- Rapid Manufacturing
CNC Machining Services in Italy
We reduce machining-induced residual stresses through dynamic toolpath optimization and controlled material engagement strategies. Upload your CAD file to get an instant quote and complete your order in just 5 minutes.
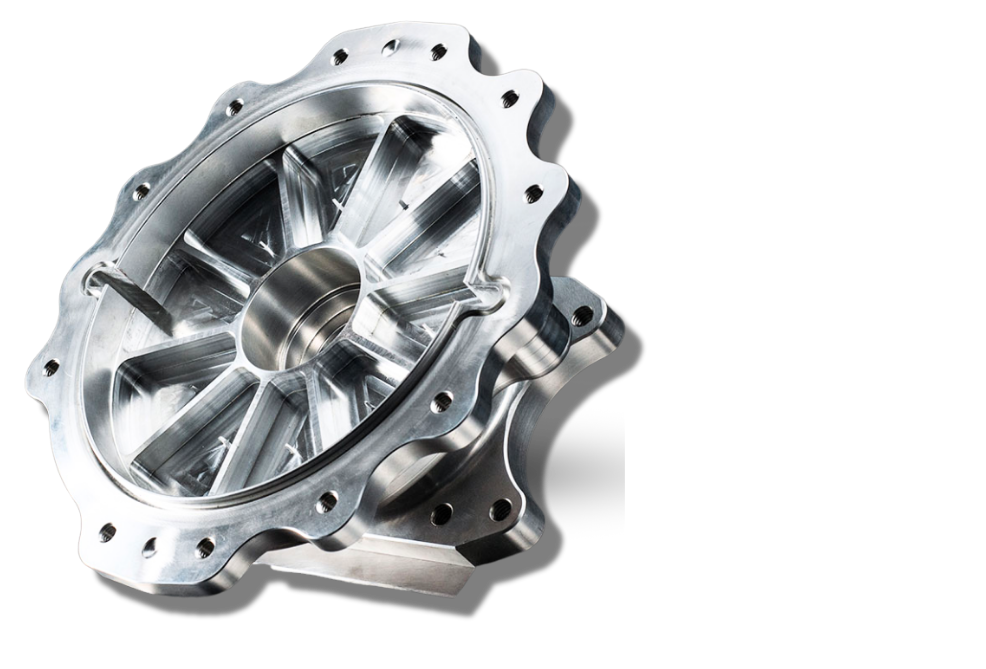
Our Clients
Trusted by Engineers and Purchasing Leaders
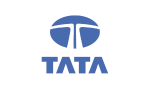
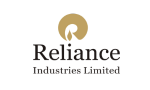


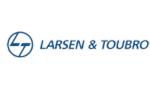
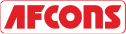


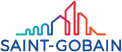

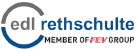

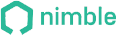
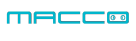









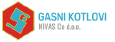
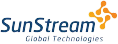

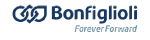


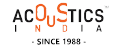
- Instant Quotes
Quote in Seconds - Parts in Days
We employ hydrostatic guideways and vibration-dampened tool holders to maintain micron-level precision across large-batch runs. Rapid fixture reconfiguration supports fast changeovers and reliable delivery within 7 days.
- Get instant quotes
- Get instant DFM feedback
- Online quote and order management
- Project Management
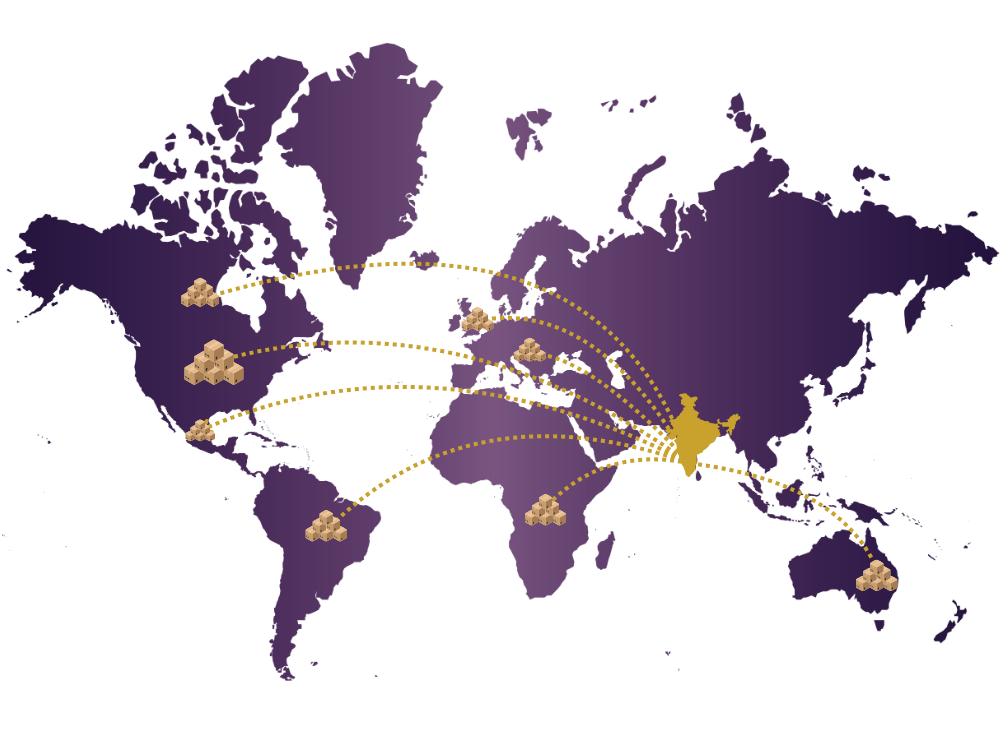
- Our Services
Online CNC Machining Service in Italy
Get high-precision CNC machined parts online with fast turnaround and cost-effective pricing.
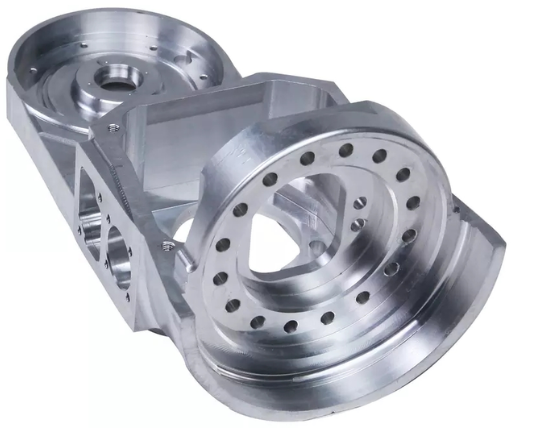
CNC Milling
Micro-feature machining applies direct-drive axes, rigid frames, and sub-micron interpolation for high aspect ratio accuracy.
- Handle tough materials with spindle power up to 30 kW
- Free design feedback with every quote
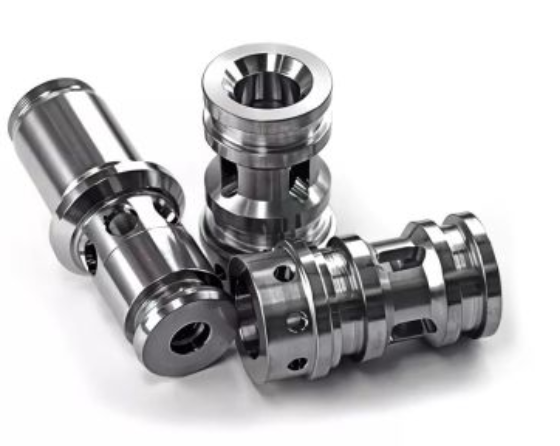
CNC Turning
5-axis contour milling utilizes RTCP (Rotational Tool Center Point), collision-avoidance software, and full-surface engagement for sculpted geometries with no manual rework.
- Complex cylindrical parts up to ⌀500mm
- Bar feeding feature for faster, continuous production
- Surface Finish
Flawless Finishes for CNC Machining Parts in Italy
We use advanced nitriding and duplex hardening to refine surface hardness while providing a uniform, wear-resistant finish.
Anodizing
Give your aluminum parts a tough, corrosion-resistant shield with anodizing, reaching surface hardness up to HV 500, while enhancing electrical insulation and durability.
Mechanical Finishing
Smooth out imperfections and refine surfaces to Ra 0.2 µm or better with mechanical finishing techniques like grinding, polishing, and bead blasting.
Heat Treatment
Boost material strength and hardness by heat treating parts at temperatures up to 1100°C, ensuring they meet the mechanical demands of your application.
Electroplating
Add protective or functional metal coatings with electroplating, delivering consistent layers as precise as ±2 µm for improved corrosion resistance and conductivity.
- Real Impact
Words from Clients
See how global OEMs and sourcing heads describe their experience with our scalable execution.
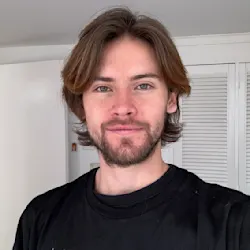
“Quick turnaround and solid quality.”
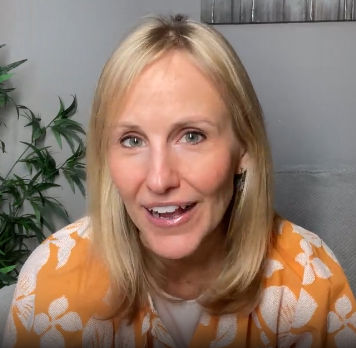
“The instant quote tool saved us time, and the parts were spot-on. Highly recommend Frigate!”
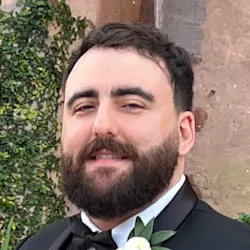
“Great service, fair price, and the parts worked perfectly in our assembly.”
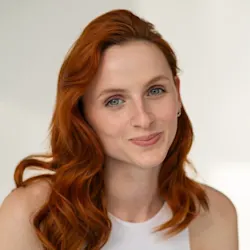
“Top-notch machining and fast shipping. Very satisfied with the results.”
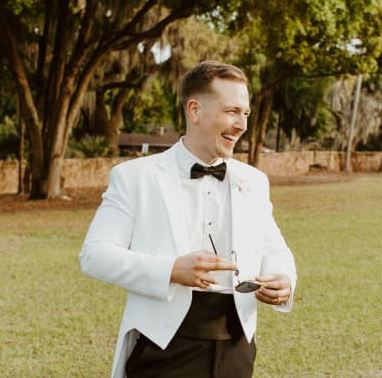
“Frigate delivered high-quality parts at a competitive price. The instant quote tool is a huge plus for us!”

“We appreciate the precision and quality of the machined components in the recent delivery—they meet our specifications perfectly and demonstrate Frigate’s capability for excellent workmanship.”
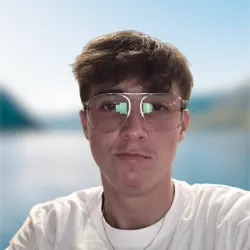
“Flawless execution from quote to delivery.”
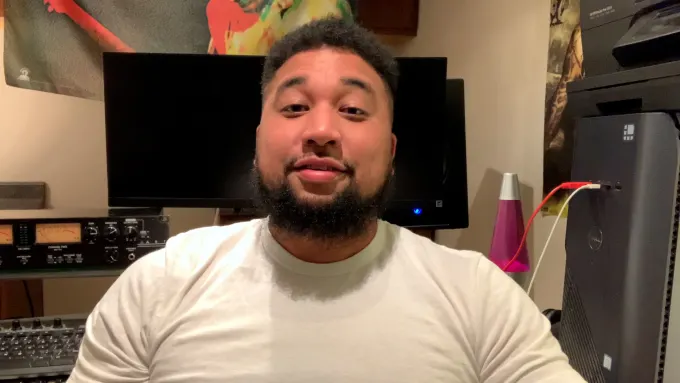
“The precision on these parts is impressive, and they arrived ahead of schedule. Frigate’s process really stands out!”
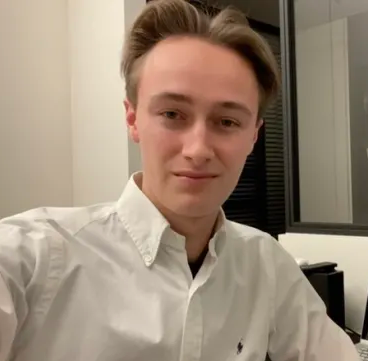
“Parts were exactly as spec’d, and the instant quote made budgeting a breeze.”
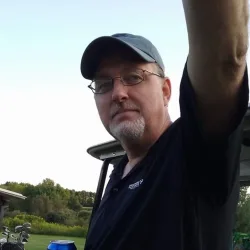
“Good value for the money.”
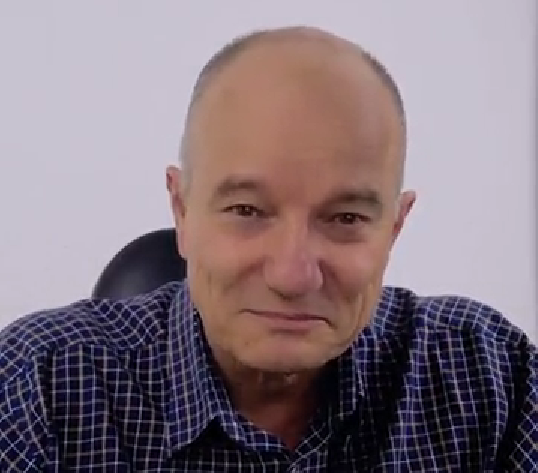
“The finish was perfect, and the team was easy to work with.”
- We export to 12+ countries
Frigate’s Global Presence
Frigate takes pride in facilitating “Make in India for the globe“. As our global network of Frigaters provides virtually limitless capacity, and through our IoT enabled platform your parts go directly into production. By digitally and technologically enabling “the silent pillars of the economy” MSME and SME manufacturing industries, we are able to tap the huge potential for manufacturing to bring the best results for our clients.

100,000+
Parts Manufactured
250+
Frigaters
2000+
Machines
450+
Materials
25+
Manufacturing Process
- Transparent Pricing
Instant Online Quote for CNC Machining Services
Our instant quoting platform applies thermal-mechanical models to dynamically evaluate heat generation and residual stress impacts. This ensures accurate pricing for tight-tolerance parts with minimal distortion, delivered in real time.
- Price updates are made in real time as you change materials, machining methods, etc.
- No hidden costs. Our instant quotes are not just indications but the actual price and include shipping and customs up front.

- Quote to Delivery
Quick and Clear Steps to Your Order
Everything moves smoothly from pricing to shipment, so you get high-quality parts without delays.
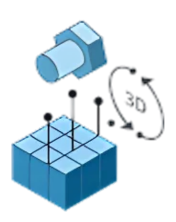
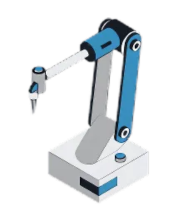
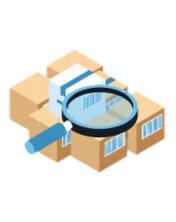
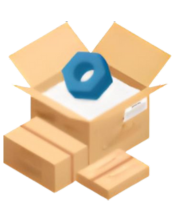
Upload CAD File
Obtain a precise and competitive quote instantly to empower your decision-making.
- Detailed cost breakdown
- Various materials and finish choices
- Market-driven unbeatable pricing
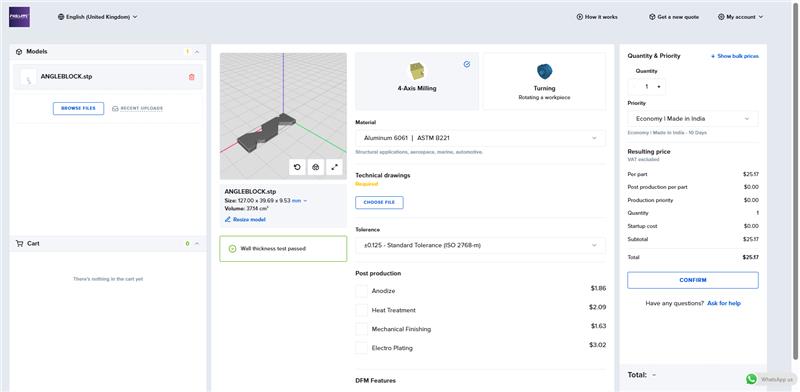
Manufacturing Begins
Transform your designs into reality with our state-of-the-art CNC production capabilities.
- Advanced machinery
- Scalable production support
- Live updates from the production floor
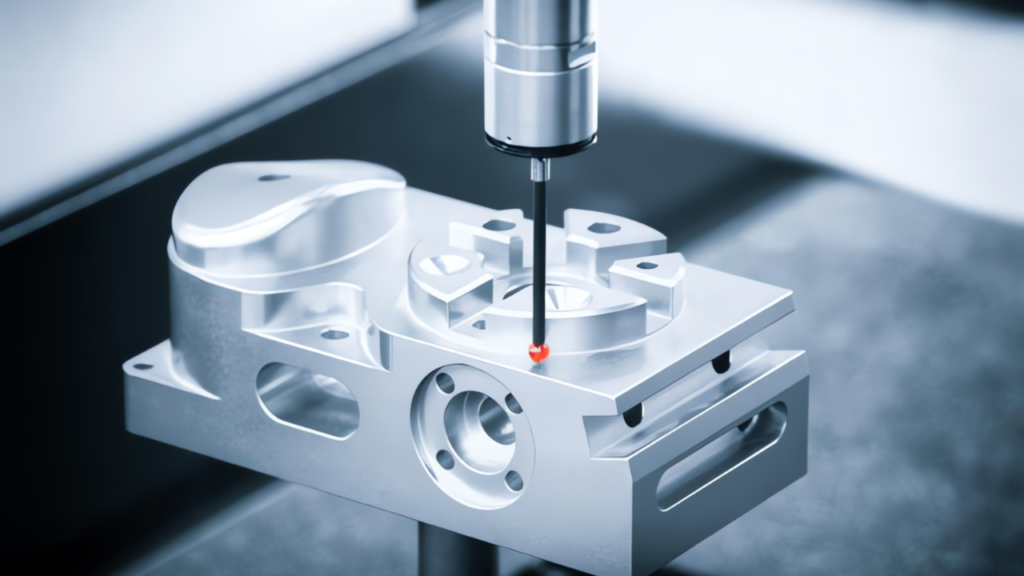
Thorough Inspection
Each part is checked to match exact specifications before moving forward.
- High-tech dimensional verification
- Surface finishing and coating checks
- Batch-wise documentation
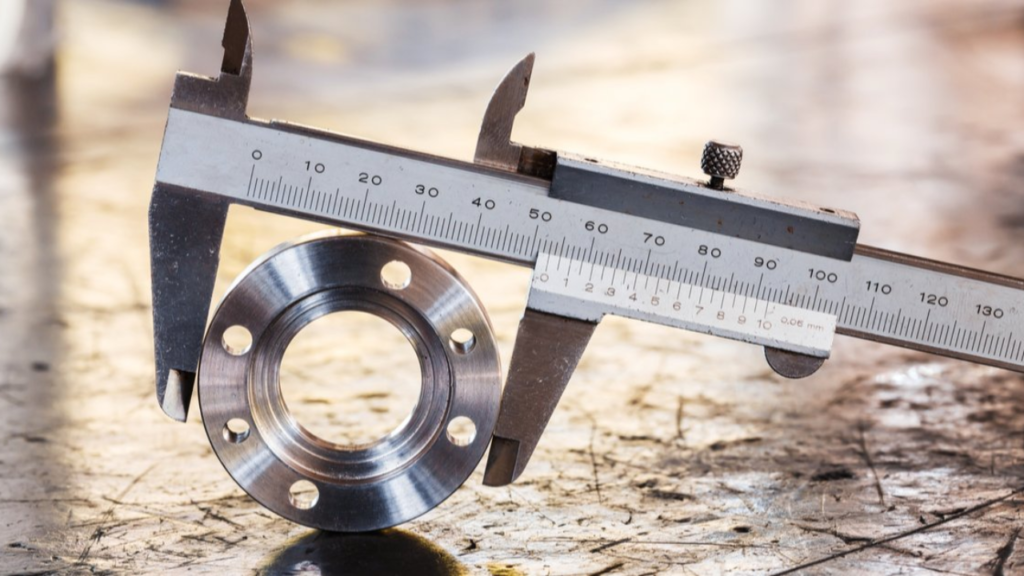
Safe & Timely Dispatch
Receive your machined parts promptly and in perfect condition.
- Multiple shipping options
- Secure packaging
- Real-time tracking during every transit
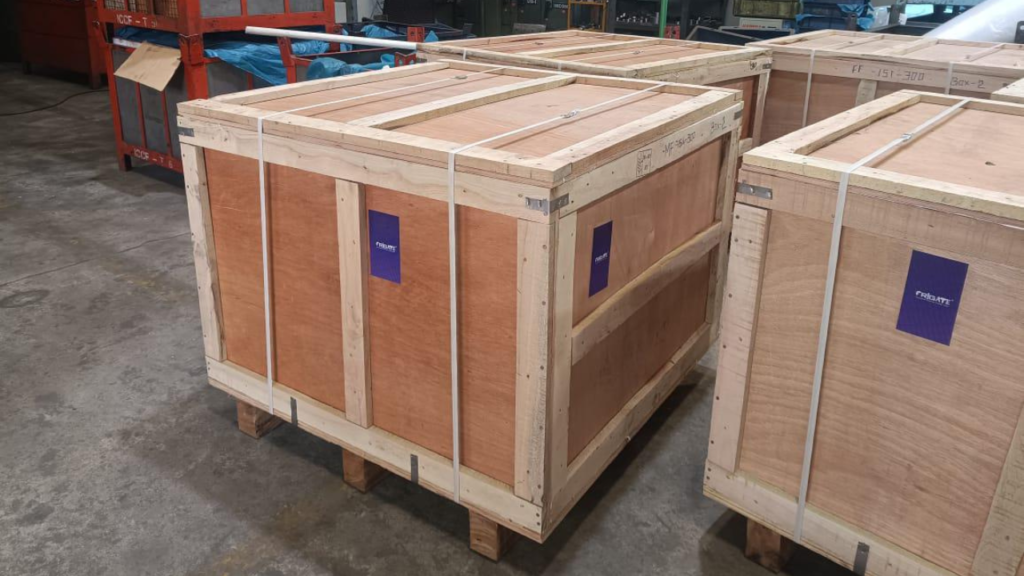
- Machining Materials
Different Materials for CNC Machining
The system employs multi-physics simulation to predict deformation and tool deflection under variable loads. This enables precise calibration of feed rates and spindle speeds, enhancing part consistency and surface quality.
Aluminum 6061
- Density - 2.7 g/cm³
- Tensile Strength - 310 MPa
- Yield Strength - 276 MPa
- Hardness (Brinell) - 95 HB
- Excellent corrosion resistance, good machinability, and heat treatable
Used in aerospace, automotive, and electronics for components like aircraft structures, bicycle frames, and heat sinks due to its lightweight and strength.
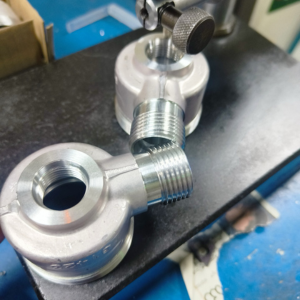
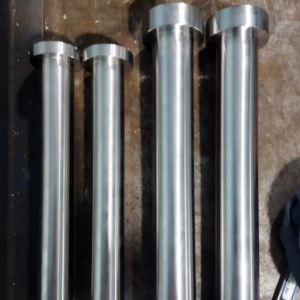
Aluminum 7075
- Density - 2.81 g/cm³
- Tensile Strength - 572 MPa
- Yield Strength - 503 MPa
- Hardness (Brinell) - 150 HB
- High fatigue resistance but limited weldability
Commonly used in aerospace, defense, and sporting goods for aircraft wings, firearm components, and high-performance bicycle parts requiring high strength.
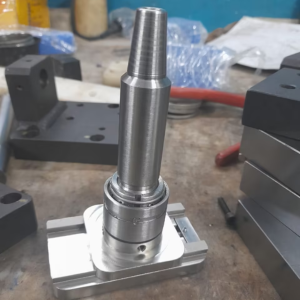

Aluminum 7050
- Density - 2.81 g/cm³
- Tensile Strength - 572 MPa
- Yield Strength - 503 MPa
- Hardness (Brinell) - 150 HB
- High fatigue resistance but limited weldability
Commonly used in aerospace, defense, and sporting goods for aircraft wings, firearm components, and high-performance bicycle parts requiring high strength.
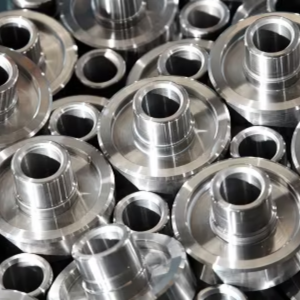

Stainless Steel 304
- Density - 8.0 g/cm³
- Tensile Strength - 515 MPa
- Yield Strength - 205 MPa
- Hardness (Brinell) - 201 HB
- High corrosion resistance, non-magnetic, and good formability
Preferred in food processing, medical, and chemical industries for tanks, surgical tools, and piping systems due to its hygiene and corrosion resistance.

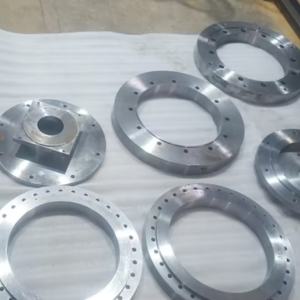
Stainless Steel 440 - Carbon
- Density - 7.8 g/cm³
- Tensile Strength - 760 MPa
- Yield Strength - 450 MPa
- Hardness (Rockwell C) - 56-60 HRC
- High hardness, excellent wear resistance, and corrosion resistance
Used in cutting tools, bearings, valves, and surgical instruments where extreme hardness and durability are required.
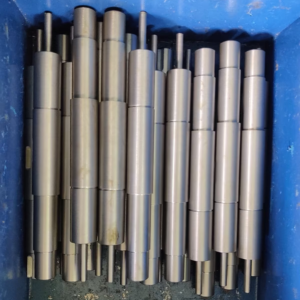
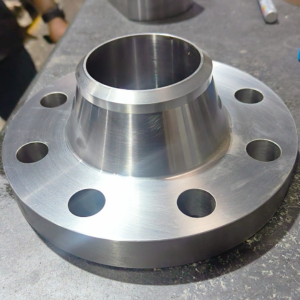
Stainless Steel 416
- Density - 7.7 g/cm³
- Tensile Strength - 585 MPa
- Yield Strength - 275 MPa
- Hardness (Brinell) - 262 HB
- Free-machining stainless steel with good strength
Ideal for automotive, firearms, and industrial applications, including gears, bolts, and shafts requiring high machinability.

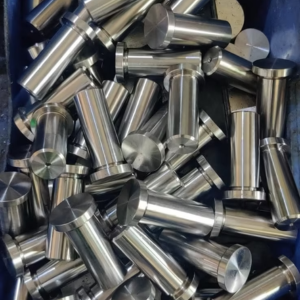
Steel 1018
- Density - 7.87 g/cm³
- Tensile Strength - 440 MPa
- Yield Strength - 370 MPa
- Hardness (Brinell) - 126 HB
- Excellent weldability and machinability
Used in automotive, machinery, and construction for shafts, pins, and fasteners where moderate strength and cost efficiency are key.

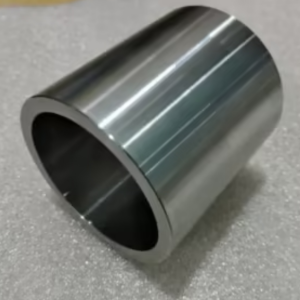
Steel 4140
- Density - 7.85 g/cm³
- Tensile Strength - 655 MPa
- Yield Strength - 415 MPa
- Hardness (Rockwell C) - 28-32 HRC
- High strength, toughness, and wear resistance
Widely used in oil & gas, aerospace, and automotive for gears, crankshafts, axles, and high-load machine components requiring extreme durability.
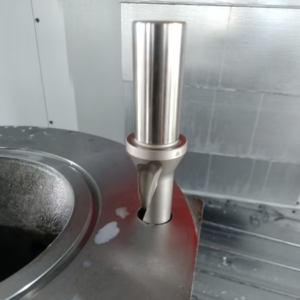
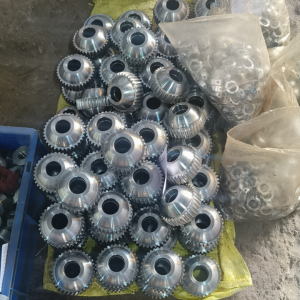
- CNC Machining Parts
CNC Machining Parts in Italy
We achieve ultra-precise machining with air-bearing spindles up to 60,000 RPM, collision avoidance, and backlash-free ball screws <0.1 µm. Browse our latest high-accuracy components built for performance.
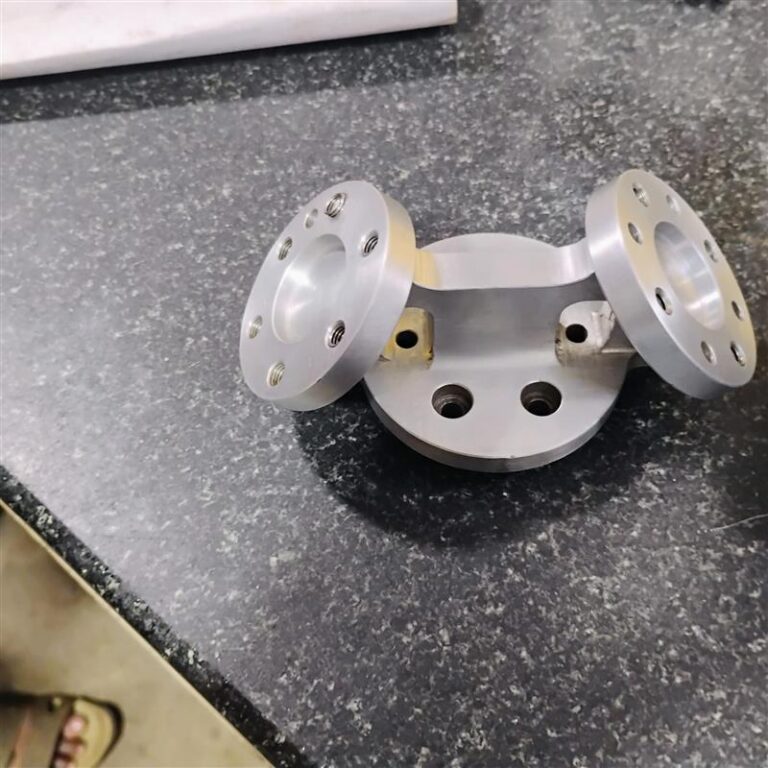
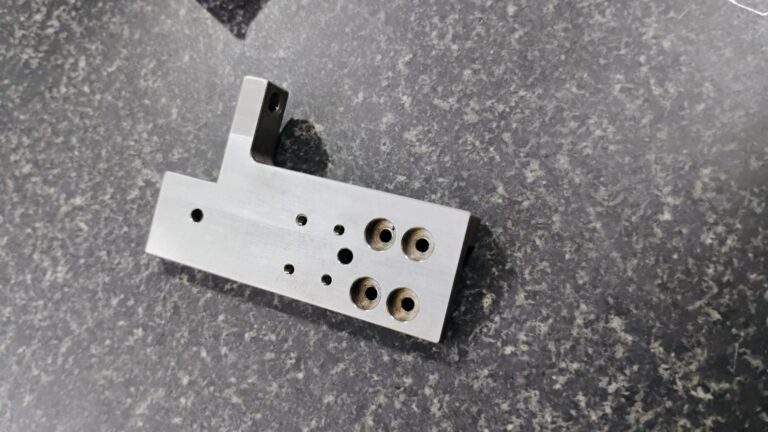
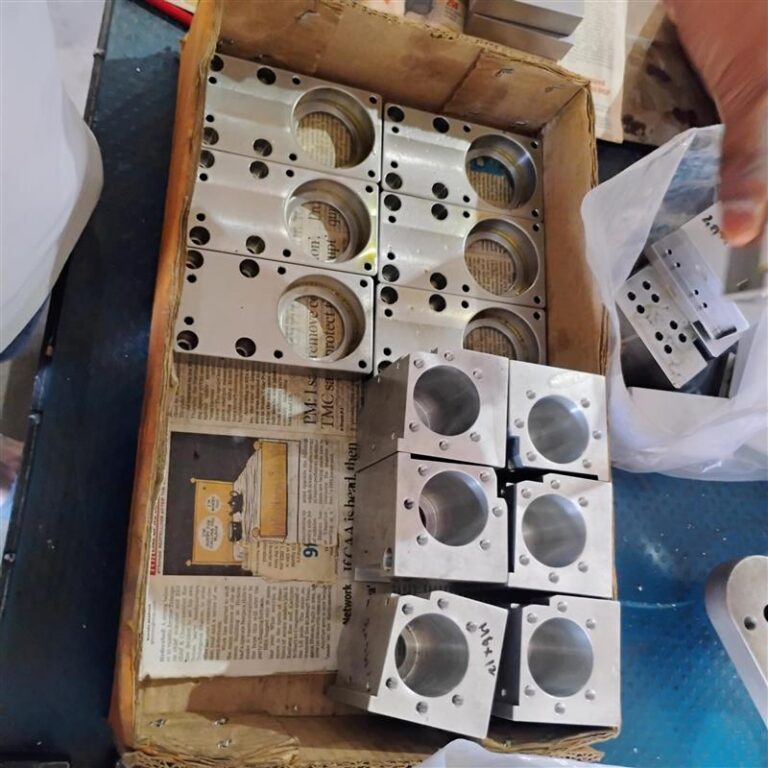
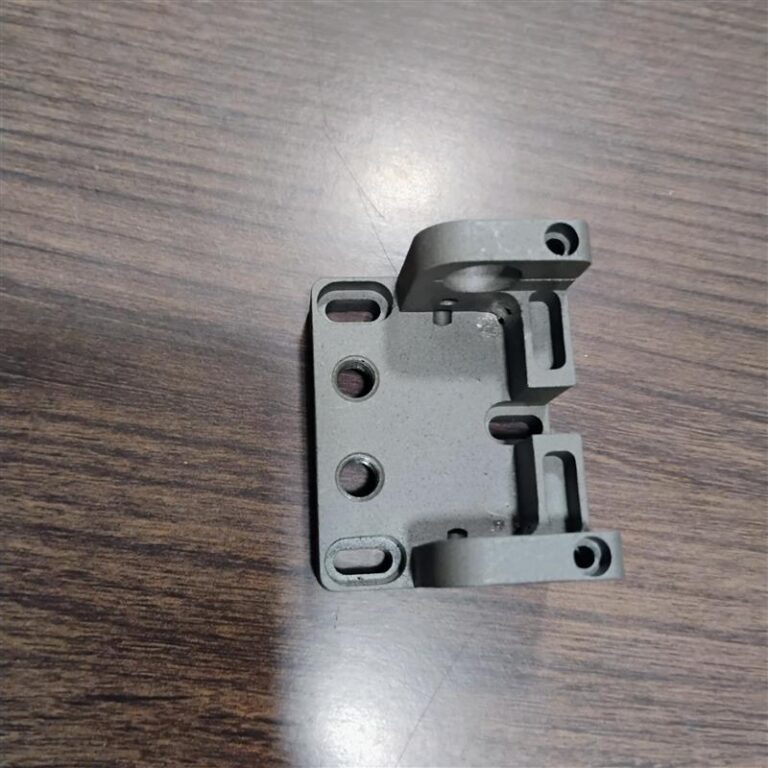
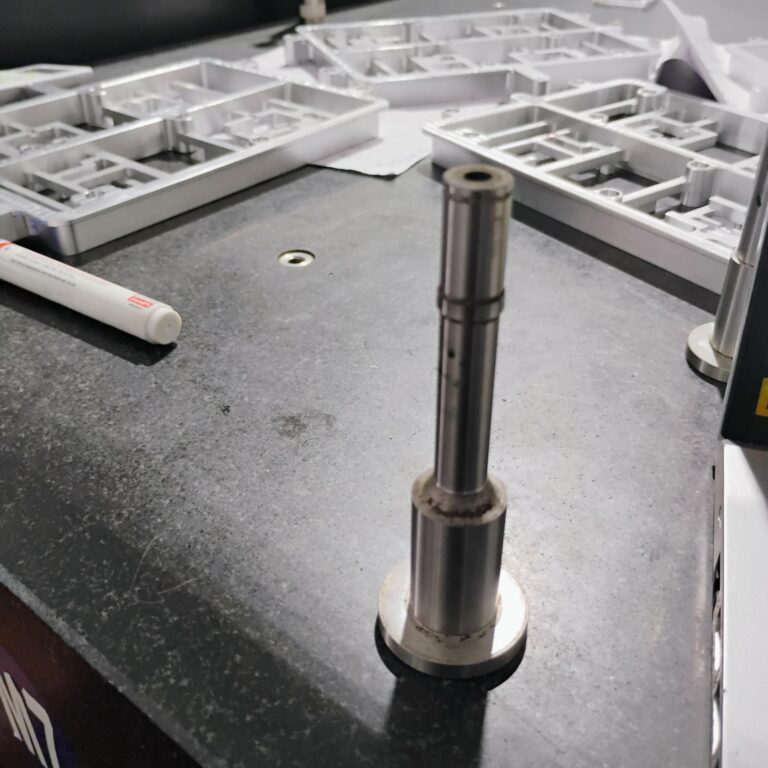
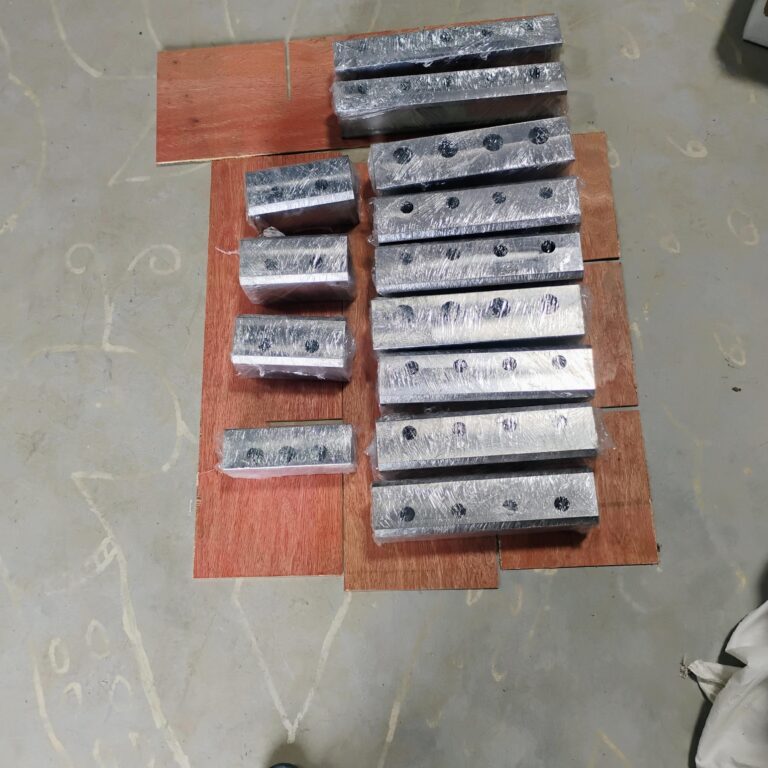
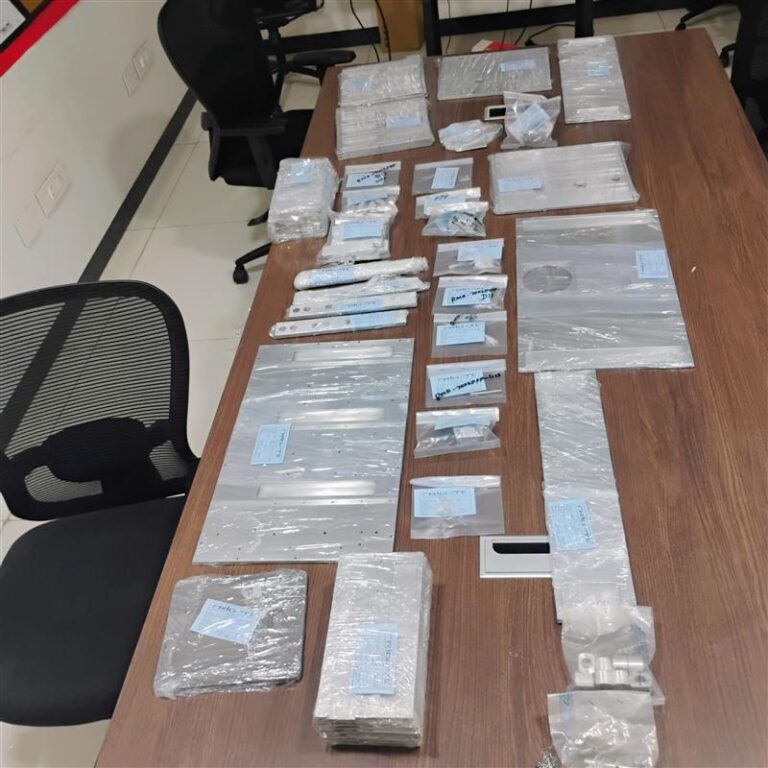

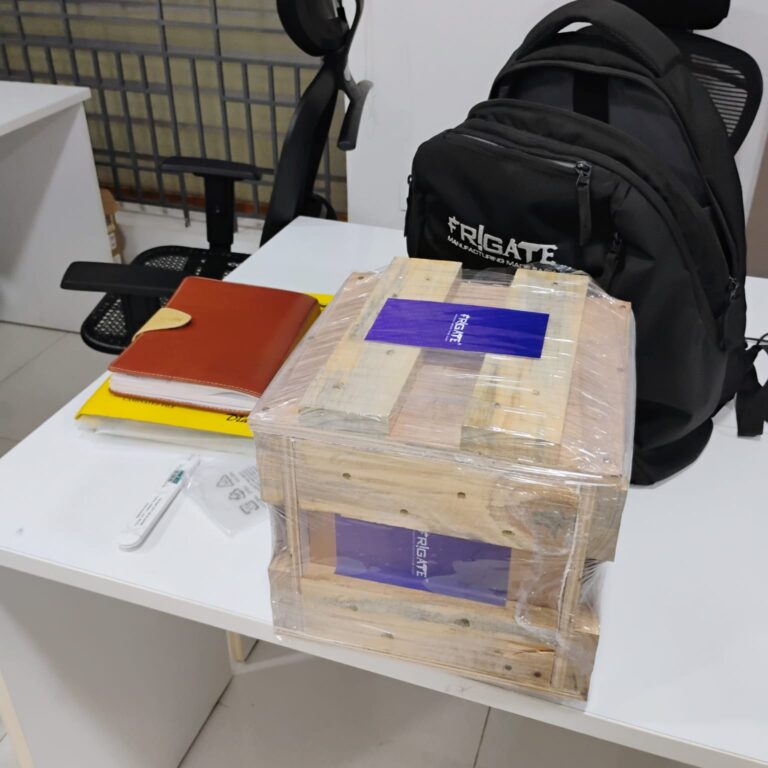


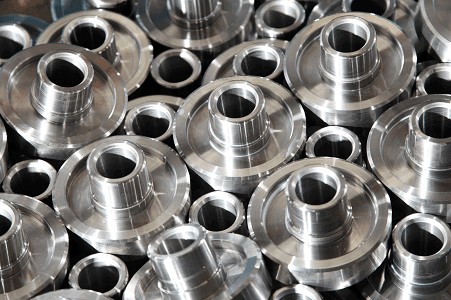
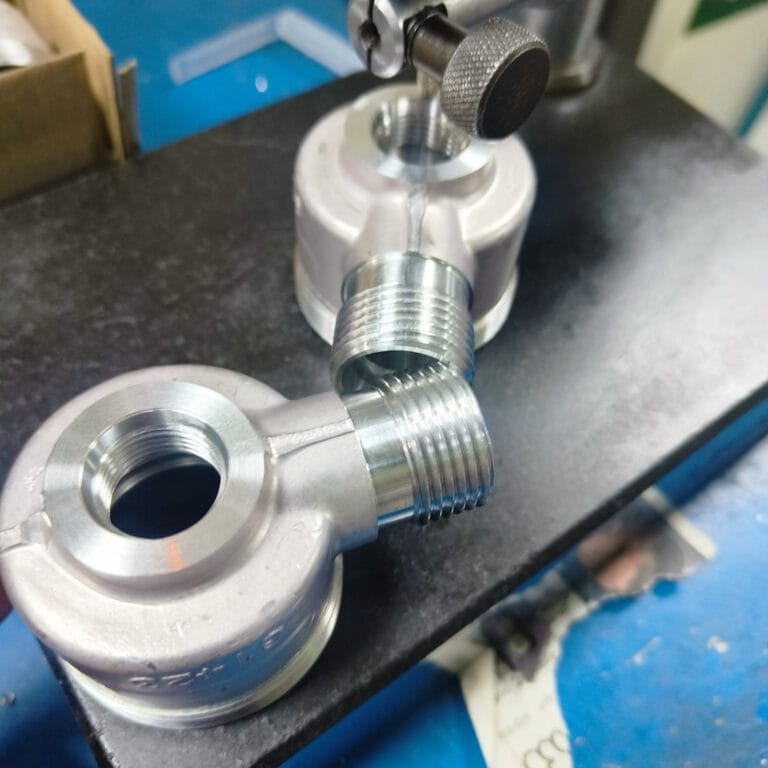
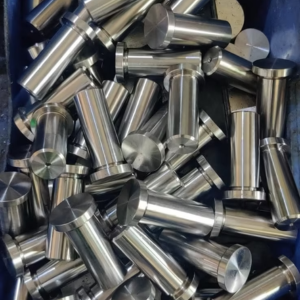
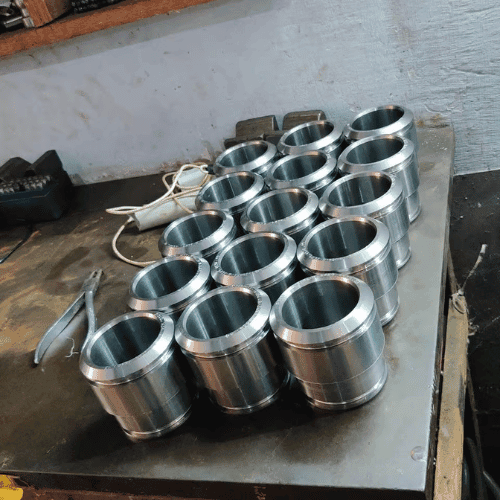
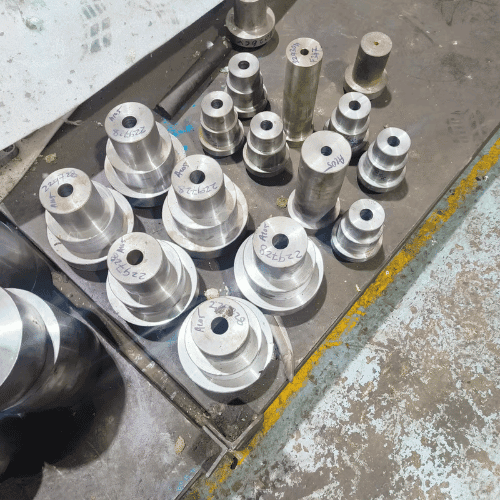
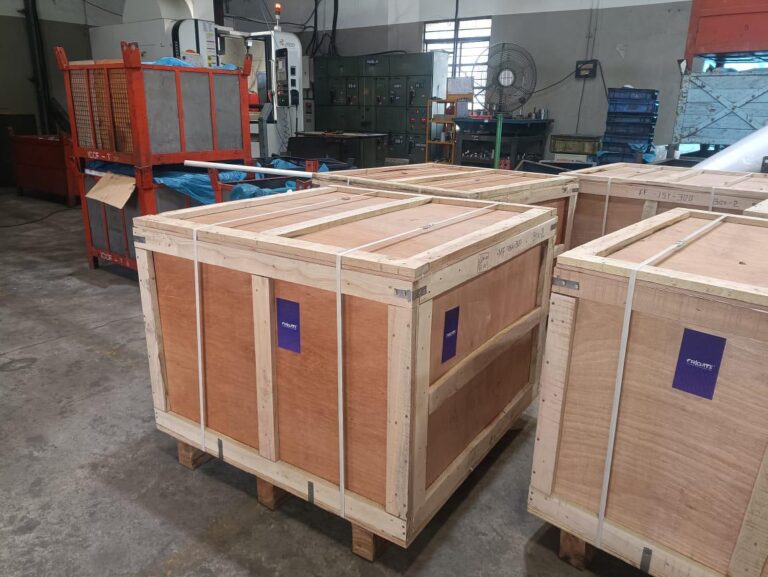
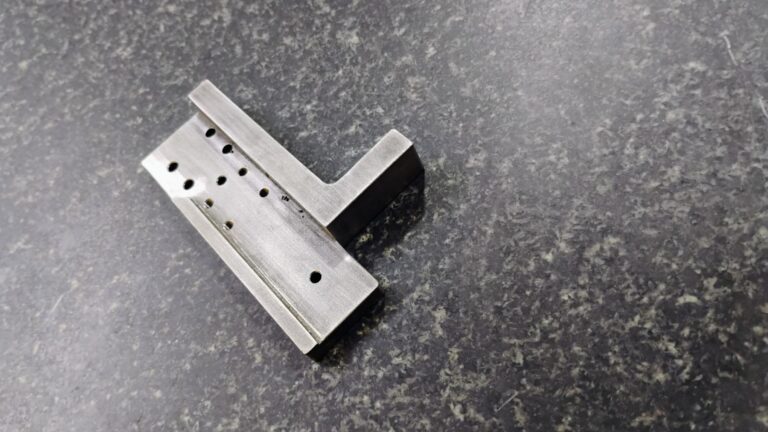
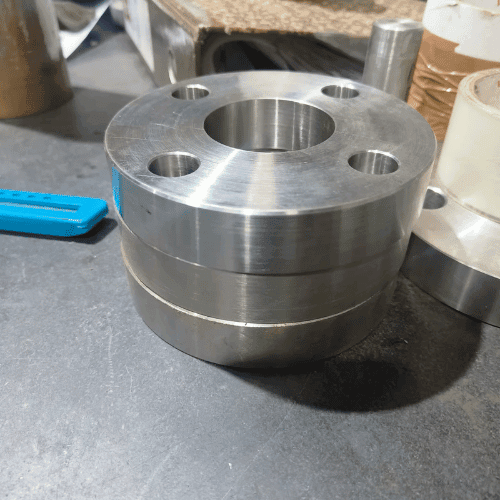
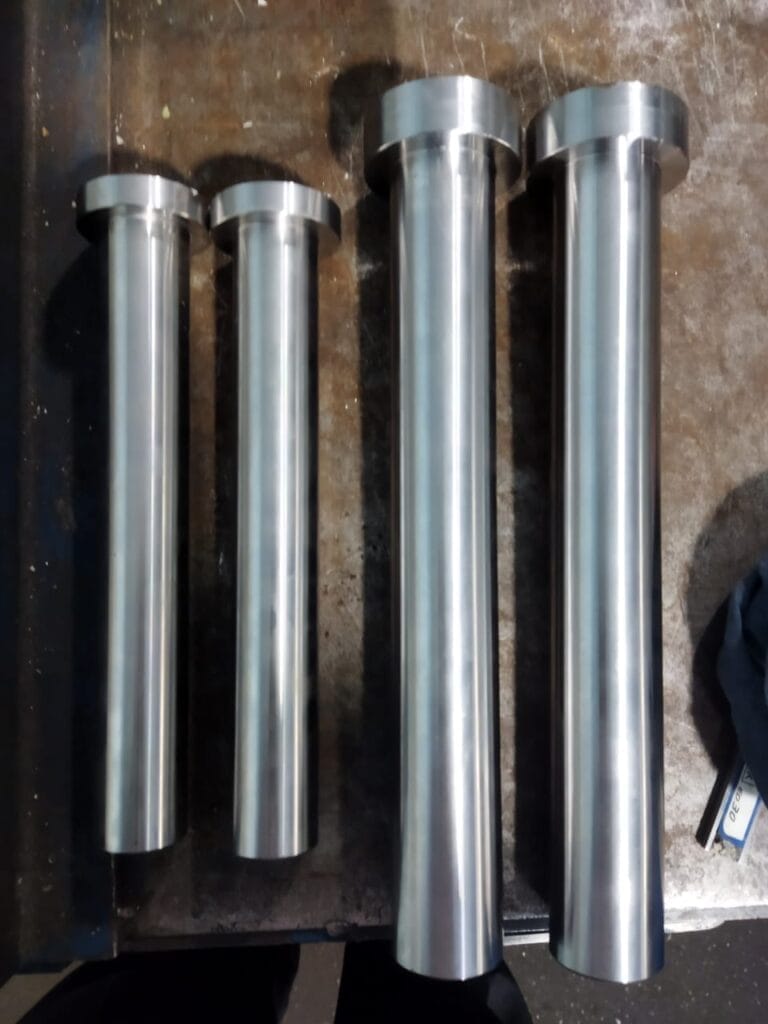

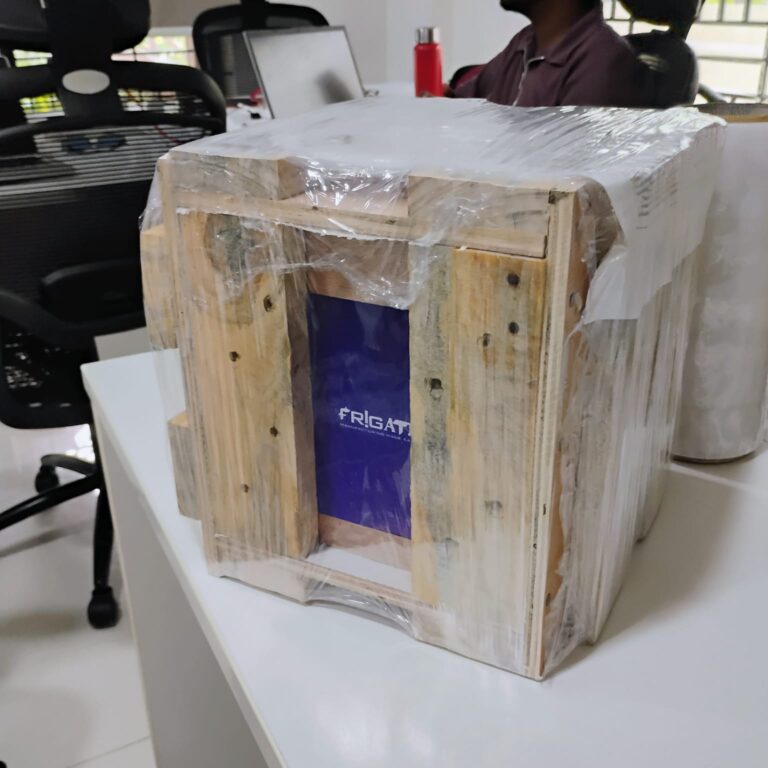

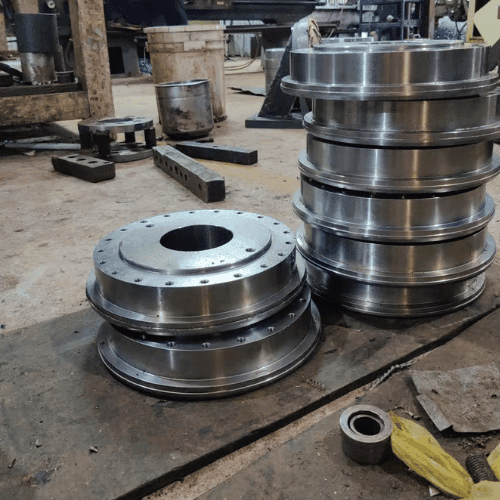
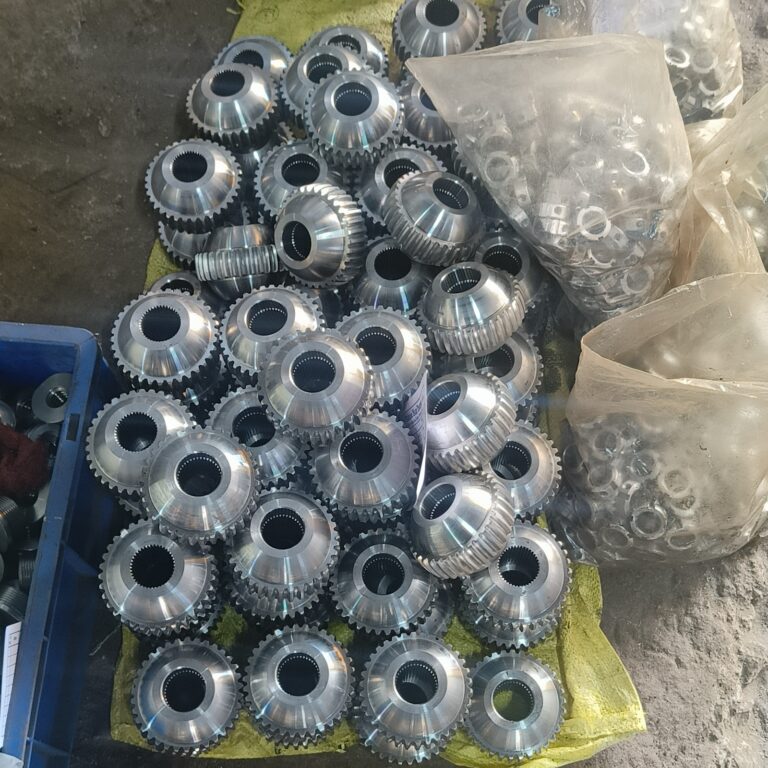
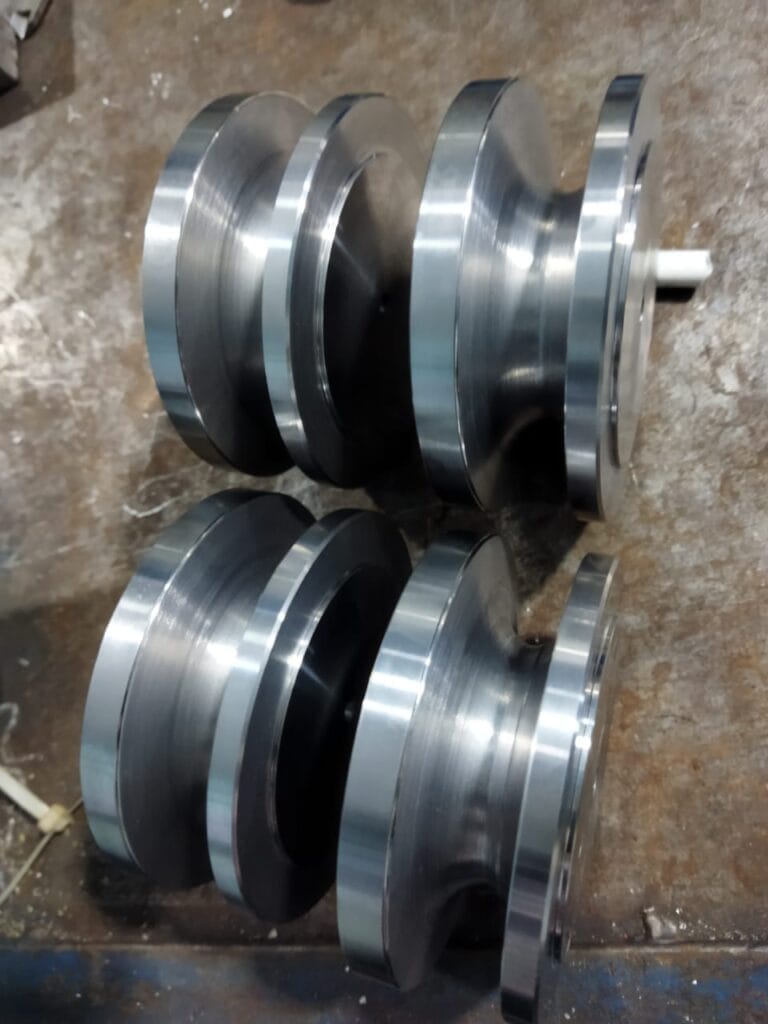
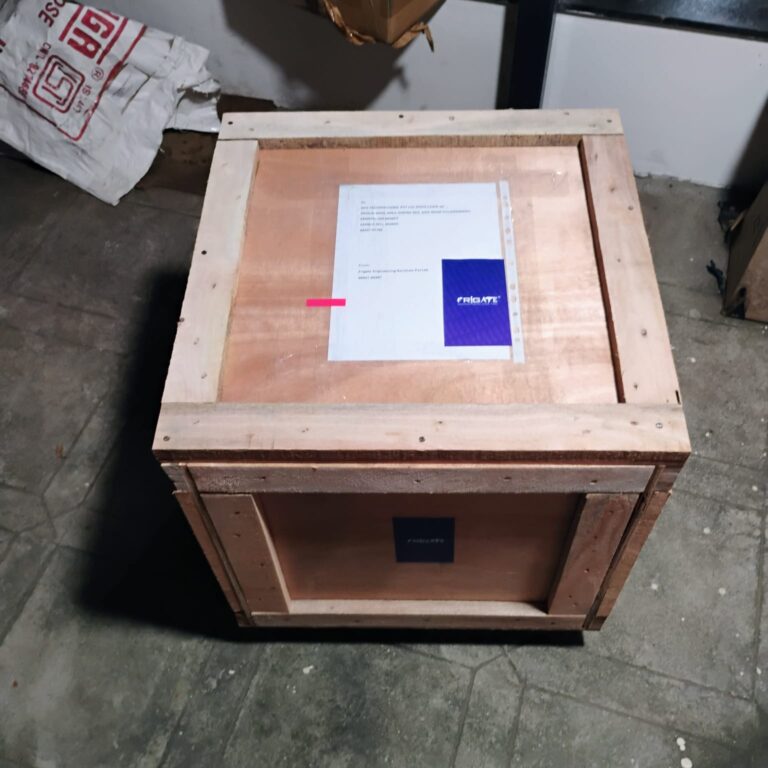
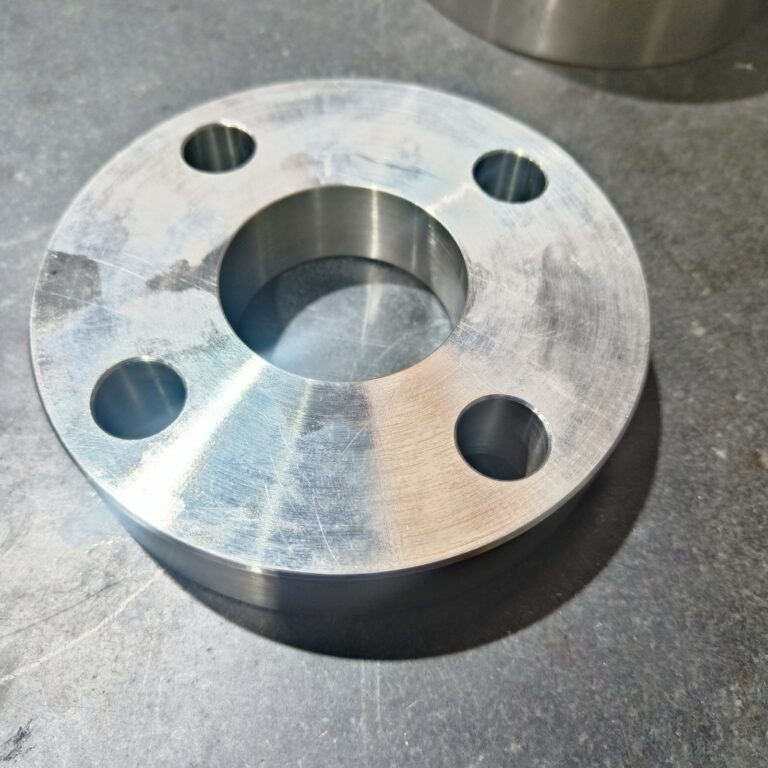
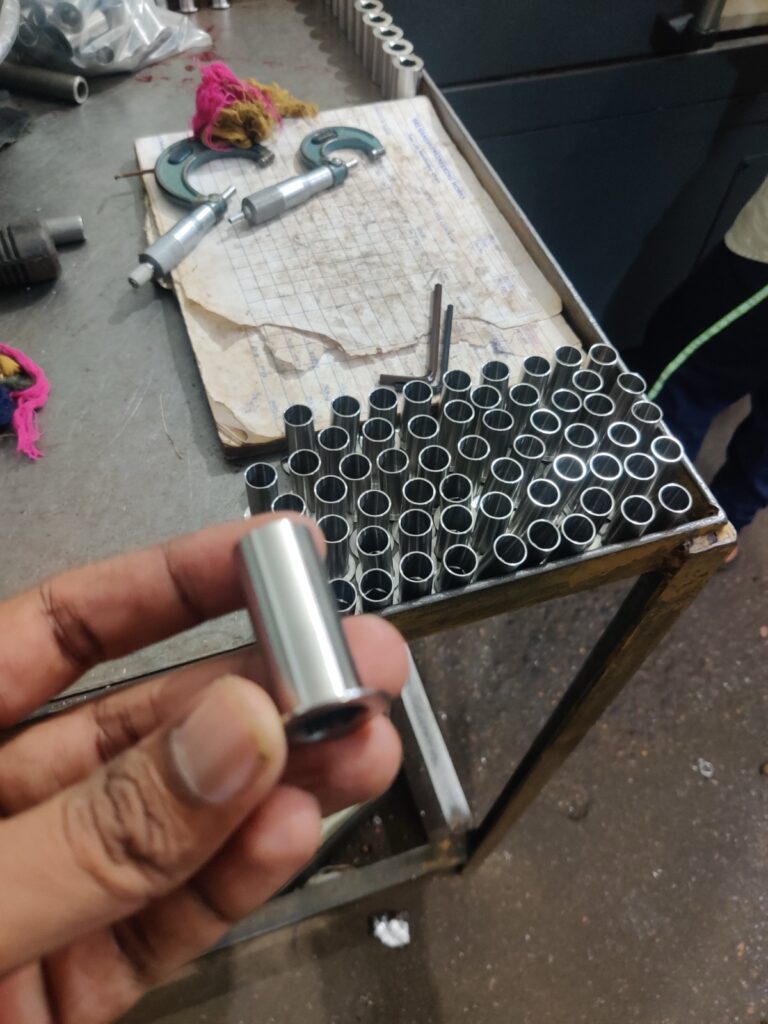
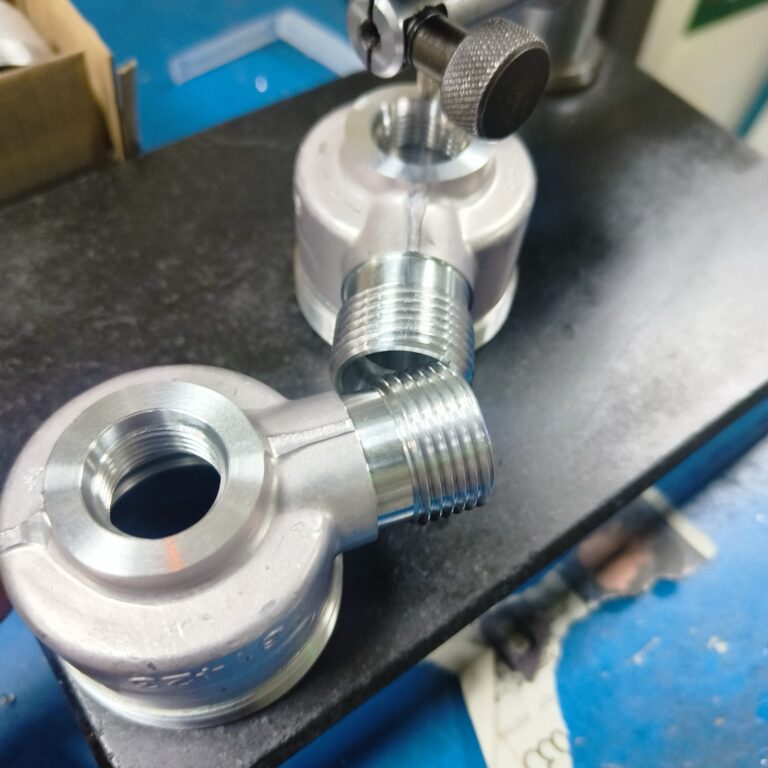
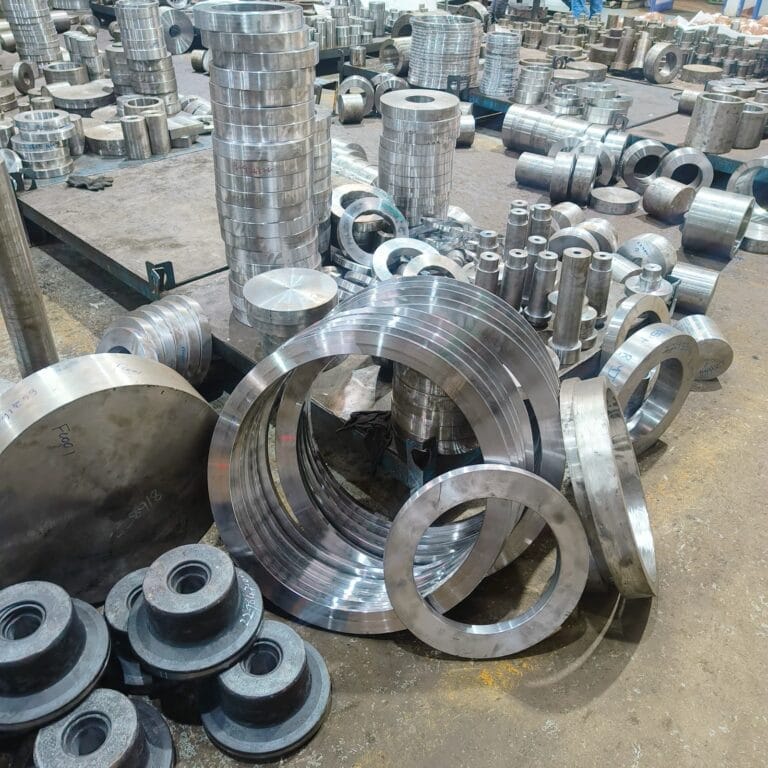
- One Stop Solution
End-to-End CNC Machining Solutions in Italy
We integrate hydrostatic guides, zero-point clamping, and isolated spindles to limit dimensional drift.
We generate estimates using real-time feedback on toolpath complexity, thermal gradients, and cut depth variation.
We verify tolerances using sub-micron tactile probes, calibrated granite setups, and controlled ambient conditions.
- Optimized Workflow
From CNC Rapid Prototyping to Production in Italy
Frigate offers fast and precise CNC machining, from rapid prototyping to full-scale production, ensuring high-quality parts with quick turnaround times.

Rapid Prototyping
We ensure uninterrupted prototyping through automated fixture calibration, toolpath verification, and spindle warm-up cycles.
- Instant quotes
- Instant DFM feedback
- Online quote and order management
- Live delivery tracking
Our process integrates spindle load balancing and automated tool calibration to maintain consistent mechanical performance.

Production Orders
We guarantee manufacturing accuracy through continuous process verification and automated dimensional validation.
- Dedicated project managers in your time zone
- Application engineers focused on DFM cost optimizations
- First Article Inspection (FAI) for quality assurance
- Supply chain support for materials and on-time delivery
We coordinate equipment availability and load balancing using real-time performance metrics and adaptive workflow management.
- Trusted Solutions
CNC Machining Solutions in Italy that You Can Trust
We apply servo-controlled mechanical clamps alongside active thermal compensation to maintain component stability throughout the cutting process. Confocal microscopy verifies surface texture uniformity at micron levels.
- Ultra-Tight Tolerances (±0.005mm)
- 5-Axis Machining for Complex Designs
- High-Speed Spindles (Up to 60,000 RPM)
- Adaptive Feed Rate Optimization
- Rigid Fixturing & Workholding

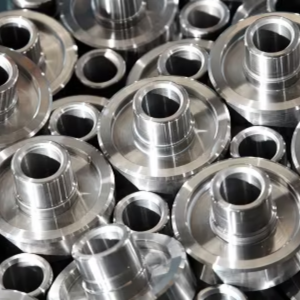
- Manufacturing Optimization
Get Started with Our CNC Machining Services
We utilize X-ray computed tomography, ultrasonic inspection, and coordinate measuring machines to ensure internal integrity and dimensional conformity.
Integrated Sensor Fusion for Machining Monitoring
Combining force, vibration, and acoustic data to provide comprehensive real-time machining condition assessment.
High-Precision Ball Screw Calibration
Utilizing laser interferometry to calibrate ball screws for positional accuracy within ±0.1 µm over long travel distances.
Closed-Loop Thermal Compensation Systems
Real-time adjustment of machine axes to counteract dimensional errors caused by thermal expansion.
- FAQ
Having Doubts? Our FAQ
Check all our Frequently Asked Questions in CNC Machining
We apply specialized fixturing and adaptive tool path strategies to minimize part distortion during cutting. Real-time force monitoring adjusts feed rates to reduce stress on thin sections. This approach preserves geometry and meets tight tolerances consistently.
We use low-vibration machining combined with controlled coolant delivery to avoid heat-induced surface damage. Ultra-precise tooling and fine finishing cuts improve surface smoothness. This ensures biocompatible, corrosion-resistant surfaces critical for medical use.
We incorporate in-process stress-relief cycles using controlled cooling and intermittent cutting patterns. Post-machining heat treatments further stabilize microstructures. This process reduces warping and extends the component’s operational life.
We use high-rigidity setups and servo-controlled axes with precision feedback loops to maintain consistent positioning. Tool wear is monitored and compensated automatically during production runs. This ensures uniform quality across large batch orders.
We utilize diamond-coated micro-end mills and slow, controlled feeds to protect fine details. Temperature control prevents thermal expansion that could affect feature accuracy. This enables the production of intricate, durable tool components.
We'd love to Manufacture for you!
Submit the form below and our representative will be in touch shortly.
LOCATIONS
Registered Office
10-A, First Floor, V.V Complex, Prakash Nagar, Thiruverumbur, Trichy-620013, Tamil Nadu, India.
Operations Office
9/1, Poonthottam Nagar, Ramanandha Nagar, Saravanampatti, Coimbatore-641035, Tamil Nadu, India. ㅤ
Other Locations
- Bhilai
- Chennai
- USA
- Germany