- Rapid Manufacturing
CNC Machining Services in New Mexico
We utilize cryogenic cooling techniques to reduce thermal expansion effects, ensuring precision in temperature-sensitive materials. Upload your CAD file to get an instant quote and complete your order in just 5 minutes.
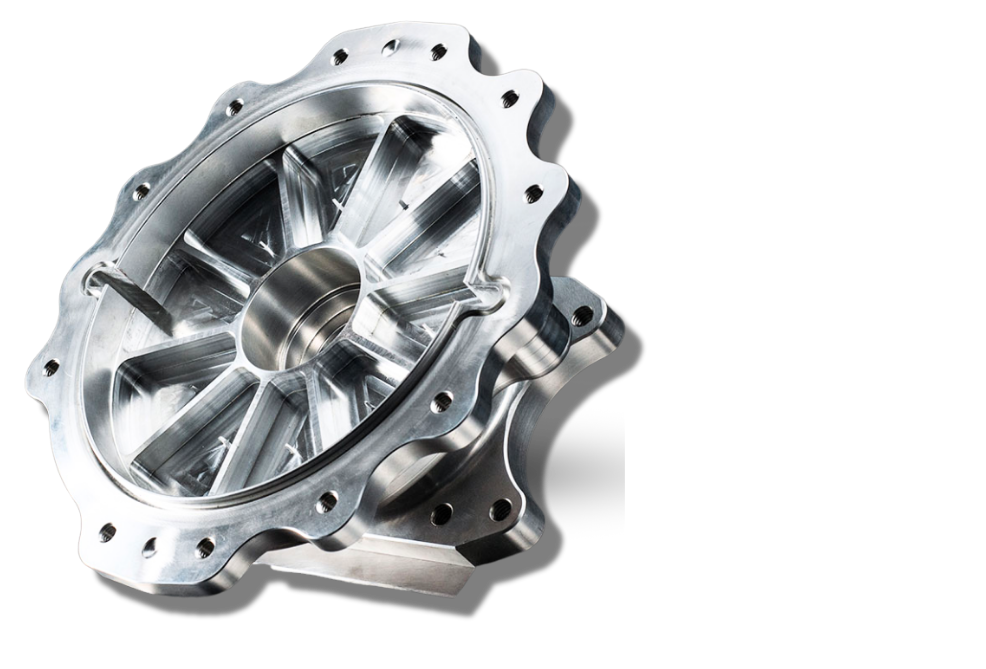
Our Clients
Trusted by Engineers and Purchasing Leaders
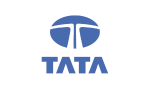
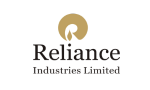


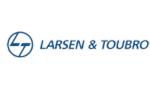
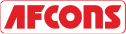


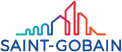

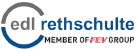

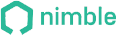
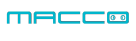









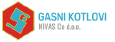
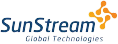

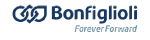


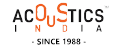
- Instant Quotes
Quote in Seconds - Parts in Days
We implement active damping systems with piezoelectric actuators to suppress vibration frequencies, reducing amplitude during high-speed machining. This dynamic stabilization ensures geometric precision, supporting a reliable 7-day lead time.
- Get instant quotes
- Get instant DFM feedback
- Online quote and order management
- Project Management
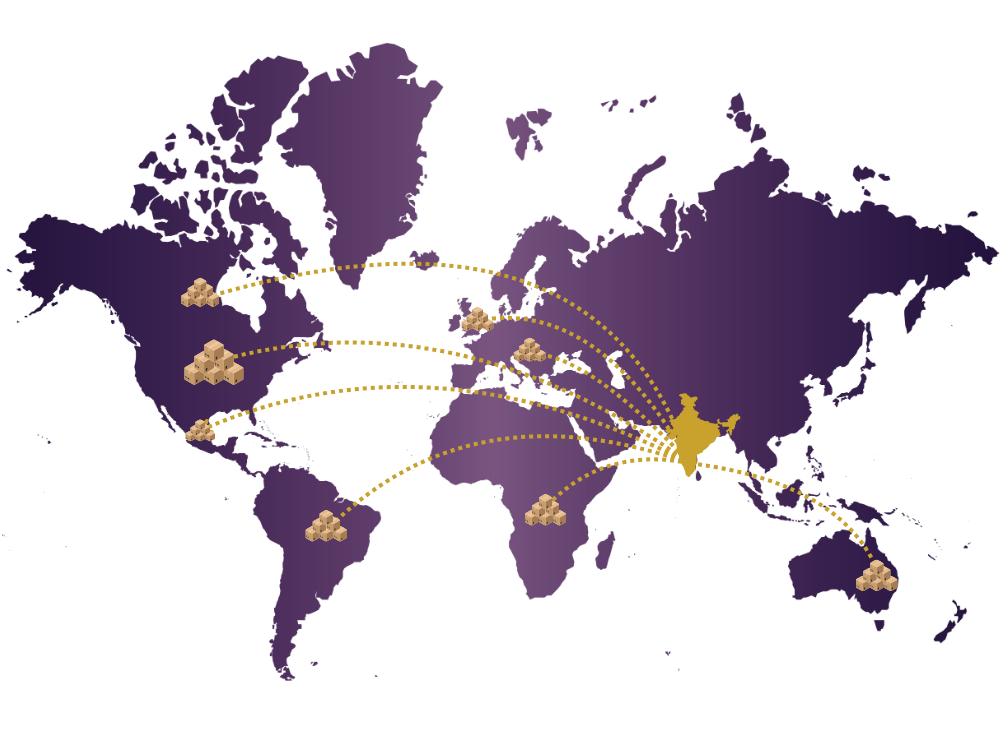
- Our Services
Online CNC Machining Service in New Mexico
Get high-precision CNC machined parts online with fast turnaround and cost-effective pricing.
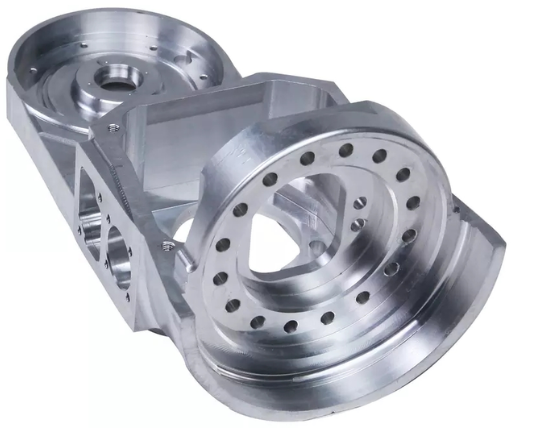
CNC Milling
Micro-milling combines fine cutting tools, vibration damping, and air mist cooling for micron-level precision.
- Handle tough materials with spindle power up to 30 kW
- Free design feedback with every quote
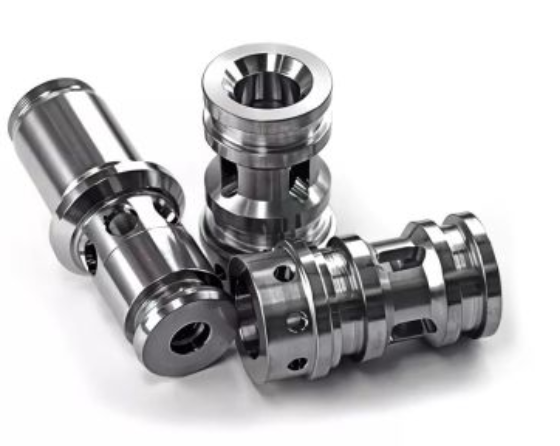
CNC Turning
CNC turning with sub-micron feed control achieves intricate surface textures and precise dimensional accuracy.
- Complex cylindrical parts up to ⌀500mm
- Bar feeding feature for faster, continuous production
- Surface Finish
Flawless Finishes for CNC Machining Parts in New Mexico
Our specialized process combines selective carburizing, compressive stress profiling, and hardened diffusion layers to strengthen components in wear-intensive conditions.
Anodizing
Give your aluminum parts a tough, corrosion-resistant shield with anodizing, reaching surface hardness up to HV 500, while enhancing electrical insulation and durability.
Mechanical Finishing
Smooth out imperfections and refine surfaces to Ra 0.2 µm or better with mechanical finishing techniques like grinding, polishing, and bead blasting.
Heat Treatment
Boost material strength and hardness by heat treating parts at temperatures up to 1100°C, ensuring they meet the mechanical demands of your application.
Electroplating
Add protective or functional metal coatings with electroplating, delivering consistent layers as precise as ±2 µm for improved corrosion resistance and conductivity.
- Real Impact
Words from Clients
See how global OEMs and sourcing heads describe their experience with our scalable execution.
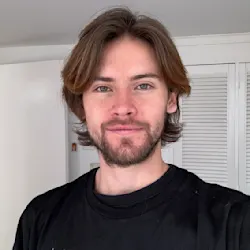
“Quick turnaround and solid quality.”
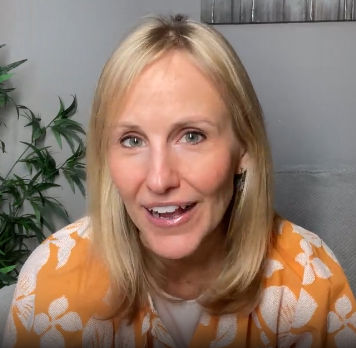
“The instant quote tool saved us time, and the parts were spot-on. Highly recommend Frigate!”
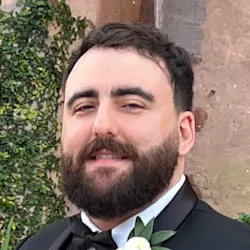
“Great service, fair price, and the parts worked perfectly in our assembly.”
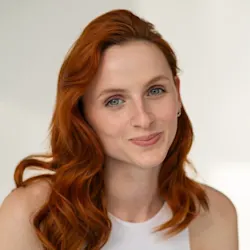
“Top-notch machining and fast shipping. Very satisfied with the results.”
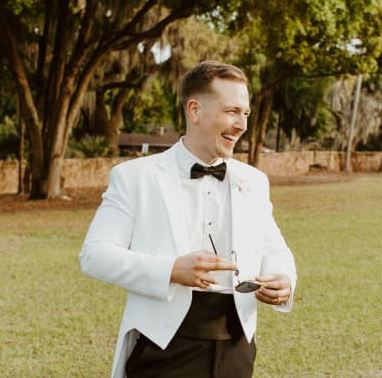
“Frigate delivered high-quality parts at a competitive price. The instant quote tool is a huge plus for us!”

“We appreciate the precision and quality of the machined components in the recent delivery—they meet our specifications perfectly and demonstrate Frigate’s capability for excellent workmanship.”
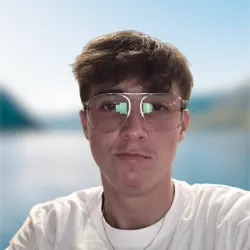
“Flawless execution from quote to delivery.”
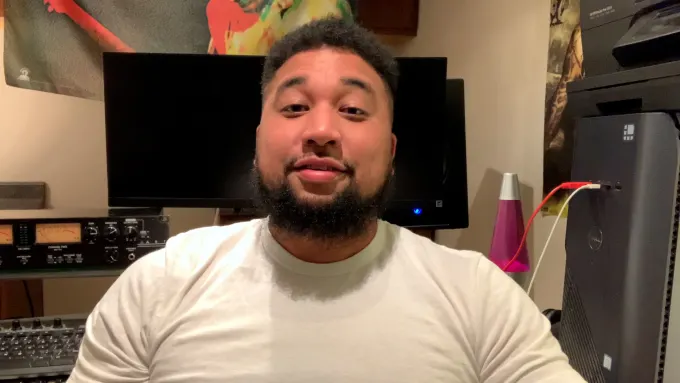
“The precision on these parts is impressive, and they arrived ahead of schedule. Frigate’s process really stands out!”
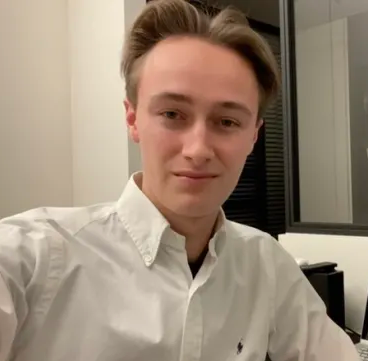
“Parts were exactly as spec’d, and the instant quote made budgeting a breeze.”
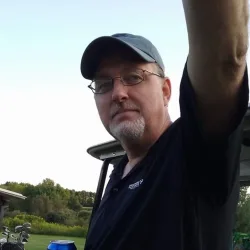
“Good value for the money.”
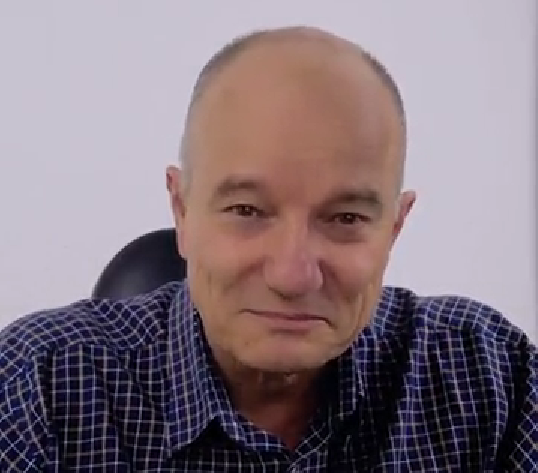
“The finish was perfect, and the team was easy to work with.”
- We export to 12+ countries
Frigate’s Global Presence
Frigate takes pride in facilitating “Make in India for the globe“. As our global network of Frigaters provides virtually limitless capacity, and through our IoT enabled platform your parts go directly into production. By digitally and technologically enabling “the silent pillars of the economy” MSME and SME manufacturing industries, we are able to tap the huge potential for manufacturing to bring the best results for our clients.

100,000+
Parts Manufactured
250+
Frigaters
2000+
Machines
450+
Materials
25+
Manufacturing Process
- Transparent Pricing
Instant Online Quote for CNC Machining Services
We apply molecular statics simulations to study lattice distortions, atomic-scale defects, and residual stress buildup. This method optimizes machining forces, ensuring consistent material performance.
- Price updates are made in real time as you change materials, machining methods, etc.
- No hidden costs. Our instant quotes are not just indications but the actual price and include shipping and customs up front.

- Quote to Delivery
Quick and Clear Steps to Your Order
Everything moves smoothly from pricing to shipment, so you get high-quality parts without delays.
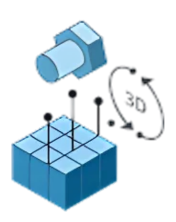
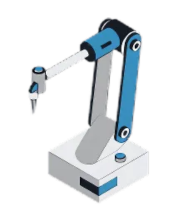
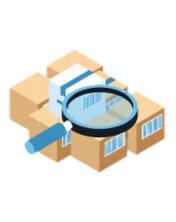
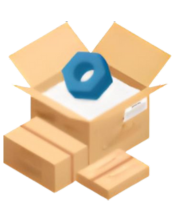
Upload CAD File
Obtain a precise and competitive quote instantly to empower your decision-making.
- Detailed cost breakdown
- Various materials and finish choices
- Market-driven unbeatable pricing
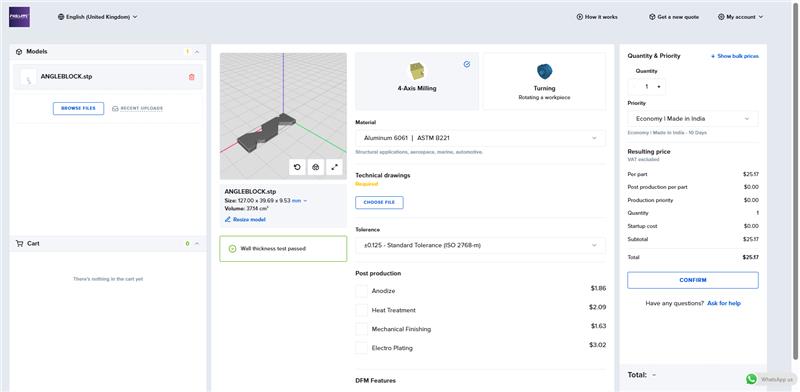
Manufacturing Begins
Transform your designs into reality with our state-of-the-art CNC production capabilities.
- Advanced machinery
- Scalable production support
- Live updates from the production floor
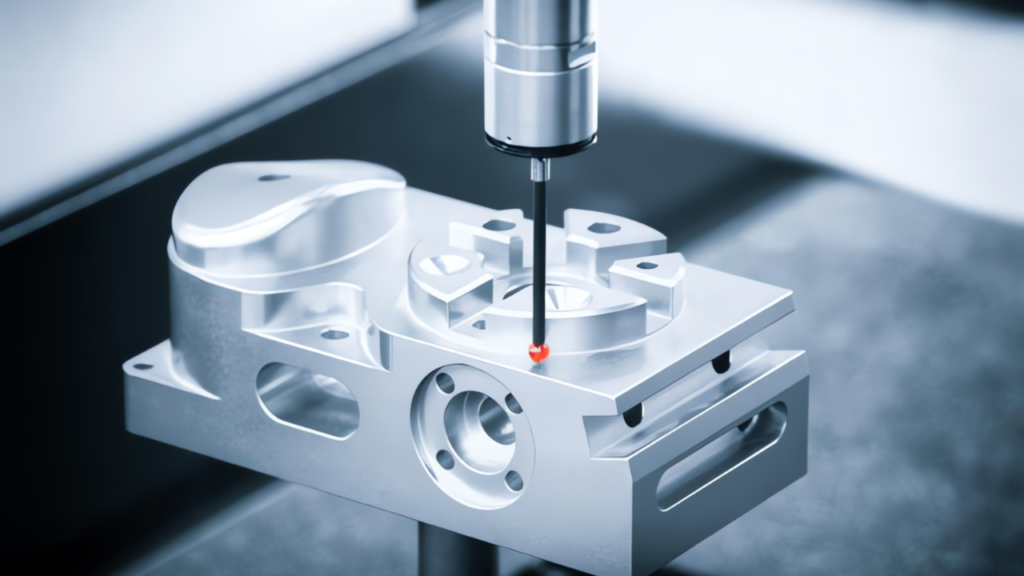
Thorough Inspection
Each part is checked to match exact specifications before moving forward.
- High-tech dimensional verification
- Surface finishing and coating checks
- Batch-wise documentation
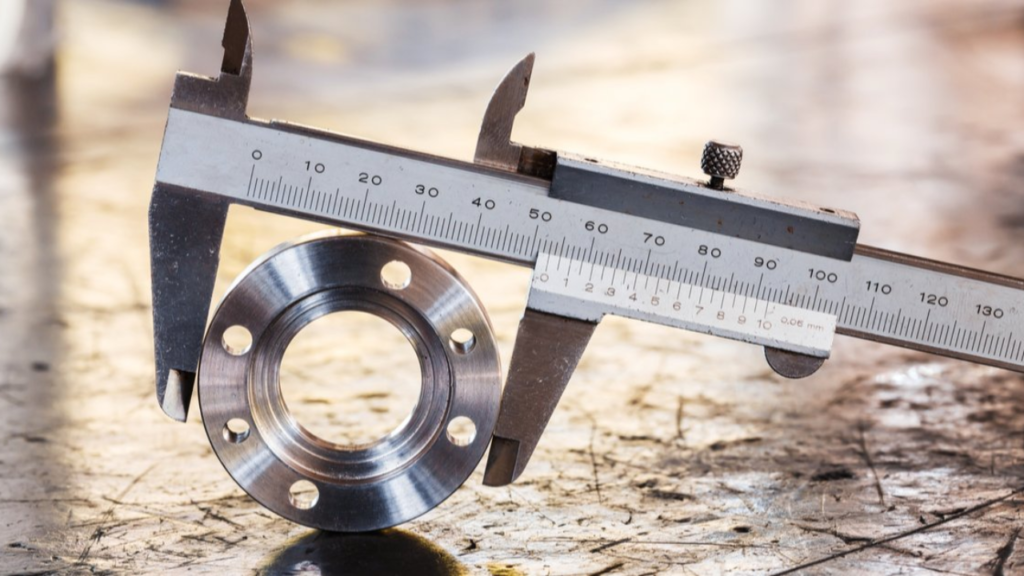
Safe & Timely Dispatch
Receive your machined parts promptly and in perfect condition.
- Multiple shipping options
- Secure packaging
- Real-time tracking during every transit
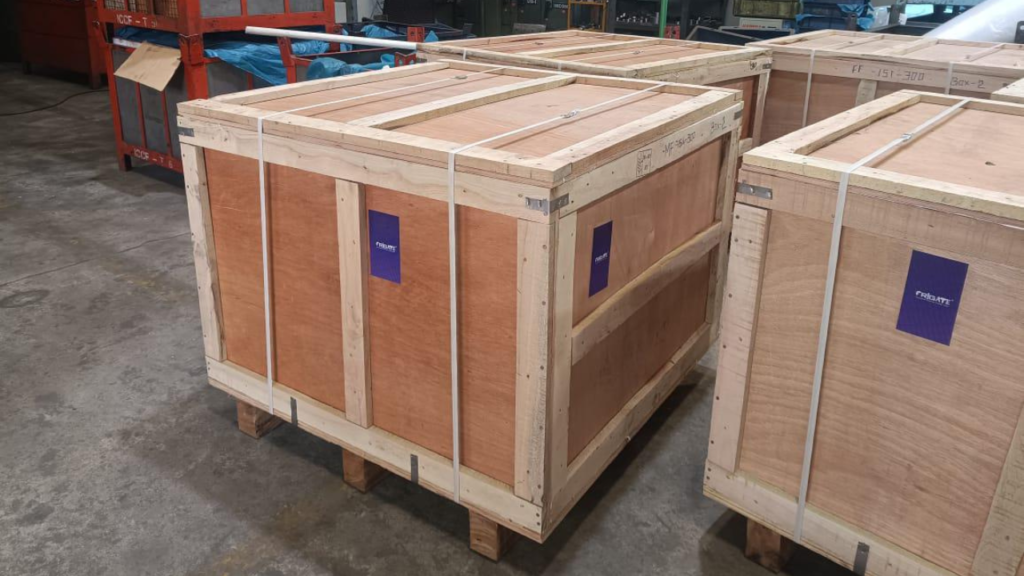
- Machining Materials
Different Materials for CNC Machining
We utilize dual-fluid cooling systems combining oil mist diffusion and liquid jet cooling to manage cutting temperatures in hardened tool steels and heat-treated alloys. Real-time force monitoring ensures accuracy.
Aluminum 6061
- Density - 2.7 g/cm³
- Tensile Strength - 310 MPa
- Yield Strength - 276 MPa
- Hardness (Brinell) - 95 HB
- Excellent corrosion resistance, good machinability, and heat treatable
Used in aerospace, automotive, and electronics for components like aircraft structures, bicycle frames, and heat sinks due to its lightweight and strength.
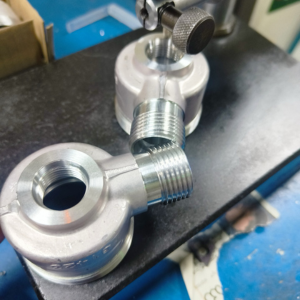
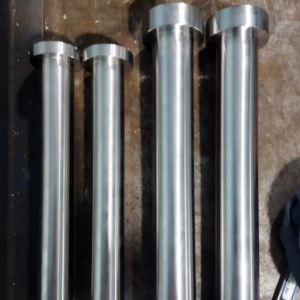
Aluminum 7075
- Density - 2.81 g/cm³
- Tensile Strength - 572 MPa
- Yield Strength - 503 MPa
- Hardness (Brinell) - 150 HB
- High fatigue resistance but limited weldability
Commonly used in aerospace, defense, and sporting goods for aircraft wings, firearm components, and high-performance bicycle parts requiring high strength.
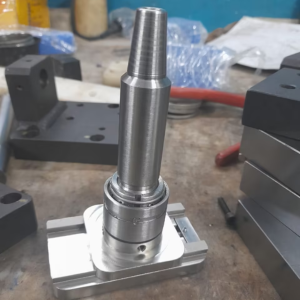

Aluminum 7050
- Density - 2.81 g/cm³
- Tensile Strength - 572 MPa
- Yield Strength - 503 MPa
- Hardness (Brinell) - 150 HB
- High fatigue resistance but limited weldability
Commonly used in aerospace, defense, and sporting goods for aircraft wings, firearm components, and high-performance bicycle parts requiring high strength.
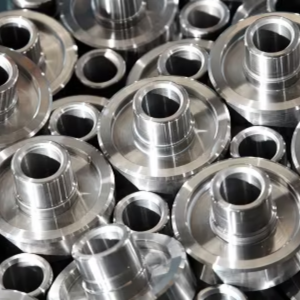

Stainless Steel 304
- Density - 8.0 g/cm³
- Tensile Strength - 515 MPa
- Yield Strength - 205 MPa
- Hardness (Brinell) - 201 HB
- High corrosion resistance, non-magnetic, and good formability
Preferred in food processing, medical, and chemical industries for tanks, surgical tools, and piping systems due to its hygiene and corrosion resistance.

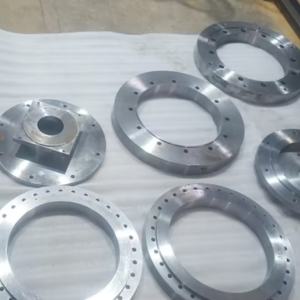
Stainless Steel 440 - Carbon
- Density - 7.8 g/cm³
- Tensile Strength - 760 MPa
- Yield Strength - 450 MPa
- Hardness (Rockwell C) - 56-60 HRC
- High hardness, excellent wear resistance, and corrosion resistance
Used in cutting tools, bearings, valves, and surgical instruments where extreme hardness and durability are required.
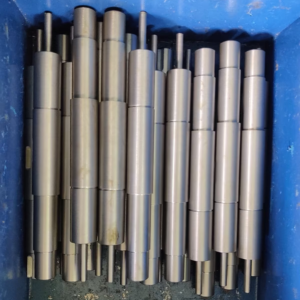
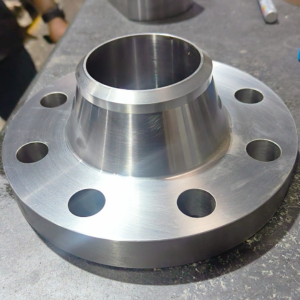
Stainless Steel 416
- Density - 7.7 g/cm³
- Tensile Strength - 585 MPa
- Yield Strength - 275 MPa
- Hardness (Brinell) - 262 HB
- Free-machining stainless steel with good strength
Ideal for automotive, firearms, and industrial applications, including gears, bolts, and shafts requiring high machinability.

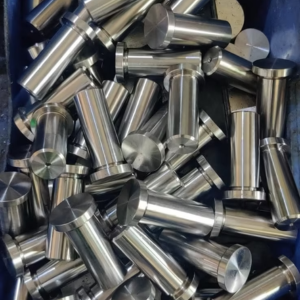
Steel 1018
- Density - 7.87 g/cm³
- Tensile Strength - 440 MPa
- Yield Strength - 370 MPa
- Hardness (Brinell) - 126 HB
- Excellent weldability and machinability
Used in automotive, machinery, and construction for shafts, pins, and fasteners where moderate strength and cost efficiency are key.

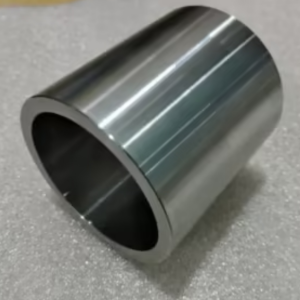
Steel 4140
- Density - 7.85 g/cm³
- Tensile Strength - 655 MPa
- Yield Strength - 415 MPa
- Hardness (Rockwell C) - 28-32 HRC
- High strength, toughness, and wear resistance
Widely used in oil & gas, aerospace, and automotive for gears, crankshafts, axles, and high-load machine components requiring extreme durability.
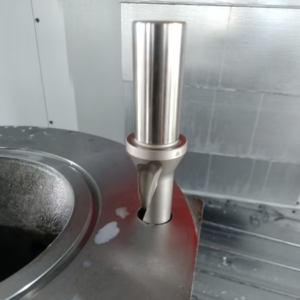
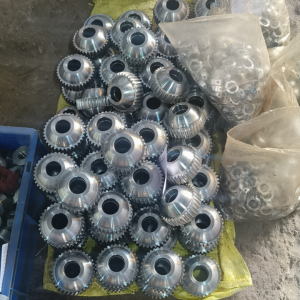
- CNC Machining Parts
CNC Machining Parts in New Mexico
We employ spindle-mounted feedback sensors, flexure-guided stages, and advanced trajectory planning algorithms to control precise motion. Browse our high-precision components built for cutting-edge manufacturing demands.
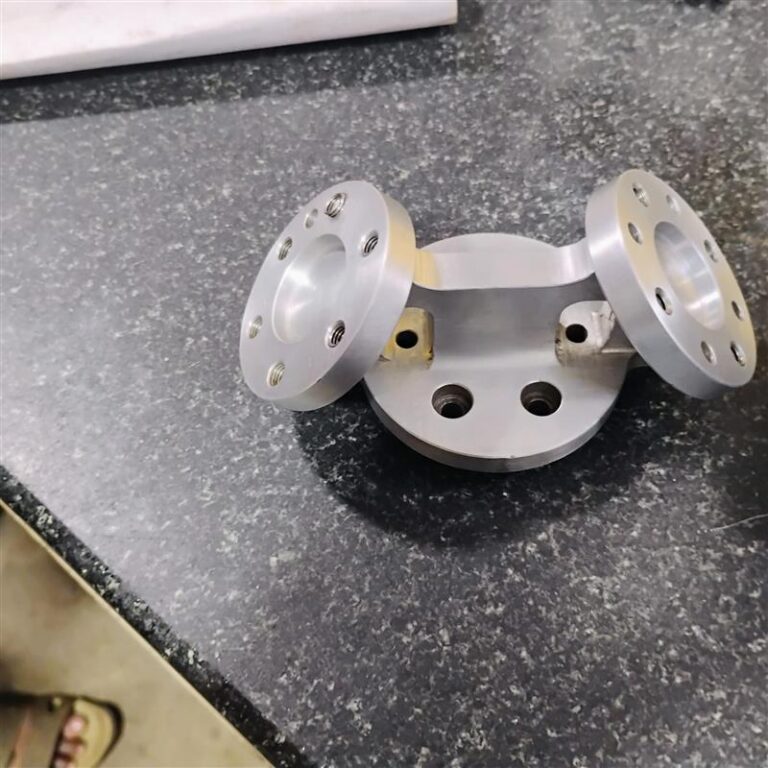
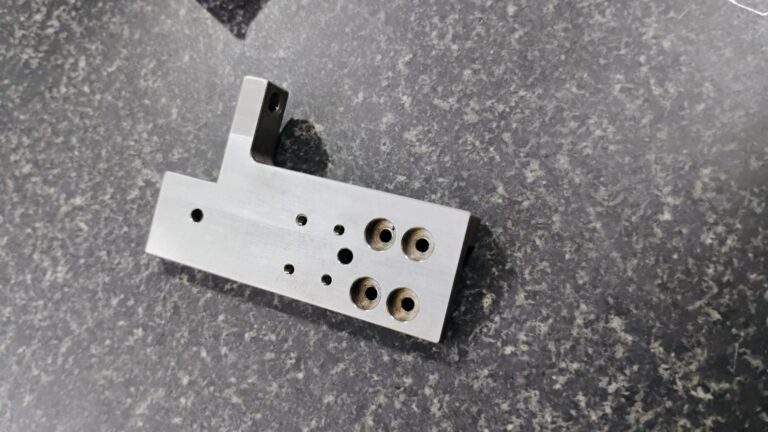
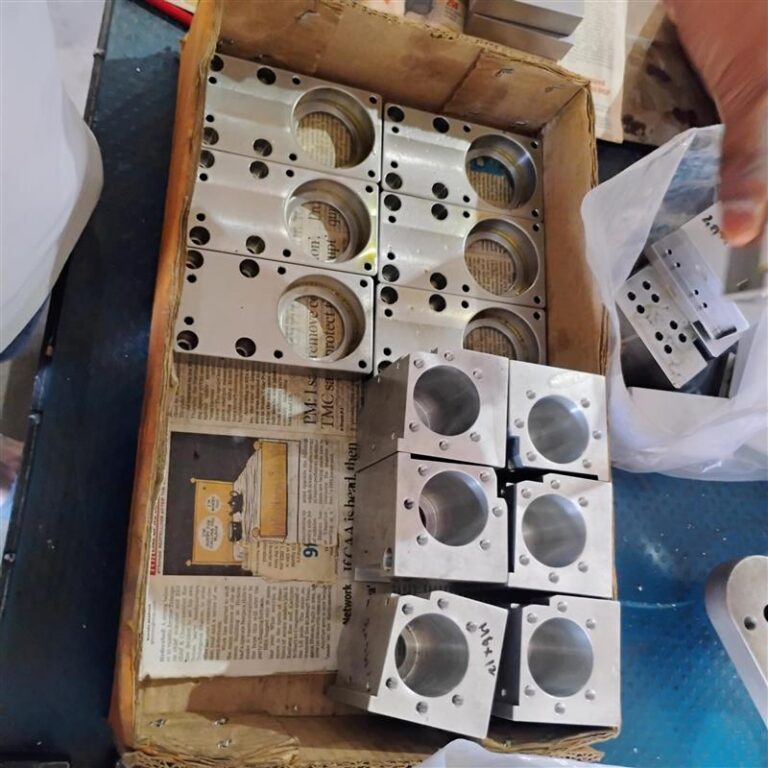
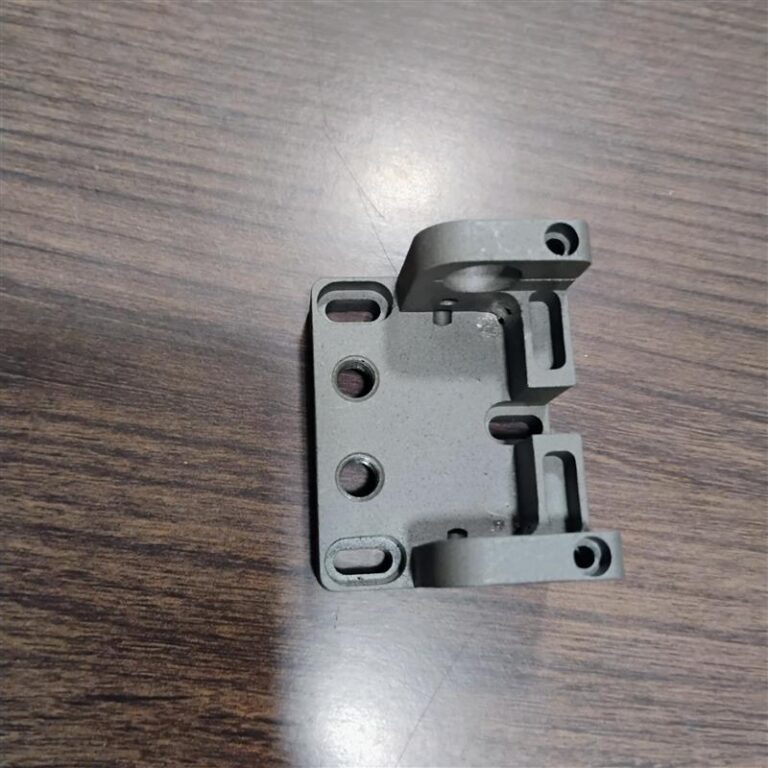
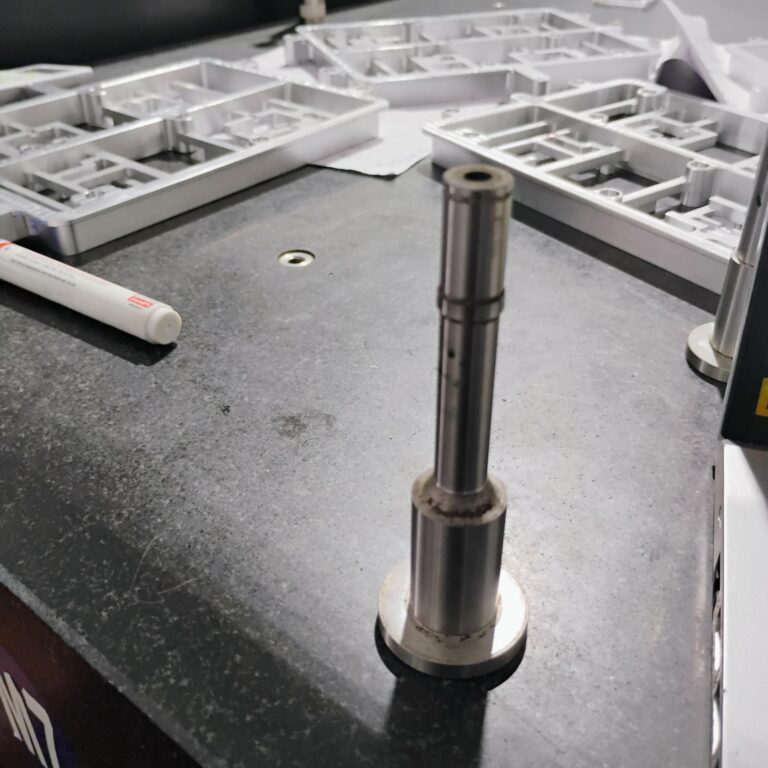
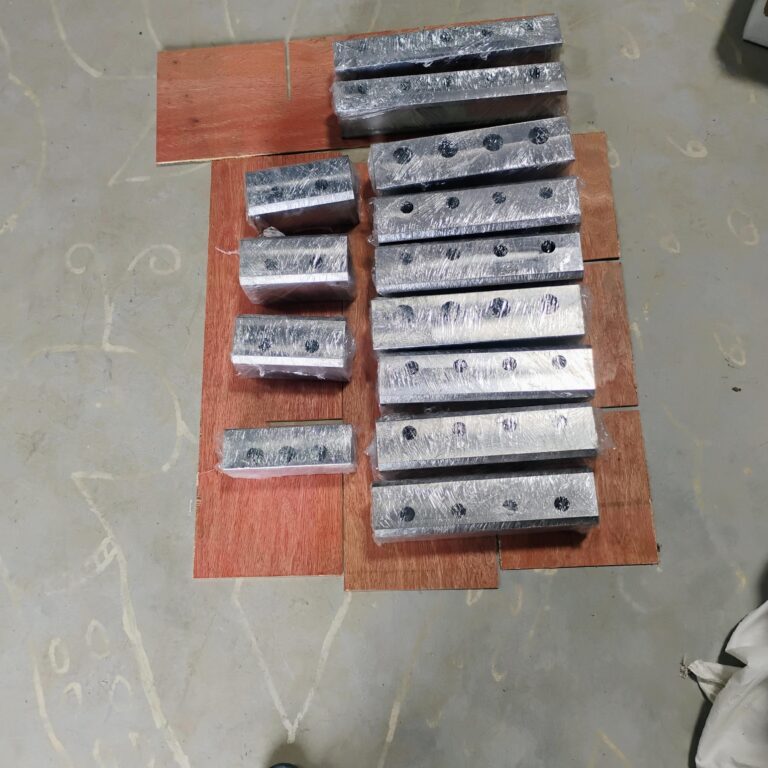
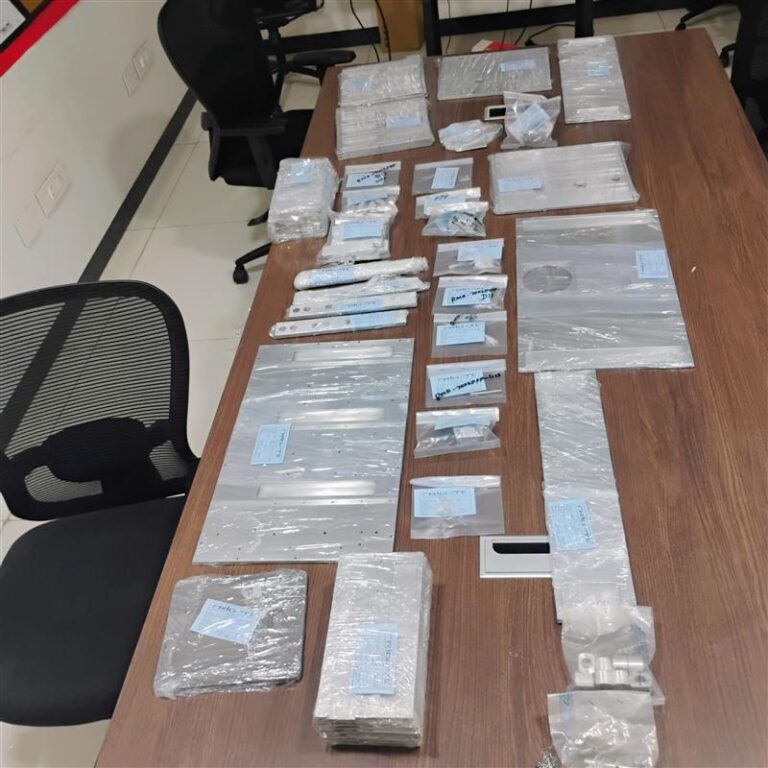

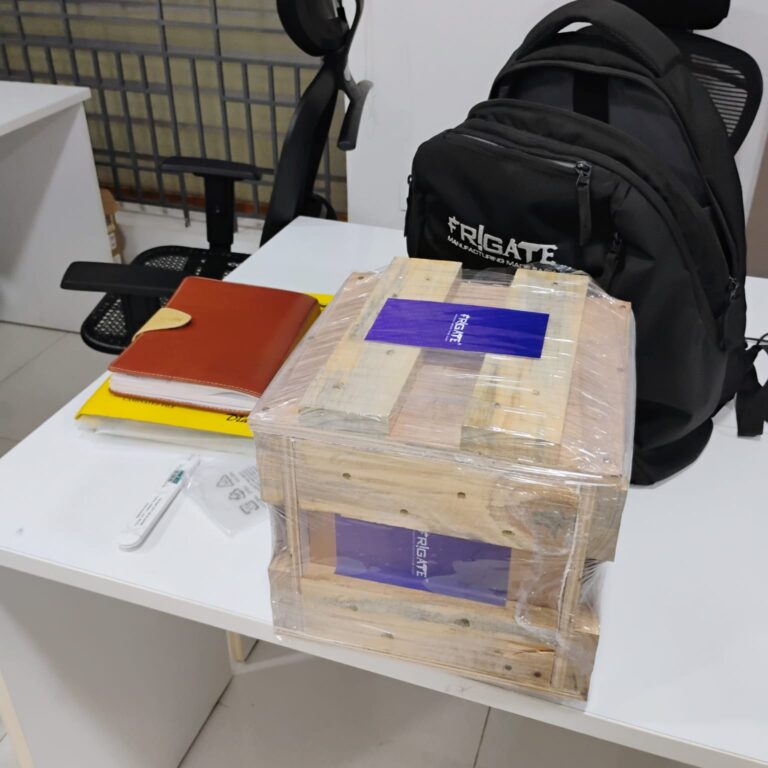


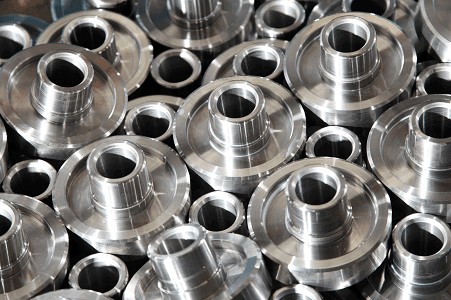
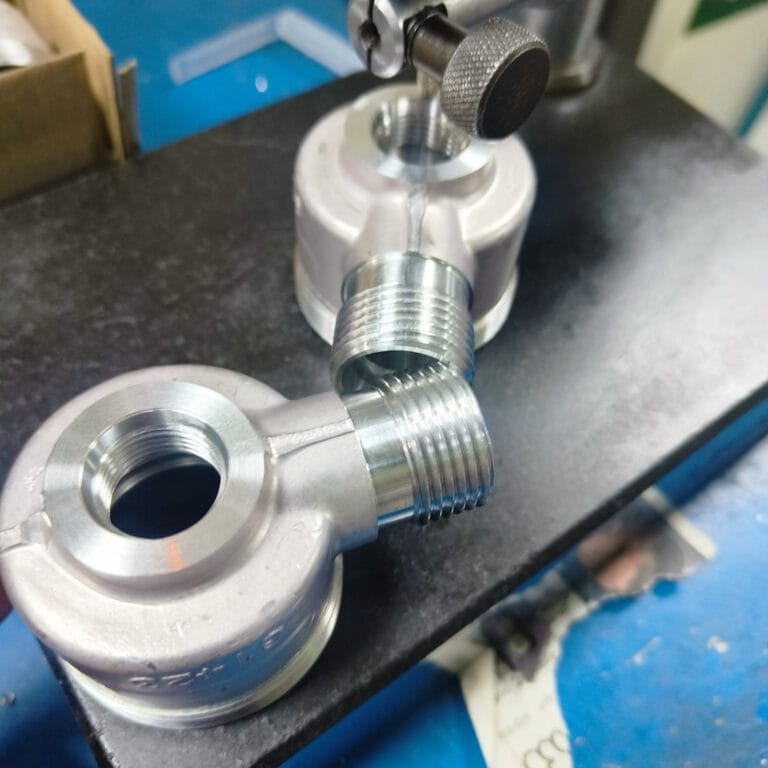
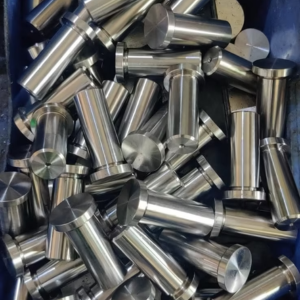
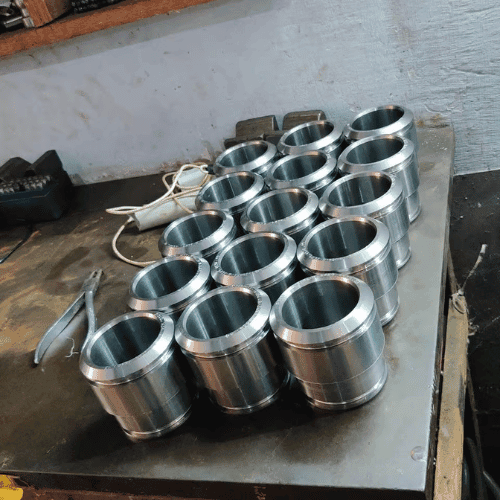
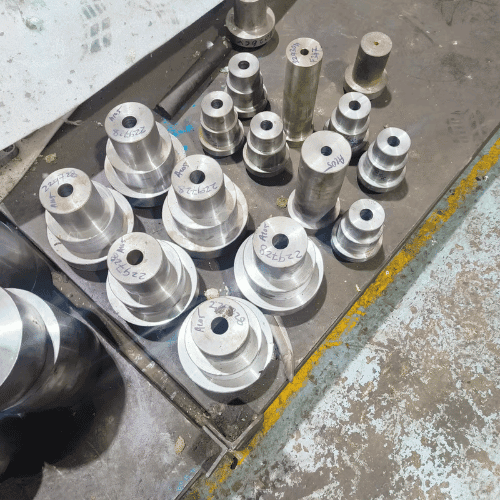
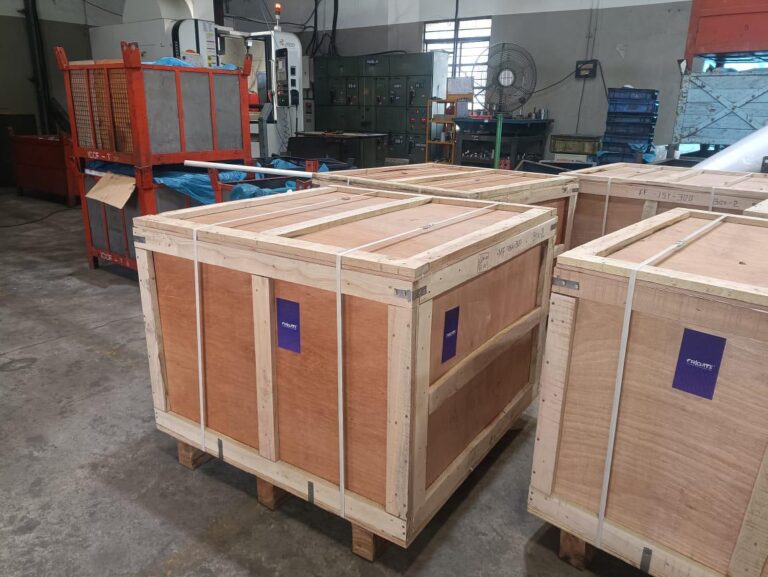
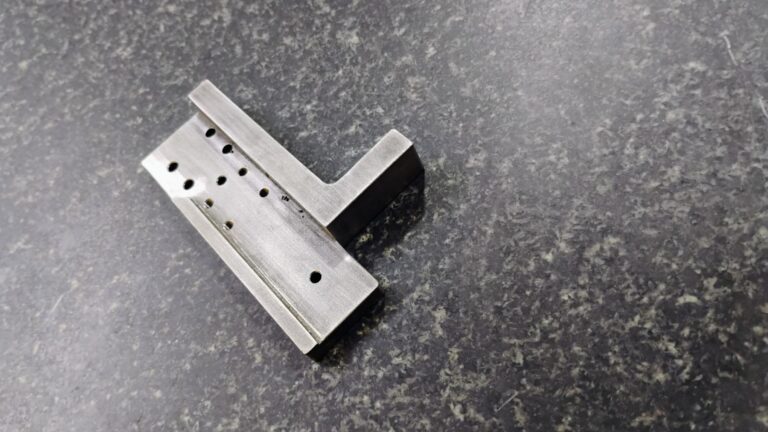
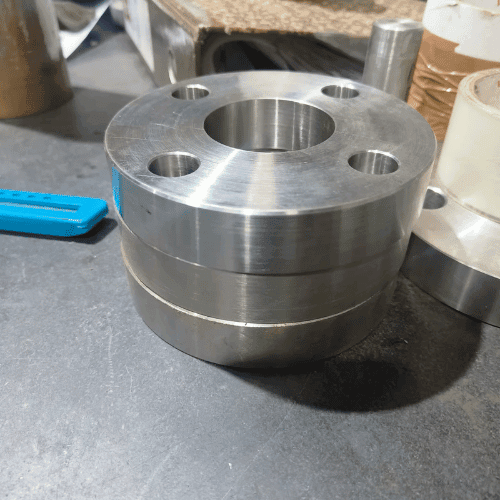
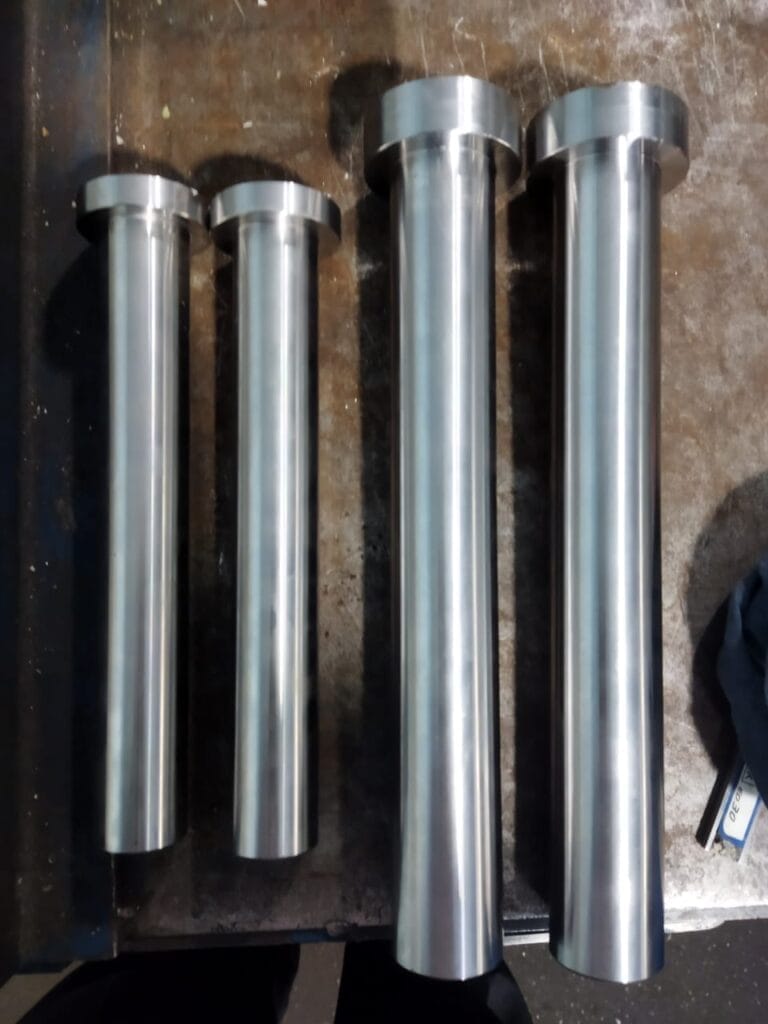

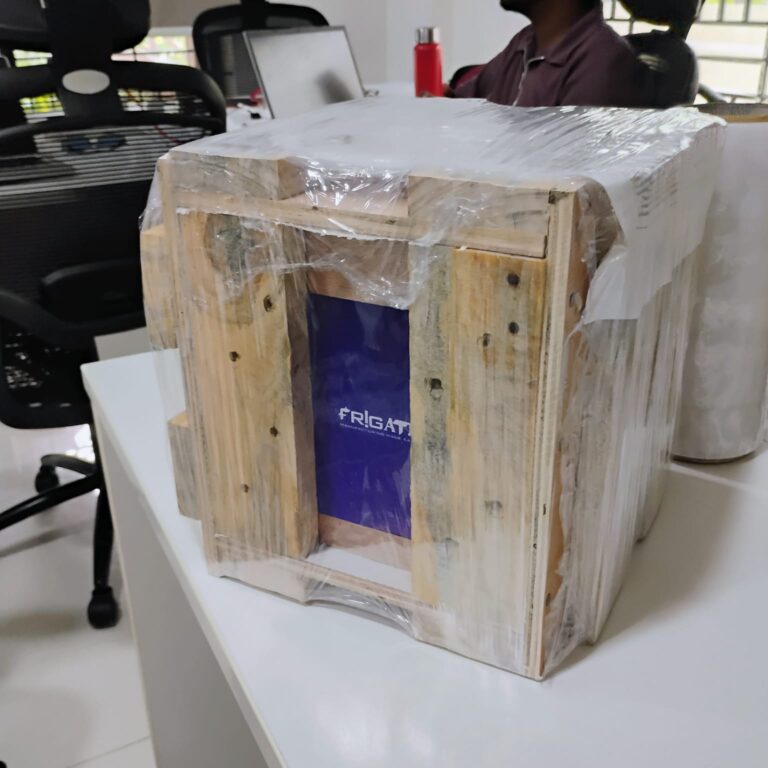

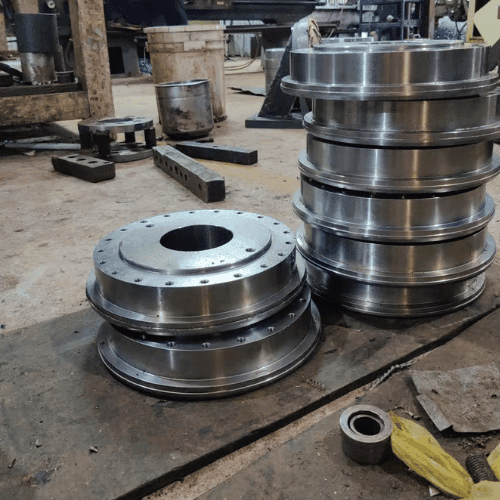
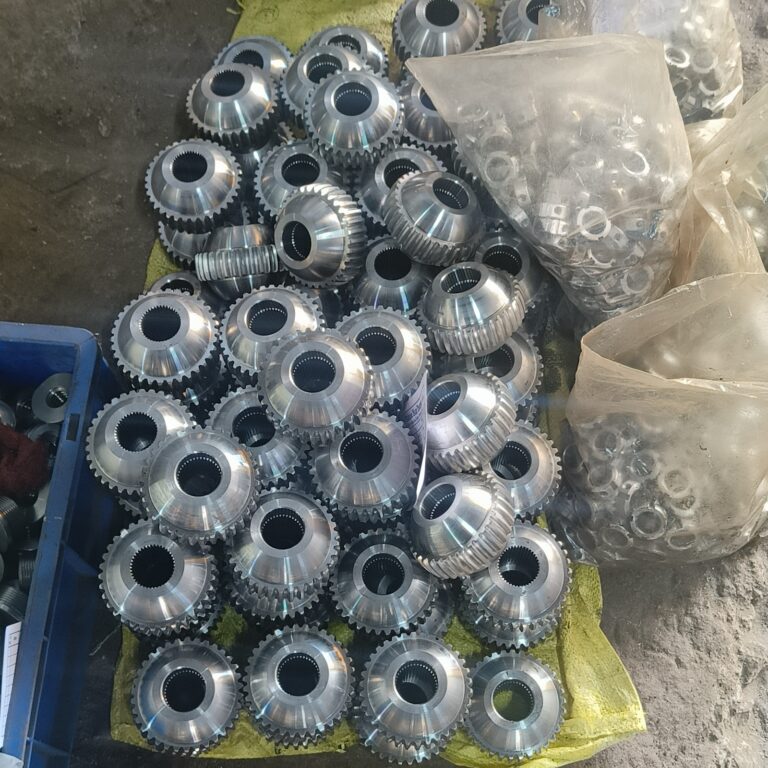
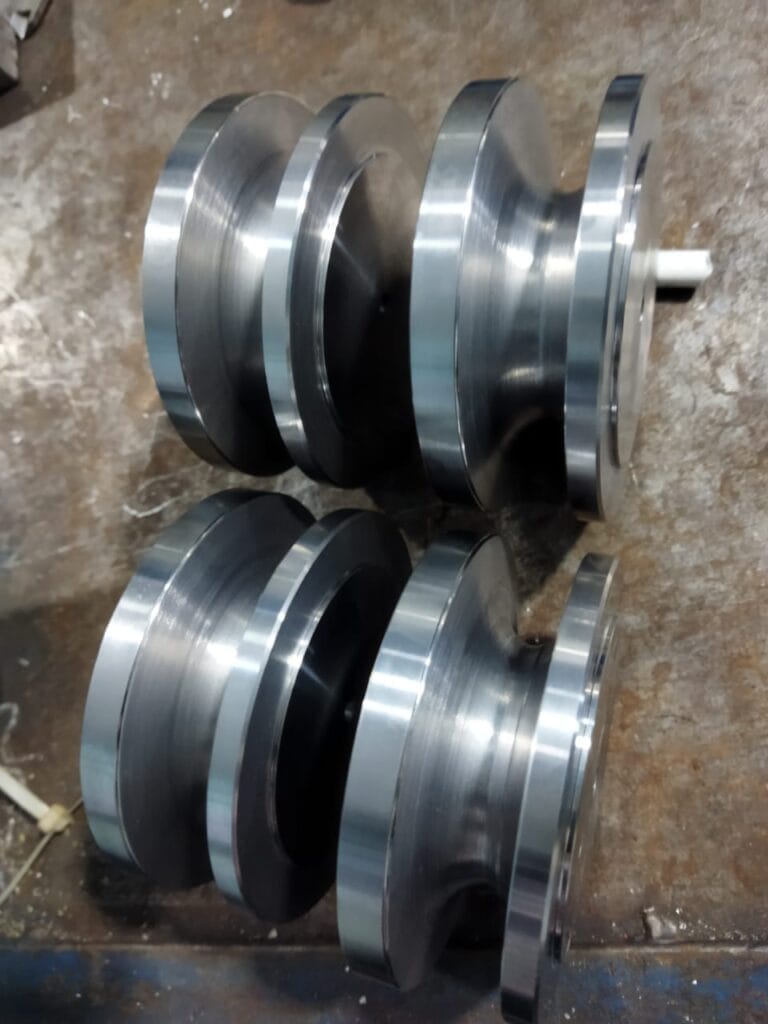
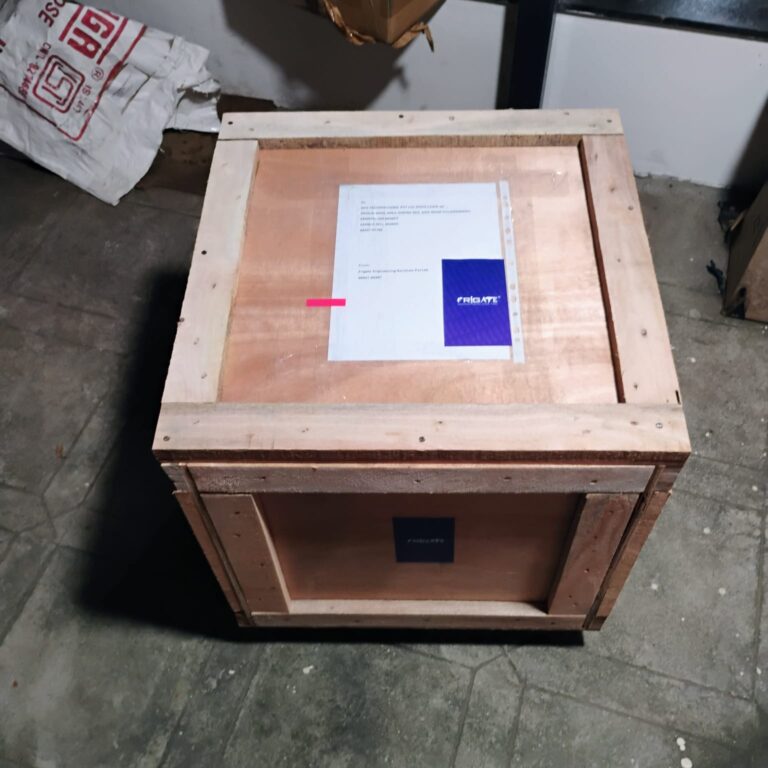
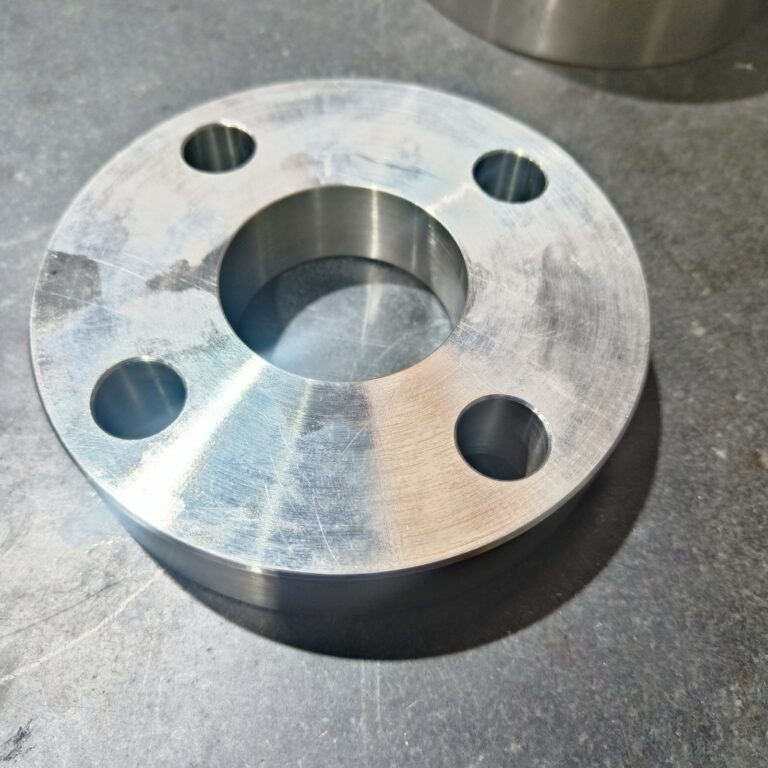
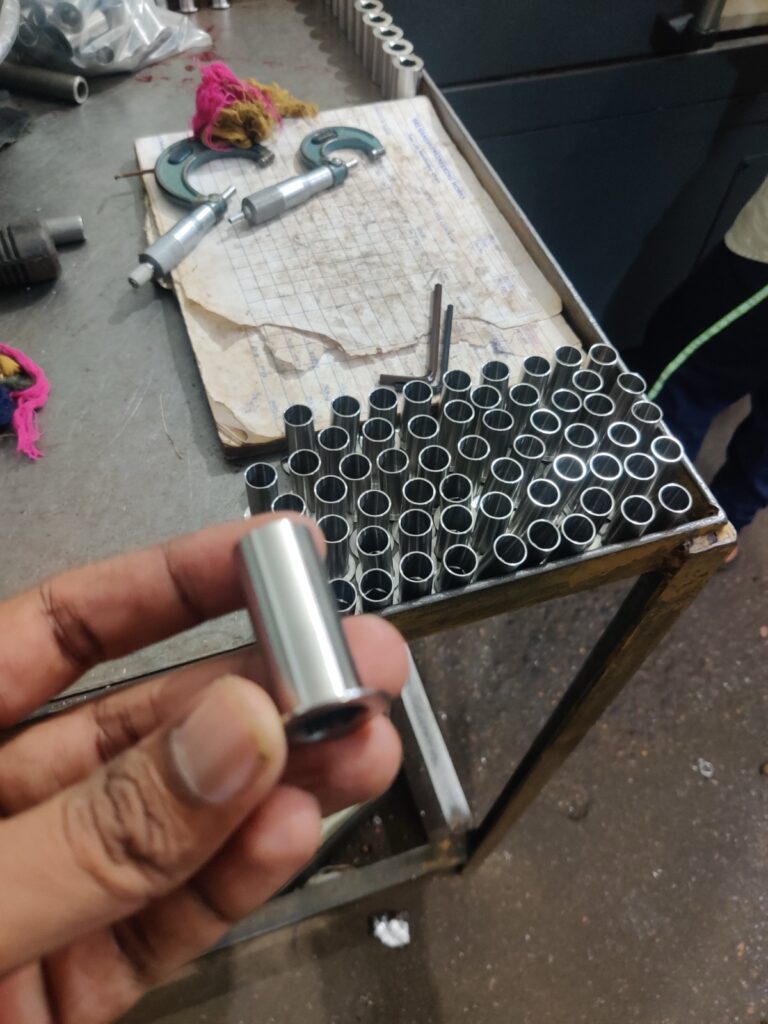
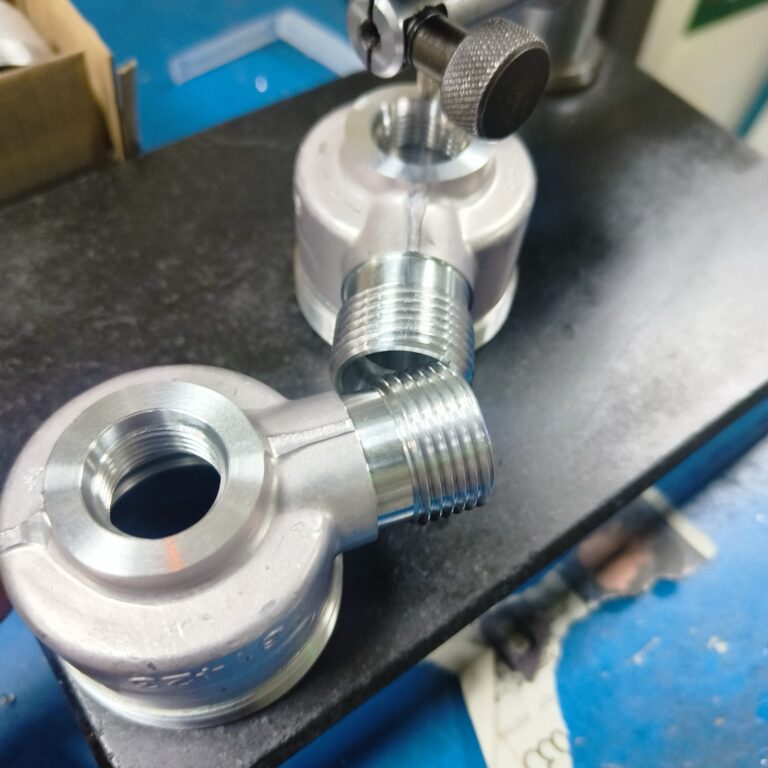
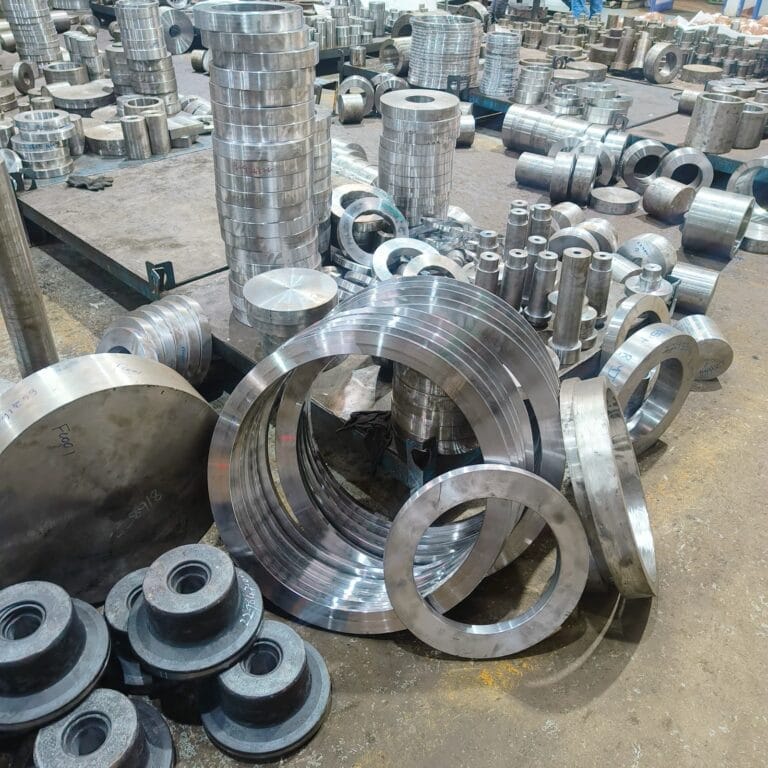
- One Stop Solution
End-to-End CNC Machining Solutions in New Mexico
Our process combines magnetic encoder scales, adaptive servo tuning, and high-frequency probing to achieve micron-level accuracy in challenging geometries.
To improve accuracy, our instant pricing model incorporates adaptive feed control data, spindle motor efficiency, and in-process calibration data.
Our inspection process combines speckle interferometry, eddy current array scanning, and thermal wave analysis for accurate defect identification.
- Optimized Workflow
From CNC Rapid Prototyping to Production in New Mexico
Frigate offers fast and precise CNC machining, from rapid prototyping to full-scale production, ensuring high-quality parts with quick turnaround times.

Rapid Prototyping
We employ thermal spray coating with dynamic milling strategies to enhance rapid prototyping by improving thermal stability and surface durability.
- Instant quotes
- Instant DFM feedback
- Online quote and order management
- Live delivery tracking
We examine plastic zone formation, crack tip stress fields, and shear band propagation to strengthen materials for dynamic loading conditions.

Production Orders
We integrate nano-polishing techniques with real-time vibration control to deliver flawless finishes in demanding applications.
- Dedicated project managers in your time zone
- Application engineers focused on DFM cost optimizations
- First Article Inspection (FAI) for quality assurance
- Supply chain support for materials and on-time delivery
We adopt real-time performance tracking and automated resource scaling to align production capacity with variable demand cycles.
- Trusted Solutions
CNC Machining Solutions in New Mexico that You Can Trust
Our technique employs adaptive clamping systems with force-sensing actuators to stabilize intricate parts during ultra-fine machining. Raman spectroscopy confirms material properties and thin-film uniformity.
- Ultra-Tight Tolerances (±0.005mm)
- 5-Axis Machining for Complex Designs
- High-Speed Spindles (Up to 60,000 RPM)
- Adaptive Feed Rate Optimization
- Rigid Fixturing & Workholding

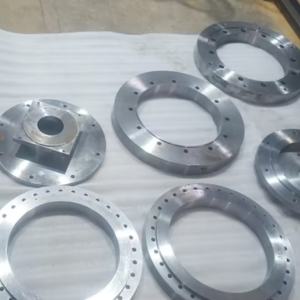
- Manufacturing Optimization
Get Started with Our CNC Machining Services
Our technique applies micro-focus X-ray inspection, laser triangulation, and dynamic thermal analysis to ensure detailed surface integrity assessment.
Self-Adaptive Machining Systems
AI-integrated systems adjust spindle speed, toolpath, and cutting force in real time to maintain optimal conditions during material variability.
Ionized Coolant Systems
Electrically charged coolant particles enhance heat transfer efficiency and improve chip breakage during aggressive cutting operations.
Microlithography-Assisted Surface Texturing
Microscale laser patterning creates engineered surface topographies, reducing friction and enhancing lubricant retention in moving parts.
- FAQ
Having Doubts? Our FAQ
Check all our Frequently Asked Questions in CNC Machining
Frigate employs advanced 5-axis CNC machines with integrated thermal compensation systems to maintain precise tolerances in aerospace-grade materials like titanium and Inconel. This approach minimizes dimensional drift caused by temperature changes, ensuring accuracy in critical flight components.
Frigate utilizes adaptive toolpath algorithms, variable spindle speeds, and cryogenic cooling systems to reduce tool wear when machining hard alloys. These methods improve surface finishes and extend tool life, ensuring consistent quality in high-volume production.
Frigate combines ceramic-coated tooling, high-pressure coolant delivery, and chip evacuation controls to manage the heat generated during machining. This method enhances cutting efficiency in heat-resistant alloys like Hastelloy and stainless steel.
Frigate applies multi-pass threading cycles, precision threading inserts, and in-process gauging systems to ensure defect-free internal and external threads. This ensures optimal thread engagement and strength, which is critical for industrial and automotive applications.
Frigate utilizes diamond burnishing tools, vibration-dampened spindles, and controlled feed rates to achieve consistent surface finishes. This combination minimizes tool marks and improves surface integrity in high-precision machined parts.
We'd love to Manufacture for you!
Submit the form below and our representative will be in touch shortly.
LOCATIONS
Registered Office
10-A, First Floor, V.V Complex, Prakash Nagar, Thiruverumbur, Trichy-620013, Tamil Nadu, India.
Operations Office
9/1, Poonthottam Nagar, Ramanandha Nagar, Saravanampatti, Coimbatore-641035, Tamil Nadu, India. ㅤ
Other Locations
- Bhilai
- Chennai
- USA
- Germany