Large-Scale Machining Solutions for Renewable Energy Components
5-axis CNC with thermal control and in-situ metrology ensures sub-50μm flatness for wind and solar system assemblies.
Frigate Expertise in High-Stress CNC Applications
Torsional Fatigue Resistance
TMCP, custom heat treatment, and fatigue-tested alloys improve crack resistance in high-speed rotating components under cyclic torsional loads.
Thermal Deformation Control
FEA-based thermal cycling, cryogenic stress relief, and CTE-matched materials minimize distortion in high-temperature operational environments.
Corrosion-Resistant Coatings
Duplex alloys, advanced anodizing, and 5000+ hour salt-spray tested coatings ensure durability in marine and high-humidity conditions.
Our Clients
Trusted by Engineers and Purchasing Leaders
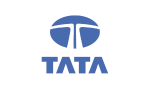
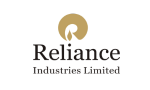


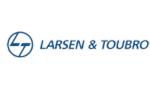
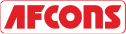


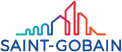

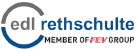

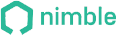
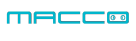









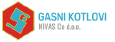
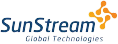

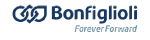


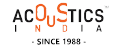
Ensure Full Traceability Across Critical Component History
Meeting traceability requirements across metallurgical and dimensional history demands tightly integrated data capture throughout the manufacturing lifecycle.
Implement QR-based digital tracking that links each part’s material batch, heat treatment curve, and dimensional log into a centralized manufacturing cloud.
Synchronize CNC, CMM, and surface treatment systems to log in-process variations directly into the part’s digital record.
Provide OEMs and EPCs with secure API access to part traceability for warranty validation, ESG compliance, and audit documentation.

Minimize Stress Concentration in Notched and Transition Zones
Eliminating stress risers in machined notches and interfaces is essential to enhance fatigue life in rotating and structural wind-solar components.
Use non-contact optical profilometers to verify radius smoothness and transition curvature within micrometer tolerances.
Apply localized surface rolling techniques to induce compressive residual stress at notch roots and sharp features.
Validate treatment effectiveness through X-ray diffraction-based stress mapping and correlate data with fatigue performance models.

Certify Dynamic Loads Using Site-Specific Simulation Protocols
Accurate structural validation under real-world site conditions requires custom fatigue spectra based on localized environmental stressors.
Integrate SCADA outputs or IEC site class data into FEA-driven structural load simulations for wind and seismic conditions.
Use servo-hydraulic testing systems to replicate worst-case R-ratios and validate fatigue resistance under site-specific cycles.
Adjust material thickness, weld positioning, and bolt torque parameters based on simulation data to avoid over- or under-engineering.

Our Machined Products
We support your production needs with CNC-machined parts, subassemblies, and performance-critical components.
- Real Impact
Words from Clients
See how global OEMs and sourcing heads describe their experience with our scalable execution.
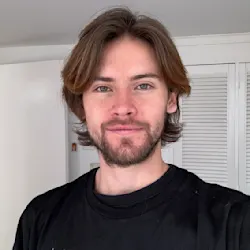
“Quick turnaround and solid quality.”
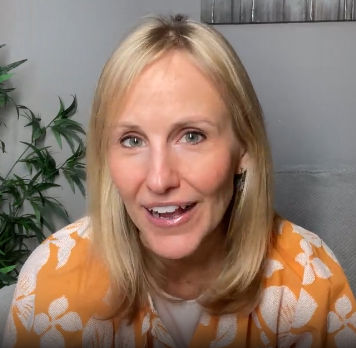
“The instant quote tool saved us time, and the parts were spot-on. Highly recommend Frigate!”
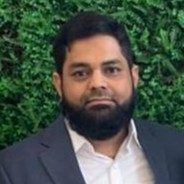
“I would strongly recommend Frigate to anyone who wants to do Rapid Prototyping, and take their ideas to manufacturing. One firm doing all kinds of Product Development!”
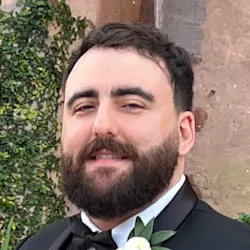
“Great service, fair price, and the parts worked perfectly in our assembly.”
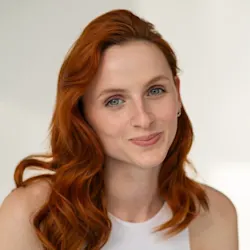
“Top-notch machining and fast shipping. Very satisfied with the results.”
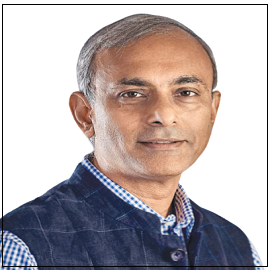
“The next disruption is happening in Prototyping & Manufacturing on-demand and Frigate is leading the way! I personally believe the Frigate's way of IIOT enabled cloud platform with Al.”
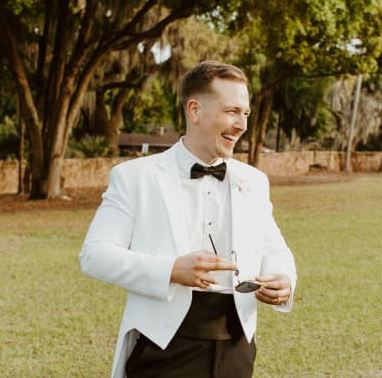
“Frigate delivered high-quality parts at a competitive price. The instant quote tool is a huge plus for us!”

“We appreciate the precision and quality of the machined components in the recent delivery—they meet our specifications perfectly and demonstrate Frigate’s capability for excellent workmanship.”
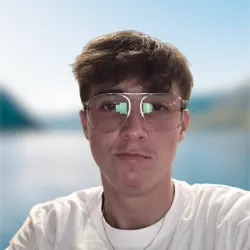
“Flawless execution from quote to delivery.”

“I am absolutely happy to work with supplier like Frigate who were quite proactive & result oriented . Frigate has high willingness team who has strong know how & their passion towards the products & process were absolutely thrilling.”
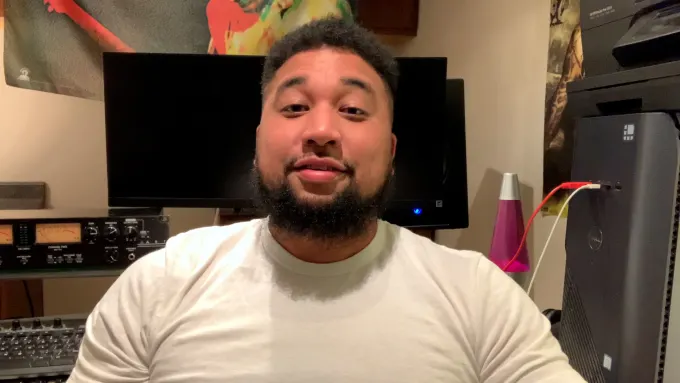
“The precision on these parts is impressive, and they arrived ahead of schedule. Frigate’s process really stands out!”
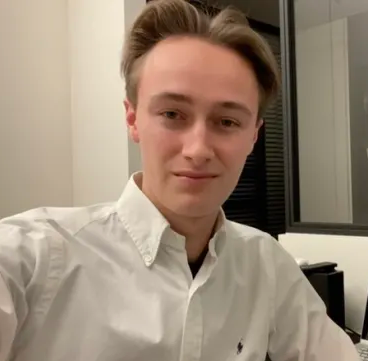
“Parts were exactly as spec’d, and the instant quote made budgeting a breeze.”
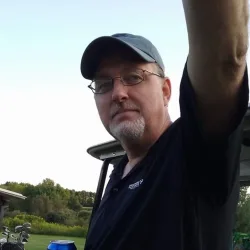
“Good value for the money.”
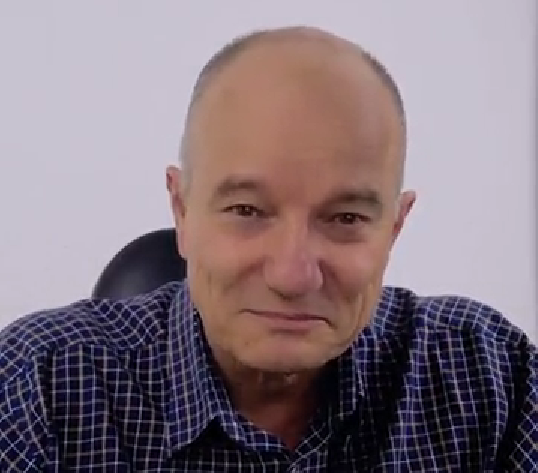
“The finish was perfect, and the team was easy to work with.”

“Working with Frigate has been great. Their proactive, results-driven approach and expertise shine through in every project. It's been a pleasure collaborating with them.”

"We are highly satisfied with the timely delivery and quality of the MIG Welding Cable from Frigate. Their attention to detail, secure packaging, and quick responsiveness stood out. We confidently recommend Frigate Engineering Services Pvt. Ltd. as a reliable manufacturing partner."
- We export to 12+ countries
Frigate’s Global Presence
Frigate takes pride in facilitating “Make in India for the globe“. As our global network of Frigaters provides virtually limitless capacity, and through our IoT enabled platform your parts go directly into production. By digitally and technologically enabling “the silent pillars of the economy” MSME and SME manufacturing industries, we are able to tap the huge potential for manufacturing to bring the best results for our clients.

100,000+
Parts Manufactured
250+
Frigaters
2000+
Machines
450+
Materials
25+
Manufacturing Process
- Solid Progress
How You Benefit with Us
Frigate brings stability, control, and predictable performance to your sourcing operations through a structured multi-vendor system.
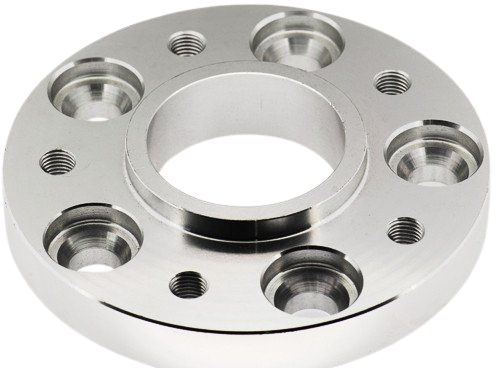
2.8X
Sourcing Cycle Speed
Frigate’s pre-qualified network shortens decision time between RFQ and PO placement.
94%
On-Time Delivery Rate
Structured planning windows and logistics-linked schedules improve project-level delivery reliability.
4X
Multi-Part Consolidation
We enable part family batching across suppliers to reduce fragmentation.
22%
Quality Rejection Rate
Multi-level quality checks and fixed inspection plans lower non-conformities.
30%
Procurement Costs
Optimized supplier negotiations and bulk order strategies reduce your overall sourcing expenses.
20%
Manual Processing Time
Automation of sourcing and supplier management significantly reduces time spent on manual tasks.
Other Industries We Serve
We deliver machining support across sectors that require consistency, material reliability, and tight dimensional control.
Get Clarity with Our Manufacturing Insights
Frigate uses advanced coolant flow systems and ceramic or carbide inserts optimized for high thermal loads. Machining parameters are dynamically adjusted using in-process monitoring to limit friction and thermal shock. This maintains part integrity and surface tolerance even under prolonged turning cycles. Each batch undergoes microstructure validation to ensure alloy properties are unaffected.
Frigate deploys variable-speed turning and harmonic dampening systems in the turret and tailstock. These reduce resonance effects when machining extended shafts with length-to-diameter ratios beyond 10:1. Custom workholding with active dampers is also used to improve rigidity. The system feedback loop fine-tunes RPM in real-time to suppress tool-induced vibration.
Frigate sets low feed rates with interrupted cuts and uses CBN-coated inserts for cutting edge stability. A precise pre-turning phase helps reduce surface strain before final passes. Continuous tool wear tracking ensures geometry remains sharp throughout. Toolpath simulation is also used to avoid sudden engagement angles that promote hardening.
Yes, Frigate employs dual-spindle machines with synchronized C-axis control for concentric pass sequencing. Live tooling and probing verify spindle alignment throughout multi-diameter features. Real-time compensation corrects thermal drift or mechanical deflection. Final verification uses CMM with roundness, coaxiality, and cylindricity analysis.
Frigate maintainsoptimal surface pressure by balancing radial and axial forces with tailored tool geometries. Machine structure thermal mapping is used to schedule dwell intervals for heat dissipation. Stress-relief cycles are also incorporated between rough and finish passes. Precision fixturing holds the part with uniform clamping pressure to prevent warping.
We'd love to Manufacture for you!
Submit the form below and our representative will be in touch shortly.
LOCATIONS
Registered Office
10-A, First Floor, V.V Complex, Prakash Nagar, Thiruverumbur, Trichy-620013, Tamil Nadu, India.
Operations Office
9/1, Poonthottam Nagar, Ramanandha Nagar, Saravanampatti, Coimbatore-641035, Tamil Nadu, India. ㅤ
Other Locations
- Bhilai
- Chennai
- USA
- Germany