- Rapid Manufacturing
CNC Machining Services in South Carolina
We manufacture precision parts with white-light interferometry to detect nano-scale surface irregularities in critical components. Upload your CAD file to get an instant quote and complete your order in just 5 minutes.
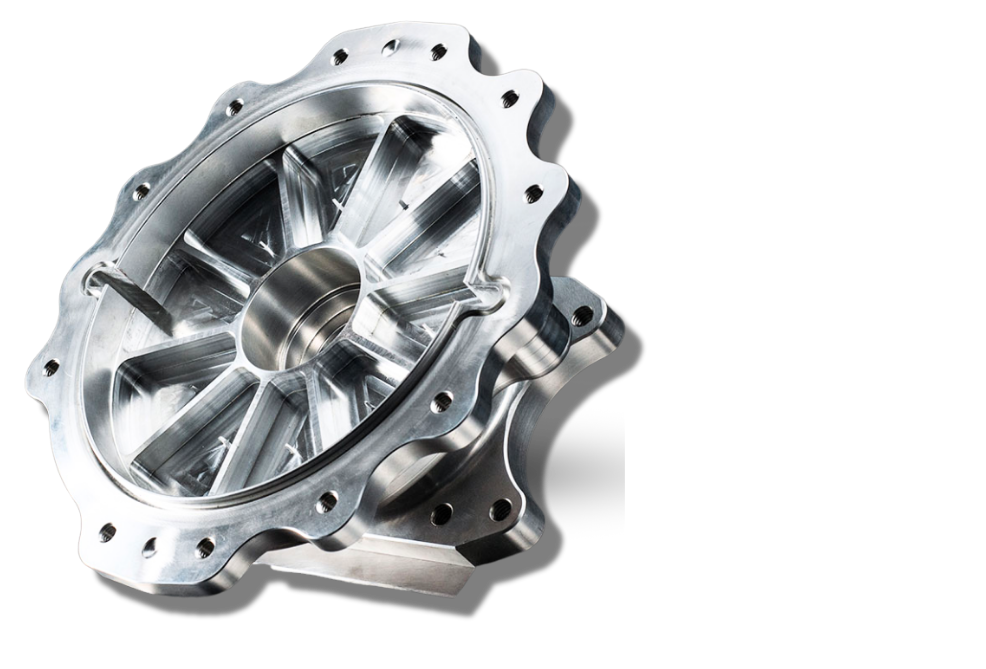
Our Clients
Trusted by Engineers and Purchasing Leaders
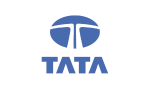
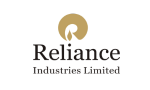


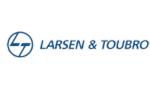
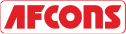


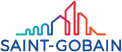

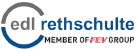

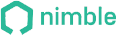
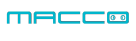









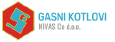
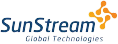

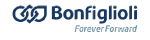


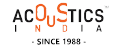
- Instant Quotes
Quote in Seconds - Parts in Days
We utilize spindle inertia control mechanisms that adjust rotational acceleration to reduce overshoot errors. This achieves precise geometries, ensuring a 7-day delivery target.
- Get instant quotes
- Get instant DFM feedback
- Online quote and order management
- Project Management
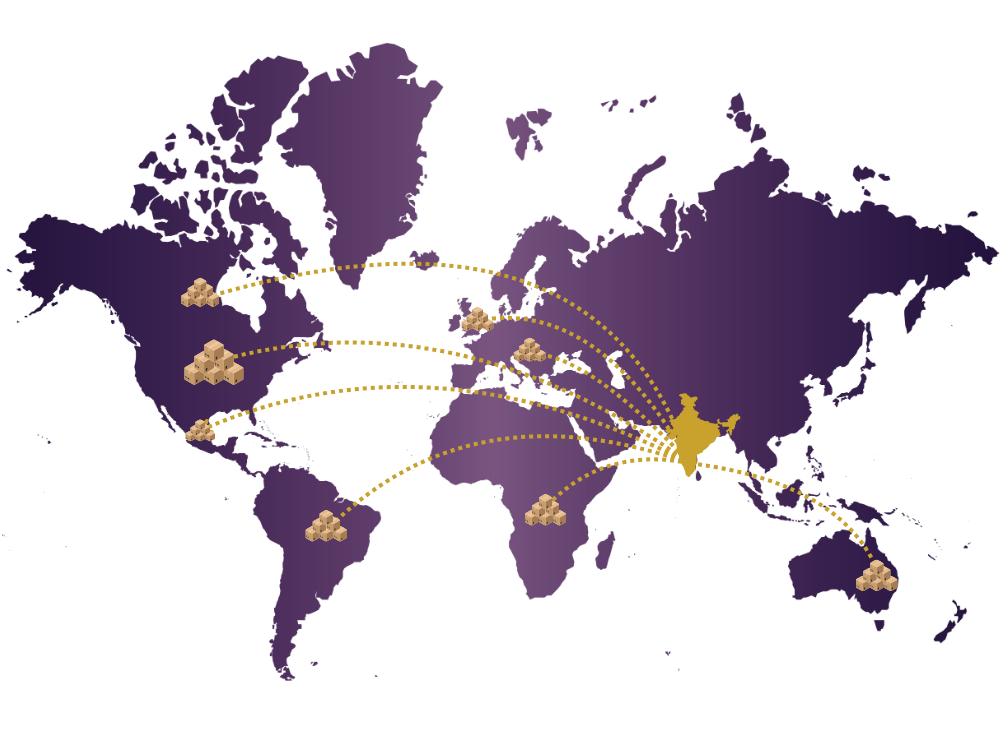
- Our Services
Online CNC Machining Service in South Carolina
Get high-precision CNC machined parts online with fast turnaround and cost-effective pricing.
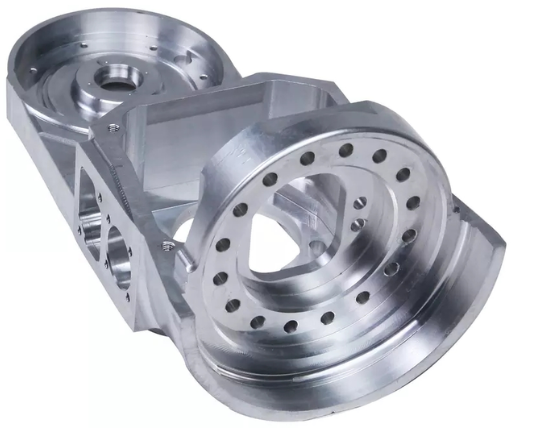
CNC Milling
Micro-milling combines dynamic spindle torque control, phase-shift compensation, and ultrasonic tool vibration to achieve smooth surfaces.
- Handle tough materials with spindle power up to 30 kW
- Free design feedback with every quote
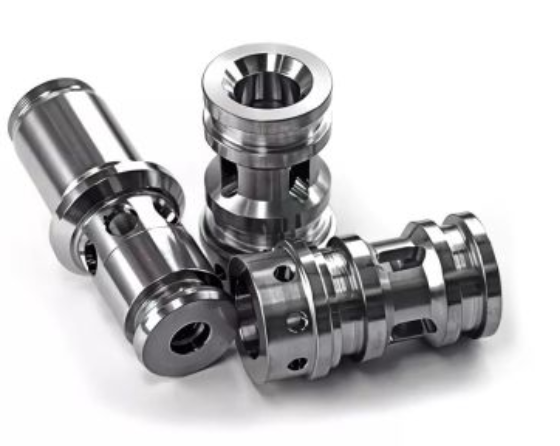
CNC Turning
Advanced CNC turning applies harmonic drive systems, spindle temperature stabilization, and in-process probing to enhance positional accuracy.
- Complex cylindrical parts up to ⌀500mm
- Bar feeding feature for faster, continuous production
- Surface Finish
Flawless Finishes for CNC Machining Parts in South Carolina
We strengthen surface finishes with controlled thermal cycling, residual stress reduction, and diamond burnishing for improved fatigue life.
Anodizing
Give your aluminum parts a tough, corrosion-resistant shield with anodizing, reaching surface hardness up to HV 500, while enhancing electrical insulation and durability.
Mechanical Finishing
Smooth out imperfections and refine surfaces to Ra 0.2 µm or better with mechanical finishing techniques like grinding, polishing, and bead blasting.
Heat Treatment
Boost material strength and hardness by heat treating parts at temperatures up to 1100°C, ensuring they meet the mechanical demands of your application.
Electroplating
Add protective or functional metal coatings with electroplating, delivering consistent layers as precise as ±2 µm for improved corrosion resistance and conductivity.
- Real Impact
Words from Clients
See how global OEMs and sourcing heads describe their experience with our scalable execution.
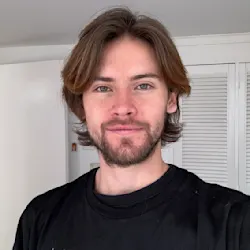
“Quick turnaround and solid quality.”
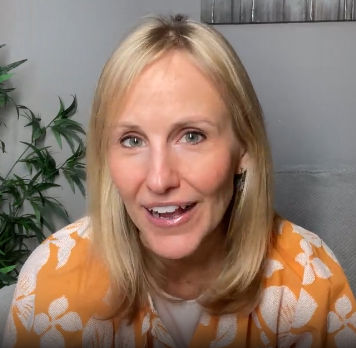
“The instant quote tool saved us time, and the parts were spot-on. Highly recommend Frigate!”
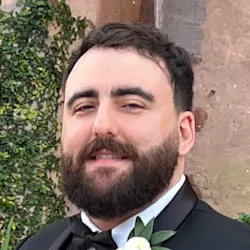
“Great service, fair price, and the parts worked perfectly in our assembly.”
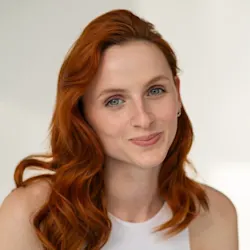
“Top-notch machining and fast shipping. Very satisfied with the results.”
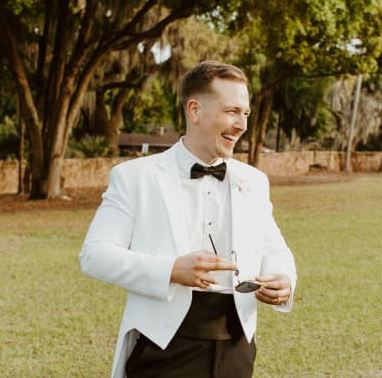
“Frigate delivered high-quality parts at a competitive price. The instant quote tool is a huge plus for us!”

“We appreciate the precision and quality of the machined components in the recent delivery—they meet our specifications perfectly and demonstrate Frigate’s capability for excellent workmanship.”
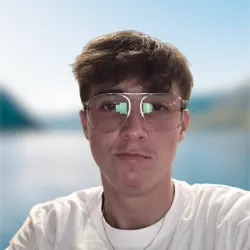
“Flawless execution from quote to delivery.”
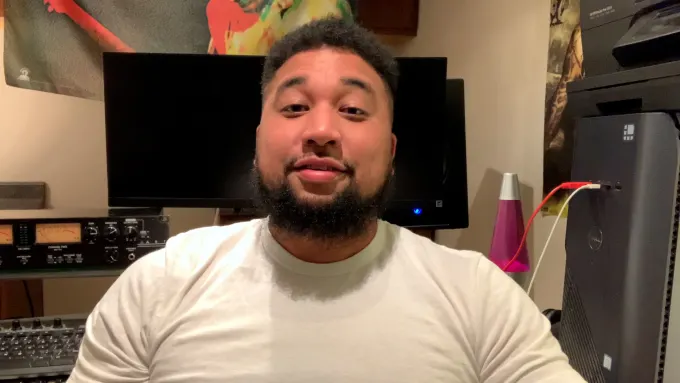
“The precision on these parts is impressive, and they arrived ahead of schedule. Frigate’s process really stands out!”
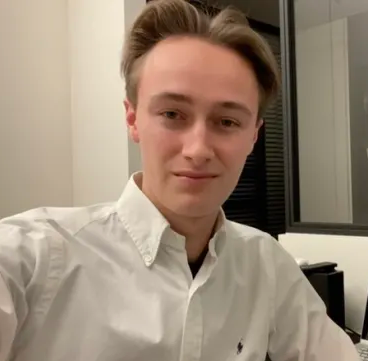
“Parts were exactly as spec’d, and the instant quote made budgeting a breeze.”
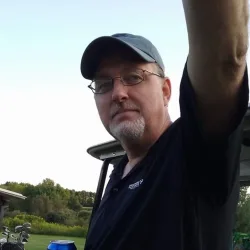
“Good value for the money.”
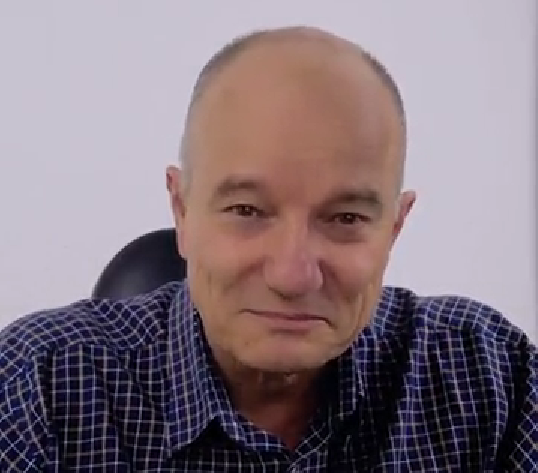
“The finish was perfect, and the team was easy to work with.”
- We export to 12+ countries
Frigate’s Global Presence
Frigate takes pride in facilitating “Make in India for the globe“. As our global network of Frigaters provides virtually limitless capacity, and through our IoT enabled platform your parts go directly into production. By digitally and technologically enabling “the silent pillars of the economy” MSME and SME manufacturing industries, we are able to tap the huge potential for manufacturing to bring the best results for our clients.

100,000+
Parts Manufactured
250+
Frigaters
2000+
Machines
450+
Materials
25+
Manufacturing Process
- Transparent Pricing
Instant Online Quote for CNC Machining Services
Our technique applies microstructure analysis and grain orientation modeling to predict deformation behavior. This data powers a seamless quoting system that calculates CNC machining costs with speed and accuracy.
- Price updates are made in real time as you change materials, machining methods, etc.
- No hidden costs. Our instant quotes are not just indications but the actual price and include shipping and customs up front.

- Quote to Delivery
Quick and Clear Steps to Your Order
Everything moves smoothly from pricing to shipment, so you get high-quality parts without delays.
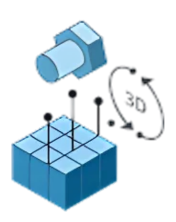
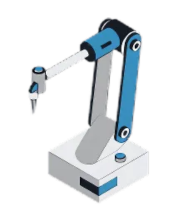
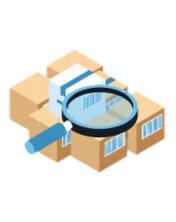
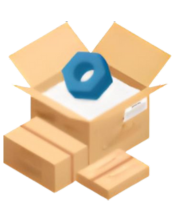
Upload CAD File
Obtain a precise and competitive quote instantly to empower your decision-making.
- Detailed cost breakdown
- Various materials and finish choices
- Market-driven unbeatable pricing
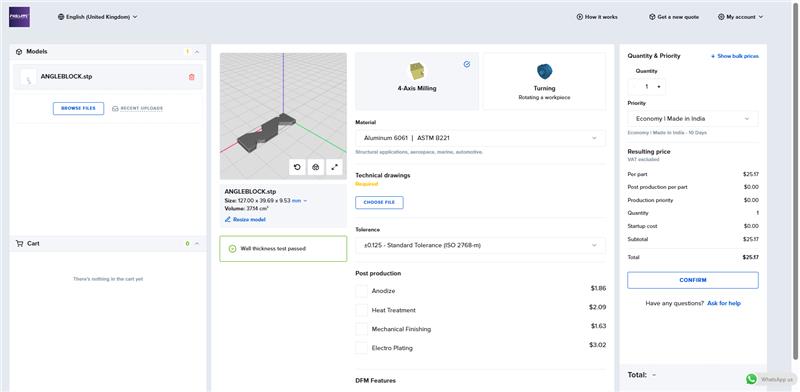
Manufacturing Begins
Transform your designs into reality with our state-of-the-art CNC production capabilities.
- Advanced machinery
- Scalable production support
- Live updates from the production floor
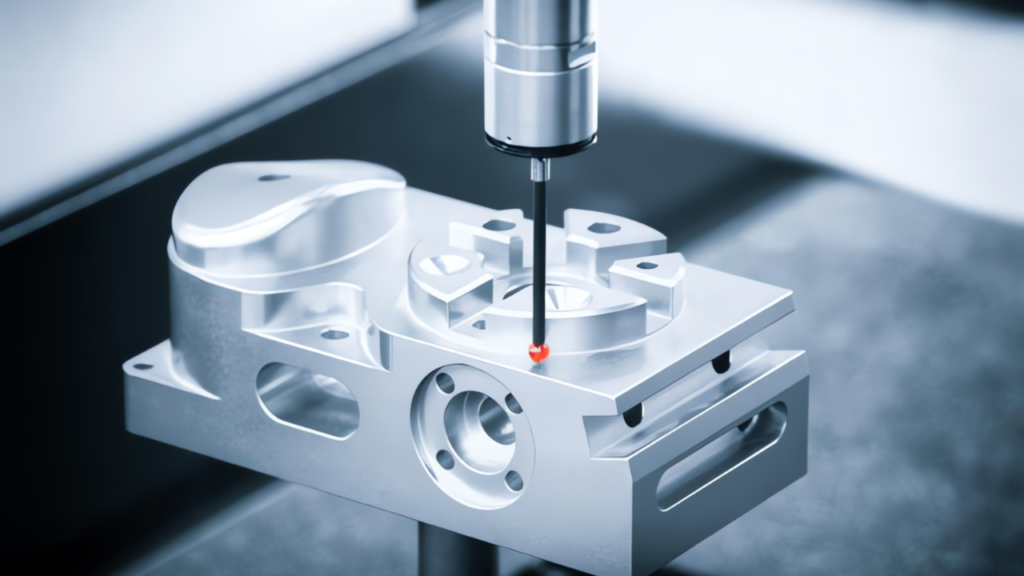
Thorough Inspection
Each part is checked to match exact specifications before moving forward.
- High-tech dimensional verification
- Surface finishing and coating checks
- Batch-wise documentation
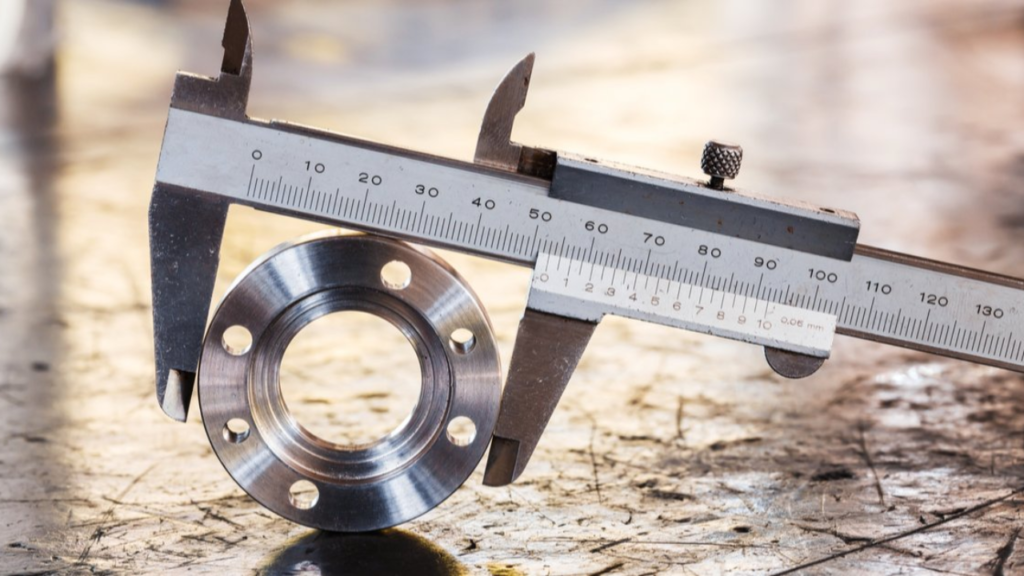
Safe & Timely Dispatch
Receive your machined parts promptly and in perfect condition.
- Multiple shipping options
- Secure packaging
- Real-time tracking during every transit
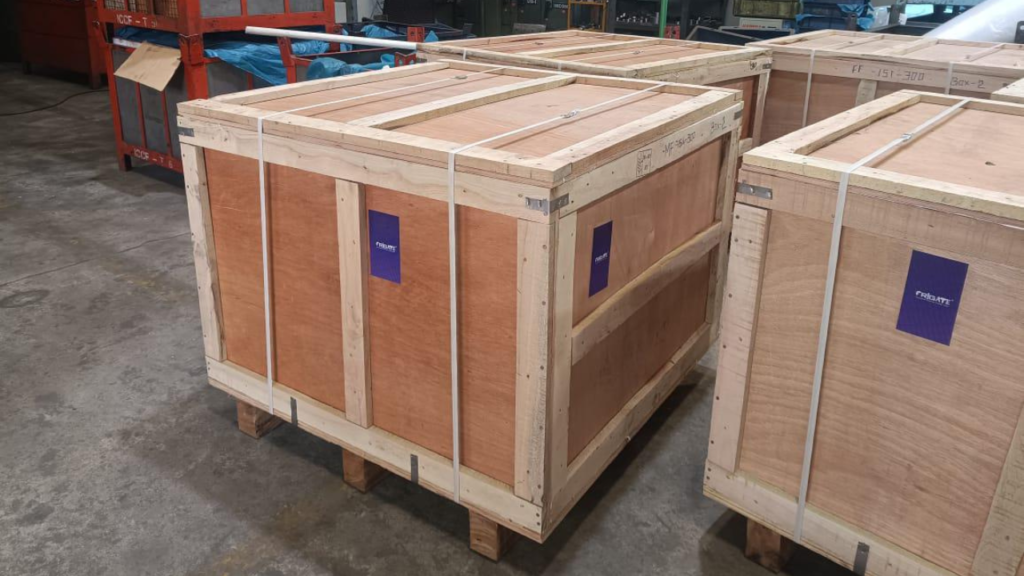
- Machining Materials
Different Materials for CNC Machining
We combine carbon-based heat absorbers with controlled convection pathways to reduce thermal stress in alloy components. Intelligent spindle adjustments maintain dimensional integrity across varying designs.
Aluminum 6061
- Density - 2.7 g/cm³
- Tensile Strength - 310 MPa
- Yield Strength - 276 MPa
- Hardness (Brinell) - 95 HB
- Excellent corrosion resistance, good machinability, and heat treatable
Used in aerospace, automotive, and electronics for components like aircraft structures, bicycle frames, and heat sinks due to its lightweight and strength.
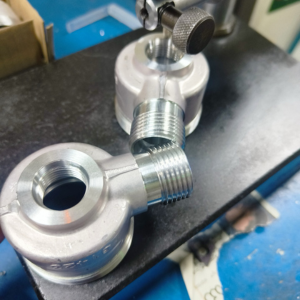
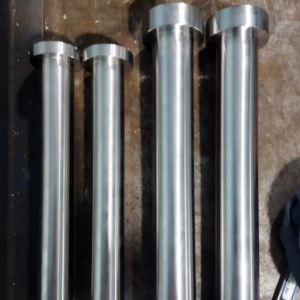
Aluminum 7075
- Density - 2.81 g/cm³
- Tensile Strength - 572 MPa
- Yield Strength - 503 MPa
- Hardness (Brinell) - 150 HB
- High fatigue resistance but limited weldability
Commonly used in aerospace, defense, and sporting goods for aircraft wings, firearm components, and high-performance bicycle parts requiring high strength.
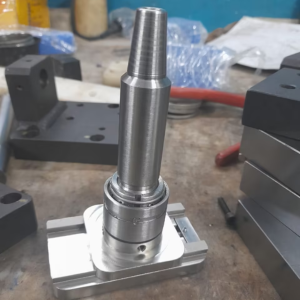

Aluminum 7050
- Density - 2.81 g/cm³
- Tensile Strength - 572 MPa
- Yield Strength - 503 MPa
- Hardness (Brinell) - 150 HB
- High fatigue resistance but limited weldability
Commonly used in aerospace, defense, and sporting goods for aircraft wings, firearm components, and high-performance bicycle parts requiring high strength.
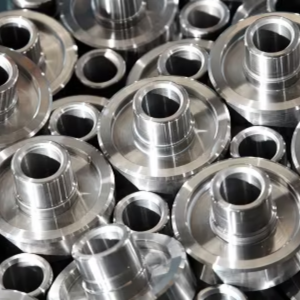

Stainless Steel 304
- Density - 8.0 g/cm³
- Tensile Strength - 515 MPa
- Yield Strength - 205 MPa
- Hardness (Brinell) - 201 HB
- High corrosion resistance, non-magnetic, and good formability
Preferred in food processing, medical, and chemical industries for tanks, surgical tools, and piping systems due to its hygiene and corrosion resistance.

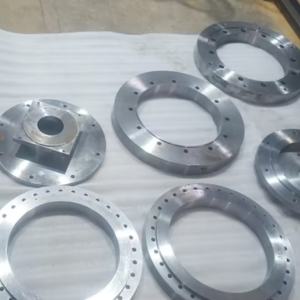
Stainless Steel 440 - Carbon
- Density - 7.8 g/cm³
- Tensile Strength - 760 MPa
- Yield Strength - 450 MPa
- Hardness (Rockwell C) - 56-60 HRC
- High hardness, excellent wear resistance, and corrosion resistance
Used in cutting tools, bearings, valves, and surgical instruments where extreme hardness and durability are required.
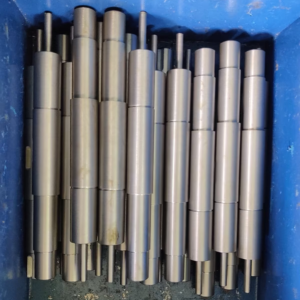
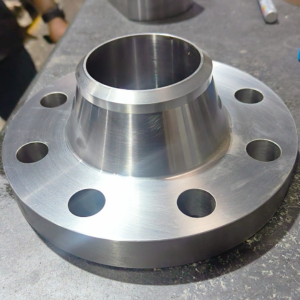
Stainless Steel 416
- Density - 7.7 g/cm³
- Tensile Strength - 585 MPa
- Yield Strength - 275 MPa
- Hardness (Brinell) - 262 HB
- Free-machining stainless steel with good strength
Ideal for automotive, firearms, and industrial applications, including gears, bolts, and shafts requiring high machinability.

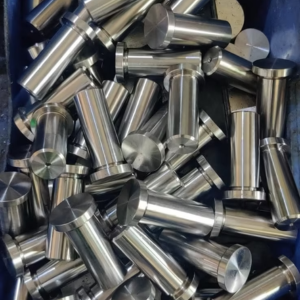
Steel 1018
- Density - 7.87 g/cm³
- Tensile Strength - 440 MPa
- Yield Strength - 370 MPa
- Hardness (Brinell) - 126 HB
- Excellent weldability and machinability
Used in automotive, machinery, and construction for shafts, pins, and fasteners where moderate strength and cost efficiency are key.

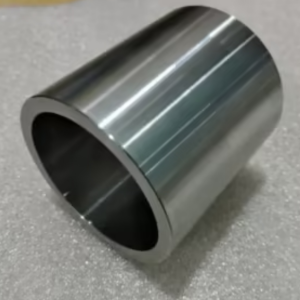
Steel 4140
- Density - 7.85 g/cm³
- Tensile Strength - 655 MPa
- Yield Strength - 415 MPa
- Hardness (Rockwell C) - 28-32 HRC
- High strength, toughness, and wear resistance
Widely used in oil & gas, aerospace, and automotive for gears, crankshafts, axles, and high-load machine components requiring extreme durability.
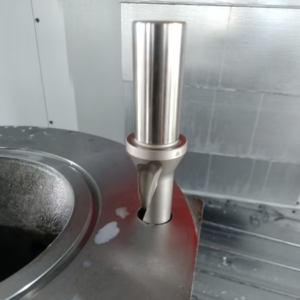
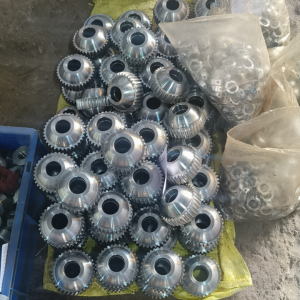
- CNC Machining Parts
CNC Machining Parts in South Carolina
We combine direct-drive motors, adaptive torque control, and micro-vibration suppression systems to achieve stable motion. Browse our advanced components designed for precision manufacturing requirements.
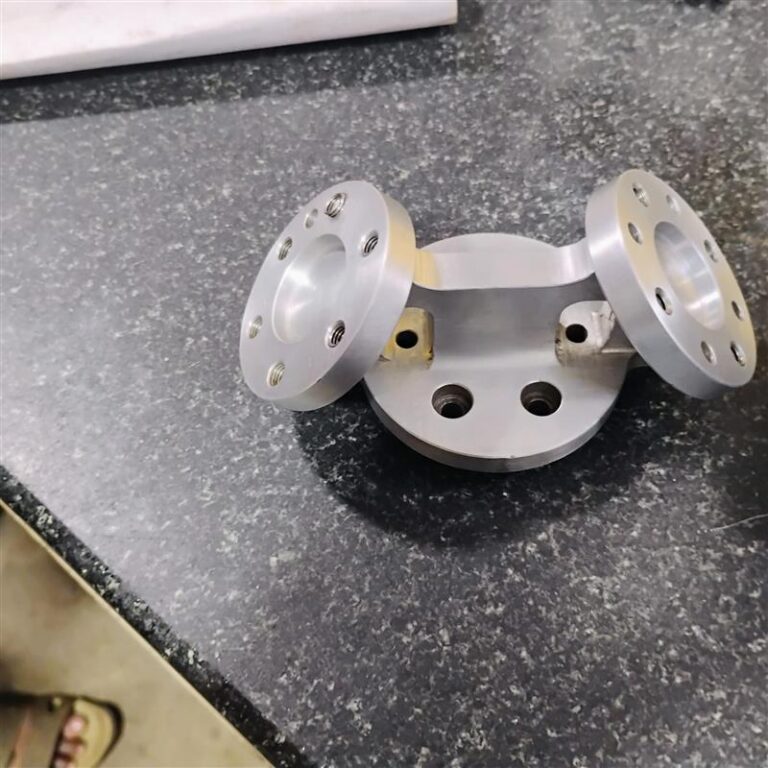
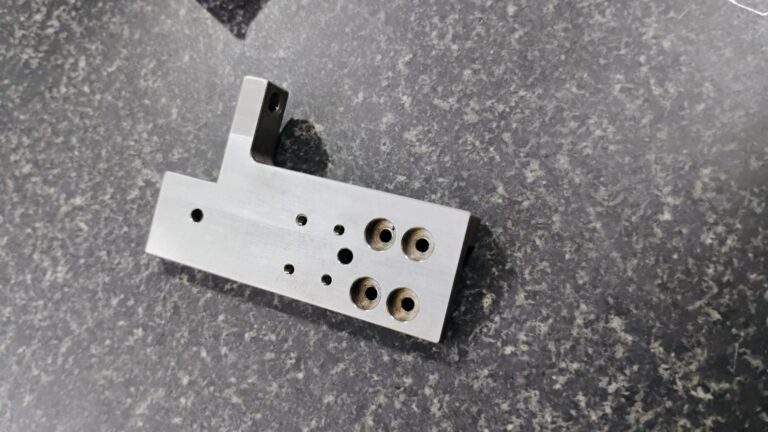
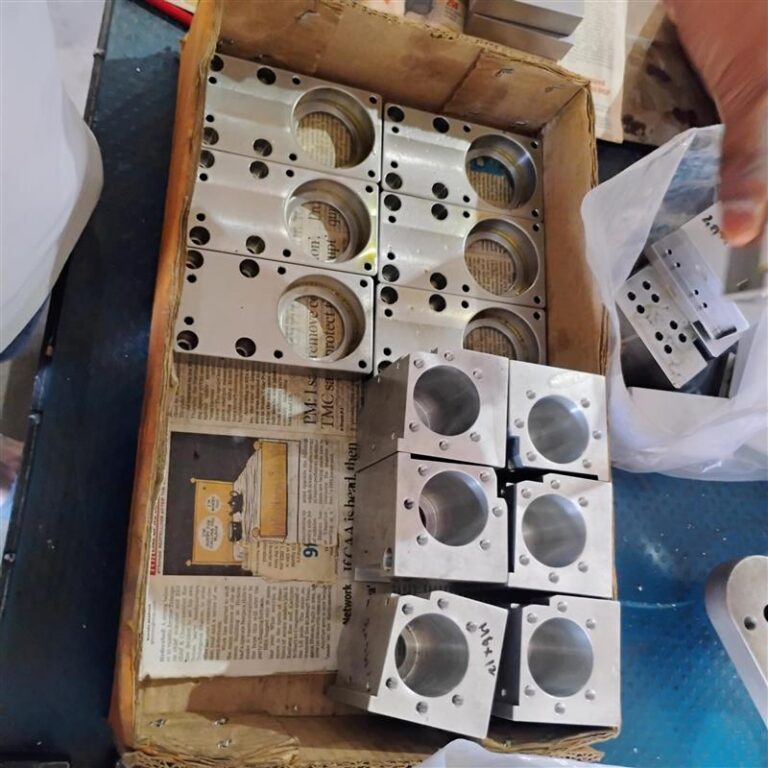
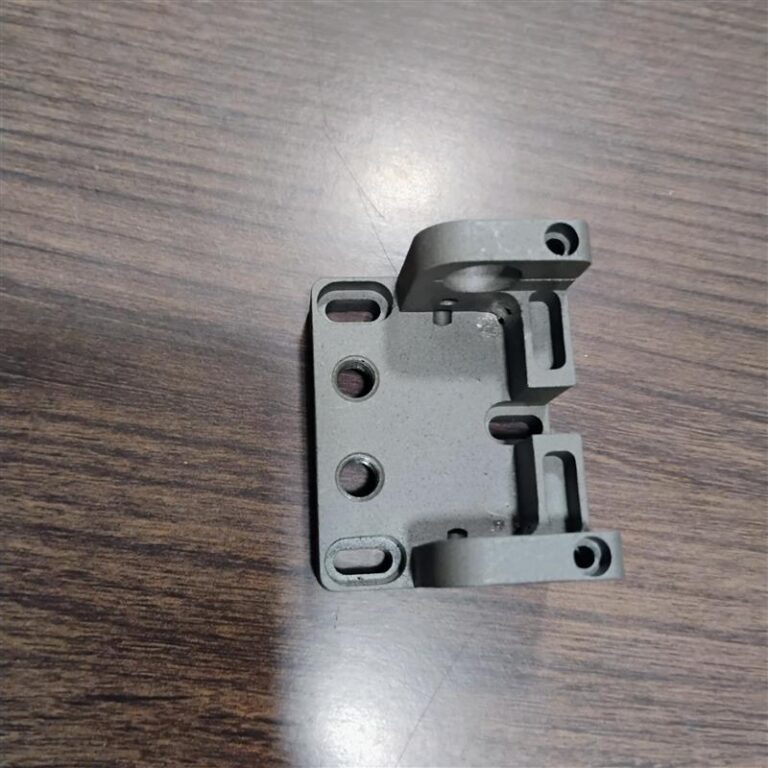
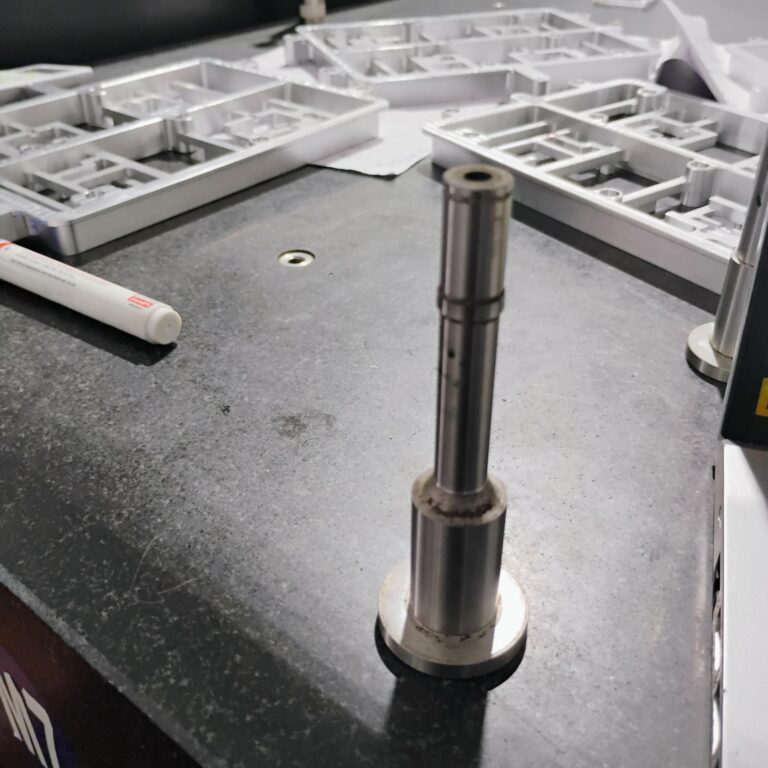
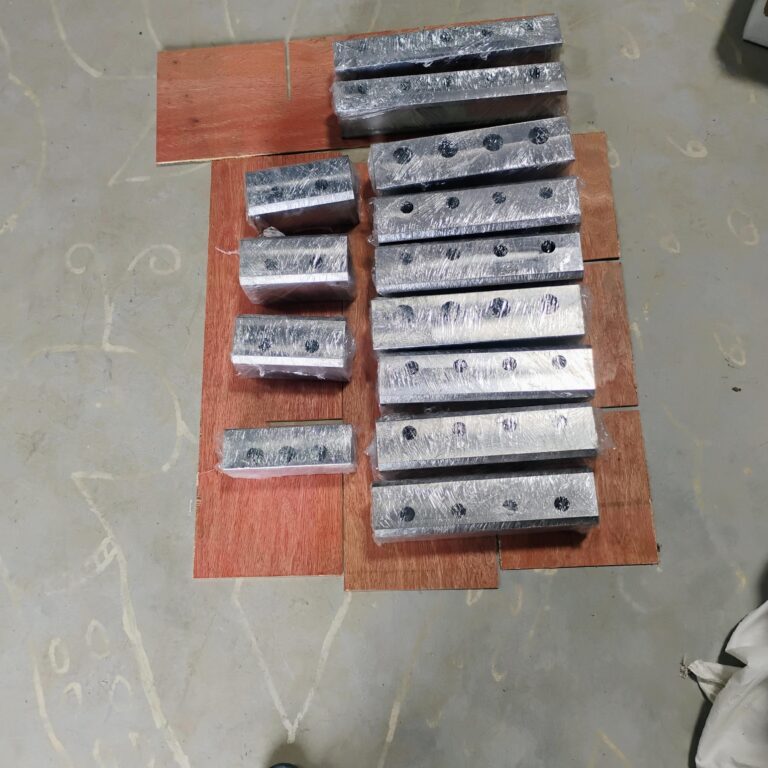
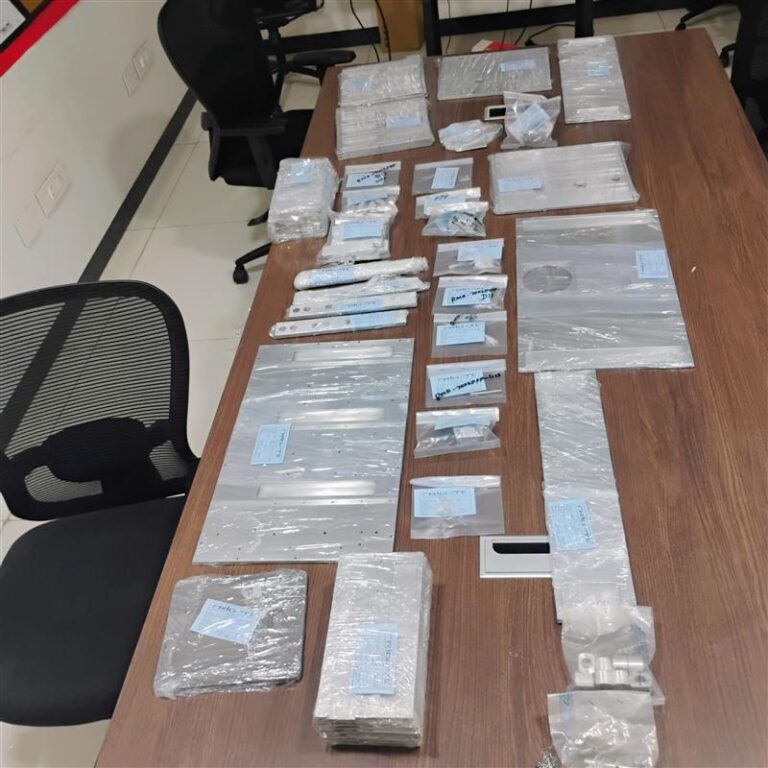

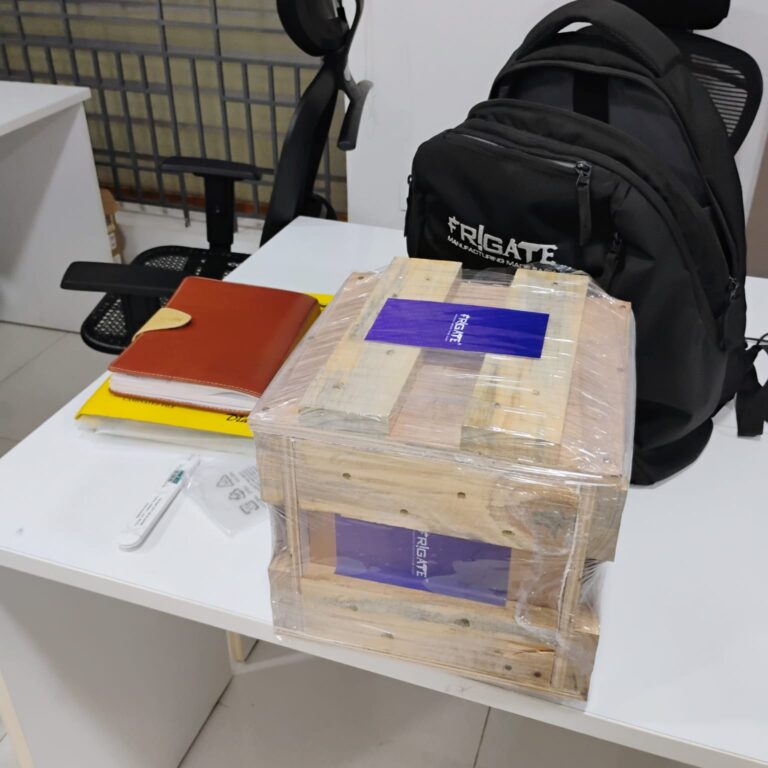


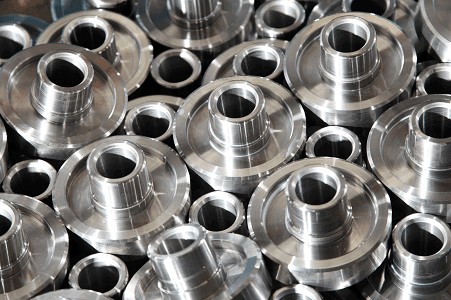
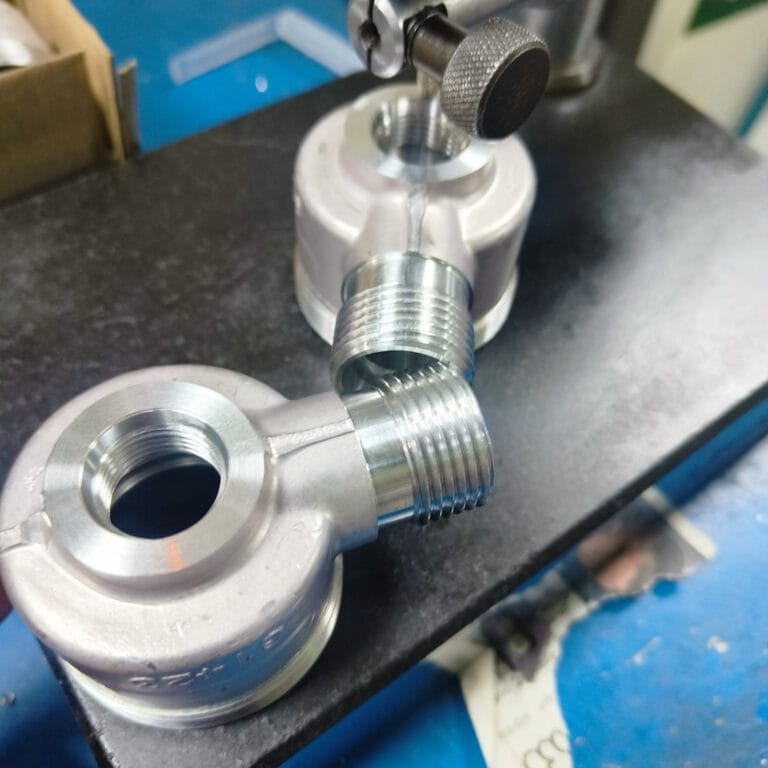
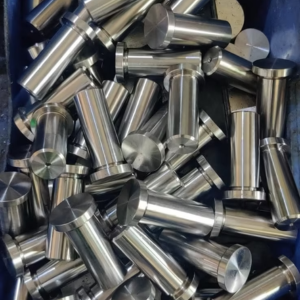
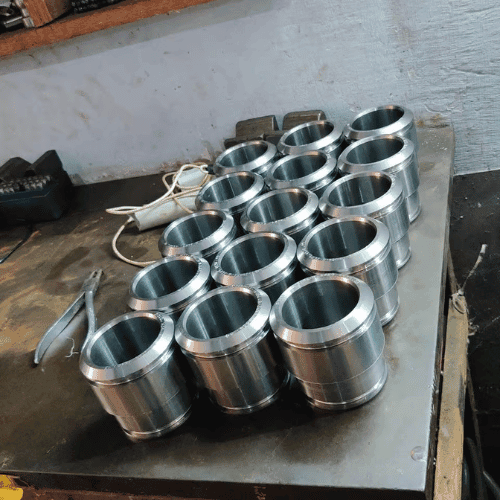
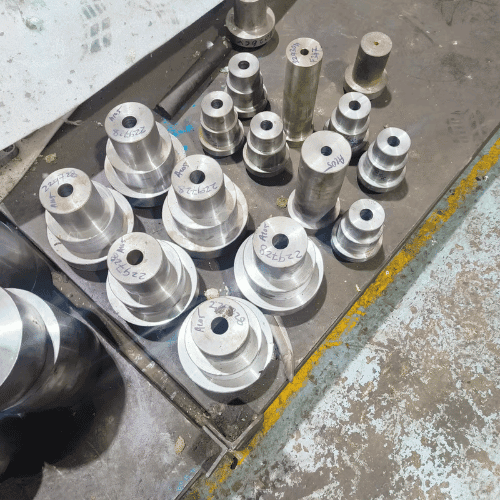
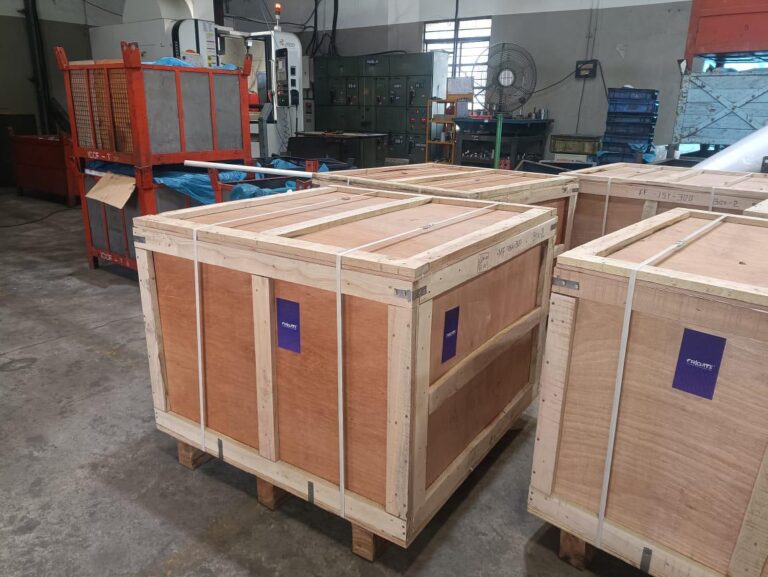
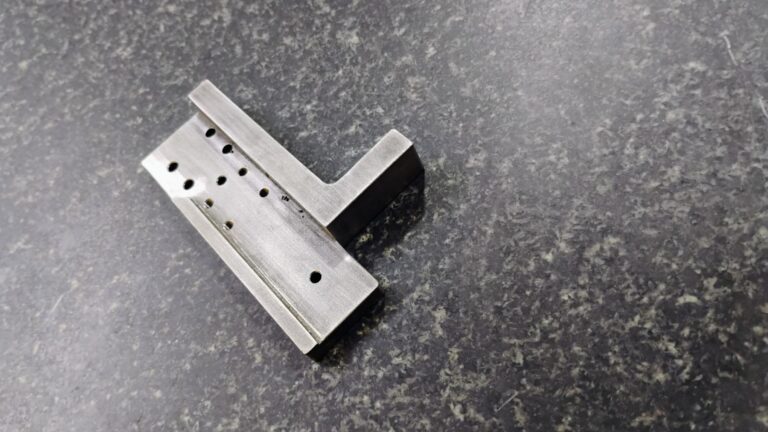
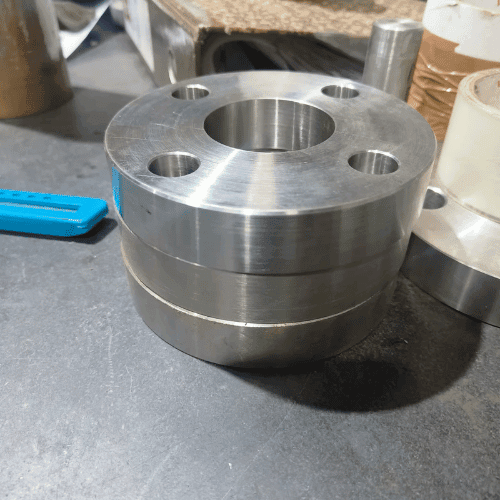
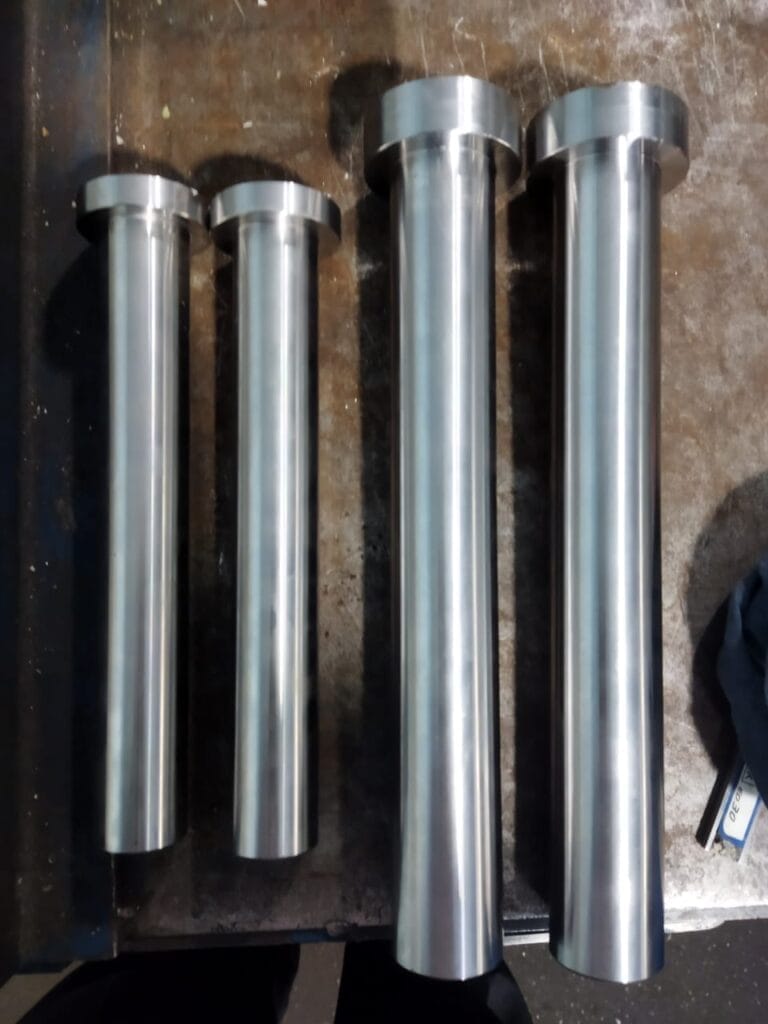

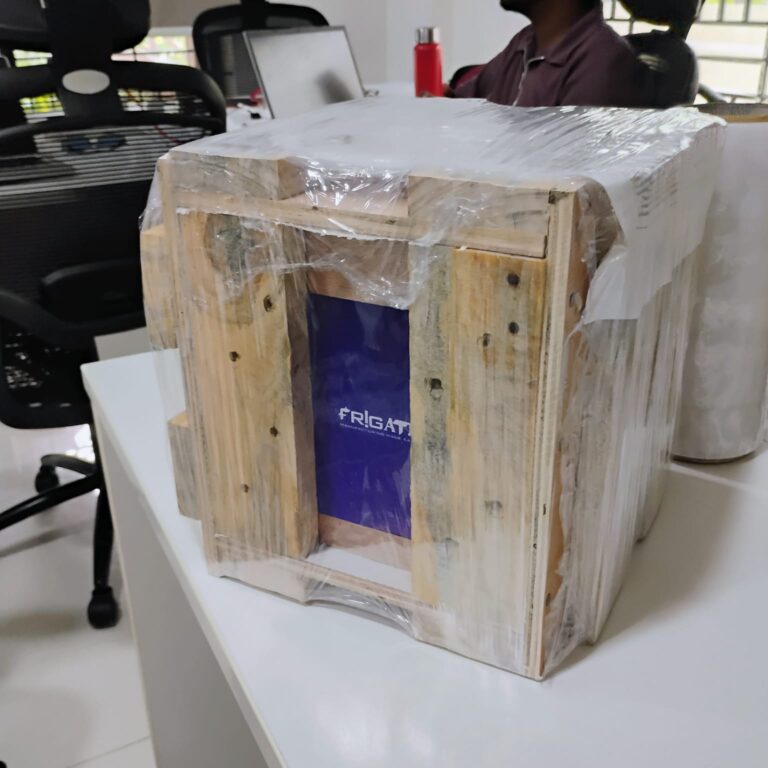

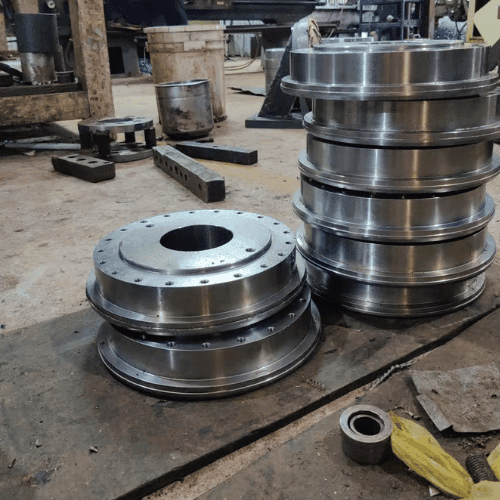
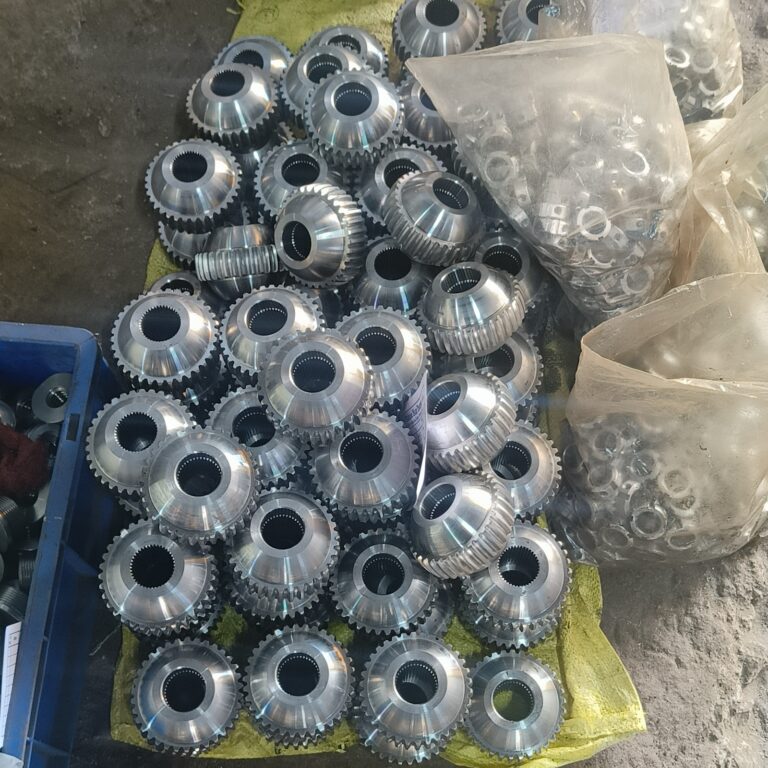
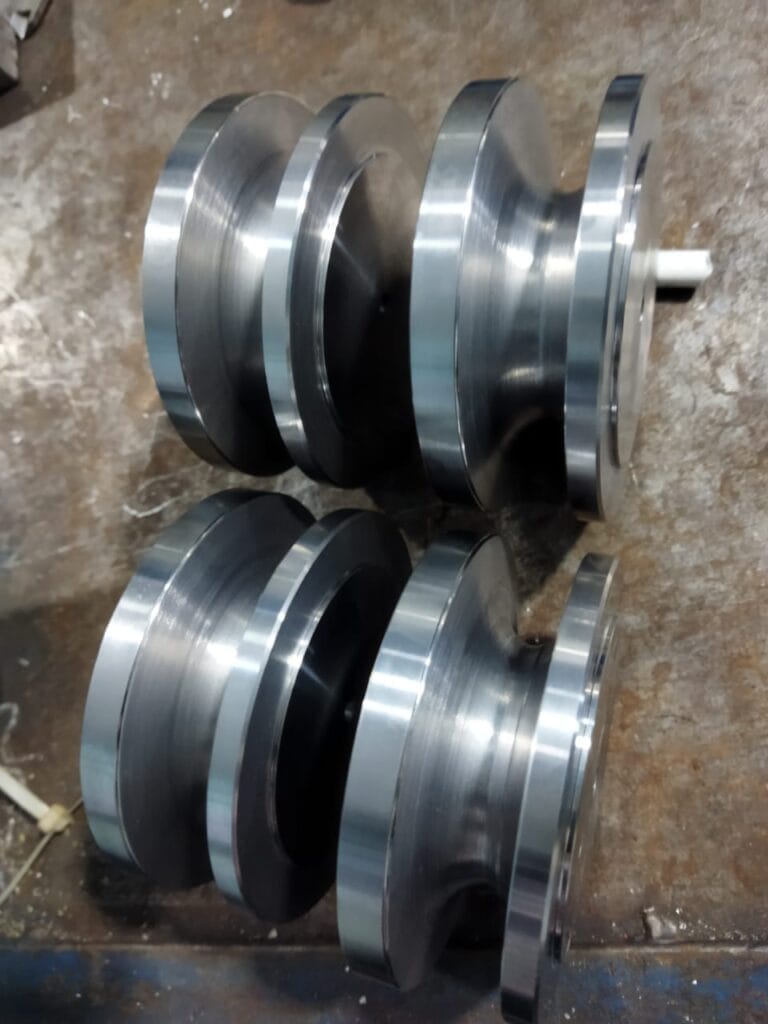
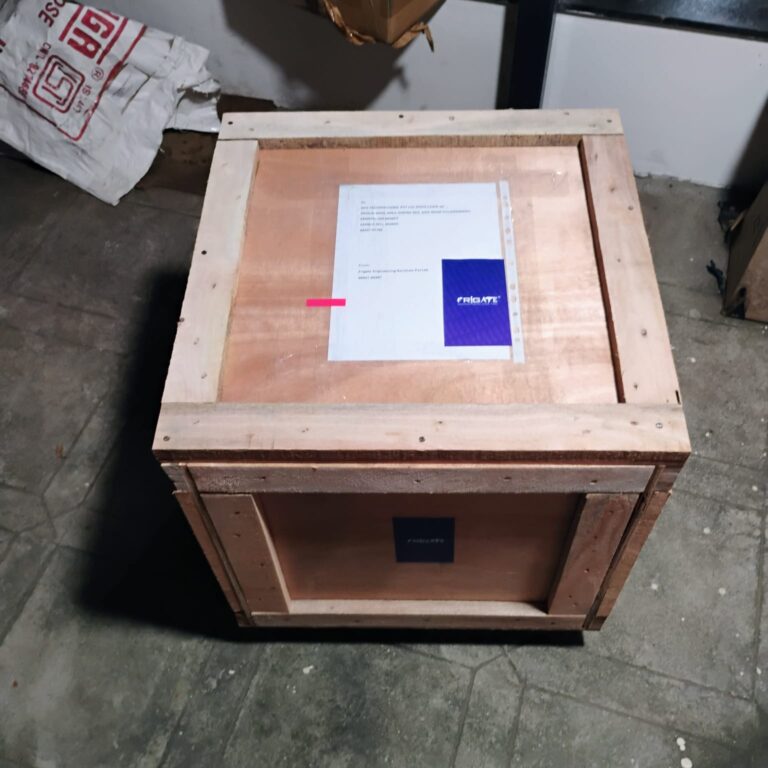
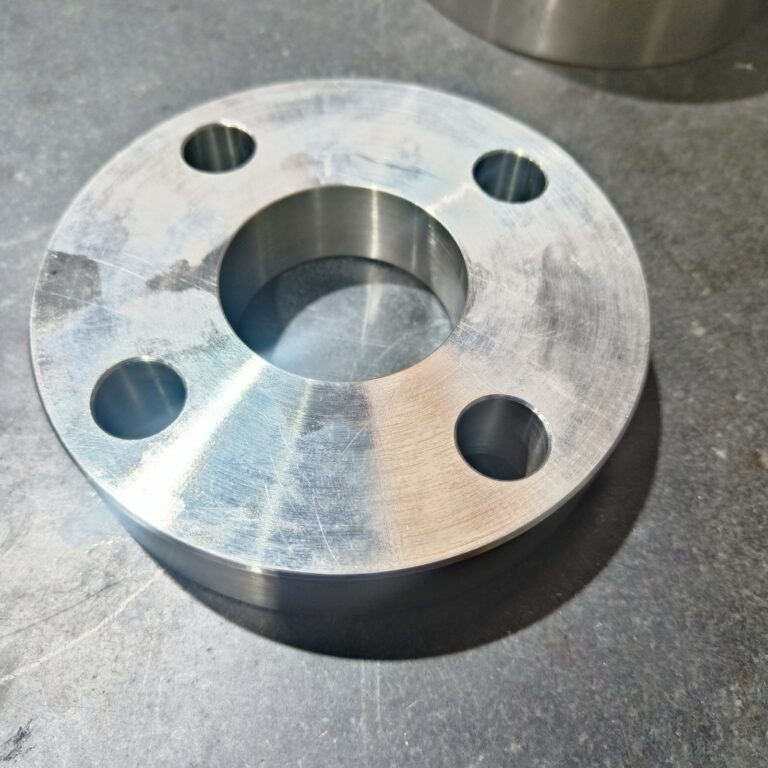
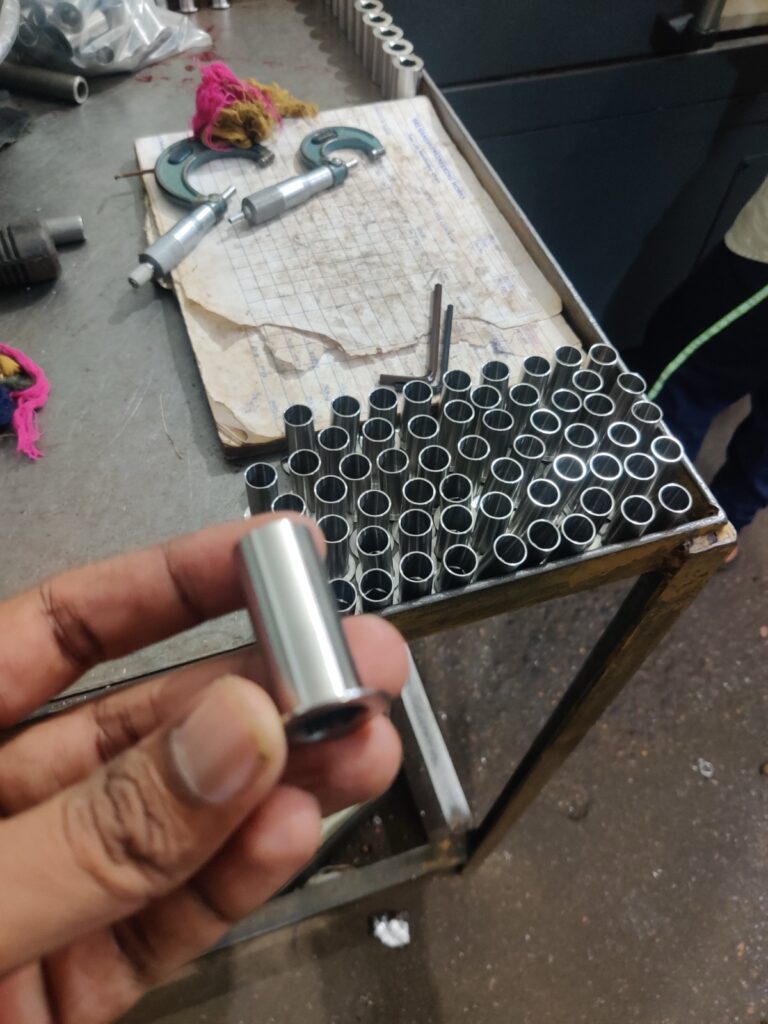
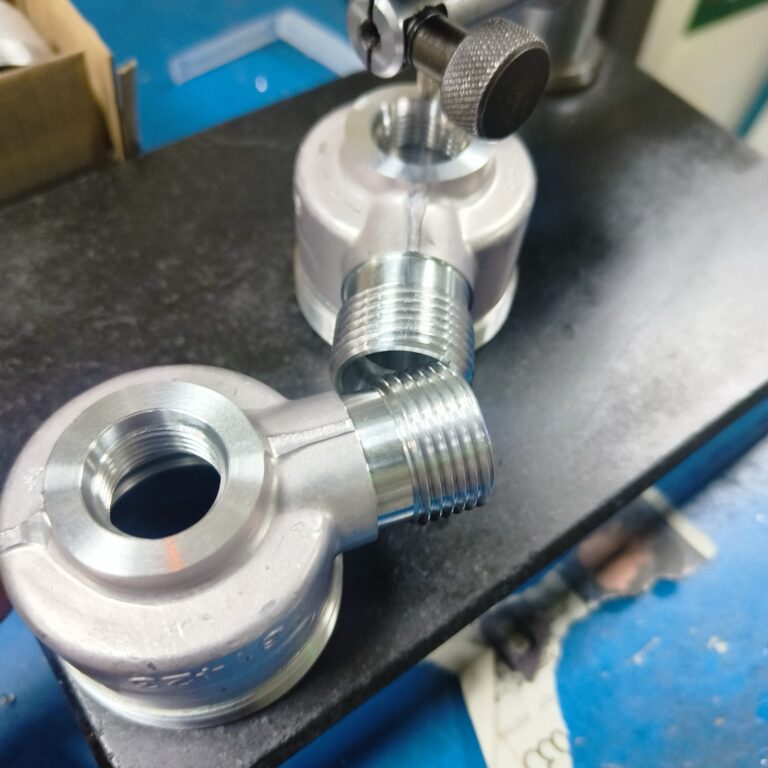
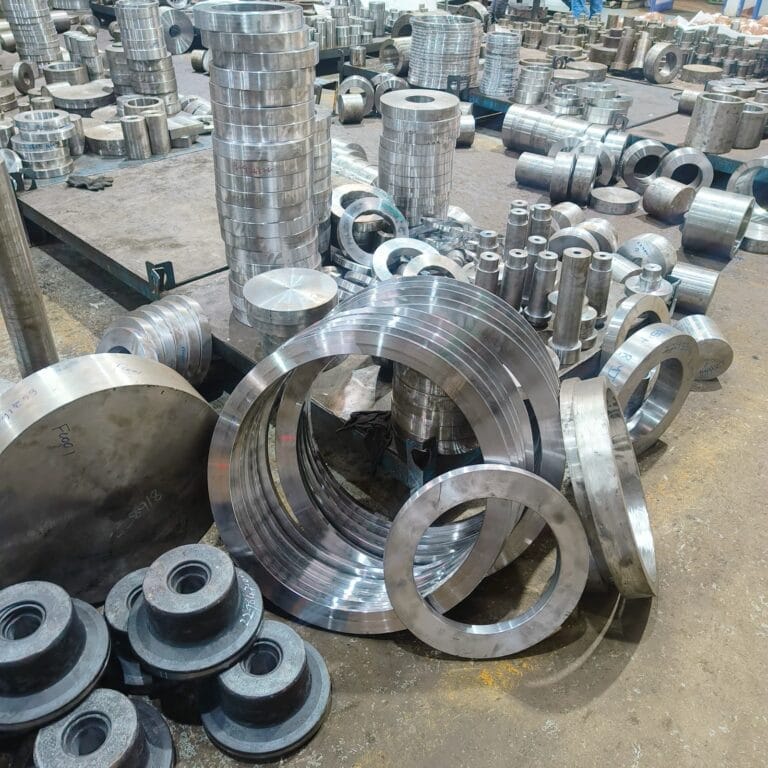
- One Stop Solution
End-to-End CNC Machining Solutions in South Carolina
Our technique combines frictionless linear guides, capacitance-based displacement sensors, and real-time position correction to ensure stable multi-directional machining.
Our pricing engine factors in multi-axis toolpath complexity, cutting zone temperature gradients, and dwell time adjustments to ensure accurate instant online quotes.
Our system combines laser profilometry, pulsed eddy current testing, and micro-CT scanning for comprehensive defect analysis.
- Optimized Workflow
From CNC Rapid Prototyping to Production in South Carolina
Frigate offers fast and precise CNC machining, from rapid prototyping to full-scale production, ensuring high-quality parts with quick turnaround times.

Rapid Prototyping
We fuse boronizing treatments with CNC machining to deliver prototypes with improved wear resistance, increased surface hardness, and superior oxidation protection.
- Instant quotes
- Instant DFM feedback
- Online quote and order management
- Live delivery tracking
Our team examines creep deformation rates, vacancy diffusion behavior, and dislocation climb mechanisms to enhance component longevity under thermal stress.

Production Orders
To reduce roughness, we ensure polished geometries in high-precision parts using laser-assisted polishing with controlled beam intensity.
- Dedicated project managers in your time zone
- Application engineers focused on DFM cost optimizations
- First Article Inspection (FAI) for quality assurance
- Supply chain support for materials and on-time delivery
Our system integrates machine learning models with adaptive workflow adjustments to improve throughput and minimize idle time during production cycles.
- Trusted Solutions
CNC Machining Solutions in South Carolina that You Can Trust
Our system integrates precision chucking with vacuum flow regulation to improve part stability. Atomic force microscopy measures thin-film roughness and structural consistency.
- Ultra-Tight Tolerances (±0.005mm)
- 5-Axis Machining for Complex Designs
- High-Speed Spindles (Up to 60,000 RPM)
- Adaptive Feed Rate Optimization
- Rigid Fixturing & Workholding


- Manufacturing Optimization
Get Started with Our CNC Machining Services
Our solution utilizes chromatic confocal sensors, shearography, and nanoindentation to assess micro-cracks, material defects, and dimensional discrepancies in precision assemblies.
Ultrasonic-Assisted Machining
High-frequency ultrasonic vibrations improve chip evacuation, reduce cutting forces, and minimize tool deflection.
Laser Ablation Profiling
Pulsed laser systems remove surface imperfections and correct dimensional inconsistencies with micron-level accuracy.
Carbon Nanotube Coatings
CNT-enhanced surface treatments improve heat dissipation and reduce friction in high-speed CNC operations.
- FAQ
Having Doubts? Our FAQ
Check all our Frequently Asked Questions in CNC Machining
Frigate uses multi-axis boring heads with digital feedback systems to properly position holes. Automated probing systems verify alignment during machining to prevent positional errors. This approach ensures accurate hole placement in parts with complex drilling patterns.
Frigate combines variable-helix end mills, rigid fixturing, and optimized tool path strategies to reduce tool deflection. This minimizes cutting force imbalance and ensures consistent feature dimensions. Such methods improve accuracy when machining deep cavities or thin-walled components.
Frigate utilizes precision fly cutting, dynamic spindle balancing, and adaptive feed rate control to enhance surface flatness. Real-time surface mapping detects minor irregularities during machining. These techniques ensure consistent flatness in parts requiring tight surface tolerances.
Frigate employs cryogenic cooling, mist lubrication, and thermal monitoring sensors to control heat buildup during machining. These systems improve thermal stability when working with heat-sensitive materials. This approach reduces distortion and maintains dimensional accuracy.
Frigate applies simultaneous 5-axis machining with synchronized tool orientation to achieve precise 3D contours. Real-time axis compensation adjusts cutting angles to maintain feature accuracy. This ensures smooth finishes and sharp edge definition in intricate designs.
We'd love to Manufacture for you!
Submit the form below and our representative will be in touch shortly.
LOCATIONS
Registered Office
10-A, First Floor, V.V Complex, Prakash Nagar, Thiruverumbur, Trichy-620013, Tamil Nadu, India.
Operations Office
9/1, Poonthottam Nagar, Ramanandha Nagar, Saravanampatti, Coimbatore-641035, Tamil Nadu, India. ㅤ
Other Locations
- Bhilai
- Chennai
- USA
- Germany