CNC Turning Services for Packaging Machinery
Frigate delivers CNC-turned components that meet the dynamic needs of packaging machinery manufacturers. We work with complex geometries, tight tolerances, and high-volume part consistency using state-of-the-art turning centers.
Our Clients





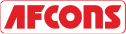

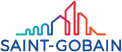


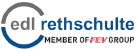

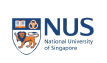
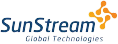

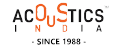




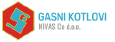
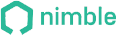
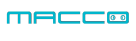












- Precision Tailored to High-Speed Systems
Advantages of Our CNC Turning Service
Our team integrates multi-axis turning with bar feeding and live tooling to enable precise part creation in a single setup.
Hard Turning of Wear Zones
This method improves surface hardness in sealing, guiding, and sliding parts used in high-cycle packaging equipment.
Interrupted Cut Handling
Toolpath strategies and reinforced inserts ensure stability during turning of components with slots, holes, or sharp transitions.
Thin-Walled Section Control
Fine-tuned speed and feed settings prevent deformation in packaging machine shells, rollers, and thin flanges.
- Process
Our CNC Turning Workflow
We use real-time tool monitoring, automated loading, and process feedback loops to manage dimensional accuracy across long runs.


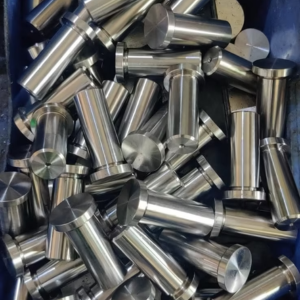
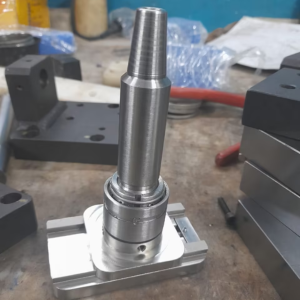
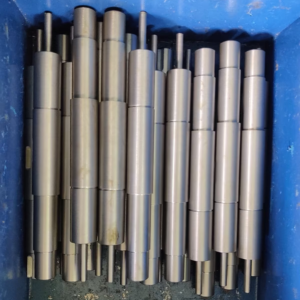

Our team designs the part in CAD software with focus on radial symmetry and tool clearance.
CAM software generates toolpaths based on spindle speeds, feed rates, and material hardness.
Operators load the raw bar stock and calibrate live tooling attachments, ensuring optimal alignment.
The part spins while stationary or live tools shape it via precision radial and axial cuts. Also, Our machines track spindle load and thermal drift in real time.
We perform part-off, facing, and secondary polishing before moving to the inspection stage.
Every part undergoes inspection using CMMs and profile projectors to verify dimensional and geometrical tolerances.
- Real Impact
Words from Clients
See how global OEMs and sourcing heads describe their experience with our scalable execution.
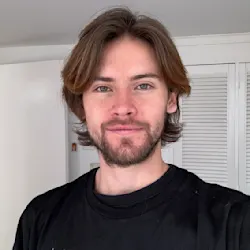
“Quick turnaround and solid quality.”
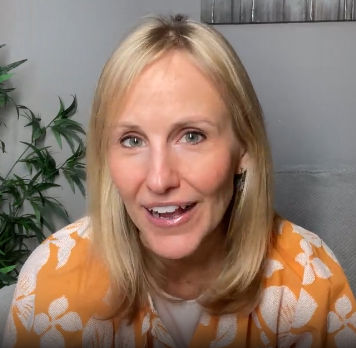
“The instant quote tool saved us time, and the parts were spot-on. Highly recommend Frigate!”
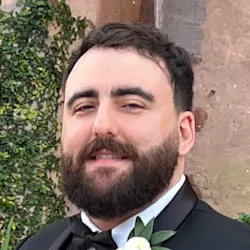
“Great service, fair price, and the parts worked perfectly in our assembly.”
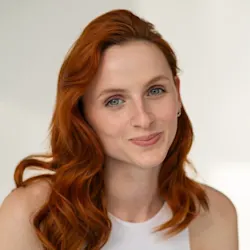
“Top-notch machining and fast shipping. Very satisfied with the results.”
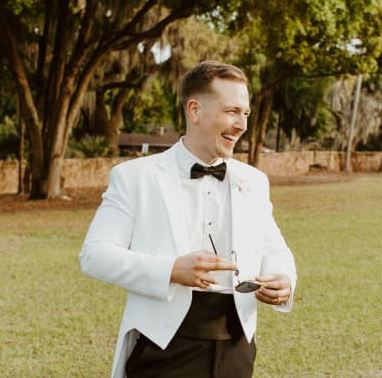
“Frigate delivered high-quality parts at a competitive price. The instant quote tool is a huge plus for us!”

“We appreciate the precision and quality of the machined components in the recent delivery—they meet our specifications perfectly and demonstrate Frigate’s capability for excellent workmanship.”
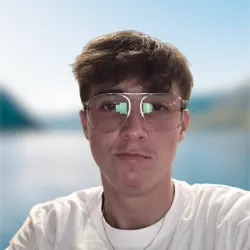
“Flawless execution from quote to delivery.”
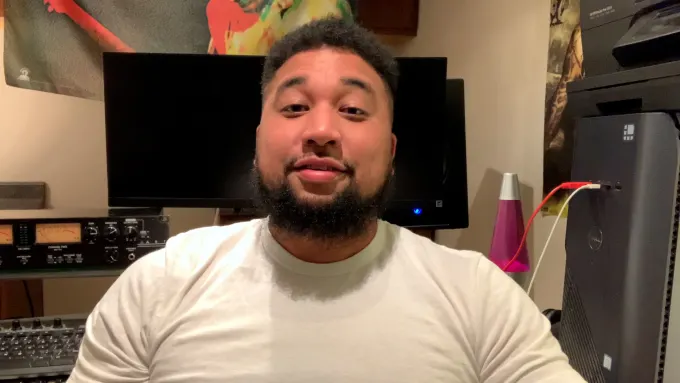
“The precision on these parts is impressive, and they arrived ahead of schedule. Frigate’s process really stands out!”
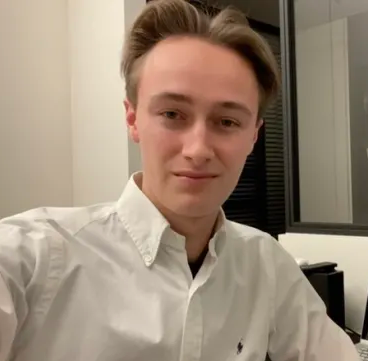
“Parts were exactly as spec’d, and the instant quote made budgeting a breeze.”
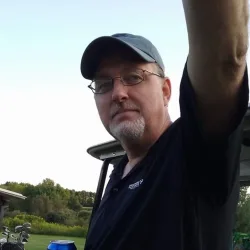
“Good value for the money.”
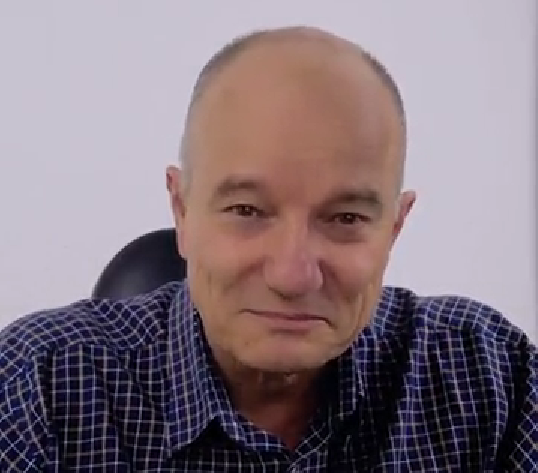
“The finish was perfect, and the team was easy to work with.”
- Surface Finish
Precision Finishes for Packaging Parts
We apply contour turning and burnishing tools to achieve surface smoothness suited for sealing, labeling, and movement-critical parts.
Anodizing
Give your aluminum parts a tough, corrosion-resistant shield with anodizing, reaching surface hardness up to HV 500, while enhancing electrical insulation and durability.
Mechanical Finishing
Smooth out imperfections and refine surfaces to Ra 0.2 µm or better with mechanical finishing techniques like grinding, polishing, and bead blasting.
Heat Treatment
Boost material strength and hardness by heat treating parts at temperatures up to 1100°C, ensuring they meet the mechanical demands of your application.
Electroplating
Add protective or functional metal coatings with electroplating, delivering consistent layers as precise as ±2 µm for improved corrosion resistance and conductivity.
Our Machined Products
We support your production needs with CNC-machined parts, subassemblies, and performance-critical components.
- Material Expertise
CNC Turning Materials
We machine stainless steel, aluminum, bronze, and plastics common in packaging lines. Each material supports specific applications such as corrosion resistance, machinability, or low friction.
- Improve equipment durability with corrosion-resistant grades
- Achieve low part weight using high-strength aluminum alloys
- Optimize wear zones with high-machinability bronze
A2 Tool Steel is a high-carbon, high-chromium steel known for its toughness and wear resistance. It’s ideal for producing durable, high-strength parts that can withstand heavy use.
Aluminum is a lightweight, corrosion-resistant metal with good machinability. Because of its strength-to-weight ratio, it’s commonly used in aerospace, automotive, and various industrial applications.
Brass is a copper-zinc alloy known for its machinability and corrosion resistance. It’s used for components requiring precise detailing and good mechanical properties.
Bronze is a copper-tin alloy with excellent wear resistance and strength. It’s often used for bushings, bearings, and other friction-prone components.
Cast Iron is known for its high wear resistance and machinability. It’s used in heavy-duty applications such as machinery parts and engine components.
Copper offers excellent thermal and electrical conductivity. It’s used in applications requiring heat dissipation or electrical conductivity, such as electronic components.
Steel is a versatile material known for its strength and durability. It’s used in various applications, from construction to automotive parts.
Titanium is a lightweight, high-strength metal with excellent corrosion resistance. It’s used in aerospace, medical implants, and high-performance engineering applications.
Stainless Steel offers high corrosion resistance and strength. It’s widely used in applications ranging from kitchen equipment to industrial machinery.
Zinc is a ductile and corrosion-resistant metal known for its excellent machinability, especially in its alloy forms. It's often used for components requiring intricate details, good surface finish, and precise dimensions, commonly found in automotive, hardware, and electrical applications.
- Cycle-Ready Integration
Key Production Features
Our methods reduce setup time, improve repeatability, and support quick ramp-ups. This allows consistent part flow even in mixed-volume orders.
- Minimize changeover delays with program-controlled tooling
- Get uniform parts across batches with SPC-driven checks
- Scale order sizes without affecting throughput
- Reduce scrap with digital simulation checks before machining
- Lower rework by using real-time deviation tracking
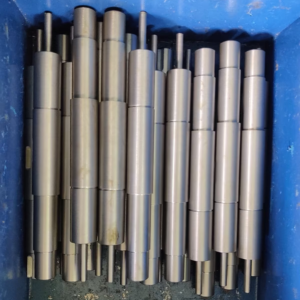
- Regulatory Assurance
Compliance for CNC Turning Services
Frigate meets strict packaging industry norms through documented practices and full batch traceability. Our team follows sector-specific guidance to maintain accuracy and hygiene requirements. We track tool life, part wear, and calibration metrics for each project.
- Maintain traceability with serial-coded part ID logs
- Align production with ISO and CE marking standards
- Reduce downtime with compliance-based preventive maintenance
Quality management practices ensure standardized machining outputs for packaging equipment parts.
Meets food-grade production support for secondary packaging components where required.
Ensures low-lead and hazardous material-free parts for eco-compliant machinery.
Controls restricted substances during turning processes aligned with EU directives.
Supports export-ready assemblies and modular components for packaging lines in regulated markets.
Covers safety assurance on select electrical-mechanical turned parts used in packaging control units.
- We export to 12+ countries
Frigate’s Global Presence
Frigate takes pride in facilitating “Make in India for the globe“. As our global network of Frigaters provides virtually limitless capacity, and through our IoT enabled platform your parts go directly into production. By digitally and technologically enabling “the silent pillars of the economy” MSME and SME manufacturing industries, we are able to tap the huge potential for manufacturing to bring the best results for our clients.

100,000+
Parts Manufactured
250+
Frigaters
2000+
Machines
450+
Materials
25+
Manufacturing Process

- Quality Verification
Testing Standards for CNC Turning Services
To measure the roundness of cylindrical features, ensuring they meet tolerance requirements.
To check internal surfaces for flatness, critical for sealing and assembly purposes.
To identify burrs or sharp edges that may affect assembly or safety.
To ensure that complex profiles (e.g., contours, curves) conform to design specifications.
To check the topography and texture of the surface, ensuring it meets the required specifications for function or aesthetics.
To verify that the surface hardness depth meets the required specifications for wear resistance.
To measure internal stresses that could lead to deformation or failure during or after machining.
To verify grain structure, inclusions, and material consistency, ensuring the part meets performance requirements.
- Production Snapshots
Turned Parts for Packaging Machinery
We apply thermal stability control and axis calibration before every shift to keep tolerances within ±5 microns. View samples of turned parts used in filling heads, rotary sealing units, label dispensers, and feed rollers.
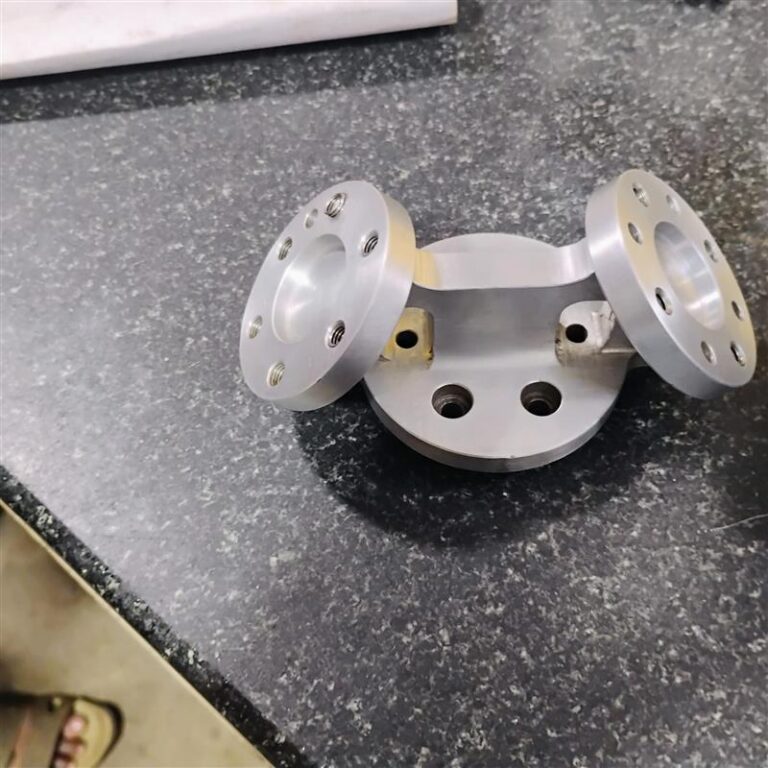
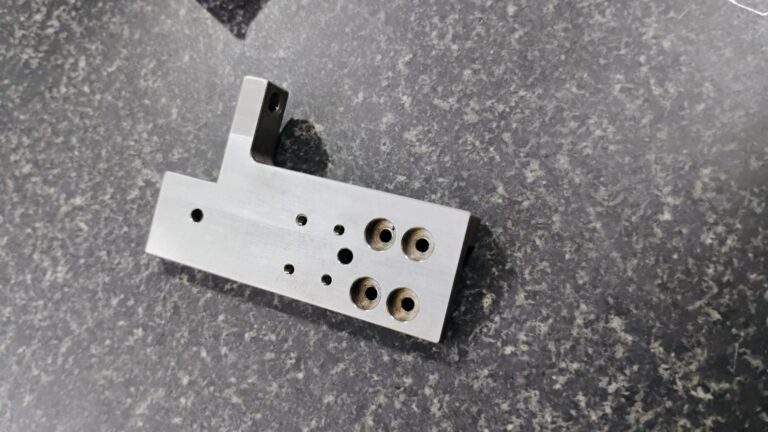
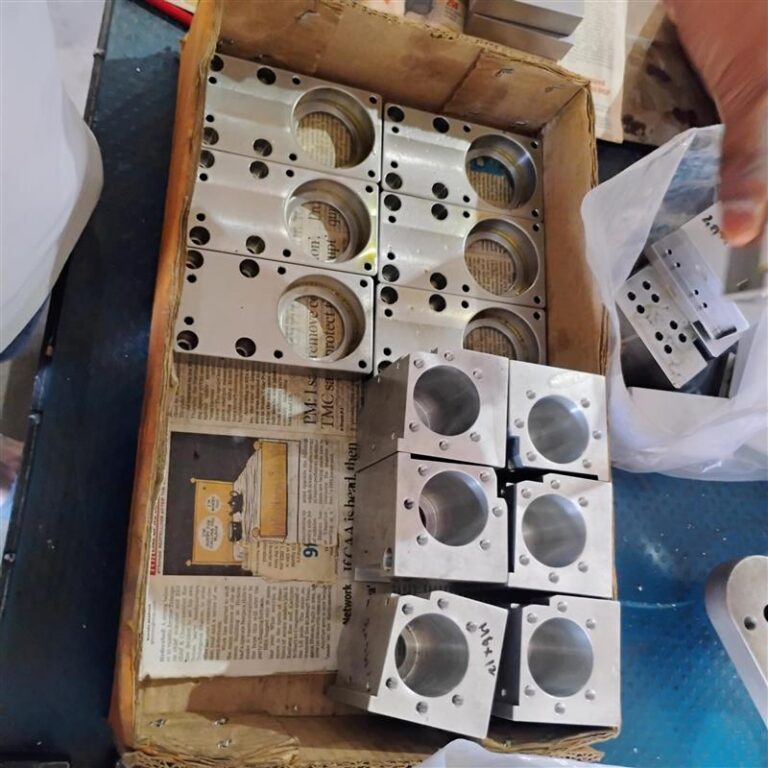
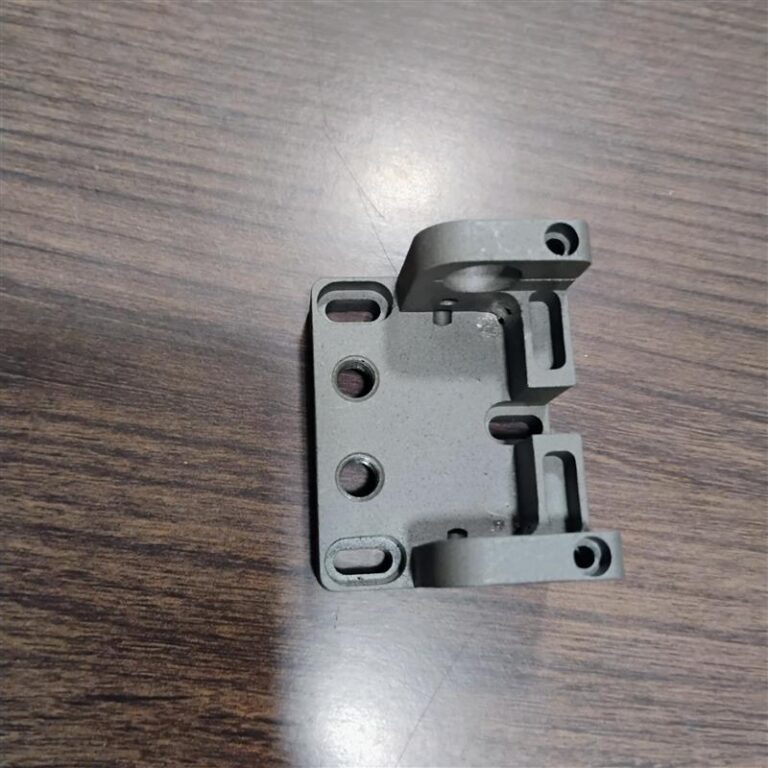
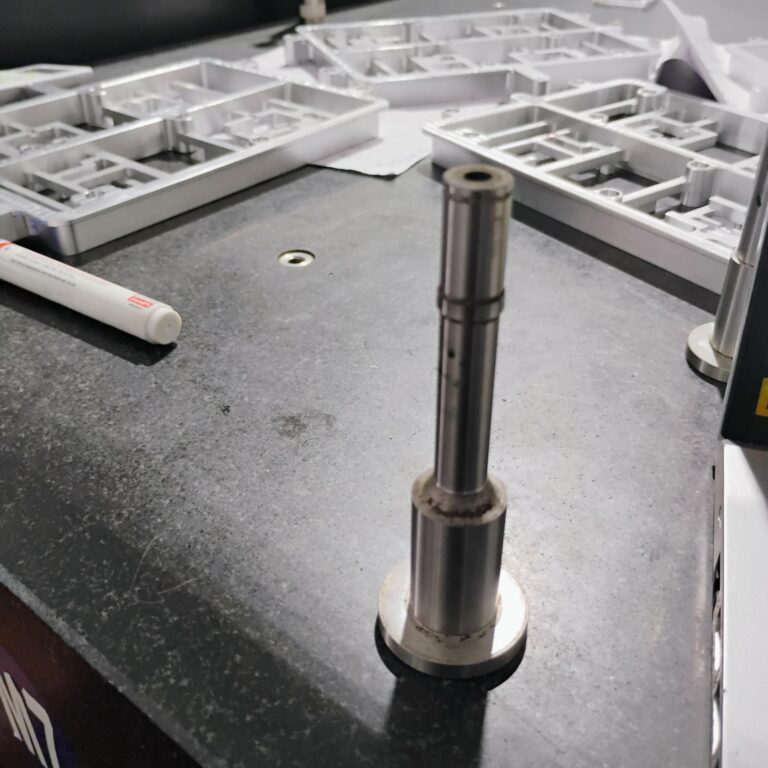
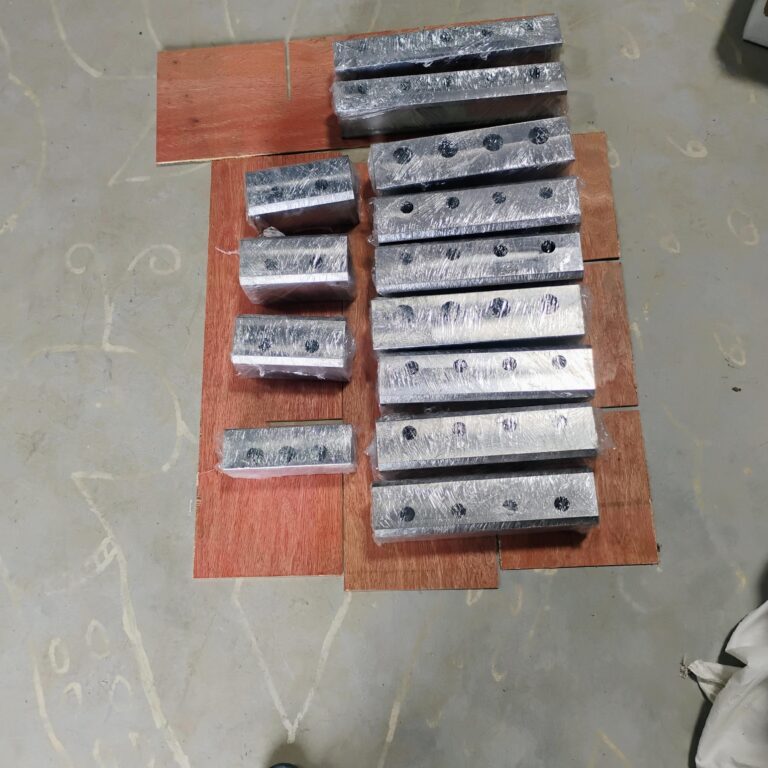
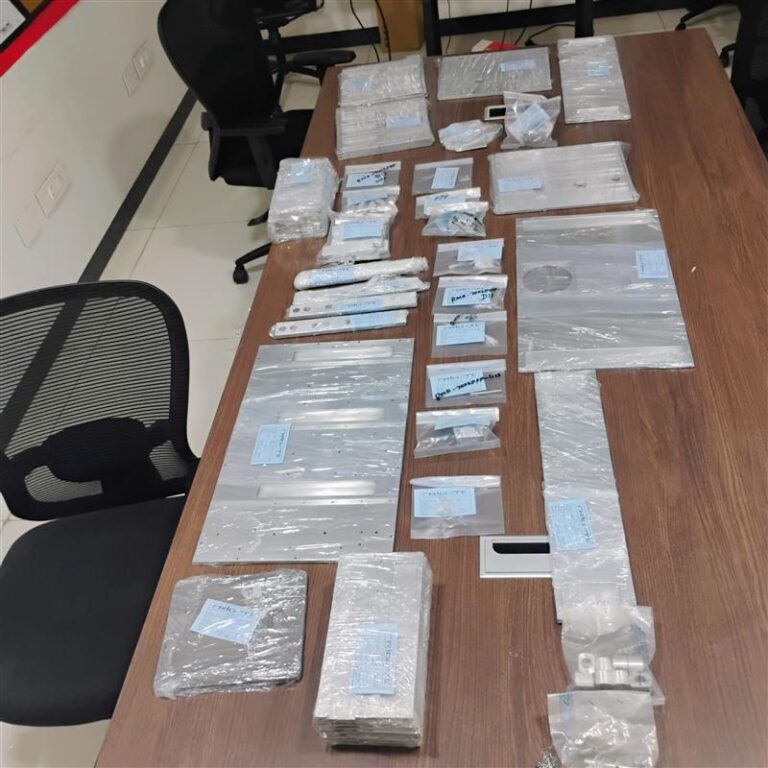

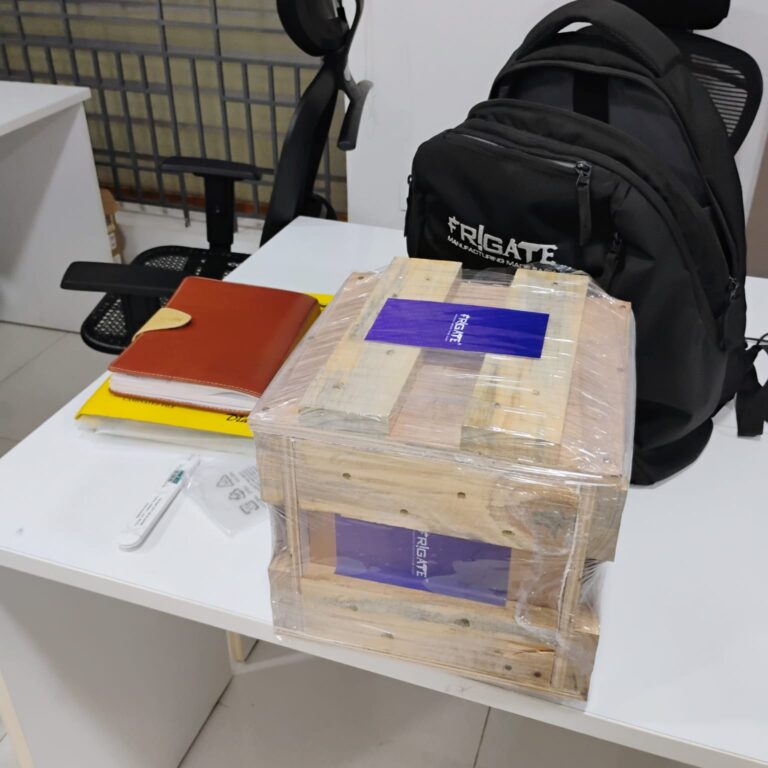


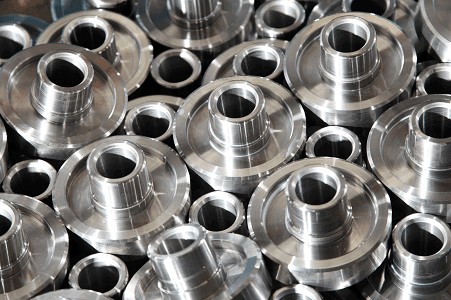
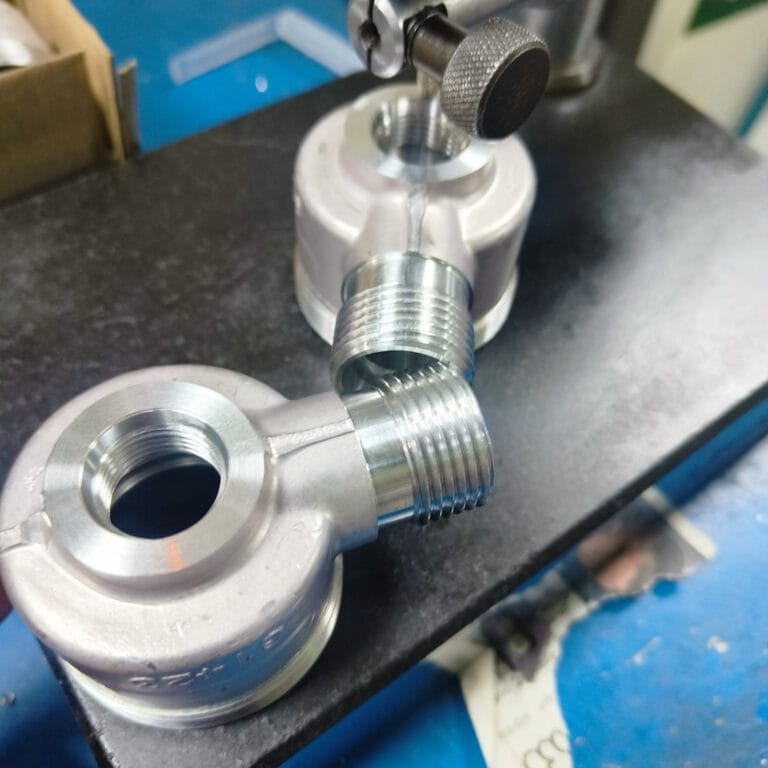
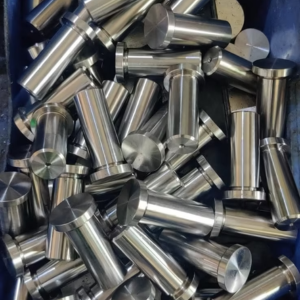
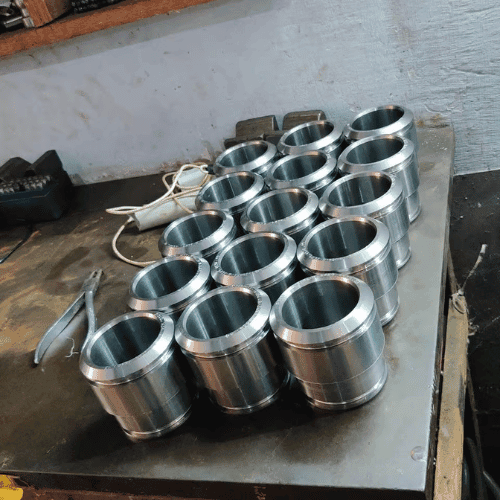
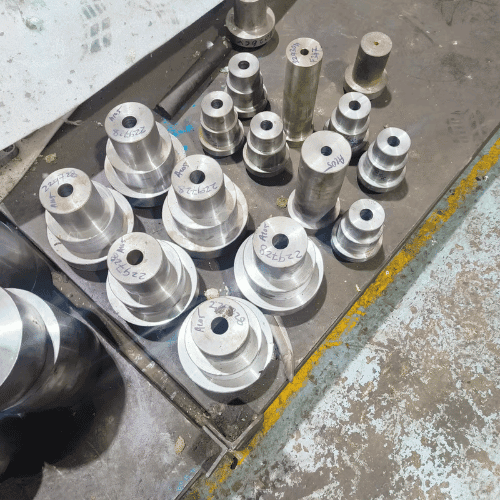
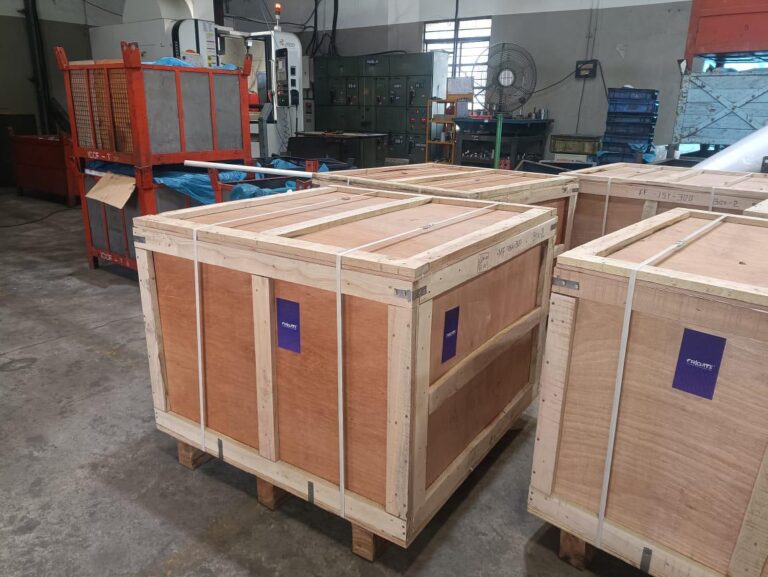
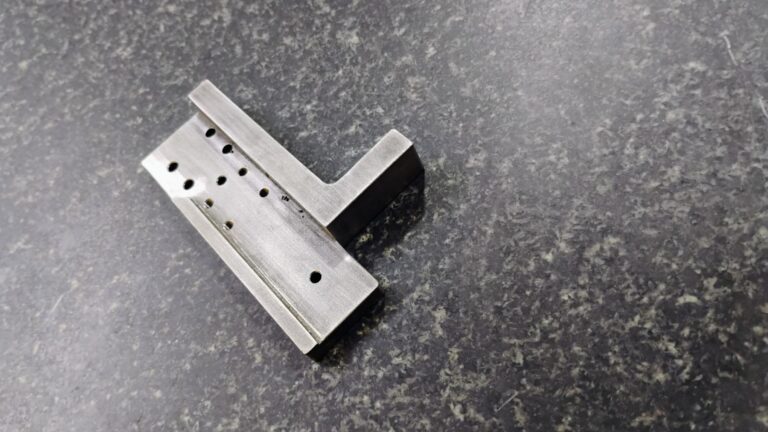
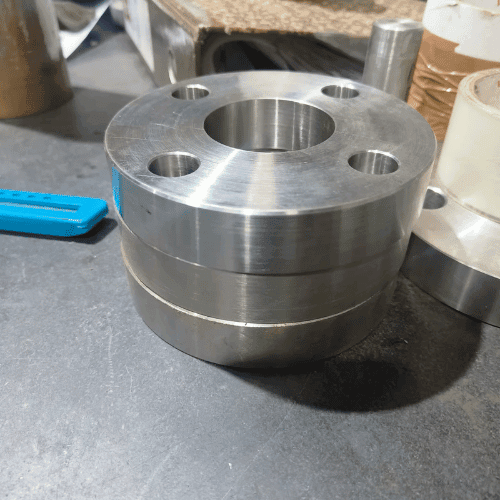
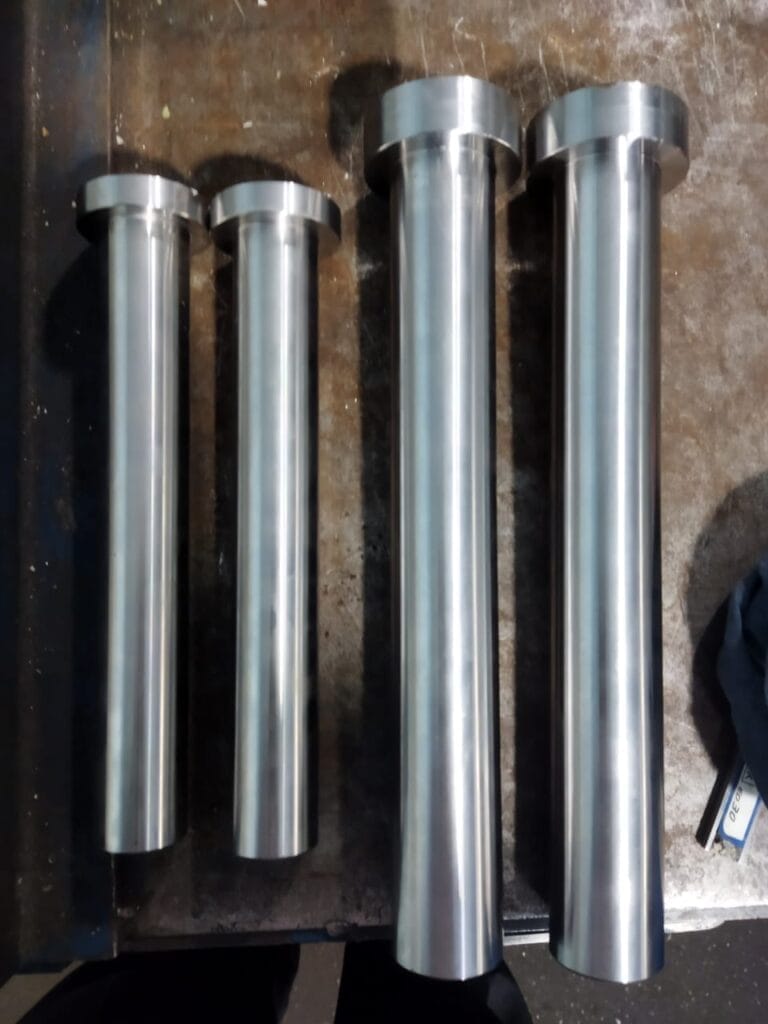

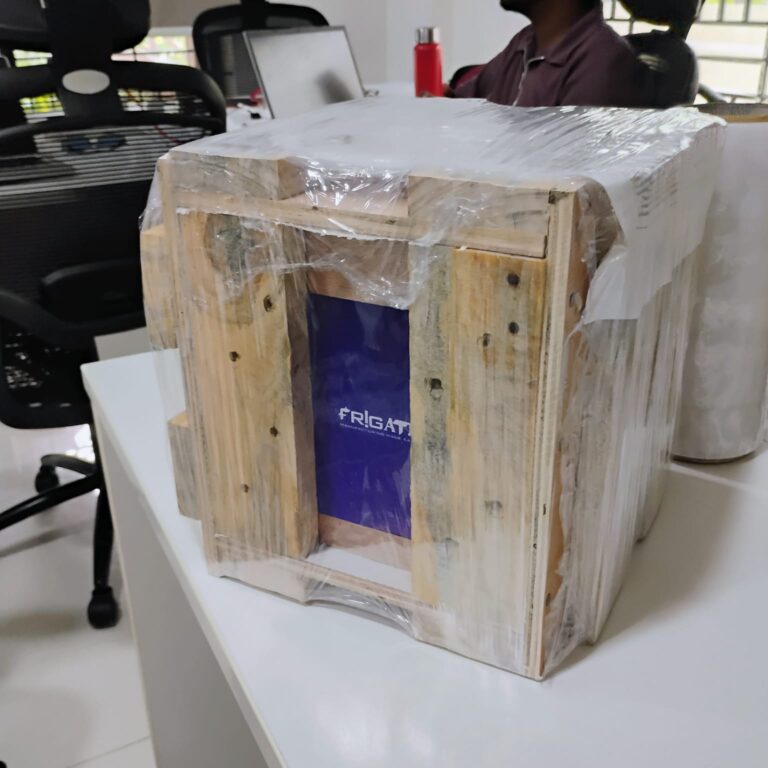

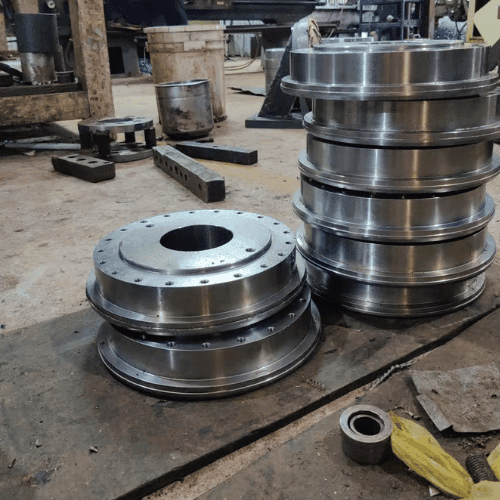
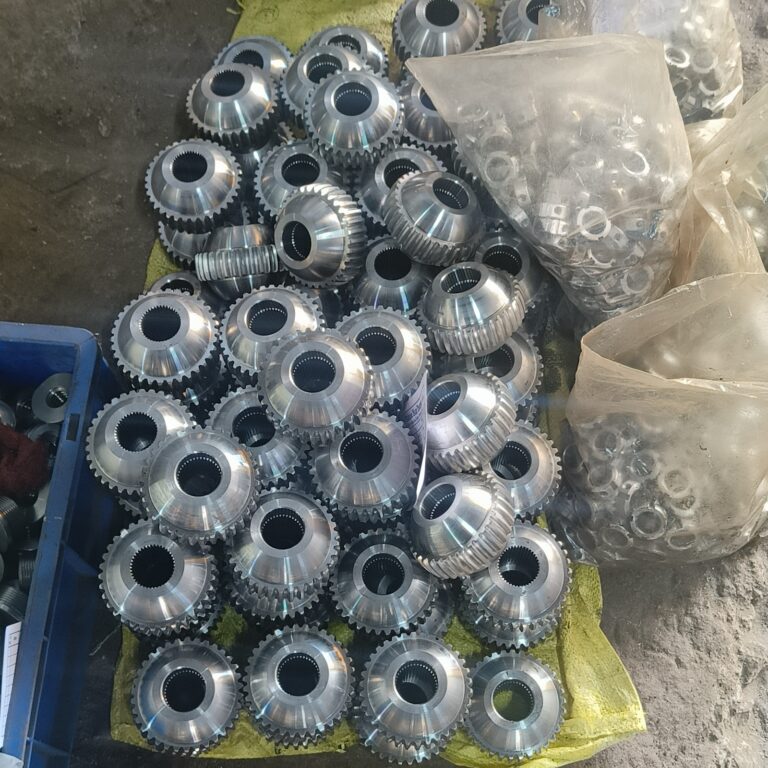
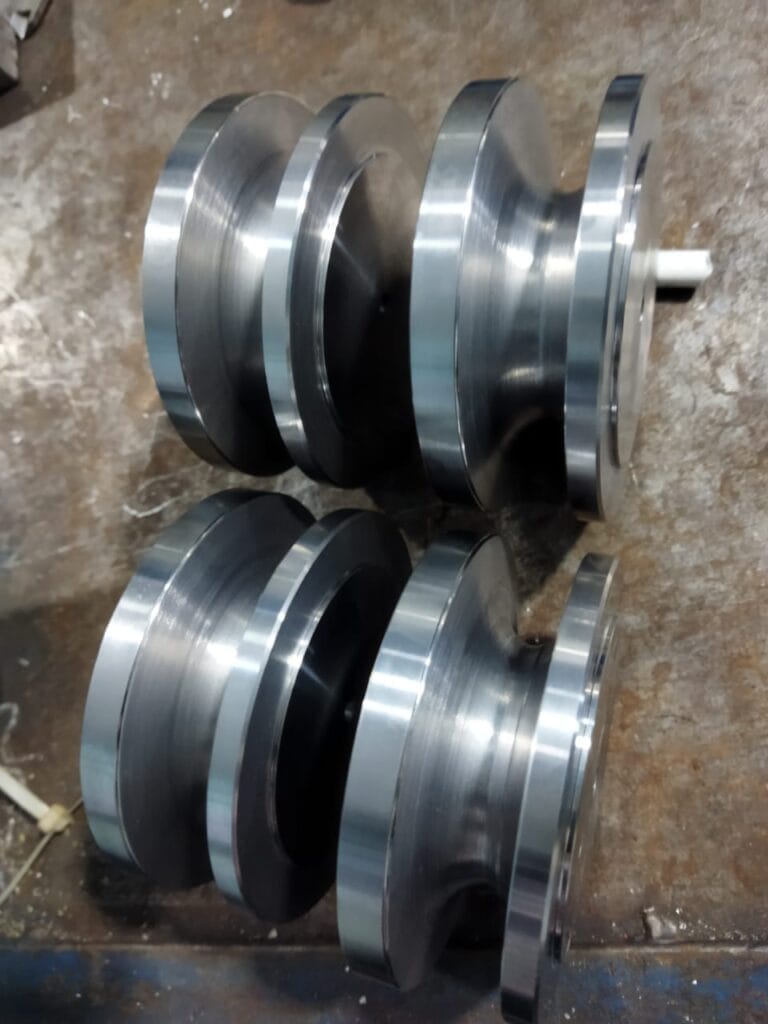
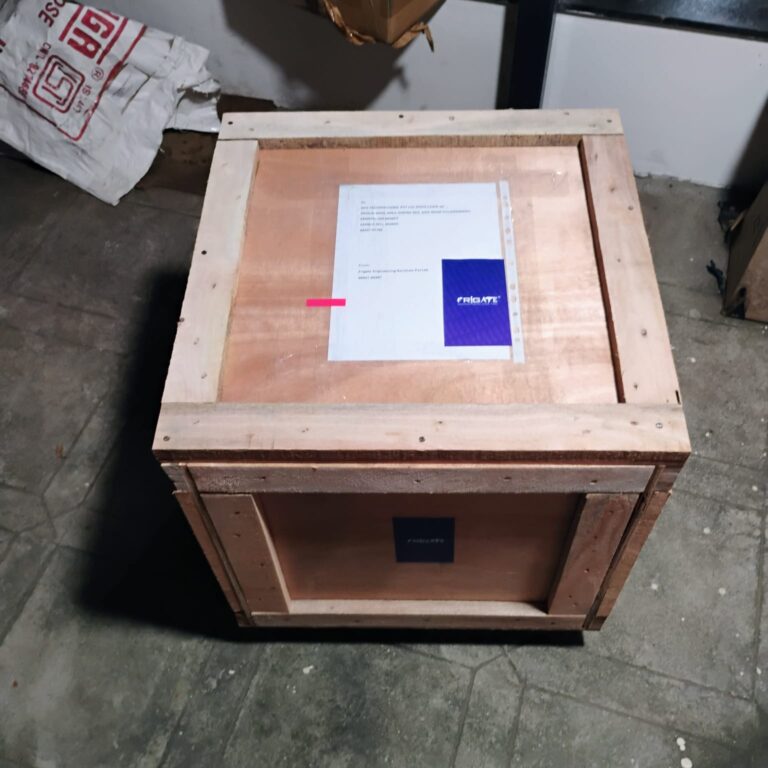
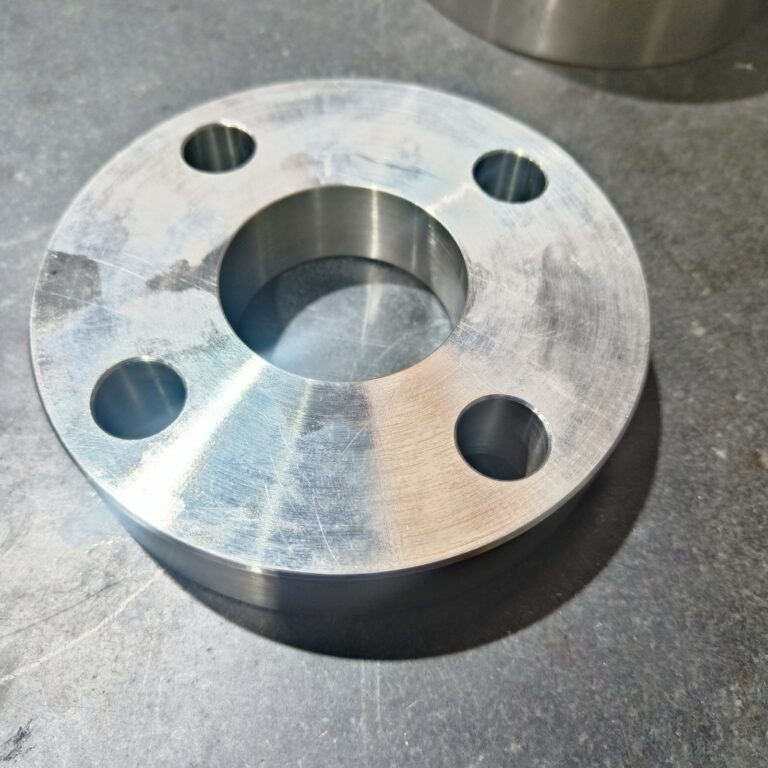
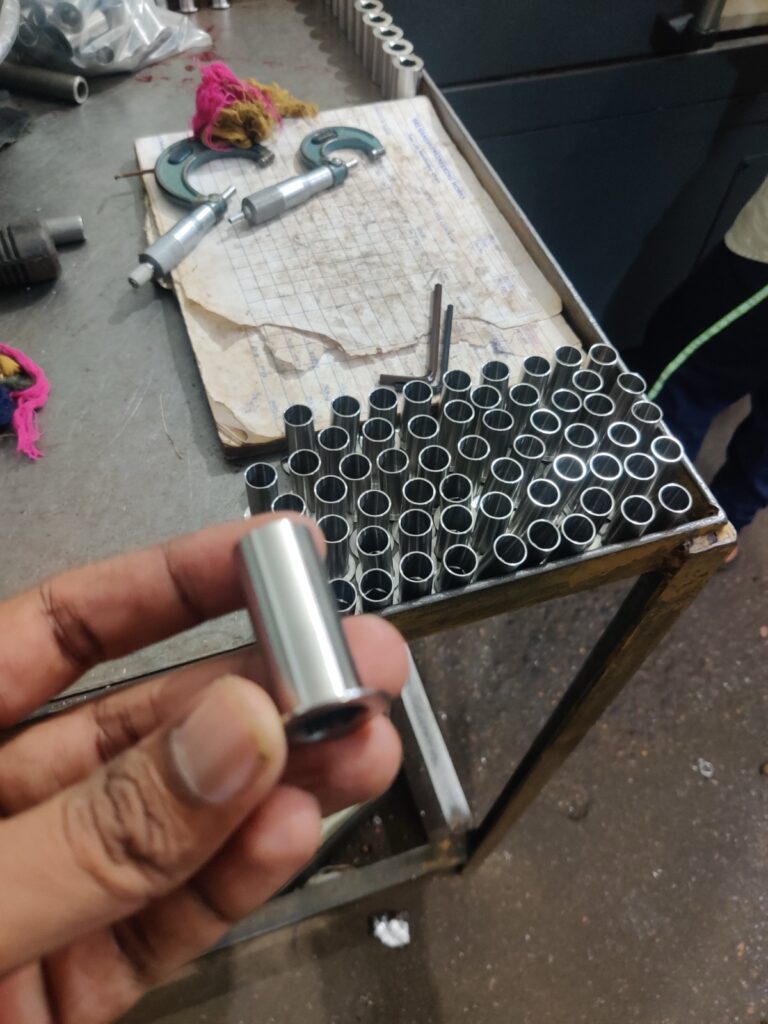
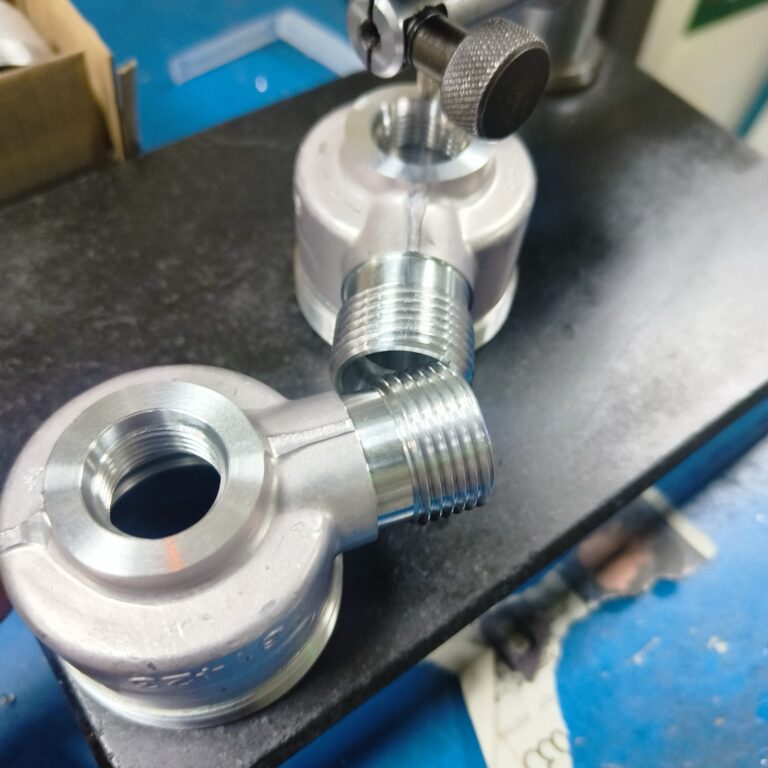
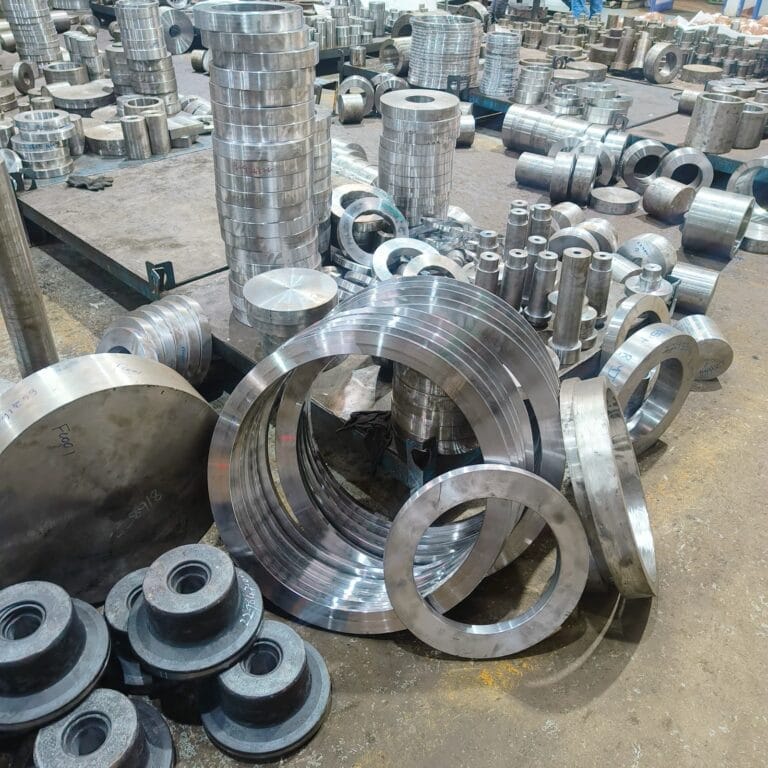
Other Industries We Serve
We deliver machining support across sectors that require consistency, material reliability, and tight dimensional control.
- Solid Progress
Our Manufacturing Metrics
Frigate brings stability, control, and predictable performance to your sourcing operations through a structured multi-vendor system.
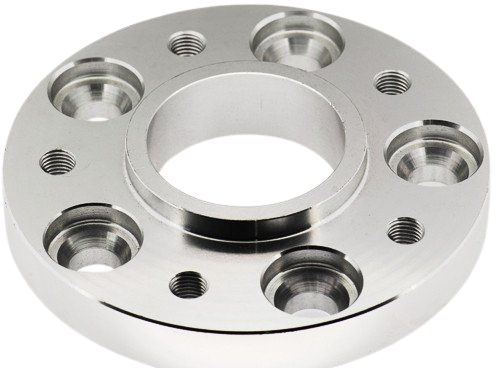
2.8X
Sourcing Cycle Speed
Frigate’s pre-qualified network shortens decision time between RFQ and PO placement.
94%
On-Time Delivery Rate
Structured planning windows and logistics-linked schedules improve project-level delivery reliability.
4X
Multi-Part Consolidation
We enable part family batching across suppliers to reduce fragmentation.
22%
Quality Rejection Rate
Multi-level quality checks and fixed inspection plans lower non-conformities.
30%
Procurement Costs
Optimized supplier negotiations and bulk order strategies reduce your overall sourcing expenses.
20%
Manual Processing Time
Automation of sourcing and supplier management significantly reduces time spent on manual tasks.
Get Clarity with Our Manufacturing Insights
- FAQ
Having Doubts? Our FAQ
Check all our Frequently Asked Questions in CNC Turning
Frigate uses spindle-synchronized probing and tool wear compensation systems to maintain tight tolerance windows during high-RPM turning. Real-time data from machine sensors tracks dimensional shifts caused by thermal drift or cutting pressure. Components such as label applicator spindles and rotating feeder hubs undergo in-cycle gauging and post-process inspection using calibrated pin gauges and roundness testers. This ensures critical motion-transfer parts stay within ±10 micron concentricity, even during long-run production.
We reduce part deformation by combining custom fixturing, back support during turning, and optimized tool entry paths. For items like nozzle collars, guide rings, and film rollers, Frigate adjusts speed-to-feed ratios to control radial pressure without compromising chip flow. Tool holders with minimal overhang and nose radius selection also minimize vibration and bending force. This method allows us to maintain shape consistency across batches, especially for components with wall thickness under 2 mm.
Frigate applies controlled pecking cycles, edge-break tooling, and dual-direction passes to limit burr formation on packaging parts like spouts, sensor brackets, and chute adapters. During finishing, we deploy negative rake inserts or multi-radius cutters to refine edge transitions without secondary operations. For parts requiring sealed or sliding interfaces, we use high-magnification visual inspection and digital profilometers to verify edge break uniformity. These steps ensure clean assembly and prevent premature wear or alignment issues on the shop floor.
Each production lot is assigned a digital process sheet containing raw material certification, tooling usage logs, and operator traceability. Frigate links every turned item such as flow dividers, valve stems, and cap closures to its source billet using heat number mapping and barcode-based part IDs. In addition, all food-contact components follow ISO 22000-aligned documentation that tracks surface finish, coolant type, and contact-free handling steps. This structured approach supports both internal QA protocols and third-party audit readiness.
Frigate uses tool life prediction models and machine-level control loops to manage variation over extended production runs. In-process checks using laser micrometers and contact probes detect drift before it crosses defined tolerance bands. Lathe spindle temperatures and Z-axis drift data feed into real-time offset correction modules. For packaging components like actuator pins and rotary bushings, we also rotate insert edges based on tool wear logs, which keeps tolerance bands tight without frequent re-inspection.
We'd love to Manufacture for you!
Submit the form below and our representative will be in touch shortly.
LOCATIONS
Global Sales Office
818, Preakness lane, Coppell, Texas, USA – 75019
Registered Office
10-A, First Floor, V.V Complex, Prakash Nagar, Thiruverumbur, Trichy-620013, Tamil Nadu, India.
Operations Office
9/1, Poonthottam Nagar, Ramanandha Nagar, Saravanampatti, Coimbatore-641035, Tamil Nadu, India. ㅤ
Other Locations
- Bhilai
- Chennai
- Texas, USA