Biotechnology & Laboratory Equipment Machining Solutions
Precision-Machined Components for Scientific Devices, Lab Systems, and Diagnostic Assemblies, delivered by Frigate’s CNC Expertise.
Frigate meets biotech manufacturing needs with validated CNC metal machining
High-Precision Component Tolerances
Maintain dimensional accuracy within ±0.002 mm for fluidic channels, sample holders, and sensor housings using 5-axis CNC setups.
Corrosion-Resistant Material Machinin
Process stainless steel 316L, aluminum alloys, and nickel-based metals under moisture-controlled conditions for lab and clinical safety.
Micro-Feature Machining for Compact Systems
Machine ports, threads, and sealing grooves under 0.5 mm with CAM-optimized strategies for microfluidics and compact analytical instruments.
Our Clients
Trusted by Engineers and Purchasing Leaders
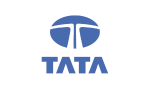
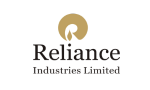


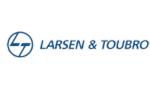
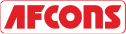


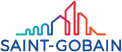

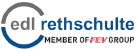

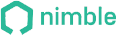
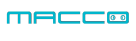









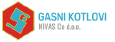
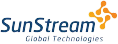

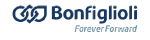


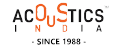
Maintain Equipment Performance Across Cleaning and Handling Cycles
Wear resistance and dimensional retention are critical in lab components exposed to frequent sanitation and mechanical adjustments.
Surface preparation and fine deburring avoid microbial buildup and preserve dimensional control through autoclaving and chemical sterilization.
Create contact surfaces using passivated stainless or coated aluminum for secure fitment in clamps, tube connectors, and stage mounts.
Edge rounding and chip load balancing help prevent cracking or distortion in mounting interfaces and screw bosses under cyclic stress.

Align with Global Laboratory Manufacturing Standards
All machining workflows support part qualification under ISO 13485, FDA 21 CFR Part 820, and ASTM-compliant inspection standards.
Use CMM, vision systems, and interferometry to inspect bore concentricity, sealing edge flatness, and enclosure symmetry.
Each production lot is documented with revision tracking, operator IDs, and machine logs to align with regulatory traceability.
Validation routines include Cp/Cpk data and gauge R&R studies to verify part consistency across batch volumes and time intervals.

Extend Part Reliability Through Surface Processing
Surface modification helps improve instrument compatibility and extend product life in lab and testing environments.
Apply DLC or anodic coatings on sliding surfaces and hinges to minimize galling in modular assemblies and micro-movement joints.
Use vibratory finishing, controlled polishing, and Ra smoothing under 0.2 µm for components interfacing with samples or labware.
Fine deburring under magnification ensures smooth assembly of enclosures, adapters, and structural mounts without tolerance interference.

Our Machined Products
We support your production needs with CNC-machined parts, subassemblies, and performance-critical components.
- Real Impact
Words from Clients
See how global OEMs and sourcing heads describe their experience with our scalable execution.
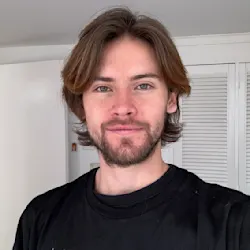
“Quick turnaround and solid quality.”
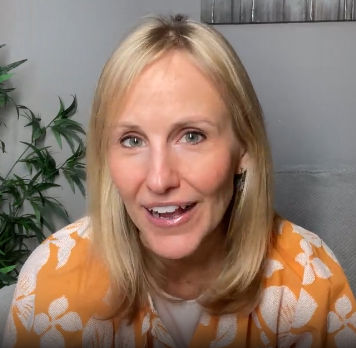
“The instant quote tool saved us time, and the parts were spot-on. Highly recommend Frigate!”
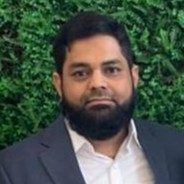
“I would strongly recommend Frigate to anyone who wants to do Rapid Prototyping, and take their ideas to manufacturing. One firm doing all kinds of Product Development!”
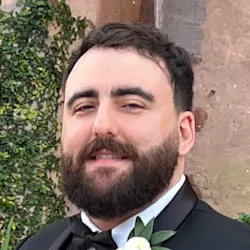
“Great service, fair price, and the parts worked perfectly in our assembly.”
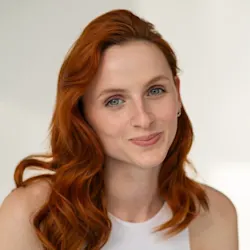
“Top-notch machining and fast shipping. Very satisfied with the results.”
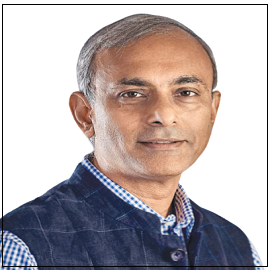
“The next disruption is happening in Prototyping & Manufacturing on-demand and Frigate is leading the way! I personally believe the Frigate's way of IIOT enabled cloud platform with Al.”
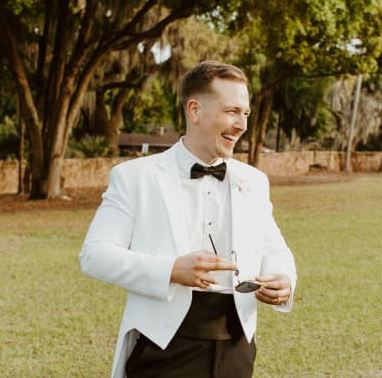
“Frigate delivered high-quality parts at a competitive price. The instant quote tool is a huge plus for us!”

“We appreciate the precision and quality of the machined components in the recent delivery—they meet our specifications perfectly and demonstrate Frigate’s capability for excellent workmanship.”
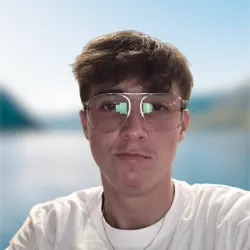
“Flawless execution from quote to delivery.”

“I am absolutely happy to work with supplier like Frigate who were quite proactive & result oriented . Frigate has high willingness team who has strong know how & their passion towards the products & process were absolutely thrilling.”
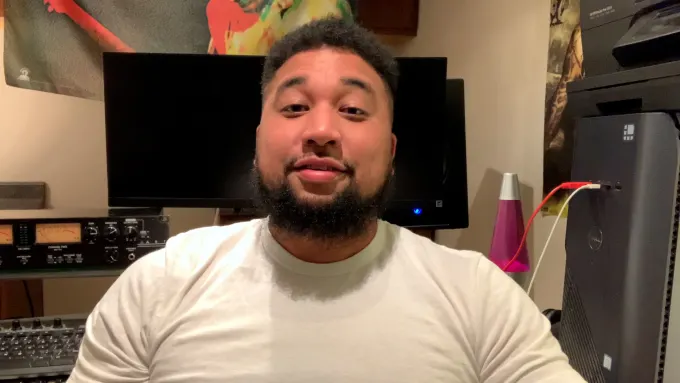
“The precision on these parts is impressive, and they arrived ahead of schedule. Frigate’s process really stands out!”
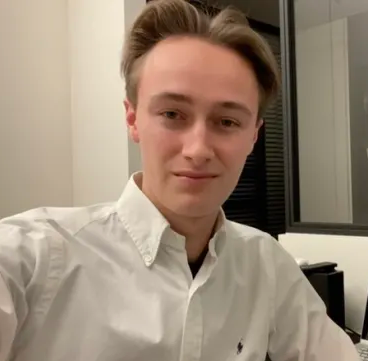
“Parts were exactly as spec’d, and the instant quote made budgeting a breeze.”
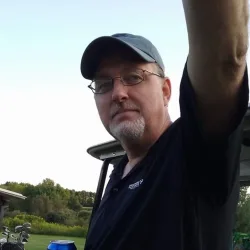
“Good value for the money.”
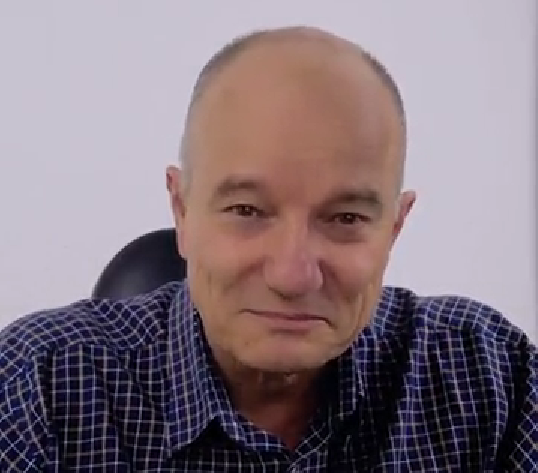
“The finish was perfect, and the team was easy to work with.”

“Working with Frigate has been great. Their proactive, results-driven approach and expertise shine through in every project. It's been a pleasure collaborating with them.”

"We are highly satisfied with the timely delivery and quality of the MIG Welding Cable from Frigate. Their attention to detail, secure packaging, and quick responsiveness stood out. We confidently recommend Frigate Engineering Services Pvt. Ltd. as a reliable manufacturing partner."
- We export to 12+ countries
Frigate’s Global Presence
Frigate takes pride in facilitating “Make in India for the globe“. As our global network of Frigaters provides virtually limitless capacity, and through our IoT enabled platform your parts go directly into production. By digitally and technologically enabling “the silent pillars of the economy” MSME and SME manufacturing industries, we are able to tap the huge potential for manufacturing to bring the best results for our clients.

100,000+
Parts Manufactured
250+
Frigaters
2000+
Machines
450+
Materials
25+
Manufacturing Process
- Solid Progress
How You Benefit with Us
Frigate brings stability, control, and predictable performance to your sourcing operations through a structured multi-vendor system.
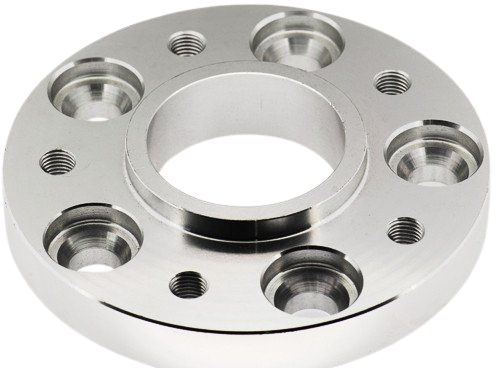
2.8X
Sourcing Cycle Speed
Frigate’s pre-qualified network shortens decision time between RFQ and PO placement.
94%
On-Time Delivery Rate
Structured planning windows and logistics-linked schedules improve project-level delivery reliability.
4X
Multi-Part Consolidation
We enable part family batching across suppliers to reduce fragmentation.
22%
Quality Rejection Rate
Multi-level quality checks and fixed inspection plans lower non-conformities.
30%
Procurement Costs
Optimized supplier negotiations and bulk order strategies reduce your overall sourcing expenses.
20%
Manual Processing Time
Automation of sourcing and supplier management significantly reduces time spent on manual tasks.
Other Industries We Serve
We deliver machining support across sectors that require consistency, material reliability, and tight dimensional control.
Get Clarity with Our Manufacturing Insights
Frigate machines components from corrosion-resistant alloys like 316L stainless steel and anodized aluminum under controlled thermal environments. All critical surfaces undergo deburring, passivation, and polishing to avoid stress concentration and microbial retention. These post-processing methods help maintain surface and dimensional integrity after multiple autoclave and chemical disinfection cycles. This ensures long-term fitment and cleanliness in laboratory applications involving strict hygiene protocols.
Frigate uses high-speed spindles paired with CAM-optimized toolpaths to produce micro features such as ports, threads, and sealing grooves below 0.5 mm. Tool deflection is minimized using balanced chip loads and short overhang tools. Real-time probing and dimensional feedback loops confirm accuracy during machining. This level of precision supports reliable performance in compact diagnostic instruments and sample-handling systems.
Frigate links each production batch with unique operator IDs, toolpaths, and machine logs embedded into a traceable digital audit trail. CMM, laser scanners, and interferometers verify all critical features, including sealing profiles and enclosure fits. Output data is formatted to align with ISO 13485 and FDA 21 CFR Part 820 recordkeeping. These systems ensure regulatory readiness and complete part qualification during client audits.
Frigate applies physical vapor deposition (PVD) coatings such as diamond-like carbon (DLC) to reduce sliding wear in joints and enclosures. Anodizing and passivation are used to boost corrosion resistance without altering tight tolerances. Surface roughness is tuned below Ra 0.2 µm for contact-sensitive parts using polishing and vibratory finishing. These treatments improve durability and compatibility in wet lab and cleanroom environments.
Frigate programs adaptive toolpaths with controlled feed rates and step-down strategies to minimize tool-induced stress. Edge rounding and precise burr removal prevent notch formation in screw bosses and mounting tabs. In-process metrology confirms wall thickness and curvature, reducing the risk of part distortion during assembly or cleaning. These techniques help ensure structural reliability in precision lab hardware.
We'd love to Manufacture for you!
Submit the form below and our representative will be in touch shortly.
LOCATIONS
Registered Office
10-A, First Floor, V.V Complex, Prakash Nagar, Thiruverumbur, Trichy-620013, Tamil Nadu, India.
Operations Office
9/1, Poonthottam Nagar, Ramanandha Nagar, Saravanampatti, Coimbatore-641035, Tamil Nadu, India. ㅤ
Other Locations
- Bhilai
- Chennai
- USA
- Germany