Welding Services
Frigate provides exceptional welding solutions tailored for any manufacturing business. With our extensive knowledge and experience, we are equipped to ensure your business thrives through our high-quality welding services.
Our Clients





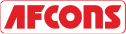

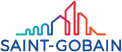


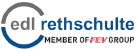

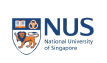
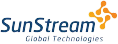

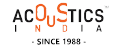




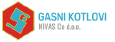
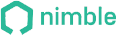
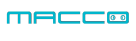












Advantages of Welding with Frigate
Thermal Properties Control
Welding allows precise control over heat input, minimizing thermal distortion and preserving the material's mechanical properties during fabrication.
Seamless Integration
Welding enables the creation of seamless structures, eliminating potential weaknesses from fasteners or joints, thus enhancing overall integrity and reliability.
Complex Geometries
Advanced welding techniques can effectively join complex geometries and shapes, allowing for innovative designs and enhanced functionality in engineering applications.
Fatigue Resistance
When executed correctly, welded joints can exhibit superior fatigue resistance, making them ideal for components subjected to cyclic loading in demanding environments.
Tailored Custom Welding Services for Your Needs
Frigate offers specialized custom welding services to meet your project requirements. Our skilled welders use advanced techniques like MIG, TIG, and stick welding, which ensure strong, durable joints across various materials, including aluminum, steel, and stainless steel. We focus on precision and quality, tailoring each weld to your specifications, resulting in seamless integrations and optimal performance.

Get Your Quote Now
- Instant Quotation
- On-Time Delivery
- Affordable Cost
Our Welding Process






We thoroughly assess the requirements, including material types, joint configurations, and load specifications. This evaluation helps us determine the most suitable welding techniques and methods.
Proper material preparation is essential for optimal weld quality. This step includes cleaning surfaces to remove contaminants, aligning components accurately, and, if necessary, preheating materials to improve weldability.
Based on the project assessment, we select the appropriate welding technique, such as MIG, TIG, or Stick welding. Each method has advantages depending on the materials and the application.
Our skilled technicians execute the welding process with precision, controlling parameters like heat input, travel speed, and filler material. This ensures strong, consistent welds that meet the desired specifications.
After welding, we conduct rigorous inspections, including visual checks, non-destructive testing, and dimensional measurements, to verify weld integrity and adherence to industry standards.
Finally, we perform any necessary post-weld treatments, such as grinding, polishing, or painting, to enhance the final product's appearance and protect against corrosion.
Welding Materials
Welding is a critical joining process that involves fusing materials to create strong, durable connections. Various materials can be effectively welded using specialized techniques tailored to their unique properties.
Steel is one of the most widely used materials for welding. It is easily formed, robust, and long-lasting.
This type of steel resists rust and corrosion. It is often used in food, medical, and chemical industries.
Aluminum is lightweight and resists corrosion well. It is commonly used in automotive, aerospace, and construction applications.
Cast iron is tough and durable. It is used in machinery, piping, and heavy equipment but requires special welding techniques.
Copper is a good heat and electricity conductor. It is often used in electrical components and plumbing.
Bronze is strong and resistant to corrosion. It is used in marine applications, bearings, and artistic sculptures.
These alloys are known for their strength and resistance to extreme temperatures. They are often used in aerospace and chemical processing.
Titanium is lightweight and very strong. It finds utility in high-performance applications, medical implants, and aircraft.
Advanced Welding Services for Various Key Challenges
Our welding services address key manufacturing challenges. We prioritize structural integrity with precise welding techniques that create strong, seamless joints, enhancing durability and reducing failure risks. Our automated processes expedite production, helping you meet tight deadlines without compromising quality. Additionally, we excel in welding various metals, accommodating complex designs, and resolving compatibility issues. By minimizing material waste, we help lower costs while maintaining the highest quality standards, ultimately boosting your bottom line.

Compliance for Welding Services
Frigate fully complies with industry standards for its Sand Casting services. It follows strict material specifications, process controls, and environmental guidelines. The company prioritizes quality and safety at every step, ensuring that each casting is precise and reliable. Our certifications demonstrate its commitment to customer satisfaction and operational excellence.
Key Compliance Standards for Welding
Structural Welding Code for steel, ensuring welds are robust and capable of withstanding high-stress environments.
Sets requirements for welder qualifications, ensuring competence for specific materials, thicknesses, and welding procedures.
Defines quality requirements for fusion welding, ensuring consistent process control and reliable welded joints.
Pipeline Welding Code for oil and gas, ensuring high-quality welds that meet safety and structural integrity standards.
Establishes quality management systems, ensuring standardized procedures and consistent weld quality in production processes.
Military standard for welding, ensuring compliance with stringent military specifications for weld integrity and performance.

Tolerance for Welding Services
Tolerance for the depth of weld penetration into the base material, ensuring complete fusion.
Tolerance for the width of the weld bead in butt welding to ensure strength and uniformity.
Variation in heat input applied during welding, controlling metallurgical properties and distortion.
Tolerance for the thickness of the reinforcement bead in a fillet weld, ensuring joint strength.
Tolerance for temperature between welding passes, ensuring optimal material properties.
Allowable variation in tensile strength of the weld to meet material specification requirements.
Control of hardness variation across the weld zone, ensuring no material weakness or brittleness.
No visible porosity allowed in the weld, ensuring full strength and integrity of the joint.
Deviation allowed in the root gap of butt welds, critical for ensuring full penetration and fusion.
Tolerance in the angle of the weld toe, critical for load distribution and strength.
Tolerance in angular distortion due to thermal effects, ensuring parts stay within alignment.
Tolerance for preheating the material to avoid cracking, especially in high-carbon steels.
Control of the temperature range during PWHT to relieve stress and optimize mechanical properties.
Tolerance in the angle of groove welds, important for maintaining correct joint fit and strength.
Control of weld toe radius, crucial to minimize stress concentration and fatigue failures.
Tolerance for overall deflection caused by welding, critical for maintaining the dimensional accuracy of large components.
Maximum allowable CSI to ensure that the weld does not exhibit excessive susceptibility to cracking under stress.
Control of residual stresses in the weld area to ensure dimensional stability and minimize distortion.
Control of visible imperfections such as undercuts, overlap, or excessive spatter in welds.

Quality Testing Standards for Welding Services
Tests the extent of fusion between the base material and weld, ensuring complete bonding and integrity.
Evaluates the ability of the weld to resist cracking under stress at different temperatures.
Measures the residual stress field in the welded zone to ensure minimal distortion and warping.
Measures changes in dimensions due to the contraction of the weld metal during cooling.
Measures variations in hardness within the heat-affected zone (HAZ) to ensure strength and toughness.
Detects the presence of hydrogen in the weld, which could lead to delayed cracking.
Assesses the internal porosity of the weld, which can impact structural integrity and fatigue resistance.
Ensures the fusion line between base metal and weld is continuous, without any gaps or weaknesses.
Measures the width and properties of the HAZ to ensure it falls within acceptable limits for strength.
Measures changes in geometry due to thermal expansion and contraction during welding.
Determines the tensile strength specifically in the heat-affected zone, ensuring no weakness in the HAZ.
Measures the depth and size of defects within the weld to assess structural safety.
Assesses the performance of the weld under cyclic loading, ensuring it can withstand long-term fatigue.
Measures the ability of a welded joint to resist crack propagation, especially at low temperatures.
Tests the susceptibility of the weld area to intergranular corrosion, particularly in stainless steel.
Transforming Aerospace Manufacturing Through Welding
The aerospace industry faces significant challenges, including strict safety, performance, and weight reduction requirements. Welding addresses these pain points by creating strong, lightweight structures for aircraft efficiency. Advanced techniques ensure precise joint integrity, reducing the risk of structural failures during flight. Combining various metals, like aluminum and titanium, enhances design flexibility for specific aerospace applications. Automated welding processes boost production speed and consistency, helping manufacturers meet tight deadlines without sacrificing quality. Effective welding services empower aerospace manufacturers to achieve superior product performance and reliability.





Industries We Serve
- Solid Progress
Our Manufacturing metrics
Frigate brings stability, control, and predictable performance to your sourcing operations through a structured multi-vendor system.
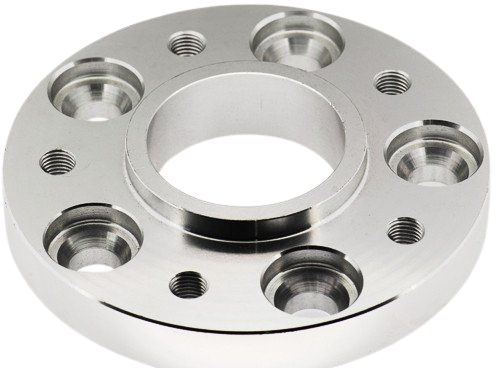
2.8X
Sourcing Cycle Speed
Frigate’s pre-qualified network shortens decision time between RFQ and PO placement.
94%
On-Time Delivery Rate
Structured planning windows and logistics-linked schedules improve project-level delivery reliability.
4X
Multi-Part Consolidation
We enable part family batching across suppliers to reduce fragmentation.
22%
Quality Rejection Rate
Multi-level quality checks and fixed inspection plans lower non-conformities.
30%
Procurement Costs
Optimized supplier negotiations and bulk order strategies reduce your overall sourcing expenses.
20%
Manual Processing Time
Automation of sourcing and supplier management significantly reduces time spent on manual tasks.
Achieving Consistent Weld Quality in High-Volume Production
In high-volume production, maintaining consistent weld quality is a significant challenge. Variations in welding techniques, heat input, and filler materials can lead to defects that compromise structural integrity. Advanced monitoring systems are essential for tracking parameters and enabling real-time adjustments to uphold quality standards. Strict inspection protocols, including visual assessments and non-destructive testing, help identify issues early and ensure regulatory compliance. Additionally, automated welding technologies enhance consistency by reducing human error and providing uniform results across components. Focusing on these quality control measures allows manufacturers to achieve reliable welds that meet stringent performance requirements.

Get Clarity with our Manufacturing Insights
- Real Impact
Words from Clients
See how global OEMs and sourcing heads describe their experience with our scalable execution.
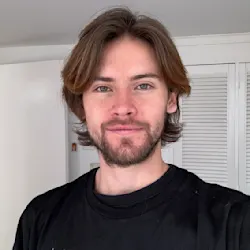
“Quick turnaround and solid quality.”
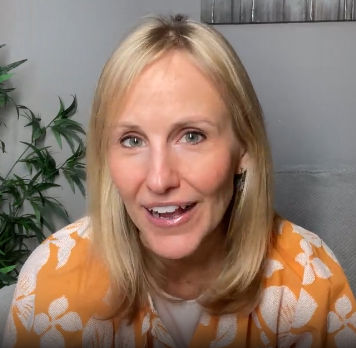
“The instant quote tool saved us time, and the parts were spot-on. Highly recommend Frigate!”
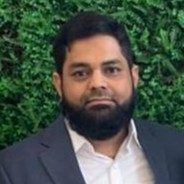
“I would strongly recommend Frigate to anyone who wants to do Rapid Prototyping, and take their ideas to manufacturing. One firm doing all kinds of Product Development!”
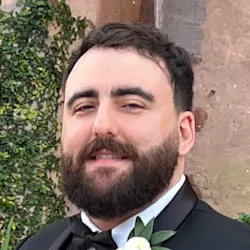
“Great service, fair price, and the parts worked perfectly in our assembly.”
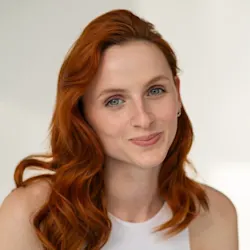
“Top-notch machining and fast shipping. Very satisfied with the results.”
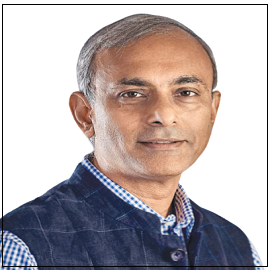
“The next disruption is happening in Prototyping & Manufacturing on-demand and Frigate is leading the way! I personally believe the Frigate's way of IIOT enabled cloud platform with Al.”
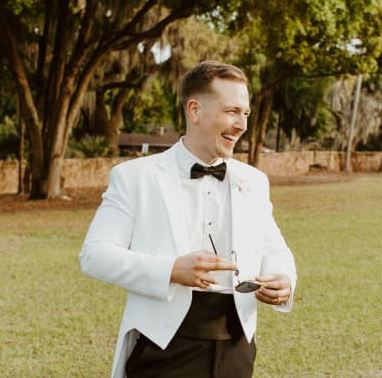
“Frigate delivered high-quality parts at a competitive price. The instant quote tool is a huge plus for us!”

“We appreciate the precision and quality of the machined components in the recent delivery—they meet our specifications perfectly and demonstrate Frigate’s capability for excellent workmanship.”
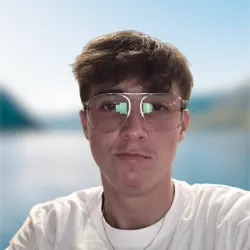
“Flawless execution from quote to delivery.”

“I am absolutely happy to work with supplier like Frigate who were quite proactive & result oriented . Frigate has high willingness team who has strong know how & their passion towards the products & process were absolutely thrilling.”
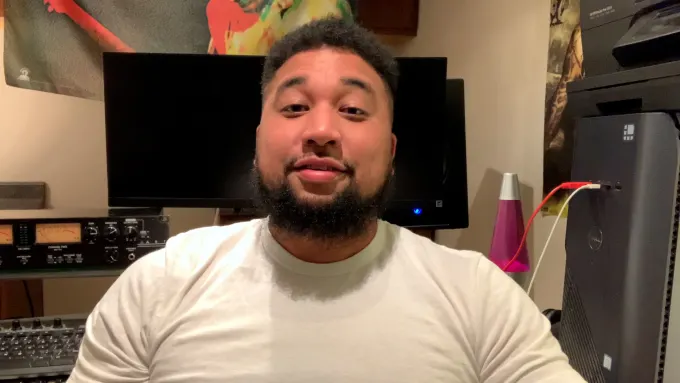
“The precision on these parts is impressive, and they arrived ahead of schedule. Frigate’s process really stands out!”
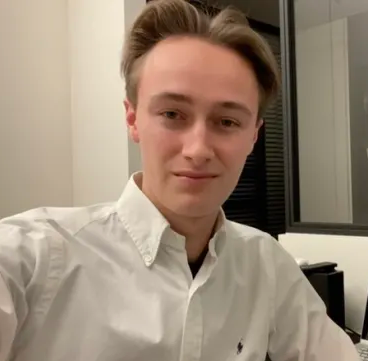
“Parts were exactly as spec’d, and the instant quote made budgeting a breeze.”
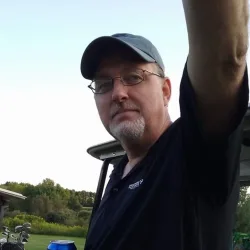
“Good value for the money.”
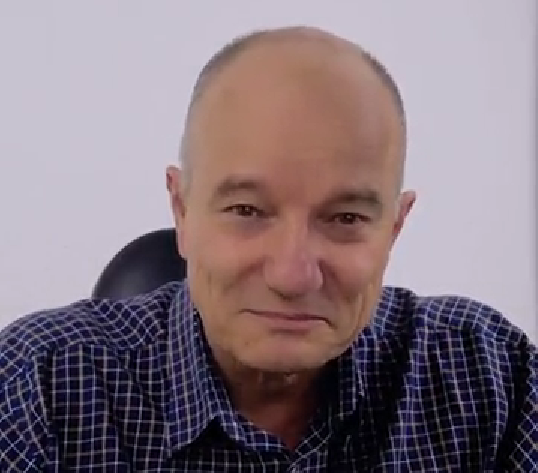
“The finish was perfect, and the team was easy to work with.”

“Working with Frigate has been great. Their proactive, results-driven approach and expertise shine through in every project. It's been a pleasure collaborating with them.”

"We are highly satisfied with the timely delivery and quality of the MIG Welding Cable from Frigate. Their attention to detail, secure packaging, and quick responsiveness stood out. We confidently recommend Frigate Engineering Services Pvt. Ltd. as a reliable manufacturing partner."
Having Doubts? Our FAQ
Check all our Frequently Asked Question
The welding current, voltage, and travel speed influence heat input during welding. Higher current and voltage increase heat, while a slower travel speed allows more heat to penetrate the material. Properly controlling these factors ensures optimal fusion and reduces the risk of defects.
The choice of filler material impacts the mechanical properties of the weld. Different fillers have varying strengths, flexibility, and corrosion resistance. Selecting the right filler ensures compatibility with the base metals and can enhance the overall performance and durability of the welded joint.
Preheating helps minimize thermal shock and reduces the risk of cracking when welding dissimilar metals. By raising the temperature of the base materials, preheating improves fusion and promotes better metallurgical bonding, leading to a stronger and more reliable weld.
Automated welding systems enhance weld quality by providing consistent heat input, travel speed, and precise control over parameters. This reduces human error and variability, resulting in uniform welds that meet strict quality standards. Automation also increases production efficiency and allows for more complex joint configurations.
Common non-destructive testing methods include ultrasonic, radiographic, and magnetic particle testing. These techniques assess weld integrity without damaging the material. Each method offers unique advantages, such as detecting internal flaws, surface defects, or material inconsistencies, ensuring the welded joints meet safety and performance requirements.
We'd love to Manufacture for you!
Submit the form below and our representative will be in touch shortly.
LOCATIONS
Global Sales Office
818, Preakness lane, Coppell, Texas, USA – 75019
Registered Office
10-A, First Floor, V.V Complex, Prakash Nagar, Thiruverumbur, Trichy-620013, Tamil Nadu, India.
Operations Office
9/1, Poonthottam Nagar, Ramanandha Nagar, Saravanampatti, Coimbatore-641035, Tamil Nadu, India. ㅤ
Other Locations
- Bhilai
- Chennai
- Texas, USA