CNC Machining Services for Biotechnology & Laboratory Equipment
Frigate supplies precision-machined components for biotechnology and laboratory applications through advanced CNC machining. Our capabilities support cleanroom compatibility and traceable materials essential to modern scientific equipment.
Our Clients





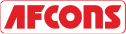

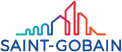


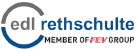

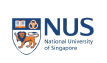
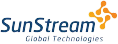

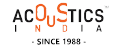




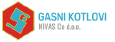
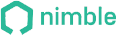
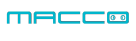












- Lab-Ready fitment
CNC Machining Built for Science
We use controlled manufacturing techniques to machine complex components for analytical instruments and life sciences systems.
Clean-Surface Cladding
Laser deposition builds chemically stable coatings that reduce corrosion risks in pH-sensitive or sterilized environments.
High Aspect Ratio Bores
Helical boring supports deep-channel manufacturing for microfluidic housings and multi-port valve systems with reduced runout.
Chip Control for Sensitive Alloys
Feed optimization and tool design minimize burring and thermal distortion during machining of titanium, aluminum, and nickel-based alloys.
- Execution Plan
Our CNC Machining Process
We apply calibrated surface engineering methods to improve chemical resistance, thermal stability, and part longevity in sterile lab environments.


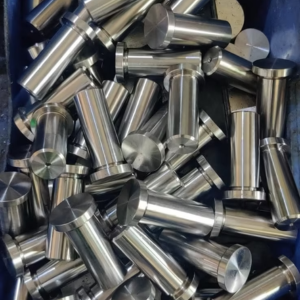

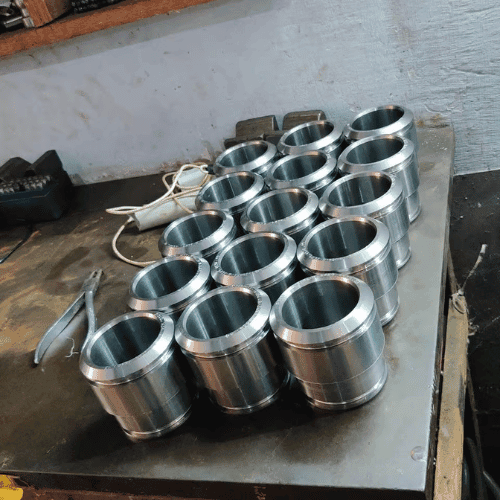

Advanced algorithms optimize tool paths, minimizing tool wear, reducing cycle times, and improving surface finishes. This involves strategically planning the sequence of movements and cuts to enhance efficiency.
Modern CNC machines often utilize 5-axis or even 6-axis capabilities, allowing for complex geometries and intricate shapes. This reduces the need to reposition the part, ensuring higher accuracy and a more refined finish.
CNC machines may integrate adaptive cutting strategies, where cutting conditions (speed, feed, depth of cut) adjust dynamically based on real-time sensor feedback or cutting force monitoring. This helps prevent tool breakage and ensures optimal material removal rates.
Specialized techniques like high-speed machining enable faster spindle speeds and advanced feed rates. This increases material removal rates while maintaining fine tolerances and reducing thermal distortion.
Some CNC setups incorporate in-process measuring systems (like laser scanners or probe-based systems) to check the part’s dimensions as it’s being machined. These systems can send real-time data back to the machine, allowing for automatic adjustments during production.
CNC machines with automated tool changers enhance efficiency by switching tools automatically without operator intervention. This allows for uninterrupted multi-operation machining without downtime, improving productivity in complex jobs with several cutting tools.
- Real Impact
Words from Clients
See how global OEMs and sourcing heads describe their experience with our scalable execution.
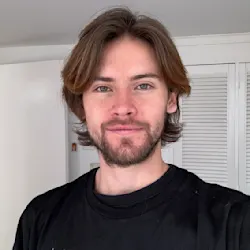
“Quick turnaround and solid quality.”
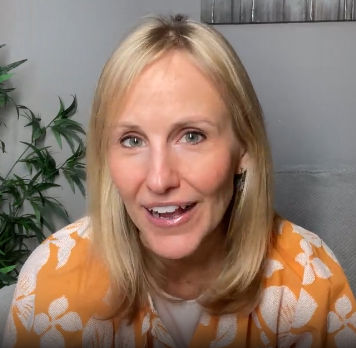
“The instant quote tool saved us time, and the parts were spot-on. Highly recommend Frigate!”
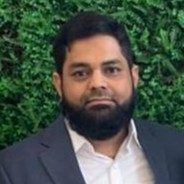
“I would strongly recommend Frigate to anyone who wants to do Rapid Prototyping, and take their ideas to manufacturing. One firm doing all kinds of Product Development!”
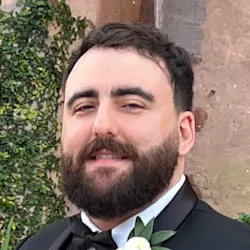
“Great service, fair price, and the parts worked perfectly in our assembly.”
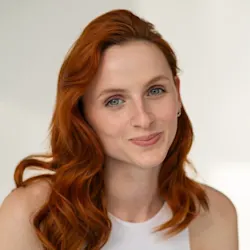
“Top-notch machining and fast shipping. Very satisfied with the results.”
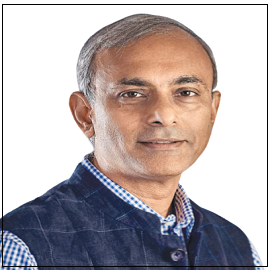
“The next disruption is happening in Prototyping & Manufacturing on-demand and Frigate is leading the way! I personally believe the Frigate's way of IIOT enabled cloud platform with Al.”
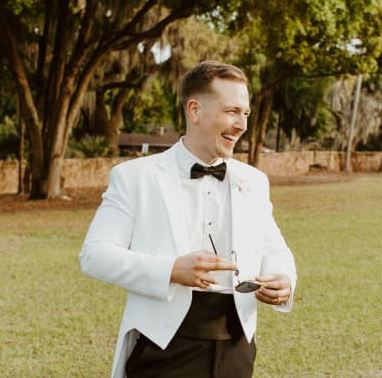
“Frigate delivered high-quality parts at a competitive price. The instant quote tool is a huge plus for us!”

“We appreciate the precision and quality of the machined components in the recent delivery—they meet our specifications perfectly and demonstrate Frigate’s capability for excellent workmanship.”
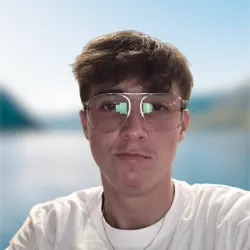
“Flawless execution from quote to delivery.”

“I am absolutely happy to work with supplier like Frigate who were quite proactive & result oriented . Frigate has high willingness team who has strong know how & their passion towards the products & process were absolutely thrilling.”
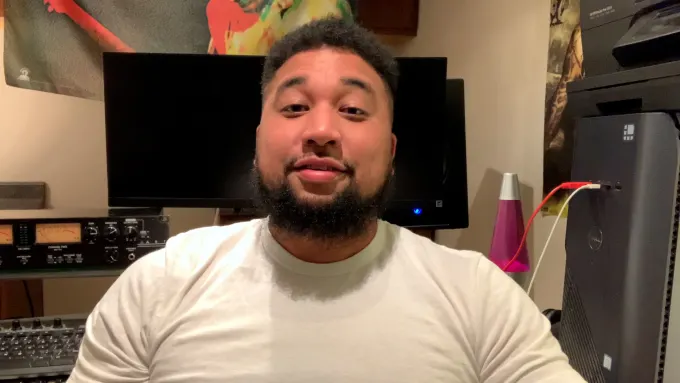
“The precision on these parts is impressive, and they arrived ahead of schedule. Frigate’s process really stands out!”
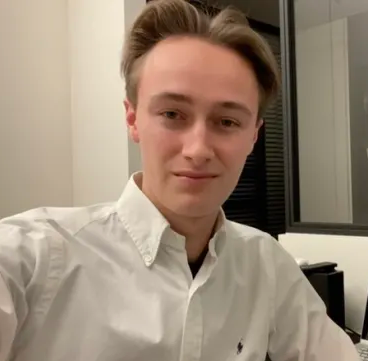
“Parts were exactly as spec’d, and the instant quote made budgeting a breeze.”
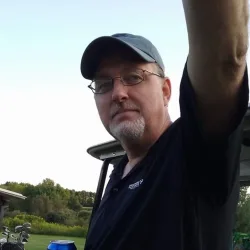
“Good value for the money.”
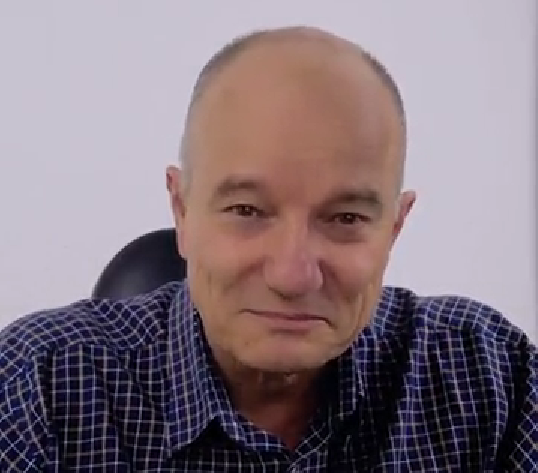
“The finish was perfect, and the team was easy to work with.”

“Working with Frigate has been great. Their proactive, results-driven approach and expertise shine through in every project. It's been a pleasure collaborating with them.”

"We are highly satisfied with the timely delivery and quality of the MIG Welding Cable from Frigate. Their attention to detail, secure packaging, and quick responsiveness stood out. We confidently recommend Frigate Engineering Services Pvt. Ltd. as a reliable manufacturing partner."
- Surface Consistency
Finishing for Scientific Systems
We fine-tune surface roughness to support sealing, bonding, and optical clarity needs common in lab-grade devices.
Anodizing
Give your aluminum parts a tough, corrosion-resistant shield with anodizing, reaching surface hardness up to HV 500, while enhancing electrical insulation and durability.
Mechanical Finishing
Smooth out imperfections and refine surfaces to Ra 0.2 µm or better with mechanical finishing techniques like grinding, polishing, and bead blasting.
Heat Treatment
Boost material strength and hardness by heat treating parts at temperatures up to 1100°C, ensuring they meet the mechanical demands of your application.
Electroplating
Add protective or functional metal coatings with electroplating, delivering consistent layers as precise as ±2 µm for improved corrosion resistance and conductivity.
Our Machined Products
We support your production needs with CNC-machined parts, subassemblies, and performance-critical components.
- High-Volume Capabilities
CNC Machining for Regulated Instruments
Submit part drawings for centrifuge enclosures, robotic pipette heads, and optical brackets with defined tolerances, finishes, and regulatory labeling.

CNC Milling
Cost-efficient milled parts delivered to medical labs with optimized toolpaths, controlled chip removal, and contamination-free finishing.
- Maintains surface flatness up to 0.01 mm across optical sensor mounts
- Delivers components from biocompatible materials like 316L and aluminum 6061

CNC Turning
We offer CNC turning with live tooling, contour cutting, concentricity control, and improved symmetry for rotating parts.
- Supports diameters up to 500 mm for centrifuge hubs and flanges
- Enables batch production via bar feeding for lab connectors and fittings
- Material Grades
CNC Machining Materials
We work with industry-approved metals that support sterility, mechanical reliability, and biocompatibility. Each metal offers performance traits matched to its intended use.
- Yield strength above 450 MPa resists flex during dynamic testing rigs
- Thermal conductivity below 20 W/m·K controls heat transfer in diagnostic housings
- Material machinability above 55% enables smooth finish and tight dimensions
A2 Tool Steel is a high-carbon, high-chromium steel known for its toughness and wear resistance. It’s ideal for producing durable, high-strength parts that can withstand heavy use.
Aluminum is a lightweight, corrosion-resistant metal with good machinability. Because of its strength-to-weight ratio, it’s commonly used in aerospace, automotive, and various industrial applications.
Brass is a copper-zinc alloy known for its machinability and corrosion resistance. It’s used for components requiring precise detailing and good mechanical properties.
Bronze is a copper-tin alloy with excellent wear resistance and strength. It’s often used for bushings, bearings, and other friction-prone components.
Cast Iron is known for its high wear resistance and machinability. It’s used in heavy-duty applications such as machinery parts and engine components.
Copper offers excellent thermal and electrical conductivity. It’s used in applications requiring heat dissipation or electrical conductivity, such as electronic components.
Steel is a versatile material known for its strength and durability. It’s used in various applications, from construction to automotive parts.
Titanium is a lightweight, high-strength metal with excellent corrosion resistance. It’s used in aerospace, medical implants, and high-performance engineering applications.
Stainless Steel offers high corrosion resistance and strength. It’s widely used in applications ranging from kitchen equipment to industrial machinery.
Zinc is a ductile and corrosion-resistant metal known for its excellent machinability, especially in its alloy forms. It's often used for components requiring intricate details, good surface finish, and precise dimensions, commonly found in automotive, hardware, and electrical applications.
- Functional Integration
Instrument-Grade Solutions
Our machining solutions are developed to support alignment accuracy, clean assembly, and consistent outcomes for high-frequency lab device usage. We streamline integration into end-use setups.
- Maintains tolerances of ±0.005 mm across optical rail mounts
- Supports shaft lengths up to 1,200 mm for chromatography system frames
- Controls runout within 0.01 mm in spindle-coupled parts
- Enables tight coupling zones for sterile-fit tubing systems
- Reduces scrap through precise fixturing during batch runs
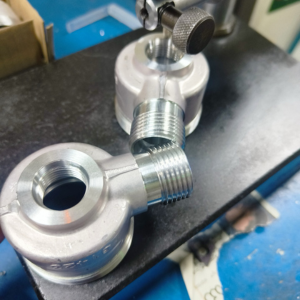
- Adhere to Compliance
Regulatory Alignment in CNC Machining
Frigate’s services comply with medical and laboratory industry regulations to protect process reliability and end-user safety. Our workflows embed certification-grade protocols, serialized tracking, and clean production planning.
- Complies with biocompatibility and sterilization test standards for metallic parts
- Retains process-level traceability from billet to batch
- Applies full inspection to verify alloy composition and performance under lab use
Follows structured documentation and QA measures for repeatable lab instrumentation components.
Implements aerospace-derived precision controls in highly regulated medical instrumentation machining.
Prevents restricted materials in components for bio-assay equipment and diagnostic tools.
Meets safety and conformity standards for lab-use equipment within EU markets.
Applies thermal and material treatment control for lab-grade structural integrity.
Enforces traceable lot control and corrective action for lab-scale production setups.
Confirms that all CNC machined components are free from substances of very high concern (SVHC).
- We export to 12+ countries
Frigate’s Global Presence
Frigate takes pride in facilitating “Make in India for the globe“. As our global network of Frigaters provides virtually limitless capacity, and through our IoT enabled platform your parts go directly into production. By digitally and technologically enabling “the silent pillars of the economy” MSME and SME manufacturing industries, we are able to tap the huge potential for manufacturing to bring the best results for our clients.

100,000+
Parts Manufactured
250+
Frigaters
2000+
Machines
450+
Materials
25+
Manufacturing Process

- Testing Compatibility
Quality Standards for CNC Machining Services
To measure the roundness of cylindrical features, ensuring they meet tolerance requirements.
To check internal surfaces for flatness, critical for sealing and assembly purposes.
To identify burrs or sharp edges that may affect assembly or safety.
To ensure that complex profiles (e.g., contours, curves) conform to design specifications.
To check the topography and texture of the surface, ensuring it meets the required specifications for function or aesthetics.
To verify that the surface hardness depth meets the required specifications for wear resistance.
To measure internal stresses that could lead to deformation or failure during or after machining.
To verify grain structure, inclusions, and material consistency, ensuring the part meets performance requirements.
- Delivered Parts
CNC Machined Components for Laboratory Systems
We ensure micron-level part precision by using ultra-rigid CNC equipment paired with thermal drift monitoring and backlash correction. Explore parts crafted for centrifuges, pipetting robots, valve mounts, and imaging equipment, ready for cleanroom assembly.
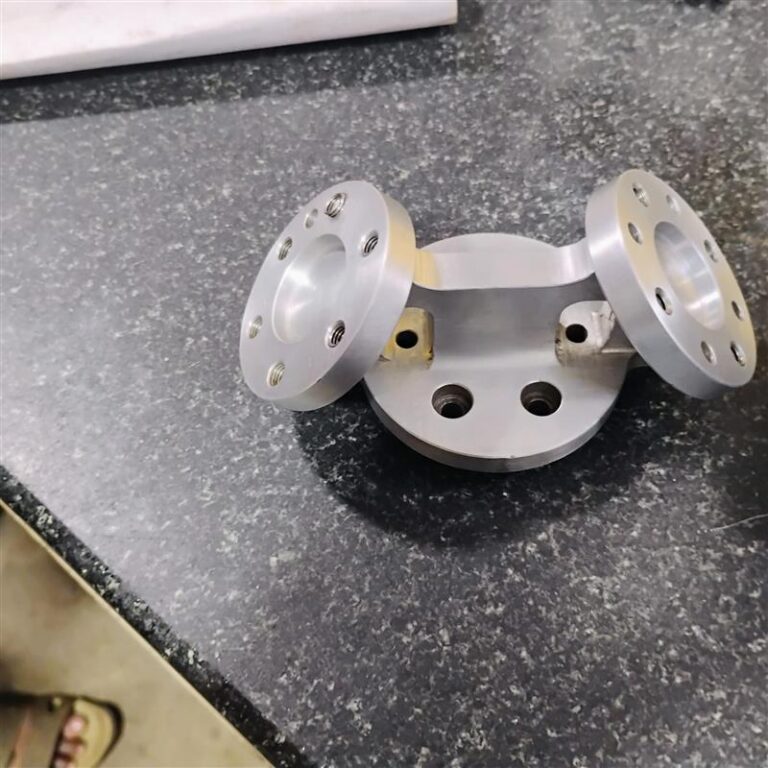
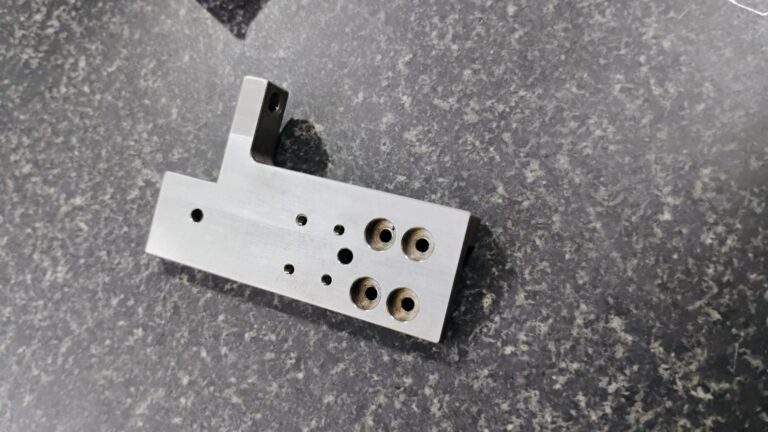
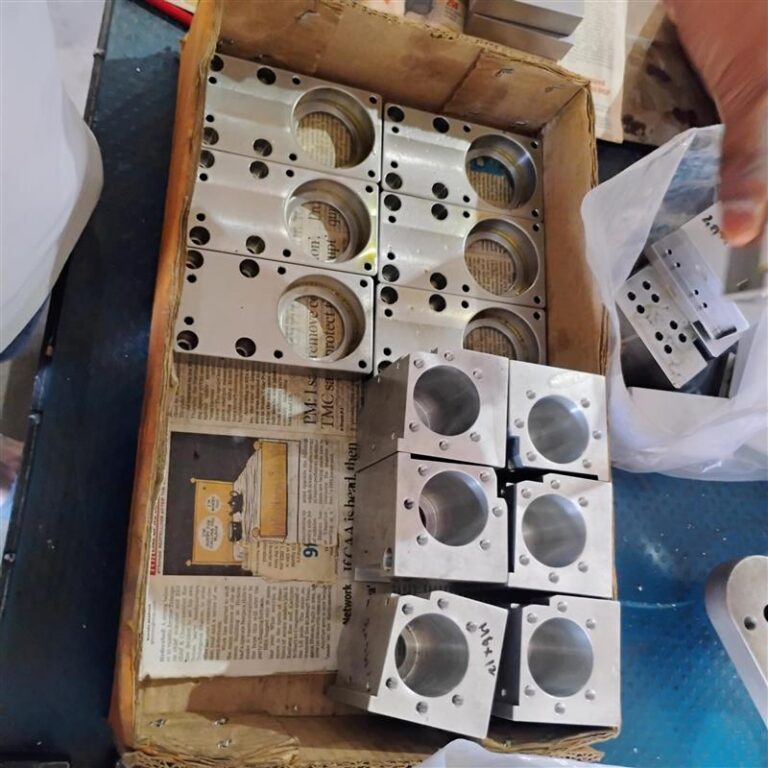
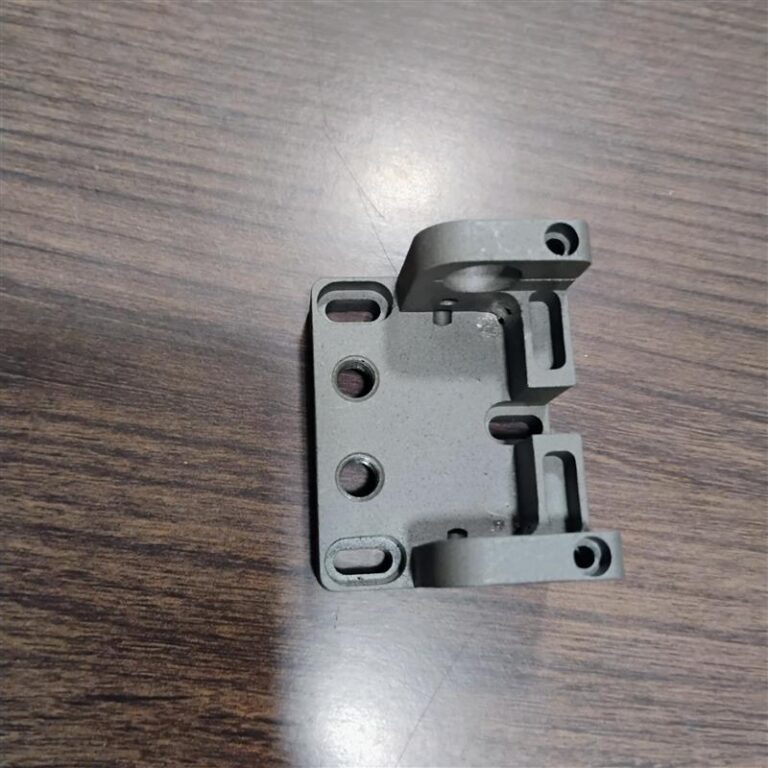
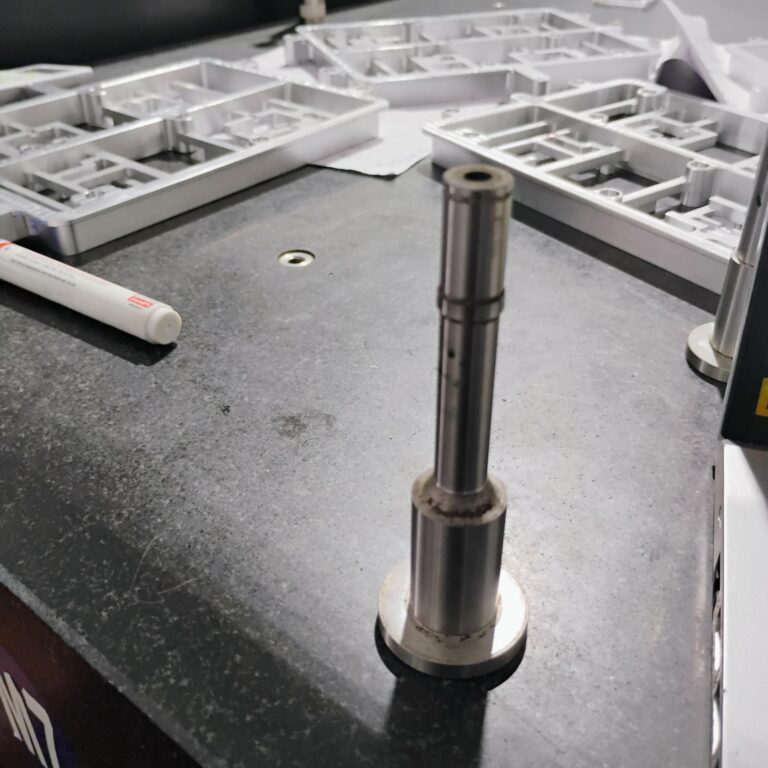
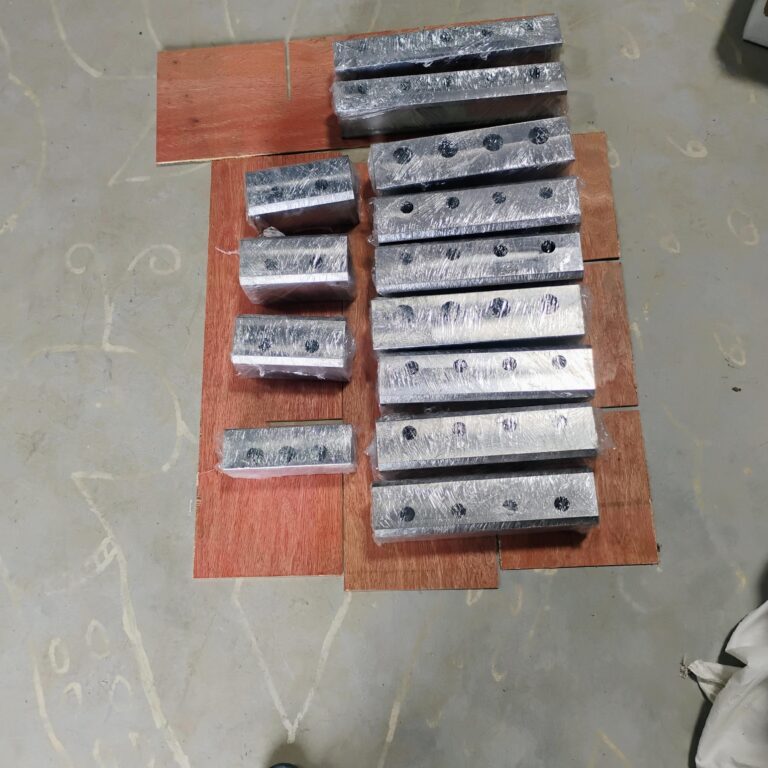
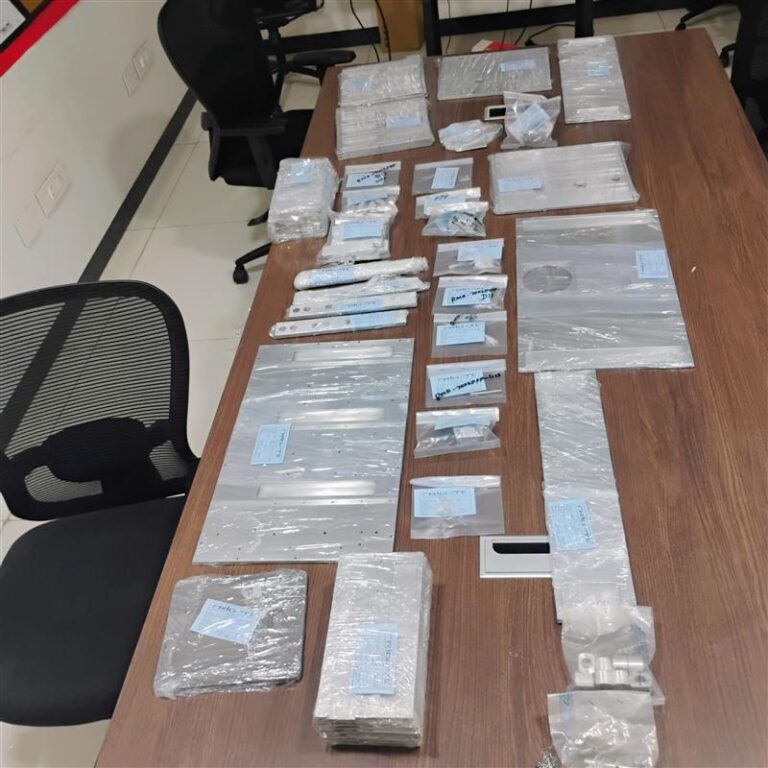

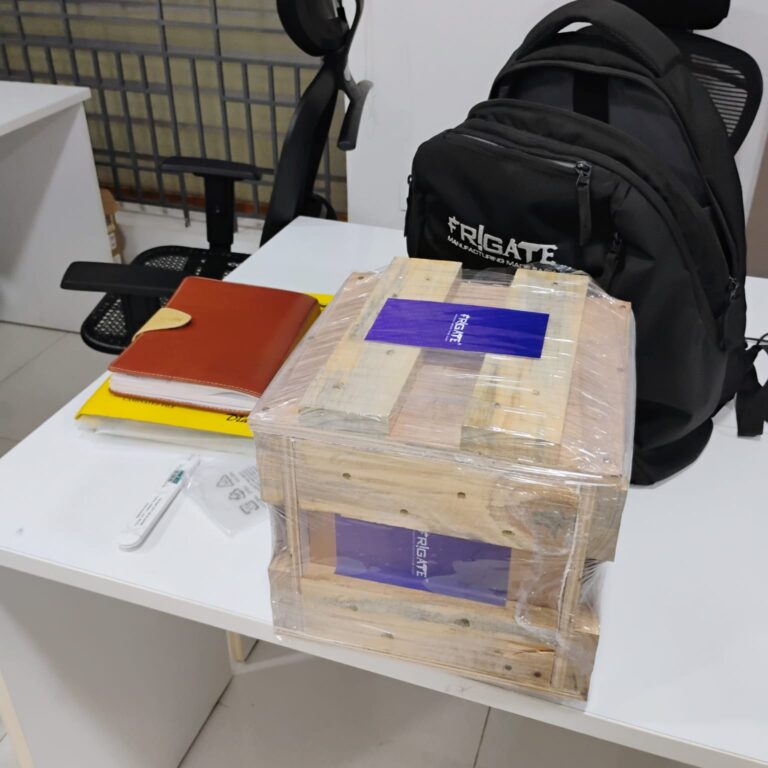


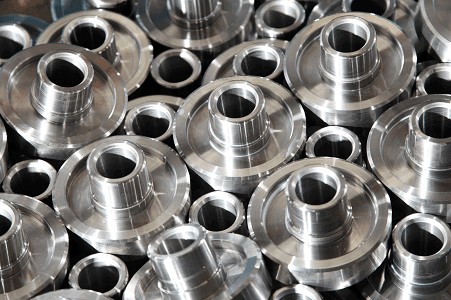
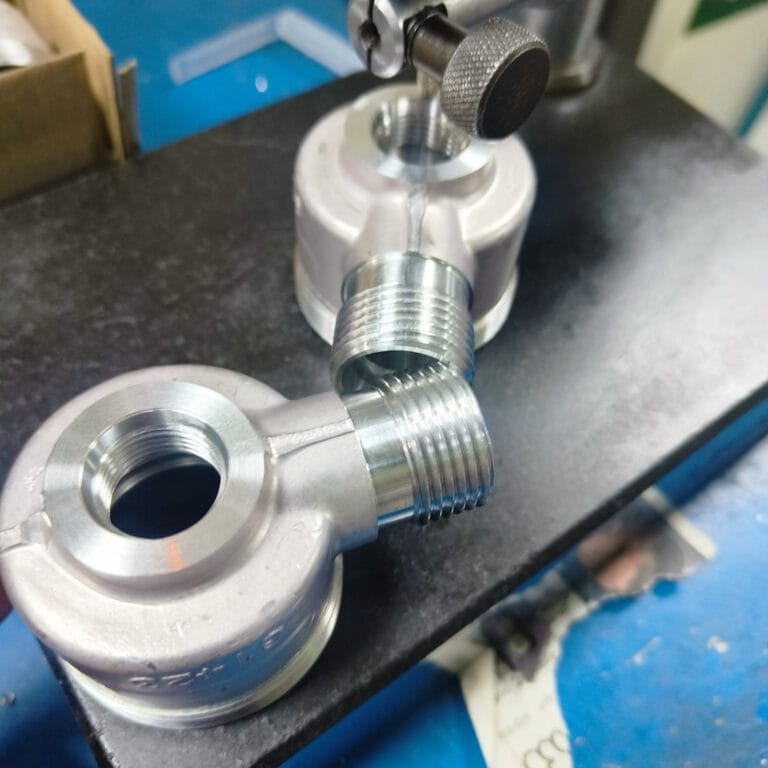
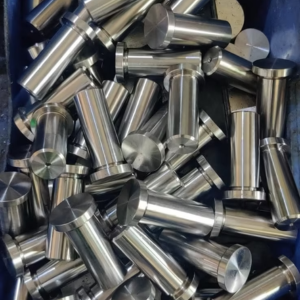
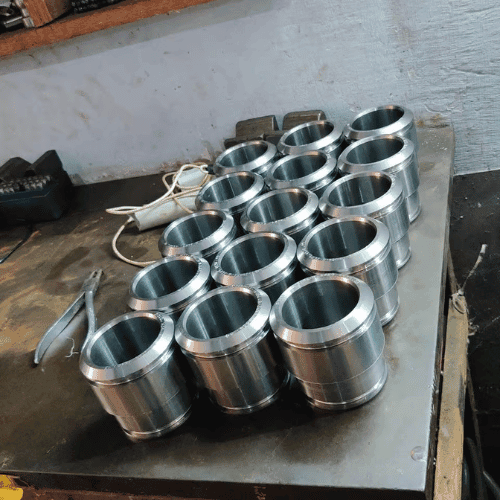
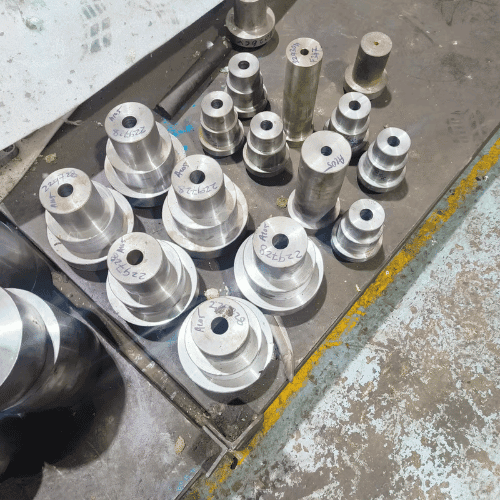
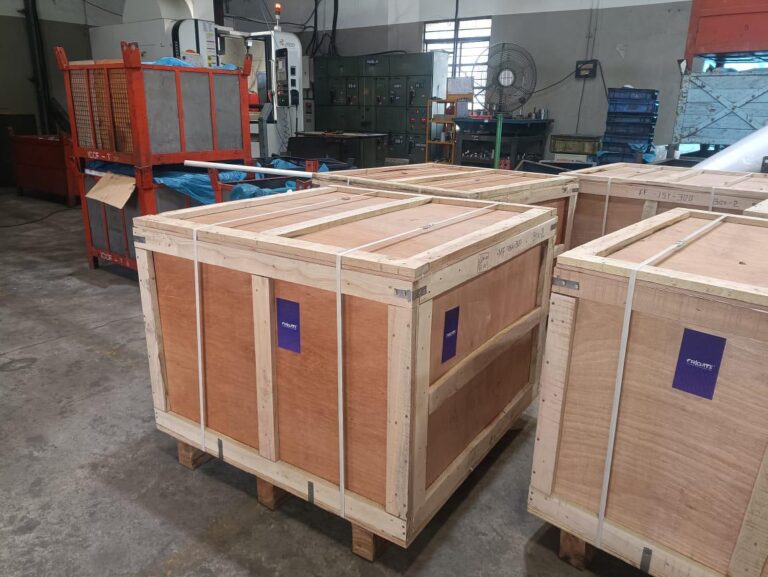
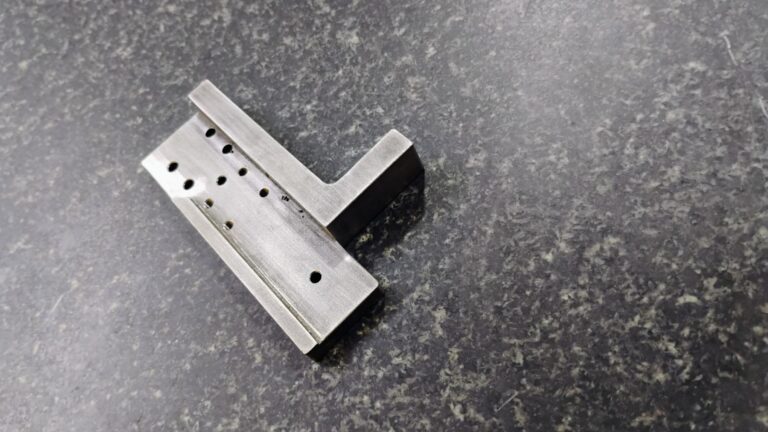
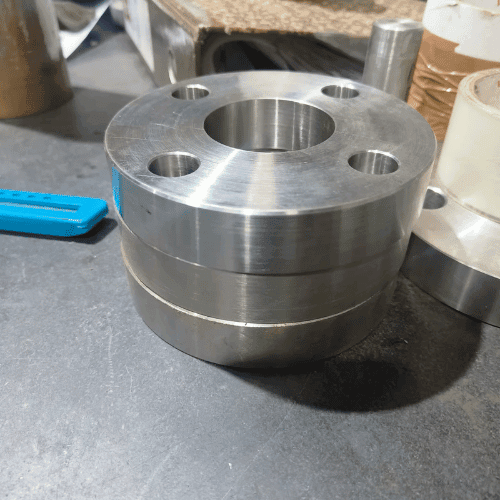
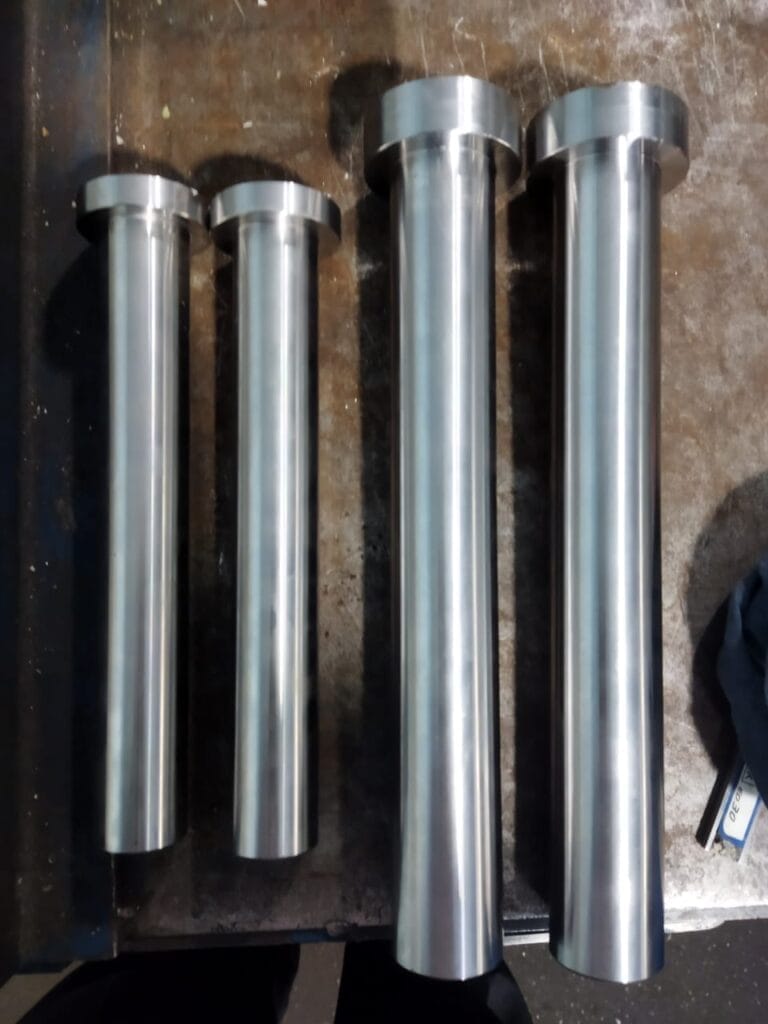

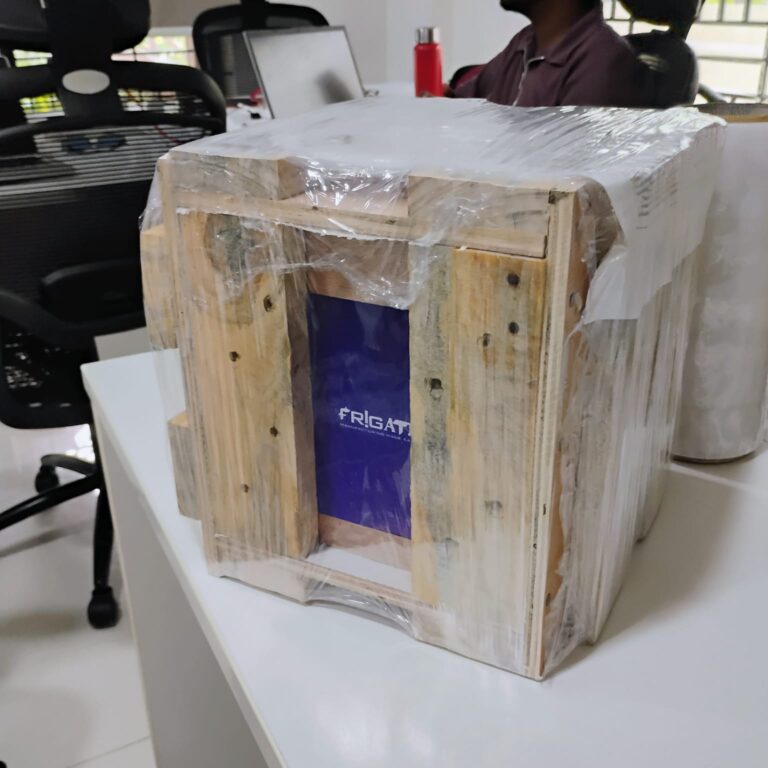

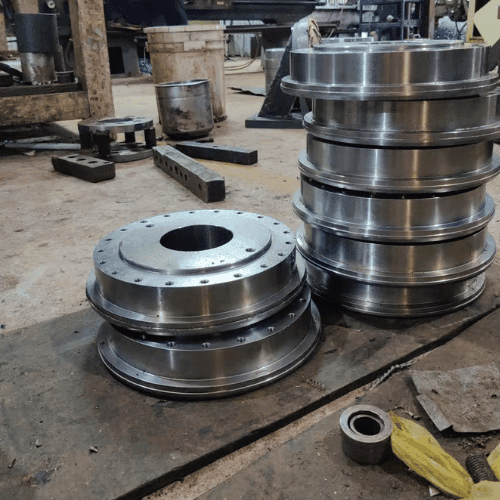
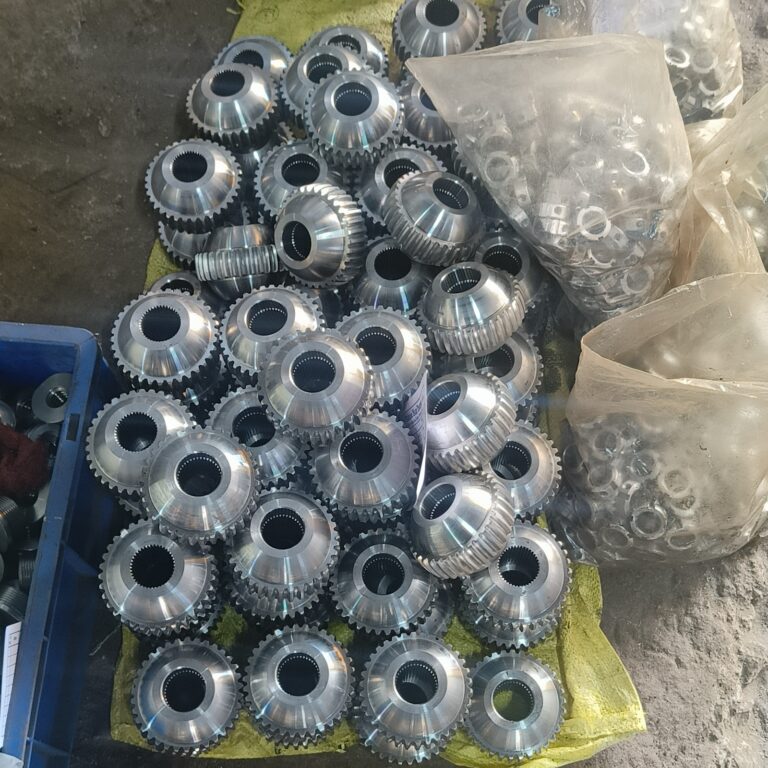
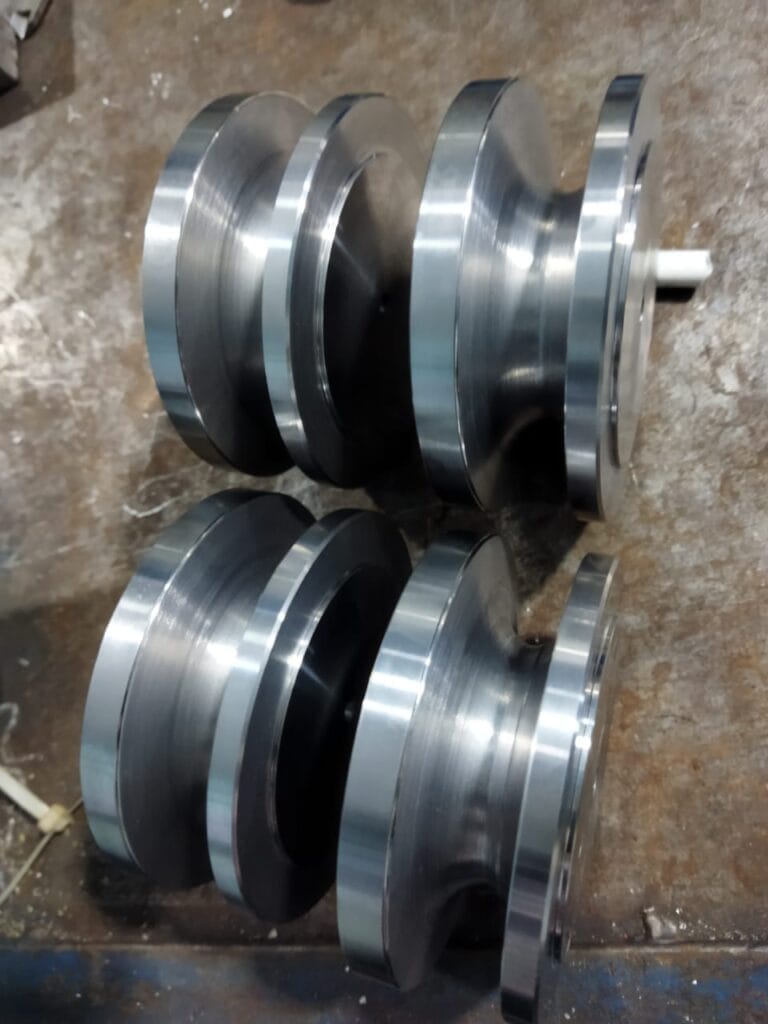
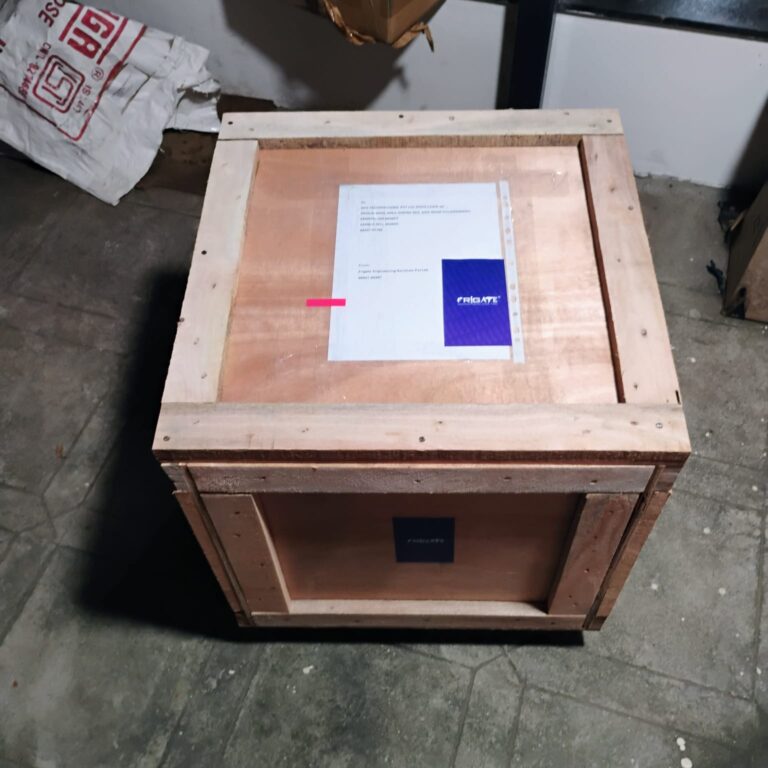
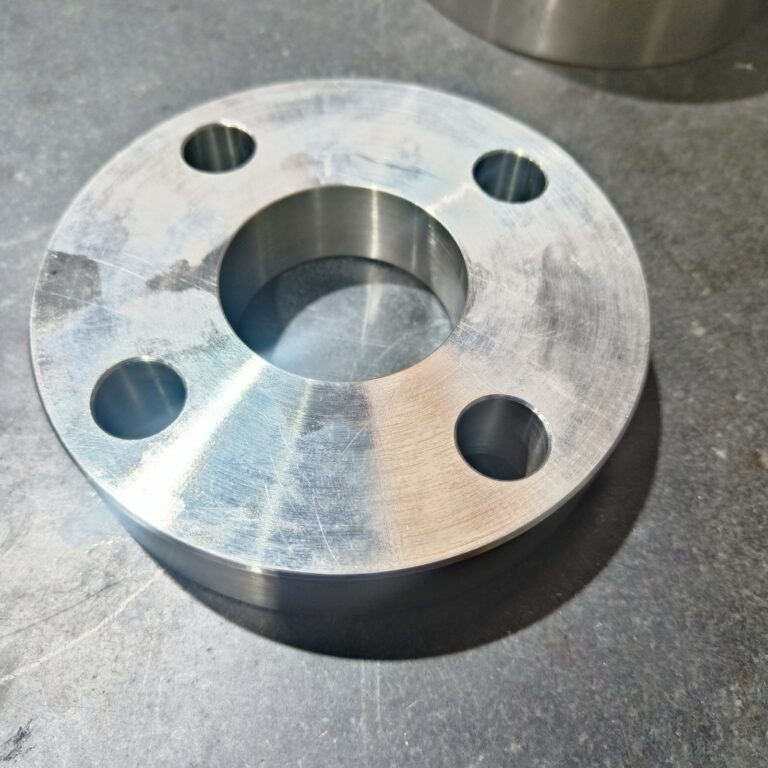
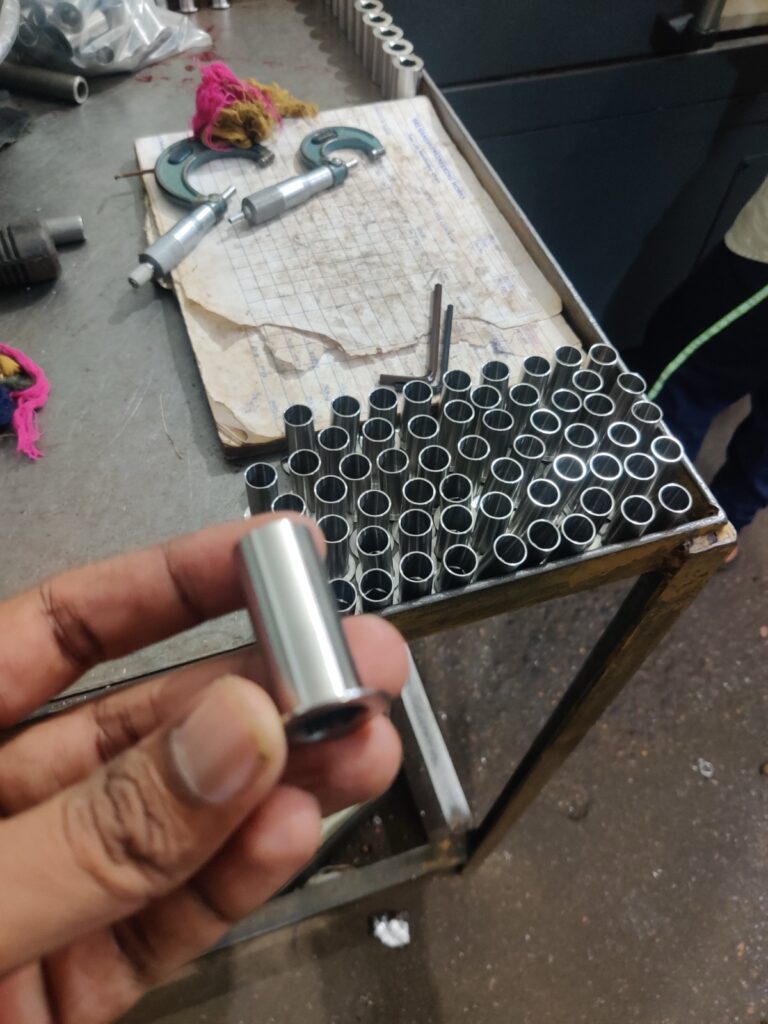
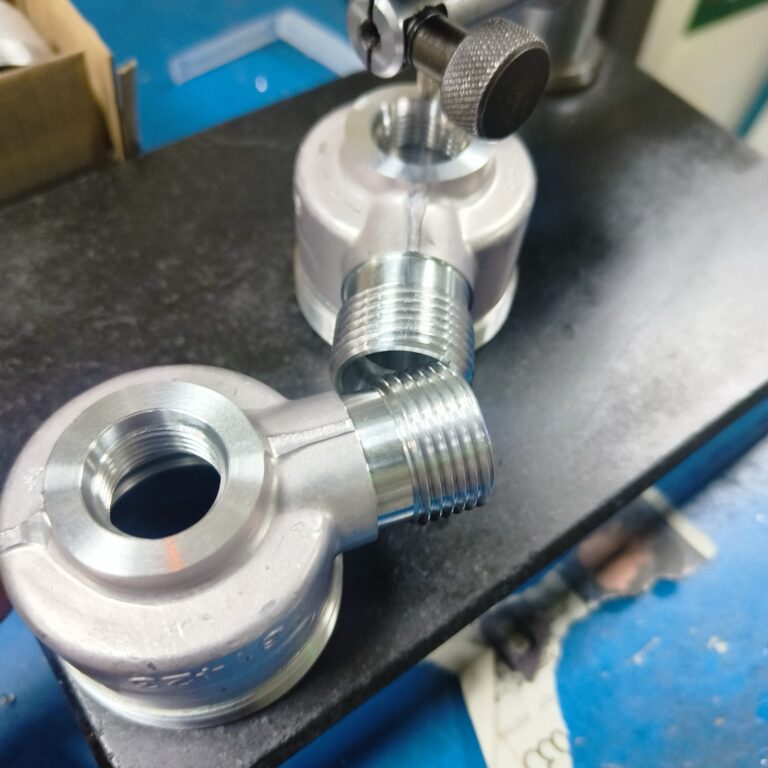
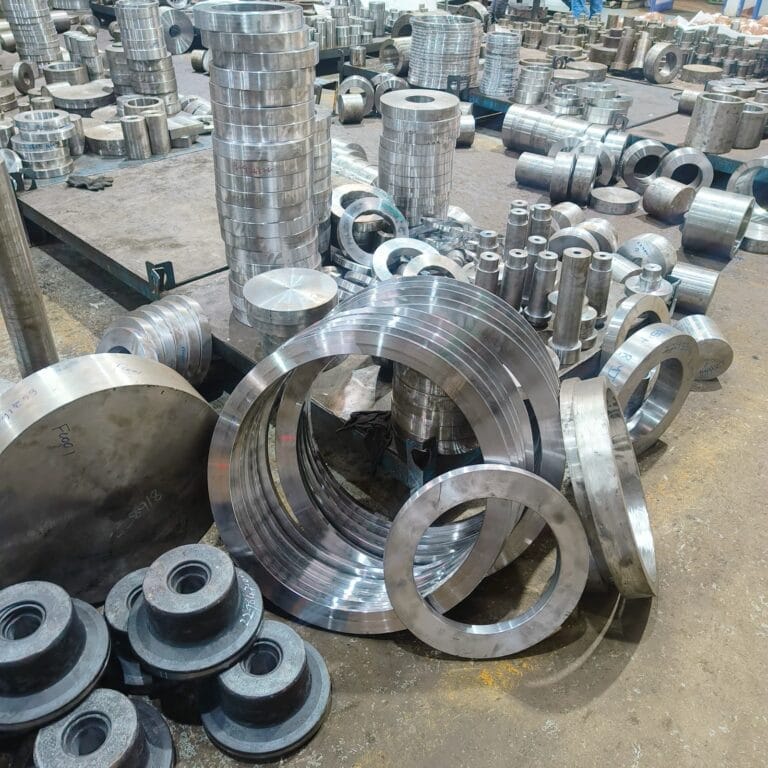
Other Industries We Serve
We deliver machining support across sectors that require consistency, material reliability, and tight dimensional control.
- Solid Progress
Our Manufacturing metrics
Frigate brings stability, control, and predictable performance to your sourcing operations through a structured multi-vendor system.
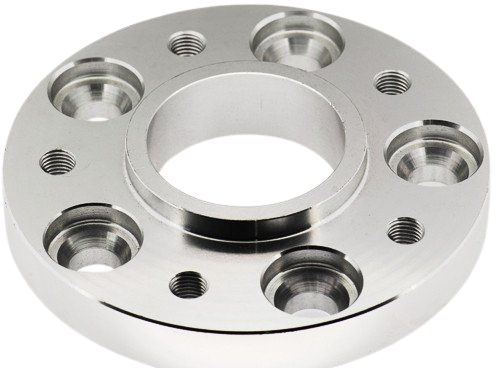
2.8X
Sourcing Cycle Speed
Frigate’s pre-qualified network shortens decision time between RFQ and PO placement.
94%
On-Time Delivery Rate
Structured planning windows and logistics-linked schedules improve project-level delivery reliability.
4X
Multi-Part Consolidation
We enable part family batching across suppliers to reduce fragmentation.
22%
Quality Rejection Rate
Multi-level quality checks and fixed inspection plans lower non-conformities.
30%
Procurement Costs
Optimized supplier negotiations and bulk order strategies reduce your overall sourcing expenses.
20%
Manual Processing Time
Automation of sourcing and supplier management significantly reduces time spent on manual tasks.
Get Clarity with our Manufacturing Insights
- FAQ
Having Doubts? Our FAQ
Check all our Frequently Asked Questions in CNC Machining
Frigate uses low-expansion alloys and actively controls tool temperature during CNC operations. Machining parameters are adjusted in real time to prevent thermal growth in parts like optical mounts and incubator brackets. Dimensional stability is verified through in-process probing and final-stage coordinate measuring machine (CMM) checks. This allows reliable installation in temperature-controlled laboratory equipment.
Frigate applies optimized toolpaths and fine-tipped carbide inserts to prevent burr formation on ports and channel openings. For materials like 316L and PTFE-seated fittings, low-pressure air blast and edge deburring are done under magnification. Post-machining inspections confirm there are no micro-obstructions that could interfere with fluid flow. This supports error-free operation in microfluidic and dispensing systems.
Frigate uses custom fixturing and low-clamp machining setups to reduce residual stress in extended frame parts. Material is rough-machined and stress-relieved before final contouring. In-process sensors track deflection during turning and milling to maintain part symmetry. The result is stable frame geometry suitable for high-precision lab platforms and analyzer assemblies.
Frigate machines optical mounts and robot head brackets using multi-axis CNC centers with thermal drift compensation. Fixtures hold the part rigidly without distortion while high-speed spindles maintain tool sharpness across all passes. Feature tolerances down to ±0.005 mm are validated using laser micrometers and 3D inspection scans. This enables consistent alignment and calibration in lab automation systems.
Frigate controls final surface finish using precision end mills and polishing passes with sub-micron feed rates. All machined parts undergo visual and tactile inspection under cleanroom lighting conditions. For critical surfaces, Ra values are measured using contact profilometers to meet lab-grade smoothness standards. This reduces contamination risk and supports long-term sterility.
We'd love to Manufacture for you!
Submit the form below and our representative will be in touch shortly.
LOCATIONS
Global Sales Office
818, Preakness lane, Coppell, Texas, USA – 75019
Registered Office
10-A, First Floor, V.V Complex, Prakash Nagar, Thiruverumbur, Trichy-620013, Tamil Nadu, India.
Operations Office
9/1, Poonthottam Nagar, Ramanandha Nagar, Saravanampatti, Coimbatore-641035, Tamil Nadu, India. ㅤ
Other Locations
- Bhilai
- Chennai
- Texas, USA