Mining & Heavy Equipment Manufacturing Machining Solutions
Drive Structural Reliability with Frigate’s Tolerance-Controlled, Wear-Resistant Components for Large-Scale Equipment and Harsh Environments.
Frigate executes your heavy equipment manufacturing needs with CNC capabilities
Precision Machining for Load-Bearing Assemblies
Frigate machines shafts, brackets, and housings to ±0.01 mm tolerances for stress-prone powertrain and suspension systems.
Hard Metal and Abrasion-Grade Machining
We process AR steels, quenched alloys, and heat-treated carbon grades under toolpaths built for consistent tool life and chip evacuation.
Large-Envelope, Multi-Axis Setup Capabilities
Frigate handles oversized blocks and profiles using multi-axis horizontal and gantry mills with setups exceeding 1500 mm in travel.
Our Clients
Trusted by Engineers and Purchasing Leaders
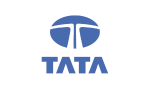
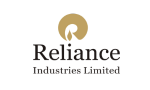


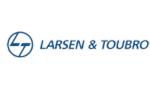
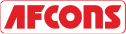


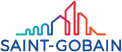

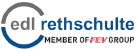

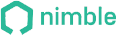
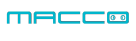









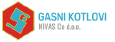
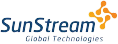

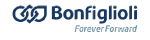


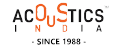
Enable Mechanical Stability in Harsh Operating Zones
Mining components must retain structural integrity during vibration, thermal cycles, and heavy-load engagement.
Grind and machine contact faces to tight flatness for clutch packs, gear seats, and bushing housings in transmission systems.
Apply CNC strategies for duplex stainless or chromium-plated interfaces in slurry-exposed or mud-facing surfaces.
Pre-machine slots, tapers, and bevels to avoid deformation during field welds or heavy-duty bolting assemblies.

Achieve Dimensional and Process Qualification Across Industrial Standards
Frigate aligns all heavy equipment machining to ISO 9001 and key industry-specific standards for documentation and consistency.
Use contact and non-contact inspection to verify shaft concentricity, bore location, and planar alignment on assembly-critical faces.
Every batch includes operator logs, revision control, and process data tagged to component IDs and inspection sets.
Deploy Cp/Cpk analysis and repeatability studies to validate tool wear, batch consistency, and setup performance over large-scale runs.

Increase Wear Life with Precision Surface Treatments
Surface quality directly affects seal retention, mating interface life, and wear resistance across demanding field conditions.
CNC-prepared surfaces enable thermal spray, PVD, or hard chrome adhesion for parts operating in dust-heavy or chemically aggressive areas.
Surface flatness is maintained under 0.03 mm for sealing grooves and compression interfaces in hydraulic systems.
Deburring and edge rounding on lifting lugs, access panels, and grip zones help reduce handling risks and edge-related fatigue.

Our Machined Products
We support your production needs with CNC-machined parts, subassemblies, and performance-critical components.
- Real Impact
Words from Clients
See how global OEMs and sourcing heads describe their experience with our scalable execution.
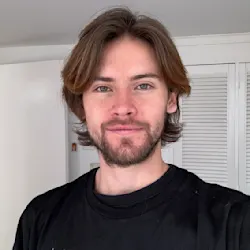
“Quick turnaround and solid quality.”
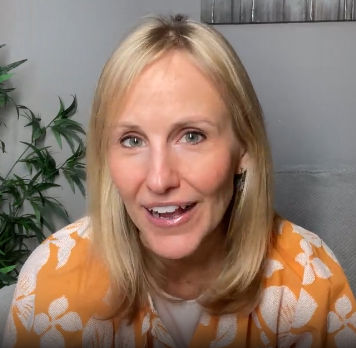
“The instant quote tool saved us time, and the parts were spot-on. Highly recommend Frigate!”
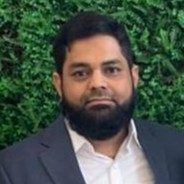
“I would strongly recommend Frigate to anyone who wants to do Rapid Prototyping, and take their ideas to manufacturing. One firm doing all kinds of Product Development!”
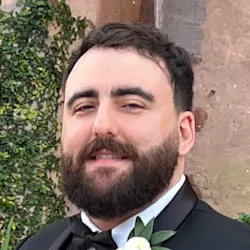
“Great service, fair price, and the parts worked perfectly in our assembly.”
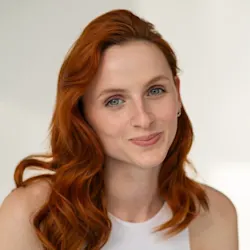
“Top-notch machining and fast shipping. Very satisfied with the results.”
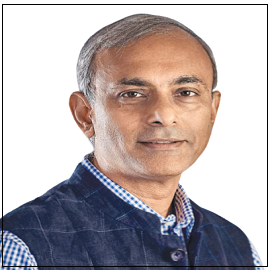
“The next disruption is happening in Prototyping & Manufacturing on-demand and Frigate is leading the way! I personally believe the Frigate's way of IIOT enabled cloud platform with Al.”
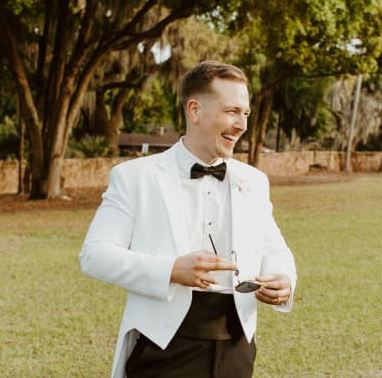
“Frigate delivered high-quality parts at a competitive price. The instant quote tool is a huge plus for us!”

“We appreciate the precision and quality of the machined components in the recent delivery—they meet our specifications perfectly and demonstrate Frigate’s capability for excellent workmanship.”
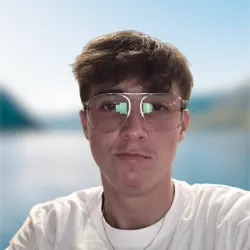
“Flawless execution from quote to delivery.”

“I am absolutely happy to work with supplier like Frigate who were quite proactive & result oriented . Frigate has high willingness team who has strong know how & their passion towards the products & process were absolutely thrilling.”
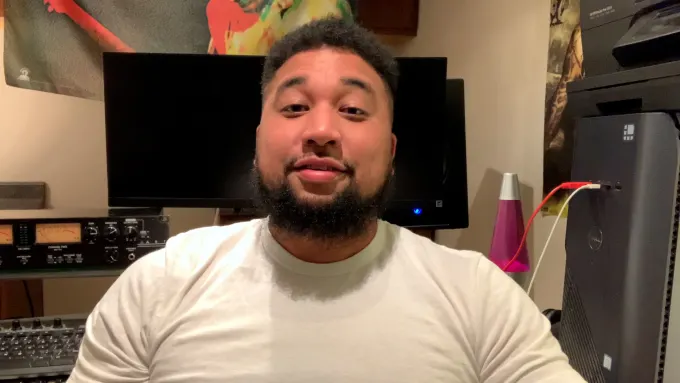
“The precision on these parts is impressive, and they arrived ahead of schedule. Frigate’s process really stands out!”
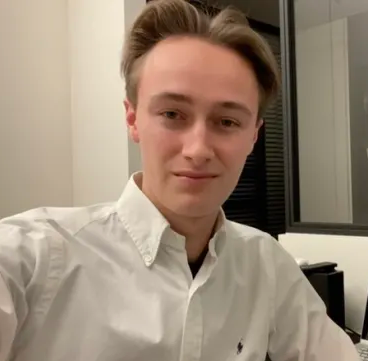
“Parts were exactly as spec’d, and the instant quote made budgeting a breeze.”
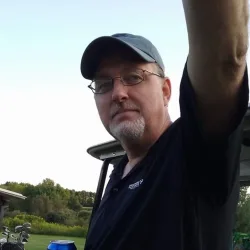
“Good value for the money.”
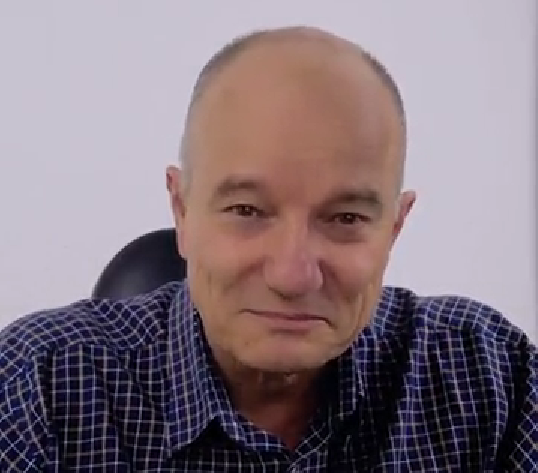
“The finish was perfect, and the team was easy to work with.”

“Working with Frigate has been great. Their proactive, results-driven approach and expertise shine through in every project. It's been a pleasure collaborating with them.”

"We are highly satisfied with the timely delivery and quality of the MIG Welding Cable from Frigate. Their attention to detail, secure packaging, and quick responsiveness stood out. We confidently recommend Frigate Engineering Services Pvt. Ltd. as a reliable manufacturing partner."
- We export to 12+ countries
Frigate’s Global Presence
Frigate takes pride in facilitating “Make in India for the globe“. As our global network of Frigaters provides virtually limitless capacity, and through our IoT enabled platform your parts go directly into production. By digitally and technologically enabling “the silent pillars of the economy” MSME and SME manufacturing industries, we are able to tap the huge potential for manufacturing to bring the best results for our clients.

100,000+
Parts Manufactured
250+
Frigaters
2000+
Machines
450+
Materials
25+
Manufacturing Process
- Solid Progress
How You Benefit with Us
Frigate brings stability, control, and predictable performance to your sourcing operations through a structured multi-vendor system.
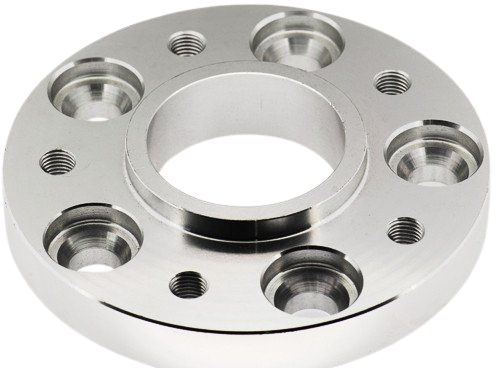
2.8X
Sourcing Cycle Speed
Frigate’s pre-qualified network shortens decision time between RFQ and PO placement.
94%
On-Time Delivery Rate
Structured planning windows and logistics-linked schedules improve project-level delivery reliability.
4X
Multi-Part Consolidation
We enable part family batching across suppliers to reduce fragmentation.
22%
Quality Rejection Rate
Multi-level quality checks and fixed inspection plans lower non-conformities.
30%
Procurement Costs
Optimized supplier negotiations and bulk order strategies reduce your overall sourcing expenses.
20%
Manual Processing Time
Automation of sourcing and supplier management significantly reduces time spent on manual tasks.
Other Industries We Serve
We deliver machining support across sectors that require consistency, material reliability, and tight dimensional control.
Get Clarity with our Manufacturing Insights
Frigate operates multi-axis horizontal mills and gantry setups with adaptive fixturing to control deflection across large workpieces. Thermal compensation systems correct for expansion, while in-process probing monitors tool deviation in real time. These steps help retain critical tolerances below ±0.01 mm on shafts, bearing seats, and bolt patterns, even on cast or forged parts exceeding 1.5 meters. This precision supports structural alignment in frames, drives, and hydraulic assemblies exposed to high impact and vibration.
Frigate uses wear-optimized toolpaths for components machined from AR steels, martensitic alloys, and quenched-hardened plates. Tool selection prioritizes coated carbide inserts and controlled engagement angles to reduce heat and maintain edge life. For surfaces exposed to slurry, dirt, or rock impact, final machining stages include burr minimization and flatness control to support post-process coatings like tungsten carbide or thermal spray. These strategies ensure long-term durability in abrasive field conditions.
Frigate pre-machines weld prep areas and assembly fits using stress-relieved paths and softened entry geometries to avoid thermal distortion during on-site fabrication. Key fits such as bores, tapers, and grooves maintain uniformity for bolt-up or insertion under field conditions. All geometry is validated using 3D probing and optical systems to ensure alignment under as-welded stress. This approach supports fast fitment during installation and reduces the need for secondary adjustments in remote environments.
Frigate applies full batch traceability through integrated ERP and inspection systems that link part IDs to process logs, operator records, and tool paths. Each production run includes dimensional inspection reports, material certifications, and Cp/Cpk data summaries. Systems are built around ISO 9001 and project-specific QA protocols. This ensures repeatable production across thousands of kilograms of machined material, reducing rework risks and aligning with documentation needs for OEM and Tier 1 suppliers.
Frigate maintains Ra values below 0.8 µm on sealing surfaces using final-pass turning, grinding, or face milling techniques. Critical grooves for O-rings and gaskets are cut using tight-tolerance tools and verified for groove width, depth, and concentricity. Toolpath sequencing prevents heat buildup, which could affect sealing performance. These controlled surfaces ensure leak-free performance in pumps, actuators, and sealed housings used in off-road and underground operations.
We'd love to Manufacture for you!
Submit the form below and our representative will be in touch shortly.
LOCATIONS
Global Sales Office
818, Preakness lane, Coppell, Texas, USA – 75019
Registered Office
10-A, First Floor, V.V Complex, Prakash Nagar, Thiruverumbur, Trichy-620013, Tamil Nadu, India.
Operations Office
9/1, Poonthottam Nagar, Ramanandha Nagar, Saravanampatti, Coimbatore-641035, Tamil Nadu, India. ㅤ
Other Locations
- Bhilai
- Chennai
- Texas, USA