Your Trusted Partner for Aerospace & Automotive CNC Manufacturing
Delivering Excellence to 100+ Manufacturing Units Worldwide
Frigate’s Advanced Manufacturing Capabilities
Certified Quality Control
AS9100-compliant production is maintained with full traceability, controlled processes, and documented inspections for aerospace and defense-grade components.
Reduced Lead Times
Lead times are minimized through integrated manufacturing, in-house operations, and dependable sourcing tailored for critical aerospace and defense schedules.
Precision in Exotic Alloys
Tight-tolerance components in titanium, Inconel, and aluminum are produced using advanced tooling, thermal control, and simulation-driven process planning.
Our Clients
Trusted by Engineers and Purchasing Leaders
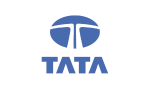
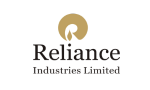


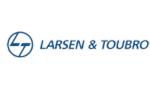
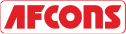


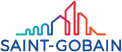

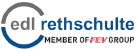

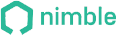
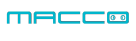









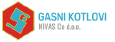
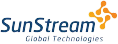

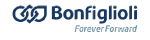


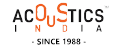
Deliver Consistent Micron-Accuracy on Complex Components
Achieving micron-level dimensional accuracy and complex part geometries requires advanced CNC machining strategies tailored for aerospace-grade components.
Utilize 5-axis CNC machines with positional accuracy up to ±5 microns (±0.005 mm), enabling the production of complex contours, pockets, and features critical for aerodynamic and structural integrity.
Apply optimized spindle speeds (up to 20,000 RPM) and feed rates while using vibration-damping fixtures to machine thin walls as thin as 0.5 mm without deformation or chatter.
Implement process monitoring systems and precision fixtures to maintain tolerances typically within ±10 microns (±0.01 mm) across batch runs, ensuring interchangeability and consistent component performance.
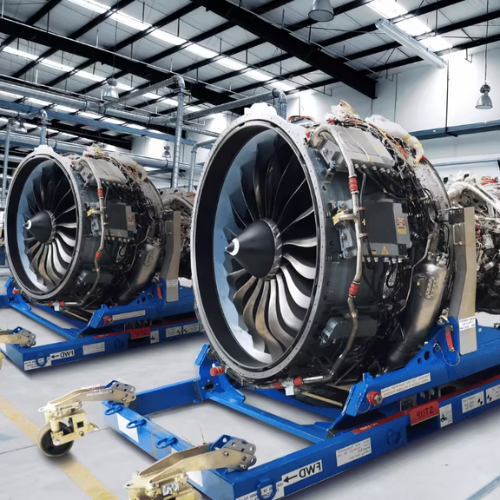
Optimize Machining for Exotic Aerospace Materials
Machining aerospace alloys like titanium, Inconel, and other nickel-based superalloys demands specialized approaches to mitigate challenges posed by their material properties.
Control cutting temperatures typically below 100°C through precise parameter optimization to minimize thermal expansion and residual stress, avoiding distortion beyond ±15 microns.
Use carbide or PVD-coated tools designed for superalloys, optimizing cutting speeds between 30–80 m/min and feed rates to maximize tool life and surface finish quality (Ra < 0.8 µm).
Employ high-pressure coolant delivery systems (up to 70 bar) for effective heat dissipation and lubrication, preventing work hardening and extending tool life by up to 30%.

Provide Complete Quality Compliance and Traceability
Manufacturing aerospace CNC components requires comprehensive quality systems ensuring regulatory compliance and traceability throughout all production stages.
Verify 100% traceability of materials back to the mill heat with full chemical composition and mechanical property certification, meeting AS9100 and NADCAP standards.
Perform first article inspections (FAI) with coordinate measuring machines (CMM) capable of accuracy ±2 microns, alongside optical and surface finish inspections to confirm conformance.
Maintain detailed inspection and process control records for 100% of production lots, compliant with AS9100, NADCAP, and ITAR, ensuring audit readiness and full traceability for safety-critical aerospace components.

Our Machined Products
We support your production needs with CNC-machined parts, subassemblies, and performance-critical components.
- Real Impact
Words from Clients
See how global OEMs and sourcing heads describe their experience with our scalable execution.
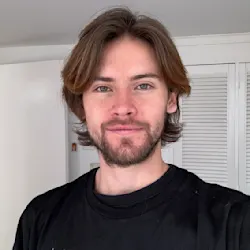
“Quick turnaround and solid quality.”
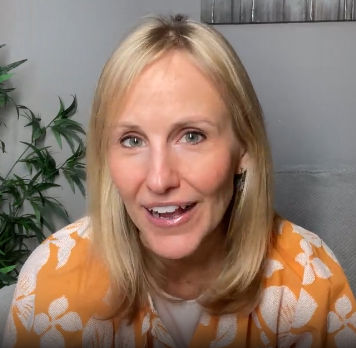
“The instant quote tool saved us time, and the parts were spot-on. Highly recommend Frigate!”
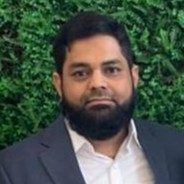
“I would strongly recommend Frigate to anyone who wants to do Rapid Prototyping, and take their ideas to manufacturing. One firm doing all kinds of Product Development!”
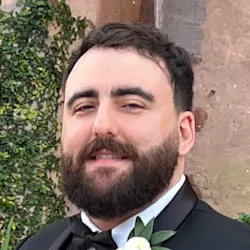
“Great service, fair price, and the parts worked perfectly in our assembly.”
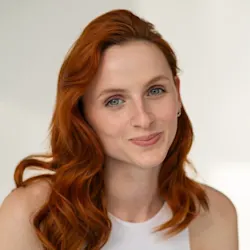
“Top-notch machining and fast shipping. Very satisfied with the results.”
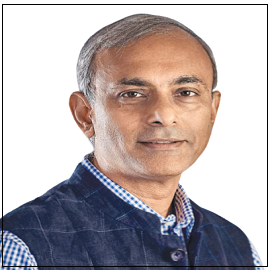
“The next disruption is happening in Prototyping & Manufacturing on-demand and Frigate is leading the way! I personally believe the Frigate's way of IIOT enabled cloud platform with Al.”
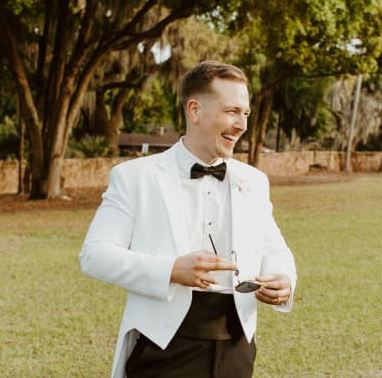
“Frigate delivered high-quality parts at a competitive price. The instant quote tool is a huge plus for us!”

“We appreciate the precision and quality of the machined components in the recent delivery—they meet our specifications perfectly and demonstrate Frigate’s capability for excellent workmanship.”
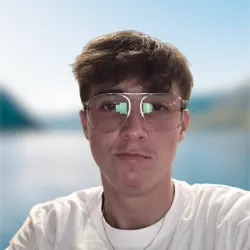
“Flawless execution from quote to delivery.”

“I am absolutely happy to work with supplier like Frigate who were quite proactive & result oriented . Frigate has high willingness team who has strong know how & their passion towards the products & process were absolutely thrilling.”
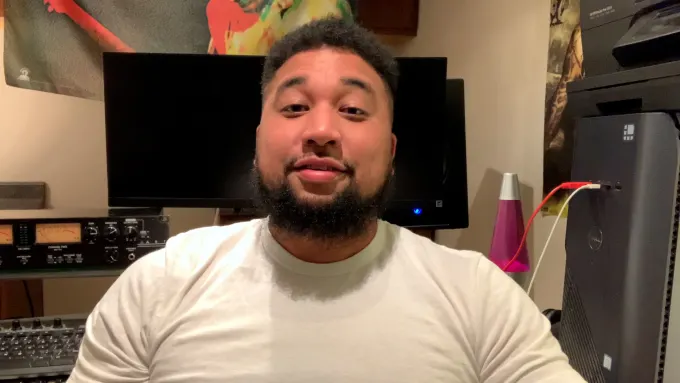
“The precision on these parts is impressive, and they arrived ahead of schedule. Frigate’s process really stands out!”
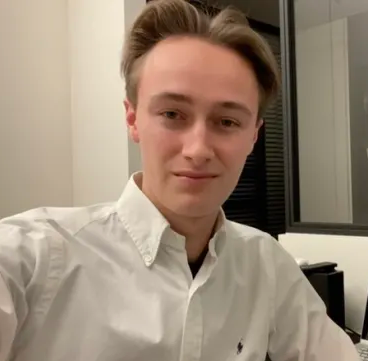
“Parts were exactly as spec’d, and the instant quote made budgeting a breeze.”
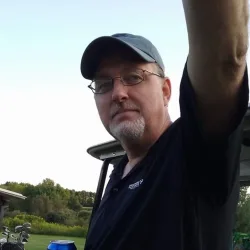
“Good value for the money.”
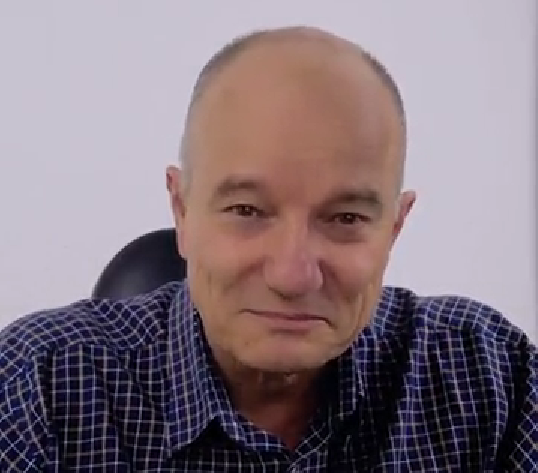
“The finish was perfect, and the team was easy to work with.”

“Working with Frigate has been great. Their proactive, results-driven approach and expertise shine through in every project. It's been a pleasure collaborating with them.”

"We are highly satisfied with the timely delivery and quality of the MIG Welding Cable from Frigate. Their attention to detail, secure packaging, and quick responsiveness stood out. We confidently recommend Frigate Engineering Services Pvt. Ltd. as a reliable manufacturing partner."
- We export to 12+ countries
Frigate’s Global Presence
Frigate takes pride in facilitating “Make in India for the globe“. As our global network of Frigaters provides virtually limitless capacity, and through our IoT enabled platform your parts go directly into production. By digitally and technologically enabling “the silent pillars of the economy” MSME and SME manufacturing industries, we are able to tap the huge potential for manufacturing to bring the best results for our clients.

100,000+
Parts Manufactured
250+
Frigaters
2000+
Machines
450+
Materials
25+
Manufacturing Process
- Solid Progress
How You Benefit with Us
Frigate brings stability, control, and predictable performance to your sourcing operations through a structured multi-vendor system.
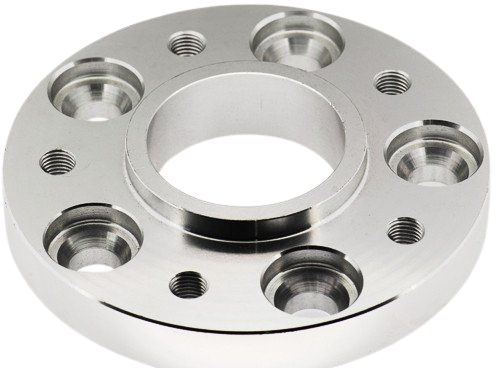
2.8X
Sourcing Cycle Speed
Frigate’s pre-qualified network shortens decision time between RFQ and PO placement.
94%
On-Time Delivery Rate
Structured planning windows and logistics-linked schedules improve project-level delivery reliability.
4X
Multi-Part Consolidation
We enable part family batching across suppliers to reduce fragmentation.
22%
Quality Rejection Rate
Multi-level quality checks and fixed inspection plans lower non-conformities.
30%
Procurement Costs
Optimized supplier negotiations and bulk order strategies reduce your overall sourcing expenses.
20%
Manual Processing Time
Automation of sourcing and supplier management significantly reduces time spent on manual tasks.
Other Industries We Serve
We deliver machining support across sectors that require consistency, material reliability, and tight dimensional control.
Get Clarity with Our Manufacturing Insights
Frigate combines aerospace precision with automotive volume needs. CNC machines are set up for quick changeovers. This reduces downtime and keeps production flexible. Process controls and statistical monitoring ensure tolerances stay within ±10 microns. Large batches maintain consistent, repeatable accuracy. This approach balances quality and volume efficiently.
Frigate machines lightweight alloys like aluminum 7075 and titanium Ti-6Al-4V. These materials offer high strength and low weight. Specialized tooling and cutting parameters prevent heat damage and tool wear. Strict quality checks confirm mechanical strength and corrosion resistance. This ensures parts perform reliably in demanding conditions.
Frigate tracks every raw material with batch and heat numbers. Material certificates are linked and documented. Inspections occur at multiple production stages, including first article inspection (FAI). Documentation complies with AS9100 and NADCAP standards. This full traceability supports audits and supply chain transparency.
Frigate uses 5-axis CNC machines for complex shapes. Simulation software optimizes tool paths for speed and accuracy. In-process measurements verify features in real time. Adjustments are made immediately if needed. This ensures parts meet ±10 micron tolerances and design specifications.
Frigate uses high-speed spindles and optimized tooling to speed machining. Predictive maintenance reduces machine downtime. CAM software minimizes non-cutting moves. Automated inspection systems check quality continuously. This approach keeps production fast without losing quality.
We'd love to Manufacture for you!
Submit the form below and our representative will be in touch shortly.
LOCATIONS
Registered Office
10-A, First Floor, V.V Complex, Prakash Nagar, Thiruverumbur, Trichy-620013, Tamil Nadu, India.
Operations Office
9/1, Poonthottam Nagar, Ramanandha Nagar, Saravanampatti, Coimbatore-641035, Tamil Nadu, India. ㅤ
Other Locations
- Bhilai
- Chennai
- USA
- Germany