Packaging Machinery Industry Machining Solutions
Improve Motion Control, Wear Resistance, and Machine Longevity with Frigate’s CNC-Machined Components for Automated Packaging Systems
Frigate offers machined components in packaging systems
Precision Fit for High-Speed Assemblies
Use CNC turning and milling to deliver tight-tolerance components that maintain motion stability in servo-driven and cam-actuated systems.
Wear-Resistant Alloys for Extended Cycles
Select nitrided steels, tool steels, and heat-treated alloys that reduce wear in repetitive contact zones like guide rails and actuator pins.
Machining for Interlocked Designs
Produce mating parts with smooth interfacing surfaces using synchronized 5-axis operations and deburring strategies for precise fit and minimal backlash.
Our Clients
Trusted by Engineers and Purchasing Leaders
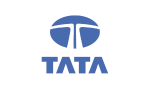
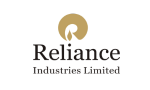


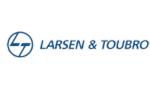
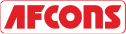


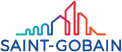

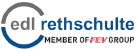

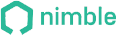
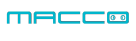









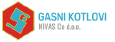
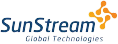

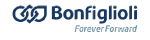


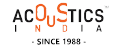
Maintain Dimensional Stability in Multi-Shift Operations
Packaging lines often run continuously, demanding parts that hold tolerance under thermal, load, and motion variations.
Use low-expansion alloys like 17-4 PH and anodized aluminum to manage dimensional shifts during long operating hours.
Apply induction or case hardening to shafts and gears to balance core toughness with wear resistance on working surfaces.
Relieve residual stresses in aluminum and stainless steel frame components to prevent warping during continuous operation and machine cycling.

Meet Compliance Standards in Food and Pharma Lines
Surfaces in contact with product or washdown fluids must meet hygienic design standards and resist contamination or corrosion.
Design and machine rounded, debris-free transitions and chamfered edges that reduce residue accumulation in contact zones.
Utilize FDA- and EU-compliant materials like 316L stainless steel and food-grade polymers in exposed components.
Apply electro-polishing or passivation on contact parts to enhance surface smoothness, reduce microbial risk, and support washdown tolerance.

Enable Repeatable Motion Through Assembly Fit Control
Component fits and bearing seats must align across production lots to ensure repeatability in mechanical assemblies.
Maintain positional tolerance of ±0.01 mm in shafts, collars, and gear seats using CMM-based inspection routines.
Machine housings and motion components in matched sets to avoid mismatch and reduce assembly variability.
Use turning centers with live tooling to achieve low runout and concentricity in rotating elements like rollers and pulleys.

Our Machined Products
We support your production needs with CNC-machined parts, subassemblies, and performance-critical components.
- Real Impact
Words from Clients
See how global OEMs and sourcing heads describe their experience with our scalable execution.
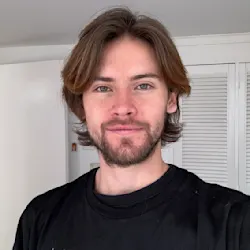
“Quick turnaround and solid quality.”
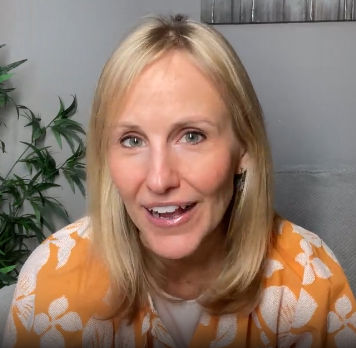
“The instant quote tool saved us time, and the parts were spot-on. Highly recommend Frigate!”
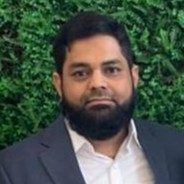
“I would strongly recommend Frigate to anyone who wants to do Rapid Prototyping, and take their ideas to manufacturing. One firm doing all kinds of Product Development!”
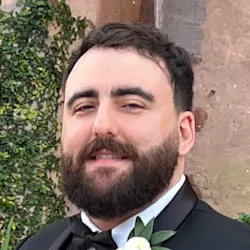
“Great service, fair price, and the parts worked perfectly in our assembly.”
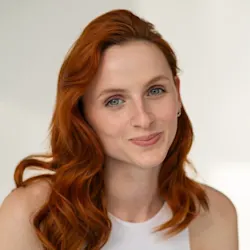
“Top-notch machining and fast shipping. Very satisfied with the results.”
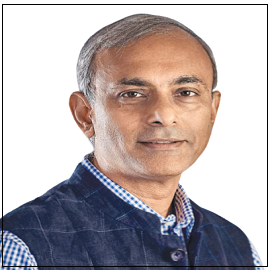
“The next disruption is happening in Prototyping & Manufacturing on-demand and Frigate is leading the way! I personally believe the Frigate's way of IIOT enabled cloud platform with Al.”
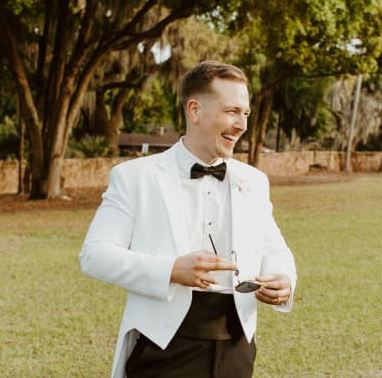
“Frigate delivered high-quality parts at a competitive price. The instant quote tool is a huge plus for us!”

“We appreciate the precision and quality of the machined components in the recent delivery—they meet our specifications perfectly and demonstrate Frigate’s capability for excellent workmanship.”
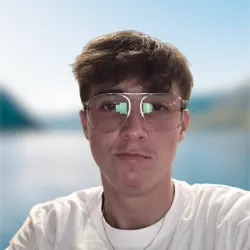
“Flawless execution from quote to delivery.”

“I am absolutely happy to work with supplier like Frigate who were quite proactive & result oriented . Frigate has high willingness team who has strong know how & their passion towards the products & process were absolutely thrilling.”
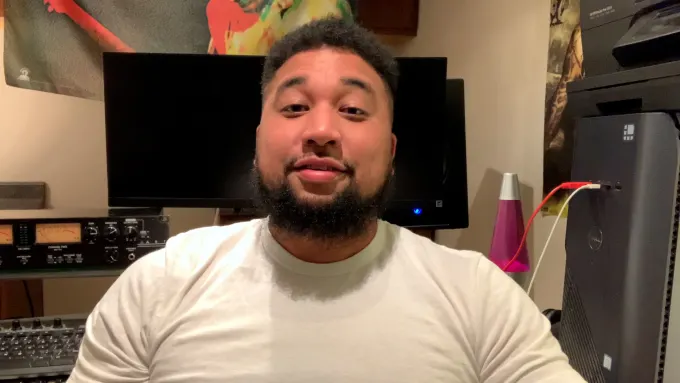
“The precision on these parts is impressive, and they arrived ahead of schedule. Frigate’s process really stands out!”
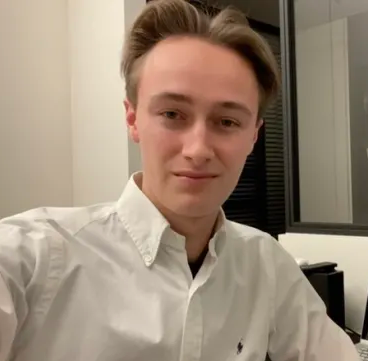
“Parts were exactly as spec’d, and the instant quote made budgeting a breeze.”
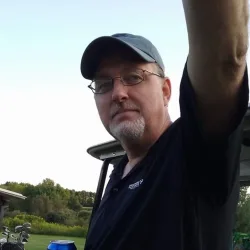
“Good value for the money.”
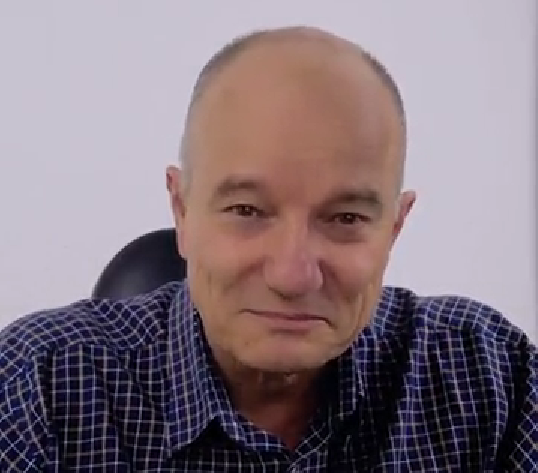
“The finish was perfect, and the team was easy to work with.”

“Working with Frigate has been great. Their proactive, results-driven approach and expertise shine through in every project. It's been a pleasure collaborating with them.”

"We are highly satisfied with the timely delivery and quality of the MIG Welding Cable from Frigate. Their attention to detail, secure packaging, and quick responsiveness stood out. We confidently recommend Frigate Engineering Services Pvt. Ltd. as a reliable manufacturing partner."
- We export to 12+ countries
Frigate’s Global Presence
Frigate takes pride in facilitating “Make in India for the globe“. As our global network of Frigaters provides virtually limitless capacity, and through our IoT enabled platform your parts go directly into production. By digitally and technologically enabling “the silent pillars of the economy” MSME and SME manufacturing industries, we are able to tap the huge potential for manufacturing to bring the best results for our clients.

100,000+
Parts Manufactured
250+
Frigaters
2000+
Machines
450+
Materials
25+
Manufacturing Process
- Solid Progress
How You Benefit with Us
Frigate brings stability, control, and predictable performance to your sourcing operations through a structured multi-vendor system.
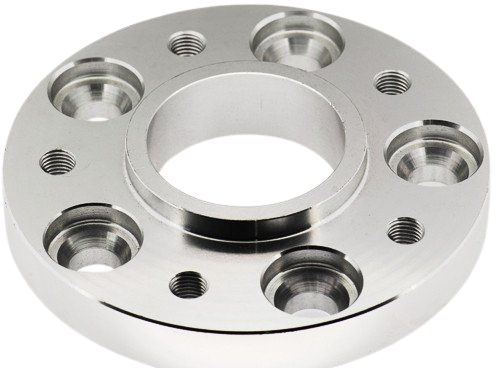
2.8X
Sourcing Cycle Speed
Frigate’s pre-qualified network shortens decision time between RFQ and PO placement.
94%
On-Time Delivery Rate
Structured planning windows and logistics-linked schedules improve project-level delivery reliability.
4X
Multi-Part Consolidation
We enable part family batching across suppliers to reduce fragmentation.
22%
Quality Rejection Rate
Multi-level quality checks and fixed inspection plans lower non-conformities.
30%
Procurement Costs
Optimized supplier negotiations and bulk order strategies reduce your overall sourcing expenses.
20%
Manual Processing Time
Automation of sourcing and supplier management significantly reduces time spent on manual tasks.
Other Industries We Serve
We deliver machining support across sectors that require consistency, material reliability, and tight dimensional control.
Get Clarity with Our Manufacturing Insights
Frigate uses concentricity-focused turning processes combined with high-resolution CMM verification to hold shaft alignment within ±0.01 mm. During multi-part machining, matched fixturing blocks are employed to retain coaxiality between shaft ends, collars, and mounting flanges. Real-time spindle load monitoring also helps detect deflection during deep cuts or live tooling operations. This process ensures smooth transmission in servo-driven or belt-driven packaging assemblies with minimal angular misalignment.
Frigate applies coatings like TiN and DLC using PVD or plasma-assisted deposition to improve wear resistance in moving guides and sealing faces. Machined components first undergo ultrasonic cleaning and deburring to enhance coating adhesion. Critical surfaces are then measured post-coating to ensure Ra remains under 0.2 µm where low-friction contact is needed. This results in longer service cycles for sliders, plungers, and cam-driven parts in continuous operation.
Yes. Frigate machines modular frame components using palletized fixturing and in-process probing to control dimensional drift across large batches. Positional tolerances are validated per frame zone using CNC-mounted probes and optical scanners. Fixtures are designed to compensate for residual stress in aluminum profiles, especially after rough milling. This enables consistent fit and assembly without manual adjustments, even across large machine footprints or split-lane systems.
Frigate selects 316L stainless steel and anodized aluminum to withstand caustic washdowns in food and pharma-grade packaging systems. All machined surfaces are passivated or treated with FDA-approved coatings to limit corrosion at contact edges and fastener points. Threads, ports, and cavities are also smoothed to remove debris-trapping zones. This protects mechanical parts in CIP or SIP environments where chemical compatibility is critical.
Frigate uses laser-based measurement systems and contact-based bore gauges to inspect motion-critical features like linear guideways, bearing seats, and coupling shafts. Machine learning models analyze tool wear and automatically trigger in-process checks at defined intervals. Data is logged per part and flagged if variation exceeds 5 µm from the baseline. This layered verification process supports sustained part quality during continuous production without manual recalibration.
We'd love to Manufacture for you!
Submit the form below and our representative will be in touch shortly.
LOCATIONS
Global Sales Office
818, Preakness lane, Coppell, Texas, USA – 75019
Registered Office
10-A, First Floor, V.V Complex, Prakash Nagar, Thiruverumbur, Trichy-620013, Tamil Nadu, India.
Operations Office
9/1, Poonthottam Nagar, Ramanandha Nagar, Saravanampatti, Coimbatore-641035, Tamil Nadu, India. ㅤ
Other Locations
- Bhilai
- Chennai
- Texas, USA