Firearms & Defense Accessories Industry Machining Solutions
Strengthen Tactical Readiness with Frigate’s CNC-Machined Components for Optics Mounts, Frames, Barrels, and Retention Systems.
Frigate supports your firearms machining goals with Defense-Grade Capabilities
High-Tolerance Machining for Combat Precision
Maintain ±0.005 mm tolerances using multi-axis CNC equipment and repeatable process setups suited for defense-critical assemblies.
Defense-Alloy Machinability and Traceability
Work with 4140, 17-4PH, 7075-T6, and stainless grades using controlled workflows linked to DFARS and ITAR compliance norms.
Repeatability Across Serialized Components
Use CAM-driven nesting and fixed tooling references to produce serialized parts with tight feature matching across batches.
Our Clients
Trusted by Engineers and Purchasing Leaders
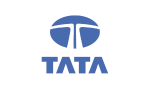
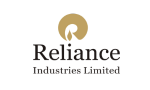


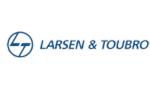
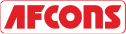


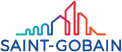

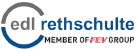

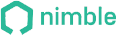
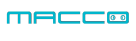









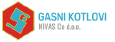
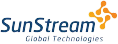

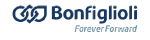


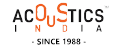
Withstand Harsh Use Cycles and High-Impact Loads in Field Conditions
Components used in tactical and defense accessories must withstand thermal cycling, mechanical shock, and constant field handling.
Media blasting and controlled burnishing help achieve matte, glare-resistant finishes and reduce particulate accumulation.
Shape engagement faces using high-strength alloys and optimize geometries for consistent contact under variable torque.
Blended transitions and radius control reduce sharp transitions around triggers, mounts, and slide components.

Adhere to Defense Industry Protocols for Quality and Documentation
Frigate’s inspection processes and documentation practices align with MIL-SPEC standards and defense-specific traceability norms.
Use CMM and profilometry to confirm engagement fitments, bore alignments, and flatness over critical mating areas.
Inspection records include serial matching, revision history, and operator credentials tied to each batch run.
Control charts, Cpk reporting, and gauge R&R ensure tolerances hold through repeat machining of defense-critical SKUs.

Maximize Functional Life with Specialized Finishes and Coatings
Surface treatments reduce wear, lower friction, and improve part resilience under rugged operational conditions.
Apply hard chrome, manganese phosphate, or Cerakote to resist abrasion on rails, bolts, and accessory rails.
Lapping, polishing, and media smoothing help reduce friction over sliding components and improve assembly response.
Under-microscope finishing removes burrs from slides, linkages, and retention interfaces without disturbing tight tolerances.

Our Machined Products
We support your production needs with CNC-machined parts, subassemblies, and performance-critical components.
- Real Impact
Words from Clients
See how global OEMs and sourcing heads describe their experience with our scalable execution.
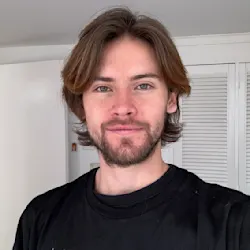
“Quick turnaround and solid quality.”
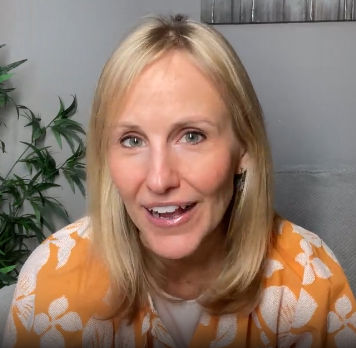
“The instant quote tool saved us time, and the parts were spot-on. Highly recommend Frigate!”
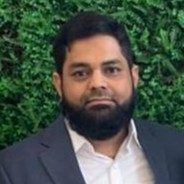
“I would strongly recommend Frigate to anyone who wants to do Rapid Prototyping, and take their ideas to manufacturing. One firm doing all kinds of Product Development!”
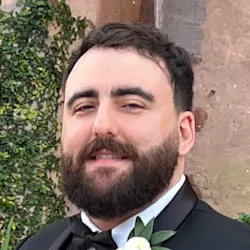
“Great service, fair price, and the parts worked perfectly in our assembly.”
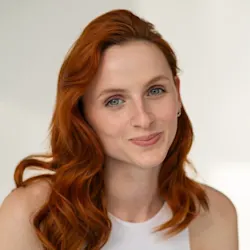
“Top-notch machining and fast shipping. Very satisfied with the results.”
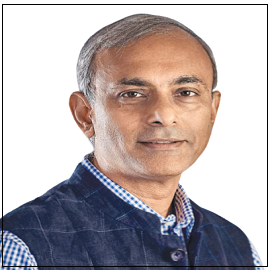
“The next disruption is happening in Prototyping & Manufacturing on-demand and Frigate is leading the way! I personally believe the Frigate's way of IIOT enabled cloud platform with Al.”
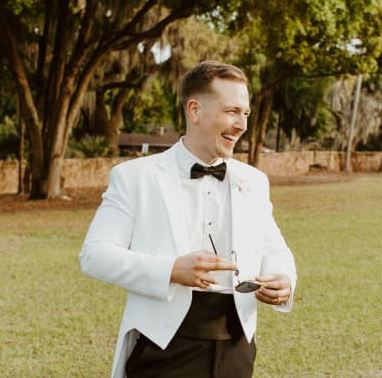
“Frigate delivered high-quality parts at a competitive price. The instant quote tool is a huge plus for us!”

“We appreciate the precision and quality of the machined components in the recent delivery—they meet our specifications perfectly and demonstrate Frigate’s capability for excellent workmanship.”
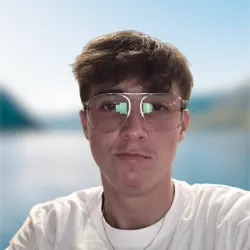
“Flawless execution from quote to delivery.”

“I am absolutely happy to work with supplier like Frigate who were quite proactive & result oriented . Frigate has high willingness team who has strong know how & their passion towards the products & process were absolutely thrilling.”
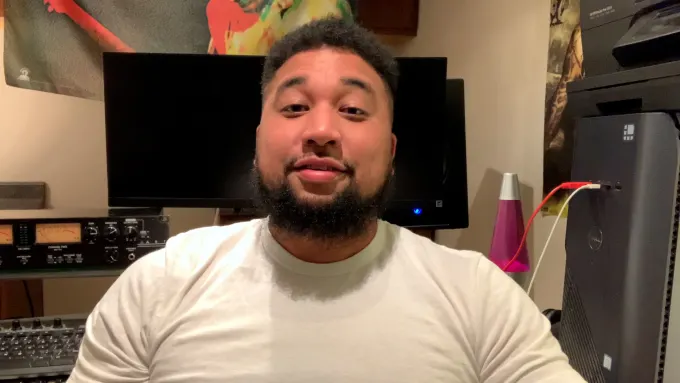
“The precision on these parts is impressive, and they arrived ahead of schedule. Frigate’s process really stands out!”
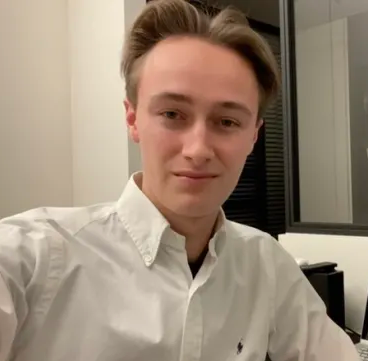
“Parts were exactly as spec’d, and the instant quote made budgeting a breeze.”
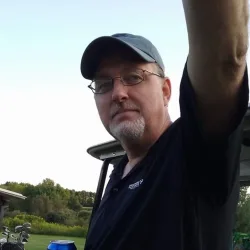
“Good value for the money.”
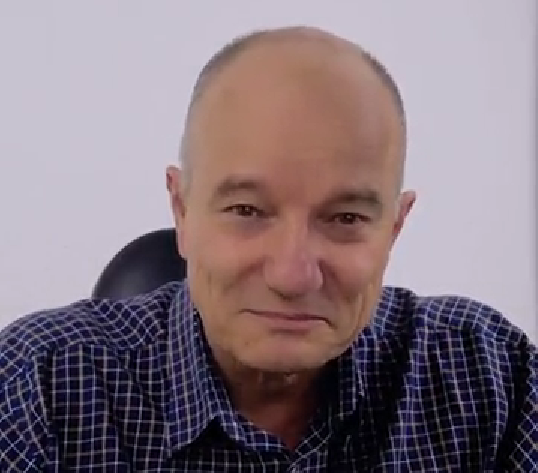
“The finish was perfect, and the team was easy to work with.”

“Working with Frigate has been great. Their proactive, results-driven approach and expertise shine through in every project. It's been a pleasure collaborating with them.”

"We are highly satisfied with the timely delivery and quality of the MIG Welding Cable from Frigate. Their attention to detail, secure packaging, and quick responsiveness stood out. We confidently recommend Frigate Engineering Services Pvt. Ltd. as a reliable manufacturing partner."
- We export to 12+ countries
Frigate’s Global Presence
Frigate takes pride in facilitating “Make in India for the globe“. As our global network of Frigaters provides virtually limitless capacity, and through our IoT enabled platform your parts go directly into production. By digitally and technologically enabling “the silent pillars of the economy” MSME and SME manufacturing industries, we are able to tap the huge potential for manufacturing to bring the best results for our clients.

100,000+
Parts Manufactured
250+
Frigaters
2000+
Machines
450+
Materials
25+
Manufacturing Process
- Solid Progress
How You Benefit with Us
Frigate brings stability, control, and predictable performance to your sourcing operations through a structured multi-vendor system.
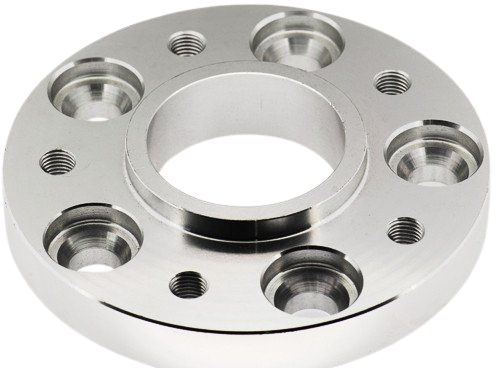
2.8X
Sourcing Cycle Speed
Frigate’s pre-qualified network shortens decision time between RFQ and PO placement.
94%
On-Time Delivery Rate
Structured planning windows and logistics-linked schedules improve project-level delivery reliability.
4X
Multi-Part Consolidation
We enable part family batching across suppliers to reduce fragmentation.
22%
Quality Rejection Rate
Multi-level quality checks and fixed inspection plans lower non-conformities.
30%
Procurement Costs
Optimized supplier negotiations and bulk order strategies reduce your overall sourcing expenses.
20%
Manual Processing Time
Automation of sourcing and supplier management significantly reduces time spent on manual tasks.
Other Industries We Serve
We deliver machining support across sectors that require consistency, material reliability, and tight dimensional control.
Get Clarity with Our Manufacturing Insights
Frigate applies balanced toolpath strategies and constant feed rate control to reduce internal stress during CNC machining. Each mount undergoes pre-machining stress relief and post-machining stabilization to maintain shape under field recoil. Tolerance consistency is verified through CMM checks at stress-bearing points such as dovetail interfaces and locking profiles. This ensures that all mounts retain zero-movement alignment under repeated discharge.
Frigate uses manganese phosphate and Cerakote coatings over hardened surfaces to reduce friction and prevent galling. Before coating, all parts are surface-prepped using media blasting and controlled roughening to support coating adhesion. High-contact zones like rails, bolt carriers, and mounting plates are profiled with repeatable geometry. This combination ensures stable wear patterns during cyclic use.
Frigate uses CAM-linked feature referencing and fixed tooling offsets to eliminate drift across serialized runs. Every part shares a digital master reference to maintain feature alignment and thread positioning. In-process inspections log tool wear trends and batch-wise dimensional variation. This controls quality for serialized components such as trigger assemblies, scope mounts, and modular chassis plates.
Frigate uses contact and non-contact metrology systems to verify bore concentricity, thread class, and external diameter profiles. Laser profilometry and CMM scans ensure concentric alignment between locking lugs, threads, and barrel shoulders. Results are cross-checked with 3D model overlays to flag deviations beyond tolerance. This maintains engagement accuracy in critical locking areas.
Frigate uses high-feed carbide tooling and chip evacuation strategies to manage thermal loads while machining dense alloys. Coolant flow is optimized using high-pressure delivery through tool centers for better temperature control. Toolpaths are adjusted to minimize radial load and reduce burr formation at slot edges and undercuts. This enables reliable machining of firing control housings, optic rail bases, and safety-critical parts.
We'd love to Manufacture for you!
Submit the form below and our representative will be in touch shortly.
LOCATIONS
Registered Office
10-A, First Floor, V.V Complex, Prakash Nagar, Thiruverumbur, Trichy-620013, Tamil Nadu, India.
Operations Office
9/1, Poonthottam Nagar, Ramanandha Nagar, Saravanampatti, Coimbatore-641035, Tamil Nadu, India. ㅤ
Other Locations
- Bhilai
- Chennai
- USA
- Germany