CNC Turning Services for Aerospace & Defense
Frigate’s CNC turning centers utilize closed-loop feedback systems integrated with high-resolution encoders and thermal sensors to continuously monitor and adjust tool positioning in real time. This advanced compensation system effectively mitigates machining errors arising from thermal expansion, spindle runout, and mechanical backlash
Our Clients





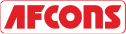

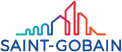


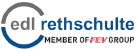

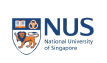
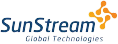

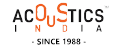




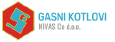
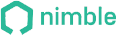
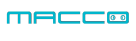












- Chip Control Strategies
Sub-Micron CNC Turning for Aerospace and Defense
Frigate integrates thermal compensation, multi-axis machining, and real-time process analytics to deliver complex aerospace components with full traceability and compliance to AS9100 and NADCAP standards.
Machining Protocols for Aerospace Alloys
Frigate applies cryogenic cooling, high-pressure coolant systems, and optimized feeds to machine superalloys, preventing thermal distortion and microstructural damage while preserving mechanical properties and tool integrity.
Multi-Axis CNC for Complex Profiles
Frigate’s multi-axis turning systems enable synchronized contouring and threading, reducing setups while maintaining geometric accuracy. Kinematic calibration and collision control ensure repeatability in tight-tolerance aerospace geometries.
Quality Control and Process Traceability
Frigate integrates in-line metrology and SPC to monitor machining parameters. Digitally logged data ensures traceability, early deviation detection, and compliance with AS9100 and NADCAP requirements.
- Precision Machining Workflow
Our CNC Turning Process
We use closed-loop control, thermal compensation, and multi-axis tooling to achieve sub-micron accuracy with full traceability and stable, validated processes.


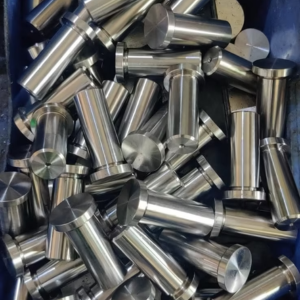
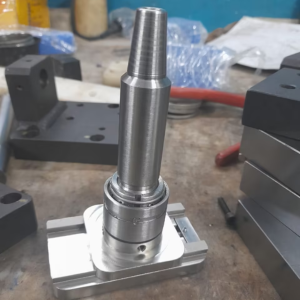
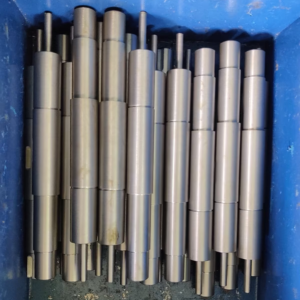

Our team designs the part in CAD software with focus on radial symmetry and tool clearance.
CAM software generates toolpaths based on spindle speeds, feed rates, and material hardness.
Operators load the raw bar stock and calibrate live tooling attachments, ensuring optimal alignment.
The part spins while stationary or live tools shape it via precision radial and axial cuts. Also, Our machines track spindle load and thermal drift in real time.
We perform part-off, facing, and secondary polishing before moving to the inspection stage.
Every part undergoes inspection using CMMs and profile projectors to verify dimensional and geometrical tolerances.
- Real Impact
Words from Clients
See how global OEMs and sourcing heads describe their experience with our scalable execution.
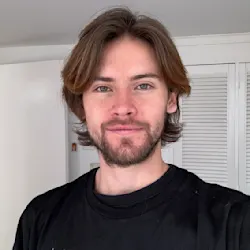
“Quick turnaround and solid quality.”
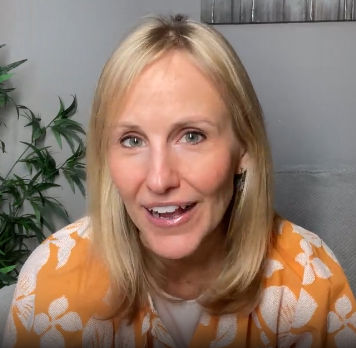
“The instant quote tool saved us time, and the parts were spot-on. Highly recommend Frigate!”
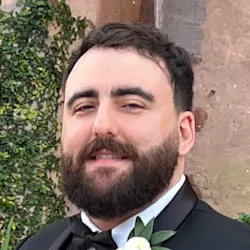
“Great service, fair price, and the parts worked perfectly in our assembly.”
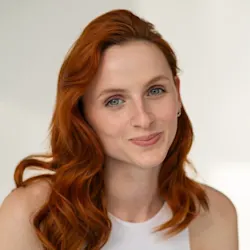
“Top-notch machining and fast shipping. Very satisfied with the results.”
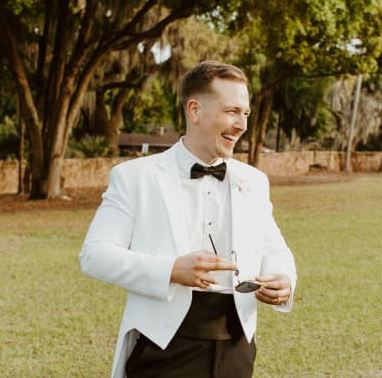
“Frigate delivered high-quality parts at a competitive price. The instant quote tool is a huge plus for us!”

“We appreciate the precision and quality of the machined components in the recent delivery—they meet our specifications perfectly and demonstrate Frigate’s capability for excellent workmanship.”
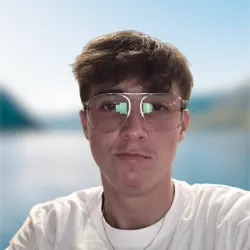
“Flawless execution from quote to delivery.”
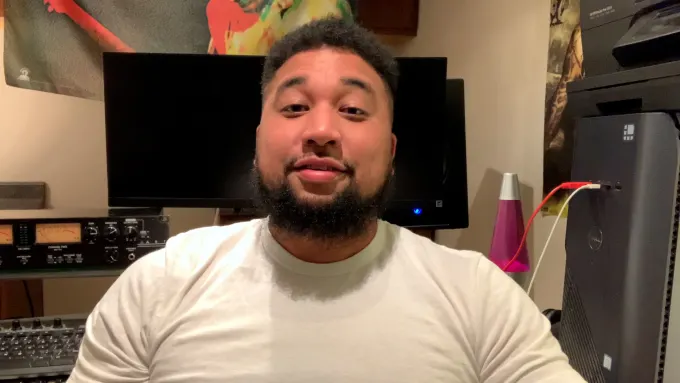
“The precision on these parts is impressive, and they arrived ahead of schedule. Frigate’s process really stands out!”
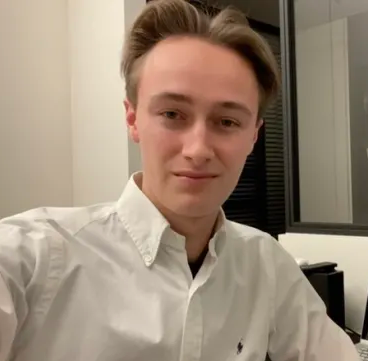
“Parts were exactly as spec’d, and the instant quote made budgeting a breeze.”
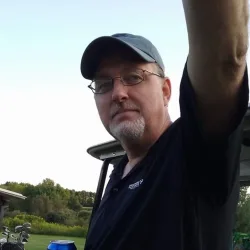
“Good value for the money.”
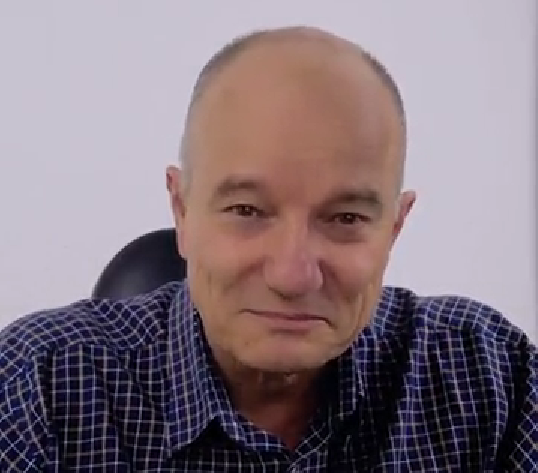
“The finish was perfect, and the team was easy to work with.”
- Consistent Finishes
Flawless Finishes for CNC Turned Parts
We apply post-turning surface refinement techniques to enhance finish quality on CNC-turned parts. Controlled deburring and fine feed strategies ensure smooth surfaces and consistent edge conditions for aerospace applications.
Anodizing
Give your aluminum parts a tough, corrosion-resistant shield with anodizing, reaching surface hardness up to HV 500, while enhancing electrical insulation and durability.
Mechanical Finishing
Smooth out imperfections and refine surfaces to Ra 0.2 µm or better with mechanical finishing techniques like grinding, polishing, and bead blasting.
Heat Treatment
Boost material strength and hardness by heat treating parts at temperatures up to 1100°C, ensuring they meet the mechanical demands of your application.
Electroplating
Add protective or functional metal coatings with electroplating, delivering consistent layers as precise as ±2 µm for improved corrosion resistance and conductivity.
Our Machined Products
We support your production needs with CNC-machined parts, subassemblies, and performance-critical components.
- Material Options
CNC Turning Materials for Aerospace and Defense
We machine aerospace-grade materials including titanium, Inconel, stainless steels, and aluminum alloys selected for thermal stability, strength-to-weight ratio, and fatigue resistance. Each material undergoes qualification based on structural performance and tolerance control in high-load environments.
- Access full material certifications with mechanical and chemical property validation.
- Receive RFQs based on mill lot traceability and aerospace batch conformance.
- Synchronize deliveries with assembly schedules and compliance checkpoints.
A2 Tool Steel is a high-carbon, high-chromium steel known for its toughness and wear resistance. It’s ideal for producing durable, high-strength parts that can withstand heavy use.
Aluminum is a lightweight, corrosion-resistant metal with good machinability. Because of its strength-to-weight ratio, it’s commonly used in aerospace, automotive, and various industrial applications.
Brass is a copper-zinc alloy known for its machinability and corrosion resistance. It’s used for components requiring precise detailing and good mechanical properties.
Bronze is a copper-tin alloy with excellent wear resistance and strength. It’s often used for bushings, bearings, and other friction-prone components.
Cast Iron is known for its high wear resistance and machinability. It’s used in heavy-duty applications such as machinery parts and engine components.
Copper offers excellent thermal and electrical conductivity. It’s used in applications requiring heat dissipation or electrical conductivity, such as electronic components.
Steel is a versatile material known for its strength and durability. It’s used in various applications, from construction to automotive parts.
Titanium is a lightweight, high-strength metal with excellent corrosion resistance. It’s used in aerospace, medical implants, and high-performance engineering applications.
Stainless Steel offers high corrosion resistance and strength. It’s widely used in applications ranging from kitchen equipment to industrial machinery.
Zinc is a ductile and corrosion-resistant metal known for its excellent machinability, especially in its alloy forms. It's often used for components requiring intricate details, good surface finish, and precise dimensions, commonly found in automotive, hardware, and electrical applications.
- Consistency in Execution
Key Highlights
Process control is maintained from CAM programming through final inspection, minimizing variability in aerospace CNC turning workflows.
- Real-time spindle load monitoring ensures stable cutting forces and dimensional uniformity
- Preventive tooling maintenance schedules reduce unplanned downtime in critical production runs
- Adaptive cycle strategies accommodate both low- and high-volume aerospace batch requirements
- Comprehensive dimensional and surface integrity inspection data provided with every delivery
- Controlled process adjustments enable precise re-machining for tight-tolerance component revisions
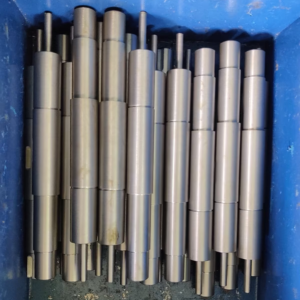
- Industry Standard Compliance
Compliance for CNC Turning Services
CNC turning operations adhere strictly to aerospace quality management frameworks, including AS9100 and NADCAP standards, ensuring rigorous process control and traceability. Inline inspection data and controlled parameter adjustments are systematically recorded to support defect prevention and process validation. Complete compliance documentation is maintained for all aerospace component manufacturing.
- Aerospace-grade documentation with full traceability
- Process validation based on PFMEA and control plans
- Comprehensive part history with revision and configuration management
Our CNC turning operations follow ISO 9001:2015 standards, supporting quality assurance through structured process control and documentation systems.
We are registered under ITAR, allowing us to manufacture and handle turned components involving restricted U.S. defense technical data.
We use DFARS-compliant metals to meet defense procurement regulations, ensuring traceability and approved country-of-origin materials for turned components.
We coordinate with NADCAP-certified providers for special processes like coatings and heat treatment applied to precision-turned aerospace components.
We follow MIL-SPEC standards for critical turning tolerances, part geometry, and surface finish required in defense-grade components.
We implement FOD prevention procedures during CNC turning, reducing contamination risk and preserving functional integrity of aerospace components.
We align with CMMC Level 2 cybersecurity protocols, securing digital CNC turning files and sensitive defense-related manufacturing data.
- We export to 12+ countries
Frigate’s Global Presence
Frigate takes pride in facilitating “Make in India for the globe“. As our global network of Frigaters provides virtually limitless capacity, and through our IoT enabled platform your parts go directly into production. By digitally and technologically enabling “the silent pillars of the economy” MSME and SME manufacturing industries, we are able to tap the huge potential for manufacturing to bring the best results for our clients.

100,000+
Parts Manufactured
250+
Frigaters
2000+
Machines
450+
Materials
25+
Manufacturing Process

- Inspection Assurance
Quality Testing Standards for CNC Turning Services
To measure the roundness of cylindrical features, ensuring they meet tolerance requirements.
To check internal surfaces for flatness, critical for sealing and assembly purposes.
To identify burrs or sharp edges that may affect assembly or safety.
To ensure that complex profiles (e.g., contours, curves) conform to design specifications.
To check the topography and texture of the surface, ensuring it meets the required specifications for function or aesthetics.
To verify that the surface hardness depth meets the required specifications for wear resistance.
To measure internal stresses that could lead to deformation or failure during or after machining.
To verify grain structure, inclusions, and material consistency, ensuring the part meets performance requirements.
- Precision in Every Profile
CNC Turned Parts
We maintain stringent dimensional consistency through high-resolution spindle encoders, thermal drift compensation, and ultra-fine servo motor tuning. Delivering components engineered to withstand extreme mechanical stresses and fluctuating thermal environments.
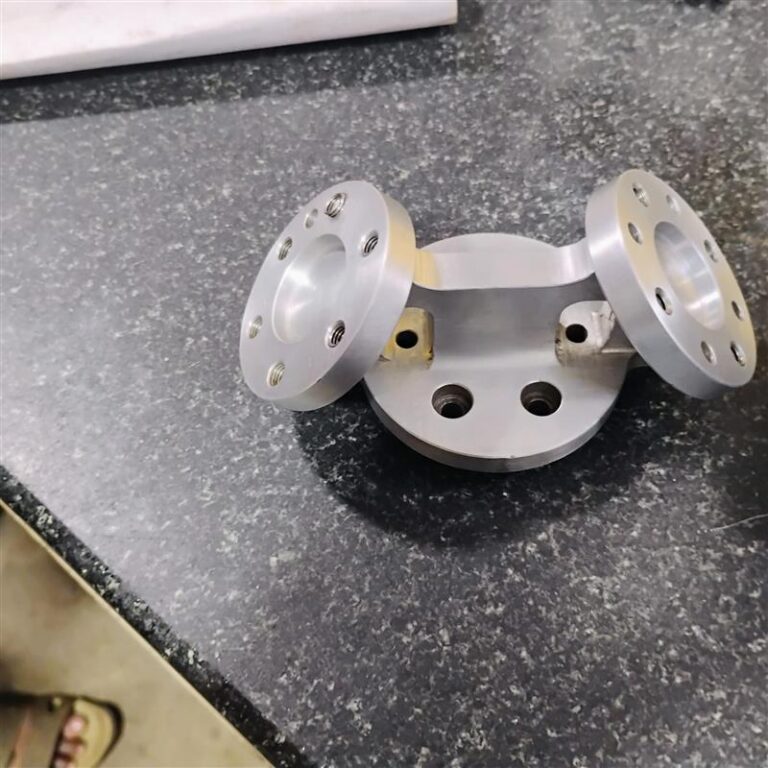
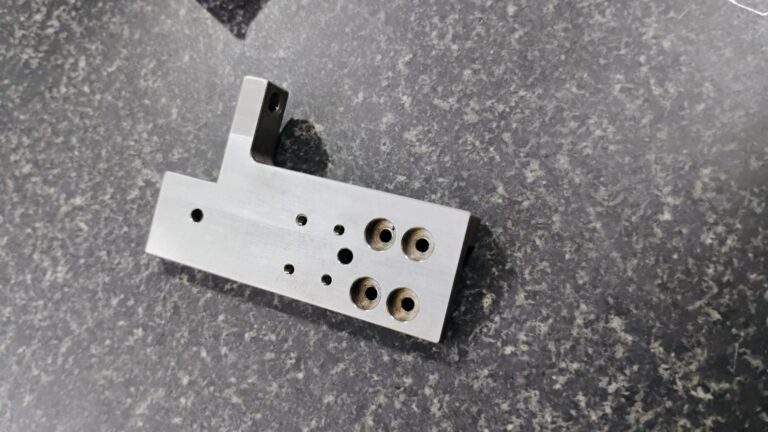
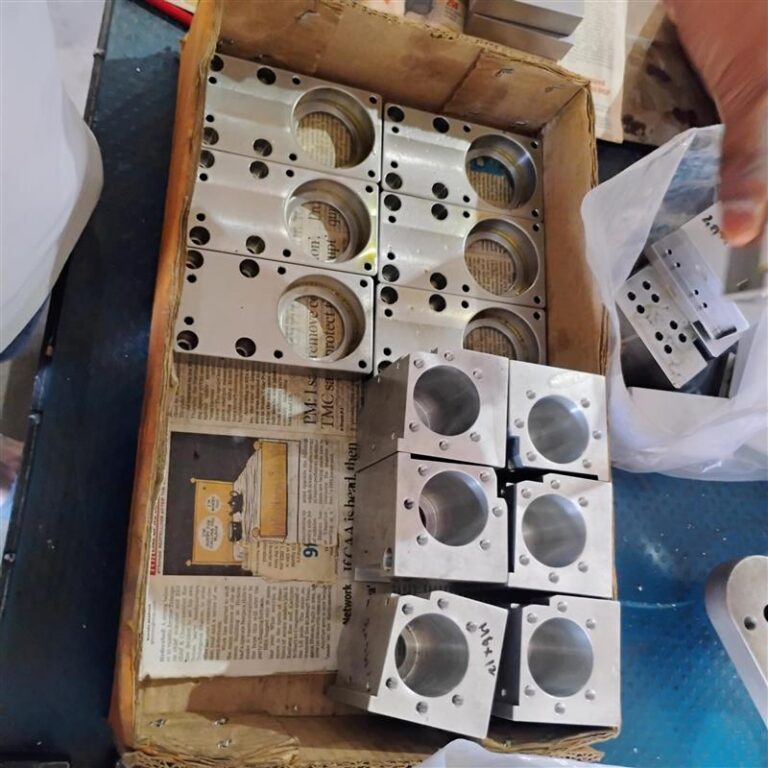
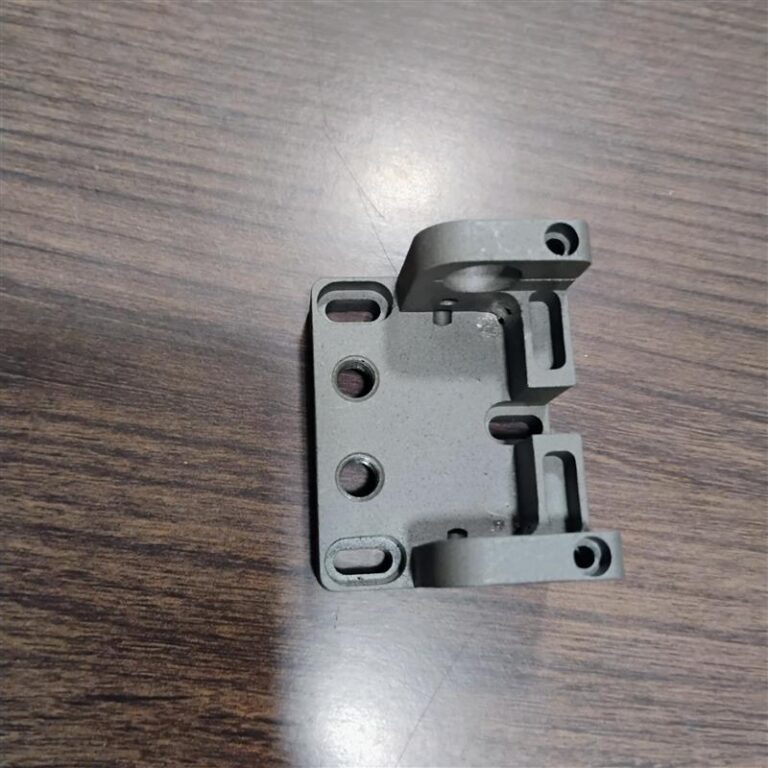
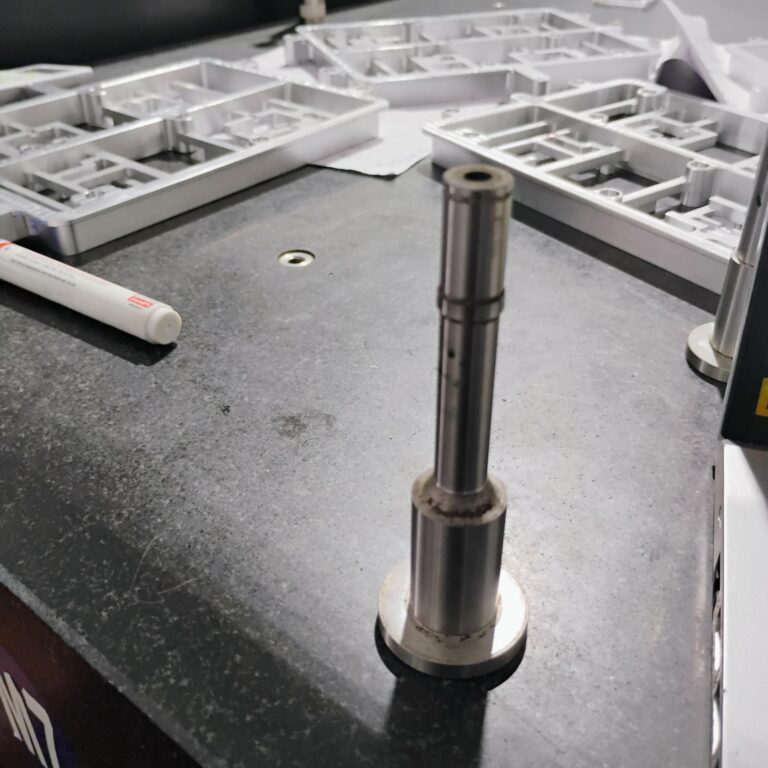
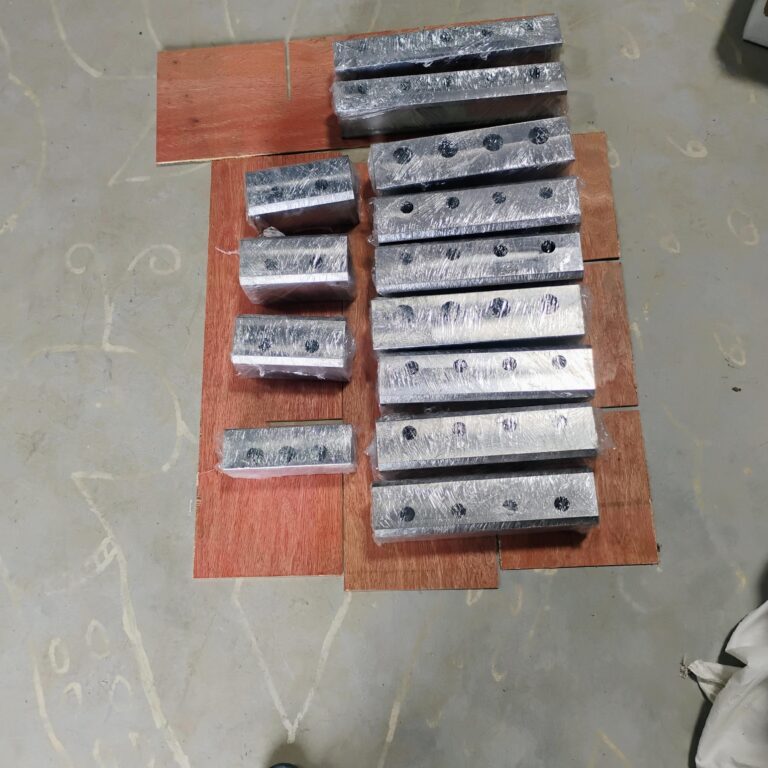
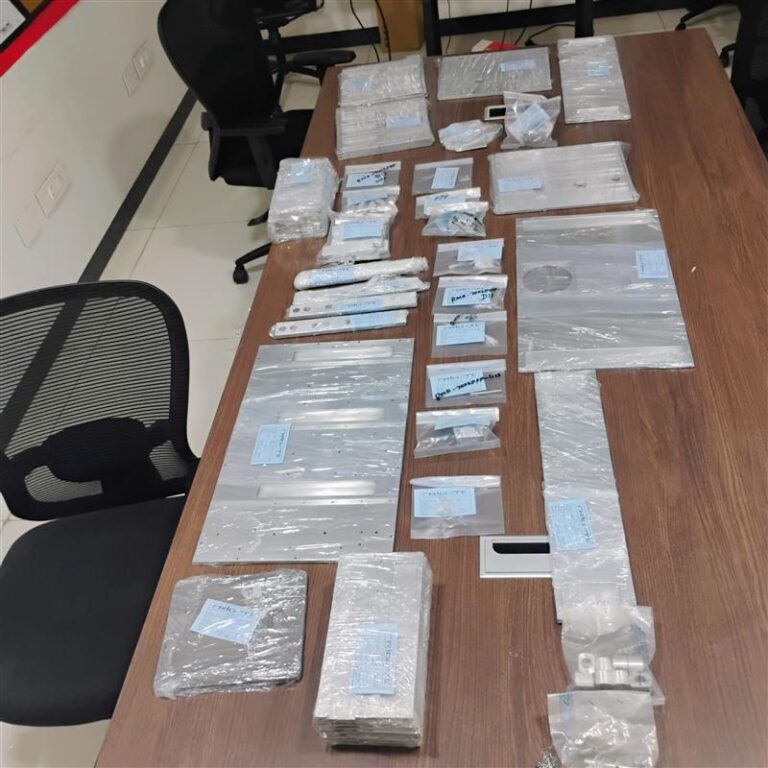

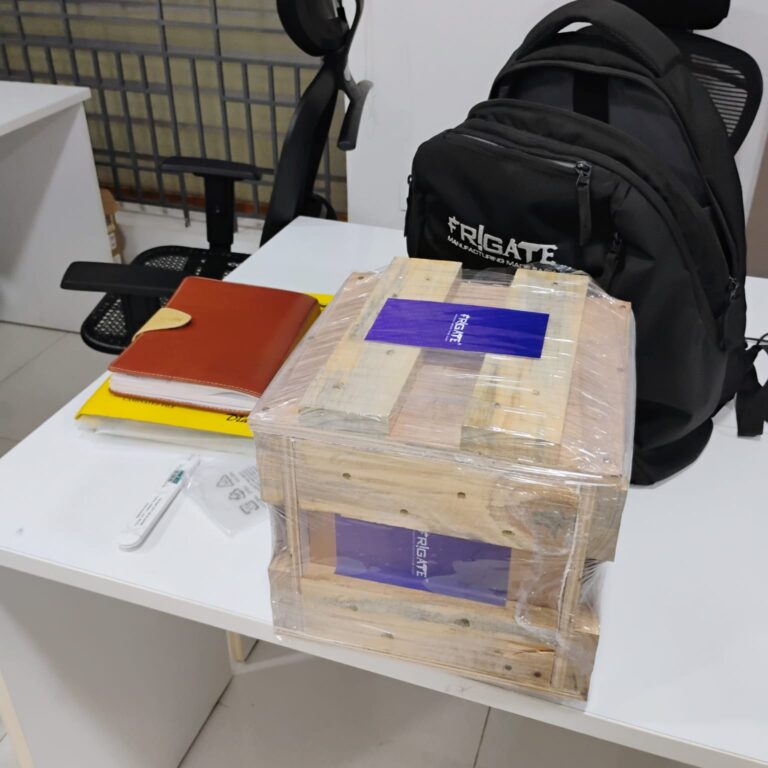


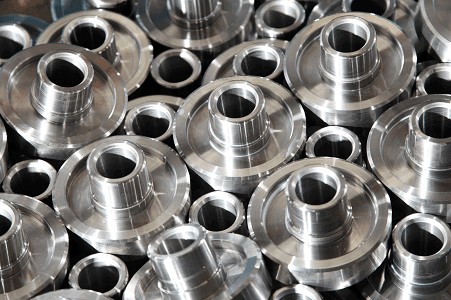
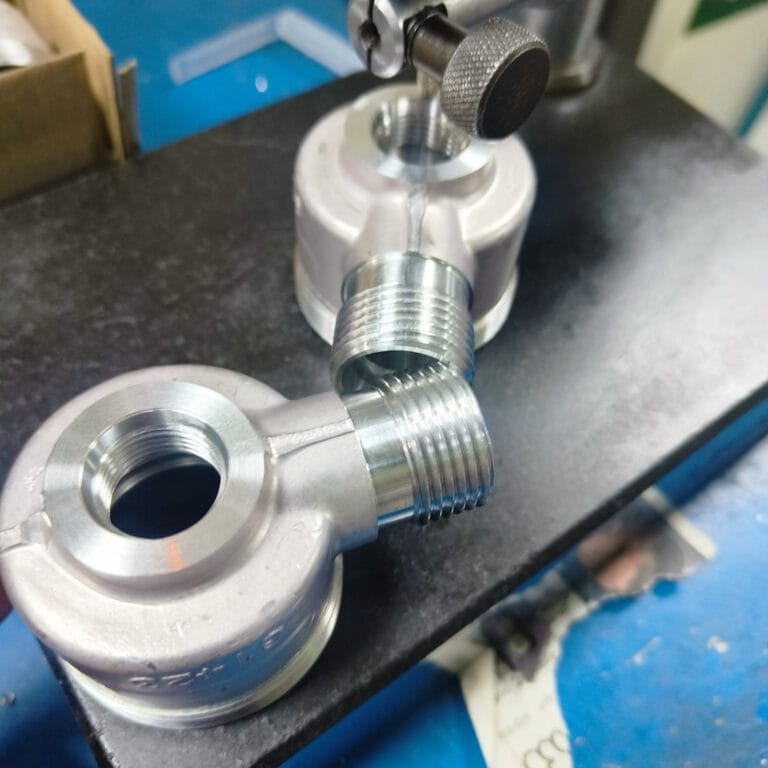
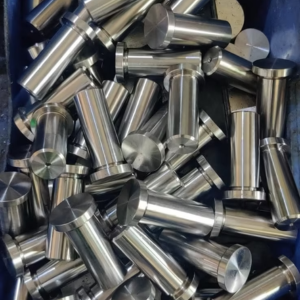
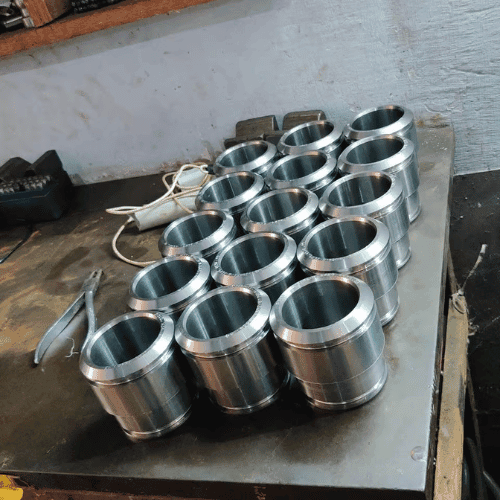
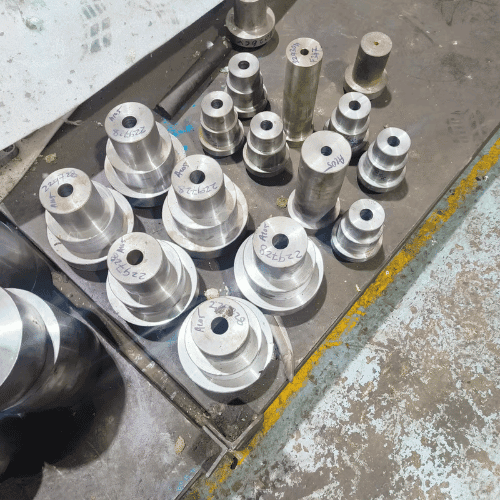
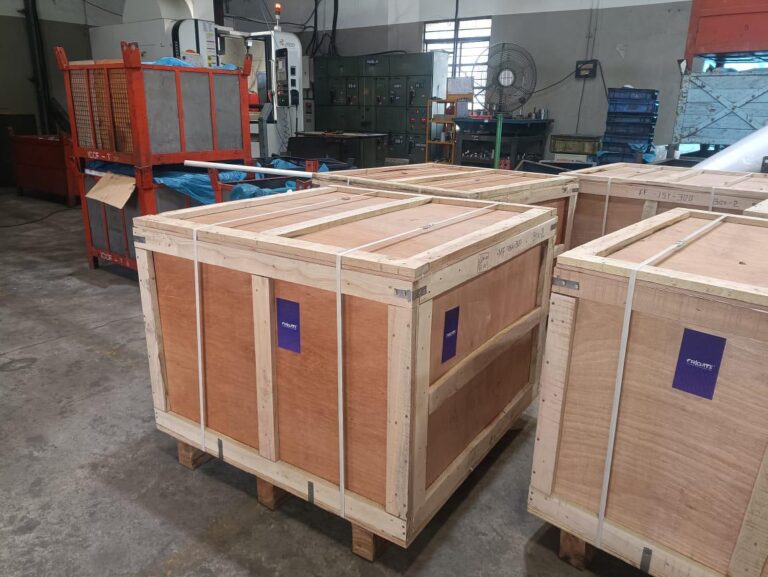
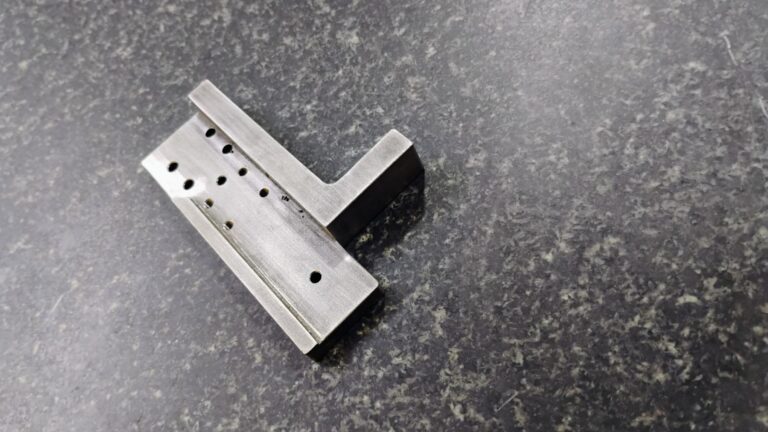
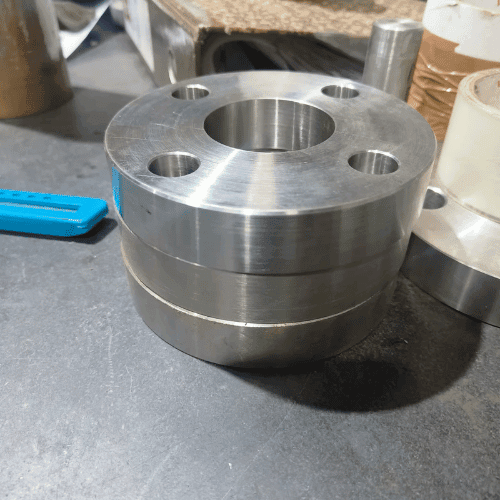
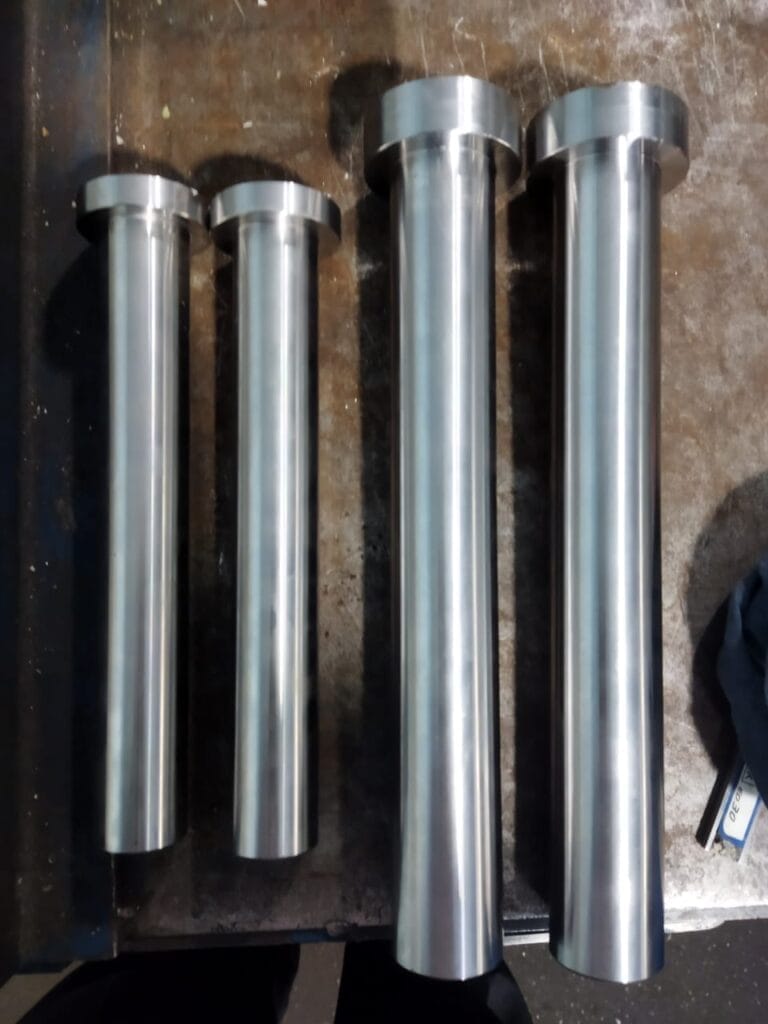

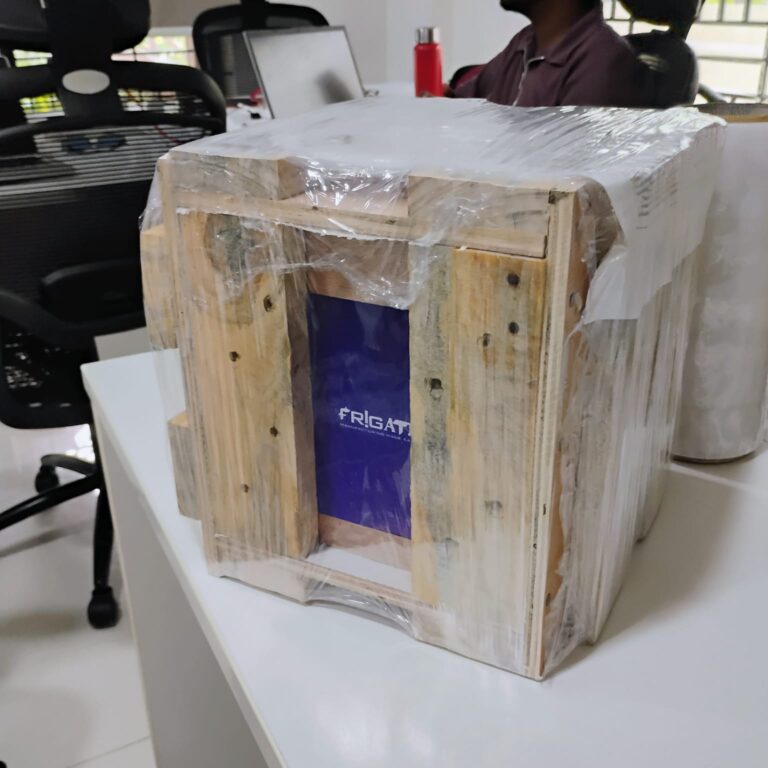

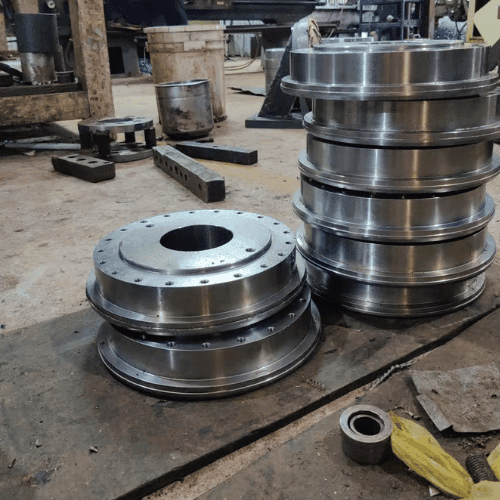
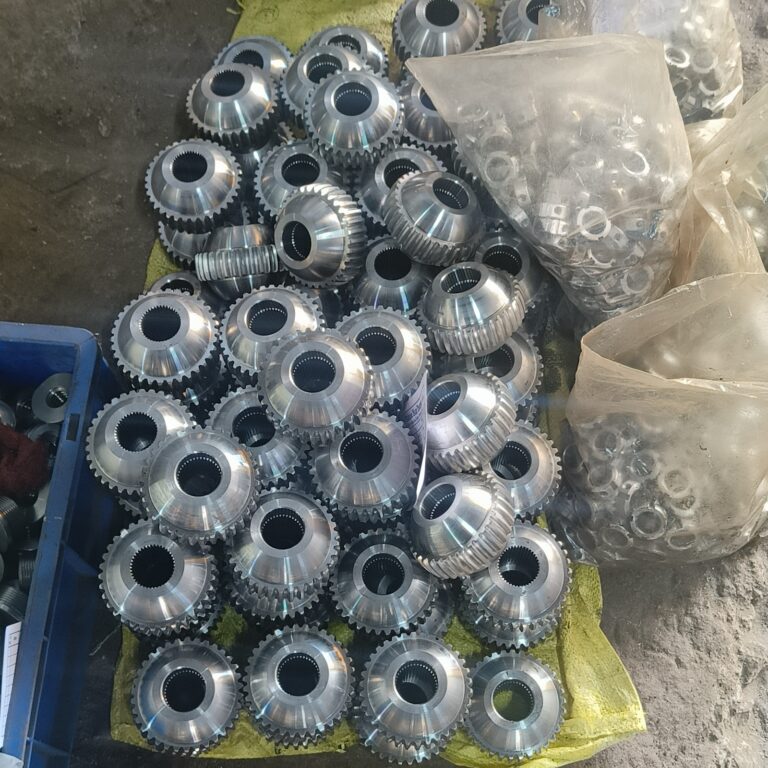
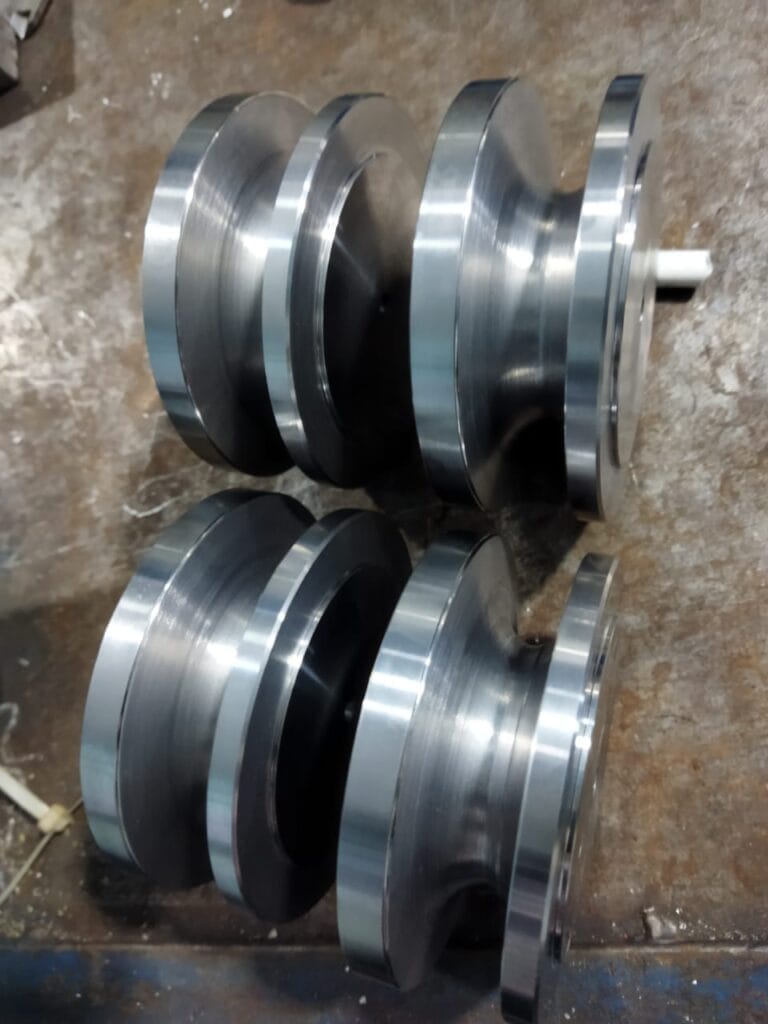
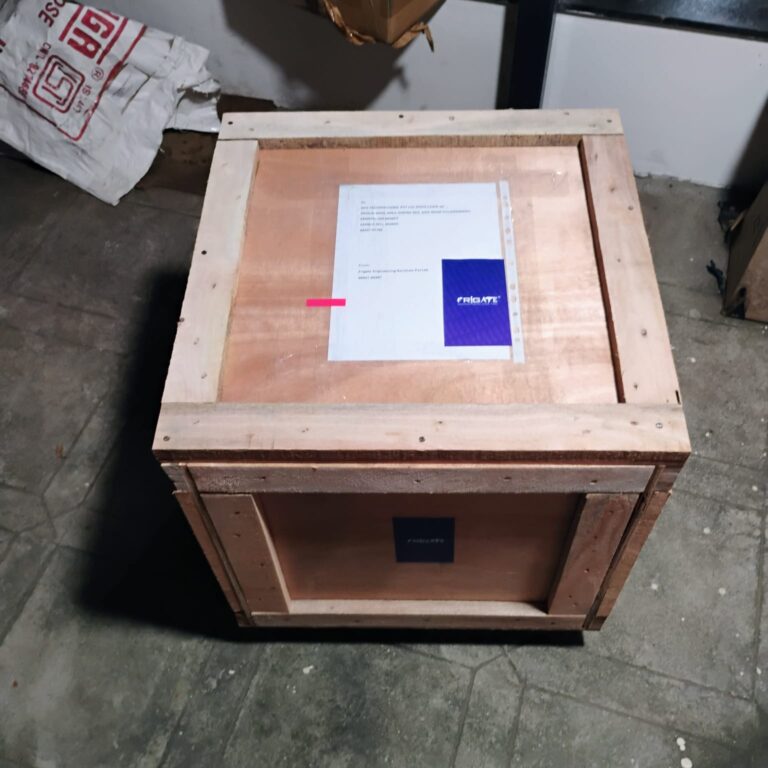
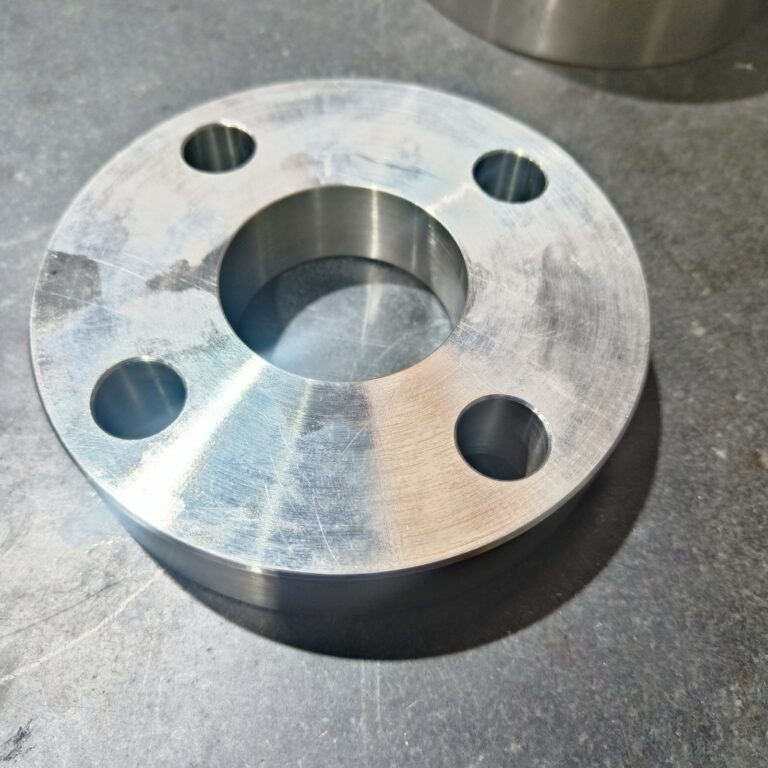
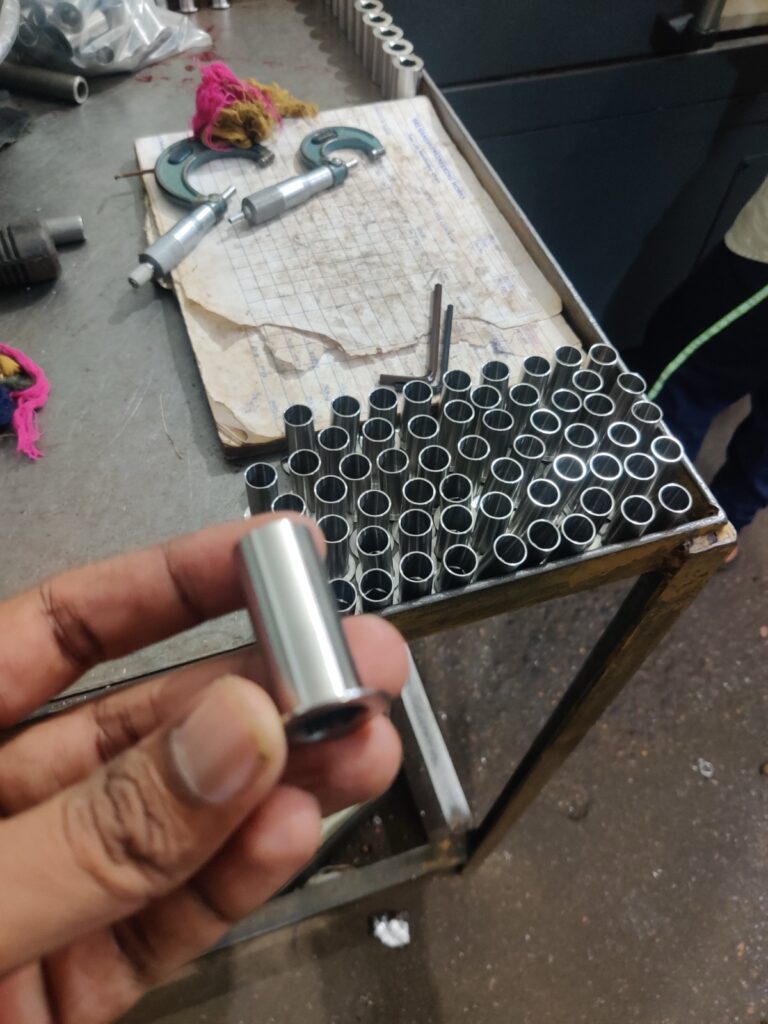
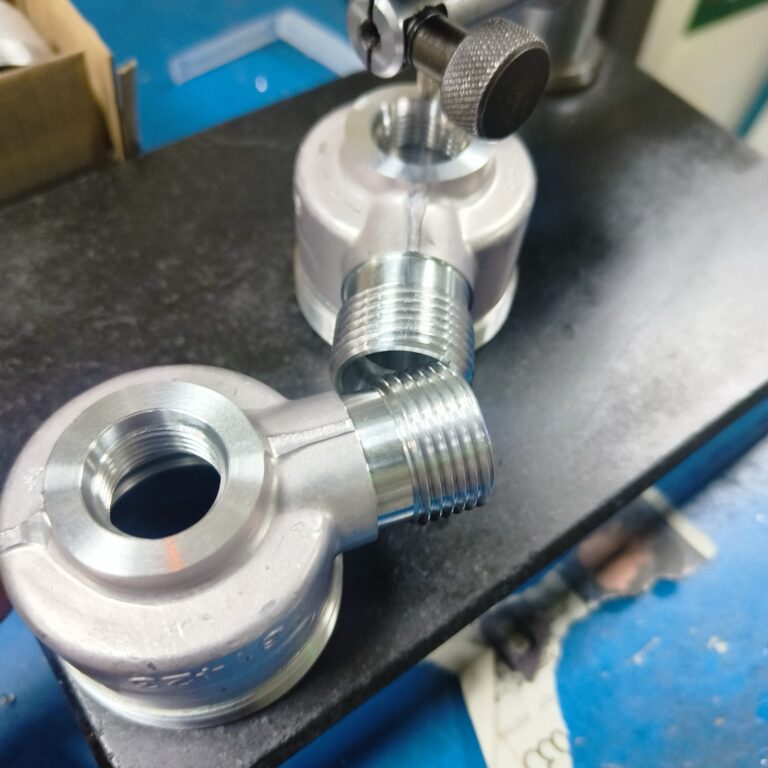
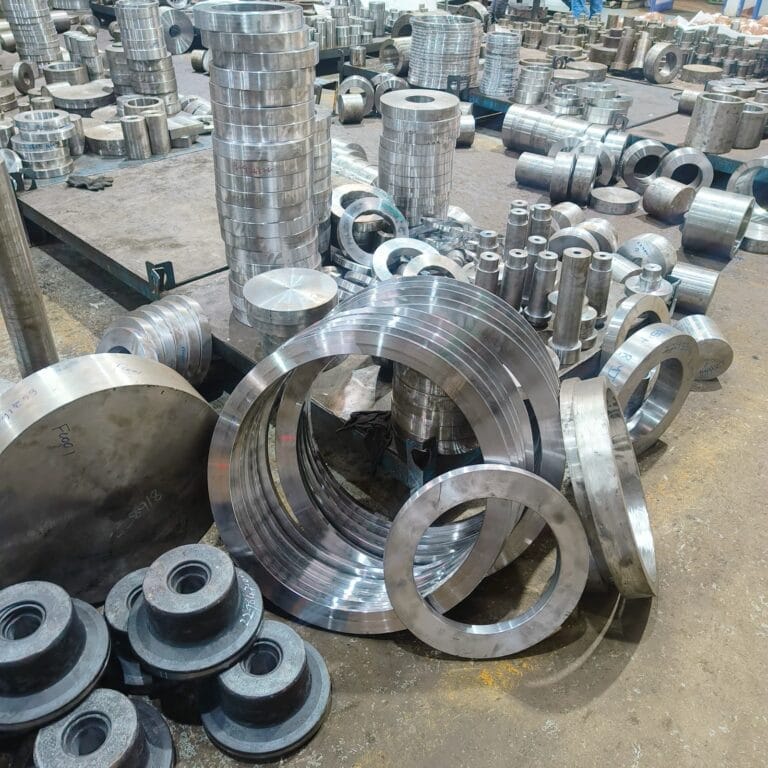
Other Industries We Serve
We deliver machining support across sectors that require consistency, material reliability, and tight dimensional control.
- Solid Progress
Our Manufacturing Metrics
Frigate brings stability, control, and predictable performance to your sourcing operations through a structured multi-vendor system.
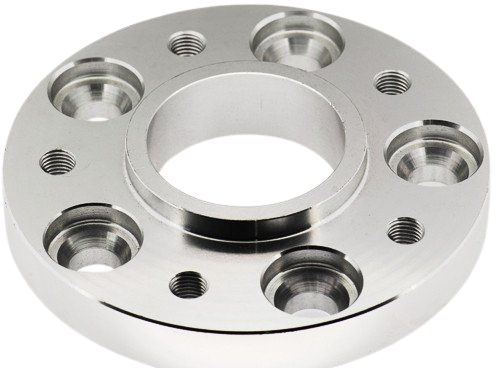
2.8X
Sourcing Cycle Speed
Frigate’s pre-qualified network shortens decision time between RFQ and PO placement.
94%
On-Time Delivery Rate
Structured planning windows and logistics-linked schedules improve project-level delivery reliability.
4X
Multi-Part Consolidation
We enable part family batching across suppliers to reduce fragmentation.
22%
Quality Rejection Rate
Multi-level quality checks and fixed inspection plans lower non-conformities.
30%
Procurement Costs
Optimized supplier negotiations and bulk order strategies reduce your overall sourcing expenses.
20%
Manual Processing Time
Automation of sourcing and supplier management significantly reduces time spent on manual tasks.
Get Clarity with Our Manufacturing Insights
- FAQ
Having Doubts? Our FAQ
Check all our Frequently Asked Questions in CNC Turning
Frigate employs closed-loop feedback systems combined with real-time thermal compensation to counteract machine and workpiece temperature variations. Continuous monitoring of spindle runout and backlash allows dynamic adjustments to maintain sub-micron dimensional tolerances. Adaptive control software optimizes cutting parameters based on tool wear and material behavior. This comprehensive approach minimizes scrap and ensures consistent part quality throughout extended runs.
Frigate utilizes high-pressure coolant delivery and cryogenic cooling to manage heat generated during machining of tough aerospace alloys like Inconel and titanium. These cooling methods reduce tool wear and prevent thermal damage to the workpiece microstructure. Tooling is selected for high abrasion resistance to complement these cooling strategies. Together, they maintain component fatigue strength and surface integrity critical for aerospace applications.
All machining parameters, tool changes, and inspection data are captured digitally and linked to unique part identifiers. Frigate maintains this data within a secure system compliant with AS9100 and NADCAP standards, ensuring complete traceability. This enables precise tracking of part history and facilitates thorough audits. Such rigor supports customer confidence and regulatory compliance.
Frigate’s CNC turning centers feature synchronized multi-axis control allowing simultaneous internal and external machining operations. This reduces setup time and eliminates alignment errors common in multi-step processes. Collision avoidance software and kinematic calibration ensure safe and accurate machining of intricate geometries. The result is improved surface finish and dimensional accuracy in complex aerospace components.
Tool life is monitored in real time using spindle load and vibration sensors, with data fed into predictive maintenance schedules. Scheduled tooling changes prevent unexpected downtime and maintain machining precision. Tool inventories are aligned with production forecasts to ensure availability. This system supports on-time delivery without compromising quality or repeatability.
We'd love to Manufacture for you!
Submit the form below and our representative will be in touch shortly.
LOCATIONS
Global Sales Office
818, Preakness lane, Coppell, Texas, USA – 75019
Registered Office
10-A, First Floor, V.V Complex, Prakash Nagar, Thiruverumbur, Trichy-620013, Tamil Nadu, India.
Operations Office
9/1, Poonthottam Nagar, Ramanandha Nagar, Saravanampatti, Coimbatore-641035, Tamil Nadu, India. ㅤ
Other Locations
- Bhilai
- Chennai
- Texas, USA