Precision Die Casting Services
Frigate specializes in creating precision-forming dies to produce high-quality metal parts. Our focus is on delivering accurate, durable dies for efficient metal-forming processes. Beyond supplying dies, we work closely with you to support your product development, ensuring that every die meets exact technical specifications and delivers reliable performance.
Our Clients
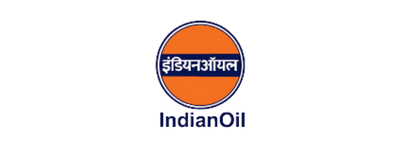
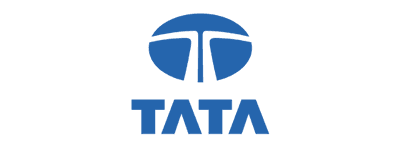
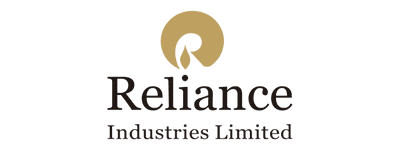

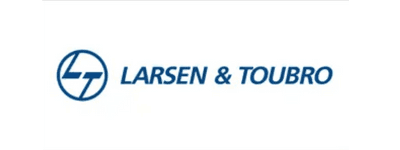
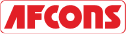

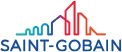
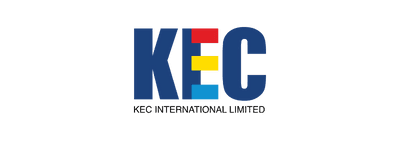

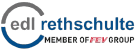
Advantages of Precision Die Casting Services
Precision in Dimensional Control
Pressure die casting delivers parts with exact dimensions, minimizing variations. This ensures uniformity in complex designs, reducing the need for additional machining.
Efficient Production Cycles
The process allows for rapid production of large volumes of components with minimal downtime, making it suitable for mass production with consistent results.
High Structural Integrity
Components made through pressure die casting are strong and dense due to the high pressure applied during the process, reducing internal voids and defects.
Material Flexibility
Pressure die casting works with various metals, including aluminum, zinc, and magnesium, offering different mechanical properties for specific applications without compromising performance.
Comprehensive High-Pressure Die Casting Solutions
Frigate Die Casting Services produces precision castings using a high-pressure die-casting process. We handle all aspects of production, including trimming, machining, and finishing, to meet exact customer requirements. With an experienced team, Frigate provides support from the initial design concept and prototyping to tooling, production, machining, and metal finishing, ensuring that all technical needs are addressed.
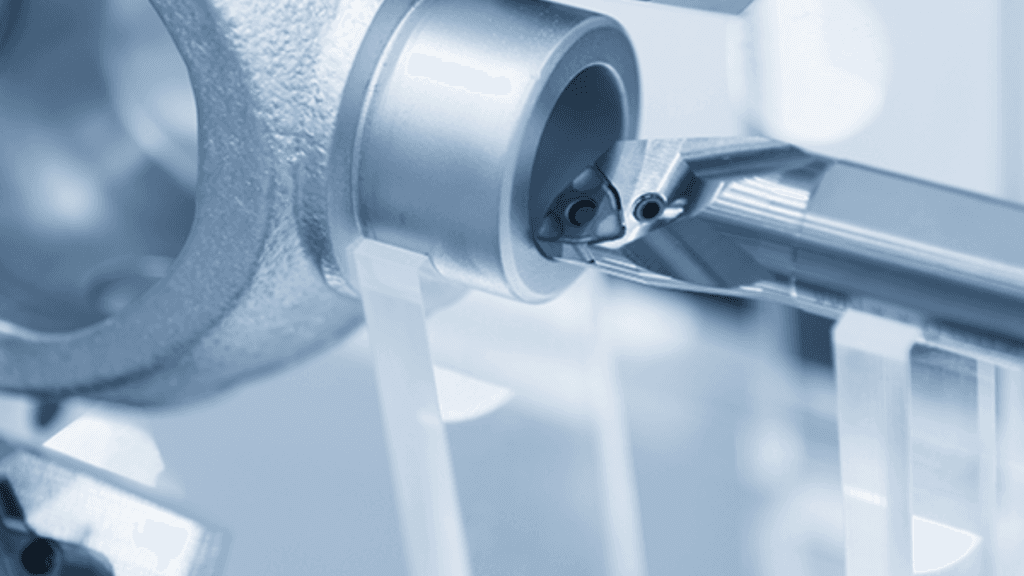
Get Your Quote Now
- Instant Quotation
- On-Time Delivery
- Affordable Cost
Our Precision Die Casting Process
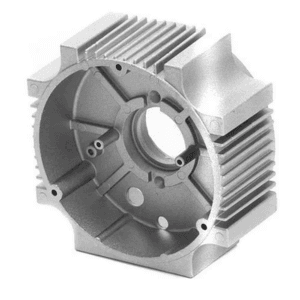
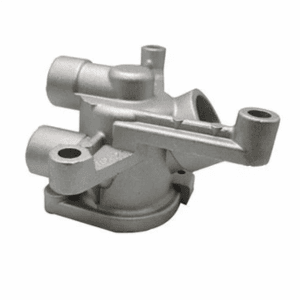
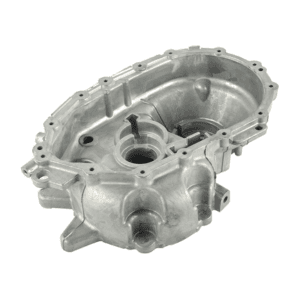
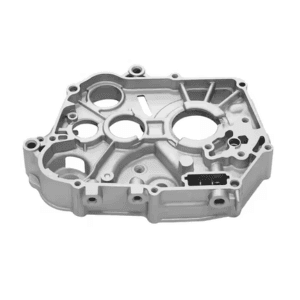
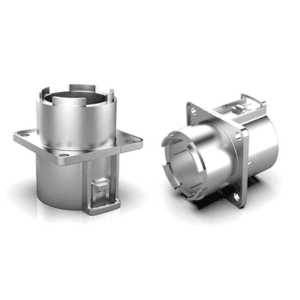
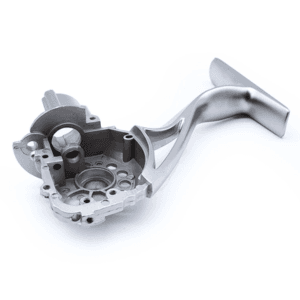
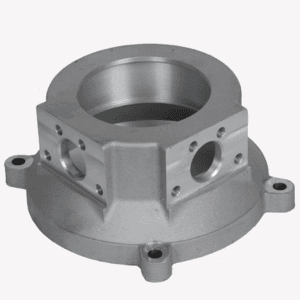
A steel mold, also known as a die, is designed and machined to the exact specifications of the part. It consists of two halves that will form the shape of the final product.
The chosen metal, such as aluminum, zinc, or magnesium, is heated to its melting point in a furnace. The molten metal must be maintained at a specific temperature to ensure proper flow and solidification.
The molten metal is injected into the die cavity under high pressure (typically between 1,500 and 25,000 psi). This pressure ensures the metal fills every mold detail, creating a precise part with smooth surfaces and tight tolerances.
The metal quickly cools and solidifies inside the mold, taking the shape of the die. Cooling times are carefully controlled to ensure consistent part quality.
Once the part has solidified, the die halves are separated, and the casting is ejected from the mold using ejector pins. This step must be carefully executed to avoid damaging the part.
Excess material, such as flash or runners, is trimmed off, and the casting may undergo additional machining to achieve exact dimensions or surface finishes.
The cast part is inspected for dimensional accuracy and surface quality. It may also undergo additional finishing processes, such as coating or polishing, to meet specific technical requirements.
Post-Processing Services in Precision Die Casting
Precision die casting doesn’t end with casting alone. To enhance durability, aesthetics, and functionality, various post-processing techniques are applied. These processes improve surface finish, dimensional accuracy, and material properties to meet industry-specific standards.
Aerospace (engine mounts, hydraulic housings), Medical (implants, prosthetics)
Electronics (micro-components, circuit housings), Automotive (gearbox components)
Aerospace (structural reinforcements), Defense (precision optics casings)
Automotive (turbine housings, suspension arms), Industrial (hydraulic components)
Medical (surgical instruments, dental components), Luxury Goods (watch casings)
Automotive (decorative trims, brake components), Aerospace (corrosion-resistant fasteners)
Aerospace (lightweight panels, UAV structures), Marine (saltwater-resistant parts)
Industrial (heavy machinery covers), Consumer (household appliances)
Automotive (chassis frames, engine covers), Aerospace (fuselage panels)
Aerospace (load-bearing components), Defense (ballistic armor parts)
Automotive (fuel system housings, transmission cases), Aerospace (leak-proof castings)
Electronics (PCB casings), Automotive (engine valve assemblies)
Methoding in Precision Die Casting
Automotive (engine blocks, transmission cases), Aerospace (aircraft brackets)
Electronics (heat sinks, LED enclosures), Consumer Goods (smartphone casings)
Medical (surgical implants, diagnostic device housings)
Automotive (brake calipers, structural brackets), Aerospace (fuel system components)
Electronics (precision enclosures), Defense (firearm components)
High-precision applications (robotic arms, semiconductor casings)
Consumer Goods (camera bodies, laptop frames), Medical (biomedical enclosures)
Aerospace (turbine blades, structural mounts), Automotive (cylinder heads)
High-volume production (gear housings, hydraulic valve bodies)
Heavy Machinery (engine housings, industrial pumps), Marine (propeller hubs)
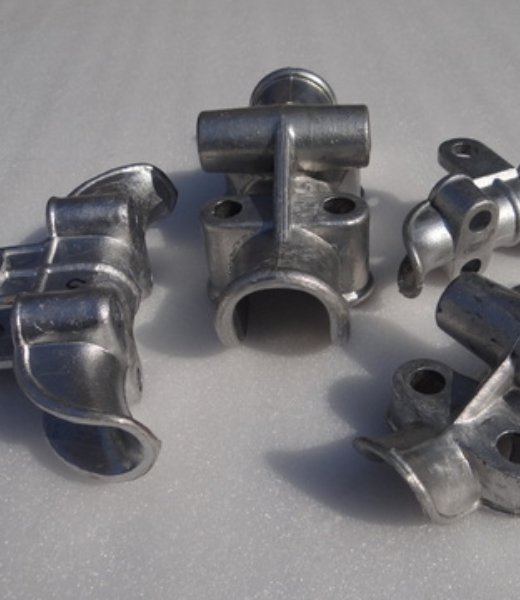
Precision Die Casting Materials
Several materials are commonly used in pressure die casting services due to their ability to be shaped under high pressure. These metals are chosen based on their mechanical properties and performance under the high-pressure die-casting process.
Lightweight and corrosion-resistant, aluminum is widely used for its excellent strength-to-weight ratio. It also has good thermal and electrical conductivity.
Known for its durability and low melting point, zinc allows for precision casting with intricate details and provides excellent dimensional stability.
One of the lightest structural metals, magnesium offers a balance of strength and low density, making it suitable for high-performance applications.
High in strength and thermal conductivity, copper is used where electrical and thermal performance is critical.
A copper-zinc alloy, brass is often used for its strength and resistance to corrosion, especially in water-based environments.
Custom Pressure Die Casting Services
Material and dimensional accuracy are critical for high-performance components, and deviations can lead to costly failures. At Frigate, our custom pressure die-casting service ensures tight tolerances and consistent material properties in every part. We use aluminum, zinc, magnesium, and copper alloys to match your application needs. We guarantee that each casting meets exact technical specifications through detailed engineering analysis and rigorous quality control, ensuring reliability and performance in demanding environments.

Compliance for Precision Die Casting Services
Frigate ensures its precision casting services comply with strict industry standards, guaranteeing high-quality, reliable components for various applications. We adhere to the latest regulations and certifications, ensuring all products meet stringent requirements for performance, material integrity, and dimensional accuracy. Our commitment to compliance supports industries such as aerospace, automotive, and defense, where quality and safety are paramount.
Key Compliance Certifications
Ensures consistent quality management and continuous improvement processes.
Meets aluminum alloy casting standards, ensuring strength and durability for aerospace and automotive applications.
Complies with EU regulations to restrict hazardous substances in electronic components.
Adheres to regulations controlling the export of casting solutions for military and defense sectors.
Ensures precise tolerance standards for critical aerospace and electronic components.
Aerospace quality management system certification ensuring reliability and compliance with safety and performance standards.
Tonnage / Capacity in Precision Die Casting
Precision die casting machines come in various tonnage capacities to accommodate different component sizes, material types, and complexity levels. The selection of tonnage is crucial for achieving optimal part integrity, minimizing defects, and maintaining cost efficiency.
Automotive (engine blocks, transmission cases), Aerospace (structural housings)
Medical (implants, surgical instruments), Industrial (valve bodies, pump housings)
Electronics (heat sinks, connector housings), Consumer Goods (smartphone casings)
Aerospace (brackets, turbine blades), Defense (ballistic-grade components)
Automotive (aluminum wheels, brake calipers), Industrial (hydraulic fittings)
High-volume production (lighting fixtures, small gear housings)
Aerospace (landing gear components), Heavy Machinery (gearbox housings)
Automotive (complex engine components), Electronics (thin-walled casings)
Consumer Electronics (laptop bodies, LED housings), Medical (biomedical enclosures)
Precision small components (watch cases, micro-gears, electrical contacts)
Dimensions in Precision Die Casting
Precision die casting allows for complex geometries with tight tolerances, ensuring high accuracy and repeatability. Dimensional parameters are critical for meeting industry standards, optimizing material usage, and ensuring component performance.
Aerospace (fuselage brackets, landing gear components), Heavy Machinery (gear housings)
Electronics (micro-components, connectors), Medical (surgical implants)
Automotive (engine covers, brackets), Consumer Electronics (laptop casings)
Aerospace (critical load-bearing parts), Automotive (precision engine components)
Medical (diagnostic device housings), Industrial (valve components)
Automotive (cylinder heads, transmission casings), Defense (firearm components)
Aerospace (engine mounts, actuator housings), Robotics (motion control parts)
Automotive (axle hubs, turbocharger housings), Electronics (precision rotary encoders)
High-precision applications (thin-walled enclosures, smartphone frames)
Medical (dental tools, orthopedic implants), Consumer (wearable tech casings)
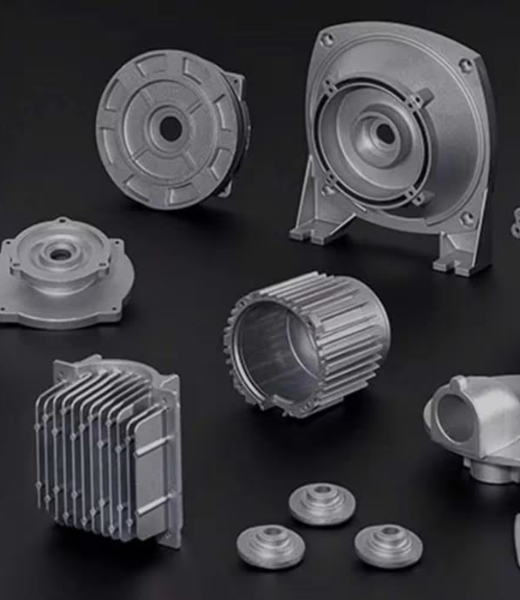
Tolerance for Precision Die Casting Services
Ensures that castings maintain strict adherence to design dimensions for critical applications.
Consistent wall thickness across castings to maintain mechanical strength and uniformity.
Achieves high-quality surface texture, suitable for functional or aesthetic requirements.
Precise placement of holes for perfect fitment in assembled systems, reducing rework.
Maintains shape control to ensure accurate alignment and proper assembly of components.
Accounts for slight material variation during cooling, ensuring consistent weight for performance.
Precision in alloy composition ensures desired mechanical properties, such as strength and corrosion resistance.
Ensures the accurate formation of internal and external threads for secure mechanical connections.
Controls the alignment of parting lines in multi-part molds for proper fit and finish.
Adjustments made for material shrinkage during cooling, ensuring final dimensions match design specifications.
Ensures low porosity in castings, critical for maintaining structural integrity and strength.
Ensures the linearity of components, critical for assemblies requiring precise alignment.
Guarantees circularity for parts like shafts and rings, essential for smooth mechanical operation.
Controls deformation that may occur during solidification, ensuring high geometric accuracy.
Ensures precise angularity in cast parts to meet strict design requirements for proper fit and function.
Guarantees the flatness of casting surfaces to ensure they can mate correctly with other parts.
Ensures uniform hardness across castings for consistent wear resistance and material properties.
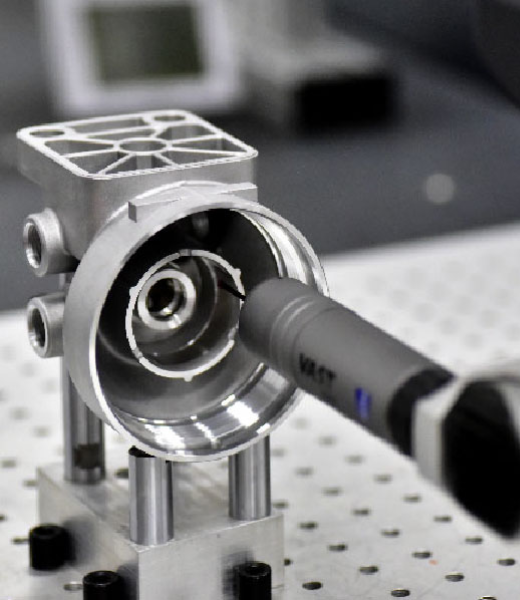
Quality Testing Standards for Precision Die Casting Services
Non-destructive testing to detect internal porosity and voids, ensuring the casting's structural integrity.
Determines the casting’s ability to withstand tensile stress, measuring yield strength and ultimate tensile strength.
Measures material hardness to assess resistance to deformation and wear, critical for high-performance applications.
Verifies that the final dimensions of the casting are within tolerance after solidification and cooling.
Employs laser scanning to measure 3D geometry and verify that parts conform to the required geometric tolerances.
Measures circularity for critical components such as shafts and rings to ensure precise alignment and functionality.
Ensures the precision and quality of internal and external threads using precision gauges for proper fitment.
Evaluates distortion and residual stresses through thermal or mechanical methods to ensure the casting retains its shape post-cooling.
Uses precise tools to measure angles and verify that cast components meet specified angular tolerances.
Measures flatness deviations in critical surfaces to ensure proper mating and dimensional accuracy.
Analyzes the grain structure, phase distribution, and material uniformity using microscopy to ensure optimal material properties.
Assesses a casting's resistance to fatigue under cyclic loading, simulating real-world operational conditions.
Measures the casting’s ability to absorb energy during sudden impact, ensuring durability in high-stress environments.
Inspection Techniques in Precision Die Casting
Value/Range - 1 - 100 µm resolution
Aerospace (turbine blades, aircraft brackets), Automotive (engine blocks)
Value/Range - ±5 µm accuracy
Medical (surgical implants), Electronics (semiconductor casings)
Value/Range - 0.1 - 50 MHz frequency range
Defense (firearm components), Industrial Machinery (hydraulic housings)
Value/Range - 0.5 - 10 µm sensitivity
Marine (propeller housings), Aerospace (structural mounts)
Value/Range - Up to 3 mm defect depth
Automotive (safety-critical components), Industrial Equipment (gearboxes)
Value/Range - ±2 - 10 µm precision
Aerospace (landing gear parts), High-precision Robotics (motion control components)
Value/Range - Ra 0.05 - 25 µm
Electronics (heat sinks, LED enclosures), Medical (biomedical enclosures)
Value/Range - ±5 - 20 µm deviation
Automotive (chassis components), Consumer Goods (laptop frames)
Value/Range - ±0.1% element detection
Aerospace (high-strength alloys), Energy (wind turbine hubs)
Value/Range - 8 - 14 µm IR wavelength
Power Electronics (battery enclosures), High-speed Motorsports (turbo housings)
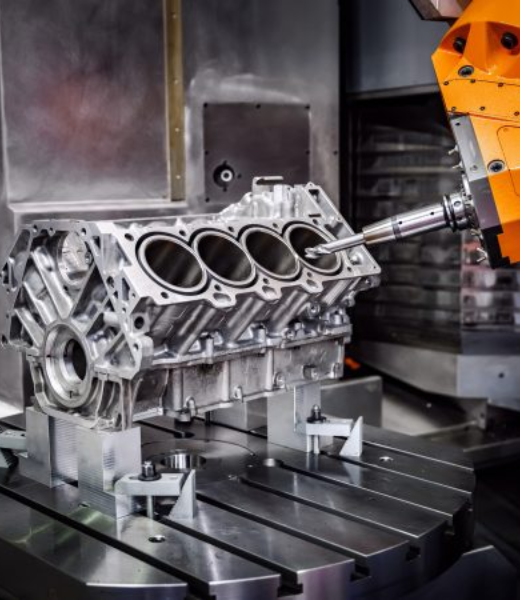
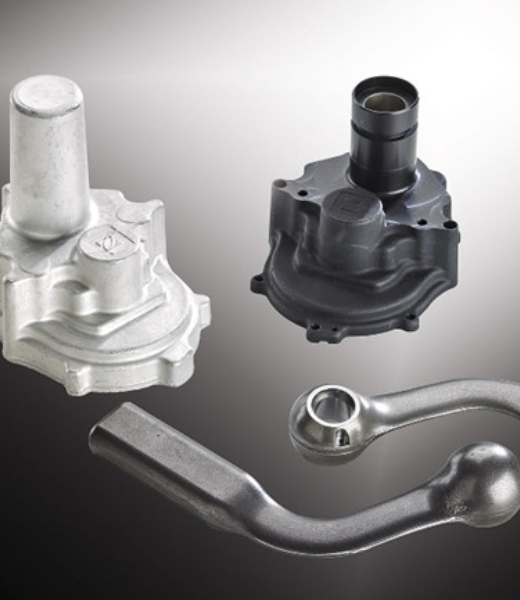
Industry Applications of Precision Die Casting
Weight reduction, thermal management, high production efficiency
High strength-to-weight ratio, extreme temperature resistance, impact durability
Precision miniaturization, EMI/RFI shielding, excellent thermal conductivity
Biocompatibility, complex micro-scale geometries, sterile finishing options
High wear resistance, dimensional stability, optimized strength-to-weight ratio
Corrosion resistance, excellent electrical conductivity, long operational lifespan
Superior thermal management, high-frequency shielding, extreme environmental durability
Extreme heat resistance, high mechanical stress endurance, aerodynamic precision
Saltwater corrosion resistance, high fatigue strength, precision for deep-sea applications
Ultra-high precision, optimized thermal dissipation, enhanced structural integrity
Integrated Technical Expertise for Die Casting Projects
Frigate’s full-service die casting capabilities ensure that every technical aspect of your project is handled precisely. From the initial design phase, we focus on optimizing your components for manufacturability, ensuring efficient material use and dimensional accuracy. Our engineers collaborate closely with you to fine-tune the design, accounting for thermal expansion, shrinkage, and complex geometries.
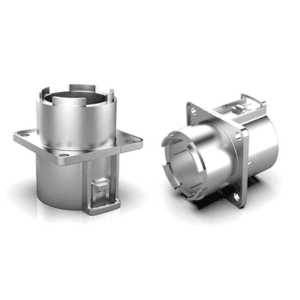
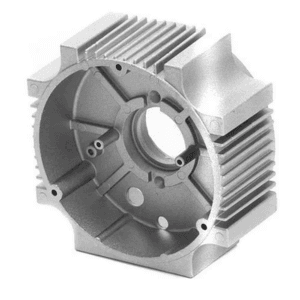
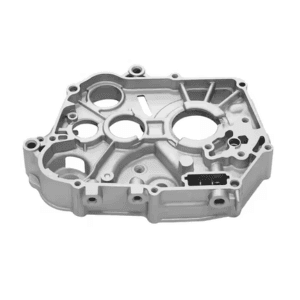
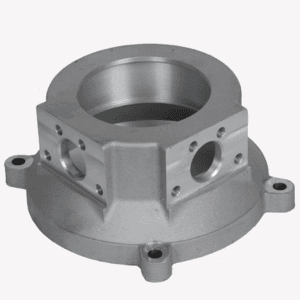
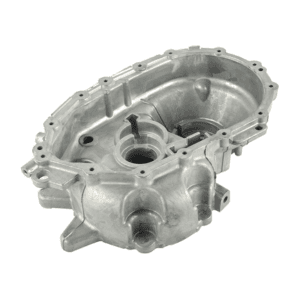
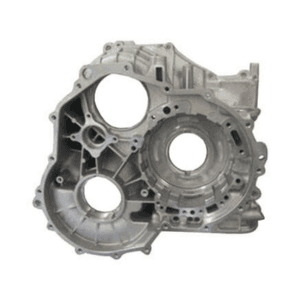
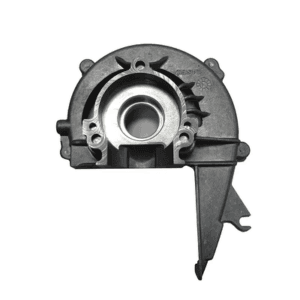
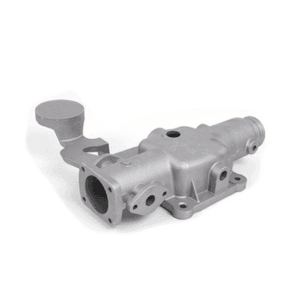
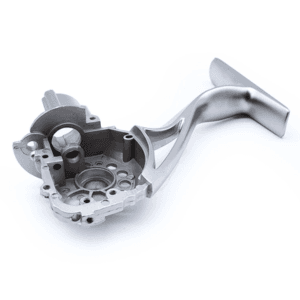
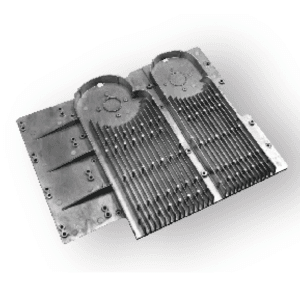
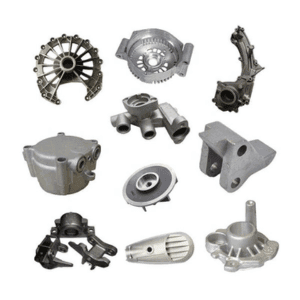
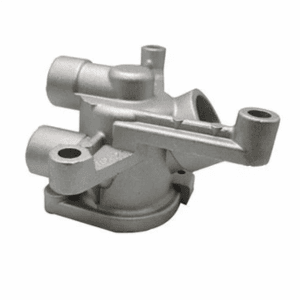
Industries We Serve
- Solid Progress
What You Gain with Us
We make your profitability and operations easier with practical approach.
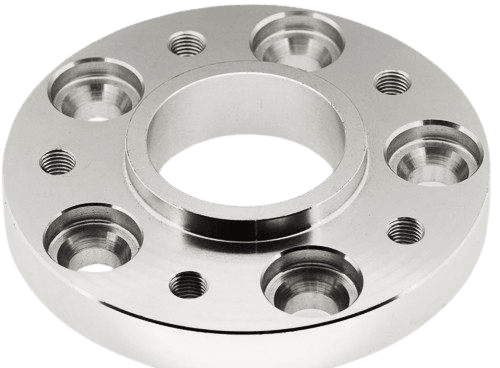
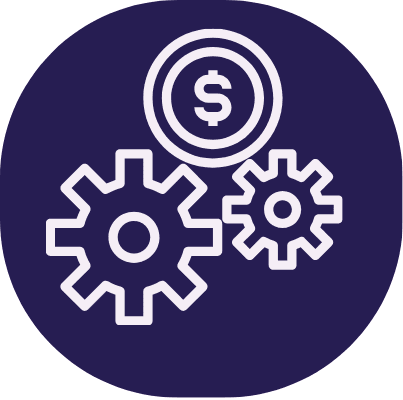
↓ 7-8%
OPS COST
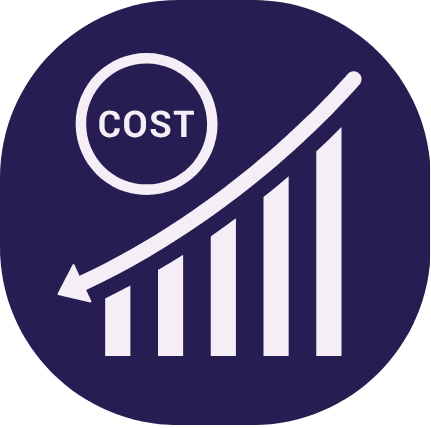
↓ 2-3%
COGM
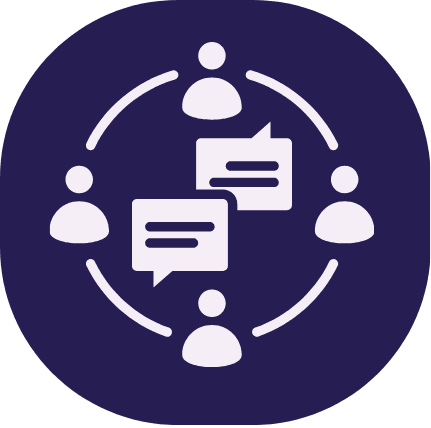
3X
Aggregation
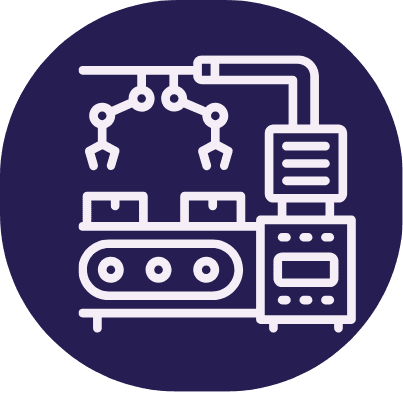
↑ 25%
Machinery Utilisation
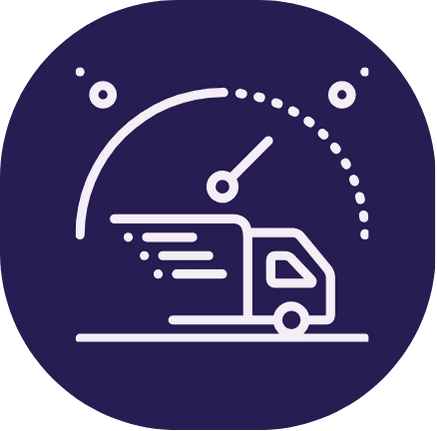
↓ 50%
Expedition
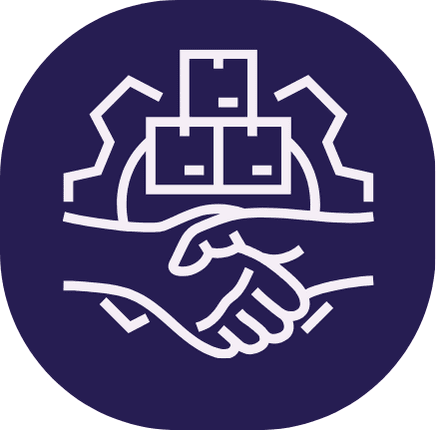
↑ 30%
Frigater Revenue
Achieving Superior Precision and Strength in Aerospace
Precision die casting services offers a significant advantage in the aerospace industry. It produces parts with outstanding dimensional accuracy and minimal porosity. This precision ensures that your components meet the tight tolerances and complex geometries needed for high-performance aerospace applications. By reducing the need for additional machining and minimizing material waste, pressure die casting enhances your components’ reliability and efficiency. Moreover, the reduced porosity improves the strength and fatigue resistance of the parts, ensuring they can handle the demanding conditions of aerospace environments.
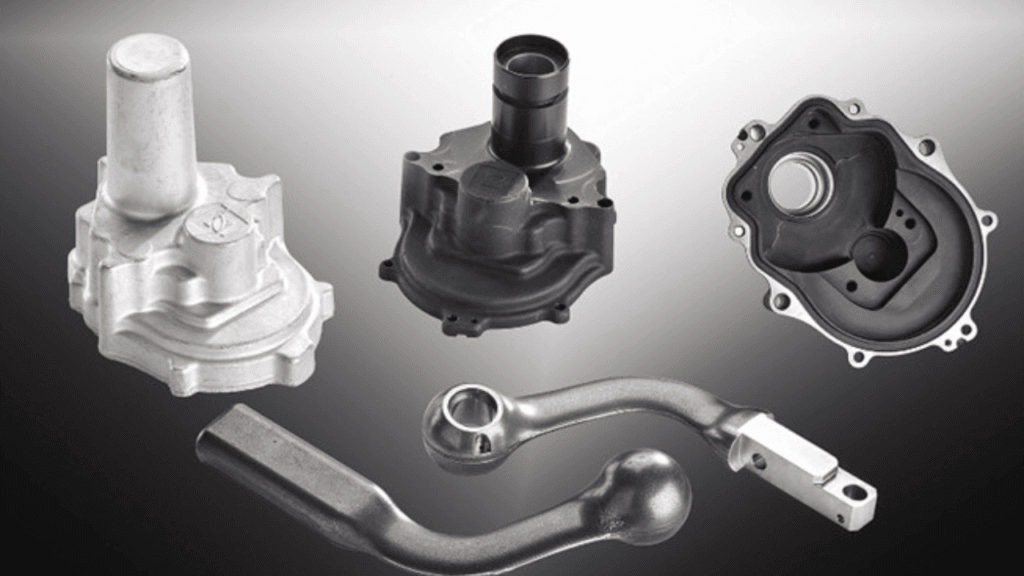
Check Out Our Blogs
What Our Customers Say about Frigate
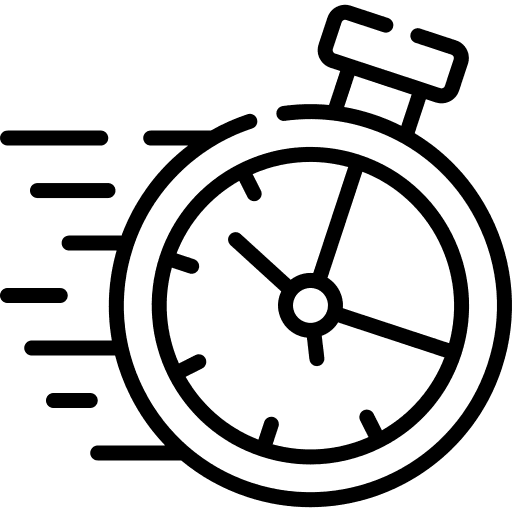
21%
Faster Manufacturing
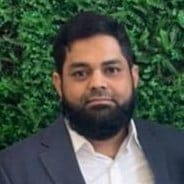
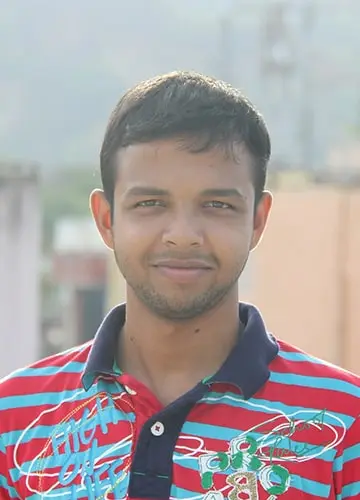

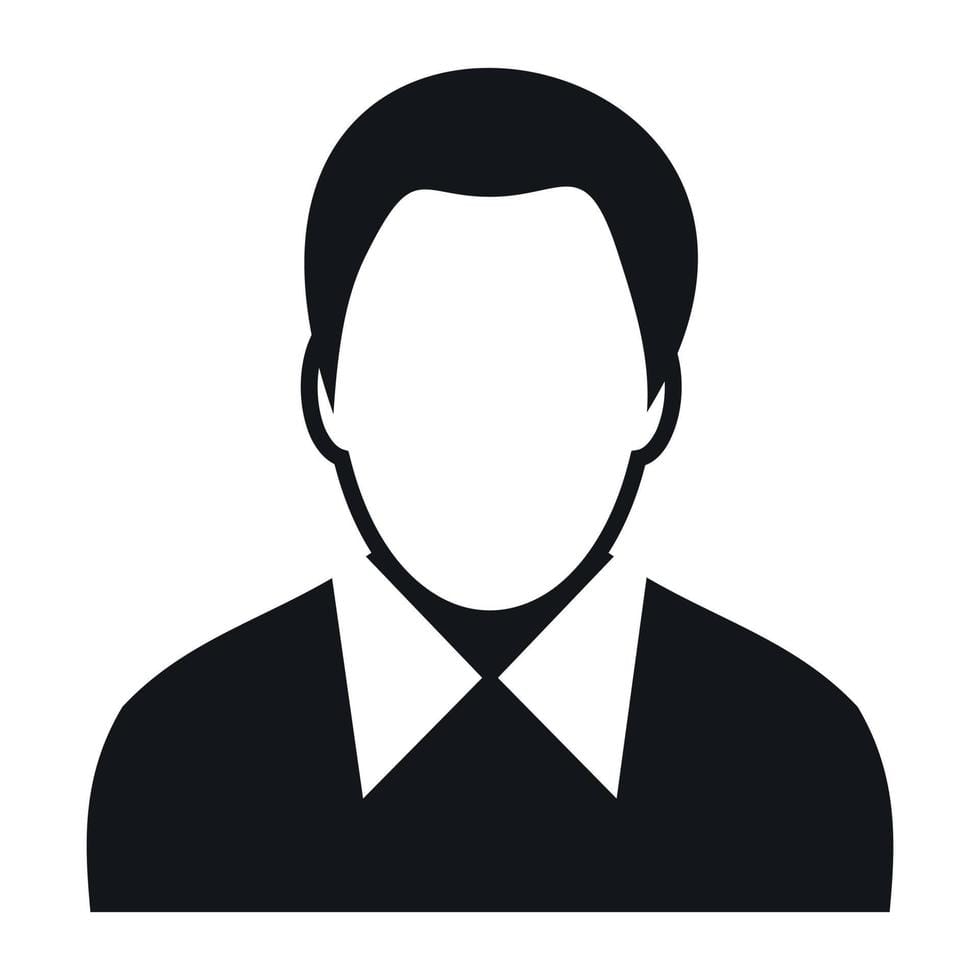
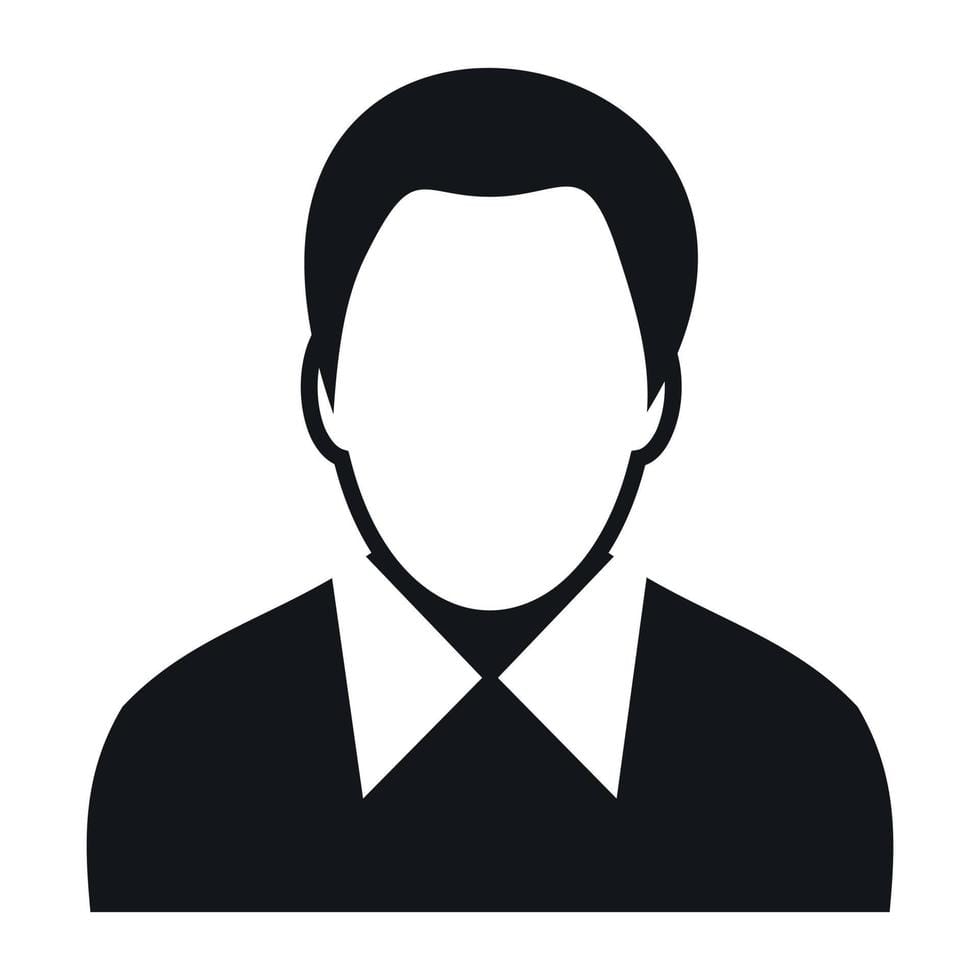
Having Doubts? Our FAQ
Check all our Frequently Asked Question
Common materials include aluminum, zinc, and magnesium. Each metal has unique properties that influence the casting process. For instance, aluminum is lightweight and strong, making it ideal for automotive parts. Zinc has excellent fluidity, which helps fill intricate mold designs. Choosing the right material impacts the quality and performance of the final product.
Higher pressure helps to fill the mold quickly, reducing air pockets and improving surface quality. Temperature is also important; if the metal is too hot, it can cause defects like porosity. Keeping both factors balanced is key for strong, smooth casts.
Mold design influences the flow of metal and the cooling rate. A well-designed mold allows the metal to fill evenly, reducing defects. It should also allow for easy removal of the cast part without damaging it. Features like draft angles and cooling channels are essential for optimal results.
Choosing the right alloy affects the final product's strength, weight, and corrosion resistance. Each alloy has specific properties, like melting point and fluidity, which influence how well it fills the mold. For example, aluminum alloys are popular for their lightweight and strength.
It’s important to control the injection speed and pressure to reduce defects, maintain proper mold temperature, and ensure good metal flow. Regular maintenance of the equipment also helps prevent issues. Implementing quality checks at different stages can catch problems early, leading to better casts.
We'd love to Manufacture for you!
Submit the form below and our representative will be in touch shortly.
LOCATIONS
Global Sales Office
818, Preakness lane, Coppell, Texas, USA – 75019
Registered Office
10-A, First Floor, V.V Complex, Prakash Nagar, Thiruverumbur, Trichy-620013, Tamil Nadu, India.
Operations Office
9/1, Poonthottam Nagar, Ramanandha Nagar, Saravanampatti, Coimbatore-641035, Tamil Nadu, India. ㅤ