Like Plastic injection molding, Metal Injection Molding involves injecting metal into a mold to create components. This innovative process offers various unique benefits compared to a traditional method.
Metal Injection molding (MIM) is a net-shaped process that provides precision metal components. As MIM is already popular in various industries, such as agriculture, consumer equipment, and firearms, other industries are also exploring opportunities for their metal components. In this article, we will explore the extensive benefits of MIM.
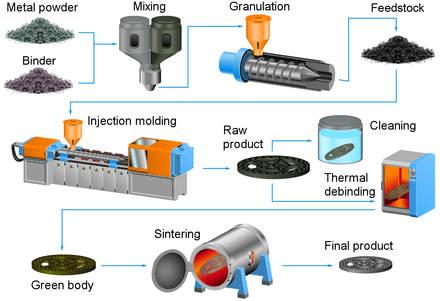
Advantages of Metal Injection Molding
Metal injection molding uses injection molding technology to create solid metal pieces. It creates a feedstock appropriate for injection molding by combining finely powdered metals with a plastic binder. The end products are renowned for their robustness and longevity while preserving affordability and creative freedom.
Here are some of the benefits of MIM to help you decide whether you should choose it for your manufacturing project or not:
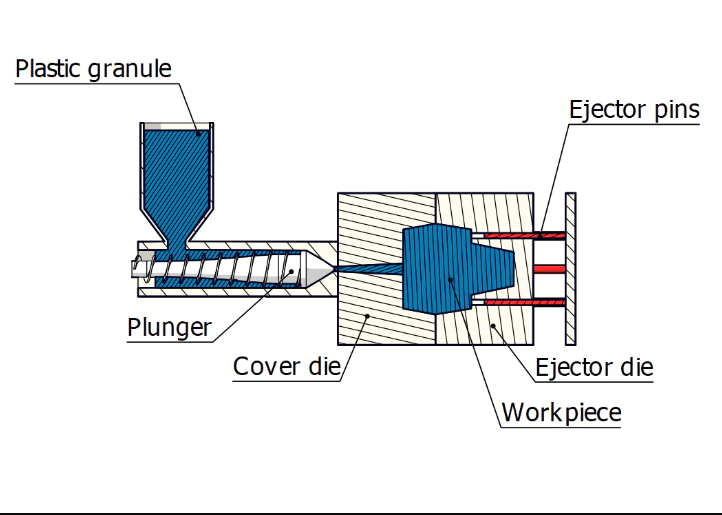
High-Value Production Volumes
Metal Injection Molding is most suitable for high-volume production requirements. MIM is the best choice for cost-effective mass-production components with precision.
Enhanced Density of Molded Parts
The molded parts using the MIM process are typically 96-98% dense after sintering, which is extensive compared to other processes. Metal injection molding uses refined powder that causes less porosity.
Material Versatility
MIM can be used with various metal materials, such as titanium, aluminum, stainless steel, etc. It helps you select raw materials according to your specific requirements and helps manufacturers fulfill custom requirements. Components produced with metal injection molding have high mechanical properties, thermal conductivity, and corrosion resistance.
High Precision and Consistency
Metal injection molding is known for its dimensional accuracy and tight tolerance, which is why it is the top choice for most industries. Moreover, an automated MIM process reduces the risk of human error. It ensures that every part is of the same quality and meets the manufacturing requirements.
Suitable for High-stress Applications
MIM suits all those components where strength and reliability are the most important factors. For example, Aerospace and medical equipment need to be strong enough to serve mankind. If you are looking for the right process for this equipment, then metal injection molding is the right process for your metal components.
Disadvantages of Metal Injection Molding
When we are talking about the advantages of MIM, it is also important to shed light on some of its limitations or disadvantages:
Initial Cost
MIM could be expensive due to the requirement of specialized equipment and tooling developments.
Limitations in Size
Metal injection molding is definitely one of the best options for producing low—to medium-sized components. However, it is not always suitable for larger components.
Post Processing
Some MIM components might require post-processing, such as surface treatment or maching. It adds to the production cost and time.
Lead Time
Debinding and sintering included in the MIM process can cause lead time delays compared to other processes.
Material Limitations
However, metal injection molding provides an extensive material choice, but not all the alloys or metals are suitable for the process.
Applications of Metal Injection Molding
MIM is the first choice of a plethora of industries due to its unique capabilities. Here are some of them:
Consumer Electronics
Small and detailed parts for different gadgets, such as laptops and smartphones, are effectively manufactured using metal injection molding.
Medical
Medical equipment such as dental braces, surgical components, and implantable devices require durability and precision that can be achieved using MIM only.
Aerospace
The aerospace industry chooses MIM because of its capability to manufacture durable and lightweight aircraft components.
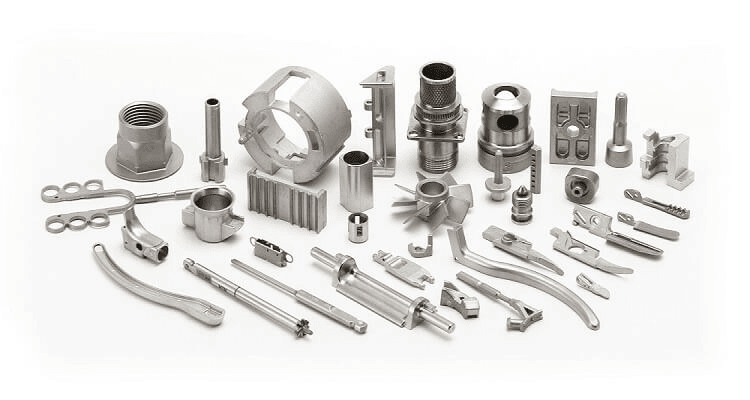
Automotive
Parts like levers, connectors, and gears need wear and stress benefits, which can be achieved with MIM’s strength.
Factors Driving MIM’s Popularity
Various factors have been contributing to the popularity of metal injection molding.
Technological Advancements
More exact control over the metal injection molding process is now possible thanks to modern hardware and software, which ensure constant quality and cut waste.
Economic Viability
The economic viability of old manufacturing methods declined as the need for complicated parts increased. MIM was more affordable since it could manufacture intricate parts in large quantities.
Sustainability
MIM is an environmentally favorable choice because of its effective material use and low waste output.
Quality
It is essential to guarantee the quality of MIM parts, particularly when they are used in vital applications. MIM parts are inspected using contemporary quality assurance methods, such as computerized tomography scanning and X-ray fluorescence. These non-destructive testing techniques guarantee that components fulfill the requirements without causing harm.
Conclusion
Metal injection molding is evidence of the industrial industry’s ongoing development and inventive spirit. With origins dating back many years, MIM’s capabilities have expanded rapidly, providing unmatched precision and design freedom. It became clear that MIM has advantages over traditional manufacturing techniques in terms of accuracy, economies of scale, and material efficiency.
Frigate holds the highest caliber of metal manufacturing, serving as a beacon on this path of accuracy and invention. Let us know your metal injection molding requirements, and we will get it done for you. Contact us for a free quote now!