Advanced Motion Systems for Demanding Industrial Machinery Operations
Built for extreme uptime and thermal stability to maintain accuracy under heavy loads and complex multi-axis conditions.
Frigate Integrates Edge Intelligence for Ultra-Fast Servo Feedback
Precision Axis Control
Cross-coupled PID and Kalman feedback enable real-time correction, ensuring 0.04 mm accuracy during high-speed multi-axis transitions.
Thermal Drift Compensation
RTD sensor networks map heat flux and auto-correct axis deviation, eliminating thermal-induced errors across continuous machining cycles.
Adaptive Spindle Stiffness
Embedded sensors adjust spindle preload dynamically, stabilizing cut forces and preserving tool life under variable cutting depths.
Our Clients
Trusted by Engineers and Purchasing Leaders
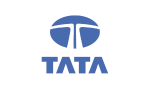
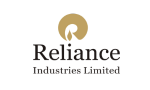


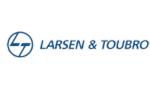
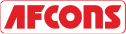


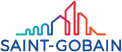

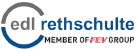

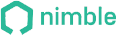
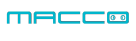









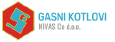
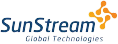

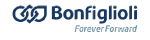


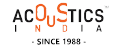
Enable Seamless IT/OT Convergence in Industrial Environments
Isolating real-time control from enterprise data flow is critical for ensuring motion stability in automated production systems.
Deploy dual-layer machine communication with deterministic EtherCAT for motion control and OPC UA over TSN for non-interfering telemetry, diagnostics, and SCADA integration.
Maintain servo loop consistency under 1ms jitter conditions, even during asynchronous enterprise-level data exchange or system diagnostics.
Use protocol-specific physical layer segmentation to prevent data collision, ensuring uninterrupted motion control in complex production cycles.

Ensure Sub-Micron Surface Integrity through Acoustic-Based Feedback
Maintaining surface quality during high-speed machining demands live feedback from tool-part interaction at the microstructural level.
Leverage embedded piezoelectric sensors to capture acoustic signatures that indicate burn marks, delamination, or microfracture risk in real time.
Dynamically adjust tool pressure, spindle retraction, and coolant delivery based on acoustic feedback to prevent surface damage before it occurs.
Achieve surface roughness below Ra 0.8 μm consistently across components with varying material densities and cut geometries.

Extend Machine Life Through Predictive Lubrication Intelligence
Minimizing wear in critical motion components requires lubrication systems responsive to actual mechanical and thermal conditions—not runtime counters.
Use embedded pressure and temperature sensors on guideways, bearings, and ball screws to compute in-situ lubrication needs.
Adjust lubricant type, volume, and interval based on real-time tribological modeling rather than fixed-cycle logic.
Reduce over-lubrication and dry-run scenarios, extending component lifespan by over 30% and maintaining motion precision over prolonged duty cycles.

Our Machined Products
We support your production needs with CNC-machined parts, subassemblies, and performance-critical components.
- Real Impact
Words from Clients
See how global OEMs and sourcing heads describe their experience with our scalable execution.
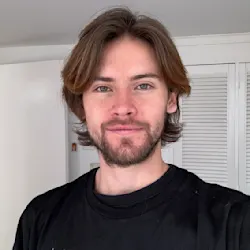
“Quick turnaround and solid quality.”
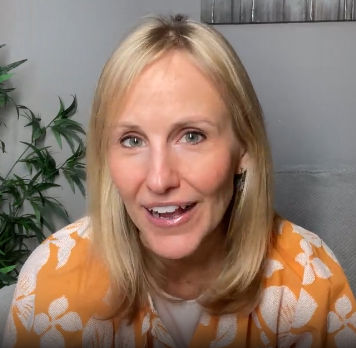
“The instant quote tool saved us time, and the parts were spot-on. Highly recommend Frigate!”
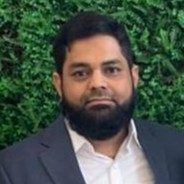
“I would strongly recommend Frigate to anyone who wants to do Rapid Prototyping, and take their ideas to manufacturing. One firm doing all kinds of Product Development!”
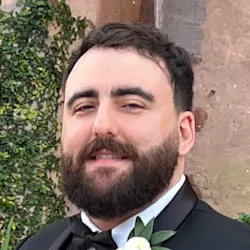
“Great service, fair price, and the parts worked perfectly in our assembly.”
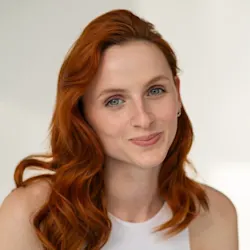
“Top-notch machining and fast shipping. Very satisfied with the results.”
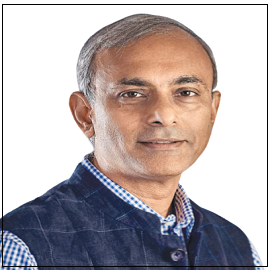
“The next disruption is happening in Prototyping & Manufacturing on-demand and Frigate is leading the way! I personally believe the Frigate's way of IIOT enabled cloud platform with Al.”
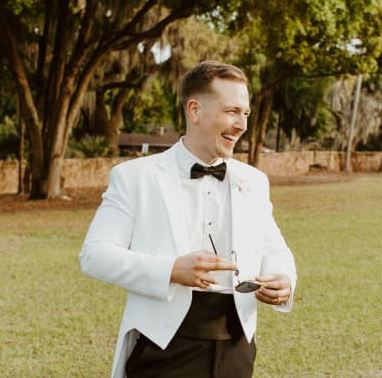
“Frigate delivered high-quality parts at a competitive price. The instant quote tool is a huge plus for us!”

“We appreciate the precision and quality of the machined components in the recent delivery—they meet our specifications perfectly and demonstrate Frigate’s capability for excellent workmanship.”
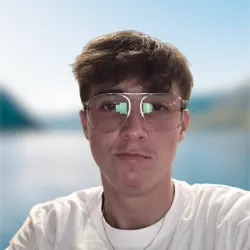
“Flawless execution from quote to delivery.”

“I am absolutely happy to work with supplier like Frigate who were quite proactive & result oriented . Frigate has high willingness team who has strong know how & their passion towards the products & process were absolutely thrilling.”
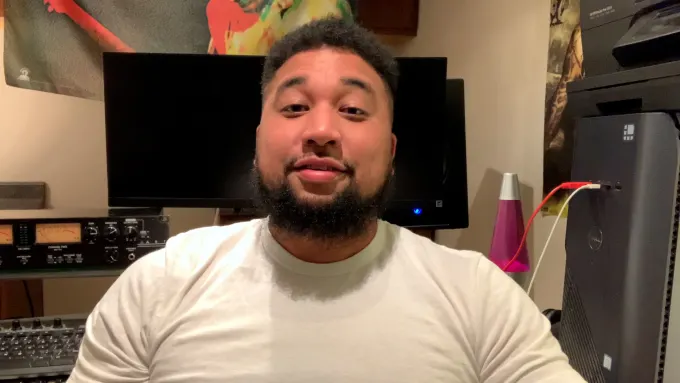
“The precision on these parts is impressive, and they arrived ahead of schedule. Frigate’s process really stands out!”
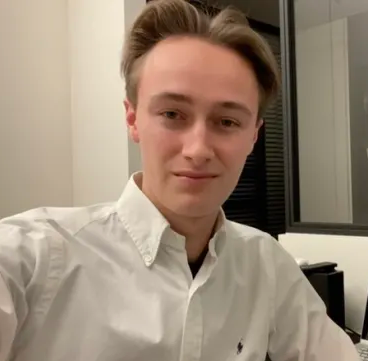
“Parts were exactly as spec’d, and the instant quote made budgeting a breeze.”
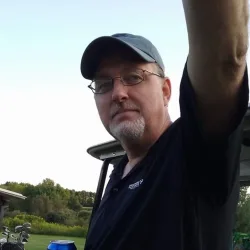
“Good value for the money.”
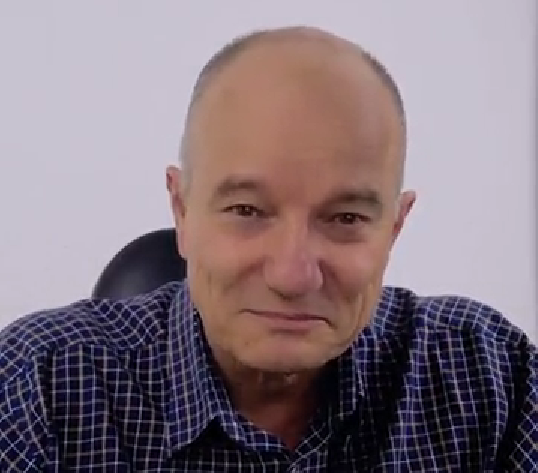
“The finish was perfect, and the team was easy to work with.”

“Working with Frigate has been great. Their proactive, results-driven approach and expertise shine through in every project. It's been a pleasure collaborating with them.”

"We are highly satisfied with the timely delivery and quality of the MIG Welding Cable from Frigate. Their attention to detail, secure packaging, and quick responsiveness stood out. We confidently recommend Frigate Engineering Services Pvt. Ltd. as a reliable manufacturing partner."
- We export to 12+ countries
Frigate’s Global Presence
Frigate takes pride in facilitating “Make in India for the globe“. As our global network of Frigaters provides virtually limitless capacity, and through our IoT enabled platform your parts go directly into production. By digitally and technologically enabling “the silent pillars of the economy” MSME and SME manufacturing industries, we are able to tap the huge potential for manufacturing to bring the best results for our clients.

100,000+
Parts Manufactured
250+
Frigaters
2000+
Machines
450+
Materials
25+
Manufacturing Process
- Solid Progress
How You Benefit with Us
Frigate brings stability, control, and predictable performance to your sourcing operations through a structured multi-vendor system.
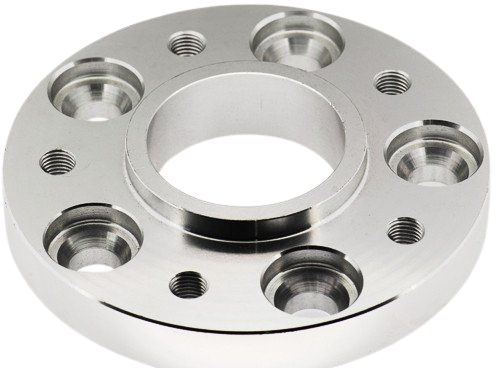
2.8X
Sourcing Cycle Speed
Frigate’s pre-qualified network shortens decision time between RFQ and PO placement.
94%
On-Time Delivery Rate
Structured planning windows and logistics-linked schedules improve project-level delivery reliability.
4X
Multi-Part Consolidation
We enable part family batching across suppliers to reduce fragmentation.
22%
Quality Rejection Rate
Multi-level quality checks and fixed inspection plans lower non-conformities.
30%
Procurement Costs
Optimized supplier negotiations and bulk order strategies reduce your overall sourcing expenses.
20%
Manual Processing Time
Automation of sourcing and supplier management significantly reduces time spent on manual tasks.
Other Industries We Serve
We deliver machining support across sectors that require consistency, material reliability, and tight dimensional control.
Get Clarity with Our Manufacturing Insights
Frigate uses thermal expansion prediction models integrated into its CAM simulations to anticipate distortion under dynamic loads. All critical joint areas are machined using controlled cooling cycles and balanced tool paths to reduce localized heat accumulation. Additionally, Frigate performs post-machining thermal stability testing on complex assemblies. This ensures that robotic joints maintain positional accuracy even after thousands of thermal cycles in the field.
Frigate employs custom modular fixturing systems designed for each component’s unique geometry and mass distribution. These fixtures allow unrestricted access during 5-axis machining while eliminating vibration and clamping distortion. Adaptive probing systems calibrate every workpiece before tool engagement, ensuring alignment to sub-micron levels. This approach is crucial for precision parts like end-effectors and rotating gear housings.
Frigate uses non-contact laser scanning systems that generate a 3D point cloud of the machined surface, compared against the original CAD model. Advanced surface deviation analysis is run to flag out-of-tolerance zones beyond 10 microns. This technique allows Frigate to validate freeform geometries used in robotic arms and covers with exceptional repeatability. All validation data is logged and traceable to each batch.
Frigate uses low-rpm finishing passes combined with high-pressure through-spindle coolant delivery to dissipate cutting heat during final machining. For titanium, toolpath strategies are optimized to reduce radial engagement and chip thickness, minimizing surface stress. Frigate also conducts in-process eddy current inspection to detect microstructural anomalies early. This helps eliminate failure risk in high-load robotic frames and fasteners.
Frigate uses matched machining setups with reference datums established across multiple parts in a single setup to control stack-up variation. High-precision dowel pin locations are interpolated using circle interpolation to maintain concentricity. Every pair of mating components undergoes kinematic simulation to ensure real-world alignment integrity. This ensures zero-play fitment in robotic gearboxes, sensor mounts, and servo motor interfaces.
We'd love to Manufacture for you!
Submit the form below and our representative will be in touch shortly.
LOCATIONS
Registered Office
10-A, First Floor, V.V Complex, Prakash Nagar, Thiruverumbur, Trichy-620013, Tamil Nadu, India.
Operations Office
9/1, Poonthottam Nagar, Ramanandha Nagar, Saravanampatti, Coimbatore-641035, Tamil Nadu, India. ㅤ
Other Locations
- Bhilai
- Chennai
- USA
- Germany