High-Fidelity CNC Machining for Structural Load Components
Maintains tolerance stability under dynamic field stress.
Frigate Optimizes High-Load Joint Machining Pathways
High Aspect Ratio Machining
Synchronized axis control and anti-deflection supports ensure straightness and torsional stability in long, load-bearing structural components.
Global Part Consistency
Standardized CAM templates and cloud-integrated controls enable repeatable dimensional output across all Frigate manufacturing locations.
Load Interface Reinforcement
Hybrid machining paths enhance surface integrity at stress zones, preventing microfractures and improving fatigue resistance under cyclic off-road loading.
Our Clients
Trusted by Engineers and Purchasing Leaders
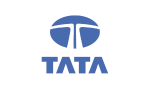
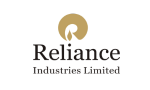


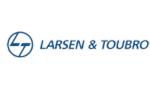
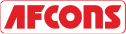


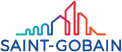

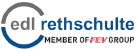

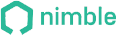
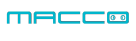









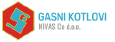
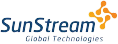

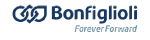


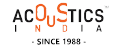
Ensure Full Traceability Across Critical Components
Lifecycle-critical parts demand traceable process control to ensure accountability, reproducibility, and failure response across operational environments.
Embed machine ID, operator credentials, and live spindle usage history within each component’s production record for real-time traceability.
Monitor tool wear cycles, cut parameters, and tool offsets to detect process deviations before they affect dimensional outcomes.
Digitally store CMM data, surface finish records, and dimensional tolerances per component, enabling audit-ready compliance and root cause diagnostics.

Enable Supply Chain Continuity for Critical SKUs
High-risk components require redundant CNC paths and disaster-resilient production strategies to ensure delivery reliability under fault conditions.
Maintain process-matched programs and tooling across two separate CNC platforms to switch production within minutes during machine failure.
Replicate jigs, zero-point clamping, and inspection fixtures across machines to avoid recalibration delays during failover.
Enforce version-locked NC code and simulation-verified paths to eliminate variation between primary and backup production streams.

Error-Proof Program Control
Parts used in kinematic systems and load-transfer zones must not only meet spec but behave correctly during final assembly.
Model functional fits and mating conditions in virtual assemblies to predict and eliminate misalignment during physical integration.
Use clash detection and real-time mockup overlays to feed critical tolerance adjustments into the machining program.
Adapt tolerances and surface specs based on mating behavior—especially for pivots, articulations, and hydraulically actuated interfaces.

Our Machined Products
We support your production needs with CNC-machined parts, subassemblies, and performance-critical components.
- Real Impact
Words from Clients
See how global OEMs and sourcing heads describe their experience with our scalable execution.
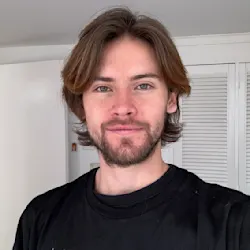
“Quick turnaround and solid quality.”
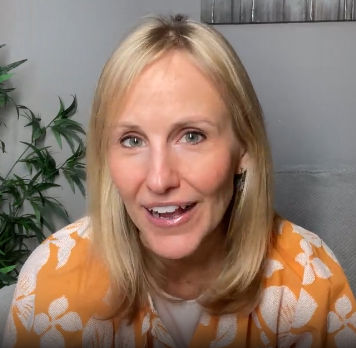
“The instant quote tool saved us time, and the parts were spot-on. Highly recommend Frigate!”
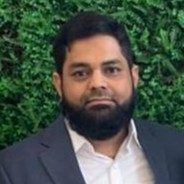
“I would strongly recommend Frigate to anyone who wants to do Rapid Prototyping, and take their ideas to manufacturing. One firm doing all kinds of Product Development!”
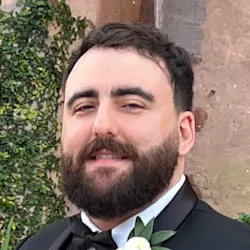
“Great service, fair price, and the parts worked perfectly in our assembly.”
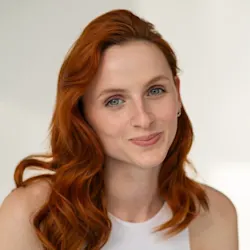
“Top-notch machining and fast shipping. Very satisfied with the results.”
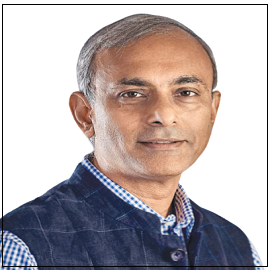
“The next disruption is happening in Prototyping & Manufacturing on-demand and Frigate is leading the way! I personally believe the Frigate's way of IIOT enabled cloud platform with Al.”
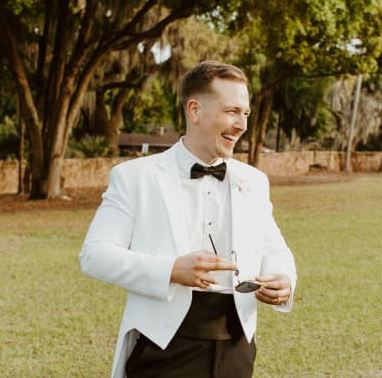
“Frigate delivered high-quality parts at a competitive price. The instant quote tool is a huge plus for us!”

“We appreciate the precision and quality of the machined components in the recent delivery—they meet our specifications perfectly and demonstrate Frigate’s capability for excellent workmanship.”
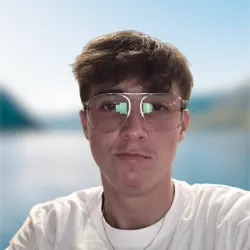
“Flawless execution from quote to delivery.”

“I am absolutely happy to work with supplier like Frigate who were quite proactive & result oriented . Frigate has high willingness team who has strong know how & their passion towards the products & process were absolutely thrilling.”
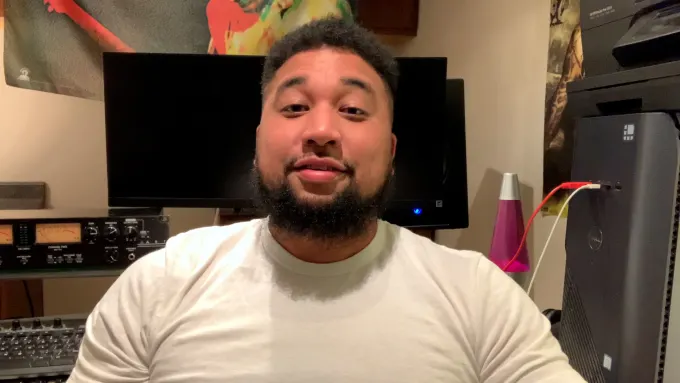
“The precision on these parts is impressive, and they arrived ahead of schedule. Frigate’s process really stands out!”
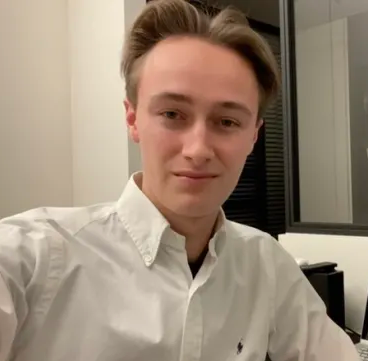
“Parts were exactly as spec’d, and the instant quote made budgeting a breeze.”
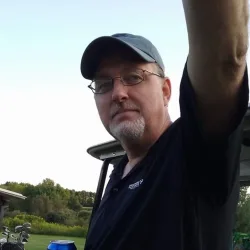
“Good value for the money.”
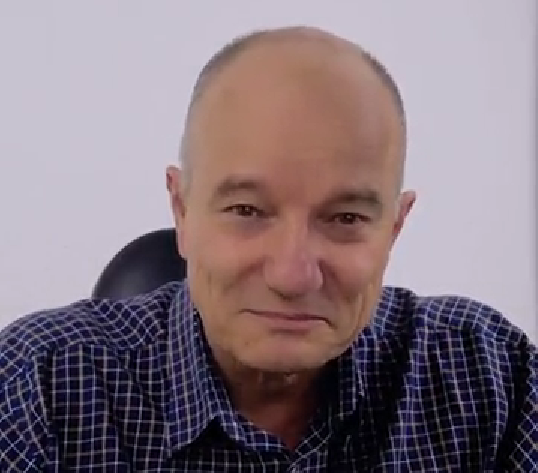
“The finish was perfect, and the team was easy to work with.”

“Working with Frigate has been great. Their proactive, results-driven approach and expertise shine through in every project. It's been a pleasure collaborating with them.”

"We are highly satisfied with the timely delivery and quality of the MIG Welding Cable from Frigate. Their attention to detail, secure packaging, and quick responsiveness stood out. We confidently recommend Frigate Engineering Services Pvt. Ltd. as a reliable manufacturing partner."
- We export to 12+ countries
Frigate’s Global Presence
Frigate takes pride in facilitating “Make in India for the globe“. As our global network of Frigaters provides virtually limitless capacity, and through our IoT enabled platform your parts go directly into production. By digitally and technologically enabling “the silent pillars of the economy” MSME and SME manufacturing industries, we are able to tap the huge potential for manufacturing to bring the best results for our clients.

100,000+
Parts Manufactured
250+
Frigaters
2000+
Machines
450+
Materials
25+
Manufacturing Process
- Solid Progress
How You Benefit with Us
Frigate brings stability, control, and predictable performance to your sourcing operations through a structured multi-vendor system.
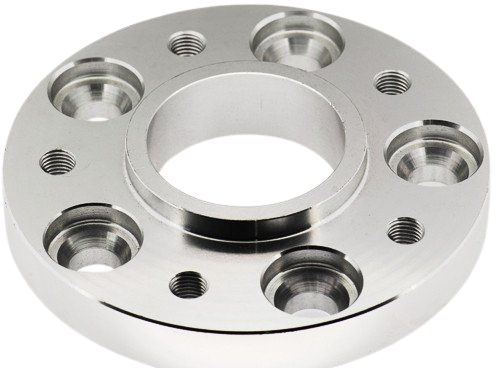
2.8X
Sourcing Cycle Speed
Frigate’s pre-qualified network shortens decision time between RFQ and PO placement.
94%
On-Time Delivery Rate
Structured planning windows and logistics-linked schedules improve project-level delivery reliability.
4X
Multi-Part Consolidation
We enable part family batching across suppliers to reduce fragmentation.
22%
Quality Rejection Rate
Multi-level quality checks and fixed inspection plans lower non-conformities.
30%
Procurement Costs
Optimized supplier negotiations and bulk order strategies reduce your overall sourcing expenses.
20%
Manual Processing Time
Automation of sourcing and supplier management significantly reduces time spent on manual tasks.
Other Industries We Serve
We deliver machining support across sectors that require consistency, material reliability, and tight dimensional control.
Get Clarity with our Manufacturing Insights
Frigate machines long structural components like booms and welded frames using synchronized axis control and anti-deflection supports. These setups eliminate bending or warping during machining, especially on parts with high length-to-diameter ratios. In-process probing checks the dimensions during machining, and toolpaths are automatically adjusted to compensate for thermal expansion and machine drift. This allows Frigate to hold tight tolerances—typically within ±0.01 mm—even on parts exceeding several meters in length.
Yes. Frigate uses a centralized CAM system and a cloud-integrated toolpath library to ensure the same CNC code runs across all facilities. Each machine is equipped with calibrated tooling and locked parameter settings to prevent variation. Even if the part is machined in different regions, it maintains identical features like bore alignment, thread depth, or mounting hole pitch. This approach guarantees dimensional uniformity, helping OEMs reduce inspection overhead and streamline final assembly.
Frigate uses hybrid cutting techniques that combine trochoidal roughing with high-feed finishing for components exposed to dynamic and cyclic loading. This method improves the surface integrity of areas like bearing seats, clevis mounts, and tie-rod ends—where fatigue failure often starts. Real-time tool load monitoring also ensures that stress does not accumulate due to uneven cutting pressure. This results in a surface that resists microcracking and holds up under vibration, impact, and long-term operational wear.
Frigate provides complete traceability on each lifecycle-critical part. Every component includes data such as machine ID, toolpath version, operator code, and tool wear history. During production, CMM inspection results and surface finish data are stored digitally and linked to the part’s serial number. If any issue arises in the field, procurement or engineering teams can trace the part’s full machining history and isolate the root cause. This exceeds ISO 9001 traceability requirements and supports high-reliability applications.
Frigate uses digital twin models and tolerance stack-up simulations before machining begins. This allows us to visualize how the part will behave once installed—especially for pivot points, hydraulic cylinder ends, and multi-hole assemblies. We then adjust the CNC programs to account for real-world behavior, not just ideal dimensions. By doing this, Frigate ensures that parts don’t just meet spec on paper but also perform flawlessly during final equipment assembly without causing alignment or fitment issues.
We'd love to Manufacture for you!
Submit the form below and our representative will be in touch shortly.
LOCATIONS
Global Sales Office
818, Preakness lane, Coppell, Texas, USA – 75019
Registered Office
10-A, First Floor, V.V Complex, Prakash Nagar, Thiruverumbur, Trichy-620013, Tamil Nadu, India.
Operations Office
9/1, Poonthottam Nagar, Ramanandha Nagar, Saravanampatti, Coimbatore-641035, Tamil Nadu, India. ㅤ
Other Locations
- Bhilai
- Chennai
- Texas, USA