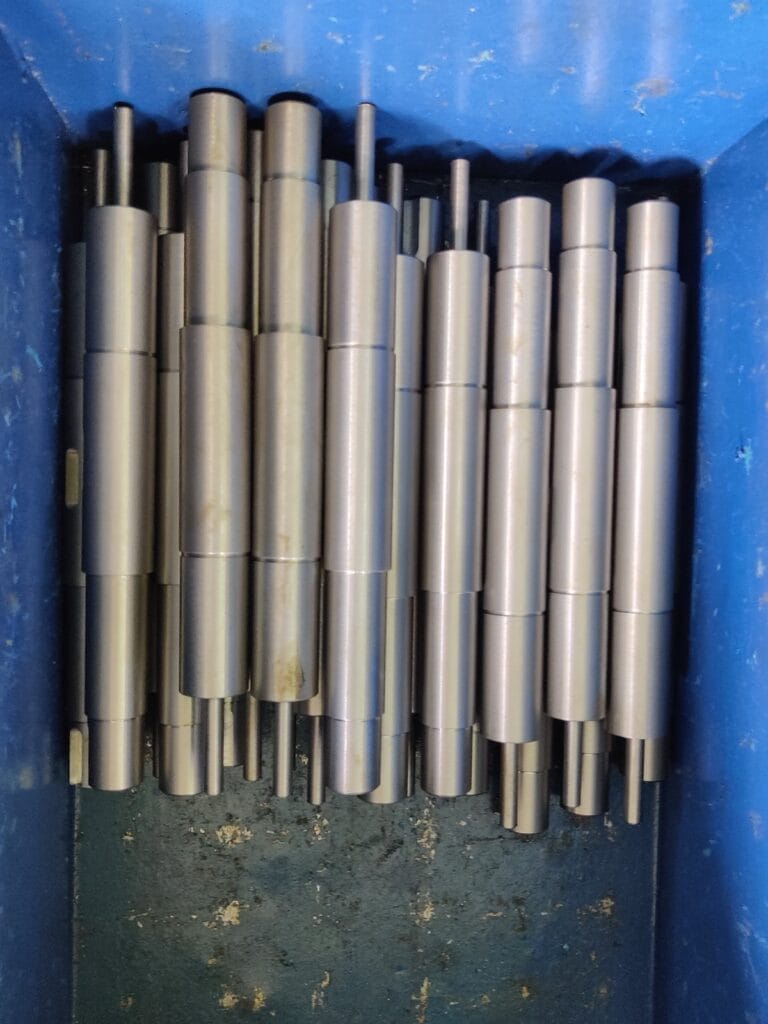
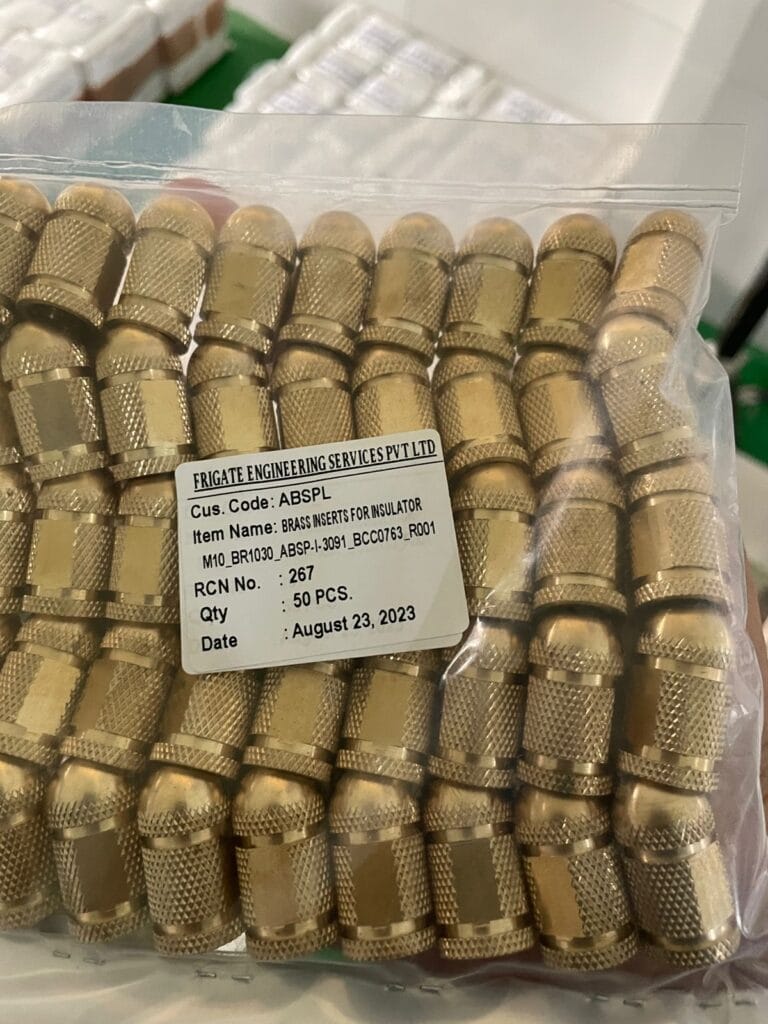
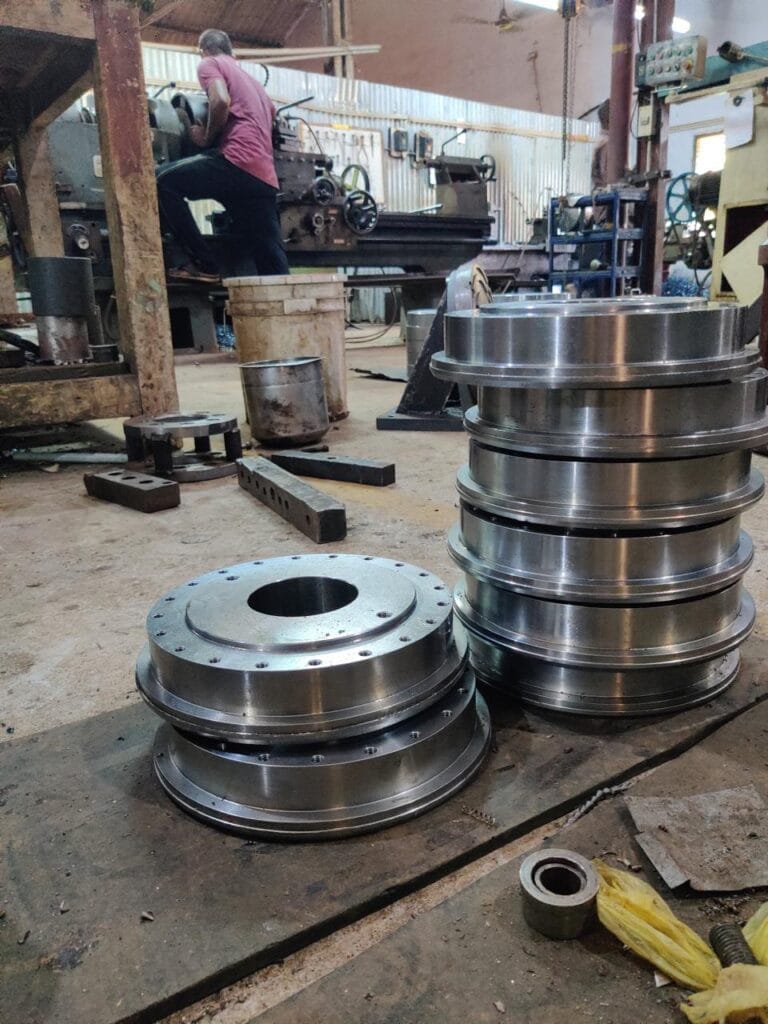
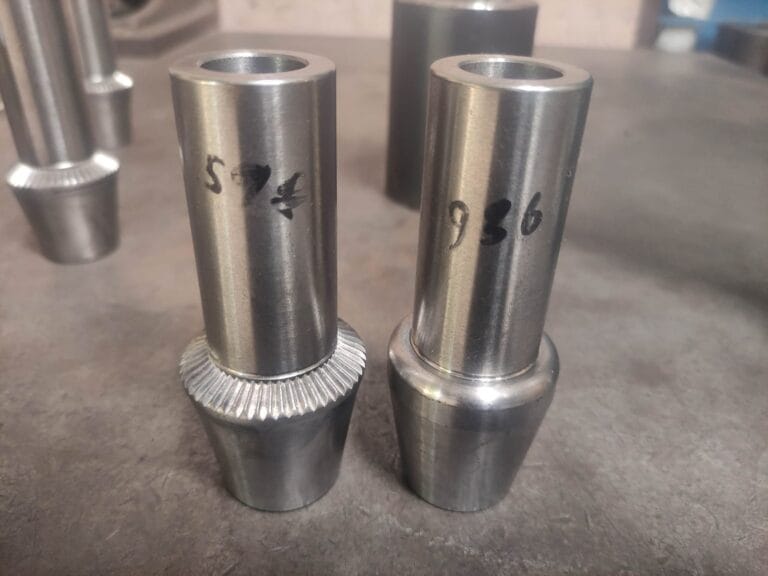
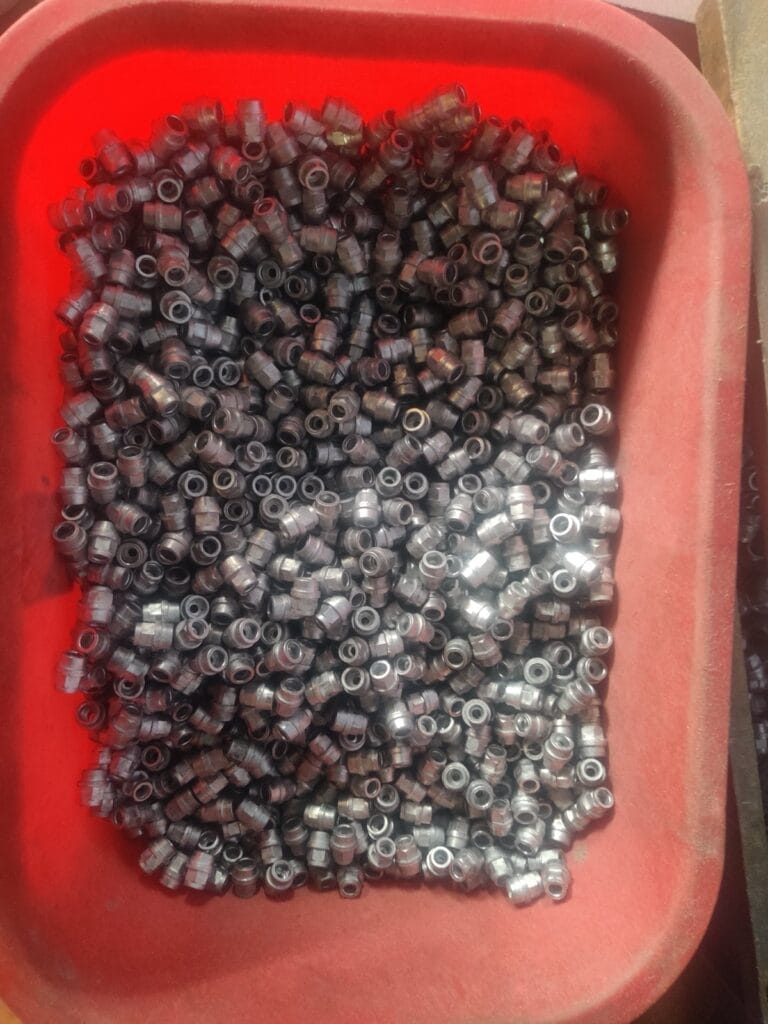
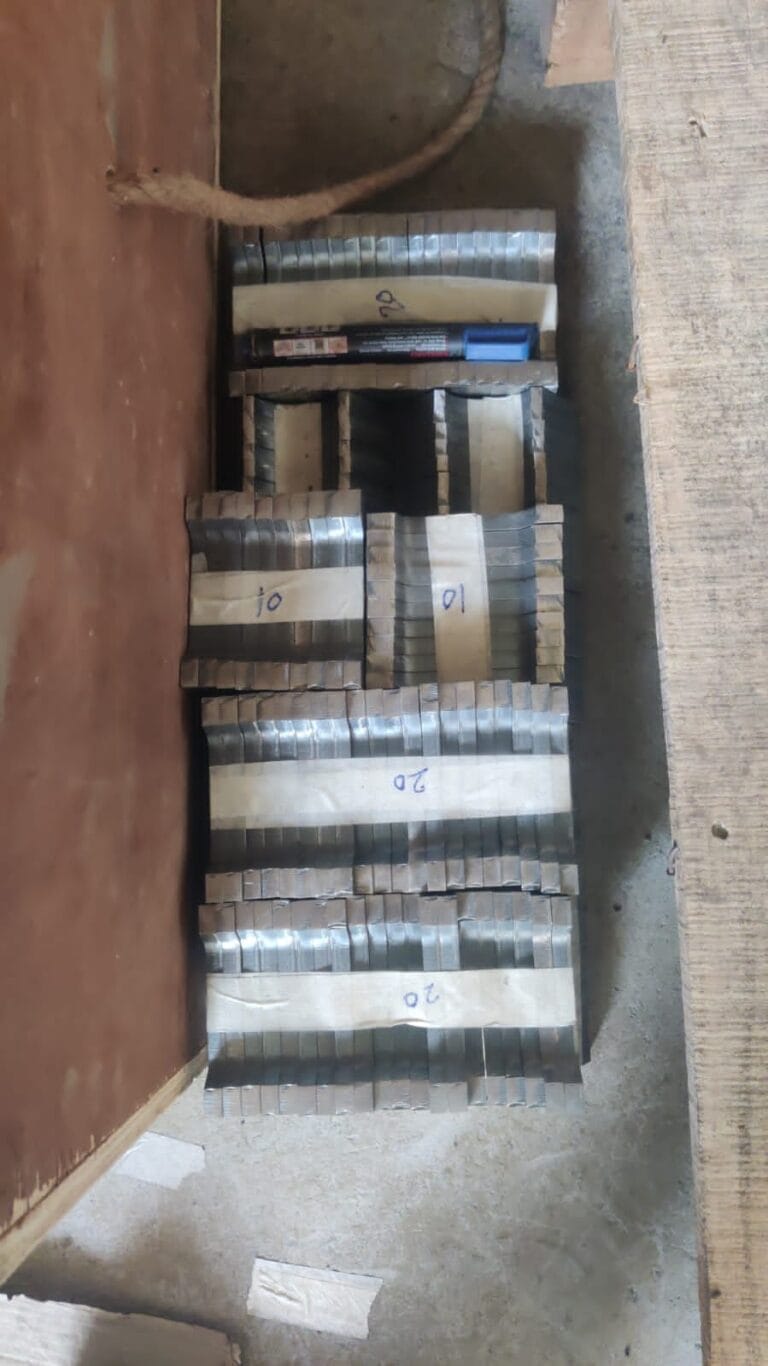
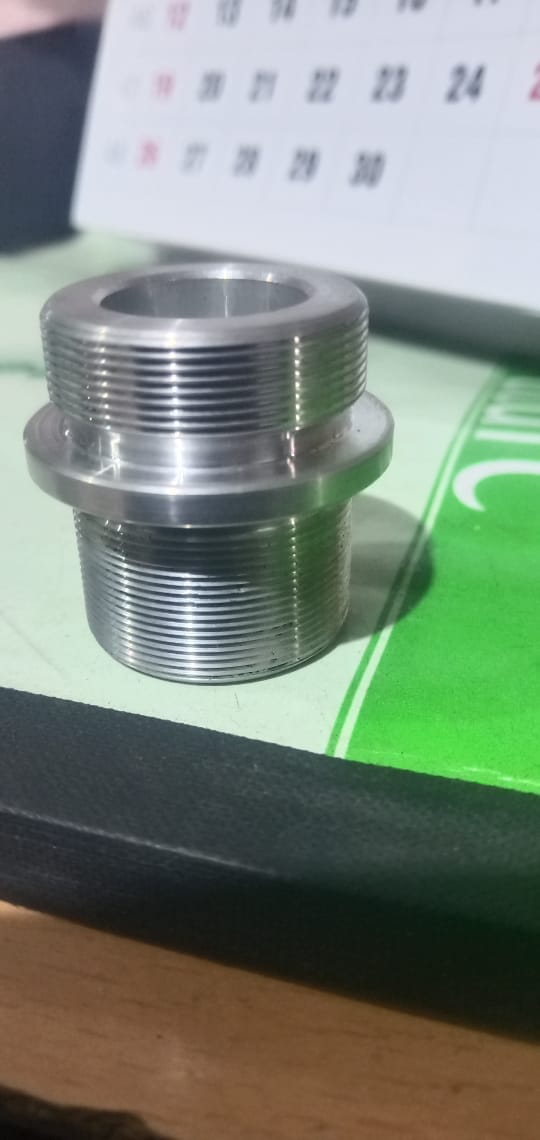
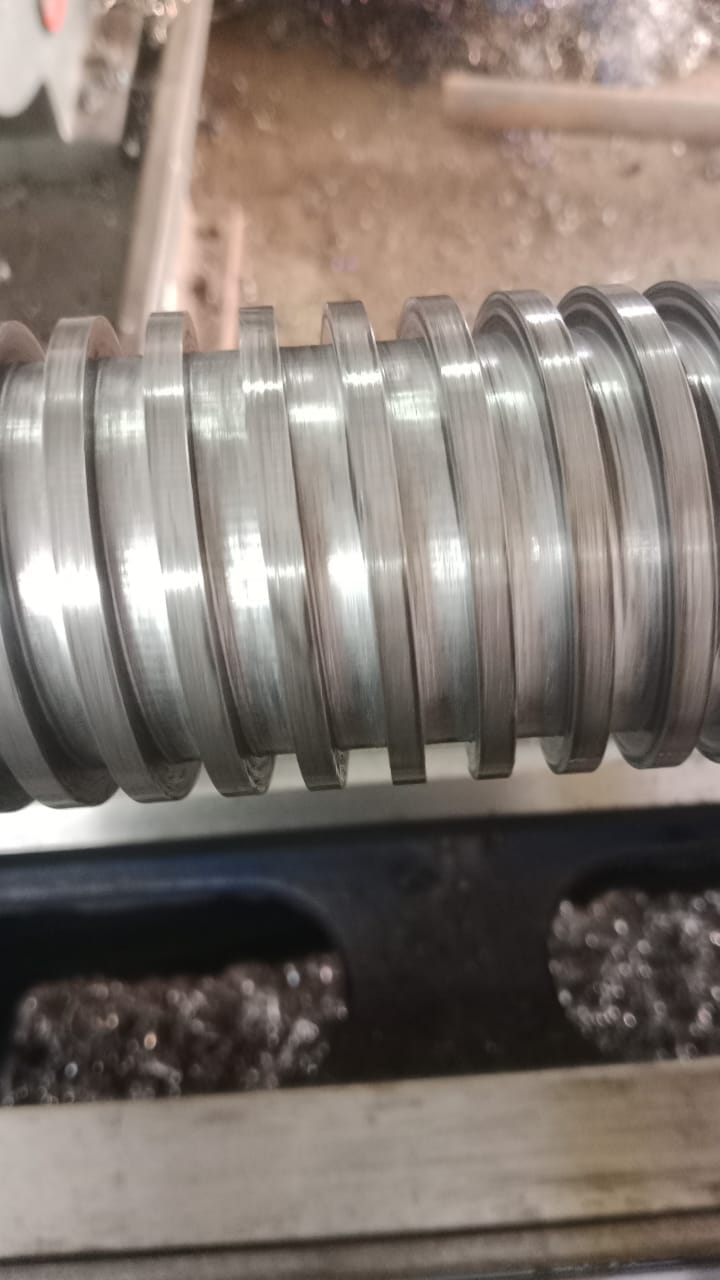
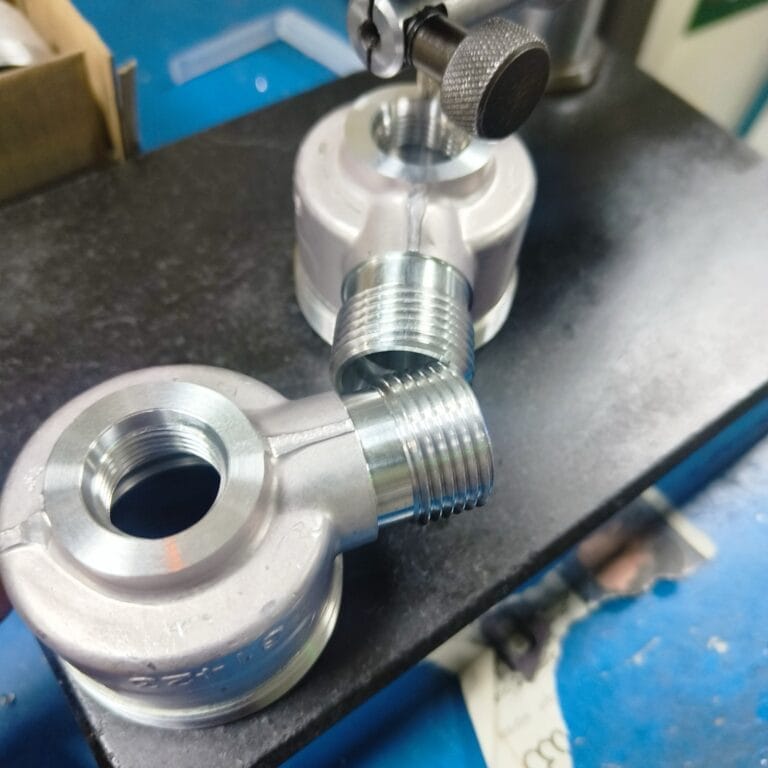
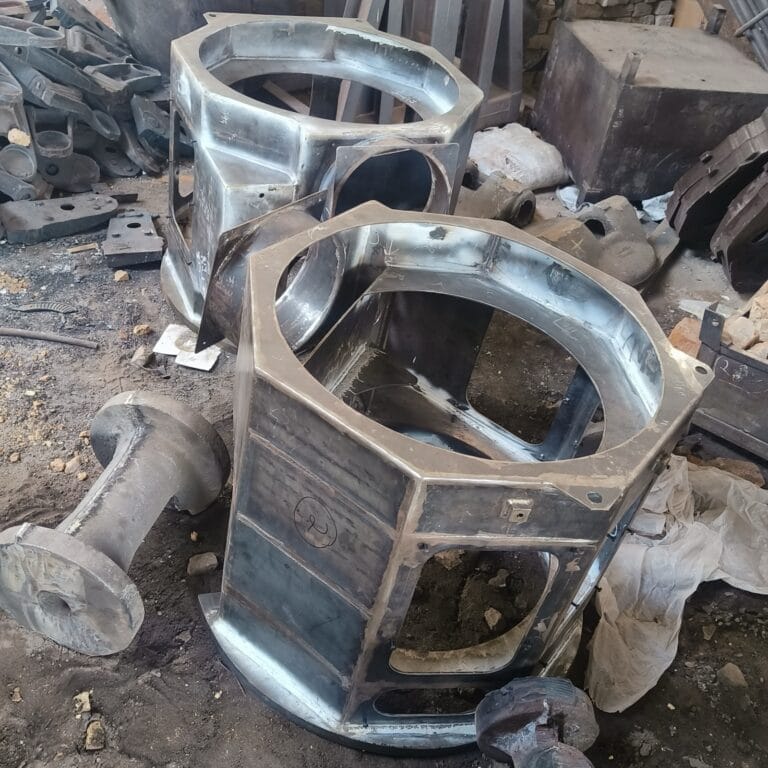
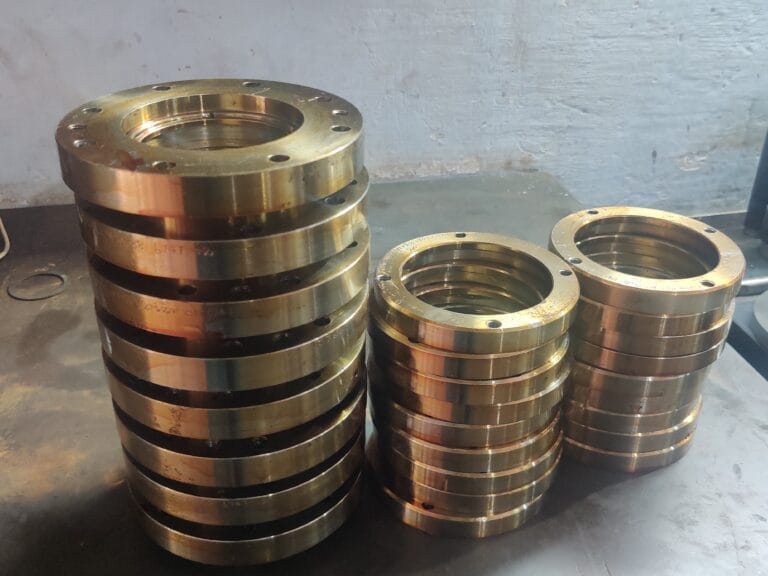
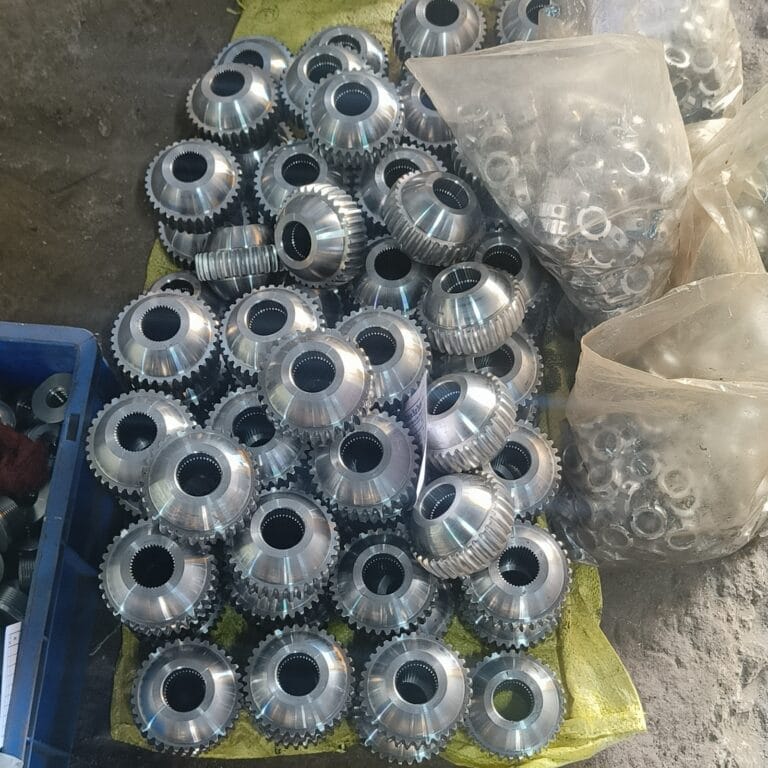
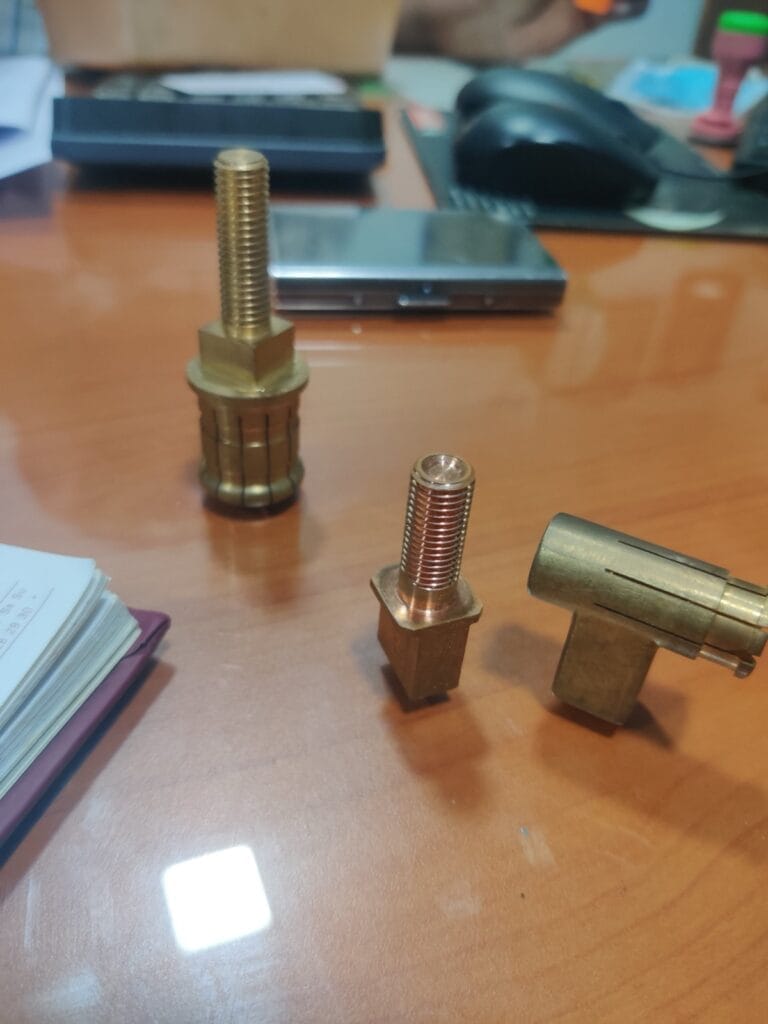
Plastics
Materials
1250 X 1250 MM
Within 10 microns
Engineering Plastics, Polyethylene, Polypropylene, Polyvinyl chloride, Polyethylene terephthalate, Bioplastics, etc.
Rubber
Materials
Natural rubber, Styrene-Butadiene Rubber, Nitrile Butadiene Rubber, Silicone Rubber, Fluorocarbon Rubber, Recycled Rubber, etc.
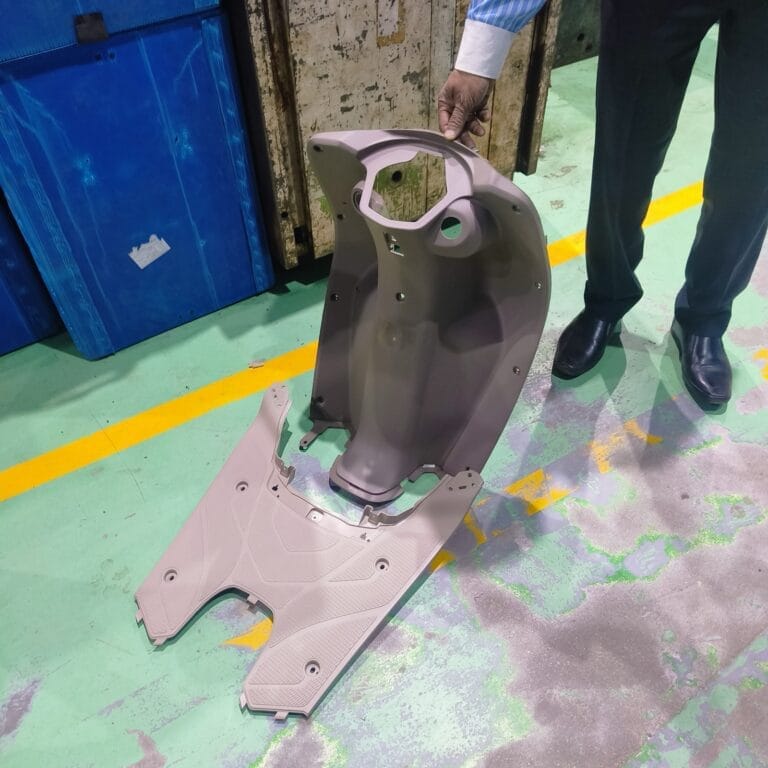
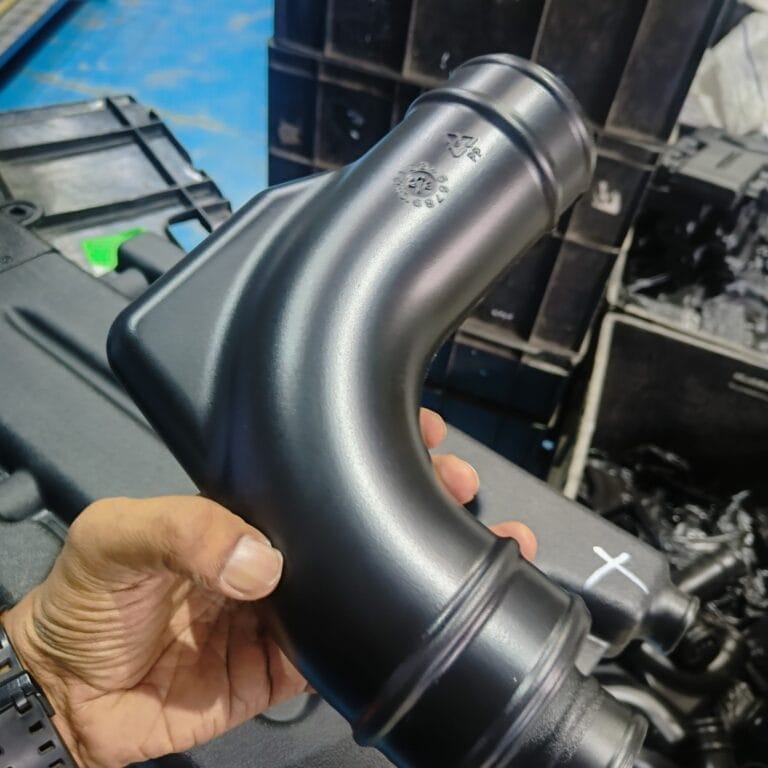
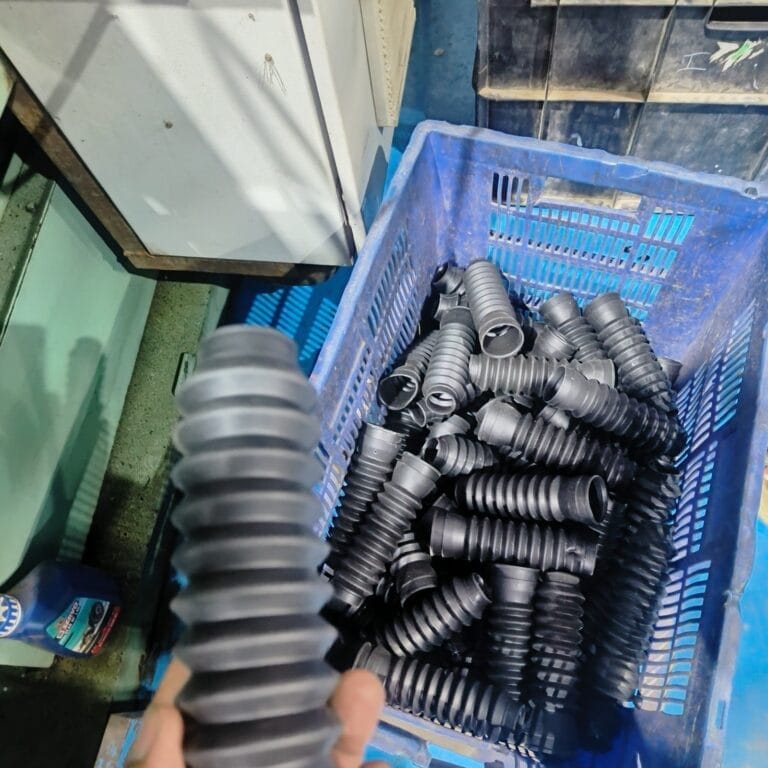
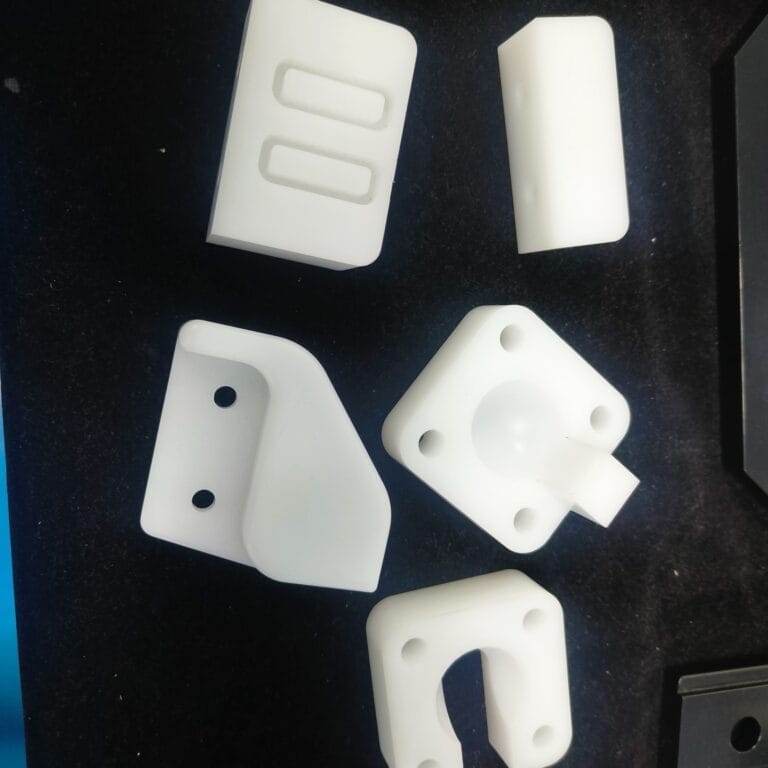
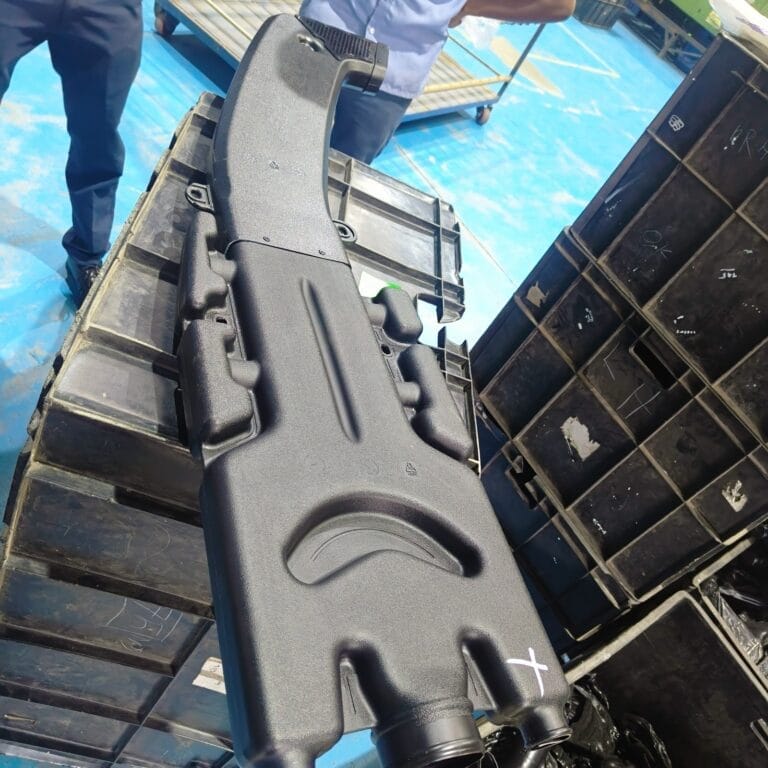
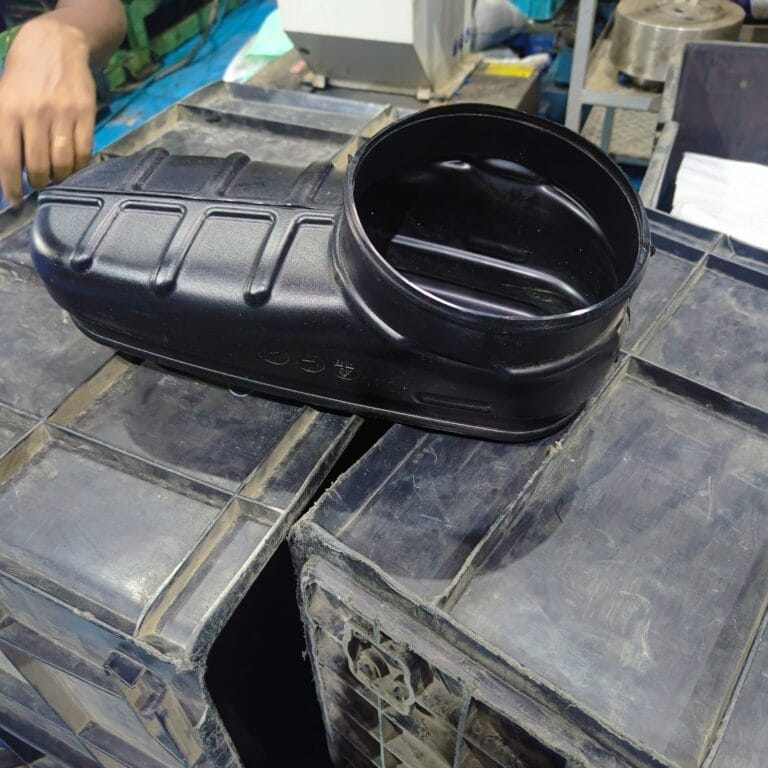
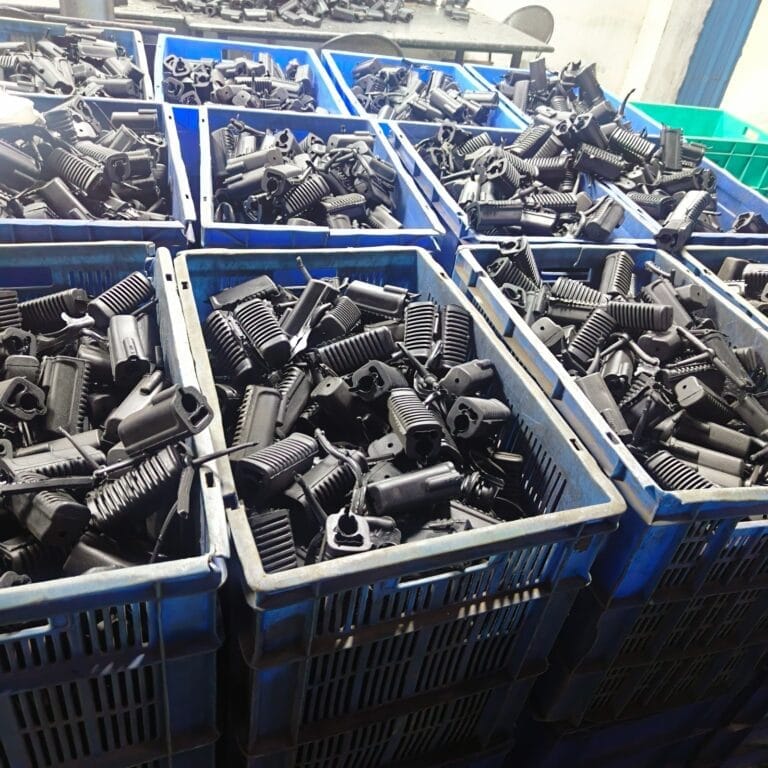
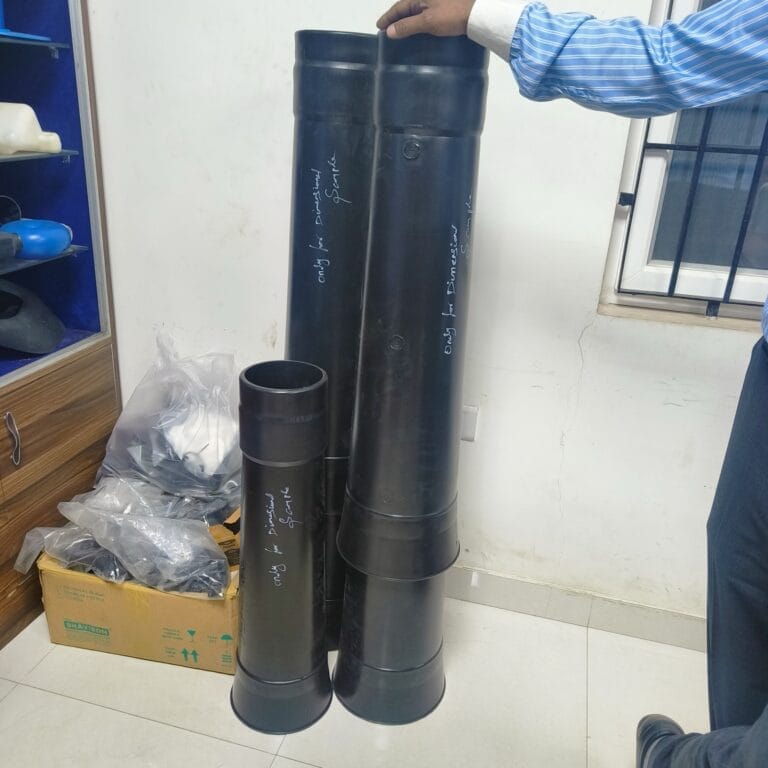
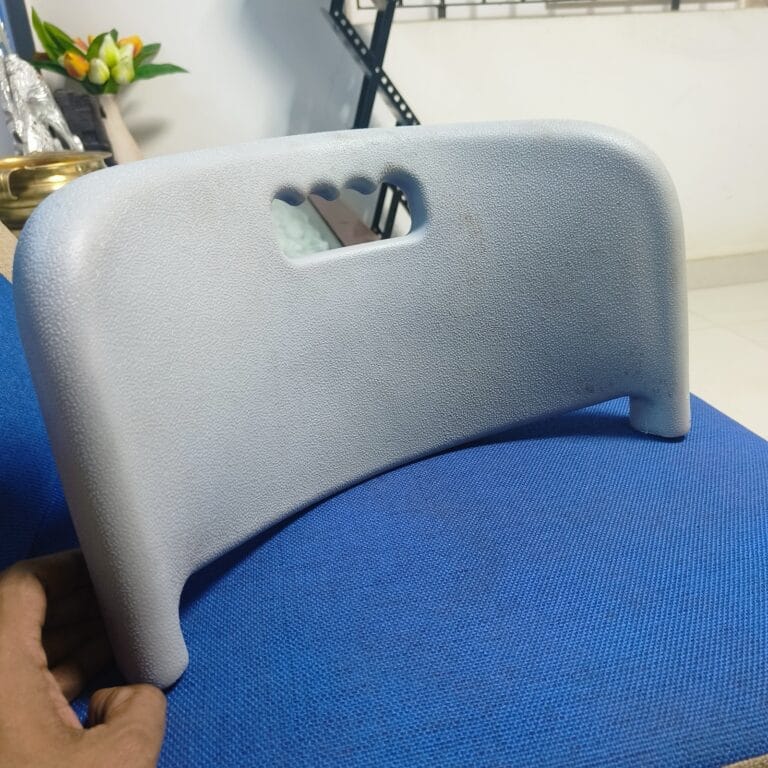
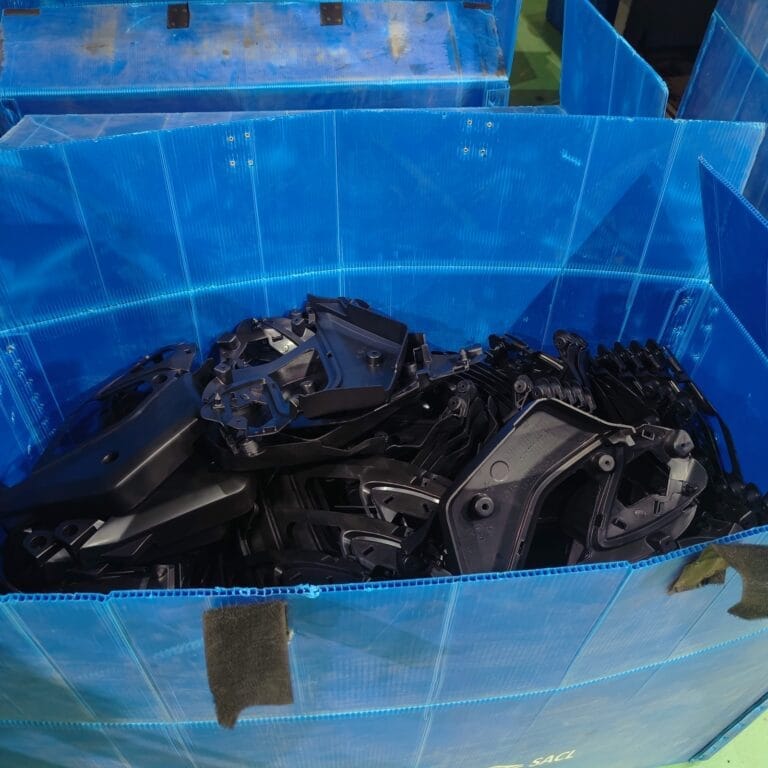
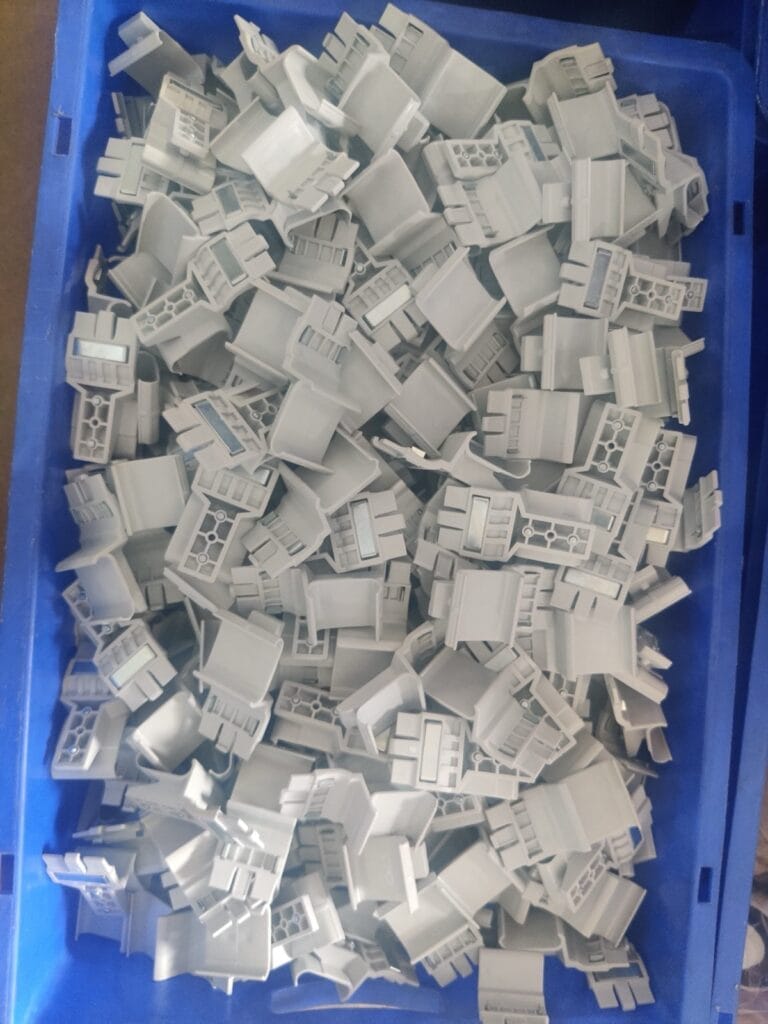
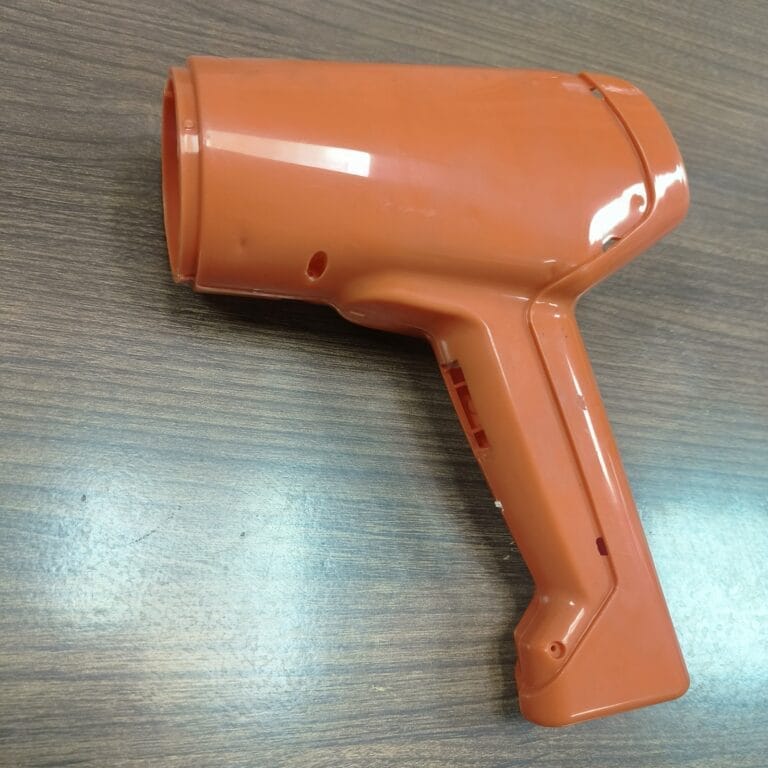
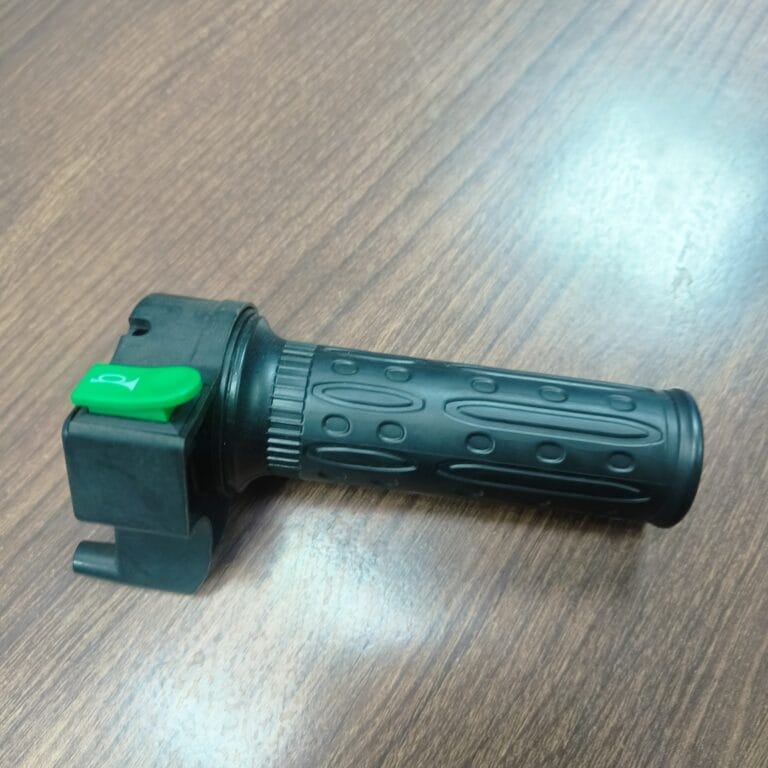
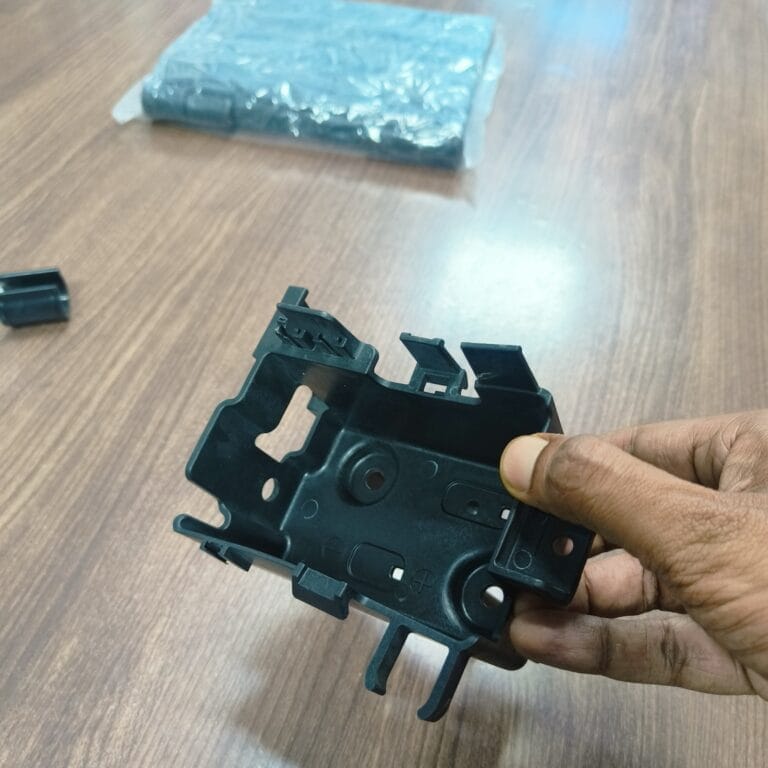
Heavy Fabrication
24000 MT/a
Materials
CS / MS, Alloy steel, Stainless Steel, etc.
Sheet Metal Fabrication
0.8 to 25 mm
Materials
Mild Steel, Stainless Steel, Aluminum, Brass, Copper, etc.
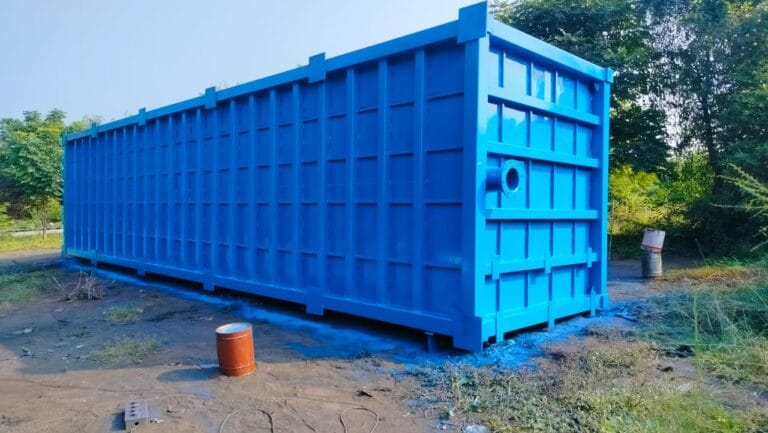
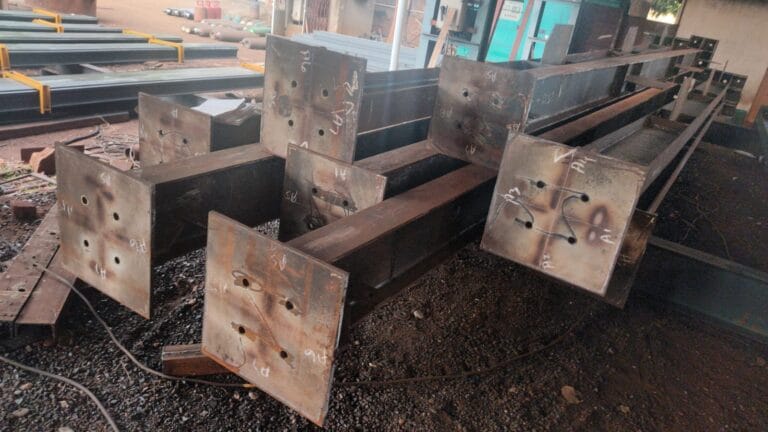
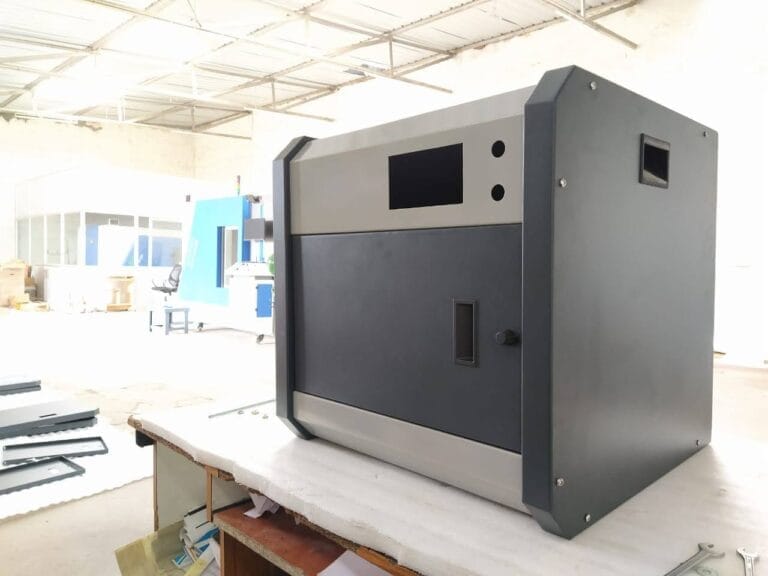
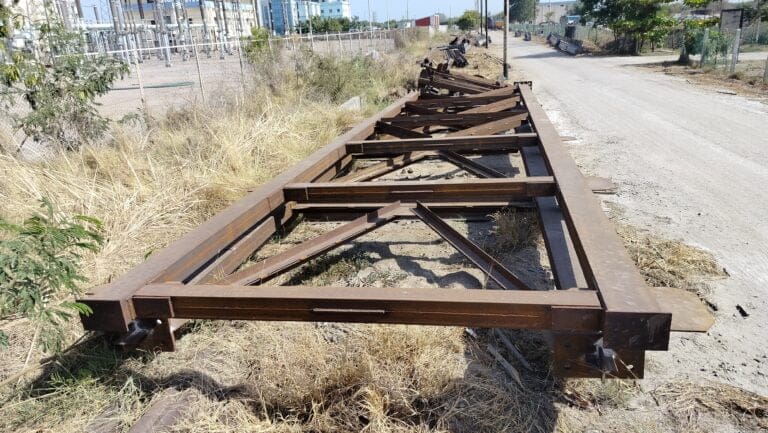
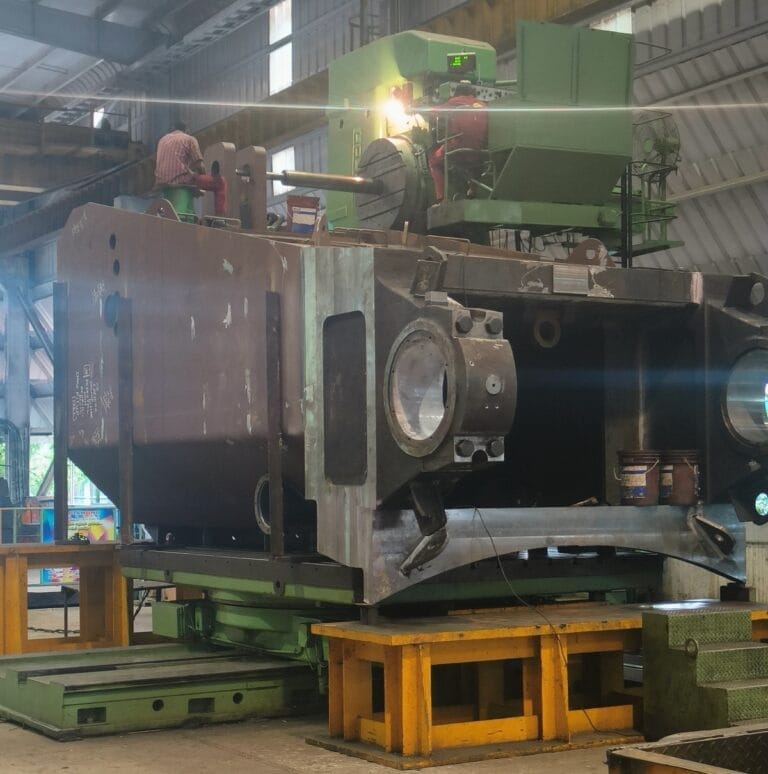
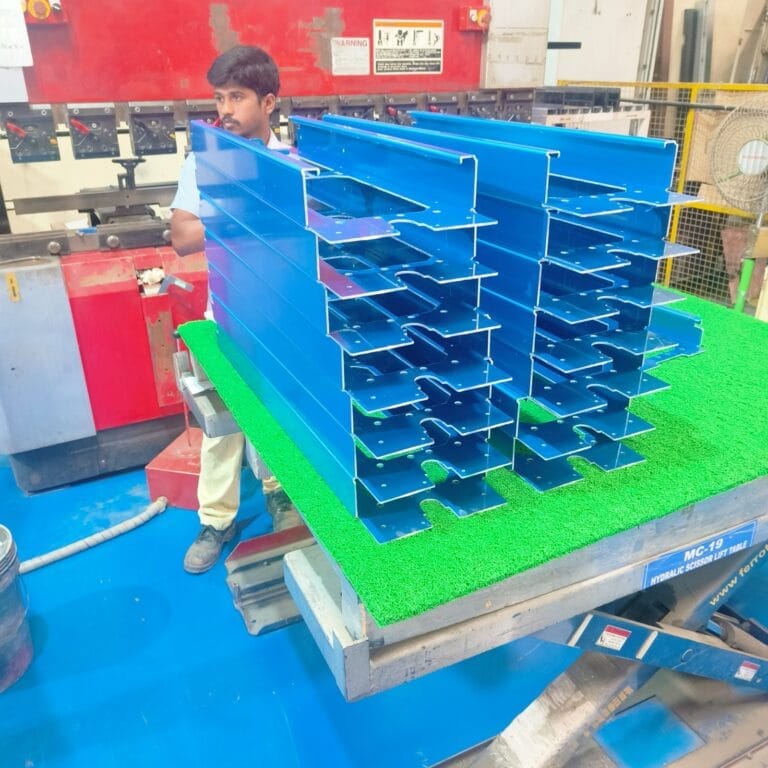
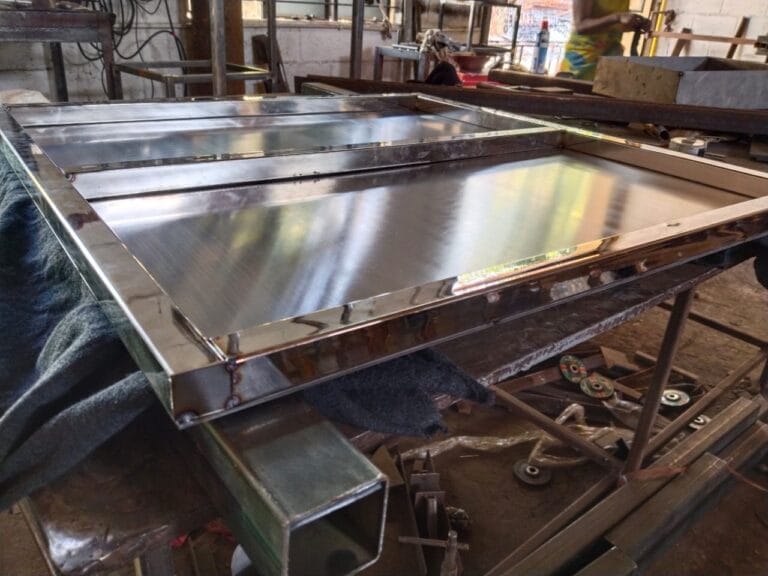
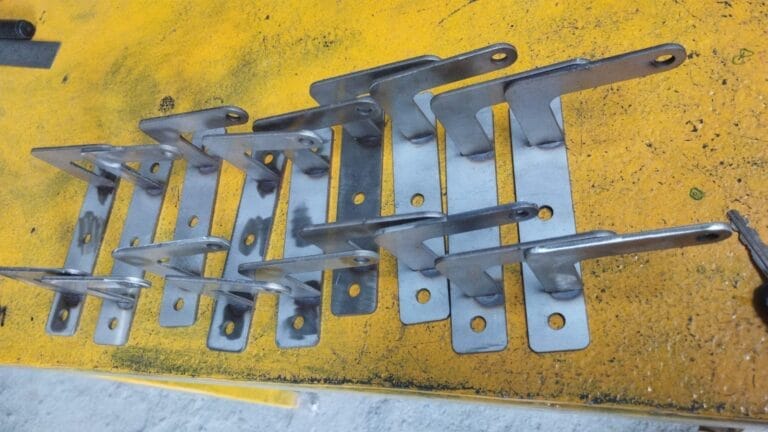
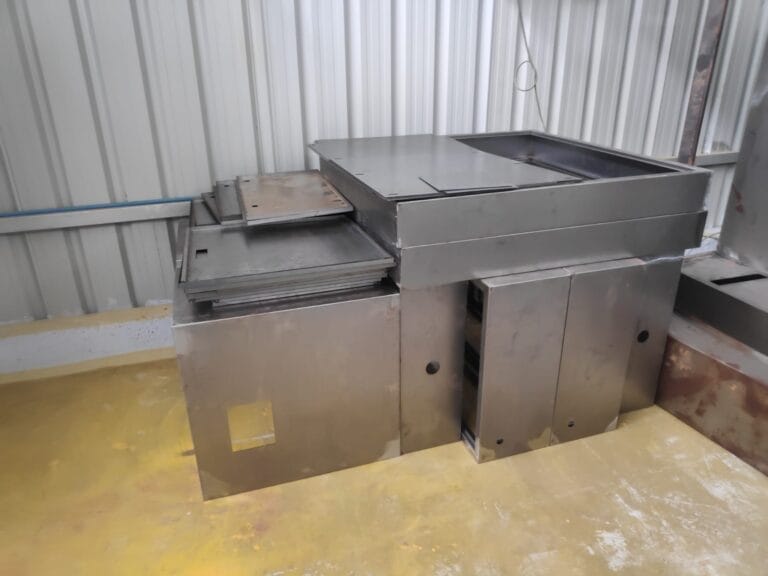
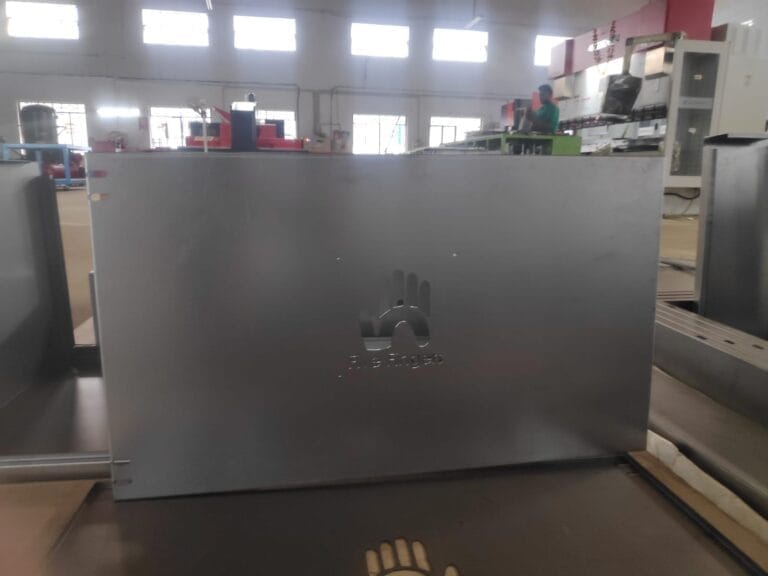
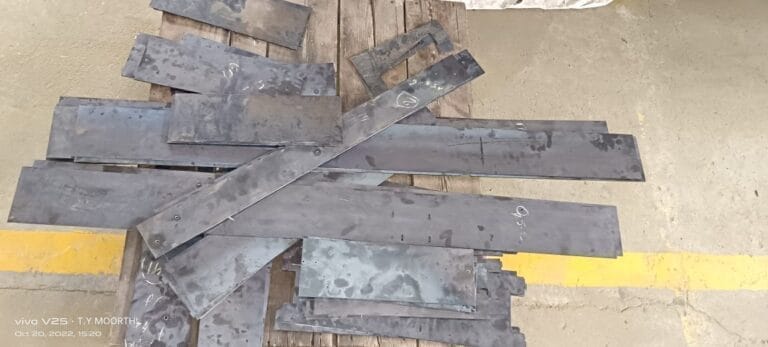
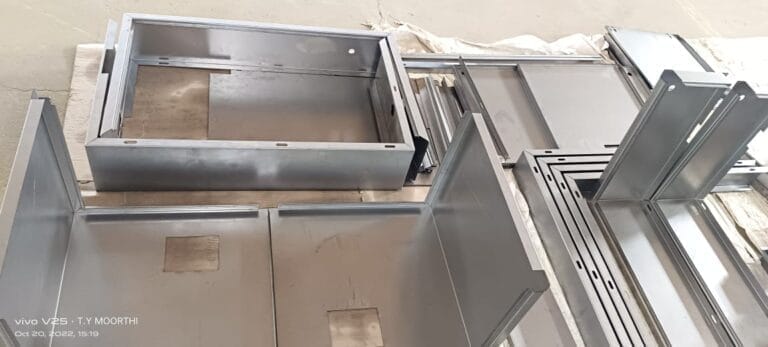
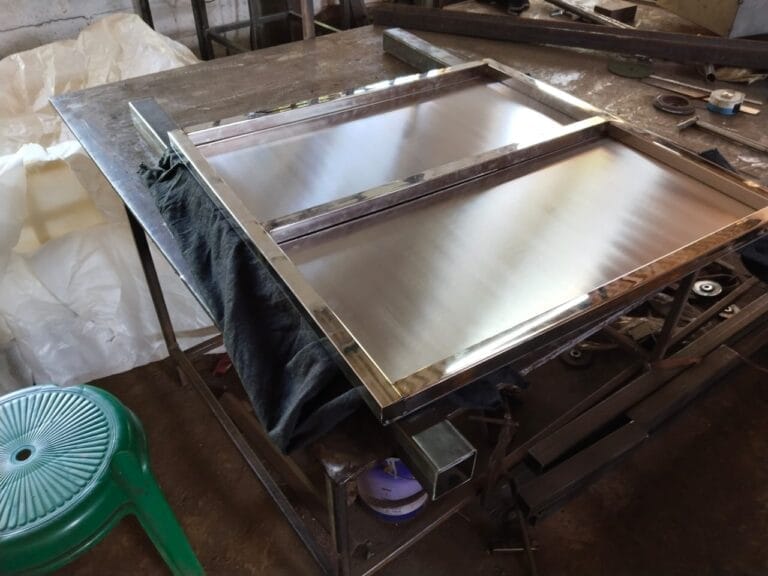
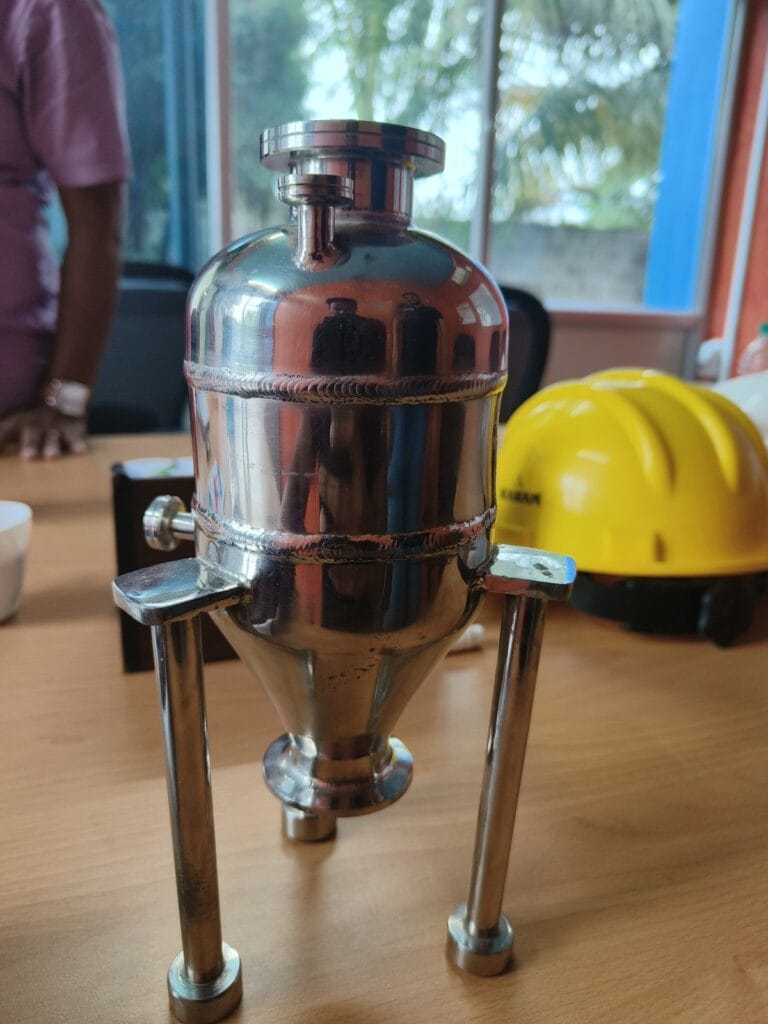
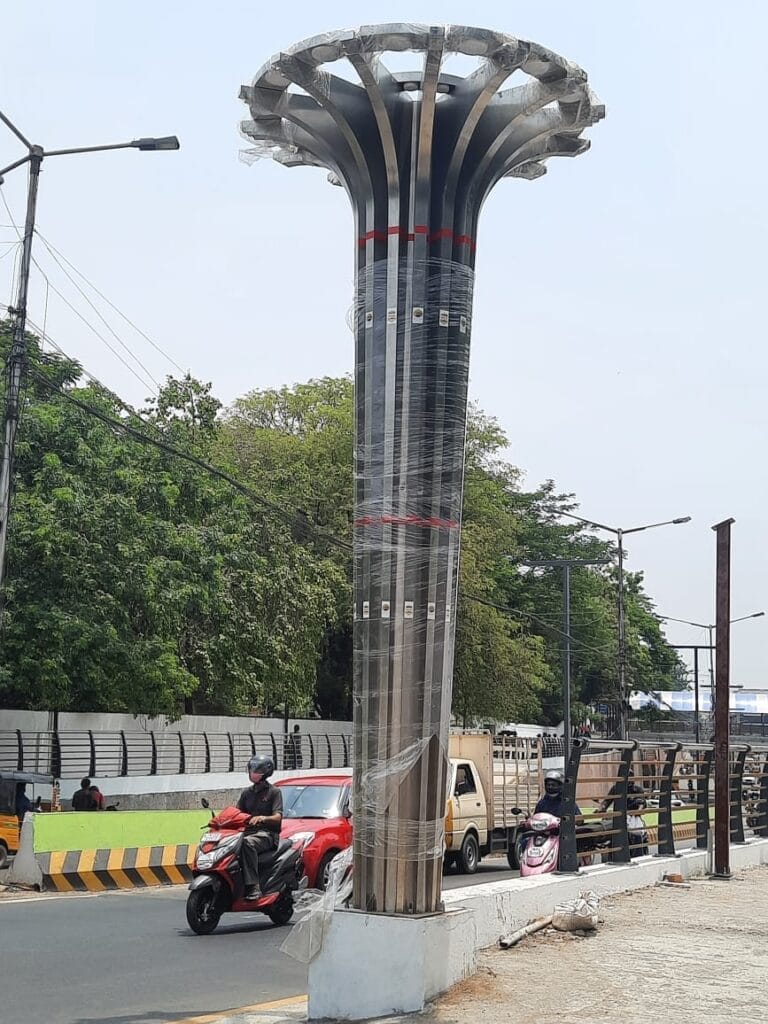
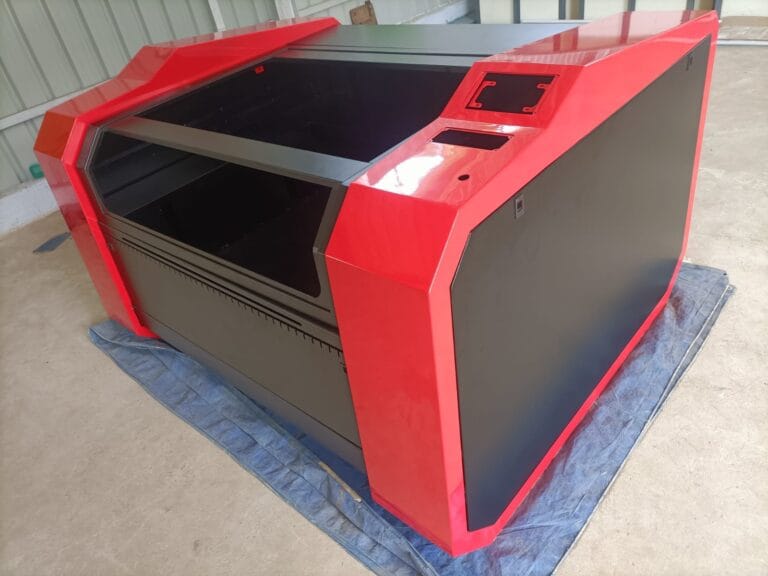
We'd love to Manufacture for you!
Submit the form below and our representative will be in touch shortly.
LOCATIONS
Global Sales Office
818, Preakness lane, Coppell, Texas, USA – 75019
Registered Office
10-A, First Floor, V.V Complex, Prakash Nagar, Thiruverumbur, Trichy-620013, Tamil Nadu, India.
Operations Office
9/1, Poonthottam Nagar, Ramanandha Nagar, Saravanampatti, Coimbatore-641035, Tamil Nadu, India. ㅤ
Other Locations
- Bhilai
- Chennai
- Texas, USA