Dental & Orthodontics Industry Machining Solutions
Achieve Clinical Outcomes with Frigate’s High-Tolerance, Biocompatible Components for Surgical Tools, Implants, and Orthodontic Systems.
Frigate execute your dental manufacturing needs with certified CNC capabilities
Tight Tolerance Consistency
Achieve ±0.002 mm tolerances using multi-axis CNC setups and contactless CMM to meet dental fit and form demands.
Biocompatible Material Machining
Process titanium grades, stainless steels, and PEEK polymers under validated workflows to align with ISO 10993 and ISO 13485 requirements.
Micro-Scale Feature Integration
Use high-speed micromachining and CAM-driven nesting to create slots, threads, and fillets under 0.5 mm with repeatable output.
Our Clients
Trusted by Engineers and Purchasing Leaders
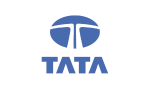
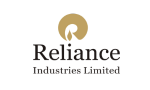


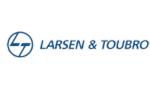
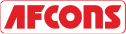


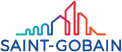

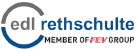

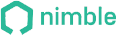
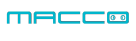









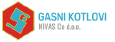
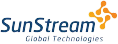

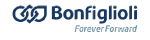


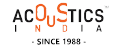
Support Sterilization and Wear Cycles in Clinical Use
Durability and dimensional control are critical for tools and implants undergoing repeated autoclaving and mechanical contact.
Polishing and controlled deburring prevent microbial retention and maintain dimensional precision after ultrasonic and chemical cleaning.
Produce friction interfaces using duplex stainless or coated titanium for orthodontic wires, fasteners, and torque transfer units.
Toolpaths and edge rounding reduce notch effects and premature cracking in small-scale hinge or engagement features.

Meet Global Dental Standards with Process-Driven Inspection
Process validation and inspection routines support qualification under ISO 13485 and FDA 21 CFR Part 820 for medical components.
Use CMM, laser scanning, and white light interferometry to verify critical areas including thread depth, taper angle, and seating surfaces.
All records follow ISO 13485 and FDA audit trails, linking revision numbers, operator IDs, and machine logs to each production lot.
Control plans include Cp/Cpk data and gauge repeatability studies to confirm tooling stability across batch sizes.

Extend Component Longevity with Surface and Coating Treatments
Functional coatings and polishing improve material compatibility and extend in-mouth or procedural part life.
Apply PVD coatings such as TiN or DLC to reduce wear on archwires, surgical drill sleeves, or torque tools.
Automated buffing, vibratory finishing, and manual polishing reduce Ra values under 0.1 µm for implants and abutments.
Micro-deburring under magnification prevents sharp edges in intraoral tools while maintaining critical dimension limits.

Our Machined Products
We support your production needs with CNC-machined parts, subassemblies, and performance-critical components.
- Real Impact
Words from Clients
See how global OEMs and sourcing heads describe their experience with our scalable execution.
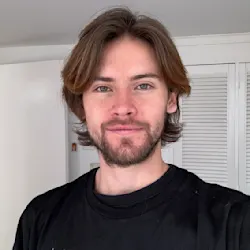
“Quick turnaround and solid quality.”
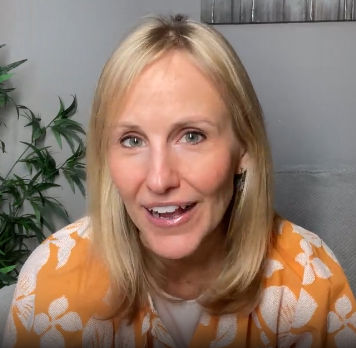
“The instant quote tool saved us time, and the parts were spot-on. Highly recommend Frigate!”
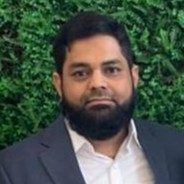
“I would strongly recommend Frigate to anyone who wants to do Rapid Prototyping, and take their ideas to manufacturing. One firm doing all kinds of Product Development!”
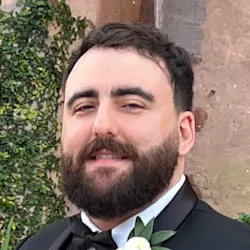
“Great service, fair price, and the parts worked perfectly in our assembly.”
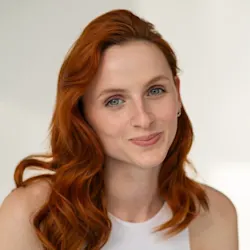
“Top-notch machining and fast shipping. Very satisfied with the results.”
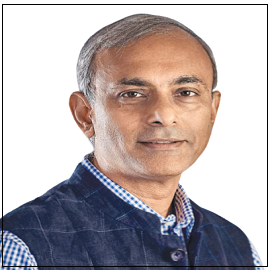
“The next disruption is happening in Prototyping & Manufacturing on-demand and Frigate is leading the way! I personally believe the Frigate's way of IIOT enabled cloud platform with Al.”
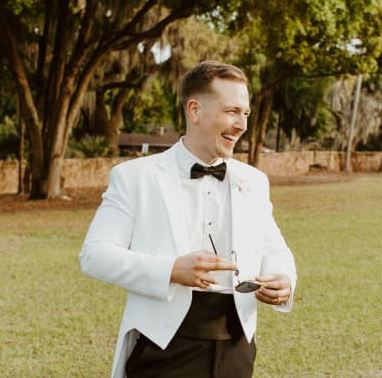
“Frigate delivered high-quality parts at a competitive price. The instant quote tool is a huge plus for us!”

“We appreciate the precision and quality of the machined components in the recent delivery—they meet our specifications perfectly and demonstrate Frigate’s capability for excellent workmanship.”
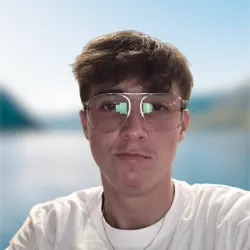
“Flawless execution from quote to delivery.”

“I am absolutely happy to work with supplier like Frigate who were quite proactive & result oriented . Frigate has high willingness team who has strong know how & their passion towards the products & process were absolutely thrilling.”
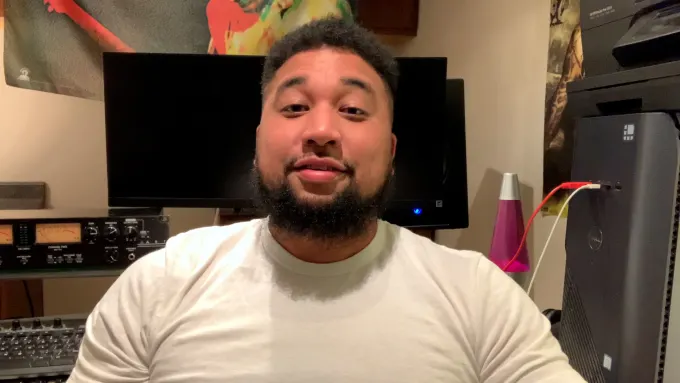
“The precision on these parts is impressive, and they arrived ahead of schedule. Frigate’s process really stands out!”
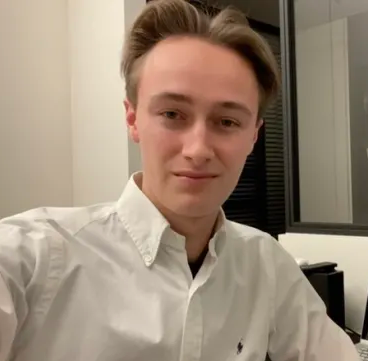
“Parts were exactly as spec’d, and the instant quote made budgeting a breeze.”
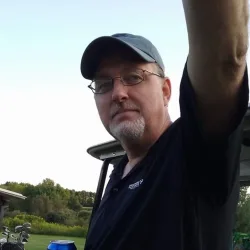
“Good value for the money.”
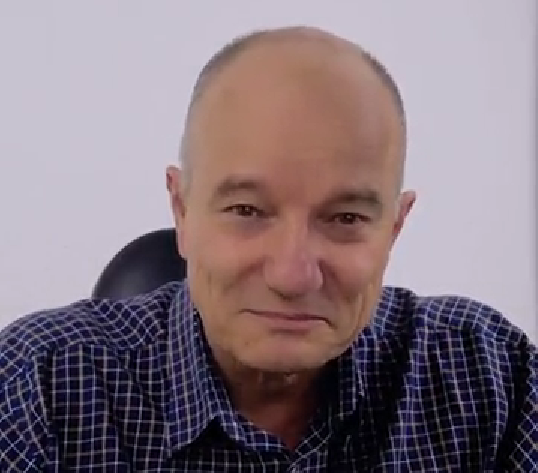
“The finish was perfect, and the team was easy to work with.”

“Working with Frigate has been great. Their proactive, results-driven approach and expertise shine through in every project. It's been a pleasure collaborating with them.”

"We are highly satisfied with the timely delivery and quality of the MIG Welding Cable from Frigate. Their attention to detail, secure packaging, and quick responsiveness stood out. We confidently recommend Frigate Engineering Services Pvt. Ltd. as a reliable manufacturing partner."
- We export to 12+ countries
Frigate’s Global Presence
Frigate takes pride in facilitating “Make in India for the globe“. As our global network of Frigaters provides virtually limitless capacity, and through our IoT enabled platform your parts go directly into production. By digitally and technologically enabling “the silent pillars of the economy” MSME and SME manufacturing industries, we are able to tap the huge potential for manufacturing to bring the best results for our clients.

100,000+
Parts Manufactured
250+
Frigaters
2000+
Machines
450+
Materials
25+
Manufacturing Process
- Solid Progress
How You Benefit with Us
Frigate brings stability, control, and predictable performance to your sourcing operations through a structured multi-vendor system.
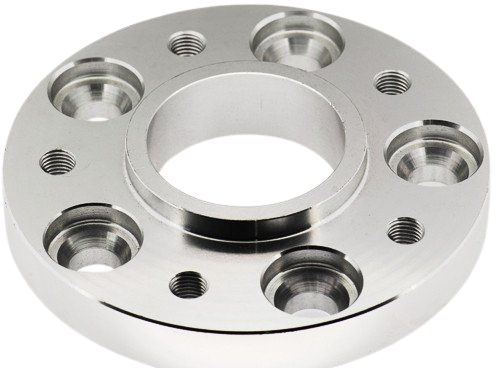
2.8X
Sourcing Cycle Speed
Frigate’s pre-qualified network shortens decision time between RFQ and PO placement.
94%
On-Time Delivery Rate
Structured planning windows and logistics-linked schedules improve project-level delivery reliability.
4X
Multi-Part Consolidation
We enable part family batching across suppliers to reduce fragmentation.
22%
Quality Rejection Rate
Multi-level quality checks and fixed inspection plans lower non-conformities.
30%
Procurement Costs
Optimized supplier negotiations and bulk order strategies reduce your overall sourcing expenses.
20%
Manual Processing Time
Automation of sourcing and supplier management significantly reduces time spent on manual tasks.
Other Industries We Serve
We deliver machining support across sectors that require consistency, material reliability, and tight dimensional control.
Get Clarity with Our Manufacturing Insights
Frigate machines dental components with tolerances down to ±0.002 mm using high-speed spindles, thermally stable setups, and in-situ CMM inspection. Real-time positional feedback and machine compensation algorithms adjust for micro-scale tool deflection and ambient thermal variation. Tool changes and spindle warm-up cycles are monitored using cycle-specific benchmarks to prevent dimensional drift. These practices help maintain geometric stability even in features under 0.5 mm, including thread leads, press fits, and intrabody tapers. Each batch undergoes statistical validation with Cp/Cpk ≥ 1.67 across critical dimensions. This process ensures functional accuracy for orthodontic brackets, implant screws, and drill guide sleeves in long production runs.
Yes. Frigate deploys multi-step deburring techniques, including ultrasonic agitation, micro-abrasive blasting, and toolpath-controlled chamfering. Edge radii as small as 0.05 mm are consistently maintained without degrading mating surfaces. Features like clip slots, interlocking arms, and self-locking hooks are processed using magnified inspection and precision tweezers to remove particulate residue. In-process air knives and vacuum evacuation limit burr formation during initial cuts. Final inspection uses high-magnification visual checks to confirm edge clarity and profile symmetry. This ensures all intraoral components meet performance and hygiene expectations without post-assembly interference or manual rework.
Frigate applies plasma-polished and acid-etched finishes that consistently meet ISO 4287-defined surface profiles with Ra < 0.1 µm. These textures promote early-stage bone contact and fluid compatibility. Surface integrity is verified using optical profilometry and contact stylus methods, comparing results against application-specific roughness and peak distribution targets. Material-specific workflows are used for Ti6Al4V and zirconia to prevent contamination during finishing. Cleanroom-compatible rinsing and vacuum drying complete the cycle. This level of surface control supports consistent tissue response in root-form implants, healing abutments, and other Class II/III implant-grade parts.
Frigate integrates part-specific data logging into its MES using UDI, operator ID, and machine telemetry. Each machined component receives a unique digital identifier linking it to tool wear records, spindle runtime, fixture location, and part inspection logs. Deviations are flagged automatically and quarantined for review before the batch proceeds. Documentation includes revision control, environmental conditions, and torque loads during fixturing. This supports regulatory submissions and end-client validation under ISO 13485, FDA 21 CFR Part 820, and EU MDR. Full traceability down to sub-batch level ensures zero-gap tracking from raw stock to packaged part.
Frigate supports cleanroom-grade manufacturing within ISO Class 7 environments equipped with positive-pressure airflow and particle-controlled zones. Machined parts undergo pre-cleaning using high-frequency ultrasonic systems and validated surfactants before being moved to assembly or packaging. HEPA filtration and antistatic protection limit airborne and contact contamination. Packaging uses ISO 11607-compatible films, sealed under laminar flow. All surfaces that come into patient contact are double-verified through bioburden testing protocols. These practices allow immediate integration into cleanroom workflows for dental implants, surgical guides, and orthodontic trays without additional decontamination steps.
We'd love to Manufacture for you!
Submit the form below and our representative will be in touch shortly.
LOCATIONS
Registered Office
10-A, First Floor, V.V Complex, Prakash Nagar, Thiruverumbur, Trichy-620013, Tamil Nadu, India.
Operations Office
9/1, Poonthottam Nagar, Ramanandha Nagar, Saravanampatti, Coimbatore-641035, Tamil Nadu, India. ㅤ
Other Locations
- Bhilai
- Chennai
- USA
- Germany