RF-Optimized Machining for Next-Gen Telecom Hardware
Micron-level enclosures ensure EMI shielding and signal integrity under thermal and mechanical stress.
Frigate Controls Tolerances in High-Frequency Hardware
Thermal Gradient Hotspots
Vapor chambers and FEA-optimized clamping ensure uniform heat transfer and stable ΔT across mounting surfaces and temperature cycles.
Mechanical Fit Variability
Unified manufacturing with common datum references and GD&T control eliminates tolerance stack-up across cast, molded, and fabricated components.
Environmental Failures in Field
Composite environmental testing with corrosion-resistant materials ensures enclosure reliability under UV, salt spray, humidity, and thermal cycling conditions.
Our Clients
Trusted by Engineers and Purchasing Leaders
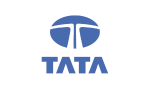
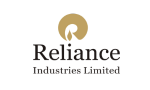


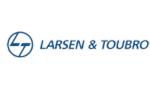
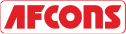


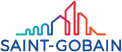

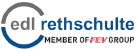

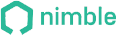
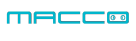









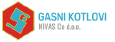
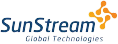

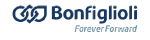


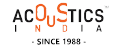
Enable Rapid Field Serviceability with Modular Mechanical Architecture
Designing for field maintenance requires predictable access paths, fast disassembly, and minimized repair downtime across high-density enclosures.
Incorporate front-access enclosures, captive fasteners, and segmented internal frames to isolate serviceable subsystems without disturbing primary structure or routing.
Simulate all tool paths, torque zones, and cable clearances using digital mockups to ensure field ergonomics and tool accessibility.
Maintain subassembly-level replaceability with indexed connectors and labeled harness paths, enabling part swaps in <15 minutes under constrained conditions.

Accelerate NPI with Early-Stage Manufacturability Simulation
Reducing tooling iterations and time-to-validation demands pre-tooling analysis of mold behavior, part fill characteristics, and warpage risk.
Use Moldflow, ProCAST, and casting simulation to predict flow fronts, air traps, sink formation, and cooling gradient imbalance before mold steel release.
Deploy soft-tooling or bridge-tool aluminum molds to evaluate part integrity, dimensional behavior, and assembly interaction within 2–3 weeks.
Model rib networks, wall transitions, and ejector load paths to avoid rework caused by internal stress and distortion during initial production runs.

Ensure Dimensional Stability Across Mixed-Material Assemblies
Thermal mismatch between polymers, aluminum, and steel often induces stress, deformation, or seal failure in dynamic environments.
Apply temperature-dependent CTE profiles in FEA to predict displacement at fastener points, joint seams, and material transitions during cycling.
Incorporate floating bushings, elastomeric decouplers, and torque-managed fasteners to absorb thermal growth differentials without mechanical overload.
Maintain constant gasket compression under variable temperature using geometry-specific load path optimization and compliant joint structures validated for fatigue.

Our Machined Products
We support your production needs with CNC-machined parts, subassemblies, and performance-critical components.
- Real Impact
Words from Clients
See how global OEMs and sourcing heads describe their experience with our scalable execution.
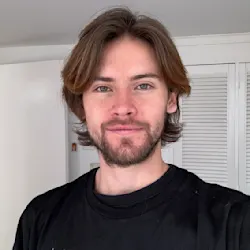
“Quick turnaround and solid quality.”
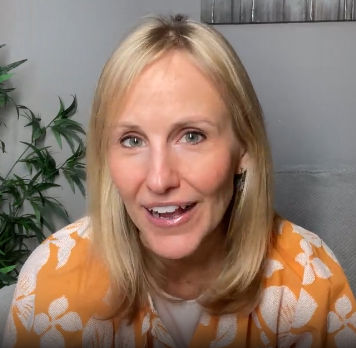
“The instant quote tool saved us time, and the parts were spot-on. Highly recommend Frigate!”
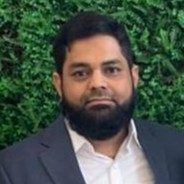
“I would strongly recommend Frigate to anyone who wants to do Rapid Prototyping, and take their ideas to manufacturing. One firm doing all kinds of Product Development!”
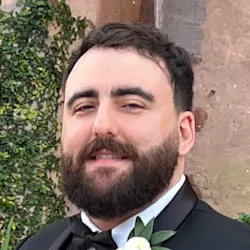
“Great service, fair price, and the parts worked perfectly in our assembly.”
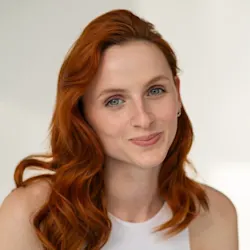
“Top-notch machining and fast shipping. Very satisfied with the results.”
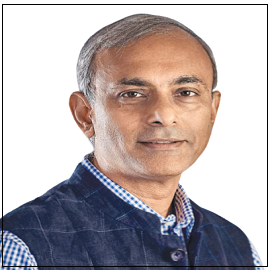
“The next disruption is happening in Prototyping & Manufacturing on-demand and Frigate is leading the way! I personally believe the Frigate's way of IIOT enabled cloud platform with Al.”
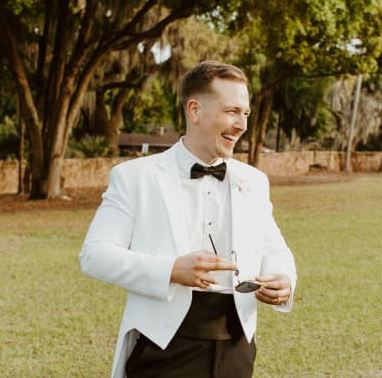
“Frigate delivered high-quality parts at a competitive price. The instant quote tool is a huge plus for us!”

“We appreciate the precision and quality of the machined components in the recent delivery—they meet our specifications perfectly and demonstrate Frigate’s capability for excellent workmanship.”
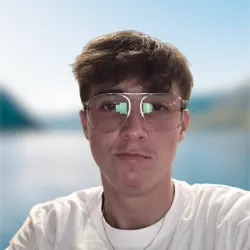
“Flawless execution from quote to delivery.”

“I am absolutely happy to work with supplier like Frigate who were quite proactive & result oriented . Frigate has high willingness team who has strong know how & their passion towards the products & process were absolutely thrilling.”
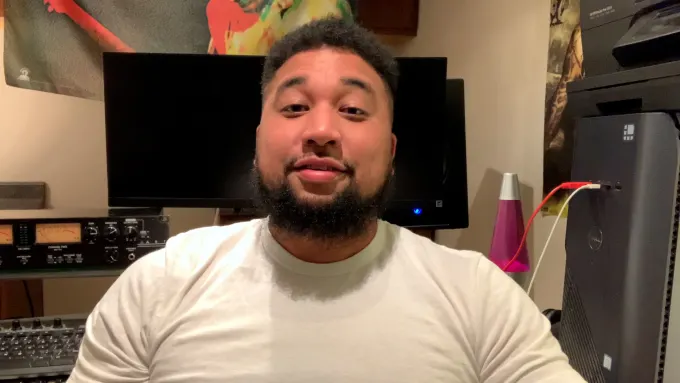
“The precision on these parts is impressive, and they arrived ahead of schedule. Frigate’s process really stands out!”
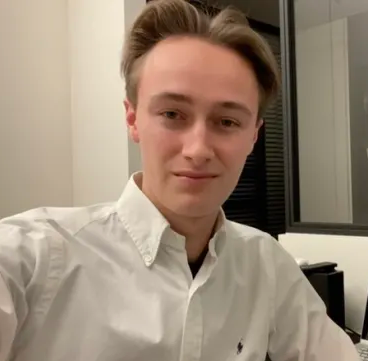
“Parts were exactly as spec’d, and the instant quote made budgeting a breeze.”
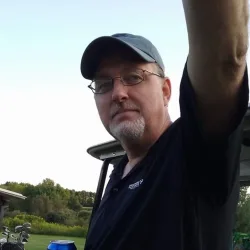
“Good value for the money.”
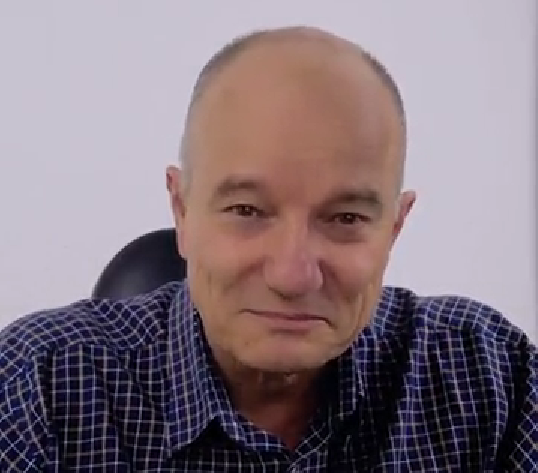
“The finish was perfect, and the team was easy to work with.”

“Working with Frigate has been great. Their proactive, results-driven approach and expertise shine through in every project. It's been a pleasure collaborating with them.”

"We are highly satisfied with the timely delivery and quality of the MIG Welding Cable from Frigate. Their attention to detail, secure packaging, and quick responsiveness stood out. We confidently recommend Frigate Engineering Services Pvt. Ltd. as a reliable manufacturing partner."
- We export to 12+ countries
Frigate’s Global Presence
Frigate takes pride in facilitating “Make in India for the globe“. As our global network of Frigaters provides virtually limitless capacity, and through our IoT enabled platform your parts go directly into production. By digitally and technologically enabling “the silent pillars of the economy” MSME and SME manufacturing industries, we are able to tap the huge potential for manufacturing to bring the best results for our clients.

100,000+
Parts Manufactured
250+
Frigaters
2000+
Machines
450+
Materials
25+
Manufacturing Process
- Solid Progress
How You Benefit with Us
Frigate brings stability, control, and predictable performance to your sourcing operations through a structured multi-vendor system.
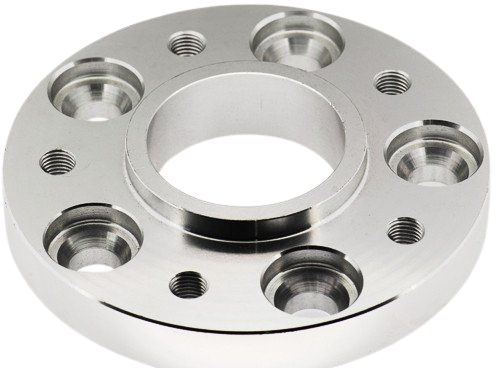
2.8X
Sourcing Cycle Speed
Frigate’s pre-qualified network shortens decision time between RFQ and PO placement.
94%
On-Time Delivery Rate
Structured planning windows and logistics-linked schedules improve project-level delivery reliability.
4X
Multi-Part Consolidation
We enable part family batching across suppliers to reduce fragmentation.
22%
Quality Rejection Rate
Multi-level quality checks and fixed inspection plans lower non-conformities.
30%
Procurement Costs
Optimized supplier negotiations and bulk order strategies reduce your overall sourcing expenses.
20%
Manual Processing Time
Automation of sourcing and supplier management significantly reduces time spent on manual tasks.
Other Industries We Serve
We deliver machining support across sectors that require consistency, material reliability, and tight dimensional control.
Get Clarity with our Manufacturing Insights
Frigate uses a unified design approach to control tolerance stack-up across different materials like die-cast aluminum, injection-molded plastics, and sheet metal. All parts are designed using a common datum reference structure, and precise GD&T (Geometric Dimensioning and Tolerancing) is applied to each interface. Before any parts are made, Frigate runs 3D tolerance analysis to calculate worst-case conditions for assembly gaps, alignment errors, or interference zones. This ensures that even when different materials expand or contract differently, the mechanical interfaces still fit perfectly. As a result, telecom assemblies built by Frigate are consistent, stress-free, and dimensionally stable—even in large production runs.
Frigate combines thermal-mechanical FEA (Finite Element Analysis) with advanced material modeling to understand how different materials expand or contract under heat. Materials like aluminum, stainless steel, and high-performance plastics all have different CTE (coefficient of thermal expansion) values, which can lead to internal stress, warping, or seal failure if not managed carefully. Frigate designs joints and mounting systems using floating bushings, flexible inserts, and torque-controlled fasteners that allow materials to move without creating stress. These designs are tested using simulated thermal cycles that match real field conditions—like rooftop heat, freezing nights, or rapid equipment start-up. This ensures long-term dimensional stability and seal integrity in telecom enclosures.
Frigate performs full-wave electromagnetic simulation using CST or HFSS to analyze RF behavior before any enclosure is manufactured. These simulations look at how electromagnetic energy flows inside and outside the housing, focusing on weak spots like seams, joints, screw holes, and ventilation slots. By optimizing gasket types, grounding methods, wall thicknesses, and internal baffle structures, Frigate ensures the shielding effectiveness meets strict telecom standards—often better than -60 dB. This virtual testing happens during the design stage and is critical for high-frequency equipment like mmWave radios or 5G base stations. It helps avoid delays and costly rework during EMC compliance testing later in the product cycle.
Frigate focuses heavily on serviceability during the design stage. Enclosures are built with modular layouts, where internal parts like PCBs, power modules, or RF shields can be accessed without dismantling the entire unit. Tool-less panels, captive screws, and fast-release clips make opening and reassembling faster and safer. Cable paths are clearly defined with labeled clips, and part replacement can be done at the sub-assembly level. To ensure nothing is missed, Frigate uses digital mockups to simulate hand-tool reach, connector access, and technician posture in the field. These strategies significantly lower Mean Time to Repair (MTTR), reduce service labor costs, and keep telecom networks running with minimal downtime.
Frigate uses bridge-tooling and soft-tooling methods to accelerate prototyping without waiting for final production molds. These temporary tools are machined from aluminum or pre-hardened steel and are capable of producing limited-run parts with close-to-final geometry. Before toolmaking, Frigate uses advanced simulation tools like Moldflow (for injection molding) and ProCAST (for die casting) to identify flow issues, cooling delays, or ejection problems. This ensures the tool design is right the first time. Once soft tools are created, real parts can be tested for dimensional accuracy, fit, and performance—allowing quick engineering changes before committing to full-volume tooling. This cuts weeks off NPI schedules while maintaining technical accuracy.
We'd love to Manufacture for you!
Submit the form below and our representative will be in touch shortly.
LOCATIONS
Global Sales Office
818, Preakness lane, Coppell, Texas, USA – 75019
Registered Office
10-A, First Floor, V.V Complex, Prakash Nagar, Thiruverumbur, Trichy-620013, Tamil Nadu, India.
Operations Office
9/1, Poonthottam Nagar, Ramanandha Nagar, Saravanampatti, Coimbatore-641035, Tamil Nadu, India. ㅤ
Other Locations
- Bhilai
- Chennai
- Texas, USA