Thermal-Stable CNC Machining for Medical-Grade Precision
Real-time compensation and kinematic correction ensure ±2 µm accuracy during extended cycles.
Frigate Delivers Precision Manufacturing with Full Regulatory Alignment
Full Process Traceability
Frigate links each part to real-time machine data, tool wear, and environmental parameters via the Manufacturing Execution System (MES) for audit-ready traceability.
Precision Across Dissimilar Materials
Achieve tight tolerance achieved through thermal mismatch compensation, vacuum fixturing, and synchronized toolpaths for multi-material medical components.
Regulatory-Ready Process Control
Locked manufacturing parameters validated under GAMP5, with real-time Cpk/Ppk monitoring and compliant electronic records for submission-ready traceability.
Our Clients
Trusted by Engineers and Purchasing Leaders
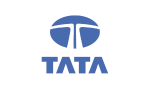
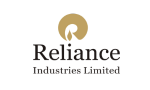


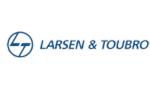
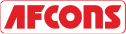


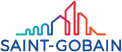

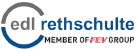

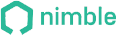
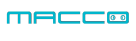









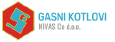
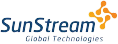

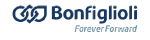


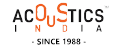
Ensure High-Volume Dimensional Repeatability
Consistency in critical dimensions over extended production cycles is essential for implantable and precision medical components.
Leverage machine learning trained on tool wear, surface finish trends, and thermal drift from validated medical production data to auto-adjust CNC toolpaths preemptively.
Integrate sensor-driven corrections to detect and adjust micro-deviations during machining, preventing tolerance breaches that could affect regulatory compliance.
Maintain dimensional variation within ±10 microns across long production runs for parts like orthopedic implants and surgical instruments through adaptive tool compensation.

Achieve Sub-50 nm Ra Surface Finishes for Biointerface Compatibility
Implant-grade surfaces require ultra-smooth textures to promote osseointegration, reduce thrombogenicity, and meet ISO and FDA surface criteria.
Utilize plasma polishing and ion-beam texturing to achieve a surface roughness(Ra) of sub-50 nm, enabling safe use in orthopedic, cardiovascular, and neurostimulator interfaces.
Use non-contact optical profilometry to measure nanoscale morphology and certify compliance with ISO 4287 for critical surface zones.
Introduce inert, biocompatible coatings post-finish to enhance tissue response and maintain stability through sterilization and implantation cycles.

Enable Sterile-Chain Compliance with Cleanroom-Based Manufacturing
Medical device components must meet strict contamination controls to ensure compatibility with sterile environments and direct patient contact.
Machine and assemble within ISO Class 7 and 8 cleanrooms, incorporating HEPA filtration, real-time particle monitoring, and ESD-safe protocols.
Employ pre-sterilized tooling, validated cleaning workflows, and clean handling processes to eliminate cross-contamination risks.
Perform ultrasonic DI water cleaning and utilizeClass VI-compatible packaging to support the integrationof sterile-barrier systems and downstream sterilization validation.

Our Machined Products
We support your production needs with CNC-machined parts, subassemblies, and performance-critical components.
- Real Impact
Words from Clients
See how global OEMs and sourcing heads describe their experience with our scalable execution.
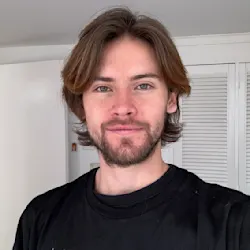
“Quick turnaround and solid quality.”
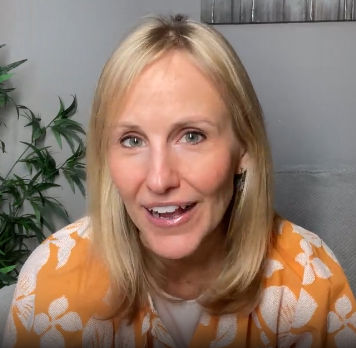
“The instant quote tool saved us time, and the parts were spot-on. Highly recommend Frigate!”
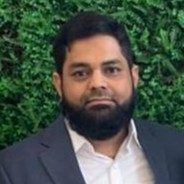
“I would strongly recommend Frigate to anyone who wants to do Rapid Prototyping, and take their ideas to manufacturing. One firm doing all kinds of Product Development!”
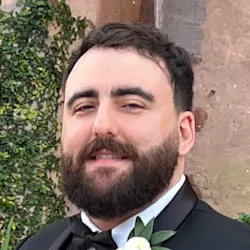
“Great service, fair price, and the parts worked perfectly in our assembly.”
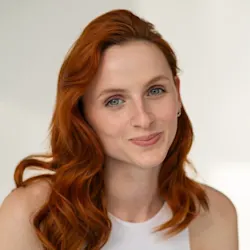
“Top-notch machining and fast shipping. Very satisfied with the results.”
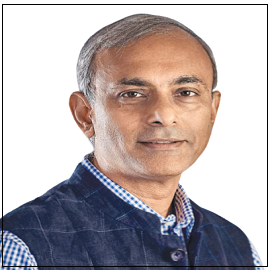
“The next disruption is happening in Prototyping & Manufacturing on-demand and Frigate is leading the way! I personally believe the Frigate's way of IIOT enabled cloud platform with Al.”
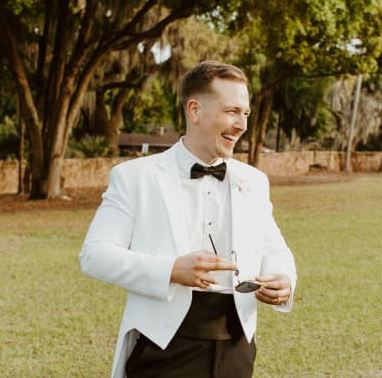
“Frigate delivered high-quality parts at a competitive price. The instant quote tool is a huge plus for us!”

“We appreciate the precision and quality of the machined components in the recent delivery—they meet our specifications perfectly and demonstrate Frigate’s capability for excellent workmanship.”
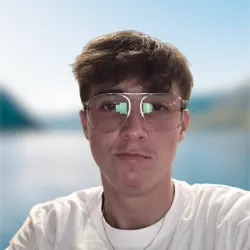
“Flawless execution from quote to delivery.”

“I am absolutely happy to work with supplier like Frigate who were quite proactive & result oriented . Frigate has high willingness team who has strong know how & their passion towards the products & process were absolutely thrilling.”
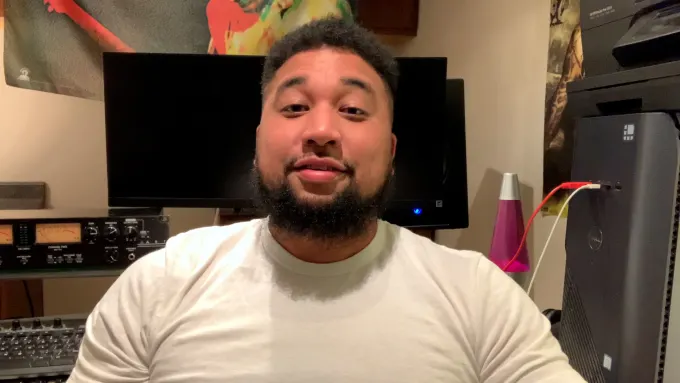
“The precision on these parts is impressive, and they arrived ahead of schedule. Frigate’s process really stands out!”
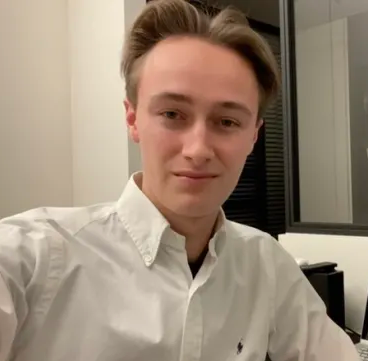
“Parts were exactly as spec’d, and the instant quote made budgeting a breeze.”
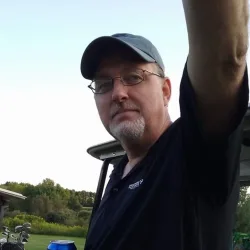
“Good value for the money.”
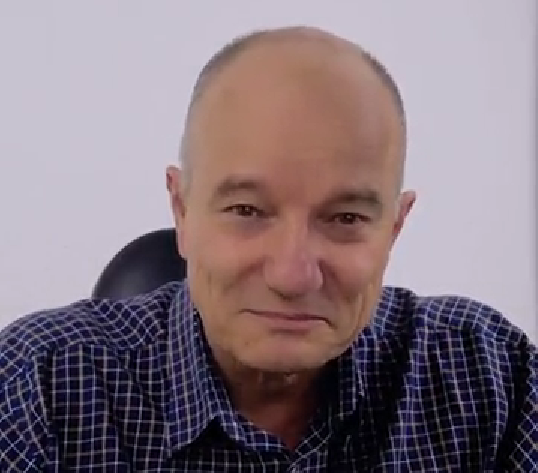
“The finish was perfect, and the team was easy to work with.”

“Working with Frigate has been great. Their proactive, results-driven approach and expertise shine through in every project. It's been a pleasure collaborating with them.”

"We are highly satisfied with the timely delivery and quality of the MIG Welding Cable from Frigate. Their attention to detail, secure packaging, and quick responsiveness stood out. We confidently recommend Frigate Engineering Services Pvt. Ltd. as a reliable manufacturing partner."
- We export to 12+ countries
Frigate’s Global Presence
Frigate takes pride in facilitating “Make in India for the globe“. As our global network of Frigaters provides virtually limitless capacity, and through our IoT enabled platform your parts go directly into production. By digitally and technologically enabling “the silent pillars of the economy” MSME and SME manufacturing industries, we are able to tap the huge potential for manufacturing to bring the best results for our clients.

100,000+
Parts Manufactured
250+
Frigaters
2000+
Machines
450+
Materials
25+
Manufacturing Process
- Solid Progress
How You Benefit with Us
Frigate brings stability, control, and predictable performance to your sourcing operations through a structured multi-vendor system.
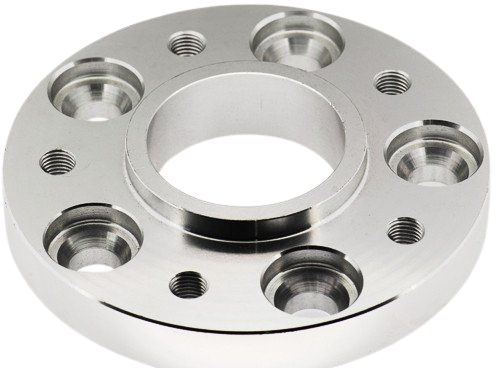
2.8X
Sourcing Cycle Speed
Frigate’s pre-qualified network shortens decision time between RFQ and PO placement.
94%
On-Time Delivery Rate
Structured planning windows and logistics-linked schedules improve project-level delivery reliability.
4X
Multi-Part Consolidation
We enable part family batching across suppliers to reduce fragmentation.
22%
Quality Rejection Rate
Multi-level quality checks and fixed inspection plans lower non-conformities.
30%
Procurement Costs
Optimized supplier negotiations and bulk order strategies reduce your overall sourcing expenses.
20%
Manual Processing Time
Automation of sourcing and supplier management significantly reduces time spent on manual tasks.
Other Industries We Serve
We deliver machining support across sectors that require consistency, material reliability, and tight dimensional control.
Get Clarity with Our Manufacturing Insights
Frigate integrates CNC systems with real-time thermal monitoring and correction algorithms that dynamically adjust toolpaths during extended machining operations. These algorithms use data from embedded sensors to detect spindle elongation, structural expansion, and ambient temperature drift. Machine-specific kinematic models continuously update positional references, allowing compensation before thermal deviation affects tolerances. This closed-loop feedback ensures that dimensional integrity is maintained within ±2 µm, even during multi-hour cycles, which is critical for precision implants and surgical instrumentation.
Yes. Frigate is engineered to machine dissimilar medical-grade materials—such as titanium, PEEK, and ceramics—by harmonizing mechanical and thermal behavior through adaptive machining strategies. Toolpath sequencing is optimized to minimize thermal gradients between adjacent materials, and vacuum-based fixturing systems stabilize parts without inducing localized stress. Compensation algorithms account for differences in thermal expansion coefficients, reducing the risk of interface warping or microcracking during and after post-processing. This approach consistently delivers multi-material assemblies with tolerances of ±10 µm or less.
Frigate utilizes a combination of advanced finishing techniques, including plasma polishing, ion-beam texturing, and inert chemical coatings, to meet stringent sub-50 nm Ra surface requirements for implantable zones. Surface topology is measured using non-contact optical profilometry and validated against ISO 4287 parameters. These methods ensure critical surfaces achieve the proper roughness, hydrophilicity, and biocompatibility needed for osseointegration, fluid transport, or cellular adhesion, depending on the implant’s application.
Frigate’s MES platform establishes a digital thread that links every manufactured component to its complete production history. Each UDI-labeled part is tagged with data such as machine ID, spindle load patterns, tool wear conditions, in-process inspection values, and ambient environmental parameters. This granular data capture enables traceability not only at the lot level but also down to individual tool offsets and batch-specific environmental influences, supporting quality investigations, validation readiness, and regulatory audits without the need for additional manual reconciliation.
Frigate operates within ISO Class 7 and 8 manufacturing environments equipped with HEPA filtration, ESD suppression, and continuous airborne particulate monitoring. Tooling and fixtures are sterilized before use, and post-machining workflows include ultrasonic cleaning using deionized water and validated detergents. Final components are packaged using Class VI-compatible materials inside laminar-flow-controlled zones. This infrastructure enables Frigate to deliver components that meet cleanroom integration requirements for Class II and Class III medical devices directly from the manufacturing floor, ensuring seamless integration.
We'd love to Manufacture for you!
Submit the form below and our representative will be in touch shortly.
LOCATIONS
Registered Office
10-A, First Floor, V.V Complex, Prakash Nagar, Thiruverumbur, Trichy-620013, Tamil Nadu, India.
Operations Office
9/1, Poonthottam Nagar, Ramanandha Nagar, Saravanampatti, Coimbatore-641035, Tamil Nadu, India. ㅤ
Other Locations
- Bhilai
- Chennai
- USA
- Germany