Have you ever felt overwhelmed by the countless regulations governing aerospace manufacturing, automotive production, or medical device manufacturing? Compliance can be daunting, but maintaining product quality, safety, and legal eligibility is critical. Aerospace manufacturing, for example, faces strict standards that ensure planes are safe and effective. Missing compliance targets in any regulated industry can lead to costly penalties, recalls, and damage to reputation. Let’s dive into the complex compliance requirements, the main pain points, and how to address these in industries where high standards are non-negotiable.
Compliance Landscape in Aerospace, Automotive, and Medical Device Manufacturing
Understanding the compliance landscape is essential for companies in regulated industries like aerospace, automotive, and medical device manufacturing. Each sector has its own strict set of standards and quality requirements to ensure safety and reliability, which vary based on the complexity and risk level of the end product. Whether it’s an aircraft component, a car engine, or a medical implant, non-compliance is simply not an option. Let’s look at some key standards shaping compliance across these industries.
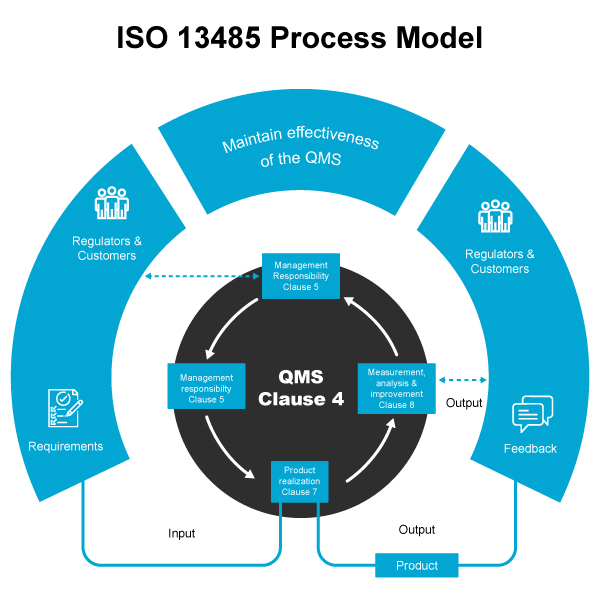
Aerospace Manufacturing Compliance
- Primary Standards: Aerospace manufacturing must adhere to AS9100, a widely recognized quality management standard for aerospace organizations. It includes requirements for traceability, process control, and rigorous documentation.
- ITAR Compliance: ITAR (International Traffic in Arms Regulations) controls the export of aerospace materials, products, and technology. Strict ITAR compliance is crucial, especially when working with international partners.
- Safety Requirements: Every component in aerospace manufacturing must undergo stringent quality checks. Parts like engines and safety-critical electronics must perform under high-stress conditions, demanding top-notch quality and reliability.
The global aerospace industry grew to $840 billion in 2022, showing a steady rise in demand. This industry’s rapid growth adds pressure to ensure that every component meets rigorous standards to avoid failure.
Automotive Manufacturing Compliance
- Core Standards: Automotive manufacturers follow IATF 16949, which focuses on quality management and continuous improvement in automotive production. Another essential standard, ISO 26262, ensures that vehicle electrical and electronic systems are functionally safe.
- Environmental and Safety Compliance: The automotive industry faces rising environmental regulations, such as the European Union’s REACH, which restricts the use of hazardous materials. Compliance with California Proposition 65 also prevents the use of harmful chemicals in car components.
With over 90 million cars manufactured globally in 2022, maintaining consistent quality and compliance across all components and markets is critical. Even one component failure can lead to large-scale recalls.
Medical Device Manufacturing Compliance
- FDA and ISO Standards: U.S. medical devices must comply with the FDA’s CFR 21 Part 820 regulations, which focus on quality systems and manufacturing processes. Globally, ISO 13485 regulates medical device manufacturing standards for quality and risk management.
- Risk and Traceability Requirements: Patient safety is paramount in medical device manufacturing. Risk management procedures require traceability of each component, from raw material to finished device. Meeting these standards can reduce contamination risks and product malfunctions.
The global medical device industry was valued at over $450 billion in 2022. With such high stakes, strict compliance is essential to protect lives and meet regulatory demands.
Key Pain Points in Navigating Compliance for Contract Manufacturing
Navigating compliance in these industries can be challenging, as companies face numerous roadblocks when ensuring regulatory adherence. The complexity of standards, high documentation requirements, and rapidly evolving regulations can lead to significant operational challenges. Here, we’ll highlight some of the main pain points companies face as they work to meet compliance standards.
Inconsistent Standards Across Markets
For companies operating in multiple countries, regulatory inconsistencies can be challenging. Aerospace manufacturing standards may differ slightly from one region to another. Adhering to each local standard can be difficult and lead to compliance gaps, which can delay market entry and increase costs.
High Documentation and Record-Keeping Requirements
All regulated industries, particularly aerospace manufacturing, require extensive documentation. For instance, part traceability, materials used, testing records, and certifications are essential. This paperwork ensures quality and regulatory compliance, but it can be burdensome. Documentation errors or missing information can result in compliance issues, leading to delays and extra costs.
Supply Chain Traceability and Accountability
Manufacturers need complete supply chain visibility to ensure that every component meets standards. Tracking each part’s journey, particularly in aerospace manufacturing, can be challenging. A lack of transparency can lead to non-compliant materials or counterfeit parts entering the supply chain, risking product integrity.
Technology and Data Integration Issues
Many manufacturers face integration issues, especially when older systems are combined with newer technologies. For example, data from multiple sources, such as ERP (Enterprise Resource Planning) systems and IoT (Internet of Things) sensors, must be seamlessly integrated into aerospace manufacturing. Inefficient data management can hinder real-time compliance monitoring, leading to delayed issue detection.
Frequent Regulatory Changes
Regulatory changes are common in aerospace manufacturing, automotive, and medical devices. Staying updated with these changes is challenging and requires continuous monitoring. Implementing changes to comply with new regulations can increase costs, impact production timelines, and strain resources.
Best Practices for Compliance in Contract Manufacturing
Companies can adopt several best practices to address these pain points effectively. These practices streamline compliance efforts and create a system that makes meeting industry requirements more manageable. Here, we outline some key strategies companies can use to stay compliant.
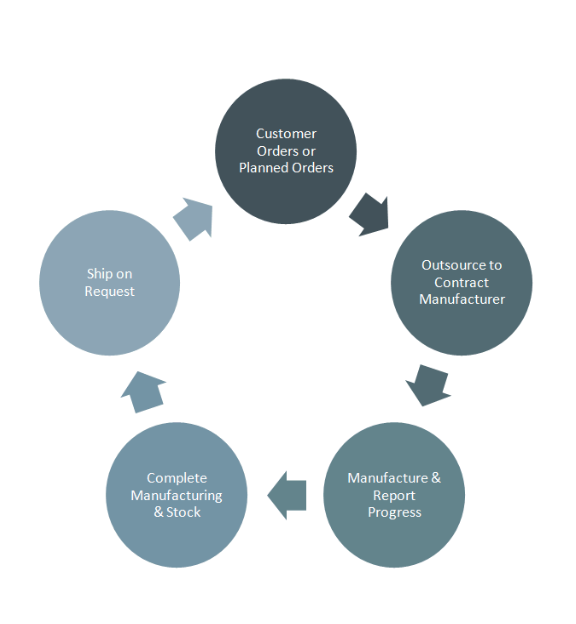
Establishing a Strong Quality Management System (QMS)
- Importance of Industry-Specific QMS: Implement a QMS that aligns with industry standards like AS9100 for aerospace manufacturing, IATF 16949 for automotive, and ISO 13485 for medical devices. An effective QMS ensures continuous monitoring and improvement.
- Proactive Approach: A proactive QMS anticipates compliance requirements early in the design phase, reducing the risk of issues during production.
Ensuring Supplier Compliance and Auditing
- Selecting Compliant Suppliers: Choosing reliable suppliers that comply with standards is critical. Regular supplier audits help verify that partners maintain quality and compliance levels.
- Supplier Scorecards and Metrics: Implement scorecards to evaluate suppliers on quality, delivery, and compliance. These metrics help maintain high standards across the supply chain.
Implementing Robust Data Management and Traceability Systems
- Digital Record-Keeping: Digitalizing records allows manufacturers to access data quickly and accurately. This practice is essential in aerospace manufacturing, where detailed traceability is often mandated.
- Real-Time Tracking Technologies: Technologies like RFID and blockchain can offer real-time visibility of each component’s journey, reducing counterfeit risks and enhancing compliance.
Training and Workforce Development for Compliance
- Regular Training: Keeping employees informed on regulatory updates ensures compliance. Regular training sessions provide teams with the knowledge to handle compliance requirements.
- Compliance-Centered Culture: Promoting a culture focused on compliance encourages employees to follow protocols. This mindset can prevent human error and foster a higher standard of accountability.
Leverage Technology for Automated Compliance Tracking
- Industry 4.0 Technologies: IoT, AI, and predictive analytics can reduce manual errors and ensure consistent compliance across the production line.
- Automated Compliance Tracking Systems: Automated systems can streamline auditing, making it easier to track compliance in real time, which is essential for aerospace manufacturing and other critical industries.
Industry-Specific Compliance Considerations
Since each industry has its own compliance needs and challenges, it’s important to understand the specific requirements in aerospace manufacturing, automotive, and medical devices. Each sector’s unique regulatory landscape requires tailored solutions and strategies.
For Aerospace Manufacturing
- Cybersecurity: Aerospace manufacturing often involves sensitive technology, making cybersecurity a top priority. Cyber breaches can result in significant compliance violations.
- Durability and Performance Testing: Aerospace components undergo rigorous testing to ensure they can handle extreme conditions. Performance failures are unacceptable as they compromise safety.
For Automotive
- Environmental Compliance: Strict environmental standards apply to automotive parts, especially in Europe. Manufacturers must meet emissions and material standards to reduce environmental impact.
- Functional Safety: Automotive components, such as braking and airbag systems, must function flawlessly. ISO 26262 ensures safety in electronic systems, which is critical for protecting passengers.
For Medical Devices
- Sterilization and Packaging: Medical devices must be sterile and safe for patient use. Compliance protocols cover sterilization and packaging, reducing contamination risks.
- Precision Calibration and Risk Management: Every medical device component must meet strict quality standards. Risk management ensures that each device is reliable, safe, and effective.
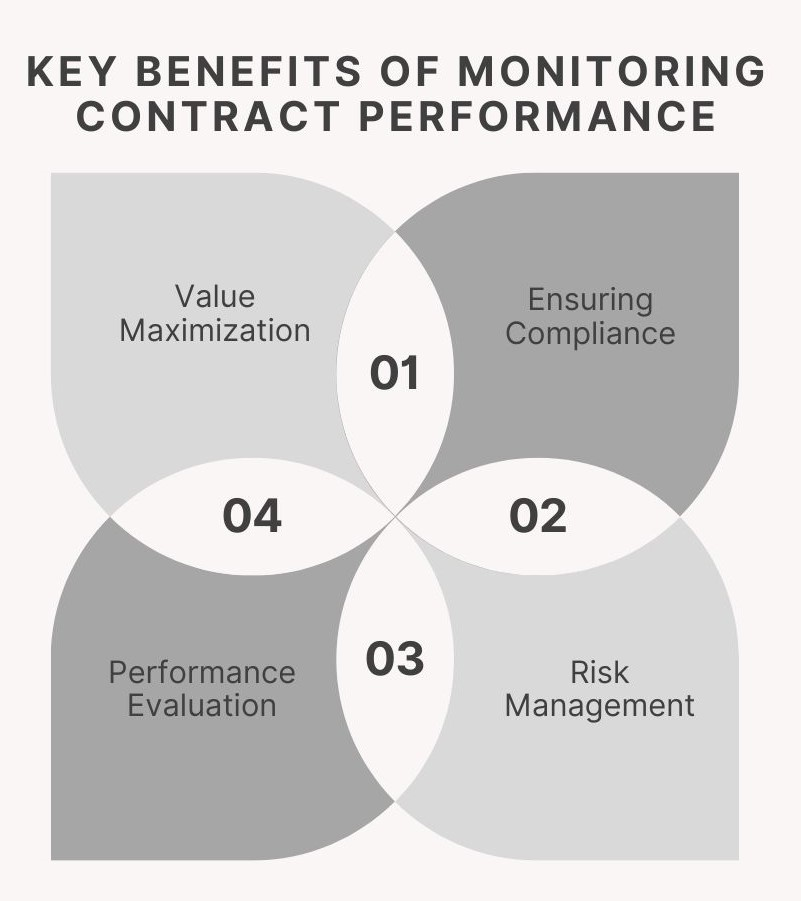
Frigate’s Commitment to Compliance-Driven Manufacturing Excellence
In highly regulated fields like aerospace manufacturing, automotive, and medical devices, Frigate’s expertise ensures every product meets rigorous standards. Through advanced solutions and strict quality controls, Frigate delivers market-ready, compliant products, supporting seamless and dependable manufacturing.
Customized Solutions for Diverse Industry Needs
Frigate provides industry-specific manufacturing solutions that meet compliance standards in aerospace manufacturing, automotive, and medical devices. Frigate’s ability to adapt processes to meet these standards makes it a trusted partner in regulated industries.
Advanced Quality Management and Continuous Improvement
Frigate’s QMS aligns with AS9100 for aerospace manufacturing, IATF 16949 for automotive, and ISO 13485 for medical devices. Frigate’s continuous quality improvement measures ensure every product meets regulatory standards.
Comprehensive Supply Chain Visibility and Traceability
Frigate’s advanced tracking and ERP systems enable real-time visibility across the supply chain. This capability ensures transparency, accountability, and compliance in every product, eliminating the risks associated with non-compliant materials.
Cutting-Edge Compliance Technology
Frigate integrates Industry 4.0 technologies like AI, IoT, and blockchain to automate compliance tracking and streamline audits. These tools enhance data integrity and allow Frigate to maintain top-tier compliance across all operations.
Conclusion
Navigating the complex compliance requirements of aerospace manufacturing, automotive, and medical devices can be challenging. However, companies like Frigate show that a robust approach to compliance can set the stage for long-term success. Whether you aim to meet aerospace regulations or stringent medical device standards, choosing a partner committed to compliance is key. Contact Frigate to learn more about how our expertise and technology can support your compliance goals across industries.