Decentralized Control Architectures for High-Speed Robotic Manufacturing
Edge processing enables real-time force, speed, and position control, reducing defects without centralized systems.
Frigate Automation for Scalable Manufacturing
Predictive Maintenance with Machine Learning
Machine learning analyzes sensor data to forecast failures, enabling proactive maintenance that maximizes uptime and extends equipment life.
Modular Decentralized Control
Microservice-based, distributed robotic cells enable scalable, flexible automation that adapts quickly to changing production needs with minimal complexity.
Cyber-Physical Security
Hardware-enforced trust zones and encrypted protocols with real-time threat detection protect automation systems from cyber-attacks and ensure data integrity.
Our Clients
Trusted by Engineers and Purchasing Leaders
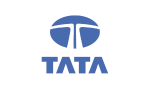
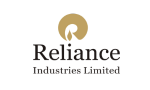


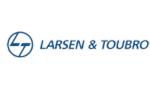
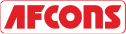


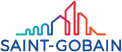

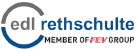

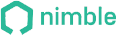
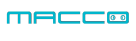









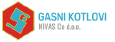
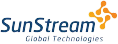

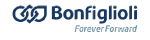


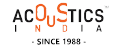
Optimize Energy Efficiency in Robotic Operations
Reducing energy consumption in high-throughput automation requires intelligent scheduling, energy recovery mechanisms, and active load balancing across robotic systems.
Deploy energy-aware task distribution algorithms that flatten peak load demand by up to 40% through synchronized robotic cell coordination.
Integrate regenerative braking systems in servo actuators to recover up to 20% of kinetic energy during deceleration phases.
Monitor real-time power draw per robot axis using embedded sensors and optimize cycle timing to reduce total energy per part by 15%.

Enhance Robotic Trajectory Precision with AI Optimization
Minimizing mechanical wear and reducing cycle time in robotic systems requires adaptive motion planning guided by AI-driven optimization techniques.
Use reinforcement learning to continuously improve motion trajectories, reducing cycle time by up to 18% without compromising precision.
Optimize joint movements to minimize high-torque segments, extending actuator lifespan by 25% under high-load conditions.
Incorporate environmental and collision constraints into planning models, maintaining path stability in unstructured manufacturing zones.

Integrate Autonomous Quality Assurance into Robotic Workflows
Inline inspection systems embedded within robotic platforms enable real-time detection of defects, improving yield and enabling immediate process correction.
Deploy cameras with up to 5 µm optical resolution for dimensional and surface flaw detection during live operation cycles.
Use inspection data to adjust weld force, path deviation, or feed rate within 200 ms of anomaly detection.
Embed multi-spectral sensors and laser profilers to inspect critical tolerances without interrupting part flow, reducing scrap by 22%.

Our Machined Products
We support your production needs with CNC-machined parts, subassemblies, and performance-critical components.
- Real Impact
Words from Clients
See how global OEMs and sourcing heads describe their experience with our scalable execution.
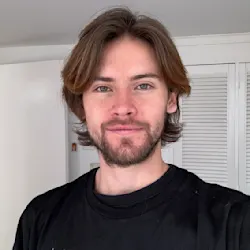
“Quick turnaround and solid quality.”
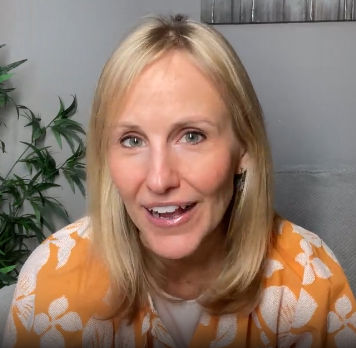
“The instant quote tool saved us time, and the parts were spot-on. Highly recommend Frigate!”
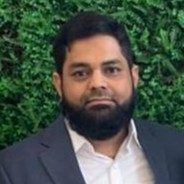
“I would strongly recommend Frigate to anyone who wants to do Rapid Prototyping, and take their ideas to manufacturing. One firm doing all kinds of Product Development!”
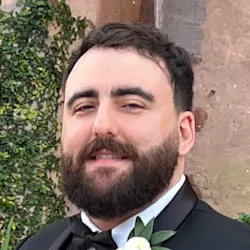
“Great service, fair price, and the parts worked perfectly in our assembly.”
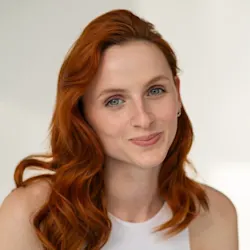
“Top-notch machining and fast shipping. Very satisfied with the results.”
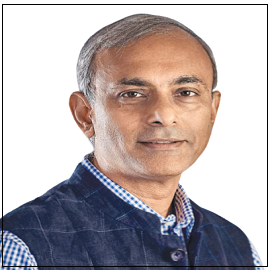
“The next disruption is happening in Prototyping & Manufacturing on-demand and Frigate is leading the way! I personally believe the Frigate's way of IIOT enabled cloud platform with Al.”
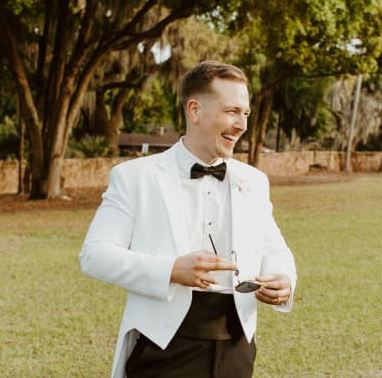
“Frigate delivered high-quality parts at a competitive price. The instant quote tool is a huge plus for us!”

“We appreciate the precision and quality of the machined components in the recent delivery—they meet our specifications perfectly and demonstrate Frigate’s capability for excellent workmanship.”
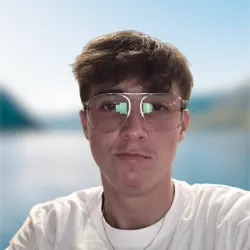
“Flawless execution from quote to delivery.”

“I am absolutely happy to work with supplier like Frigate who were quite proactive & result oriented . Frigate has high willingness team who has strong know how & their passion towards the products & process were absolutely thrilling.”
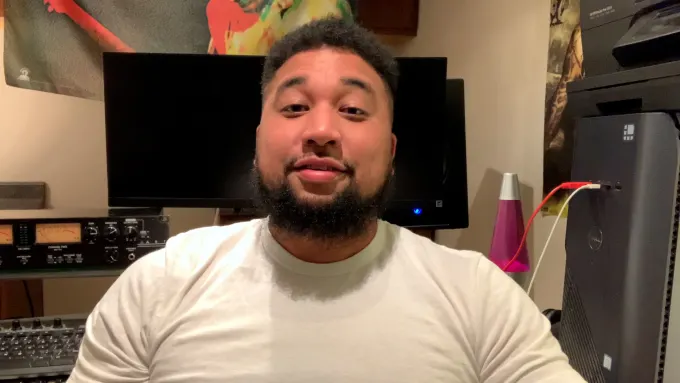
“The precision on these parts is impressive, and they arrived ahead of schedule. Frigate’s process really stands out!”
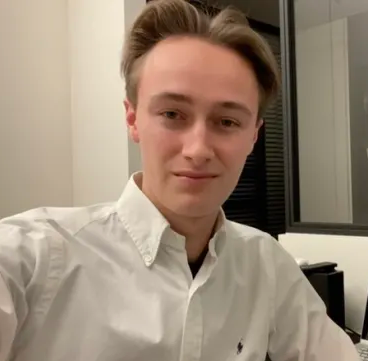
“Parts were exactly as spec’d, and the instant quote made budgeting a breeze.”
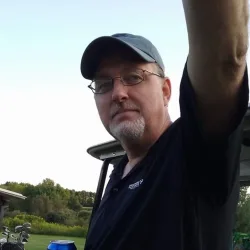
“Good value for the money.”
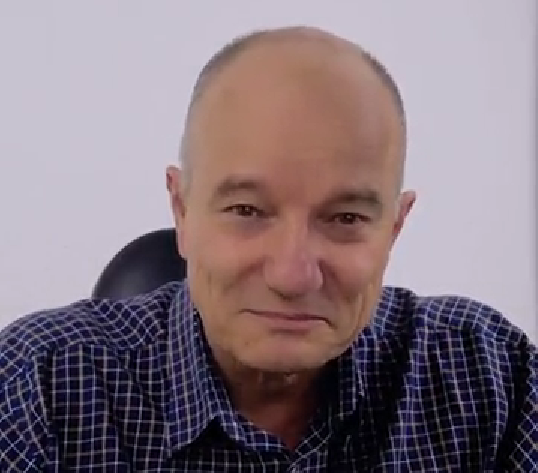
“The finish was perfect, and the team was easy to work with.”

“Working with Frigate has been great. Their proactive, results-driven approach and expertise shine through in every project. It's been a pleasure collaborating with them.”

"We are highly satisfied with the timely delivery and quality of the MIG Welding Cable from Frigate. Their attention to detail, secure packaging, and quick responsiveness stood out. We confidently recommend Frigate Engineering Services Pvt. Ltd. as a reliable manufacturing partner."
- We export to 12+ countries
Frigate’s Global Presence
Frigate takes pride in facilitating “Make in India for the globe“. As our global network of Frigaters provides virtually limitless capacity, and through our IoT enabled platform your parts go directly into production. By digitally and technologically enabling “the silent pillars of the economy” MSME and SME manufacturing industries, we are able to tap the huge potential for manufacturing to bring the best results for our clients.

100,000+
Parts Manufactured
250+
Frigaters
2000+
Machines
450+
Materials
25+
Manufacturing Process
- Solid Progress
How You Benefit with Us
Frigate brings stability, control, and predictable performance to your sourcing operations through a structured multi-vendor system.
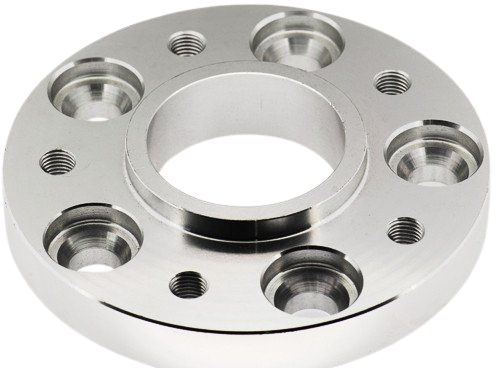
2.8X
Sourcing Cycle Speed
Frigate’s pre-qualified network shortens decision time between RFQ and PO placement.
94%
On-Time Delivery Rate
Structured planning windows and logistics-linked schedules improve project-level delivery reliability.
4X
Multi-Part Consolidation
We enable part family batching across suppliers to reduce fragmentation.
22%
Quality Rejection Rate
Multi-level quality checks and fixed inspection plans lower non-conformities.
30%
Procurement Costs
Optimized supplier negotiations and bulk order strategies reduce your overall sourcing expenses.
20%
Manual Processing Time
Automation of sourcing and supplier management significantly reduces time spent on manual tasks.
Other Industries We Serve
We deliver machining support across sectors that require consistency, material reliability, and tight dimensional control.
Get Clarity with Our Manufacturing Insights
Frigate uses advanced simulation models to map spindle torque and power curves based on real-time sensor data and material feedback. This helps match tool engagement angles and cutting speeds dynamically with part geometry and material hardness. The system ensures that the spindle operates close to peak efficiency without overloading. This method reduces cycle time while extending tool life during high-variability production runs.
Frigate integrates closed-loop thermal compensation systems that monitor ambient temperature, coolant flow, and internal machine heat signatures. These systems apply real-time offsets to machine positioning using predictive models based on part mass and fixture conductivity. By correcting for thermal drift at the micron level, part dimensions remain stable across long production cycles. This is especially useful for large structural components in wind, rail, or off-road applications.
Frigate runs kinematic simulations using high-resolution digital twins that replicate actual machine axes, tool deflection, and part fixturing conditions. Complex 5-axis paths are digitally tested for gouging, overcut, and surface chatter before physical machining begins. This ensures both surface finish quality and structural integrity on non-prismatic, high-stress features. Toolpaths are auto-adjusted for optimal chip load and cutter orientation per region.
Frigate applies pre-compensation strategies based on empirical springback data for specific titanium and aluminum alloy batches. Initial roughing operations include deflection-controlled cuts, and final passes incorporate inverse-deformed geometries. These profiles are based on historic process signatures stored in Frigate’s machining knowledge base. As a result, tight tolerances are maintained even in parts with thin walls or complex ribbing.
Frigate uses inline acoustic emission sensors and vibration analysis tools directly mounted on the spindle housing. These sensors track frequency deviations associated with flank wear and notch formation. Signals are compared against baseline tool condition models, enabling predictive tool replacement scheduling. This approach avoids unscheduled downtimes and preserves surface quality in critical parts without interrupting the production cycle.
We'd love to Manufacture for you!
Submit the form below and our representative will be in touch shortly.
LOCATIONS
Registered Office
10-A, First Floor, V.V Complex, Prakash Nagar, Thiruverumbur, Trichy-620013, Tamil Nadu, India.
Operations Office
9/1, Poonthottam Nagar, Ramanandha Nagar, Saravanampatti, Coimbatore-641035, Tamil Nadu, India. ㅤ
Other Locations
- Bhilai
- Chennai
- USA
- Germany