Micron Level Component Manufacturing for Metrology Instruments
Frigate enables sub-micron tolerances for stable and repeatable measurement performance.
Frigate Builds Thermal-Stable Parts for Metrology Systems
Metrology-Grade Manufacturing
Frigate uses advanced CNC and flow analysis to ensure stable, uniform components for high-mix, low-volume metrology applications.
Thermal Dimensional Stability
Vacuum-stabilized alloys and stress-relief cycles control deformation under temperature shifts in CMM fixtures and probe assemblies.
Functional Surface Precision
Tool deflection compensation and isolated fixturing achieve <1 μm flatness and exact angularity, validated via laser interferometry.
Our Clients
Trusted by Engineers and Purchasing Leaders
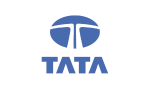
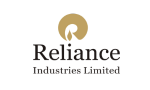


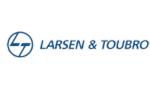
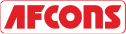


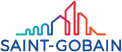

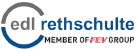

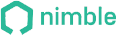
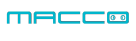









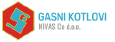
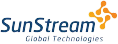

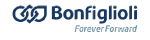


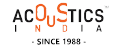
Ensure Precision Alignment in Bore Interfacing
Achieving sub-micron alignment in bore-to-bore and shaft fits is essential for air gauges, calibration mandrels, and probe carriers.
Machine bores and shafts within ±1 μm using fine boring heads, hydrostatic guides, and thermal drift compensation for high-precision mating parts.
Use Renishaw probing systems during machining cycles to capture dimensional shifts and auto-correct paths within ±0.5 μm tolerances.
Employ SPC data analysis to monitor drift, tool wear, and geometry shifts—ensuring batch-wide conformance and long-term instrument repeatability.

Deliver Tool-Mark-Free Surfaces for Critical Contact
Surface integrity on optical flats, stylus holders, and metrology bases demands ultra-smooth finishes with no tool-induced artifacts or micro-chatter.
Apply ultra-precision fly-cutting using single-point diamond tools to achieve optical-grade surface finish on non-ferrous and glass materials.
Use fine-particle abrasive lapping and non-contact polishing to achieve Ra < 0.05 μm, preventing surface noise in optical and tactile interfaces.
Inspect all contact-critical planes using white-light interferometry and optical profilometers to ensure form, waviness, and micro-finish compliance.

Maintain Traceable Metadata for High-Mix Production
In metrology, low-volume high-variety part production requires each component to carry a validated digital footprint for standards compliance.
Encode each part with traceable metadata including machine ID, operator stamp, tool batch, and thermal cycle records via embedded laser marking.
Maintain complete machining history with time-stamped parameter logs and fixture ID tracking to support ISO 17025 and NIST requirements.
Generate certifiable trace paths and inspection reports linked to CAD files and SPC charts, enabling end-to-end component lifecycle validation.

Our Machined Products
We support your production needs with CNC-machined parts, subassemblies, and performance-critical components.
- Real Impact
Words from Clients
See how global OEMs and sourcing heads describe their experience with our scalable execution.
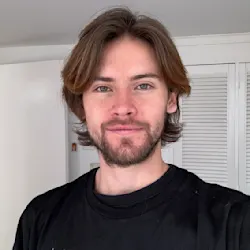
“Quick turnaround and solid quality.”
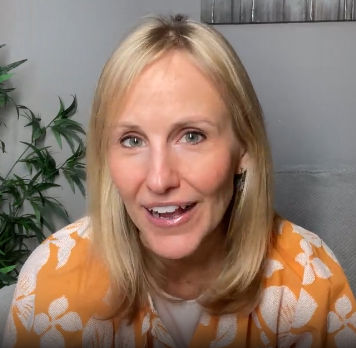
“The instant quote tool saved us time, and the parts were spot-on. Highly recommend Frigate!”
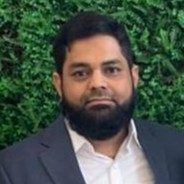
“I would strongly recommend Frigate to anyone who wants to do Rapid Prototyping, and take their ideas to manufacturing. One firm doing all kinds of Product Development!”
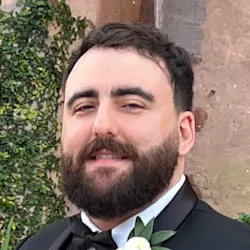
“Great service, fair price, and the parts worked perfectly in our assembly.”
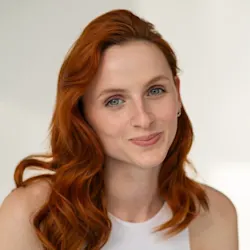
“Top-notch machining and fast shipping. Very satisfied with the results.”
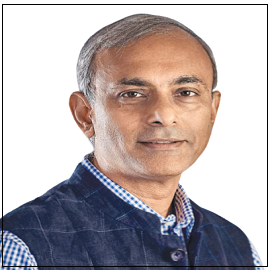
“The next disruption is happening in Prototyping & Manufacturing on-demand and Frigate is leading the way! I personally believe the Frigate's way of IIOT enabled cloud platform with Al.”
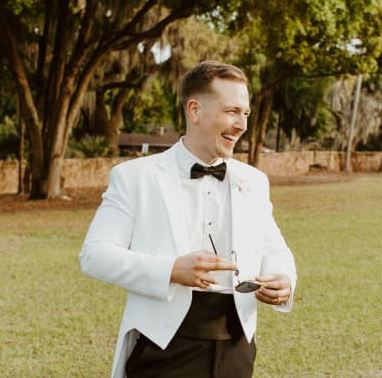
“Frigate delivered high-quality parts at a competitive price. The instant quote tool is a huge plus for us!”

“We appreciate the precision and quality of the machined components in the recent delivery—they meet our specifications perfectly and demonstrate Frigate’s capability for excellent workmanship.”
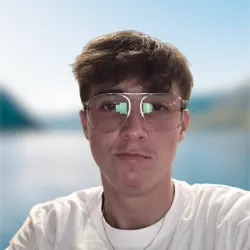
“Flawless execution from quote to delivery.”

“I am absolutely happy to work with supplier like Frigate who were quite proactive & result oriented . Frigate has high willingness team who has strong know how & their passion towards the products & process were absolutely thrilling.”
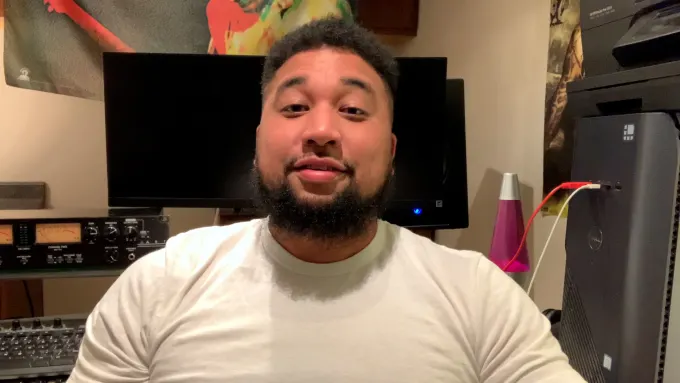
“The precision on these parts is impressive, and they arrived ahead of schedule. Frigate’s process really stands out!”
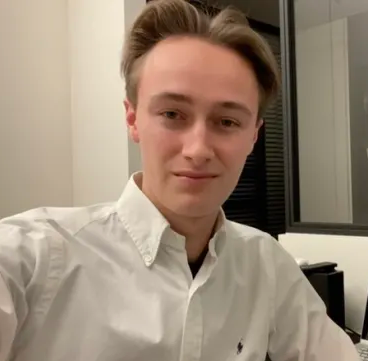
“Parts were exactly as spec’d, and the instant quote made budgeting a breeze.”
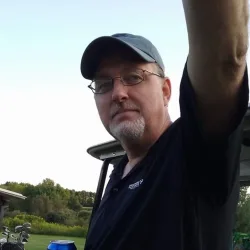
“Good value for the money.”
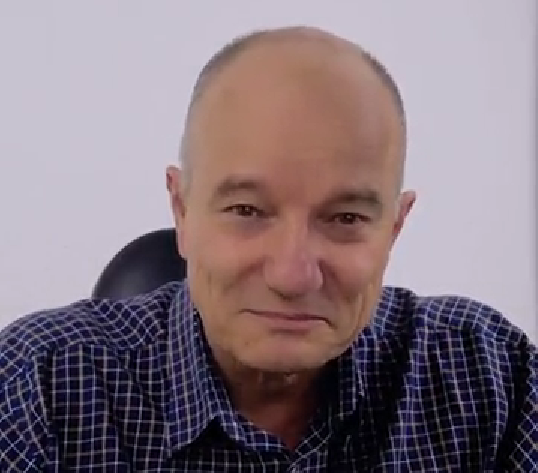
“The finish was perfect, and the team was easy to work with.”

“Working with Frigate has been great. Their proactive, results-driven approach and expertise shine through in every project. It's been a pleasure collaborating with them.”

"We are highly satisfied with the timely delivery and quality of the MIG Welding Cable from Frigate. Their attention to detail, secure packaging, and quick responsiveness stood out. We confidently recommend Frigate Engineering Services Pvt. Ltd. as a reliable manufacturing partner."
- We export to 12+ countries
Frigate’s Global Presence
Frigate takes pride in facilitating “Make in India for the globe“. As our global network of Frigaters provides virtually limitless capacity, and through our IoT enabled platform your parts go directly into production. By digitally and technologically enabling “the silent pillars of the economy” MSME and SME manufacturing industries, we are able to tap the huge potential for manufacturing to bring the best results for our clients.

100,000+
Parts Manufactured
250+
Frigaters
2000+
Machines
450+
Materials
25+
Manufacturing Process
- Solid Progress
How You Benefit with Us
Frigate brings stability, control, and predictable performance to your sourcing operations through a structured multi-vendor system.
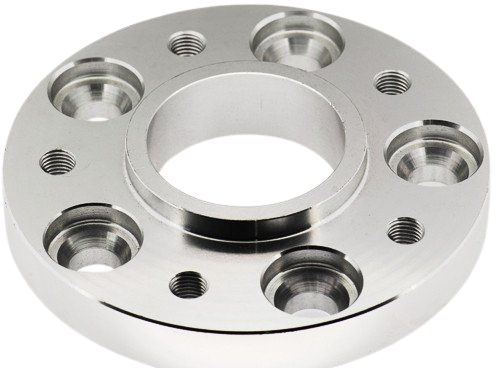
2.8X
Sourcing Cycle Speed
Frigate’s pre-qualified network shortens decision time between RFQ and PO placement.
94%
On-Time Delivery Rate
Structured planning windows and logistics-linked schedules improve project-level delivery reliability.
4X
Multi-Part Consolidation
We enable part family batching across suppliers to reduce fragmentation.
22%
Quality Rejection Rate
Multi-level quality checks and fixed inspection plans lower non-conformities.
30%
Procurement Costs
Optimized supplier negotiations and bulk order strategies reduce your overall sourcing expenses.
20%
Manual Processing Time
Automation of sourcing and supplier management significantly reduces time spent on manual tasks.
Other Industries We Serve
We deliver machining support across sectors that require consistency, material reliability, and tight dimensional control.
Get Clarity with Our Manufacturing Insights
Frigate uses high-stability machining centers equipped with thermally balanced spindles and nano-precision feedback systems. Bore features are machined using ultra-fine boring heads, followed by in-cycle inspection using Renishaw OMP probes that detect deviations in real time. The machine auto-corrects for tool wear, thermal drift, and axis backlash before continuing to the next feature. Final bore-to-bore alignment is verified using calibrated air gauges and high-resolution coordinate measuring machines (CMMs), ensuring concentricity and roundness within ±1 μm across multiple components in the same or different batches.
Yes, Frigate specializes in machining ultra-stable frames using low-CTE alloys like Invar, Super Invar, and low-expansion stainless steels. These materials are sensitive to internal stresses caused by uneven material removal and localized heating. To avoid this, Frigate separates roughing and finishing operations using thermal soak cycles between stages. Additionally, parts are pre-stabilized using cryogenic treatments or vibratory stress-relief processes before final machining. This approach prevents stress-induced deformation over time, ensuring long-term dimensional stability critical in high-accuracy metrology frames used in CMMs and calibration benches.
Frigate achieves ultra-flat surfaces by controlling every variable in the machining environment. All finishing operations are performed in temperature-controlled zones held within ±0.2°C. Fixtures are mounted on zero-vibration granite bases during the final cuts, and cutter paths are dynamically adjusted based on real-time tool deflection feedback. To avoid distortions, low-depth passes are used with balanced cutting forces. After machining, each surface is inspected using laser interferometry and autocollimators to confirm flatness and parallelism within sub-micron limits. This ensures optical and contact measurement planes remain true across the instrument’s lifetime.
Frigate has built a custom Manufacturing Execution System (MES) tailored for high-mix, low-volume precision work. Every component is tagged digitally with process data including machine ID, operator code, tool lot number, cutting parameters, and thermal history. During production, measurement data is logged in real time and linked to each unique part ID. This allows every unit—even in one-off or prototype batches—to be fully traceable for ISO 17025 or NIST calibration requirements. Purchasers receive digital quality reports that include SPC charts, machine logs, and inspection certificates tied directly to each part.
To achieve flawless optical and tactile surfaces, Frigate uses diamond fly-cutting, single-point turning, and ultra-fine abrasive lapping. These techniques are applied on dedicated ultra-precision machines with controlled spindle speeds, minimal vibration, and micron-level tool offset adjustment. The finishing process eliminates tool-induced chatter, micro-scratches, or burrs that can distort optical readings. Each surface is inspected using non-contact metrology tools like white-light interferometers and profilometers to confirm roughness values below Ra 0.05 μm. This ensures surfaces are clean, uniform, and compatible with high-sensitivity metrology functions like stylus contact or laser reflection.
We'd love to Manufacture for you!
Submit the form below and our representative will be in touch shortly.
LOCATIONS
Registered Office
10-A, First Floor, V.V Complex, Prakash Nagar, Thiruverumbur, Trichy-620013, Tamil Nadu, India.
Operations Office
9/1, Poonthottam Nagar, Ramanandha Nagar, Saravanampatti, Coimbatore-641035, Tamil Nadu, India. ㅤ
Other Locations
- Bhilai
- Chennai
- USA
- Germany