High-Tolerance Manufacturing for Railway Load-Bearing Components
Frigate produces micron-accurate parts engineered for extreme fatigue, thermal shifts, and multi-axis dynamic loading in railway applications.
Frigate Enables Digital Rail Production Systems
Traceability Backbone
Frigate links microstructure, dimensions, and heat data to digital IDs, enabling audit-ready genealogy for fleet, ESG, and compliance assurance.
Zero Drift Interfaces
Closed-loop machining with AI-corrected toolpaths maintains sub-50μm tolerances for safety-critical parts across large-scale production volumes.
Digital Homologation
Simulation-integrated prototyping ensures compliance with global rail standards and accelerates approvals with documentation packages aligned to OEM specs.
Our Clients
Trusted by Engineers and Purchasing Leaders
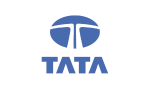
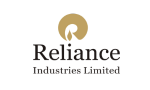


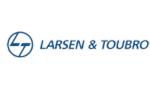
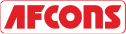


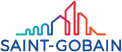

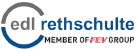

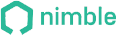
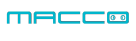









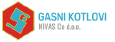
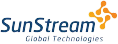

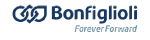


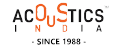
Enable Predictive Quality with Spectral and Statistical Intelligence
Ensuring first-pass yield and reducing NCRs at volume requires predictive QA built on real-time data and in-process spectral insights.
Deploy inline LIBS and XRF to detect alloy phase shifts and chemical deviations before they reach final inspection, eliminating latent material defects.
Integrate robotic 3D scanning arms on the shop floor for real-time geometry clustering and immediate feedback into the machining loop.
Use multivariate SPC to generate dimensional drift alerts when process variation exceeds ±3σ, enabling corrective action before failure thresholds.
Tie supplier quality modules directly into customer MES/QMS systems, triggering live alerts and digital tracebacks for nonconformance events.

Achieve JIT Fulfillment with Field-Ready Component Kitting
Supporting depot overhauls and system rollouts demands synchronized production and deployment logistics tailored to fleet maintenance cycles and program phasing.
Analyze historical fleet data to model wear-prone component lifespans, enabling preemptive production scheduling and batch optimization.
Package replacement systems with serialized BOMs and grouped assemblies, ready for direct install at depots or field service stations.
Generate advanced shipment notifications (ASNs) with API-based sync to client ERP systems, supporting inventory visibility and delivery coordination.
Maintain bonded warehouse hubs near key rail corridors for sub-24-hour deployment of mission-critical parts during outages or emergencies.

Deliver Multi-Standard Compliance with Digital Manufacturing Control
Navigating AAR, EN, and regional rail certifications requires synchronized QA, engineering, and documentation processes purpose-built for multi-standard programs.
Combine PPAP, IRIS, EN15085, and internal QMS checkpoints into a unified, digitally traceable process with revision-controlled audit logs.
Engineer components with dual-compliance metallurgical profiles suited for both European and U.S. rail applications, minimizing revalidation costs.
Auto-generate certificates for welders, NDT procedures, material traceability, and dimensional conformance as part of final part release.
Deliver qualification-ready digital dossiers including FAI, CPK reports, and design compliance records for fast-track supplier onboarding.

Our Machined Products
We support your production needs with CNC-machined parts, subassemblies, and performance-critical components.
- Real Impact
Words from Clients
See how global OEMs and sourcing heads describe their experience with our scalable execution.
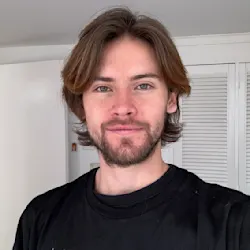
“Quick turnaround and solid quality.”
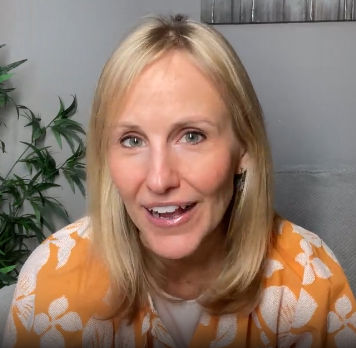
“The instant quote tool saved us time, and the parts were spot-on. Highly recommend Frigate!”
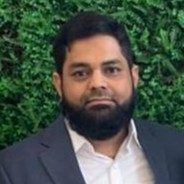
“I would strongly recommend Frigate to anyone who wants to do Rapid Prototyping, and take their ideas to manufacturing. One firm doing all kinds of Product Development!”
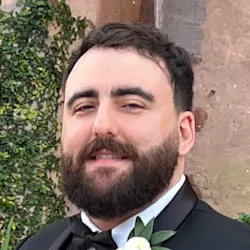
“Great service, fair price, and the parts worked perfectly in our assembly.”
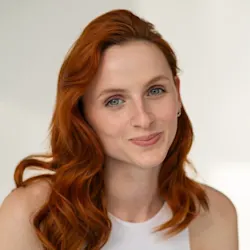
“Top-notch machining and fast shipping. Very satisfied with the results.”
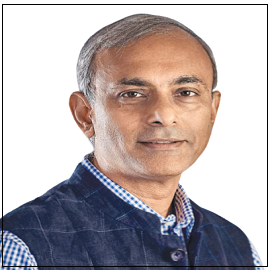
“The next disruption is happening in Prototyping & Manufacturing on-demand and Frigate is leading the way! I personally believe the Frigate's way of IIOT enabled cloud platform with Al.”
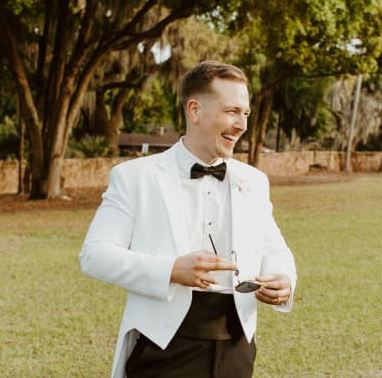
“Frigate delivered high-quality parts at a competitive price. The instant quote tool is a huge plus for us!”

“We appreciate the precision and quality of the machined components in the recent delivery—they meet our specifications perfectly and demonstrate Frigate’s capability for excellent workmanship.”
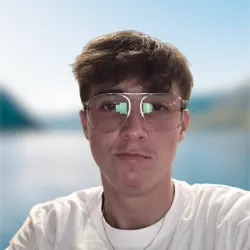
“Flawless execution from quote to delivery.”

“I am absolutely happy to work with supplier like Frigate who were quite proactive & result oriented . Frigate has high willingness team who has strong know how & their passion towards the products & process were absolutely thrilling.”
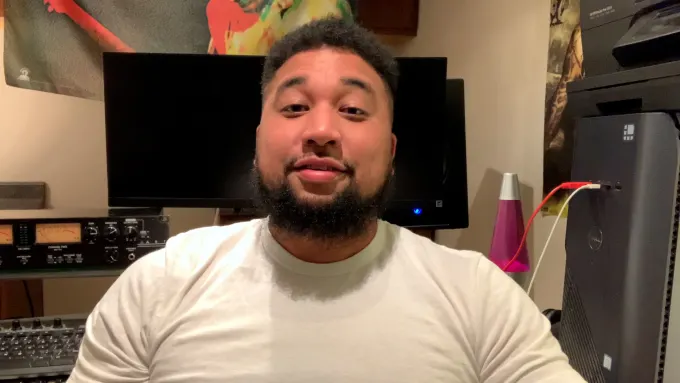
“The precision on these parts is impressive, and they arrived ahead of schedule. Frigate’s process really stands out!”
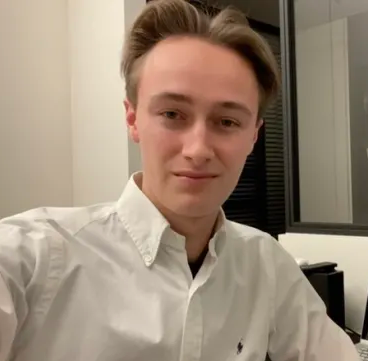
“Parts were exactly as spec’d, and the instant quote made budgeting a breeze.”
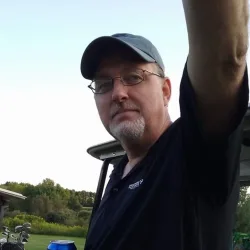
“Good value for the money.”
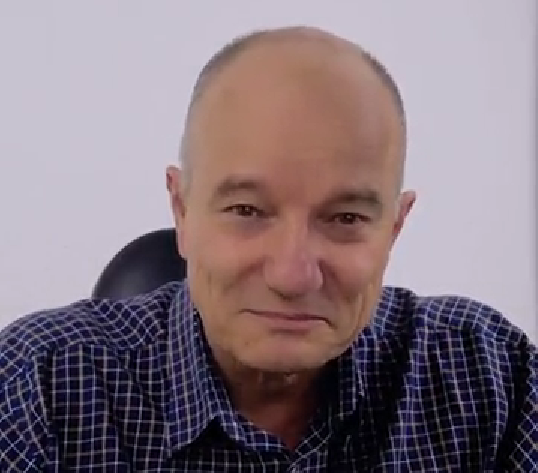
“The finish was perfect, and the team was easy to work with.”

“Working with Frigate has been great. Their proactive, results-driven approach and expertise shine through in every project. It's been a pleasure collaborating with them.”

"We are highly satisfied with the timely delivery and quality of the MIG Welding Cable from Frigate. Their attention to detail, secure packaging, and quick responsiveness stood out. We confidently recommend Frigate Engineering Services Pvt. Ltd. as a reliable manufacturing partner."
- We export to 12+ countries
Frigate’s Global Presence
Frigate takes pride in facilitating “Make in India for the globe“. As our global network of Frigaters provides virtually limitless capacity, and through our IoT enabled platform your parts go directly into production. By digitally and technologically enabling “the silent pillars of the economy” MSME and SME manufacturing industries, we are able to tap the huge potential for manufacturing to bring the best results for our clients.

100,000+
Parts Manufactured
250+
Frigaters
2000+
Machines
450+
Materials
25+
Manufacturing Process
- Solid Progress
How You Benefit with Us
Frigate brings stability, control, and predictable performance to your sourcing operations through a structured multi-vendor system.
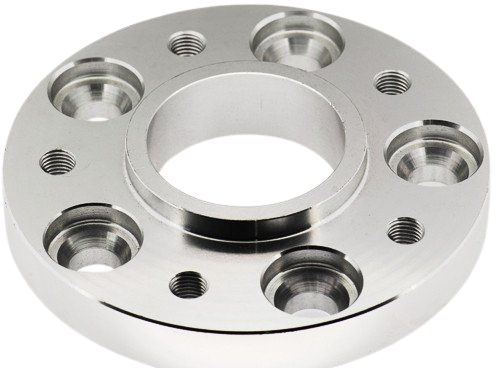
2.8X
Sourcing Cycle Speed
Frigate’s pre-qualified network shortens decision time between RFQ and PO placement.
94%
On-Time Delivery Rate
Structured planning windows and logistics-linked schedules improve project-level delivery reliability.
4X
Multi-Part Consolidation
We enable part family batching across suppliers to reduce fragmentation.
22%
Quality Rejection Rate
Multi-level quality checks and fixed inspection plans lower non-conformities.
30%
Procurement Costs
Optimized supplier negotiations and bulk order strategies reduce your overall sourcing expenses.
20%
Manual Processing Time
Automation of sourcing and supplier management significantly reduces time spent on manual tasks.
Other Industries We Serve
We deliver machining support across sectors that require consistency, material reliability, and tight dimensional control.
Get Clarity with our Manufacturing Insights
Frigate uses a combination of real-time spectroscopic analysis and high-resolution metallography to ensure the internal quality of each forged part. Right after forging, Laser-Induced Breakdown Spectroscopy (LIBS) and X-ray Fluorescence (XRF) are applied inline to verify alloy consistency down to trace elements. We also cut and examine cross-sections of random samples under 500x magnification to analyze grain flow, detect non-metallic inclusions, and validate the uniformity of phase distribution (such as ferrite, pearlite, bainite, etc.).
Yes. Frigate machines complex, asymmetric parts—like bogie crossbeams, coupler arms, and draft gear supports—using 5-axis CNC systems equipped with sub-micron thermal compensation software. These machines are fitted with sensors that monitor spindle temperature, ambient conditions, and part deformation in real time. When thermal changes are detected, the system adjusts the toolpath dynamically to hold critical features within ±10 microns. For highly sensitive zones, pre-stress clamping techniques and low-heat tool strategies are used to reduce residual stress.
Frigate relies on predictive quality systems, not just final inspections. During high-volume runs, every CNC cell feeds data into a centralized Statistical Process Control (SPC) engine that tracks tool wear, cutting force, and dimensional drift. When the system detects trends that exceed 3-sigma control limits, automatic tool recalibration or process pauses are triggered before any out-of-spec parts are made. Frigate also uses machine learning algorithms trained on historical defect patterns to anticipate failure modes before they occur.
Frigate designs every production workflow to align with dual certification requirements, especially for customers operating in both North America and Europe. Material selection, forging, welding, and machining are all done in accordance with both AAR M-1003 and EN 15085 Class 1 requirements. Each batch is supplied with automated documentation packages that include material certificates, weld qualifications (WPS/PQR/WPQ), dimensional inspection reports, and NDT logs. Welders and quality inspectors are trained and certified under both regulatory frameworks.
For large-scale or geometrically complex parts—such as side frames, traction brackets, or bolsters—Frigate uses robotic 3D metrology systems deployed right on the shop floor. These arms perform high-resolution surface scans using laser triangulation and structured light, capturing millions of data points per part. The scans are instantly compared to the original CAD model using AI-based geometric clustering, which flags even minor deformation or contour drift that traditional CMMs or gauges might miss. This system works in parallel with the machining cycle, reducing downtime and eliminating the need for post-process rework.
We'd love to Manufacture for you!
Submit the form below and our representative will be in touch shortly.
LOCATIONS
Global Sales Office
818, Preakness lane, Coppell, Texas, USA – 75019
Registered Office
10-A, First Floor, V.V Complex, Prakash Nagar, Thiruverumbur, Trichy-620013, Tamil Nadu, India.
Operations Office
9/1, Poonthottam Nagar, Ramanandha Nagar, Saravanampatti, Coimbatore-641035, Tamil Nadu, India. ㅤ
Other Locations
- Bhilai
- Chennai
- Texas, USA