CNC Machining for Oil & Gas Equipment
Frigate machines complex alloys like Inconel 718, Super Duplex, and MP35N using thermal load modeling to prevent phase distortion and microcracking. Surface integrity is validated post-process with EBSD and residual stress mapping to ensure grain stability.
Our Clients





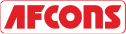

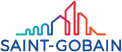


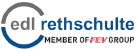

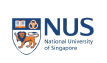
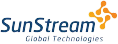

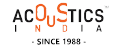




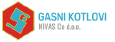
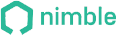
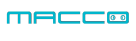












- Precision at Every Stage
Thermo-Mechanical Machining of Refractory Alloys
Advanced strategies control thermal loads and surface integrity to reduce microcracks and maintain grain structure in heat-affected zones.
Submicron Machining Accuracy
Submicron precision is achieved using 5-axis CNC systems with kinematic calibration, volumetric compensation, and dual-probe alignment, maintaining tolerances under 0.0015 mm across complex contours and rotational axes.
Thermal Distortion Control
Thermal distortion is minimized by applying predictive expansion models, adaptive toolpath corrections, and isothermal machining strategies, ensuring dimensional integrity in large or heat-sensitive precision components.
Engineered Surface Finishes
Surface finishes are optimized using synchronized multi-stage polishing, real-time tool wear feedback, and interferometric inspection, achieving consistent Ra values for sealing, wear resistance, or biocompatibility-critical surfaces.
- Step-by-Step Machining Approach
Our CNC Machining Process
Every component is machined through a controlled sequence of thermal, mechanical, and dimensional operations tailored to the material and application.


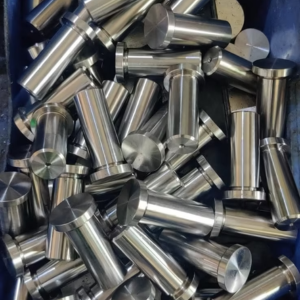

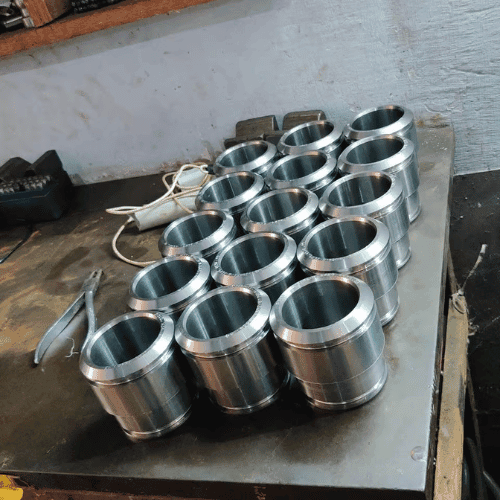

Advanced algorithms optimize tool paths, minimizing tool wear, reducing cycle times, and improving surface finishes. This involves strategically planning the sequence of movements and cuts to enhance efficiency.
Modern CNC machines often utilize 5-axis or even 6-axis capabilities, allowing for complex geometries and intricate shapes. This reduces the need to reposition the part, ensuring higher accuracy and a more refined finish.
CNC machines may integrate adaptive cutting strategies, where cutting conditions (speed, feed, depth of cut) adjust dynamically based on real-time sensor feedback or cutting force monitoring. This helps prevent tool breakage and ensures optimal material removal rates.
Specialized techniques like high-speed machining enable faster spindle speeds and advanced feed rates. This increases material removal rates while maintaining fine tolerances and reducing thermal distortion.
Some CNC setups incorporate in-process measuring systems (like laser scanners or probe-based systems) to check the part’s dimensions as it’s being machined. These systems can send real-time data back to the machine, allowing for automatic adjustments during production.
CNC machines with automated tool changers enhance efficiency by switching tools automatically without operator intervention. This allows for uninterrupted multi-operation machining without downtime, improving productivity in complex jobs with several cutting tools.
- Real Impact
Words from Clients
See how global OEMs and sourcing heads describe their experience with our scalable execution.
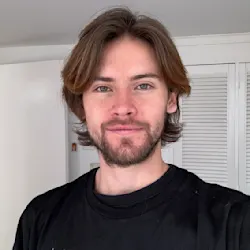
“Quick turnaround and solid quality.”
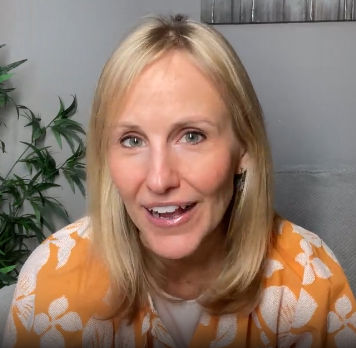
“The instant quote tool saved us time, and the parts were spot-on. Highly recommend Frigate!”
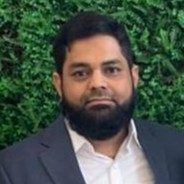
“I would strongly recommend Frigate to anyone who wants to do Rapid Prototyping, and take their ideas to manufacturing. One firm doing all kinds of Product Development!”
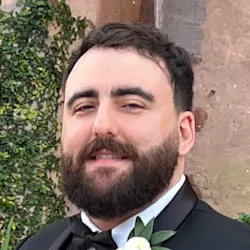
“Great service, fair price, and the parts worked perfectly in our assembly.”
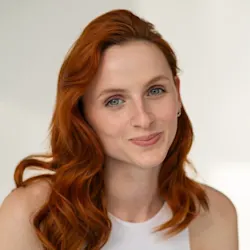
“Top-notch machining and fast shipping. Very satisfied with the results.”
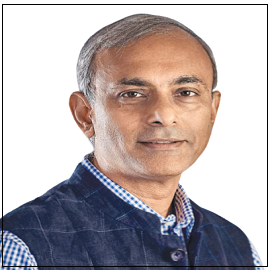
“The next disruption is happening in Prototyping & Manufacturing on-demand and Frigate is leading the way! I personally believe the Frigate's way of IIOT enabled cloud platform with Al.”
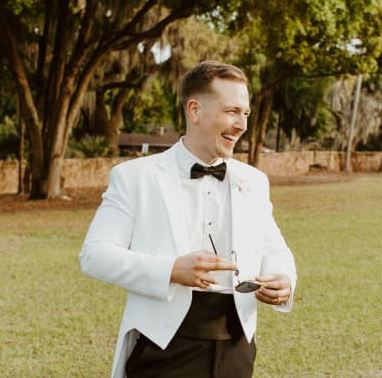
“Frigate delivered high-quality parts at a competitive price. The instant quote tool is a huge plus for us!”

“We appreciate the precision and quality of the machined components in the recent delivery—they meet our specifications perfectly and demonstrate Frigate’s capability for excellent workmanship.”
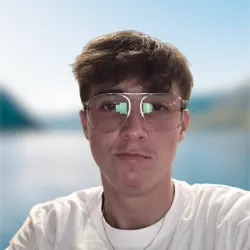
“Flawless execution from quote to delivery.”

“I am absolutely happy to work with supplier like Frigate who were quite proactive & result oriented . Frigate has high willingness team who has strong know how & their passion towards the products & process were absolutely thrilling.”
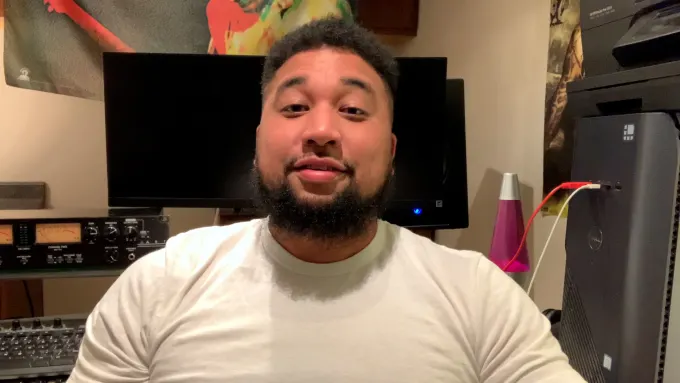
“The precision on these parts is impressive, and they arrived ahead of schedule. Frigate’s process really stands out!”
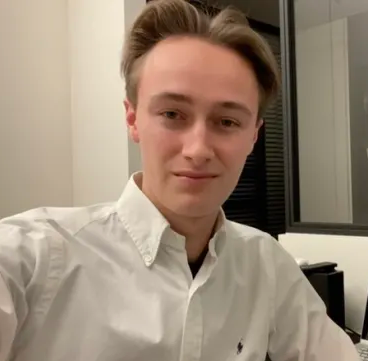
“Parts were exactly as spec’d, and the instant quote made budgeting a breeze.”
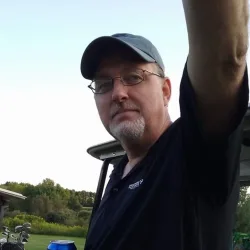
“Good value for the money.”
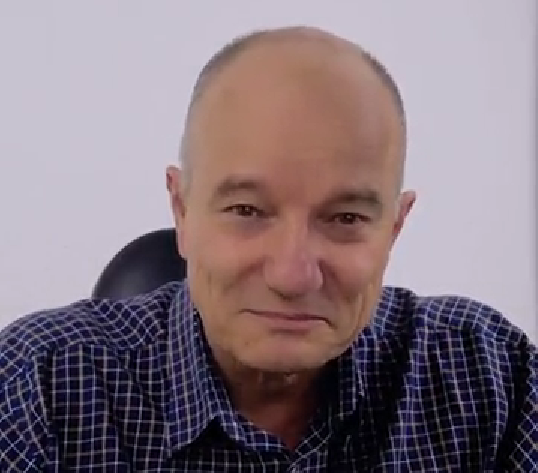
“The finish was perfect, and the team was easy to work with.”

“Working with Frigate has been great. Their proactive, results-driven approach and expertise shine through in every project. It's been a pleasure collaborating with them.”

"We are highly satisfied with the timely delivery and quality of the MIG Welding Cable from Frigate. Their attention to detail, secure packaging, and quick responsiveness stood out. We confidently recommend Frigate Engineering Services Pvt. Ltd. as a reliable manufacturing partner."
- Surface Finish
Flawless Finishes for CNC Machining Parts
Surface integrity is governed by tool geometry, feed modulation, and coolant delivery to reduce sub-surface deformation. Post-process treatments are applied selectively based on application-specific stress or contamination thresholds.
Anodizing
Give your aluminum parts a tough, corrosion-resistant shield with anodizing, reaching surface hardness up to HV 500, while enhancing electrical insulation and durability.
Mechanical Finishing
Smooth out imperfections and refine surfaces to Ra 0.2 µm or better with mechanical finishing techniques like grinding, polishing, and bead blasting.
Heat Treatment
Boost material strength and hardness by heat treating parts at temperatures up to 1100°C, ensuring they meet the mechanical demands of your application.
Electroplating
Add protective or functional metal coatings with electroplating, delivering consistent layers as precise as ±2 µm for improved corrosion resistance and conductivity.
Our Machined Products
We support your production needs with CNC-machined parts, subassemblies, and performance-critical components.
- Machining Capabilities
Multi-Axis Machining Solutions for Complex Oilfield Geometries
High-performance CNC solutions engineered for critical oilfield parts with tight tolerances, corrosion resistance, and demanding geometries.

CNC Milling
We perform structural cavity milling, flange surface routing, and threaded bore creation for pressure-containing components.
- Spindle speeds up to 18,000 RPM with adaptive feed rate control
- Precision milling of stainless alloys like 17-4PH and duplex steels

CNC Turning
We produce threaded connectors, mandrels, and seal housings with strict runout and concentricity tolerances.
- Turning lengths up to 1200 mm with steady rest support
- Y-axis turning for offset holes, relief cuts, and undercuts
- Material Scope
Advanced Materials for Demanding Environments
Oil and gas CNC machining requires materials that handle extreme pressure, corrosion, and thermal loads. Our machining process supports high-performance alloys suited to these harsh conditions.
- Withstands up to 25,000 psi operating pressure in downhole and subsea assemblies.
- Retains dimensional stability at temperatures above 400°F.
- Supports sour gas resistance with ≤0.1% hydrogen sulfide exposure.
A2 Tool Steel is a high-carbon, high-chromium steel known for its toughness and wear resistance. It’s ideal for producing durable, high-strength parts that can withstand heavy use.
Aluminum is a lightweight, corrosion-resistant metal with good machinability. Because of its strength-to-weight ratio, it’s commonly used in aerospace, automotive, and various industrial applications.
Brass is a copper-zinc alloy known for its machinability and corrosion resistance. It’s used for components requiring precise detailing and good mechanical properties.
Bronze is a copper-tin alloy with excellent wear resistance and strength. It’s often used for bushings, bearings, and other friction-prone components.
Cast Iron is known for its high wear resistance and machinability. It’s used in heavy-duty applications such as machinery parts and engine components.
Copper offers excellent thermal and electrical conductivity. It’s used in applications requiring heat dissipation or electrical conductivity, such as electronic components.
Steel is a versatile material known for its strength and durability. It’s used in various applications, from construction to automotive parts.
Titanium is a lightweight, high-strength metal with excellent corrosion resistance. It’s used in aerospace, medical implants, and high-performance engineering applications.
Stainless Steel offers high corrosion resistance and strength. It’s widely used in applications ranging from kitchen equipment to industrial machinery.
Zinc is a ductile and corrosion-resistant metal known for its excellent machinability, especially in its alloy forms. It's often used for components requiring intricate details, good surface finish, and precise dimensions, commonly found in automotive, hardware, and electrical applications.
- Machining Dynamics
Key Highlights
CNC machining ensures dimensional integrity and material integrity for critical oilfield components. It supports high-strength alloys and complex geometries for extreme downhole and topside conditions.
- Maintains ±0.002 mm tolerance for high-pressure sealing surfaces and threaded connections in BOPs and manifolds.
- Enables 5-axis contouring for internal porting in valve blocks and mud pump housings.
- Supports duplex stainless steel, Inconel, and Hastelloy machining for sour gas and high-salinity resistance.
- Achieves deep boring up to 1000 mm with internal cooling to reduce tool deflection and thermal drift.
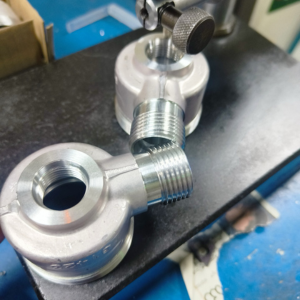
- Standards Driven
Compliance & Certification
CNC machining for oil & gas equipment demands strict compliance with global engineering and quality standards. Every part must perform reliably under extreme pressure and corrosive environments.
- Machined components follow industry-specific performance and material guidelines.
- Dimensional checks and testing ensure conformance to design intent.
- Documentation and traceability are maintained from raw material to final inspection.
- Manufacturing practices undergo regular audits to verify process integrity.
We comply with API Q1 standards, ensuring our CNC machining processes meet quality management requirements for oilfield equipment manufacturing.
We are ISO 9001:2015 certified, supporting consistent CNC machining process control, quality assurance, and traceable documentation for critical components.
We machine components in accordance with API 6A and 6D standards for valves, flanges, and pressure control assemblies.
We use NACE-compliant materials to machine parts that resist sulfide stress cracking in sour gas service environments.
We follow ASME codes for pressure piping and flanges, ensuring CNC-machined components meet dimensional and structural specifications.
We provide machining for materials certified by DNV or ABS, supporting offshore equipment with full traceability and documentation.
- We export to 12+ countries
Frigate’s Global Presence
Frigate takes pride in facilitating “Make in India for the globe“. As our global network of Frigaters provides virtually limitless capacity, and through our IoT enabled platform your parts go directly into production. By digitally and technologically enabling “the silent pillars of the economy” MSME and SME manufacturing industries, we are able to tap the huge potential for manufacturing to bring the best results for our clients.

100,000+
Parts Manufactured
250+
Frigaters
2000+
Machines
450+
Materials
25+
Manufacturing Process

- Quality Standards
Quality Testing for Mold Machining Projects
To measure the roundness of cylindrical features, ensuring they meet tolerance requirements.
To check internal surfaces for flatness, critical for sealing and assembly purposes.
To identify burrs or sharp edges that may affect assembly or safety.
To ensure that complex profiles (e.g., contours, curves) conform to design specifications.
To check the topography and texture of the surface, ensuring it meets the required specifications for function or aesthetics.
To verify that the surface hardness depth meets the required specifications for wear resistance.
To measure internal stresses that could lead to deformation or failure during or after machining.
To verify grain structure, inclusions, and material consistency, ensuring the part meets performance requirements.
- Machined Component Showcase
CNC Machining Parts
We maintain stringent dimensional consistency through high-resolution spindle encoders, thermal drift compensation, and ultra-fine servo motor tuning. Delivering components engineered to withstand extreme mechanical stresses and fluctuating thermal environments.
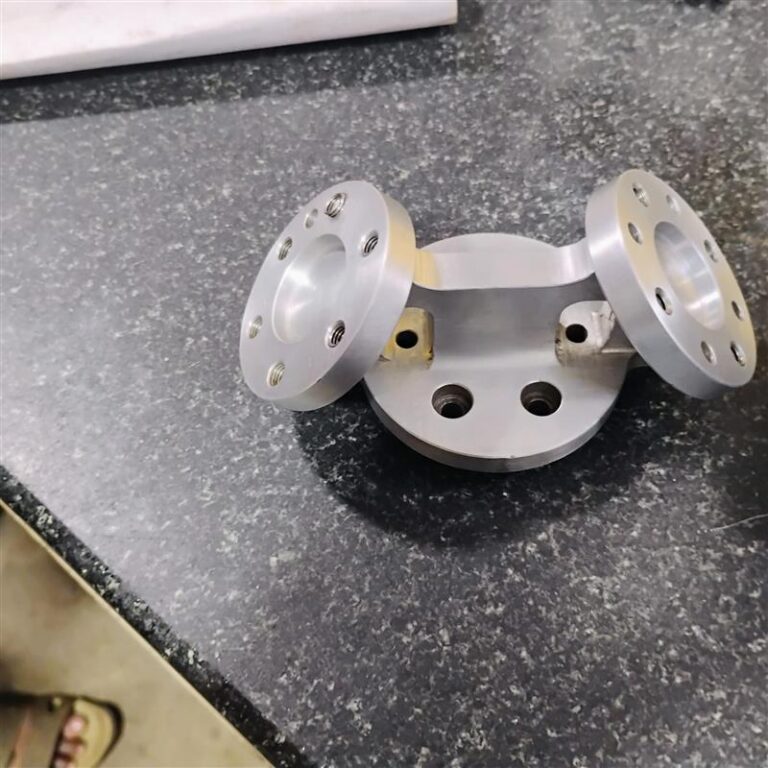
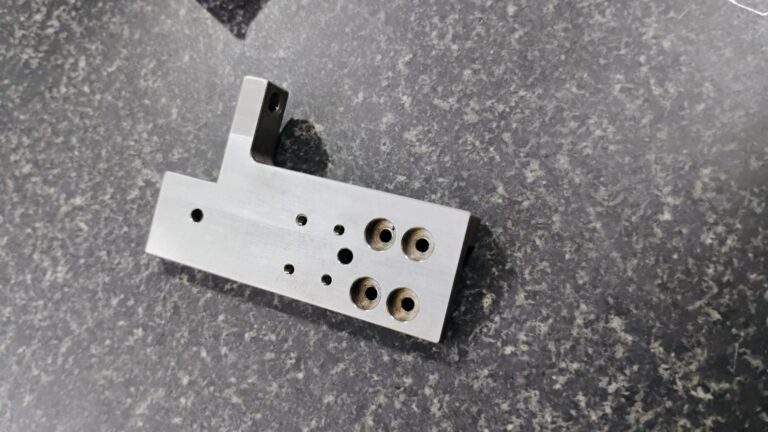
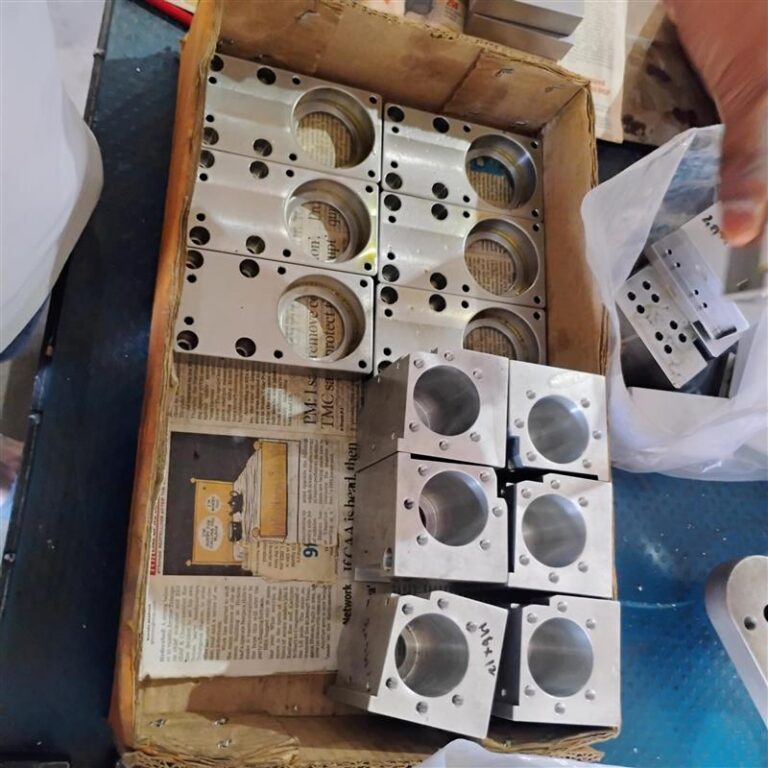
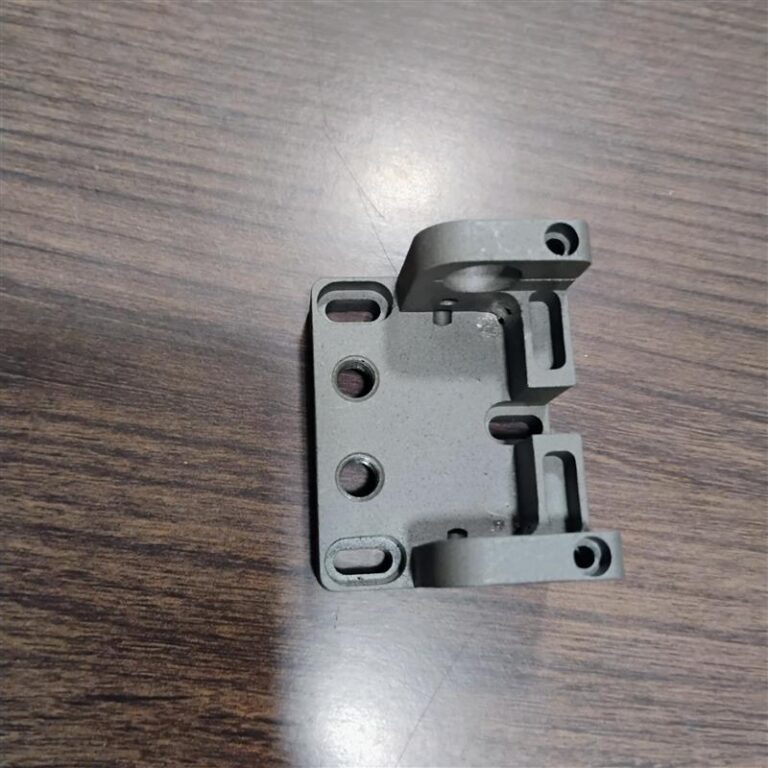
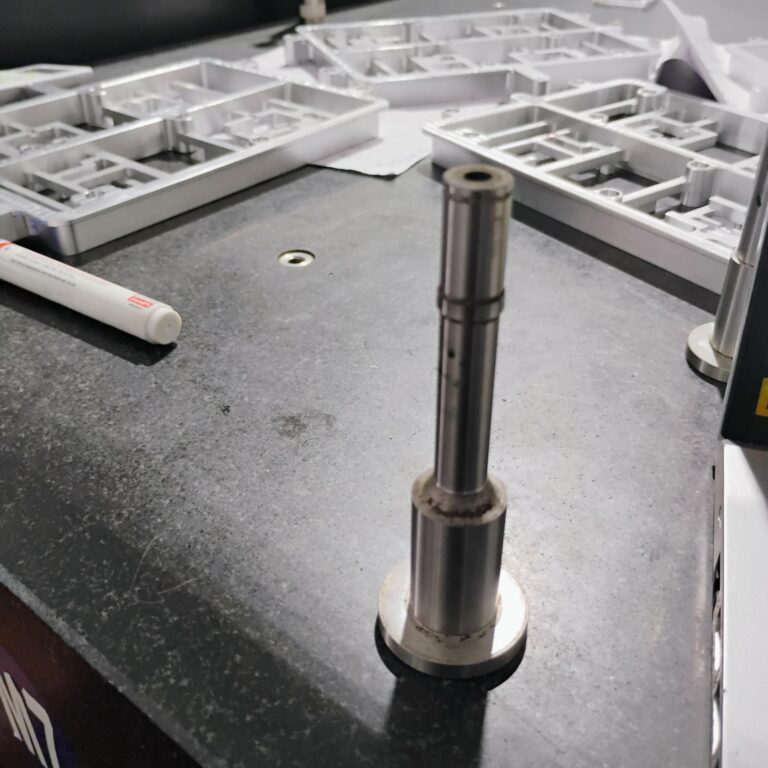
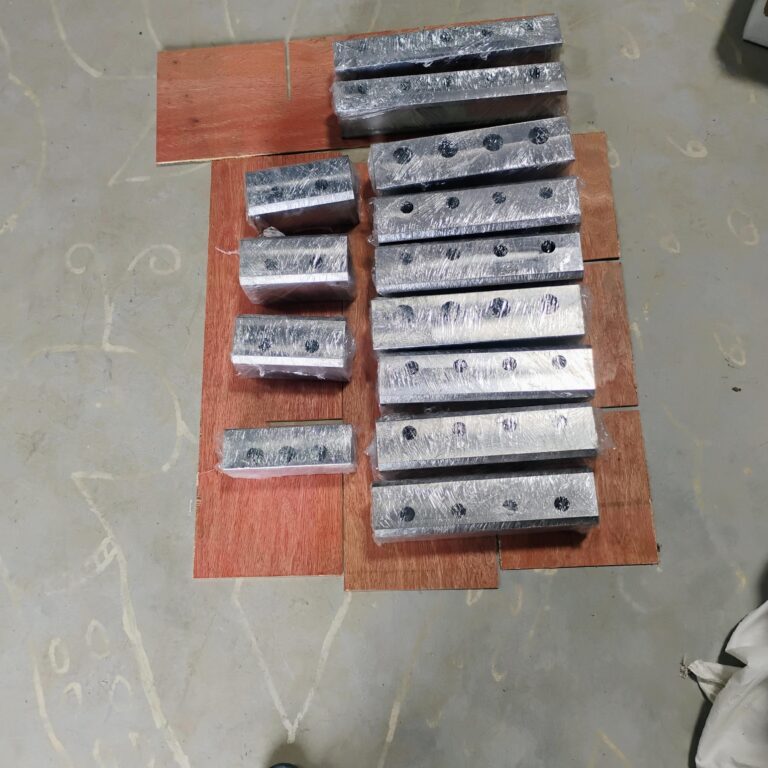
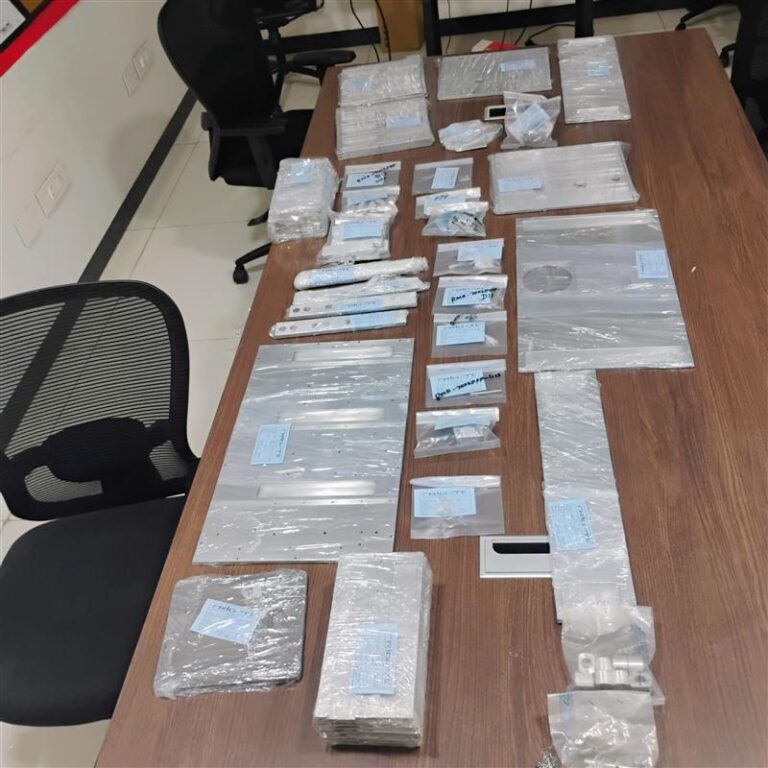

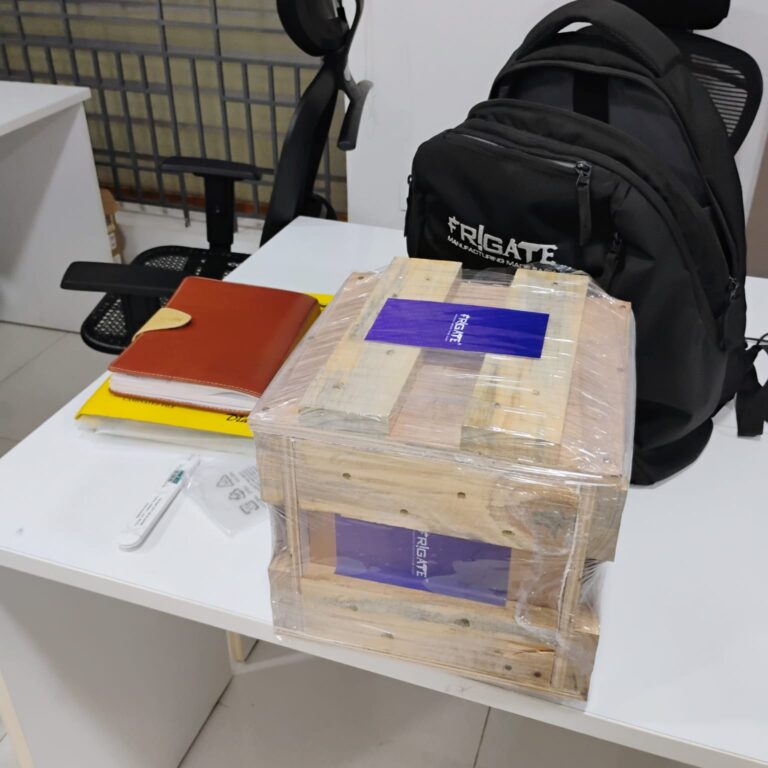


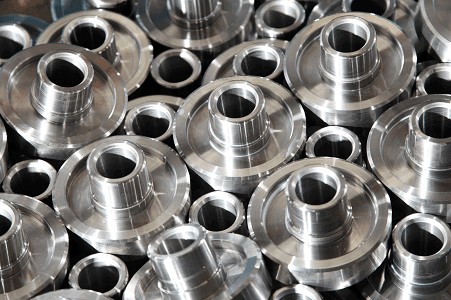
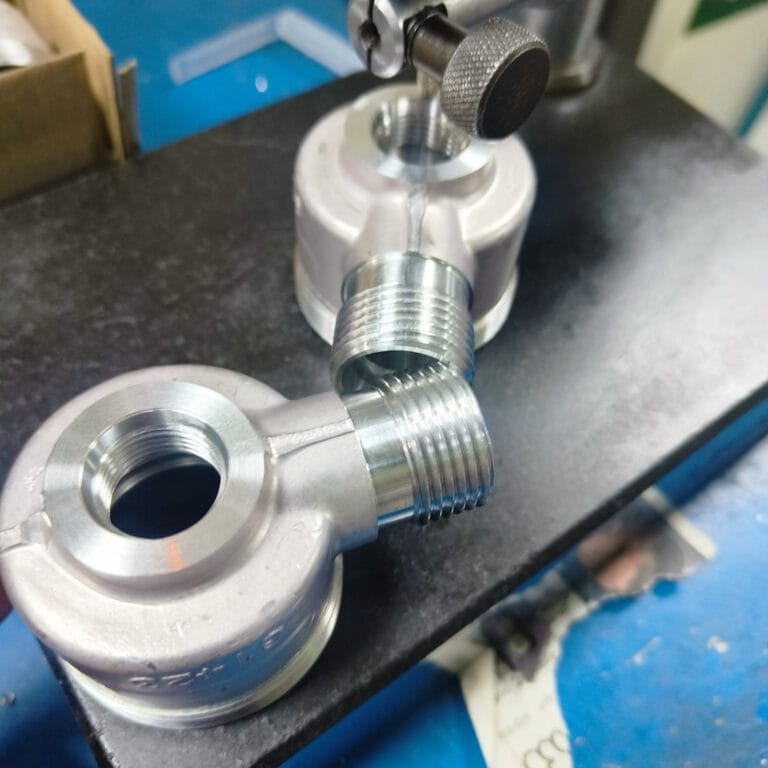
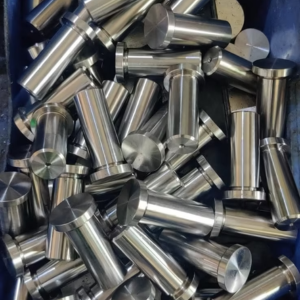
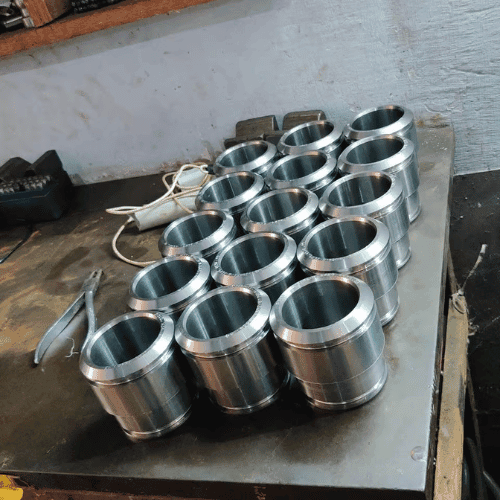
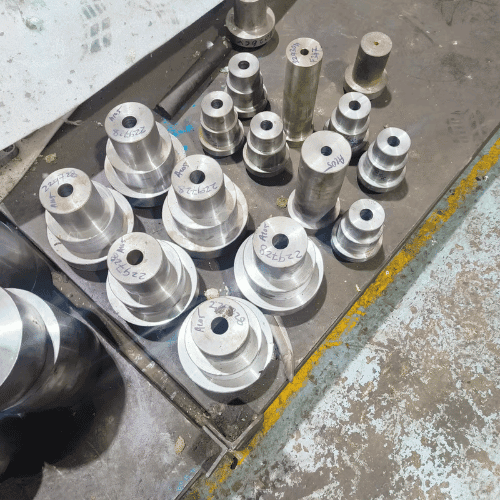
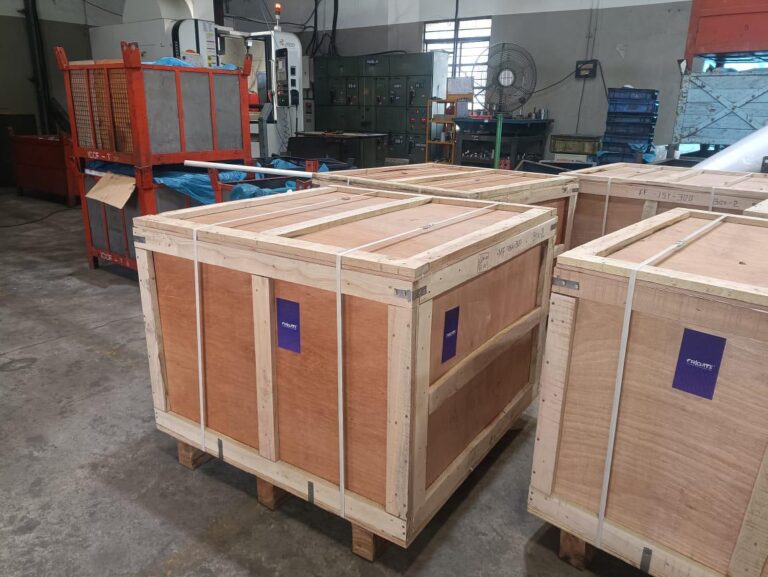
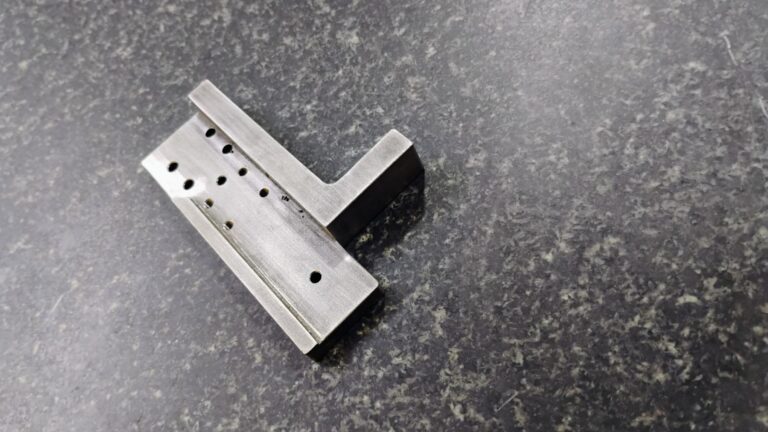
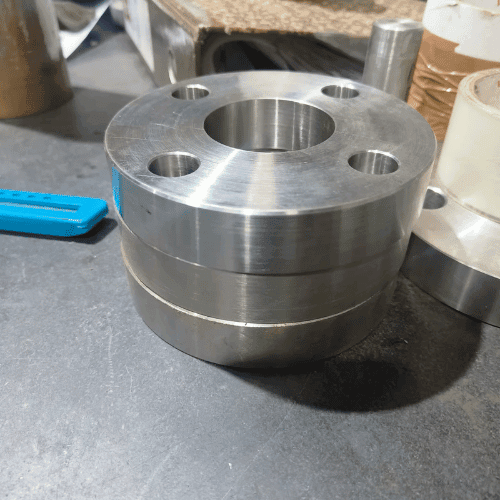
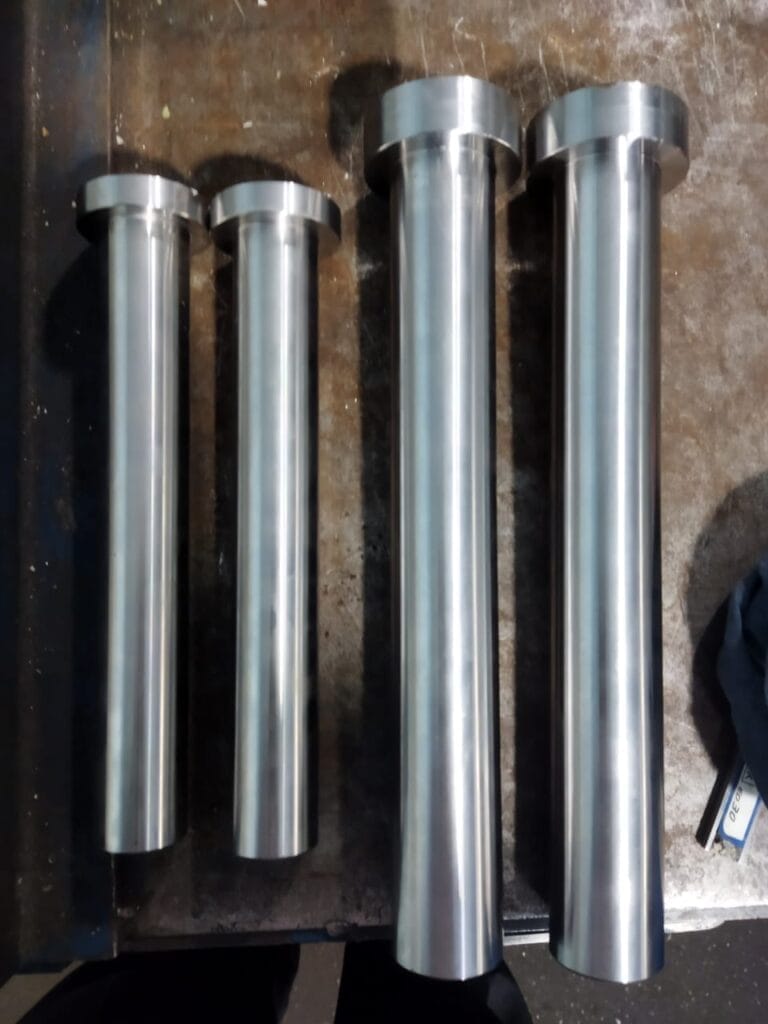

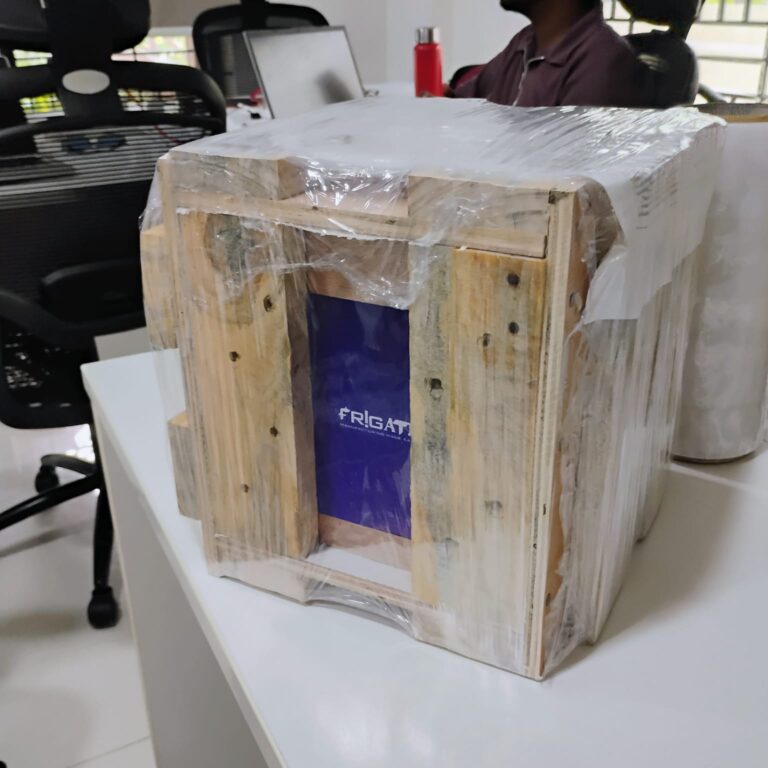

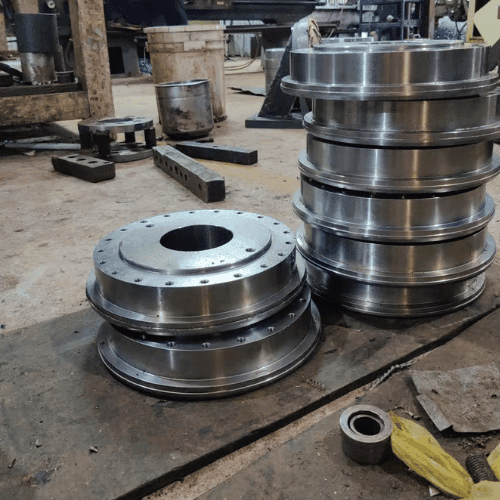
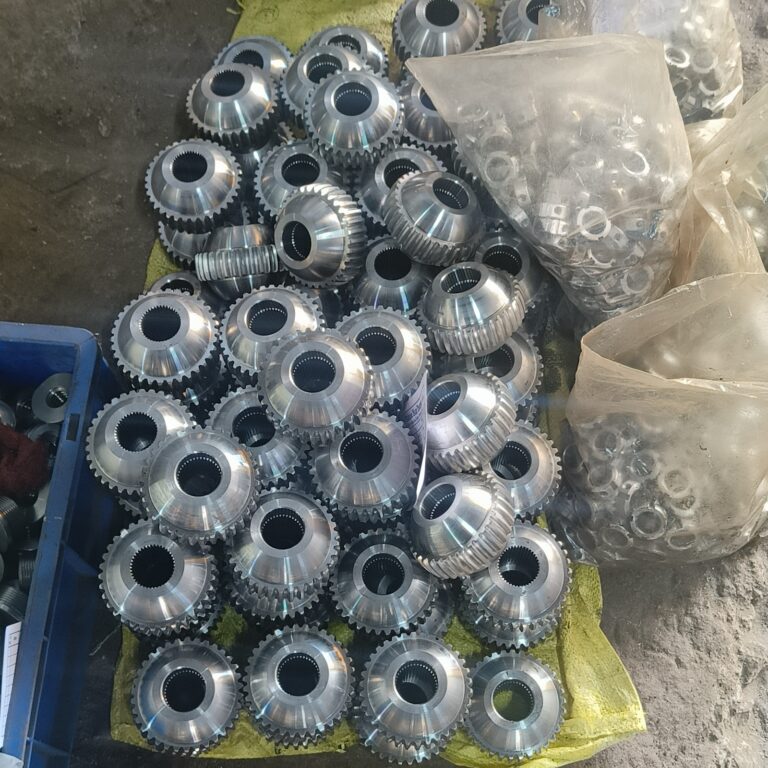
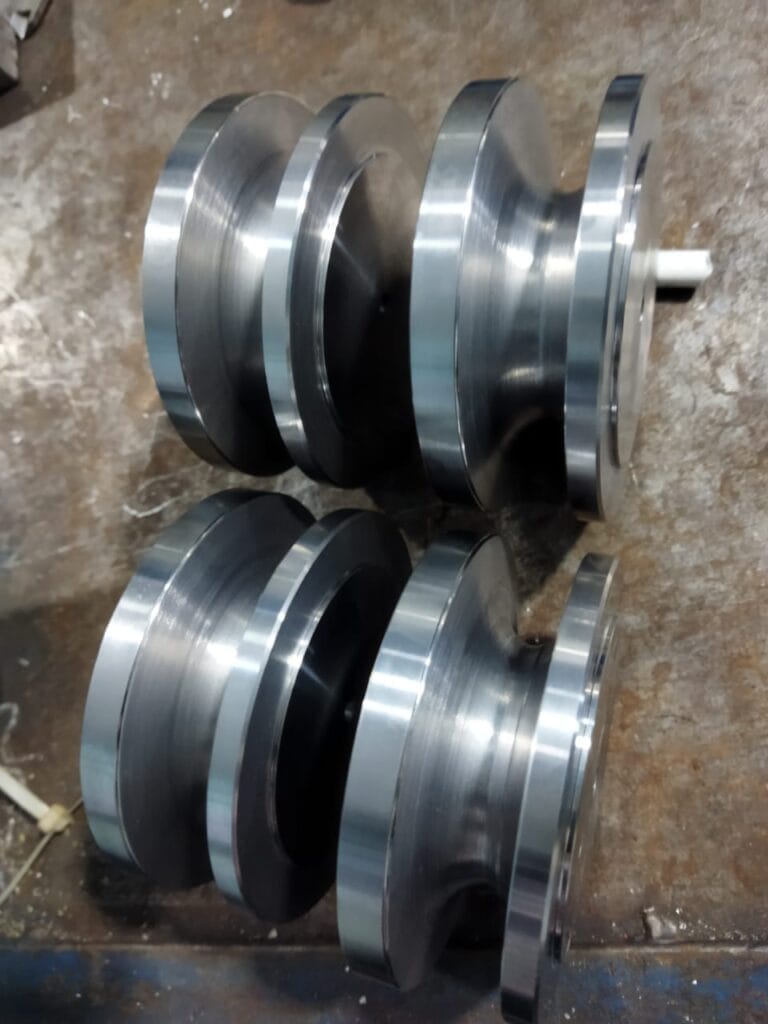
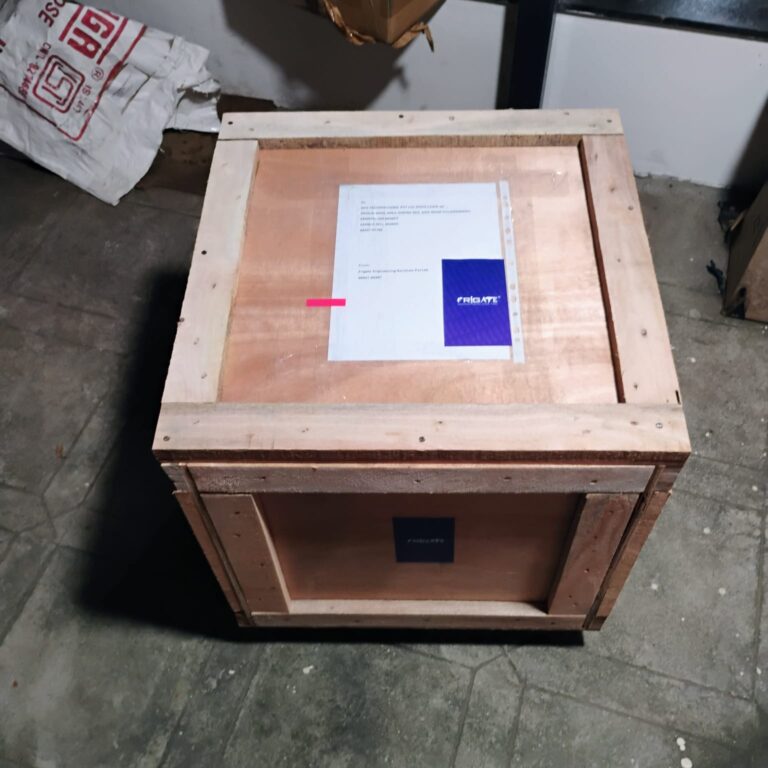
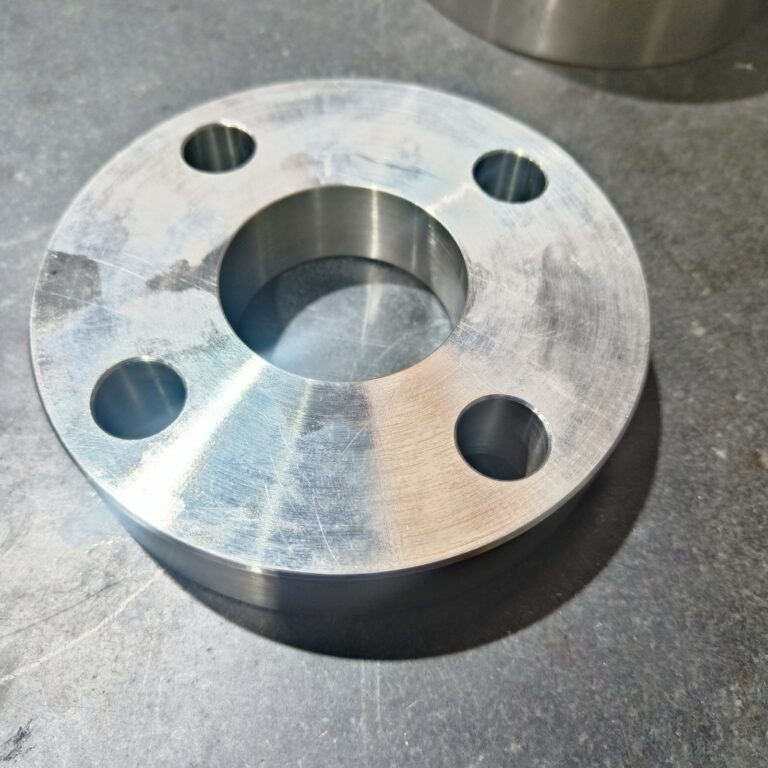
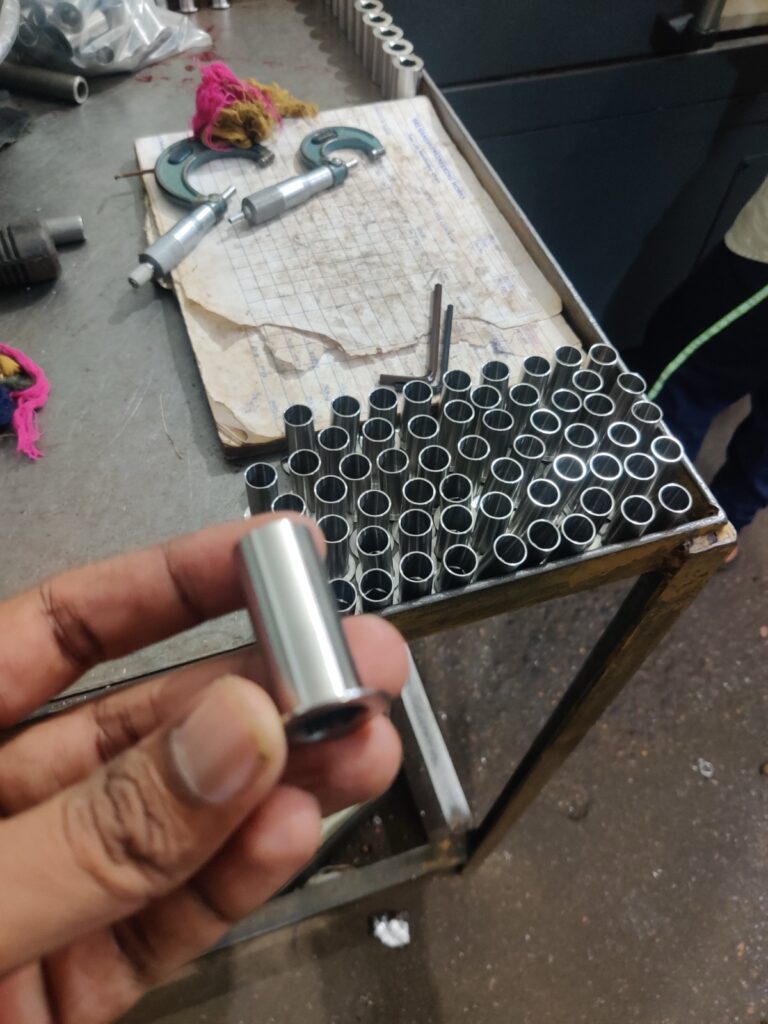
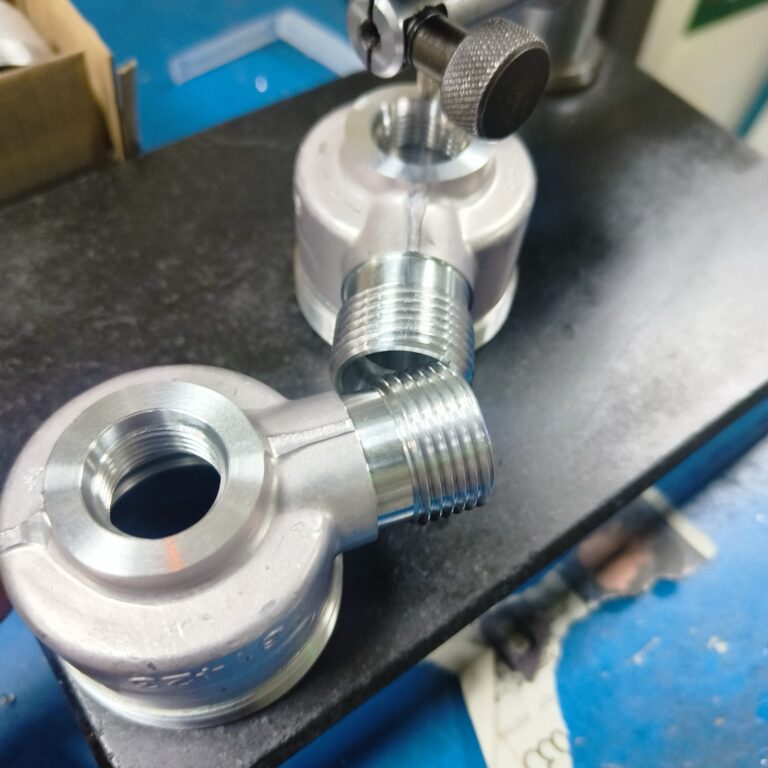
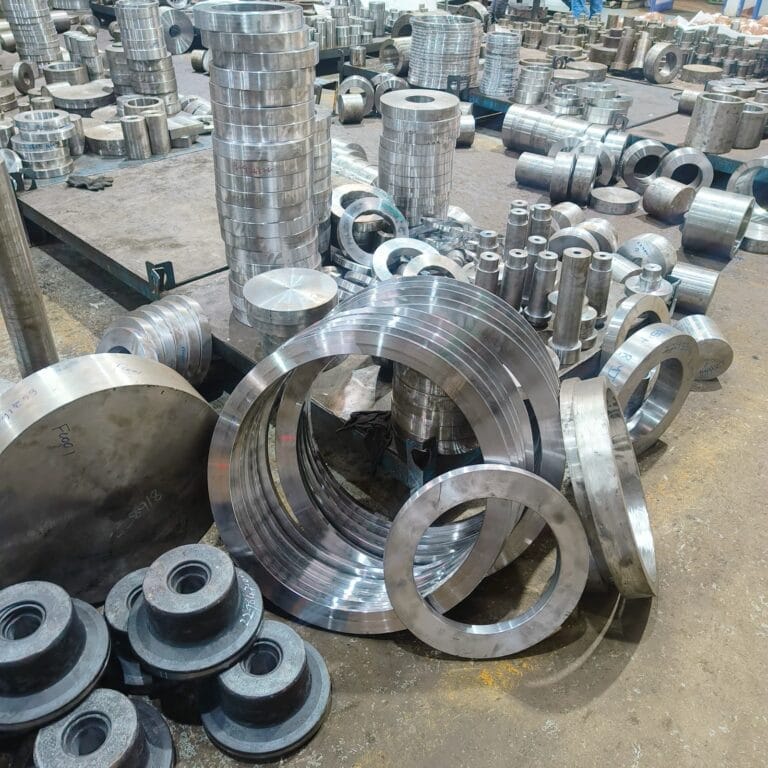
Other Industries We Serve
We deliver machining support across sectors that require consistency, material reliability, and tight dimensional control.
- Solid Progress
Our Manufacturing Metrics
Frigate brings stability, control, and predictable performance to your sourcing operations through a structured multi-vendor system.
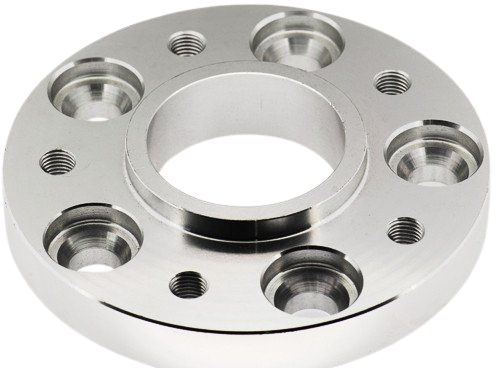
2.8X
Sourcing Cycle Speed
Frigate’s pre-qualified network shortens decision time between RFQ and PO placement.
94%
On-Time Delivery Rate
Structured planning windows and logistics-linked schedules improve project-level delivery reliability.
4X
Multi-Part Consolidation
We enable part family batching across suppliers to reduce fragmentation.
22%
Quality Rejection Rate
Multi-level quality checks and fixed inspection plans lower non-conformities.
30%
Procurement Costs
Optimized supplier negotiations and bulk order strategies reduce your overall sourcing expenses.
20%
Manual Processing Time
Automation of sourcing and supplier management significantly reduces time spent on manual tasks.
Get Clarity with Our Manufacturing Insights
- FAQ
Having Doubts? Our FAQ
Check all our Frequently Asked Questions in CNC Machining
Frigate uses wear-resistant alloys and controlled machining parameters to extend part life. Advanced simulation is used before production to check how the component will behave in high-pressure, corrosive environments. Each machined part is tested for dimensional stability under thermal cycling. This ensures long-term reliability even in offshore or deep well operations.
Frigate uses 5-axis CNC machines to create intricate oilfield connectors with tight threading tolerances. CAM software generates optimized toolpaths for internal and external threads, reducing tool deflection. Surface finish is enhanced using controlled cutting speeds and post-machining treatments. This allows consistent sealing performance in high-pressure joints.
Toolpath optimization minimizes machine vibration and thermal distortion during long tool engagements. Frigate uses real-time monitoring systems to dynamically adjust speeds and feeds. This reduces wear on carbide tools when cutting tough materials like Inconel or duplex stainless steel. The result is improved feature accuracy in long borehole parts.
Frigate uses dual-spindle lathes and in-process probing to control concentricity within microns. Each part is inspected using CMMs for true position and roundness deviation. Precision workholding and thermal compensation are used to avoid distortion. This ensures functional alignment between mating surfaces during fluid regulation.
Frigate uses horizontal machining centers with rotary tables to machine large housings in a single setup. This eliminates tolerance stack-up from multiple repositions. Stress-relieving heat treatments are applied before and after machining to reduce deformation. Final verification includes ultrasonic and dye-penetrant testing of all machined interfaces.
We'd love to Manufacture for you!
Submit the form below and our representative will be in touch shortly.
LOCATIONS
Registered Office
10-A, First Floor, V.V Complex, Prakash Nagar, Thiruverumbur, Trichy-620013, Tamil Nadu, India.
Operations Office
9/1, Poonthottam Nagar, Ramanandha Nagar, Saravanampatti, Coimbatore-641035, Tamil Nadu, India. ㅤ
Other Locations
- Bhilai
- Chennai
- Texas, USA