Are you tired of metal components failing under stress or extreme temperatures? If you’re in the aerospace, automotive, or energy industry, you know that subpar materials can lead to costly breakdowns or dangerous malfunctions. Traditional forging methods don’t always provide the precision or durability required for these high-stress environments.
Isothermal forging offers a reliable solution. Maintaining consistent temperatures during the forging process allows for the creation of components with superior mechanical properties, reduced defects, and enhanced performance. This makes it the go-to technique for manufacturing high-performance parts that must withstand extreme conditions.
In this blog, we’ll explore isothermal forging’s workings, key advantages, industries it serves, and its associated challenges. We’ll also explore future trends in this fascinating forging process and why it might be the perfect solution for your manufacturing needs.
What Is Isothermal Forging?
Isothermal forging is a specialized process in which the workpiece and the die (the tool that shapes the metal) are maintained at the same temperature throughout the operation. This consistent temperature helps minimize cooling rates, reduce defects, and create a high-quality finished product.
In traditional forging, the dies are cooler than the workpiece, causing the metal to cool rapidly as it is shaped. This quick cooling can lead to stress fractures, reduced material properties, and less control over the final shape. Isothermal forging solves these problems by ensuring uniform temperature distribution during the forging process, especially for difficult-to-forge materials like titanium and superalloys.
How Does Isothermal Forging Work?
Before discussing the technical benefits, it’s essential to understand how isothermal forging operates. The process is precise and involves several key steps, making it ideal for manufacturing high-performance components.

source : https://www.iqsdirectory.com/
Material Selection
Isothermal forging is typically used for metals that are difficult to forge using conventional methods, such as titanium, nickel-based superalloys, and high-strength steels. By choosing the right material, manufacturers can ensure that components perform under extreme conditions without cracking or losing strength.
Precision Temperature Control
The most critical aspect of isothermal forging is temperature control. The dies and the workpiece are heated to the same temperature. It ranges between 1,000°C and 1,200°C for materials like titanium. Maintaining this constant temperature throughout the forging process prevents rapid cooling and helps the metal flow smoothly into its desired shape without developing internal stresses or defects.
Slow Strain Rate
Another unique feature of isothermal forging is a low strain rate. The process is intentionally slow, allowing the metal to be shaped with greater control. This slow deformation leads to a uniform grain structure, which is critical for the strength and durability of the final product.
Specialized Hydraulic Presses
Isothermal forging requires specialized hydraulic presses that can apply the correct pressure to shape the heated material. These presses have temperature control systems and precision tools to ensure the forging process remains consistent.
Lubrication and Metal Flow
During the forging process, lubricants are applied to prevent the metal from sticking to the dies. This protects the tools from wear and ensures that the metal flows smoothly and fills every part of the die cavity, resulting in an accurate final shape.
Advantages of Isothermal Forging
So, why choose isothermal forging over traditional forging methods? The advantages are numerous, and it can significantly improve the performance and durability of your components.
Superior Mechanical Properties
Components forged using the isothermal process exhibit superior mechanical properties. By maintaining a constant temperature and controlling the strain rate, isothermal forging produces parts with better ductility, toughness, and fatigue resistance. This is a significant benefit for industries that require components to withstand extreme forces.
Enhanced Precision for Complex Parts
One of the standout benefits of isothermal forging is its ability to create complex geometries with high precision. The uniform metal flow ensures that even intricate shapes can be forged without defects or warping. This is particularly important in industries like aerospace, where components such as turbine blades must meet strict dimensional tolerances.
Reduced Residual Stresses
In traditional forging, uneven cooling can introduce residual stresses that weaken the final part. Isothermal forging avoids this by maintaining a constant temperature, which minimizes thermal gradients and stress buildup. As a result, components are stronger and more resistant to wear and tear.
Lower Material Waste
Because isothermal forging allows for more controlled metal flow, less material is wasted. This is particularly beneficial when working with costly metals like titanium or nickel-based superalloys, where minimizing waste can significantly reduce costs.
Applications of Isothermal Forging
Let’s examine how isothermal forging is used in various industries. These applications showcase the process’s ability to meet the demands of environments where strength, precision, and durability are critical.
Aerospace Industry
The aerospace industry is one of the primary beneficiaries of isothermal forging. Due to the high demands placed on aerospace materials, components like turbine blades, engine disks, and structural airframe parts are often produced using this method.
For instance, turbine blades operate in temperatures exceeding 1,000°C and are subjected to immense mechanical stress. Traditional forging methods can lead to defects in these critical components, which could have catastrophic consequences in flight. Manufacturers can create turbine blades with superior heat resistance and fatigue life by using isothermal forging, ensuring long-term reliability in extreme environments.
Additionally, structural components like airframe parts must be lightweight yet incredibly strong. Titanium alloys, commonly used in aerospace applications, are difficult to forge using conventional methods. Isothermal forging allows for precisely shaping these materials, ensuring high strength while reducing weight—crucial factors in achieving fuel efficiency and performance.
Automotive Industry
The automotive industry is increasingly turning to isothermal forging to meet the demands of modern vehicles, especially in the electric vehicle (EV) sector. As automakers push for lighter and more efficient components, materials like high-strength steel and titanium are becoming more common in engine parts, transmission gears, and suspension systems.
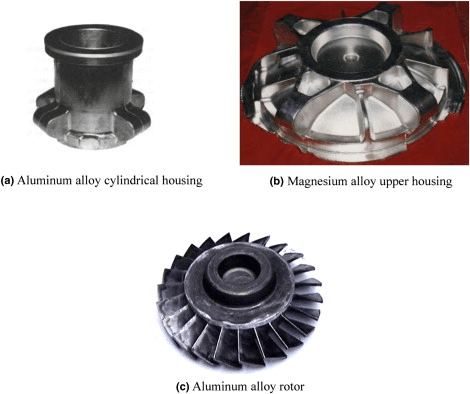
Manufacturers can create lightweight, high-strength parts that improve vehicle performance and fuel efficiency by using isothermal forging. For example, forged titanium engine components offer a significant weight reduction compared to traditional steel parts without sacrificing strength or durability. This helps automakers meet stringent fuel economy standards and reduce emissions.
Medical Devices
In the medical industry, isothermal forging produces biocompatible implants and surgical tools. Titanium, known for its strength, corrosion resistance, and compatibility with the human body, is often forged using this method to create joint replacements, dental implants, and other medical devices.
Medical components must meet stringent quality standards because they are implanted in the human body. Isothermal forging ensures that these parts have the necessary mechanical properties to function reliably over long periods, minimizing the risk of failure.
Energy and Power Generation
The energy sector also benefits from isothermal forging, particularly in manufacturing gas and steam turbine components. These turbines operate under extreme conditions, with high temperatures and mechanical stresses. Parts like turbine blades and rotors, forged from nickel-based superalloys, require the precision and durability that isothermal forging offers.
For example, gas turbines in power plants need blades that can withstand high temperatures and intense centrifugal forces. Isothermal forging helps produce blades that maintain strength and integrity over time, improving turbine efficiency and reducing maintenance costs.
Challenges in Isothermal Forging
While isothermal forging offers many benefits, it also presents some challenges. Let’s examine the potential hurdles manufacturers might face when adopting this process.
High Equipment Costs
One of the main challenges with isothermal forging is the cost of the equipment. The required specialized hydraulic presses, temperature control systems, and precision tooling are expensive, which can make the initial investment substantial for manufacturers.
Longer Production Cycles
The slow strain rates in isothermal forging result in longer production cycles than conventional forging methods. This can be a disadvantage in industries where time is of the essence, as it may take longer to produce each component.
Skilled Workforce
Operating isothermal forging equipment requires highly skilled technicians and engineers. The process demands precise control over temperature and force, meaning operators must be well-trained to avoid costly mistakes.
Future Trends in Isothermal Forging
As manufacturing technology advances, isothermal forging is expected to become more efficient and widespread. Here are some trends shaping its future.
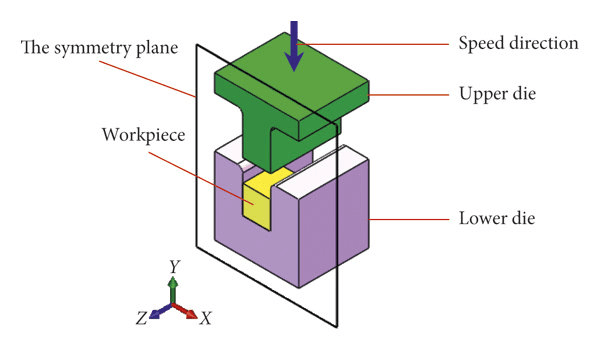
Advanced Materials
New alloys and composites are being developed specifically for isothermal forging. These materials will offer improved mechanical properties, such as higher heat resistance and strength, making them even more suitable for extreme environments.
Digital Twins
Manufacturers are starting to integrate digital twin technology into the isothermal forging process. Engineers can simulate and optimize production by creating a virtual replica of the forging process, leading to faster and more precise outcomes.
Sustainability
With increasing emphasis on sustainability, isothermal forging offers a more material-efficient process, reducing waste and energy consumption. As industries aim to lower their environmental impact, isothermal forging will likely play a key role in producing eco-friendly, high-performance components.
Conclusion
Isothermal forging is an advanced process that delivers superior mechanical properties, precision, and durability for components used in critical industries. Whether you’re in the aerospace, automotive, medical, or energy sectors, this process offers numerous advantages, including better control over material properties and reduced waste.
If you want to improve the quality and performance of your components, contact Frigate as your go-to manufacturing solution.