Laser Cutting Services
Our Clients





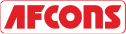

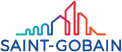


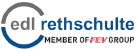

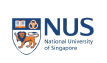
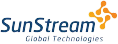

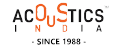




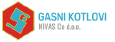
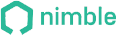
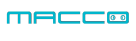












Advantages of Laser Cutting with Frigate
High Precision
Laser cutting delivers exceptional accuracy, ensuring tight tolerances for intricate designs and complex shapes.
Minimal Material Waste
Laser technology maximizes material efficiency by producing clean cuts, reducing scrap, and optimizing material utilization.
Versatility
Laser cutting works on various materials, including metals and plastics, making it suitable for diverse industrial applications.
Fast Processing Time
Laser machines operate at high speeds, reducing production time while maintaining consistent quality across large batch runs.
Custom Laser Cutting Services
Custom laser cutting services deliver precise solutions for metal and plastic materials using high-powered lasers to cut and engrave designs. This technology ensures accuracy for intricate shapes and is widely used in automotive, aerospace, and electronics industries. Key benefits include speed, flexibility, and minimal waste, promoting cost-efficient production. Quality control measures, such as edge inspection and material testing, maintain the integrity of finished products, ensuring reliable outcomes.

Get Your Quote Now
- Instant Quotation
- On-Time Delivery
- Affordable Cost
Our Laser Cutting Process






The process begins with creating a detailed digital design using CAD software. This design is the blueprint for the laser cutting operation, ensuring precise dimensions and shapes.
The appropriate material is chosen based on the project requirements. Common materials include metals, plastics, and wood, each selected for its specific properties and intended application.
The laser cutting machine is set up with the selected material. Technicians calibrate the laser's power, speed, and focus settings to match the material type and thickness, ensuring optimal cutting performance.
The machine follows the digital design to cut through the material. The laser melts, burns, or vaporizes the material, creating precise cuts and clean edges.
Once the cutting is complete, each piece undergoes a quality inspection. This step checks for dimensions and surface finish accuracy.
Finally, any necessary finishing processes, such as deburring or engraving, are applied to enhance the product's quality and aesthetics.
Laser Cutting Materials
Laser cutting accommodates various materials, ensuring precision and quality across various applications. Working with different substrates allows for tailored solutions that meet specific project requirements.
Available in hot-rolled, cold-rolled, and galvanized forms, mild steel is known for its excellent weldability and machinability. This makes it suitable for structural components and fabrication.
This metal comes in several grades, such as 304, 316, and 430. They offer varying corrosion resistance and strength levels, perfect for food processing, marine environments, and medical device applications.
Commonly found in alloys like 6061 and 7075, aluminum is lightweight and versatile. It allows for intricate designs while maintaining strength and rigidity, ideal for aerospace and automotive applications.
This alloy typically consists of copper and zinc and is available in various forms, such as cartridge brass and naval brass.
Available in oxygen-free and electrolytic tough pitch varieties, laser cutting copper allows for high precision. Due to its excellent conductivity, it is ideal for electrical applications, heat exchangers, and intricate designs.
Available in commercially pure grades (CP) and alloyed forms, titanium is renowned for its strength-to-weight ratio.
Equipped to Handle Your Toughest Laser-Cutting Jobs
Advanced laser cutting technology enables us to handle even the most challenging projects. Our state-of-the-art laser machines provide high precision, ensuring intricate designs meet exact specifications for every job. The ability to cut a wide range of metals, including stainless steel, aluminum, and titanium, enhances our versatility for diverse applications.
Our experienced team is trained to manage complex geometries, optimizing cutting paths to minimize waste and reduce production time. With fast turnaround times and the capability to handle small and large production runs, we effortlessly accommodate varying project scales.

Compliance for Laser Cutting Services
Frigate fully complies with industry standards for its Sand Casting services. It follows strict material specifications, process controls, and environmental guidelines. The company prioritizes quality and safety at every step, ensuring that each casting is precise and reliable. Our certifications demonstrate its commitment to customer satisfaction and operational excellence.
Compliance for Laser Cutting Services
Certification number: 1234567. Ensures quality management, process control, and continuous improvement in all operations.
Ensures a safe work environment by setting equipment, procedures, and worker safety standards during operations.
Certifies compliance with EU safety requirements for electrical equipment and machinery, ensuring safe operation within European markets.
Ensures air quality and emissions standards compliance to reduce environmental impact during industrial operations.
Certification number: 7654321. Ensures aerospace industry compliance with stringent quality and safety management standards for components and processes.
Certification number: 8901234. Meets automotive industry quality standards, focusing on defect prevention and continuous improvement in manufacturing.
This is Compliant with directive 2011/65/EU, which restricts the use of hazardous materials in manufacturing electronic and electrical equipment.
REACH (Registration, Evaluation, Authorisation, and Restriction of Chemicals) ensures the safe use and regulation of chemicals in manufacturing, preventing hazardous substances from entering products and processes.

Tolerance for Laser Cutting Services
Precision of the laser beam focus, affecting cutting accuracy and kerf width.
Variations in thickness of the material affecting cutting precision.
Deviation from a perfect perpendicular cut along the Z-axis (material thickness).
Precision in following complex contours during the cutting process.
Stability in laser power, critical for consistent cut quality and heat input.
Tolerance of stitch marks when cutting parts that require multiple passes or sections.
Deviation from the intended edge, relevant for tight tolerances and critical geometries.
Variability in cutting speed, impacting overall cut precision and heat generation.
Deviation in material preheating near the cut edge, affecting edge finish and heat-affected zone (HAZ).
Accuracy of the path the laser follows, critical for tight tolerance applications.
Width of the heat-affected zone, affecting material properties around the cut.
Deviation from a perfect round shape in laser-cut holes, depending on material and settings.
Accuracy of parting lines when cutting sheets, especially with nested parts.

Quality Testing Standards for Laser Cutting Services
Assesses the laser beam's spatial quality, ensuring uniform energy distribution for precision cutting.
Measures the size and uniformity of the laser focus spot, affecting cut precision and edge quality.
Measures the frequency of laser pulses to ensure consistent energy application during cutting.
Assesses the hardness and structure changes within the heat-affected zone to ensure minimal distortion.
Measures the efficiency of laser power delivery and ensures optimal cutting performance.
Tests the consistency of assist gas pressure during cutting, ensuring stable and clean cuts.
Monitors cutting speed consistency across different areas of the material to ensure uniform cuts.
Measures the material's ability to conduct heat, ensuring minimal heat buildup during cutting.
Verifies the alignment of optical components to ensure proper laser path for cutting accuracy.
Tests the purity of assist gases (oxygen, nitrogen, etc.) to ensure optimal cutting conditions and surface finish.
Measures the laser beam's divergence to ensure it remains focused over long cutting distances.
Verifies the stability of the laser's wavelength to ensure consistent cutting performance.
Measures material thickness to verify accuracy before cutting and ensure proper cutting settings.
Measures the force exerted on the material during cutting to ensure minimal deformation.
Precision Laser Cutting for the Aerospace Industry
Frigate Sheet Metal Fabrication Services offers advanced laser cutting solutions tailored for the aerospace industry, ensuring precision and reliability in every project. Our state-of-the-art laser technology efficiently processes a variety of metals, including aluminum, titanium, and stainless steel, which are essential for aircraft components.
With exceptional accuracy and clean edges, our laser cutting services meet stringent industry standards while minimizing waste. Whether you require intricate parts for aircraft structures or lightweight components for fuel efficiency, we are here for you.





Industries We Serve
- Solid Progress
Our Manufacturing metrics
Frigate brings stability, control, and predictable performance to your sourcing operations through a structured multi-vendor system.
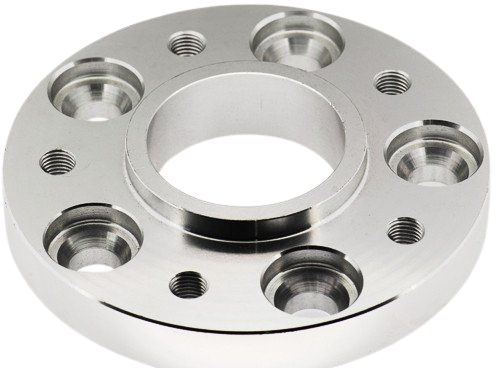
2.8X
Sourcing Cycle Speed
Frigate’s pre-qualified network shortens decision time between RFQ and PO placement.
94%
On-Time Delivery Rate
Structured planning windows and logistics-linked schedules improve project-level delivery reliability.
4X
Multi-Part Consolidation
We enable part family batching across suppliers to reduce fragmentation.
22%
Quality Rejection Rate
Multi-level quality checks and fixed inspection plans lower non-conformities.
30%
Procurement Costs
Optimized supplier negotiations and bulk order strategies reduce your overall sourcing expenses.
20%
Manual Processing Time
Automation of sourcing and supplier management significantly reduces time spent on manual tasks.
Streamlines Solutions for Unmatched Quality
With Frigate‘s precision laser cutting services, there’s no direct mechanical force on parts, eliminating the risk of damage from residual material. Fixturing and setup for precision laser cutting are accomplished quickly, even with tight tolerances. Depending on the material and specifications, parts can often be laser cut and finished in a single step, reducing the need for time-consuming and costly secondary post-processing. Experience efficiency and precision with our advanced laser cutting technology, designed to meet your specific manufacturing needs seamlessly.

Get Clarity with our Manufacturing Insights
- Real Impact
Words from Clients
See how global OEMs and sourcing heads describe their experience with our scalable execution.
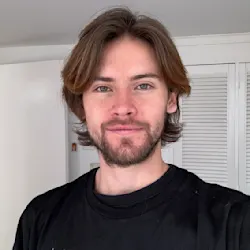
“Quick turnaround and solid quality.”
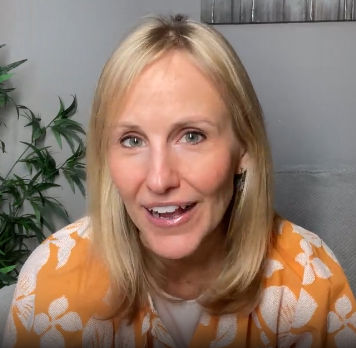
“The instant quote tool saved us time, and the parts were spot-on. Highly recommend Frigate!”
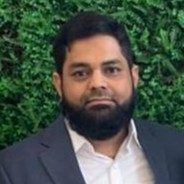
“I would strongly recommend Frigate to anyone who wants to do Rapid Prototyping, and take their ideas to manufacturing. One firm doing all kinds of Product Development!”
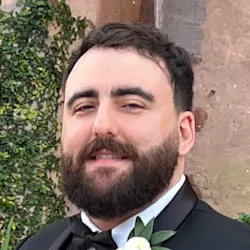
“Great service, fair price, and the parts worked perfectly in our assembly.”
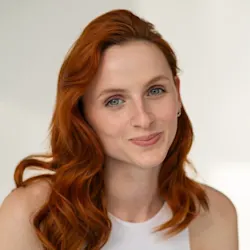
“Top-notch machining and fast shipping. Very satisfied with the results.”
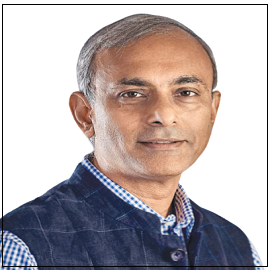
“The next disruption is happening in Prototyping & Manufacturing on-demand and Frigate is leading the way! I personally believe the Frigate's way of IIOT enabled cloud platform with Al.”
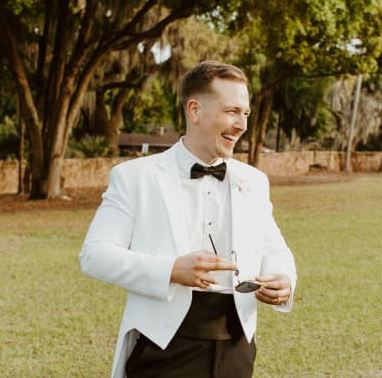
“Frigate delivered high-quality parts at a competitive price. The instant quote tool is a huge plus for us!”

“We appreciate the precision and quality of the machined components in the recent delivery—they meet our specifications perfectly and demonstrate Frigate’s capability for excellent workmanship.”
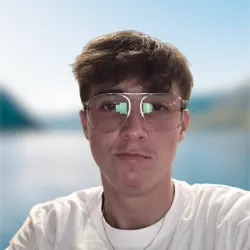
“Flawless execution from quote to delivery.”

“I am absolutely happy to work with supplier like Frigate who were quite proactive & result oriented . Frigate has high willingness team who has strong know how & their passion towards the products & process were absolutely thrilling.”
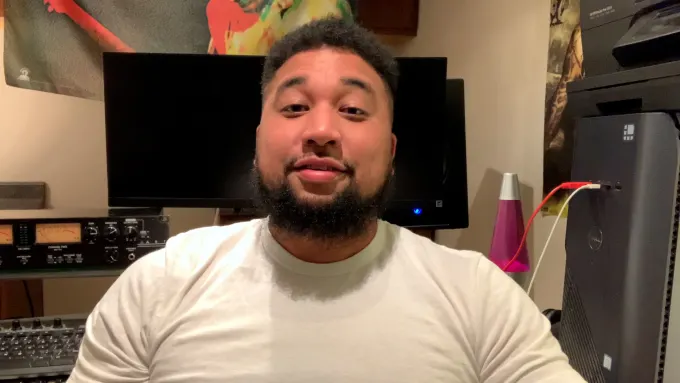
“The precision on these parts is impressive, and they arrived ahead of schedule. Frigate’s process really stands out!”
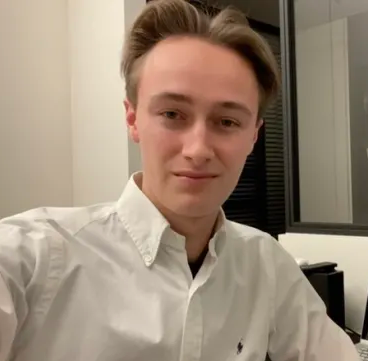
“Parts were exactly as spec’d, and the instant quote made budgeting a breeze.”
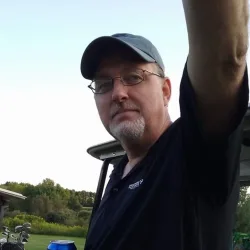
“Good value for the money.”
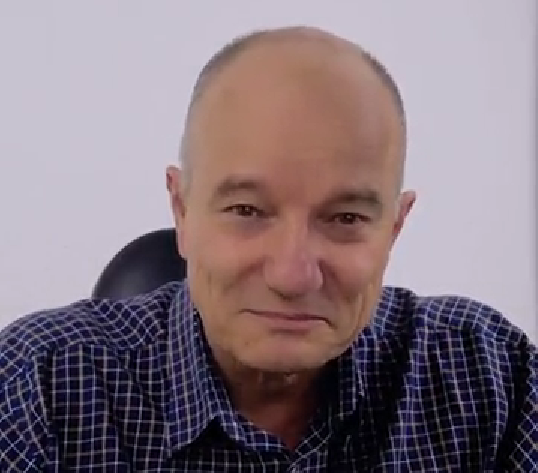
“The finish was perfect, and the team was easy to work with.”

“Working with Frigate has been great. Their proactive, results-driven approach and expertise shine through in every project. It's been a pleasure collaborating with them.”

"We are highly satisfied with the timely delivery and quality of the MIG Welding Cable from Frigate. Their attention to detail, secure packaging, and quick responsiveness stood out. We confidently recommend Frigate Engineering Services Pvt. Ltd. as a reliable manufacturing partner."
Having Doubts? Our FAQ
Check all our Frequently Asked Question
The industry primarily uses CO2 and fiber laser cutting methods. CO2 lasers are ideal for cutting non-metal materials like wood and acrylic, while fiber lasers excel at cutting metals due to their shorter wavelength and higher power density.
The thickness of the material directly impacts cutting speed and quality. Thicker materials may require more powerful lasers and slower speeds to ensure clean cuts and avoid excessive heat, which can lead to warping or burning.
Laser cutting speed affects edge quality and kerf width. Faster speeds can lead to rougher edges and heat-affected zones, while slower speeds provide cleaner cuts and finer details, ensuring that the final product meets specifications.
Laser settings, including power, speed, and frequency, are adjusted based on the material type and thickness. Each material has optimal settings to achieve the best cut quality, minimize waste, and avoid damaging the part.
The focal point is where the laser beam converges and produces the highest intensity. Properly setting the focal point is crucial for achieving optimal cut quality and efficiency, as it affects the depth of the cut and the width of the kerf.
We'd love to Manufacture for you!
Submit the form below and our representative will be in touch shortly.
LOCATIONS
Global Sales Office
818, Preakness lane, Coppell, Texas, USA – 75019
Registered Office
10-A, First Floor, V.V Complex, Prakash Nagar, Thiruverumbur, Trichy-620013, Tamil Nadu, India.
Operations Office
9/1, Poonthottam Nagar, Ramanandha Nagar, Saravanampatti, Coimbatore-641035, Tamil Nadu, India. ㅤ
Other Locations
- Bhilai
- Chennai
- Texas, USA