CNC Drilling Services
Frigate provides top-notch CNC drilling services, capable of producing components with intricate and complex geometries and exceptional surface finishes. Our advanced machinery and skilled team ensure high-quality results for even the most detailed designs.
Our Clients





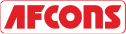

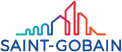


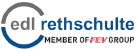

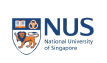
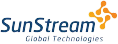

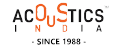




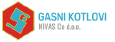
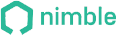
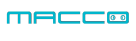












Advantages of CNC Drilling Services
Precision and Accuracy
CNC drilling machines deliver high precision, ensuring exact hole placement and consistent diameters, which are crucial for complex components and tight tolerances.
Complex Hole Patterns
CNC drilling can easily handle intricate patterns and multiple hole sizes, accommodating detailed design requirements and enhancing component functionality.
Consistency and Reproducibility
CNC technology guarantees uniform results across multiple parts, maintaining the same high quality throughout large production runs.
Automated Efficiency
CNC drilling's automated nature speeds up the manufacturing process, reducing manual intervention and increasing overall production efficiency.
Advanced CNC Drilling for Complex and High-Volume Fabrication
At Frigate, we deliver top-notch CNC drilling services for parts of any complexity, whether in small or large quantities. Our advanced equipment and expertise ensure outstanding results for all your drilling needs. We use a variety of CNC drilling machines, including upright, bench, and radial models, to handle simple and intricate hole patterns. Whether you need precise drilling in metals like aluminum, steel, copper, or various polymers, our services cover a wide range of materials, providing reliable and efficient solutions for your projects.

Get Your Quote Now
- Instant Quotation
- On-Time Delivery
- Affordable Cost
Our CNC Drilling Process






The CNC drilling process starts with creating a detailed computer-aided design (CAD) of the part, which outlines the exact locations and dimensions of the holes. This design is then converted into a G-code program, a set of instructions that guides the CNC machine in moving and drilling.
Next, the material to be drilled is securely mounted on the CNC machine's worktable. Proper workpiece securing is crucial to prevent any movement during the drilling process, ensuring accuracy and consistency.
With the material in place, the appropriate drill bit or tool is selected based on the material type and the specific requirements of the holes. The CNC machine is calibrated, with adjustments to drill speed, feed rate, and hole depth to ensure precise drilling.
Following the G-code instructions, the CNC machine automatically positions the drill bit and performs the drilling operations. This automation ensures that each hole is drilled with high precision. The operation is monitored throughout the process to address any issues and ensure the drilling is performed correctly.
After drilling, the part undergoes a quality check to ensure all holes meet the design specifications. Any sharp edges or burrs are removed in the finishing stage, providing a smooth and accurate final product.
Finally, any additional machining or finishing operations needed to meet the final specifications are carried out. This step ensures the part achieves its intended design and functionality.
CNC Drilling Materials
CNC drilling can be performed on various materials, requiring different techniques and tools for optimal results.
Lightweight and machinable, ideal for various applications, including aerospace and automotive components.
Available in many grades, such as carbon steel and stainless steel, steel is used for its strength and durability in industrial applications.
Copper is known for its excellent thermal and electrical conductivity, and it is used in electronics and electrical components.
It is highly corrosion-resistant and strong, often used in aerospace and medical implants.
Offers good machinability and is often used for decorative and precision components.
This category includes materials like acrylic, polycarbonate, and nylon, which are used in applications where lightweight and versatility are important.
Materials such as carbon fiber and fiberglass are used for their strength-to-weight ratio and durability in specialized applications.
Hard and brittle, used in applications requiring high wear resistance and high-temperature stability.
Precision CNC Drilling for All Your Fabrication Needs
We offer CNC drilling services for fabricating parts in small and large quantities, regardless of complexity. Our advanced drill presses, including upright, bench, and radial types, enable us to drill holes with simple or intricate patterns up to 7 cm in diameter. We work with Various materials, including metals and alloys like aluminum, steel, and copper, as well as various polymers, to ensure high-quality results for diverse manufacturing needs.

Compliance for CNC Drilling Services
At Frigate, compliance for CNC drilling services is critical for maintaining industry-leading precision and quality. Rigorous standards govern our operations to ensure safety, environmental sustainability, and exacting accuracy. We adhere to the highest industry benchmarks to meet customer specifications and deliver reliable, high-performance parts.
Ensures consistent product quality and process improvement across all manufacturing stages.
Guarantees compliance with aerospace quality management standards, ensuring precision and reliability.
Ensures all products are free from restricted hazardous substances.
Adheres to ANSI standards for manufacturing safety and equipment performance.
Certifies that products meet European Union regulations on safe chemical use.
This position ensures adherence to workplace safety standards as defined by the Occupational Safety and Health Administration.
Demonstrates environmental management practices, focusing on reducing waste and energy consumption.

Tolerance for CNC Drilling Services
Ensures tight fit for parts requiring interference, such as press fits.
Tolerances for clearance fits, ensuring proper space between mating components.
Ensures precise placement of holes relative to reference points on the part.
Controls the angular alignment of drilled holes relative to the part’s surface.
Ensures holes are drilled perpendicular to the part surface for correct alignment.
Ensures that drilled holes maintain a straight axis over their entire length.
Ensures that holes maintain uniform diameter along their depth.
Precision in hole surface roughness for better functionality and part fit.
Ensures counterbore diameter aligns perfectly with fasteners or other components.
Ensures precise countersink angles for optimal fastener seating and alignment.
Controls depth for accurate threading, ensuring full thread engagement.
Ensures accurate chamfer dimensions for smooth transitions between edges.
Ensures the hole maintains both straightness and correct angular orientation throughout its length.
Ensures that the hole maintains a constant diameter along its entire length.

Quality Testing Standards for CNC Drilling Services
Monitors tool wear to ensure consistent hole quality and to prevent dimensional drift.
Measures the deviation of the tool’s rotation axis from its true position, ensuring precise drilling alignment.
Verifies effective chip removal during drilling to prevent tool blockage and ensure optimal surface quality.
Measures the forces acting on the tool during drilling to optimize the cutting parameters and tool life.
Measures the offset of the cutting tool to ensure proper alignment and hole accuracy.
Verifies that spindle speed is consistent and within required parameters to maintain precise drilling.
Ensures that the feed rate remains stable and consistent during the drilling process to maintain hole quality.
Measures the deviation of hole location and orientation from the intended path during deep-hole drilling.
Tests the effect of heat buildup during drilling on part tolerance, ensuring parts stay within dimensional limits.
Ensures that vibration is minimized during drilling to prevent inaccuracies in hole location and finish.
Verifies that the drilled path follows the intended geometry precisely, especially in complex multi-axis drilling.
Measures the hardness of the drilled surface to ensure the material is correctly processed without hardening issues.
Ensures that any taper in the drilled hole is within specified limits for correct fitting or sealing.
Tests the surface quality and roughness of the hole walls to ensure they meet functional and aesthetic standards.
Detects distortion or warping in the material caused by thermal or mechanical stresses during the drilling process.
CNC Drilling for the Aerospace Industry
Precision and reliability are critical aspects in the aerospace industry, making CNC drilling an essential process for manufacturing high-quality components. CNC drilling ensures the accurate creation of holes in complex and often high-strength materials used in aerospace applications, such as titanium, aluminum alloys, and advanced composites. This process addresses several challenges inherent in aerospace manufacturing, including the need for exacting tolerances and the ability to handle intricate designs.
CNC drilling begins with detailed CAD designs that specify the exact location and dimensions of each hole. This is followed by converting these designs into G-code, which guides the CNC machine to perform precise drilling operations. By using advanced drill presses and automated systems, CNC drilling achieves the high level of accuracy required for aerospace parts, whether for structural components, engine parts, or intricate assemblies.





Industries We Serve
- Solid Progress
Our Manufacturing metrics
Frigate brings stability, control, and predictable performance to your sourcing operations through a structured multi-vendor system.
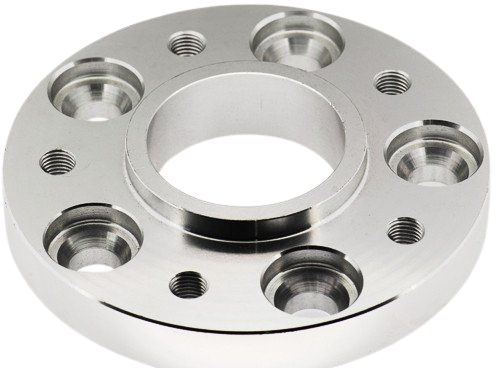
2.8X
Sourcing Cycle Speed
Frigate’s pre-qualified network shortens decision time between RFQ and PO placement.
94%
On-Time Delivery Rate
Structured planning windows and logistics-linked schedules improve project-level delivery reliability.
4X
Multi-Part Consolidation
We enable part family batching across suppliers to reduce fragmentation.
22%
Quality Rejection Rate
Multi-level quality checks and fixed inspection plans lower non-conformities.
30%
Procurement Costs
Optimized supplier negotiations and bulk order strategies reduce your overall sourcing expenses.
20%
Manual Processing Time
Automation of sourcing and supplier management significantly reduces time spent on manual tasks.
Custom CNC Drilling Solutions at Frigate
Our Custom CNC drilling services offer precise and efficient solutions for creating holes in a variety of materials, including metals, alloys, and polymers. We utilize advanced CNC technology and high-performance drill presses to handle small and large production runs with complex patterns and diameters up to 7 cm. Starting with detailed CAD designs, we convert them into accurate G-code instructions for optimal drilling. This automated process ensures high precision, reduces turnaround times, and addresses quality concerns through thorough inspections and finishing. Our services solve the problems of manual drilling inefficiencies and inaccuracies, delivering custom-drilled parts that meet exact specifications and industry standards.

Get Clarity with our Manufacturing Insights
- Real Impact
Words from Clients
See how global OEMs and sourcing heads describe their experience with our scalable execution.
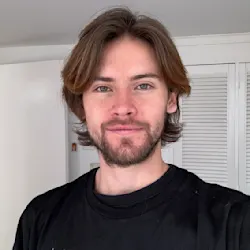
“Quick turnaround and solid quality.”
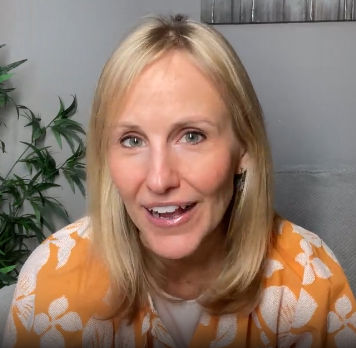
“The instant quote tool saved us time, and the parts were spot-on. Highly recommend Frigate!”
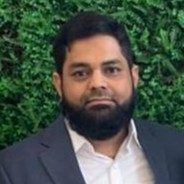
“I would strongly recommend Frigate to anyone who wants to do Rapid Prototyping, and take their ideas to manufacturing. One firm doing all kinds of Product Development!”
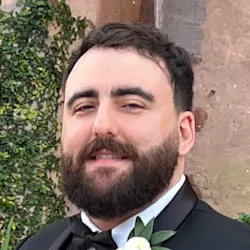
“Great service, fair price, and the parts worked perfectly in our assembly.”
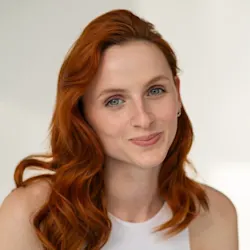
“Top-notch machining and fast shipping. Very satisfied with the results.”
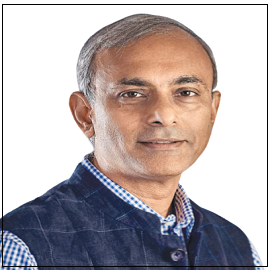
“The next disruption is happening in Prototyping & Manufacturing on-demand and Frigate is leading the way! I personally believe the Frigate's way of IIOT enabled cloud platform with Al.”
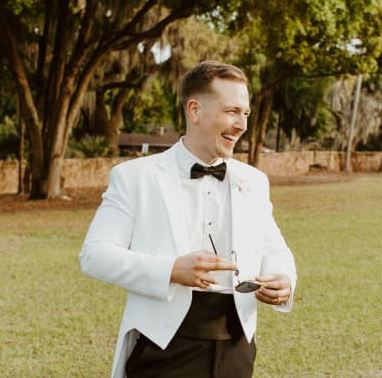
“Frigate delivered high-quality parts at a competitive price. The instant quote tool is a huge plus for us!”

“We appreciate the precision and quality of the machined components in the recent delivery—they meet our specifications perfectly and demonstrate Frigate’s capability for excellent workmanship.”
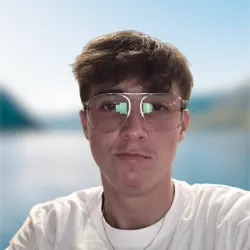
“Flawless execution from quote to delivery.”

“I am absolutely happy to work with supplier like Frigate who were quite proactive & result oriented . Frigate has high willingness team who has strong know how & their passion towards the products & process were absolutely thrilling.”
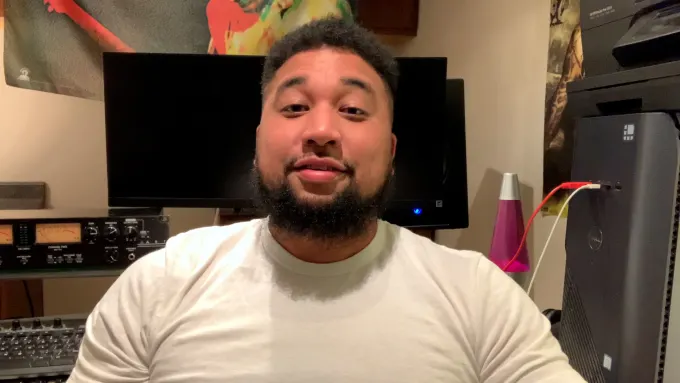
“The precision on these parts is impressive, and they arrived ahead of schedule. Frigate’s process really stands out!”
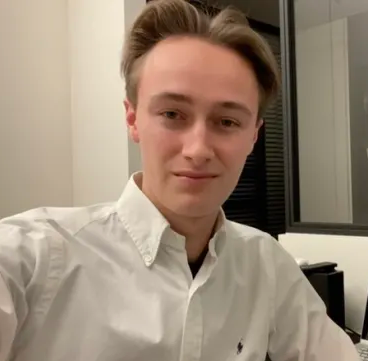
“Parts were exactly as spec’d, and the instant quote made budgeting a breeze.”
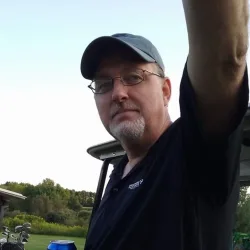
“Good value for the money.”
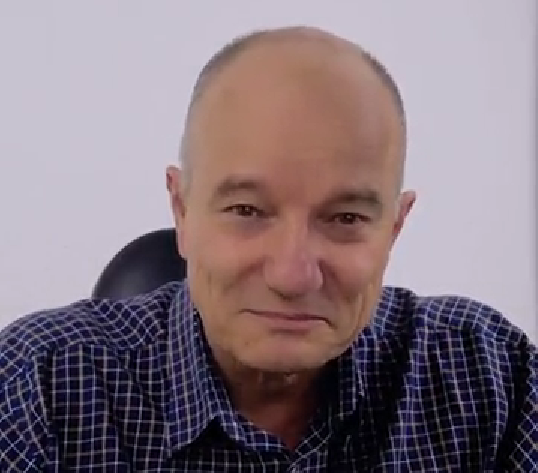
“The finish was perfect, and the team was easy to work with.”

“Working with Frigate has been great. Their proactive, results-driven approach and expertise shine through in every project. It's been a pleasure collaborating with them.”

"We are highly satisfied with the timely delivery and quality of the MIG Welding Cable from Frigate. Their attention to detail, secure packaging, and quick responsiveness stood out. We confidently recommend Frigate Engineering Services Pvt. Ltd. as a reliable manufacturing partner."
Having Doubts? Our FAQ
Check all our Frequently Asked Question
CNC drilling machines can handle various materials, such as metal, plastic, wood, and composites. Each material requires specific drill bits and settings to achieve the best results. For example, drilling aluminum requires a different approach than drilling hard steel.
CNC drilling uses computer programs to control the drill's movements. This automation ensures that each hole is drilled at the exact depth and position specified in the design. It minimizes human error and increases consistency in production.
Choosing the right drill bit is crucial. Different bits are designed for specific materials and hole sizes. For example, twist drill bits are good for general use, while carbide bits are better for hard materials. The wrong bit can lead to poor-quality holes and damage to the material.
Coolant systems help keep the drill bit and material cool during the process. This prevents overheating, which can damage both the tool and the workpiece. Additionally, coolant reduces friction, leading to smoother drilling and longer tool life.
Monitoring tool wear is essential for maintaining quality. As drill bits wear down, they can create larger holes or rough edges. CNC machines can be equipped with sensors to track wear and alert operators when it's time to replace the bit, ensuring high-quality results throughout production.
We'd love to Manufacture for you!
Submit the form below and our representative will be in touch shortly.
LOCATIONS
Global Sales Office
818, Preakness lane, Coppell, Texas, USA – 75019
Registered Office
10-A, First Floor, V.V Complex, Prakash Nagar, Thiruverumbur, Trichy-620013, Tamil Nadu, India.
Operations Office
9/1, Poonthottam Nagar, Ramanandha Nagar, Saravanampatti, Coimbatore-641035, Tamil Nadu, India. ㅤ
Other Locations
- Bhilai
- Chennai
- Texas, USA