Consumer Electronics Industry Machining Solutions
Accelerate Device Innovation with Frigate’s Tight-Tolerance Machining for Thermal Frames, Structural Enclosures, and EMI-Shielded Assemblies.
Frigate machines your electronic assemblies with process-driven CNC capabilities
High-Purity Metal Processing
Machine aluminum alloys, stainless steels, and magnesium blocks under cleanroom-compatible conditions to avoid oxidation and surface contamination.
Precision Machining for Miniature Assemblies
Maintain ±0.005 mm tolerances on small-scale frames, heatsinks, and housing parts using multi-axis setups and thermal-stable fixturing.
Thin-Wall and Pocketed Part Accuracy
Deploy adaptive toolpaths and synchronized spindle speeds to maintain integrity in wall thicknesses below 0.6 mm and deep cavities.
Our Clients
Trusted by Engineers and Purchasing Leaders
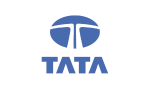
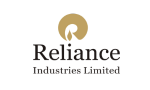


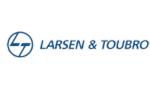
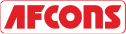


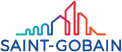

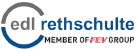

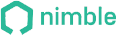
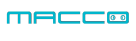









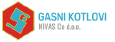
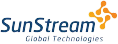

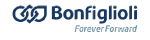


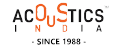
Achieve Dimensional Control Across High-Throughput Production Cycles
Production stability and tight tolerances are essential for mass-scale enclosures, connectors, and chassis used in mobile, wearables, and home tech.
Use automation-enabled pallet changers and tool wear compensation to support 50,000+ part runs with minimal dimensional shift.
Create gasket grooves, snap-fit interfaces, and metal overlap zones while retaining critical gap tolerances for electrical shielding.
Control edge quality through in-machine deburring, passivation, and corner rounding for button zones, ports, and slot entries.

Meet Global Quality Standards for Consumer Electronics Components
Inspection and documentation systems meet international quality compliance for telecom, computing, and personal electronics hardware.
3D inspection using CMM and multi-sensor probes confirms features under 1 mm, including mounting bosses, thread starts, and vent holes.
Maintain digital logs for revision tracking, operator ID, part ID, and process timestamping for traceable batch manufacturing.
Collect Cp/Cpk and gauge R&R data across shifts to qualify machining programs for multi-month production cycles.

Increase Component Function and Finish with Controlled Surface Processing
Controlled surface preparation supports cosmetic quality, corrosion resistance, and interface performance under various consumer use conditions.
Apply anodizing, electroless nickel, or conversion coatings to enhance appearance and provide conductive or resistive layer options.
Use vibratory polishing, media blasting, and brush finishing to achieve matte, gloss, or textured finishes on high-contact surfaces.
CNC-controlled deburring and corner profiling remove sharp edges from handheld device parts while preserving all functional fits.

Our Machined Products
We support your production needs with CNC-machined parts, subassemblies, and performance-critical components.
- Real Impact
Words from Clients
See how global OEMs and sourcing heads describe their experience with our scalable execution.
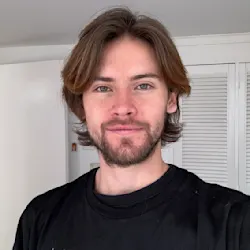
“Quick turnaround and solid quality.”
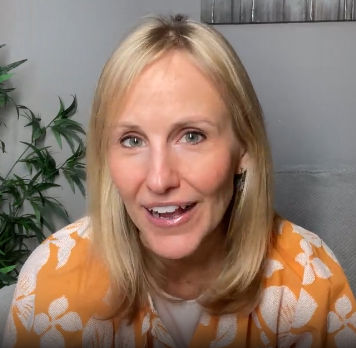
“The instant quote tool saved us time, and the parts were spot-on. Highly recommend Frigate!”
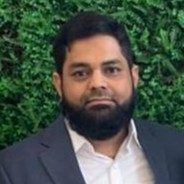
“I would strongly recommend Frigate to anyone who wants to do Rapid Prototyping, and take their ideas to manufacturing. One firm doing all kinds of Product Development!”
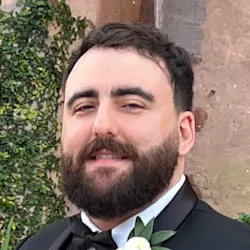
“Great service, fair price, and the parts worked perfectly in our assembly.”
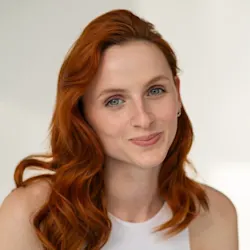
“Top-notch machining and fast shipping. Very satisfied with the results.”
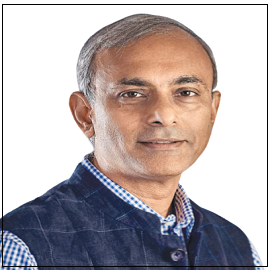
“The next disruption is happening in Prototyping & Manufacturing on-demand and Frigate is leading the way! I personally believe the Frigate's way of IIOT enabled cloud platform with Al.”
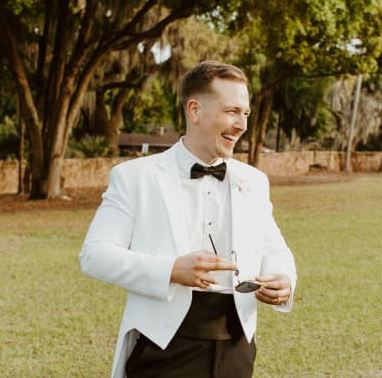
“Frigate delivered high-quality parts at a competitive price. The instant quote tool is a huge plus for us!”

“We appreciate the precision and quality of the machined components in the recent delivery—they meet our specifications perfectly and demonstrate Frigate’s capability for excellent workmanship.”
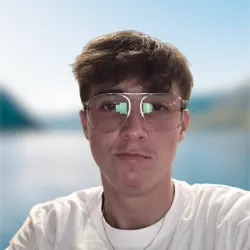
“Flawless execution from quote to delivery.”

“I am absolutely happy to work with supplier like Frigate who were quite proactive & result oriented . Frigate has high willingness team who has strong know how & their passion towards the products & process were absolutely thrilling.”
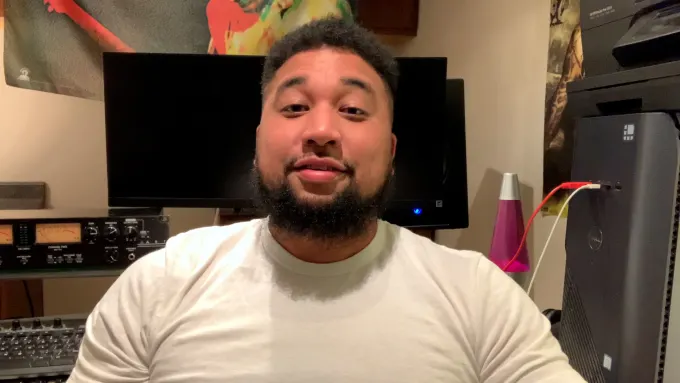
“The precision on these parts is impressive, and they arrived ahead of schedule. Frigate’s process really stands out!”
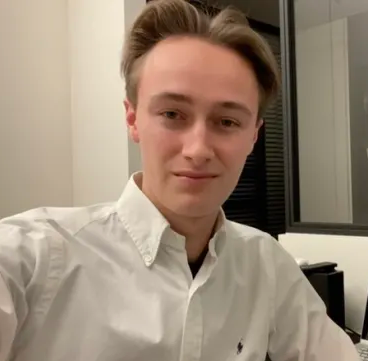
“Parts were exactly as spec’d, and the instant quote made budgeting a breeze.”
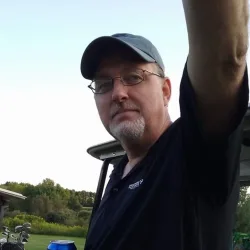
“Good value for the money.”
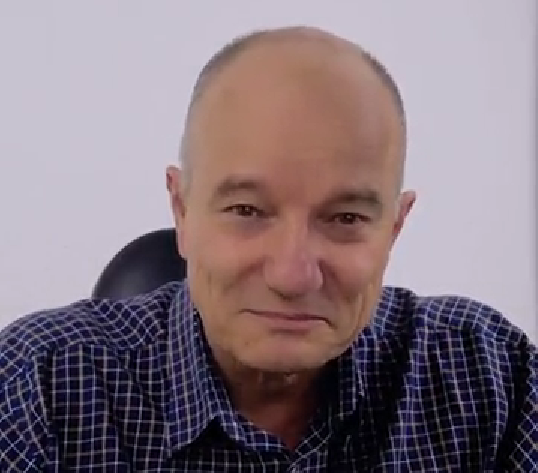
“The finish was perfect, and the team was easy to work with.”

“Working with Frigate has been great. Their proactive, results-driven approach and expertise shine through in every project. It's been a pleasure collaborating with them.”

"We are highly satisfied with the timely delivery and quality of the MIG Welding Cable from Frigate. Their attention to detail, secure packaging, and quick responsiveness stood out. We confidently recommend Frigate Engineering Services Pvt. Ltd. as a reliable manufacturing partner."
- We export to 12+ countries
Frigate’s Global Presence
Frigate takes pride in facilitating “Make in India for the globe“. As our global network of Frigaters provides virtually limitless capacity, and through our IoT enabled platform your parts go directly into production. By digitally and technologically enabling “the silent pillars of the economy” MSME and SME manufacturing industries, we are able to tap the huge potential for manufacturing to bring the best results for our clients.

100,000+
Parts Manufactured
250+
Frigaters
2000+
Machines
450+
Materials
25+
Manufacturing Process
- Solid Progress
How You Benefit with Us
Frigate brings stability, control, and predictable performance to your sourcing operations through a structured multi-vendor system.
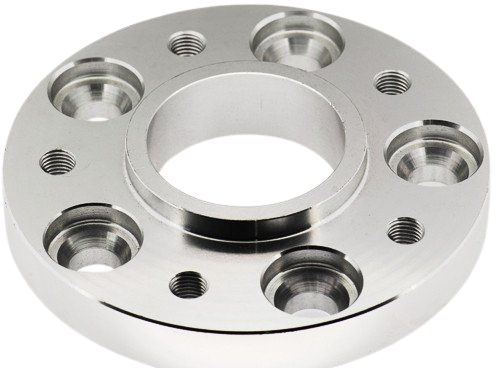
2.8X
Sourcing Cycle Speed
Frigate’s pre-qualified network shortens decision time between RFQ and PO placement.
94%
On-Time Delivery Rate
Structured planning windows and logistics-linked schedules improve project-level delivery reliability.
4X
Multi-Part Consolidation
We enable part family batching across suppliers to reduce fragmentation.
22%
Quality Rejection Rate
Multi-level quality checks and fixed inspection plans lower non-conformities.
30%
Procurement Costs
Optimized supplier negotiations and bulk order strategies reduce your overall sourcing expenses.
20%
Manual Processing Time
Automation of sourcing and supplier management significantly reduces time spent on manual tasks.
Other Industries We Serve
We deliver machining support across sectors that require consistency, material reliability, and tight dimensional control.
Get Clarity with Our Manufacturing Insights
Frigate uses synchronized spindle speed control and low-force cutting strategies to protect thin-walled frames during rough and finish passes. Fixture designs isolate vibration while heat buildup is minimized using adaptive coolant flow. These methods maintain dimensional accuracy in wall sections under 0.6 mm. As a result, structural integrity and part conformity are preserved across thousands of housing units.
Frigate applies toolpath optimization routines that manage cutter entry angles and reduce step-over marks on visible surfaces. Controlled feed rates and fine-finish inserts minimize tool lines, reducing post-machining polishing needs. These measures help achieve consistent gloss, matte, or textured finishes before anodizing or coating. This ensures compliance with both functional and visual product specifications.
Frigate integrates in-cycle edge conditioning and deburring routines that align with microfeature dimensions. Toolpath exit points are adjusted to prevent tear-out in slot and port features. In-machine inspection checks for edge break consistency at contact areas like USB slots or button holes. These processes eliminate manual rework while meeting user-safety and assembly-fit requirements.
Frigate relies on closed-loop feedback from tool wear monitors and part metrology sensors across long production cycles. Tool offsets auto-update based on in-process inspection feedback, ensuring minimal dimensional drift. Cpk levels are tracked in real time, and machining parameters are tuned for each lot. This allows consistent part output across high-volume runs exceeding 100,000 units.
Frigate coordinates with finishing partners to apply anodizing, conversion coatings, or electroless nickel plating on CNC-machined parts. Prior to coating, machined surfaces are polished or media blasted to match gloss level and texture specs. Fixture setups maintain critical surface flatness during processing. These steps result in coatings that meet EMI shielding, wear resistance, and brand appearance standards.
We'd love to Manufacture for you!
Submit the form below and our representative will be in touch shortly.
LOCATIONS
Registered Office
10-A, First Floor, V.V Complex, Prakash Nagar, Thiruverumbur, Trichy-620013, Tamil Nadu, India.
Operations Office
9/1, Poonthottam Nagar, Ramanandha Nagar, Saravanampatti, Coimbatore-641035, Tamil Nadu, India. ㅤ
Other Locations
- Bhilai
- Chennai
- USA
- Germany