Forged Solutions for Marine & Shipbuilding Industry
Frigate delivers fatigue-resistant forged components with controlled grain flow and spectral validation for critical marine systems.
Frigate Optimizes Marine Casting and Machining Processes
Controlled Microstructure in Large Castings
Frigate uses thermal modeling and directional solidification to minimize segregation, ensuring uniform grain structure in heavy marine castings.
Precision in Modular Ship Assemblies
Advanced pattern compensation and 3D scanning ensure tight tolerances with <20μm deviation in large modular marine components.
Corrosion-Resistant Marine Alloys
Engineered alloys with optimized phase balance and galvanic mapping deliver long-term corrosion resistance in immersion and splash zone conditions.
Our Clients
Trusted by Engineers and Purchasing Leaders
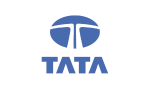
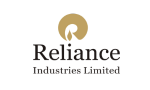


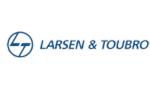
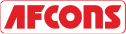


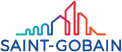

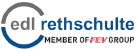

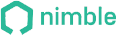
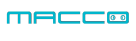









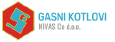
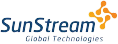

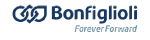


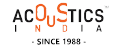
Enable Digital Traceability for Marine Classification Compliance
Ensuring part-level traceability from melt to inspection is critical for classification society audits and lifecycle material documentation.
Encode each casting or forging with a digital identifier linked to heat number, ladle batch, and part-level trace data.
Maintain all melt chemistry, NDT records, thermal history, and mechanical test results in a structured, cloud-accessible database.
Export certification packages in formats compatible with ABS, DNV, BV, and IACS software to streamline inspection and recertification workflows.

Ensure Weld Stability Across Dissimilar Marine Alloys
Joining dissimilar metals in marine structures requires metallurgical compatibility, weld zone control, and post-weld property restoration.
Modify chemistries (e.g., Mn:S ratio tuning) to stabilize fusion lines and reduce risk of heat-affected zone cracking.
Machine custom bevel geometries and apply inert gas shielding to limit oxidation and intergranular corrosion at the weld seam.
Use alloy-specific TTT diagrams to restore ductility and microstructural uniformity across complex dissimilar joints.

Optimize Vibration Resistance in Marine Drive Systems
Vibration fatigue in propulsion and auxiliary systems requires tuned geometry and damping integration to prevent resonance-induced failure.
Conduct harmonic response analysis using ODS data to avoid natural frequency alignment with operational loads.
Integrate structural ribs and tuned mass dampers during casting to reduce acoustic and mechanical vibration transfer.
Select alloy grades with high internal damping coefficients to mitigate torsional oscillation and surface fatigue.

Our Machined Products
We support your production needs with CNC-machined parts, subassemblies, and performance-critical components.
- Real Impact
Words from Clients
See how global OEMs and sourcing heads describe their experience with our scalable execution.
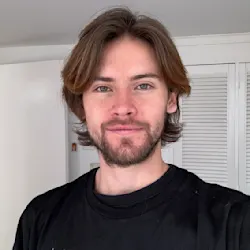
“Quick turnaround and solid quality.”
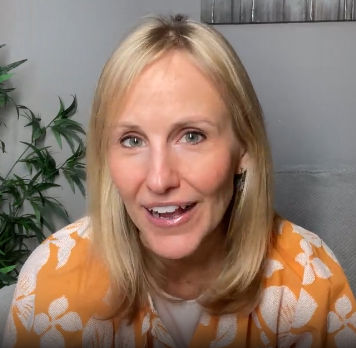
“The instant quote tool saved us time, and the parts were spot-on. Highly recommend Frigate!”
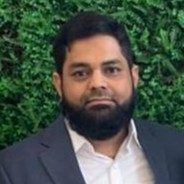
“I would strongly recommend Frigate to anyone who wants to do Rapid Prototyping, and take their ideas to manufacturing. One firm doing all kinds of Product Development!”
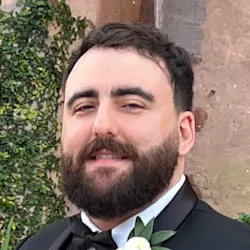
“Great service, fair price, and the parts worked perfectly in our assembly.”
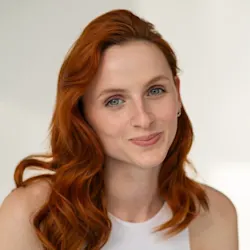
“Top-notch machining and fast shipping. Very satisfied with the results.”
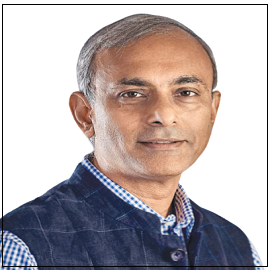
“The next disruption is happening in Prototyping & Manufacturing on-demand and Frigate is leading the way! I personally believe the Frigate's way of IIOT enabled cloud platform with Al.”
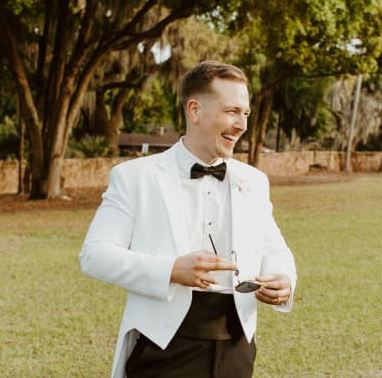
“Frigate delivered high-quality parts at a competitive price. The instant quote tool is a huge plus for us!”

“We appreciate the precision and quality of the machined components in the recent delivery—they meet our specifications perfectly and demonstrate Frigate’s capability for excellent workmanship.”
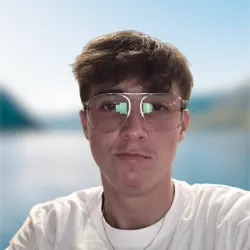
“Flawless execution from quote to delivery.”

“I am absolutely happy to work with supplier like Frigate who were quite proactive & result oriented . Frigate has high willingness team who has strong know how & their passion towards the products & process were absolutely thrilling.”
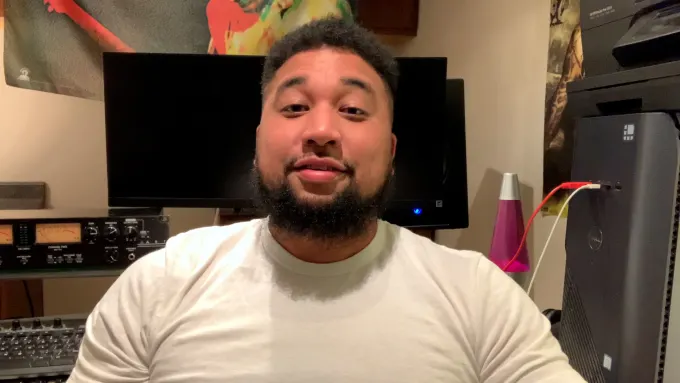
“The precision on these parts is impressive, and they arrived ahead of schedule. Frigate’s process really stands out!”
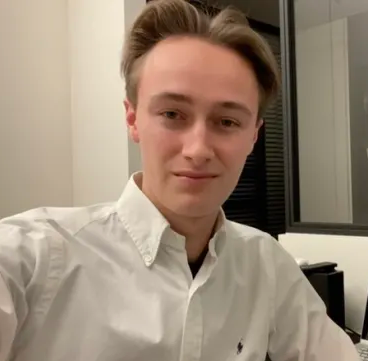
“Parts were exactly as spec’d, and the instant quote made budgeting a breeze.”
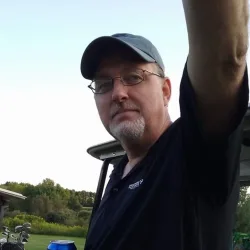
“Good value for the money.”
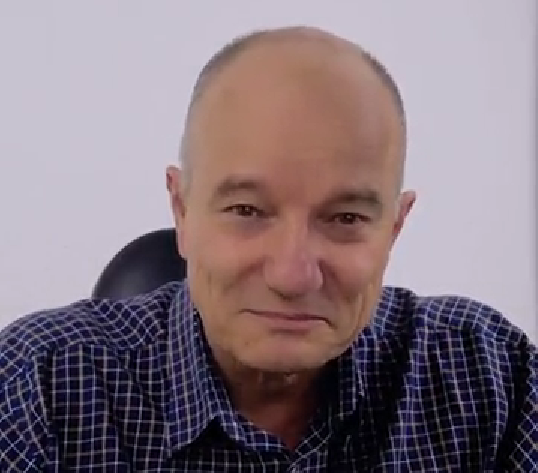
“The finish was perfect, and the team was easy to work with.”

“Working with Frigate has been great. Their proactive, results-driven approach and expertise shine through in every project. It's been a pleasure collaborating with them.”

"We are highly satisfied with the timely delivery and quality of the MIG Welding Cable from Frigate. Their attention to detail, secure packaging, and quick responsiveness stood out. We confidently recommend Frigate Engineering Services Pvt. Ltd. as a reliable manufacturing partner."
- We export to 12+ countries
Frigate’s Global Presence
Frigate takes pride in facilitating “Make in India for the globe“. As our global network of Frigaters provides virtually limitless capacity, and through our IoT enabled platform your parts go directly into production. By digitally and technologically enabling “the silent pillars of the economy” MSME and SME manufacturing industries, we are able to tap the huge potential for manufacturing to bring the best results for our clients.

100,000+
Parts Manufactured
250+
Frigaters
2000+
Machines
450+
Materials
25+
Manufacturing Process
- Solid Progress
How You Benefit with Us
Frigate brings stability, control, and predictable performance to your sourcing operations through a structured multi-vendor system.
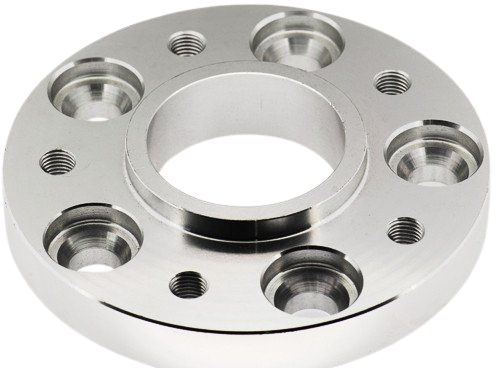
2.8X
Sourcing Cycle Speed
Frigate’s pre-qualified network shortens decision time between RFQ and PO placement.
94%
On-Time Delivery Rate
Structured planning windows and logistics-linked schedules improve project-level delivery reliability.
4X
Multi-Part Consolidation
We enable part family batching across suppliers to reduce fragmentation.
22%
Quality Rejection Rate
Multi-level quality checks and fixed inspection plans lower non-conformities.
30%
Procurement Costs
Optimized supplier negotiations and bulk order strategies reduce your overall sourcing expenses.
20%
Manual Processing Time
Automation of sourcing and supplier management significantly reduces time spent on manual tasks.
Other Industries We Serve
We deliver machining support across sectors that require consistency, material reliability, and tight dimensional control.
Get Clarity with Our Manufacturing Insights
Frigate uses solidification simulation software to predict hot spots and shrinkage-prone areas in complex marine components. Based on simulation data, chill placements and riser dimensions are optimized to ensure directional solidification. In-mold thermocouples monitor real-time cooling curves during pouring to control thermal gradients. This reduces centerline shrinkage and internal voids in heavy cross-section castings.
Frigate carefully selects compatible filler materials and modifies alloy chemistries to balance thermal expansion differences. Joint designs are customized using precise weld bevel angles to control heat input. Inert gas shielding and interpass temperature controls are applied during welding to prevent intergranular corrosion. Post-weld heat treatments are tailored using material-specific TTT diagrams to restore microstructure and toughness.
Frigate subjects forged and cast parts to high-cycle fatigue testing using wave spectrum loading based on OCIMF and DNV standards. Grain flow in forgings is aligned with principal stress directions to suppress crack initiation. Shot peening or laser peening is applied to induce compressive stress layers on critical surfaces. Fatigue life predictions are supported by FEA models using real-world loading histories.
Yes. Frigate encodes each part with a digital ID that links to a full traceability database. This includes melt chemistry, mechanical test results, thermal history, and NDT reports. All data is stored in audit-friendly formats accepted by ABS, DNV, and BV systems. Each part's trace data remains accessible for over 15 years, supporting future inspections and warranty claims.
Frigate performs harmonic response analysis to avoid resonance with shipboard machinery frequencies. Cast geometries are tuned based on modal analysis to shift natural frequencies away from operational ranges. Where necessary, ribs and damping features are built into the casting itself. Material selection also considers internal damping capacity to reduce vibration transmission and surface fatigue.
We'd love to Manufacture for you!
Submit the form below and our representative will be in touch shortly.
LOCATIONS
Registered Office
10-A, First Floor, V.V Complex, Prakash Nagar, Thiruverumbur, Trichy-620013, Tamil Nadu, India.
Operations Office
9/1, Poonthottam Nagar, Ramanandha Nagar, Saravanampatti, Coimbatore-641035, Tamil Nadu, India. ㅤ
Other Locations
- Bhilai
- Chennai
- USA
- Germany