Food Processing Machinery Industry Machining Solutions
Get Clean-In-Place Designs, Sanitary Standards, and High-Throughput Machinery with Frigate’s CNC-Machined Stainless Components for Reliable Plant Operations.
Frigate strengthen supply reliability for hygiene-focused production lines
Precision Fit for Hygienic Seals
Use 3-axis and 5-axis CNC milling to maintain ±0.001 inch tolerances for valve housings, pump rotors, and sanitary pipe fittings.
Food-Grade Material Machining
Apply 304, 316L, and 17-4 PH stainless steels with specific machining strategies that reduce work hardening and ensure clean finishes.
Smooth Surface Finishing
Use fine-pass cutting, reaming, and electropolishing steps to achieve low Ra values suitable for direct food contact zones.
Our Clients
Trusted by Engineers and Purchasing Leaders
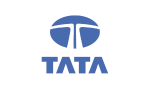
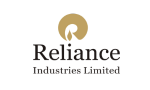


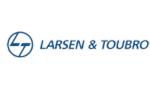
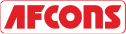


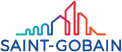

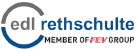

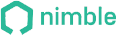
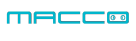









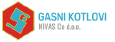
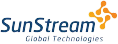

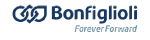


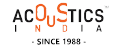
Certify Product Contact Compliance with Documented Quality Checks
Verification of material traceability and compliance with food safety codes is necessary for assemblies that contact consumables.
Parts are delivered with EN 10204 3.1 certificates and meet guidelines per FDA 21 CFR and EC 1935/2004 where applicable.
Each machined batch includes unique heat numbers and lot identification for downstream compliance and recall readiness.
Surface finish reports are recorded digitally, with post-process Ra measurements for all wetted or exposed zones.

Maintain Sanitary Reliability in Washdown and High-Moisture Zones
High humidity and routine washdowns demand tight material control to prevent bacterial growth and surface degradation.
Machined parts maintain Ra < 0.8 µm via polishing and microfinishing processes for pumps, dispensers, and mixing blades.
Thermal Processing Stability
Material choices and finishing techniques support resistance to caustic and acidic CIP chemicals used in food-grade line cleaning.

Improve Uptime with Hard Coatings and Wear Surface Upgrades
Wear protection and reduced friction are key in high-speed conveyors, slicers, and rotary filling equipment.
PTFE and ceramic-based coatings reduce drag and improve cleanability on high-cycle contact surfaces.
Laser-cladded or plasma-sprayed overlays are applied on contact surfaces to reduce erosion and extend tooling life.
Critical tolerances are restored through finish machining post-coating, ensuring dimensional fit for mating components.

Our Machined Products
We support your production needs with CNC-machined parts, subassemblies, and performance-critical components.
- Real Impact
Words from Clients
See how global OEMs and sourcing heads describe their experience with our scalable execution.
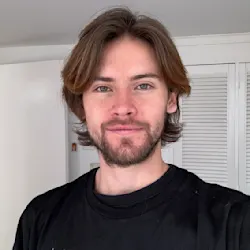
“Quick turnaround and solid quality.”
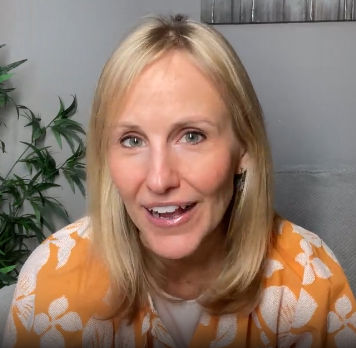
“The instant quote tool saved us time, and the parts were spot-on. Highly recommend Frigate!”
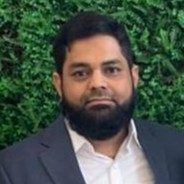
“I would strongly recommend Frigate to anyone who wants to do Rapid Prototyping, and take their ideas to manufacturing. One firm doing all kinds of Product Development!”
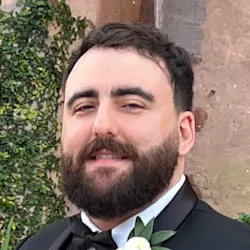
“Great service, fair price, and the parts worked perfectly in our assembly.”
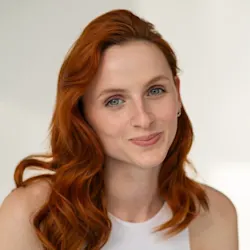
“Top-notch machining and fast shipping. Very satisfied with the results.”
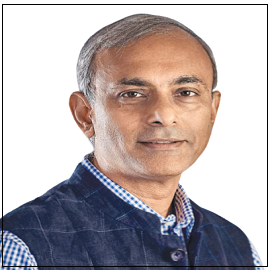
“The next disruption is happening in Prototyping & Manufacturing on-demand and Frigate is leading the way! I personally believe the Frigate's way of IIOT enabled cloud platform with Al.”
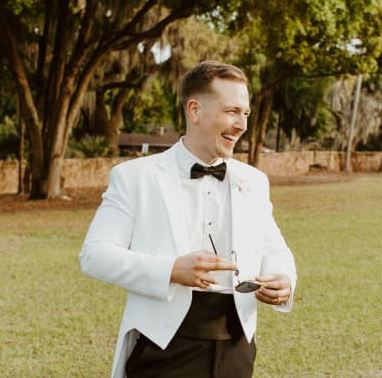
“Frigate delivered high-quality parts at a competitive price. The instant quote tool is a huge plus for us!”

“We appreciate the precision and quality of the machined components in the recent delivery—they meet our specifications perfectly and demonstrate Frigate’s capability for excellent workmanship.”
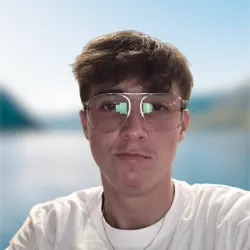
“Flawless execution from quote to delivery.”

“I am absolutely happy to work with supplier like Frigate who were quite proactive & result oriented . Frigate has high willingness team who has strong know how & their passion towards the products & process were absolutely thrilling.”
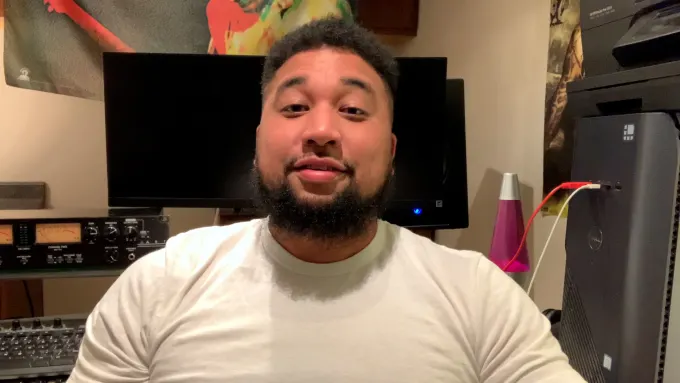
“The precision on these parts is impressive, and they arrived ahead of schedule. Frigate’s process really stands out!”
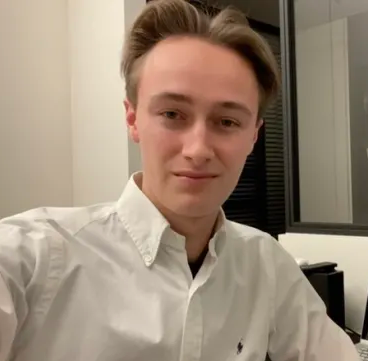
“Parts were exactly as spec’d, and the instant quote made budgeting a breeze.”
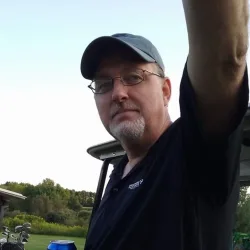
“Good value for the money.”
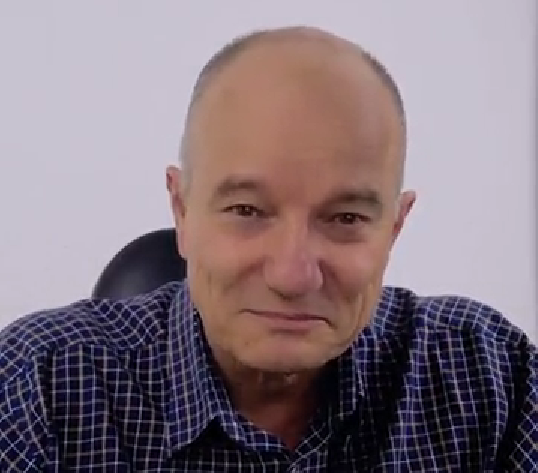
“The finish was perfect, and the team was easy to work with.”

“Working with Frigate has been great. Their proactive, results-driven approach and expertise shine through in every project. It's been a pleasure collaborating with them.”

"We are highly satisfied with the timely delivery and quality of the MIG Welding Cable from Frigate. Their attention to detail, secure packaging, and quick responsiveness stood out. We confidently recommend Frigate Engineering Services Pvt. Ltd. as a reliable manufacturing partner."
- We export to 12+ countries
Frigate’s Global Presence
Frigate takes pride in facilitating “Make in India for the globe“. As our global network of Frigaters provides virtually limitless capacity, and through our IoT enabled platform your parts go directly into production. By digitally and technologically enabling “the silent pillars of the economy” MSME and SME manufacturing industries, we are able to tap the huge potential for manufacturing to bring the best results for our clients.

100,000+
Parts Manufactured
250+
Frigaters
2000+
Machines
450+
Materials
25+
Manufacturing Process
- Solid Progress
How You Benefit with Us
Frigate brings stability, control, and predictable performance to your sourcing operations through a structured multi-vendor system.
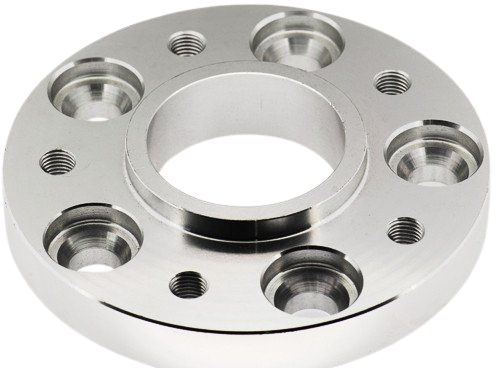
2.8X
Sourcing Cycle Speed
Frigate’s pre-qualified network shortens decision time between RFQ and PO placement.
94%
On-Time Delivery Rate
Structured planning windows and logistics-linked schedules improve project-level delivery reliability.
4X
Multi-Part Consolidation
We enable part family batching across suppliers to reduce fragmentation.
22%
Quality Rejection Rate
Multi-level quality checks and fixed inspection plans lower non-conformities.
30%
Procurement Costs
Optimized supplier negotiations and bulk order strategies reduce your overall sourcing expenses.
20%
Manual Processing Time
Automation of sourcing and supplier management significantly reduces time spent on manual tasks.
Other Industries We Serve
We deliver machining support across sectors that require consistency, material reliability, and tight dimensional control.
Get Clarity with Our Manufacturing Insights
Frigate uses specialized multi-pass milling and controlled-speed polishing to reach Ra values below 0.8 µm on contact surfaces. Toolpaths are optimized to reduce vibration and cutter marks, especially on valves, impellers, and mixers. Post-machining processes like electropolishing and fine abrasive flow machining smooth the surface while minimizing embedded particles. Each wetted part undergoes non-contact profilometry to verify compliance with FDA and EC surface finish guidelines. This method allows Frigate to meet hygiene-driven specifications without manual rework or inconsistent operator input, ensuring all machined components are compatible with CIP and SIP procedures used in modern food processing lines.
Frigate applies process controls that adapt to environmental changes such as humidity and temperature fluctuations common in washdown zones. Closed-loop thermal compensation adjusts offsets in real time using live data from machine probes and spindle sensors. All stainless steel grades, such as 316L and 17-4 PH, are preconditioned to stabilize grain structure and minimize distortion. After roughing, semi-finish passes allow for controlled stress release before final cuts. This sequence maintains tight tolerances across rotating parts, modular tooling, and pressure-sealed assemblies, even when plant conditions change between wet and dry cycles during daily production.
Frigate sources and documents all raw materials from certified mills with 3.1 traceability per EN 10204. Materials like 316L, 304, and food-grade plastics (such as UHMW-PE and PTFE) are batch-verified for chemical composition and surface integrity. CNC operations are run on dedicated machines for stainless production, avoiding cross-contamination from other metals. All fluids used in the machining process are FDA-approved and tested for residue. After machining components undergo ultrasonic cleaning and are inspected visually and dimensionally under white-light conditions. These steps ensure all machined parts meet contact safety criteria without introducing contamination risks.
Frigate maintains a digital record for each machined food equipment part, including material batch numbers, machine IDs, in-process inspection results, and surface finish reports. Quality plans are linked to the part number, providing auditors with direct access to compliance documents, COC, and final inspection logs. All records are time-stamped and stored in traceable archives compatible with ISO 22000, HACCP, and GFSI frameworks. This traceability extends to surface Ra values, weld maps (if applicable), and coating certifications, helping manufacturers demonstrate hygiene protocol adherence during both internal reviews and third-party audits.
Frigate applies coatings and treatments that improve wear resistance in augers, blade mounts, and contact chutes used in high-speed lines. Low-friction coatings such as ceramic-filled PTFE or FDA-approved PVD layers reduce galling and surface drag. In abrasive applications like flour or sugar handling, Frigate uses hardened stainless or nitrided surfaces to delay degradation. Coated parts are re-machined to meet tolerances after curing to retain proper fit. Each upgrade is validated with coating thickness measurement and adhesion testing, ensuring performance without compromising food safety or cleanability.
We'd love to Manufacture for you!
Submit the form below and our representative will be in touch shortly.
LOCATIONS
Registered Office
10-A, First Floor, V.V Complex, Prakash Nagar, Thiruverumbur, Trichy-620013, Tamil Nadu, India.
Operations Office
9/1, Poonthottam Nagar, Ramanandha Nagar, Saravanampatti, Coimbatore-641035, Tamil Nadu, India. ㅤ
Other Locations
- Bhilai
- Chennai
- USA
- Germany