CNC Milling Services for Firearms & Defense Accessories
Frigate supplies high-precision milled components tailored for firearms and defense assemblies. Our milling solutions ensure dimensional stability, structural fit, and production reliability at every scale.
Our Clients





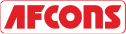

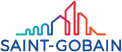


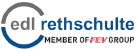

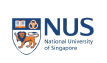
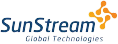

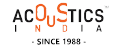




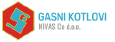
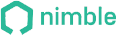
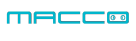












- Operational Performance
Benefits of Our CNC Milling Services
Our in-house operations apply calibrated spindle mapping, vibration-dampened fixturing, and high-pressure coolant systems to maintain accuracy during high-speed milling.
Contour-Fit Milling for Receivers
Adaptive 4-axis operations deliver smooth internal transitions across forged receiver blanks, supporting improved bolt carrier alignment.
Barrel Extension Profiling
Our setups maintain bore concentricity below 0.01 mm, enabling repeatable alignment for barrel extensions under chambered stress.
Serration & Grip Surface Milling
Custom grip surface milling on hardened stock enhances tactile control without compromising part integrity under operational loads.
- Manufacturing Discipline
Our CNC Milling Process
Each stage of our process integrates controlled feed simulation, axis recalibration, and validation runs support performance in recoil-bearing assemblies.

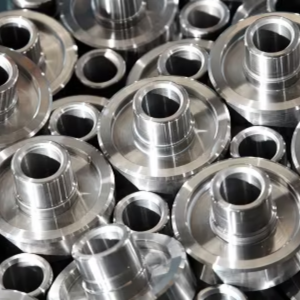

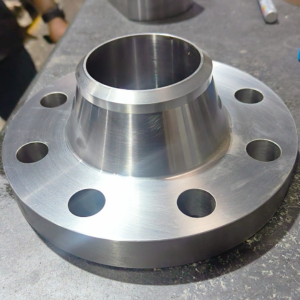

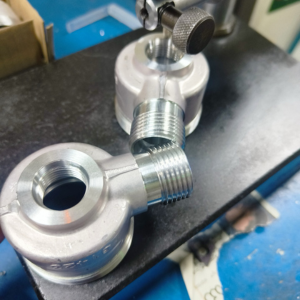
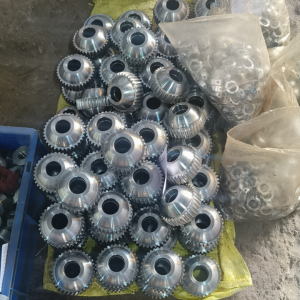
Engineers design the part using CAD (Computer-Aided Design) software. The design includes all dimensions and specifications.
The CAD design is converted into CNC code, often using CAM (Computer-Aided Manufacturing) software. This code tells the milling machine how to move and cut the material.
Operators prepare the CNC milling machine by securing the material (workpiece) and installing the appropriate cutting tools.
The CNC machine reads the code and starts milling. The cutting tool rotates and moves along multiple axes to remove material from the workpiece and shape it into the desired part.
The machine monitors the cutting operations throughout the process. Operators may make adjustments to ensure precision and quality.
After milling, the part may undergo additional processes like deburring or polishing to achieve the final specifications.
The finished part is thoroughly inspected to meet all design requirements and tolerances.
- Real Impact
Words from Clients
See how global OEMs and sourcing heads describe their experience with our scalable execution.
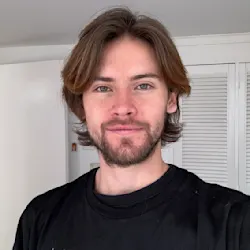
“Quick turnaround and solid quality.”
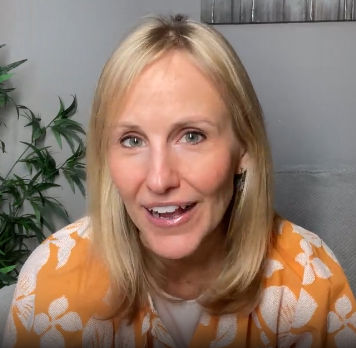
“The instant quote tool saved us time, and the parts were spot-on. Highly recommend Frigate!”
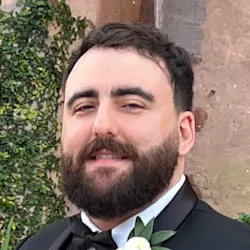
“Great service, fair price, and the parts worked perfectly in our assembly.”
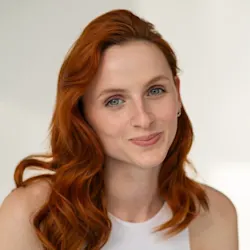
“Top-notch machining and fast shipping. Very satisfied with the results.”
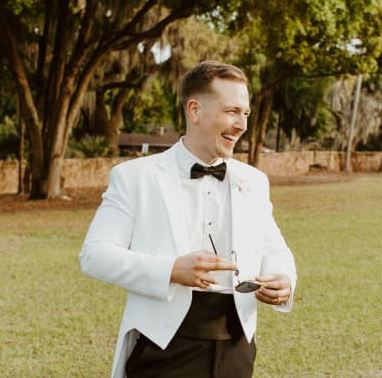
“Frigate delivered high-quality parts at a competitive price. The instant quote tool is a huge plus for us!”

“We appreciate the precision and quality of the machined components in the recent delivery—they meet our specifications perfectly and demonstrate Frigate’s capability for excellent workmanship.”
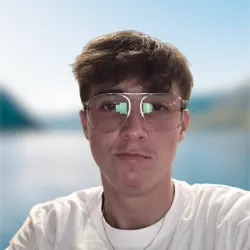
“Flawless execution from quote to delivery.”
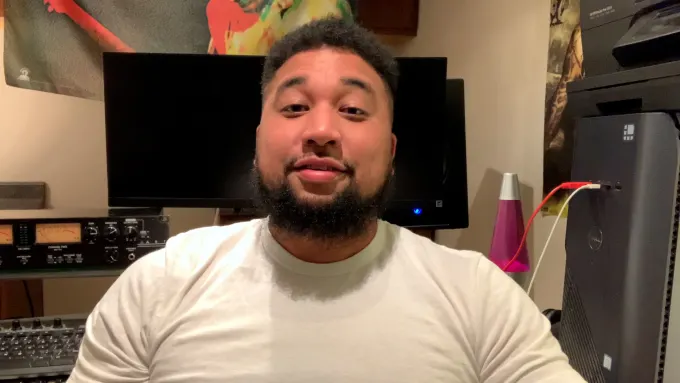
“The precision on these parts is impressive, and they arrived ahead of schedule. Frigate’s process really stands out!”
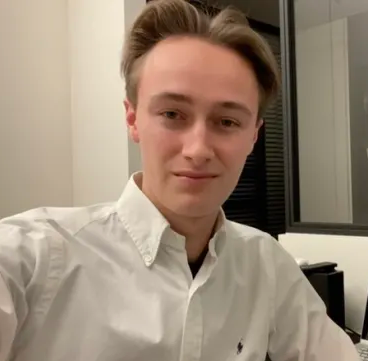
“Parts were exactly as spec’d, and the instant quote made budgeting a breeze.”
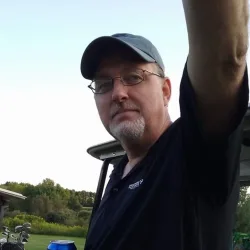
“Good value for the money.”
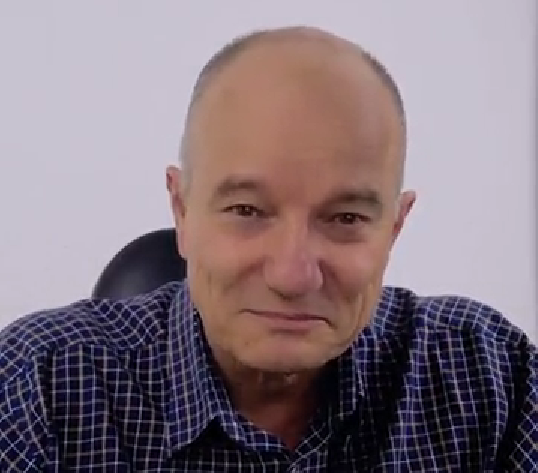
“The finish was perfect, and the team was easy to work with.”
- Tolerances That Withstand
Surface Finishing for Milled Metal Parts
Every machined part undergoes passivation, grain structure review, and surface roughness tests to meet sliding, locking, and thermal transition tolerances.
Anodizing
Give your aluminum parts a tough, corrosion-resistant shield with anodizing, reaching surface hardness up to HV 500, while enhancing electrical insulation and durability.
Mechanical Finishing
Smooth out imperfections and refine surfaces to Ra 0.2 µm or better with mechanical finishing techniques like grinding, polishing, and bead blasting.
Heat Treatment
Boost material strength and hardness by heat treating parts at temperatures up to 1100°C, ensuring they meet the mechanical demands of your application.
Electroplating
Add protective or functional metal coatings with electroplating, delivering consistent layers as precise as ±2 µm for improved corrosion resistance and conductivity.
Our Machined Products
We support your production needs with CNC-machined parts, subassemblies, and performance-critical components.
- Built for Mission-Fit
CNC Milling Materials
We use firearm-grade metal alloys engineered for fatigue resistance, strength-to-weight ratio, and dimensional consistency under field use. These materials support consistent cycling, firing, and impact scenarios.
- Tensile yield over 850 MPa supports critical lower receiver bodies under repeated live-fire.
- Expansion coefficient under 13 µm/m°C avoids misfit in heat-treated suppressor mounts.
- Brinell hardness of 240+ ensures wear resistance in slide rails and locking blocks.
A2 Tool Steel is a high-carbon, high-chromium steel known for its toughness and wear resistance. It’s ideal for producing durable, high-strength parts that can withstand heavy use.
Aluminum is a lightweight, corrosion-resistant metal with good machinability. Because of its strength-to-weight ratio, it’s commonly used in aerospace, automotive, and various industrial applications.
Brass is a copper-zinc alloy known for its machinability and corrosion resistance. It’s used for components requiring precise detailing and good mechanical properties.
Bronze is a copper-tin alloy with excellent wear resistance and strength. It’s often used for bushings, bearings, and other friction-prone components.
Cast Iron is known for its high wear resistance and machinability. It’s used in heavy-duty applications such as machinery parts and engine components.
Copper offers excellent thermal and electrical conductivity. It’s used in applications requiring heat dissipation or electrical conductivity, such as electronic components.
Steel is a versatile material known for its strength and durability. It’s used in various applications, from construction to automotive parts.
Titanium is a lightweight, high-strength metal with excellent corrosion resistance. It’s used in aerospace, medical implants, and high-performance engineering applications.
Stainless Steel offers high corrosion resistance and strength. It’s widely used in applications ranging from kitchen equipment to industrial machinery.
Zinc is a ductile and corrosion-resistant metal known for its excellent machinability, especially in its alloy forms. It's often used for components requiring intricate details, good surface finish, and precise dimensions, commonly found in automotive, hardware, and electrical applications.
- Assembly-Grade Compatibility
Performance Metrics
Our workflows ensure you receive structurally stable, toleranced parts that integrate directly into high-performance tactical systems. We tune every aspect of the milling profile for durability and dimensional trust.
- Maintains profile flatness within 0.01 mm across optic mount interfaces.
- Supports monolithic rail sections exceeding 1,000 mm with no thermal distortion.
- Enables frame cutouts with ±0.005 mm accuracy for tight trigger module housing.
- Produces magazine catch pockets without secondary grinding or manual correction.
- Delivers low-variation slot widths across slide assemblies for smoother cycling.
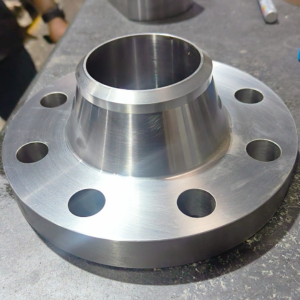
- Aligned with Field Standards
Compliance in CNC Milling for Firearms
Frigate’s CNC milling operations strictly comply with applicable defense, firearm, and export standards. Our workflows align with U.S. DoD sourcing requirements and global firearm quality benchmarks. We maintain traceability, inspection records, and machining logs to support full production verification.
- Follows ITAR and U.S. DoD manufacturing protocols for serialized parts.
- Maintains lot-level documentation for steel and aluminum billet traceability.
- Verifies tolerance compliance through calibrated CMM inspections.
Supports audited quality management systems across all firearm milling workflows.
Aligns our operations with aerospace-level tolerancing suitable for firearm-grade components.
Guarantees all materials used meet restricted substance guidelines.
Supports parts integration into NATO-compliant firearm subsystems.
Covers controlled processes related to heat-treated and coated components.
Used for cross-compatibility with vehicle-mounted defense gear.
Validates component integrity for field-deployed electronics within firearms accessories.
- We export to 12+ countries
Frigate’s Global Presence
Frigate takes pride in facilitating “Make in India for the globe“. As our global network of Frigaters provides virtually limitless capacity, and through our IoT enabled platform your parts go directly into production. By digitally and technologically enabling “the silent pillars of the economy” MSME and SME manufacturing industries, we are able to tap the huge potential for manufacturing to bring the best results for our clients.

100,000+
Parts Manufactured
250+
Frigaters
2000+
Machines
450+
Materials
25+
Manufacturing Process

- Machining Practices
Quality Testing Standards for CNC Milling Services
To measure the roundness of cylindrical features, ensuring they meet tolerance requirements.
To check internal surfaces for flatness, critical for sealing and assembly purposes.
To identify burrs or sharp edges that may affect assembly or safety.
To ensure that complex profiles (e.g., contours, curves) conform to design specifications.
To check the topography and texture of the surface, ensuring it meets the required specifications for function or aesthetics.
To verify that the surface hardness depth meets the required specifications for wear resistance.
To measure internal stresses that could lead to deformation or failure during or after machining.
To verify grain structure, inclusions, and material consistency, ensuring the part meets performance requirements.
- Built to Perform
CNC Milled Components
We ensure micron-level precision by employing ultra-rigid ball screws paired with real-time thermal compensation and backlash elimination. Browse our examples of milled components built to withstand temperature cycles, and repeated mechanical stress.
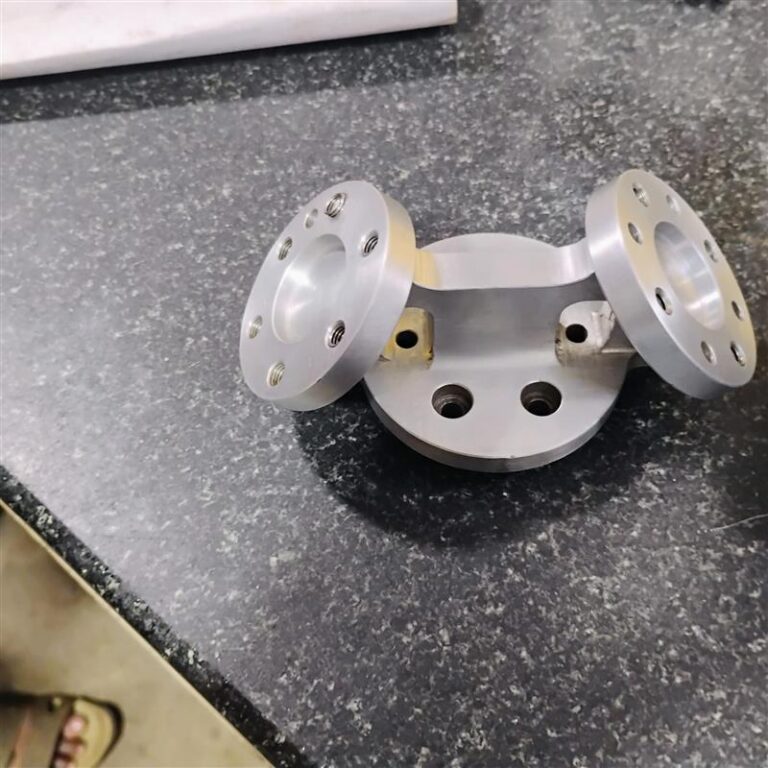
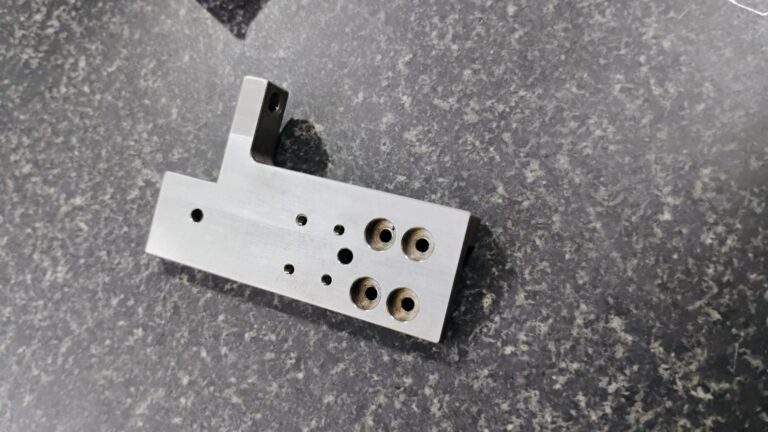
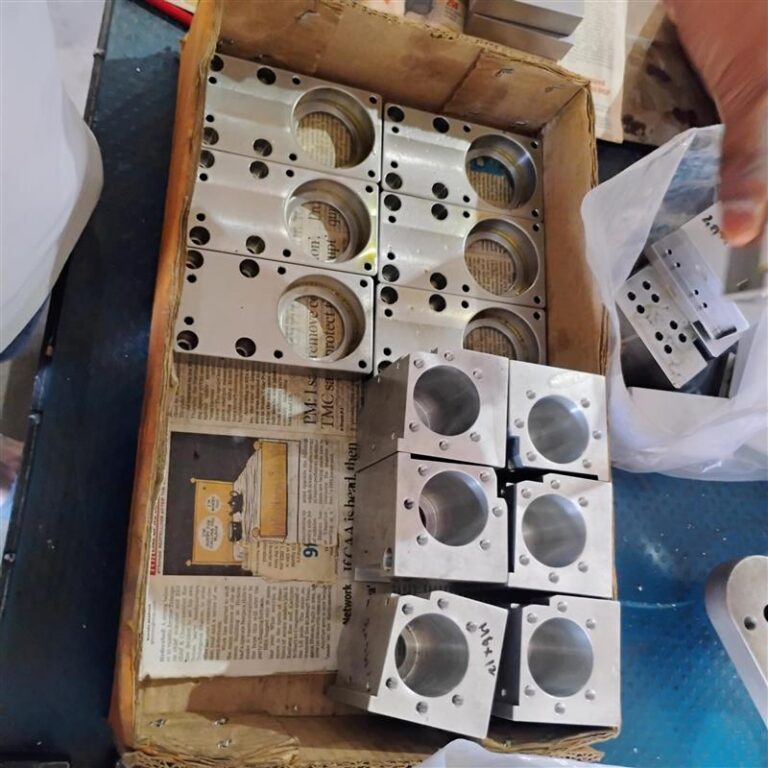
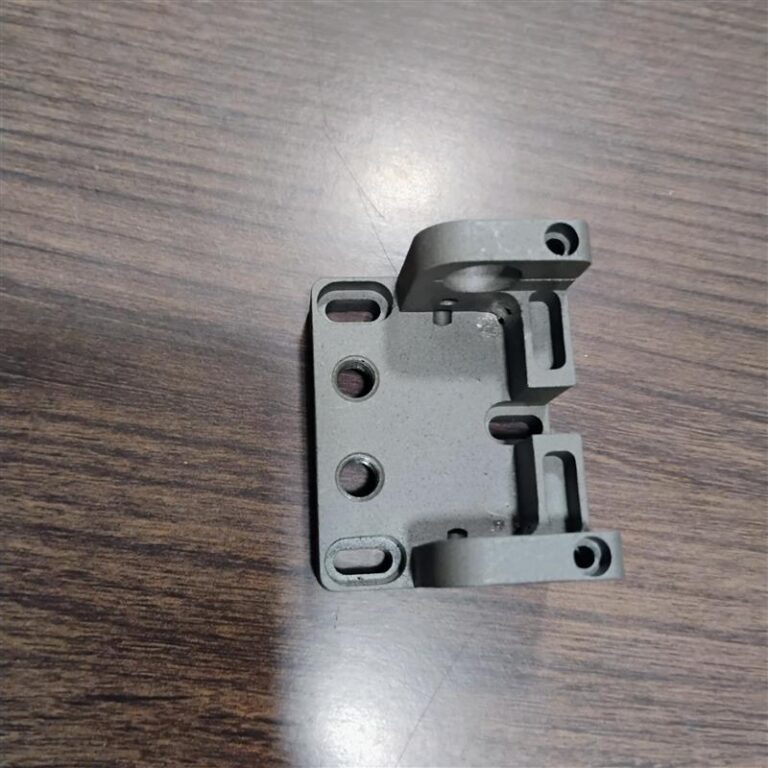
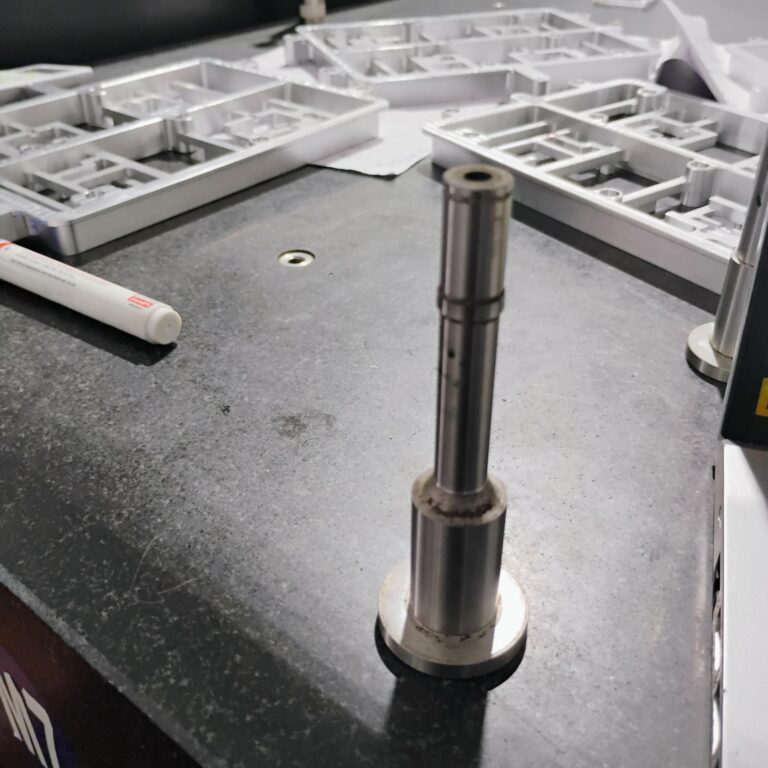
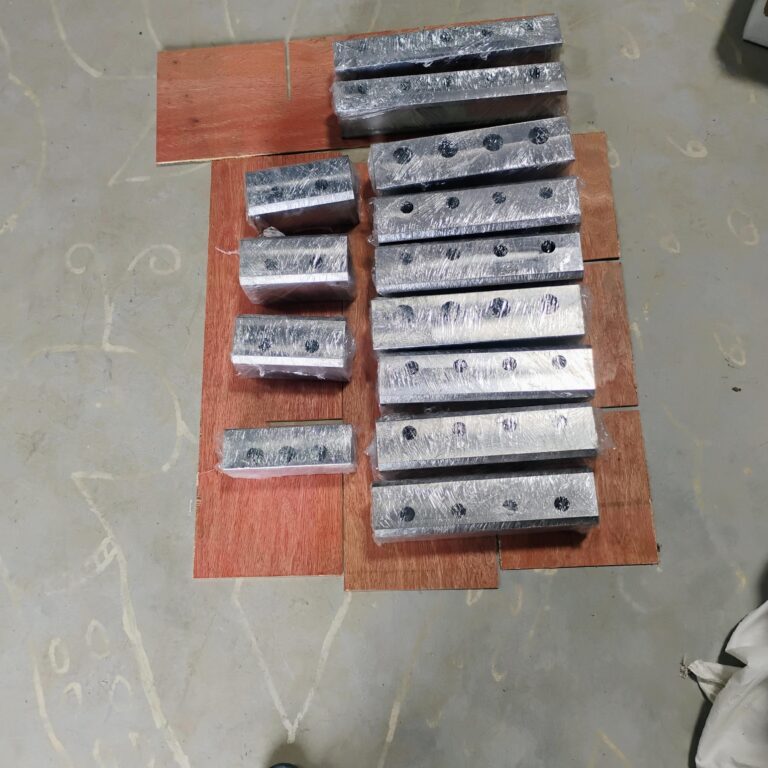
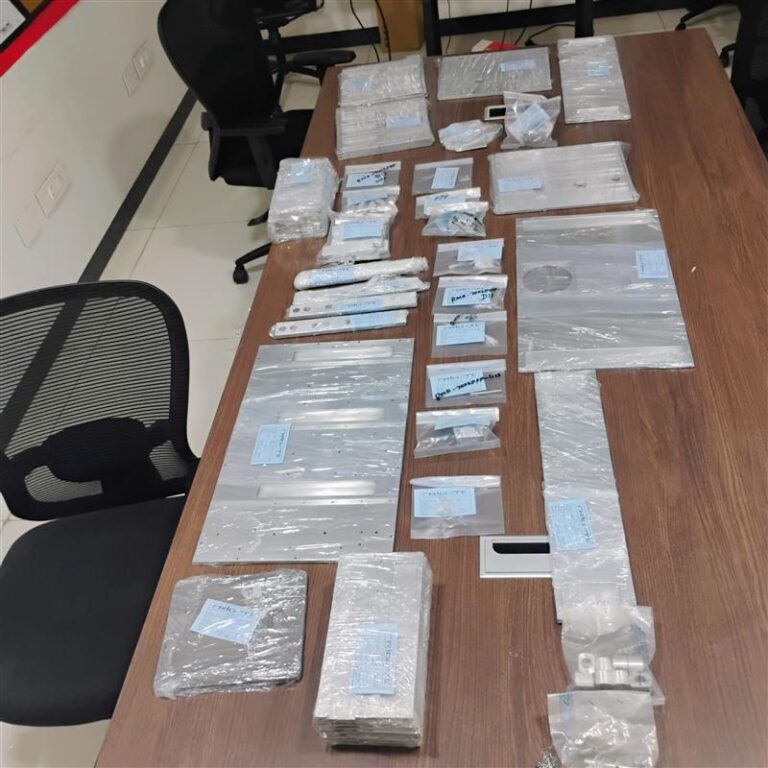

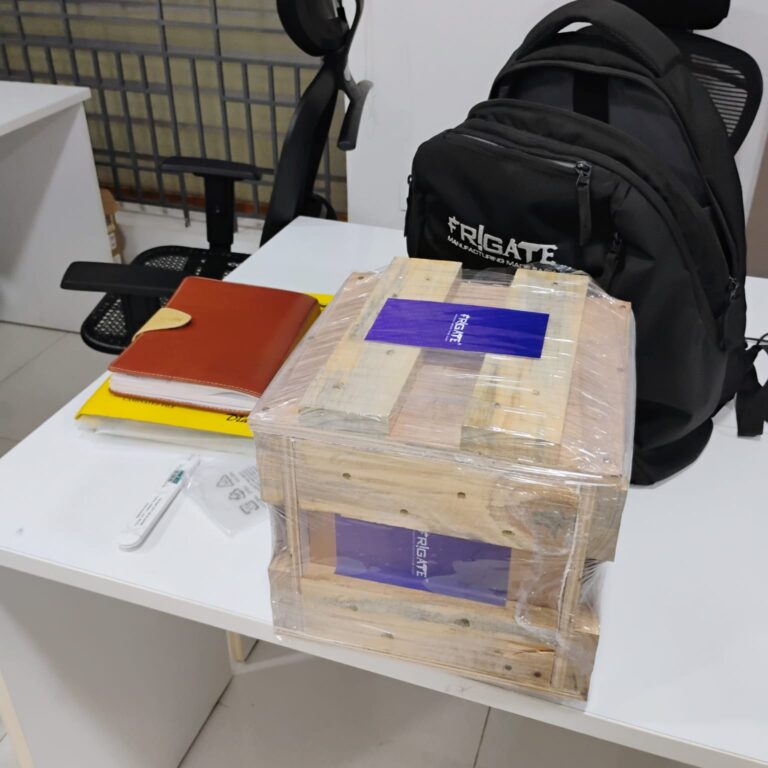


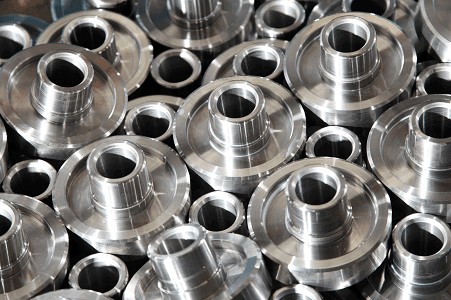
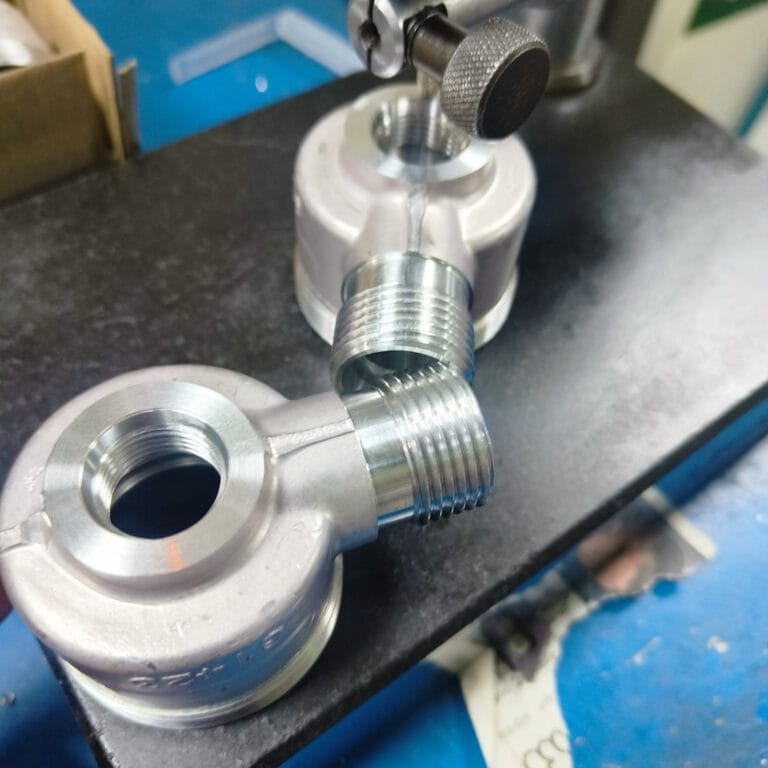
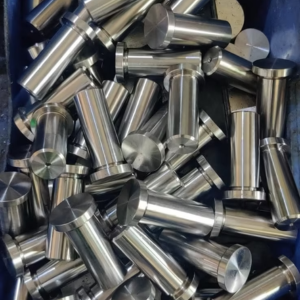
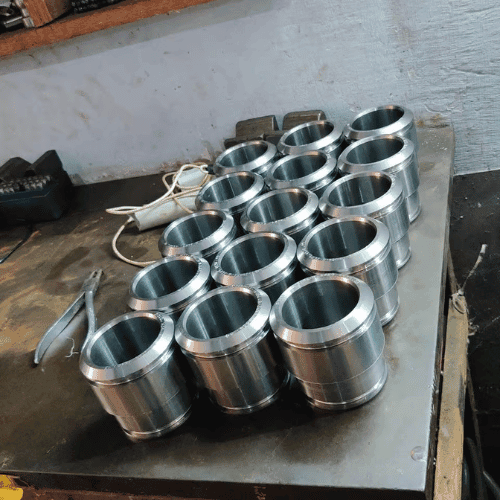
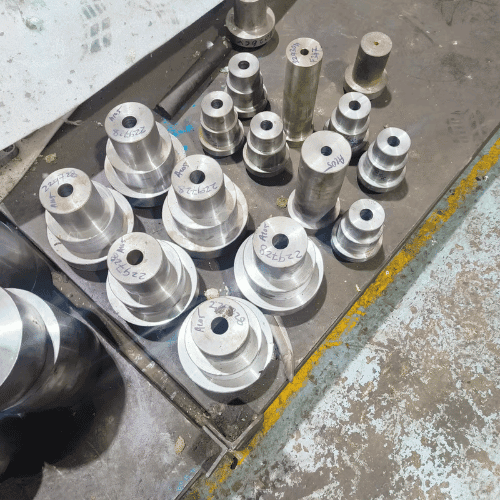
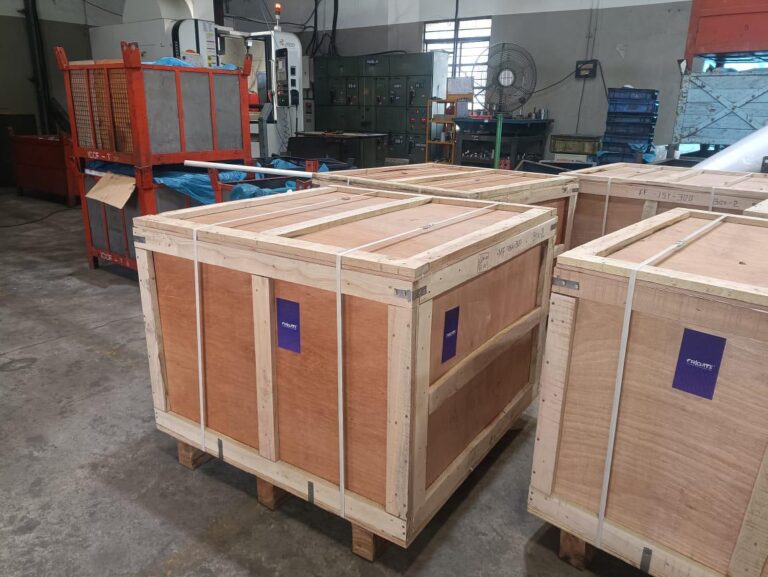
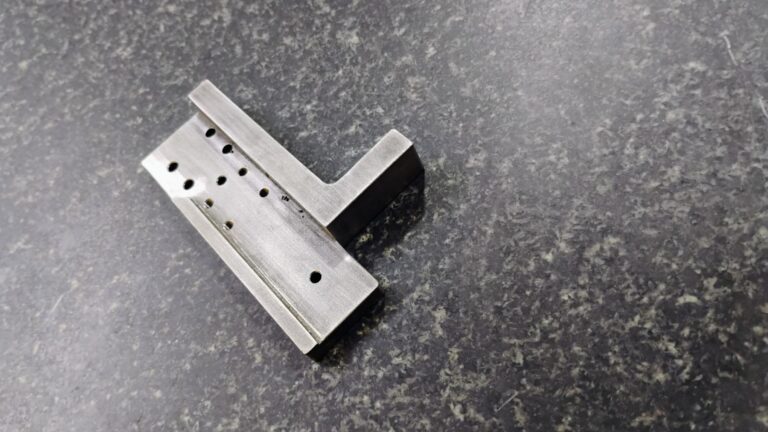
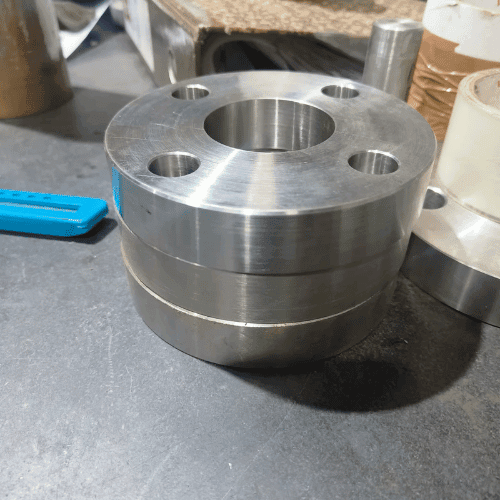
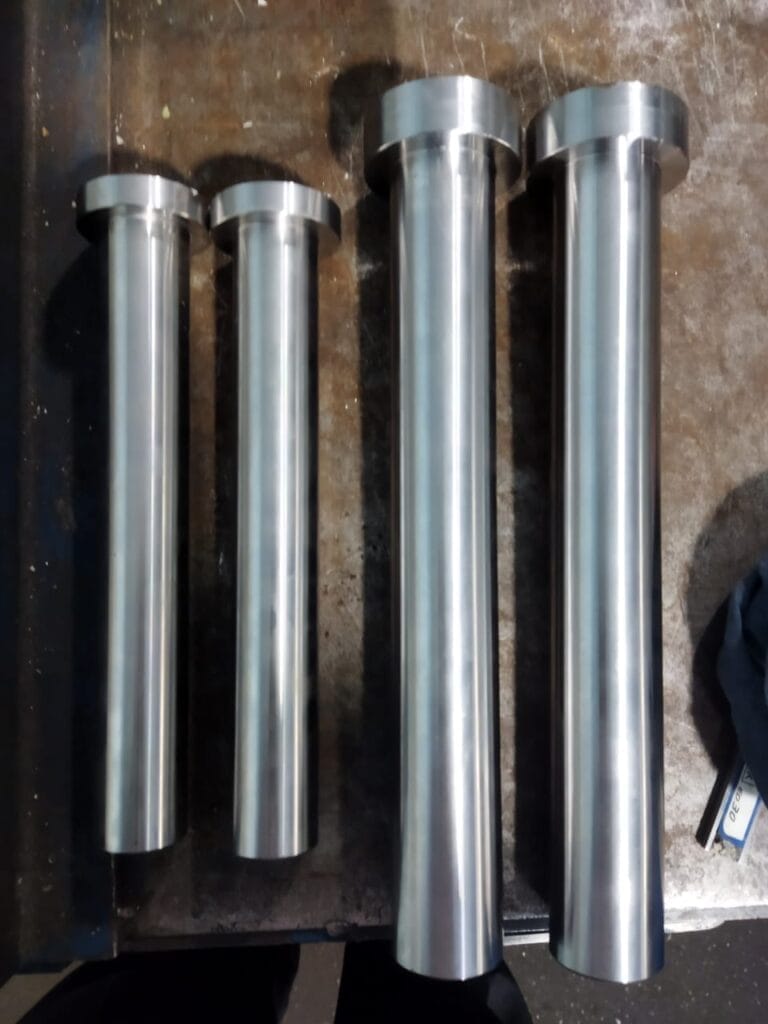

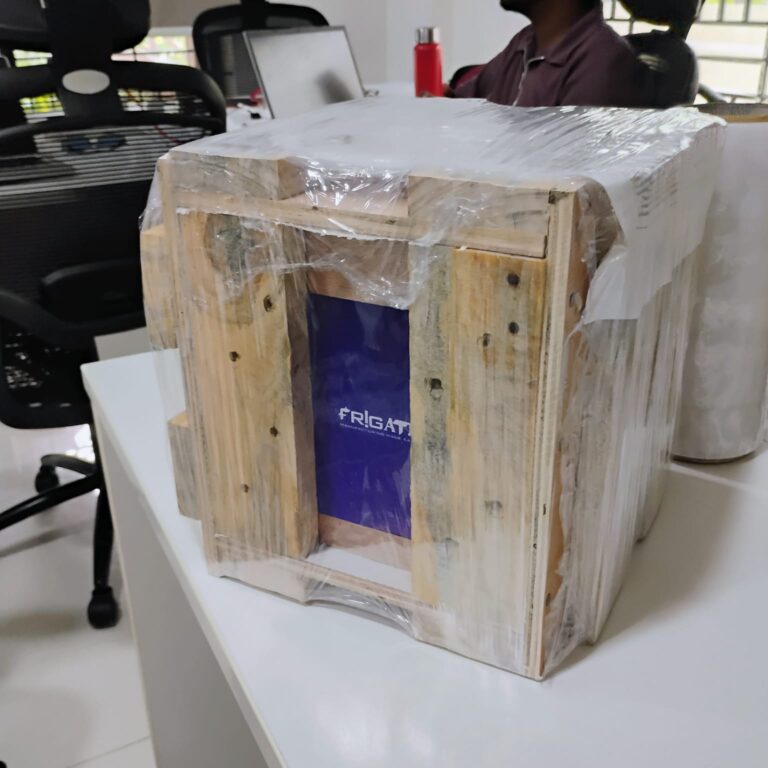

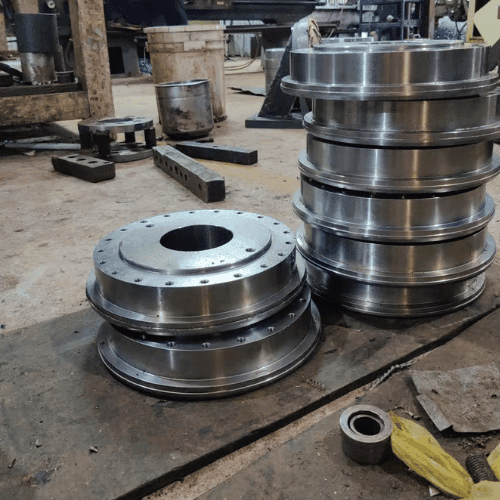
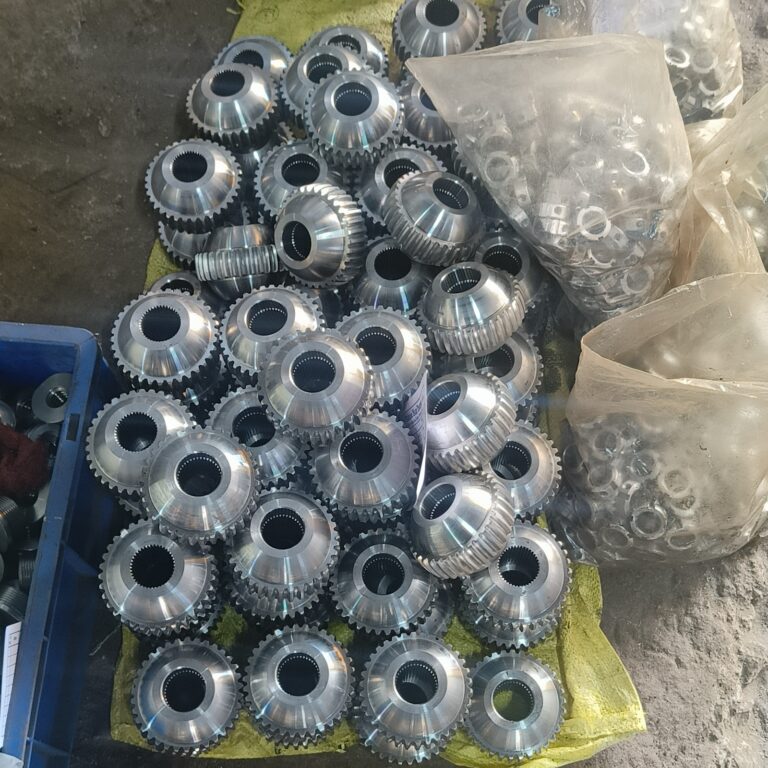
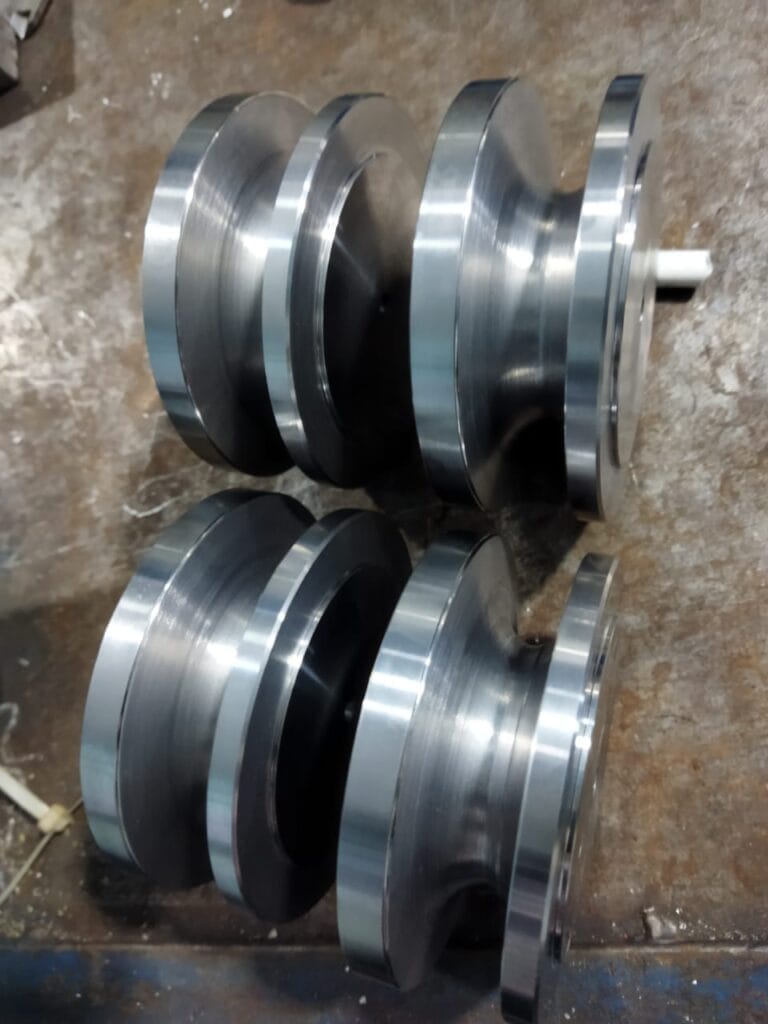
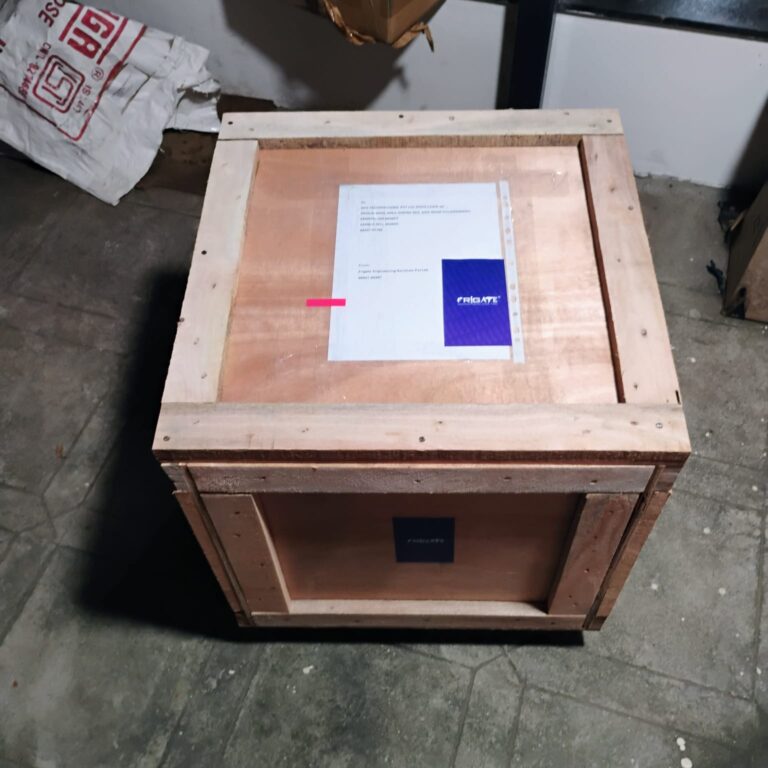
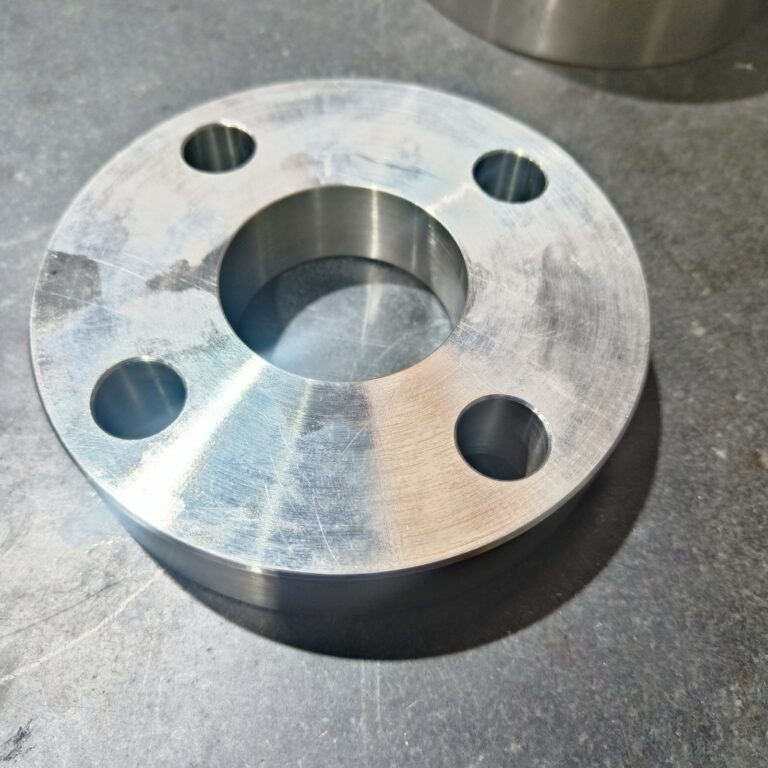
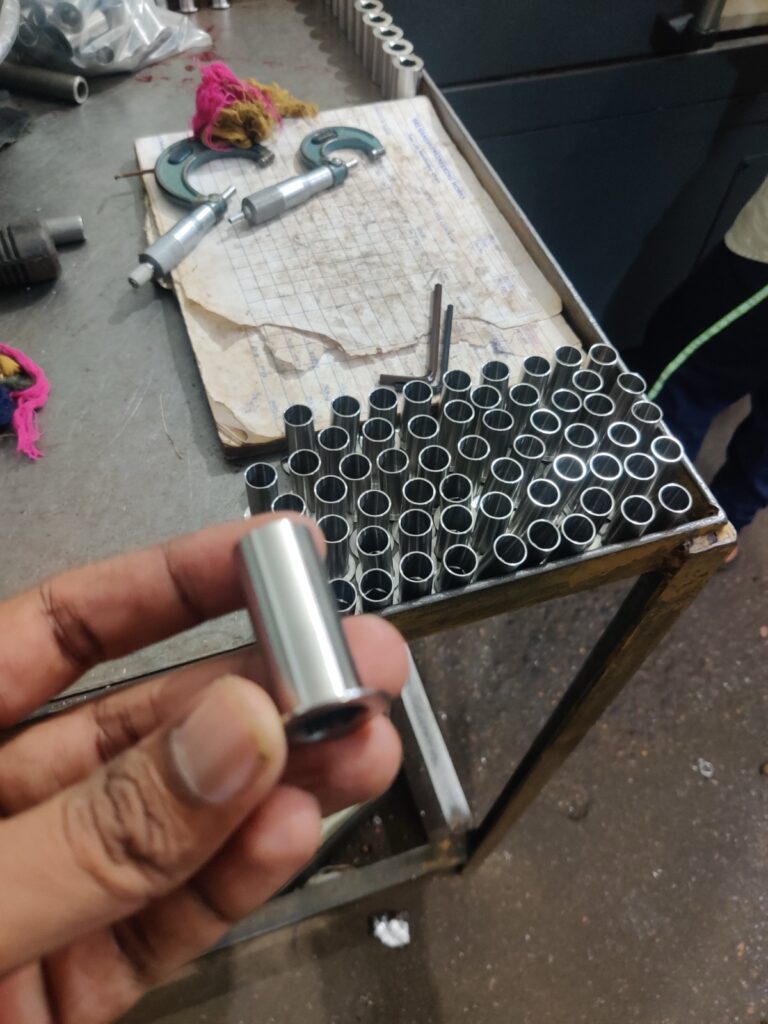
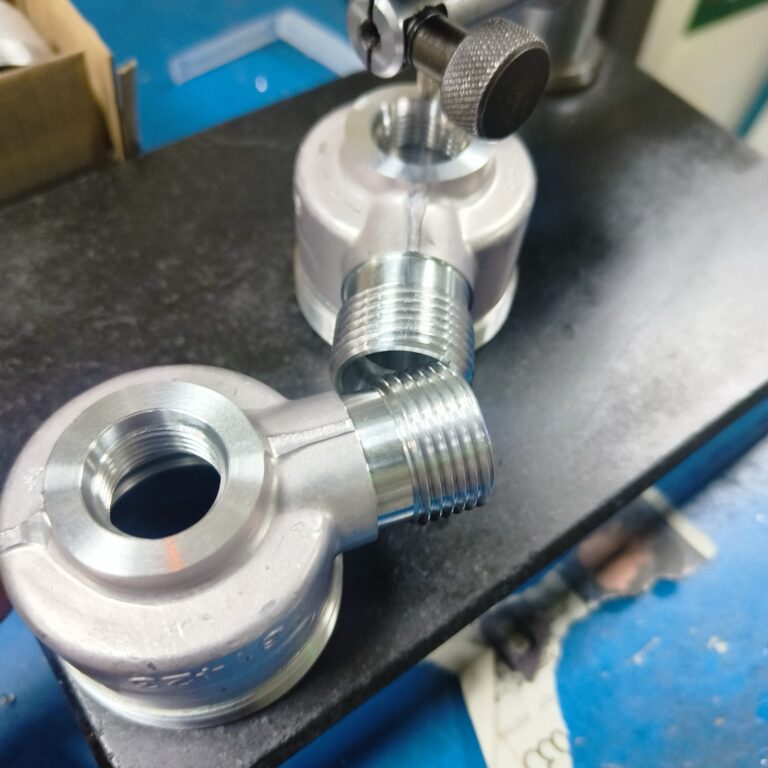
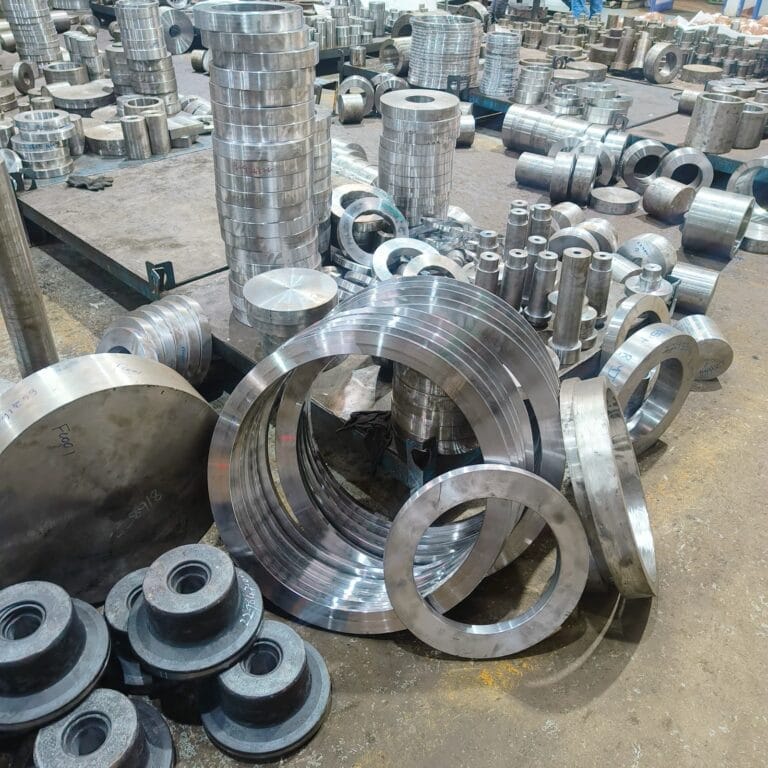
Other Industries We Serve
We deliver machining support across sectors that require consistency, material reliability, and tight dimensional control.
- Solid Progress
Our Manufacturing Metrics
Frigate brings stability, control, and predictable performance to your sourcing operations through a structured multi-vendor system.
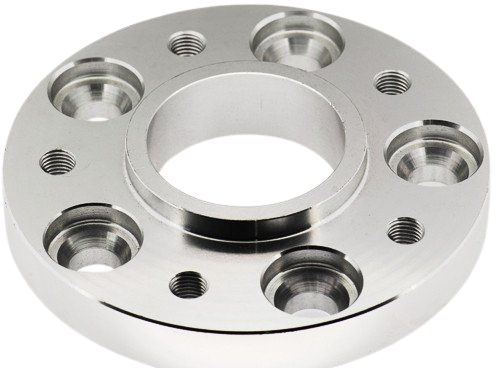
2.8X
Sourcing Cycle Speed
Frigate’s pre-qualified network shortens decision time between RFQ and PO placement.
94%
On-Time Delivery Rate
Structured planning windows and logistics-linked schedules improve project-level delivery reliability.
4X
Multi-Part Consolidation
We enable part family batching across suppliers to reduce fragmentation.
22%
Quality Rejection Rate
Multi-level quality checks and fixed inspection plans lower non-conformities.
30%
Procurement Costs
Optimized supplier negotiations and bulk order strategies reduce your overall sourcing expenses.
20%
Manual Processing Time
Automation of sourcing and supplier management significantly reduces time spent on manual tasks.
Get Clarity with Our Manufacturing Insights
- FAQ
Having Doubts? Our FAQ
Check all our Frequently Asked Questions in CNC Milling
Frigate uses synchronized dual-axis milling heads with temperature-regulated spindle enclosures to minimize thermal expansion over long barrel lengths. Adaptive toolpath correction compensates for real-time Z-axis deviation detected by linear encoders. Tool pressure is distributed using variable entry angles to prevent taper shift in deep cuts. Final parts are scanned with coordinate measuring machines to confirm receiver straightness and consistent bore alignment.
Frigate applies 4-axis contour milling with indexed fixture rotation to retain perpendicularity across all planes of the slide frame. Dynamic work offsets are calibrated during each tool change using reference-edge probing. Coolant delivery is modulated by axis position to reduce local heat buildup and part warping. Final inspection includes comparative CMM checks to validate squareness against GD&T reference frames.
Frigate tunes spindle speeds through harmonic testing and phase matching with cutting tool geometry to reduce chatter. Feed rates are progressively adjusted based on wall thickness to control load spikes during tool exit. Multi-point fixturing adds structural support in open sections without distorting surface access. Toolpaths are verified through dry-run simulations and vibration feedback monitoring.
Yes, Frigate applies radial step-down milling with low-engagement tools to reduce force impact in internal pockets. Tool coatings are selected to prevent friction-induced surface hardening in titanium. High-pressure through-spindle coolant removes chips rapidly, maintaining surface quality throughout cavity transitions. Final parts are tested using fluorescent penetrant inspection to confirm absence of subsurface cracking.
Frigate uses modular vacuum fixtures and mechanical stops to hold multiple rail blanks in identical orientation. Spindle alignment is laser-verified before each production cycle to maintain datum consistency. Tool deflection is modeled in CAM to pre-compensate radial shift during cavity replication. Final outputs are batch-verified with optical comparators and traceable to dimensional records per customer specification.
We'd love to Manufacture for you!
Submit the form below and our representative will be in touch shortly.
LOCATIONS
Registered Office
10-A, First Floor, V.V Complex, Prakash Nagar, Thiruverumbur, Trichy-620013, Tamil Nadu, India.
Operations Office
9/1, Poonthottam Nagar, Ramanandha Nagar, Saravanampatti, Coimbatore-641035, Tamil Nadu, India. ㅤ
Other Locations
- Bhilai
- Chennai
- USA
- Germany