Investment Casting Services
Frigate Die Casting Services offers top-notch investment casting for various industries. This method creates metal parts with very precise details and smooth surfaces. It produces parts close to their final shape with excellent dimensional accuracy. This means you get high-quality, well-fitting parts every time.
Our Clients





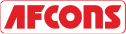

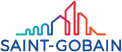


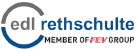

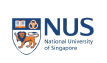
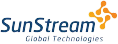

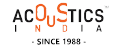




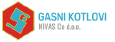
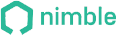
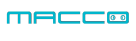












Advantages of Investment Casting Services
High Dimensional Accuracy
Investment casting ensures parts are made to exact measurements. This means each part fits perfectly and works as intended.
Smooth Surface Finish
The process creates very smooth surfaces on parts, reducing the need for extra finishing and improving the look and feel.
Flash-free Parting Lines
Investment casting leaves no extra metal on parting lines. This means fewer defects and a cleaner final product without extra trimming.
Compatible with Most Metals
This casting method works with many metals. It's flexible and can handle different materials for various needs and industries.
Full-Service Precision Quality Investment Castings
Our experts handle over 200 types of ferrous and non-ferrous alloys, like strong stainless steel, aluminum, armor, and nickel-based alloys. Our process starts with smart design and quick prototyping to ensure high quality and efficiency. After casting, we provide in-house machining, coating, and assembly to deliver complete, ready-to-use components.

Get Your Quote Now
- Instant Quotation
- On-Time Delivery
- Affordable Cost
Our Investment Casting Process






Start by making a wax pattern of the part you want to cast. This pattern is a replica of the final product.
Dip the wax pattern into a ceramic slurry to create a mold. This coating hardens to form a shell around the wax pattern.
Heat the mold to melt and remove the wax. This leaves a hollow ceramic shell that shapes the final part.
Involves Pouring molten metal into a hollow shell. The metal fills the space left by the wax pattern, taking its shape.
Once the metal has cooled and solidified, break away the ceramic shell, revealing the metal part.
Clean and finish the metal part to remove any leftover shell material and achieve the desired surface quality.
Post-Processing Services in Investment Casting
Investment casting creates precise components, but they require further refinement to achieve optimal performance. Post-processing enhances strength, durability, and surface quality, ensuring the parts meet industry specifications. It improves resistance to wear, corrosion, and extreme operating conditions. These finishing techniques guarantee high-performance components with exceptional reliability and aesthetics.
Hardness: 35-60 HRC
Aerospace (turbine blades), Automotive (engine parts)
Shot Peening Intensity: 0.15-0.35 mmA
Medical (implants), Automotive (decorative parts)
Surface Finish: Ra 0.4-1.6 µm
Industrial (valves, pumps), Defense (weapon components)
Corrosion Resistance: 500-2000 hrs (salt spray)
Oil & Gas (drill bits), Aerospace (aircraft components)
Penetrant Strength: Level 3+
Aerospace (structural parts), Energy (turbine casings)
Weld Strength: 400-900 MPa
Marine (propellers), Defense (armor parts)
Interference Fit Pressure: 50-200 MPa
Automotive (brake systems), Medical (prosthetics)
Methoding in Investment Casting
Runner width: 3–20 mm
Aerospace (turbine blades), Automotive (engine parts)
Volume: 5–20% of casting
Energy (turbine components), Oil & Gas (valve bodies)
Medical (implants), Electronics (sensor housings)
Defense (armor fittings), Industrial (machine tool parts)
600–800°C (aluminum)
Automotive (lightweight parts), Aerospace (structural components)
Marine (corrosion-resistant components), Energy (heat exchangers)
Industrial (precision gears), Electronics (micro-components)
Aerospace (thin-walled structures), Oil & Gas (drilling tools)

Investment Casting Materials
We specialize in casting advanced parts from many metals and materials. Our investment casting method helps us cast components to meet your complex needs and handle tricky tasks.
It is known for its strength, durability, and resistance to corrosion. It's used in industries like aerospace, automotive, and medical devices for parts that need to withstand tough conditions.
Carbon steel is used for parts that require high strength and wear resistance. It's commonly found in automotive, machinery, and industrial applications.
Alloy steel contains additional elements like chromium, nickel, or molybdenum to improve properties like strength, toughness, and resistance to heat. It's used in demanding applications like tools and heavy machinery.
Nickel-based alloys offer excellent resistance to high temperatures and corrosion. They are used in applications like turbines, aerospace components, and chemical processing.
Cobalt-based alloys are known for their hardness and wear resistance. They are often used in high-stress environments, such as gas turbines and medical implants.
Aluminum alloys are lightweight and have good corrosion resistance. They are used in automotive, aerospace, and consumer products where weight and durability are important.
Bronze is a durable and corrosion-resistant alloy of copper and tin. It's used in applications like marine hardware, sculptures, and bearings.
Copper alloys, including brass and bronze, are used for their good electrical conductivity and corrosion resistance. They are common in electrical components and decorative items.
Streamlined Casting for Top Quality and Speed
Frigate knows customers want high quality, low cost, and quick delivery. A lean manufacturing approach is used in the investment casting services to meet these needs. This method cuts out waste, reduces costs, and boosts quality. Combining multiple steps like wax injection, mold building, and first dipping into single processes makes casting faster and smoother. Technicians are trained to handle different tasks, speeding up the process and minimizing handoffs. This approach is applied throughout the company, saving both time and money for customers.

Compliance for Investment Casting Services
We ensure full compliance with industry-specific standards, integrating advanced quality control and safety measures into every stage of our investment casting services. Our services align with rigorous regulatory requirements to provide various industries with precise, reliable, and safe components. Adherence to these certifications guarantees that our products meet or exceed expectations, reducing risks and improving overall performance.
Key Compliance Certifications
Quality management systems ensuring consistent production and customer satisfaction.
Standard practice for sampling steel castings for mechanical testing, ensuring material reliability.
Restricts hazardous substances in electrical and electronic products, ensuring environmental compliance.
Compliance with U.S. regulations on defense and aerospace technologies to prevent unauthorized export.
Compliance with defense industry standards for materials, manufacturing processes, and sourcing.
Certification for flammability standards in electrical and electronic components.
Ensures that chemicals used in investment castings are safe for human health and the environment.
Tonnage/Capacity in Investment Casting
Investment casting offers precise, high-strength components across various sizes and complexities. With weight capacities up to 500 kg, tight tolerances, and high-temperature pouring, it ensures durability and accuracy. The process supports industries like aerospace, automotive, and energy, delivering cost-effective, high-performance parts.
Aerospace (turbine blades), Defense (missile components)
Industrial (valve bodies), Energy (turbine casings)
Medical (implants), Electronics (heat sinks)
Automotive (engine parts), Oil & Gas (drill components)
Automotive (mass production), Aerospace (critical parts)
Energy (steam turbine blades), Marine (propellers)
Defense (armor components), Machinery (gears)
Medical (prosthetics), Industrial (pumps and valves)
Dimensions in Investment Casting
Investment casting enables the production of complex geometries with exceptional precision, minimizing the need for secondary machining. Advanced mold designs allow for intricate internal structures, sharp edges, and fine surface details. The process supports high aspect ratios, uniform wall thickness, and micro-scale features while maintaining structural integrity.
Aerospace (engine housings), Industrial (pump casings)
Medical (implants), Electronics (sensor housings)
Automotive (thin-walled components), Energy (heat exchangers)
Defense (firearm parts), Oil & Gas (drill components)
Industrial (valve bodies), Aerospace (cooling channels)
Medical (prosthetics), Automotive (decorative trim)
Aerospace (thin fins), Electronics (heat sinks)

Tolerance for Investment Casting Services
The permissible variation in linear dimensions (length, width, height) based on part complexity and casting method. Higher precision is achievable on smaller parts.
Variation in the thickness of the walls. Critical for ensuring uniform mechanical properties and preventing defects like hot spots or thin areas.
Tolerances related to the geometry of the casting, such as flatness, roundness, or concentricity. Ensures correct part alignment and mating with other components.
The roughness of the casting surface, which affects the part’s performance, friction, and aesthetic qualities. Ra 0.8 is often for critical sealing surfaces.
Maximum allowable porosity in the casting, a key factor in determining strength, durability, and integrity. Critical for aerospace and automotive applications.
Tolerance on roundness, crucial for parts like rings, shafts, or gears. Ensures proper fit and function, reducing wear and improving performance in rotating parts.
Deviation from perfect flatness, important for proper sealing, assembly, and performance in both static and dynamic applications.
Deviation in parallel surfaces or features, critical for part assembly and function, ensuring correct spacing and alignment between mating components.
Deviation in angles between casting surfaces. Used for ensuring proper assembly, fitting, and orientation of parts in applications like engine blocks or frames.
Deviation in the position of holes relative to other features. Essential for precise component assembly and mechanical function in parts like brackets or fixtures.
Tolerance on internal and external threads for castings, ensuring correct fit and engagement of screws and bolts, vital for structural integrity in mechanical assemblies.
Variation in part size due to material shrinkage during solidification. This is a critical factor for achieving accurate final part dimensions after cooling.
Tolerance on the distribution of metal flow during casting, ensuring uniform thickness and eliminating defects such as cold shuts or misruns.
Tolerance for the radii or fillet corners in castings, which affect stress distribution and part strength, particularly in fatigue-critical applications.
Tolerance for movement or misalignment of cores inside the mold, which could result in dimensional errors, affecting the overall shape and functionality of the part.
Roughness of internal surfaces, particularly important for parts with complex internal passages or channels, such as aerospace or automotive engine components.
Tolerance for corner radii, which is critical for ensuring smooth transitions and reducing stress concentration in parts exposed to high mechanical loads.
Variation in wall thickness across the part, which impacts casting uniformity, mechanical properties, and resistance to thermal or mechanical stresses.
Deviation between aligned surfaces or features, essential for ensuring that parts fit and assemble properly with other components in the final product.
Tolerance for part dimensions, critical for large-scale assemblies and ensuring proper fit with mating components in applications such as automotive or aerospace.

Quality Testing Standards for Investment Casting Services
Uses laser scanners to quickly and accurately measure the part’s geometry to confirm it meets precise dimensional tolerances.
Utilizes micro-computed tomography (CT) to detect and quantify internal porosity at a microstructural level, ensuring integrity.
Detects surface and subsurface cracks or inclusions by inducing electric currents, especially useful for detecting fine cracks.
Measures the number of cycles a component can endure under alternating bending stresses before failure, crucial for cyclic loading.
Assesses the corrosion resistance of the material under controlled exposure to salt fog, simulating aggressive environmental conditions.
Non-destructive imaging technique to detect defects and ensure the quality and uniformity of internal cavities and cores.
Measures the material’s behavior under compressive loads, particularly important for parts exposed to compression during use.
Tests the material’s ability to withstand rapid temperature changes, simulating extreme thermal cycles during operational use.
Scanning electron microscopy (SEM) is used to examine sintered regions in castings, ensuring proper bonding and material flow.
Measures how a material reacts to a magnetic field, useful for evaluating casting material for electromagnetic applications.
Assesses the material’s resistance to high-temperature stress over prolonged periods, indicating its ability to perform under heat.
Determines the elemental composition of alloys, ensuring material meets the specific chemical requirements for casting.
Verifies that any surface coatings adhere properly under mechanical stress, maintaining long-term performance and aesthetic quality.
Measures how refractory molds shrink during casting, ensuring that dimensional stability is maintained through the casting process.
Subject castings to vibrational stress using a shaker table to test their fatigue resistance under dynamic loading conditions.
Assesses mold integrity by checking for leaks, ensuring that the casting process is not compromised due to mold defects.
Determines the material's ability to resist sudden forces or impacts, critical for parts subjected to high-energy environments.
Evaluates the flow of material in the mold to ensure uniform grain structure, important for minimizing stress points in the casting.
Measures the stiffness or rigidity of the material by analyzing its stress-strain curve under tensile loading.
Assesses how well the material can be welded without causing defects, essential for parts that may require post-casting welding.
Measures the material's ability to conduct heat, which is crucial for applications requiring heat dissipation or thermal control.
Measures the extent to which a material can be stretched before breaking, indicating its ability to undergo deformation without failure.
Ensures that heat treatment processes do not cause excessive distortion or warping in cast parts, maintaining dimensional integrity.
Simulates the recycling of metal castings, ensuring that the material can be reused in future casting processes without loss of quality.
Measures the ability of the material to absorb vibrational energy, which is particularly relevant in applications like automotive or aerospace.
Inspection Techniques in Investment Casting
Resolution: 1–10 µm
Aerospace (turbine blades), Defense (armor components)
Frequency: 1–10 MHz
Energy (nuclear components), Marine (propellers)
Detection depth: Up to 6 mm
Automotive (engine blocks), Industrial (gears)
Crack detection: ≥0.001 mm
Medical (implants), Aerospace (airframe parts)
Frequency: 100 Hz – 10 MHz
Electronics (sensor housings), Oil & Gas (valve bodies)
Precision: ±0.001 mm
Automotive (transmission parts), Industrial (machined castings)
Accuracy: ±0.01 mm
Aerospace (complex geometries), Robotics (precision parts)
Elemental detection: ppm level
Medical (biocompatible alloys), Energy (heat exchangers)


Industry Applications of Investment Casting
High-temperature strength, lightweight alloys, extreme precision
Complex geometries, wear resistance, high-performance materials
Biocompatibility, ultra-fine surface finish, dimensional accuracy
Thermal efficiency, corrosion resistance, fatigue strength
Extreme pressure resistance, high-strength alloys, chemical stability
Load-bearing capacity, near-net-shape accuracy, cost efficiency
Saltwater resistance, long-term durability, precision engineering
High conductivity, minimal material waste, micro-feature accuracy
Reliable Investment Castings for Defense Applications
Military and defense soldiers depend on high-quality castings to perform their jobs effectively. Investment castings are crucial for creating parts that meet strict standards for defense applications. These castings are made precisely, ensuring they are strong, reliable, and fit perfectly. They help soldiers have the best equipment and perform their duties safely and efficiently. At Frigate, investment casting expertise guarantees that parts meet exact specifications and quality requirements. For defense applications, rely on Frigate to provide precise and dependable castings that support your critical needs.






Industries We Serve
- Solid Progress
Our Manufacturing metrics
Frigate brings stability, control, and predictable performance to your sourcing operations through a structured multi-vendor system.
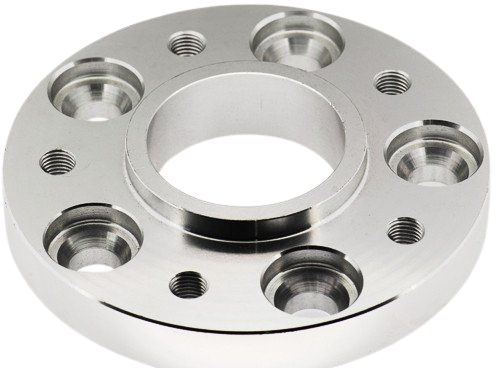
2.8X
Sourcing Cycle Speed
Frigate’s pre-qualified network shortens decision time between RFQ and PO placement.
94%
On-Time Delivery Rate
Structured planning windows and logistics-linked schedules improve project-level delivery reliability.
4X
Multi-Part Consolidation
We enable part family batching across suppliers to reduce fragmentation.
22%
Quality Rejection Rate
Multi-level quality checks and fixed inspection plans lower non-conformities.
30%
Procurement Costs
Optimized supplier negotiations and bulk order strategies reduce your overall sourcing expenses.
20%
Manual Processing Time
Automation of sourcing and supplier management significantly reduces time spent on manual tasks.
Investment Casting for Complex Parts and Large Batches
Frigate’s investment casting services includes making ceramic molds, advanced machining, heat treatment, and casting with various materials. This ensures precise parts that meet your project’s needs. Our advanced equipment allows for high-volume production, fitting within budgets and timelines. If machining is needed, you can rely on us for surface finishing for complex parts.

Get Clarity with our Manufacturing Insights
- Real Impact
Words from Clients
See how global OEMs and sourcing heads describe their experience with our scalable execution.
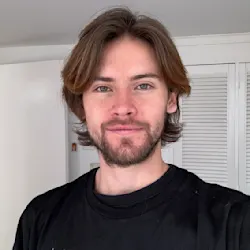
“Quick turnaround and solid quality.”
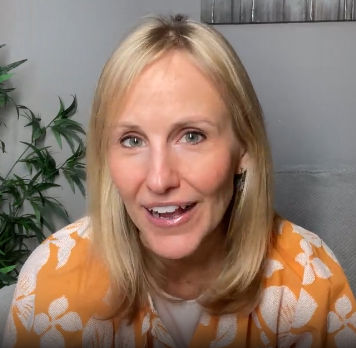
“The instant quote tool saved us time, and the parts were spot-on. Highly recommend Frigate!”
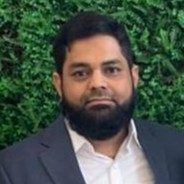
“I would strongly recommend Frigate to anyone who wants to do Rapid Prototyping, and take their ideas to manufacturing. One firm doing all kinds of Product Development!”
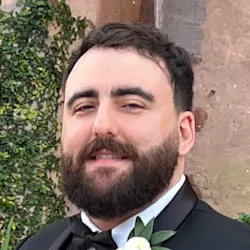
“Great service, fair price, and the parts worked perfectly in our assembly.”
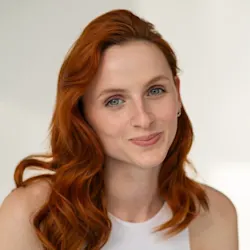
“Top-notch machining and fast shipping. Very satisfied with the results.”
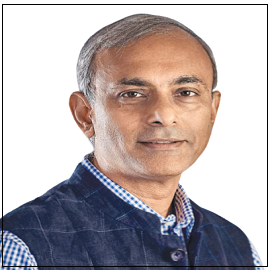
“The next disruption is happening in Prototyping & Manufacturing on-demand and Frigate is leading the way! I personally believe the Frigate's way of IIOT enabled cloud platform with Al.”
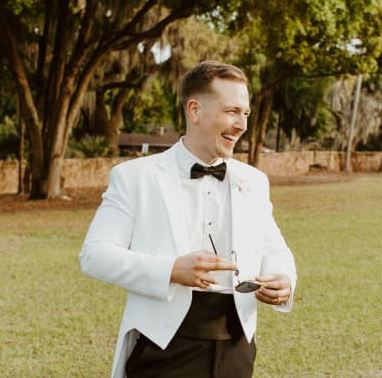
“Frigate delivered high-quality parts at a competitive price. The instant quote tool is a huge plus for us!”

“We appreciate the precision and quality of the machined components in the recent delivery—they meet our specifications perfectly and demonstrate Frigate’s capability for excellent workmanship.”
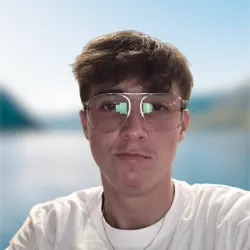
“Flawless execution from quote to delivery.”

“I am absolutely happy to work with supplier like Frigate who were quite proactive & result oriented . Frigate has high willingness team who has strong know how & their passion towards the products & process were absolutely thrilling.”
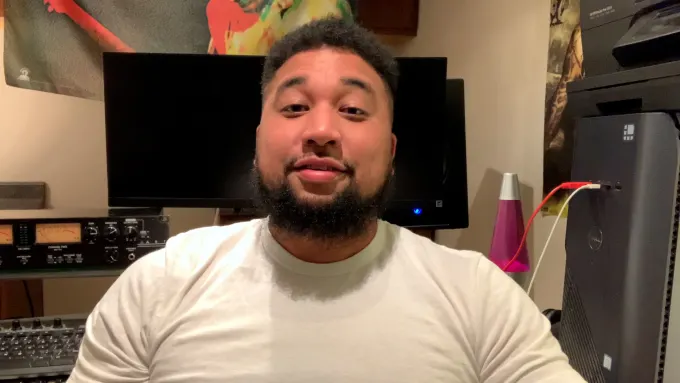
“The precision on these parts is impressive, and they arrived ahead of schedule. Frigate’s process really stands out!”
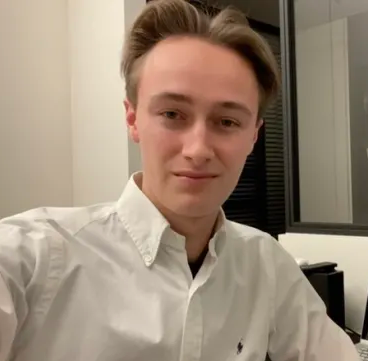
“Parts were exactly as spec’d, and the instant quote made budgeting a breeze.”
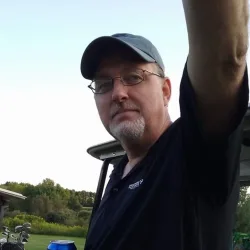
“Good value for the money.”
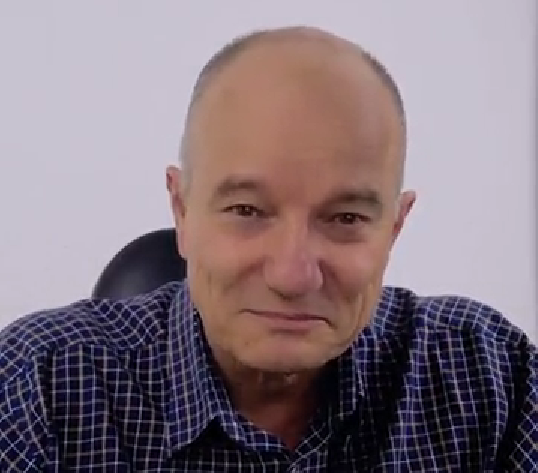
“The finish was perfect, and the team was easy to work with.”

“Working with Frigate has been great. Their proactive, results-driven approach and expertise shine through in every project. It's been a pleasure collaborating with them.”

"We are highly satisfied with the timely delivery and quality of the MIG Welding Cable from Frigate. Their attention to detail, secure packaging, and quick responsiveness stood out. We confidently recommend Frigate Engineering Services Pvt. Ltd. as a reliable manufacturing partner."
Having Doubts? Our FAQ
Check all our Frequently Asked Question
Investment casting allows for the creation of highly complex shapes with intricate details. It uses a wax pattern coated in a ceramic shell. The wax is then melted away, leaving a hollow mold. The process can achieve near-net shapes without needing extensive machining, making it perfect for parts with fine features and complex geometries.
The investment casting process uses ceramic molds that can capture precise details of the wax pattern. When the metal is poured into the mold, it solidifies to match the exact shape, allowing for tight tolerances. Controlling the cooling and solidification process also helps minimize defects, ensuring parts have consistent dimensions.
Investment casting can handle a wide range of alloys, including stainless steel, carbon steel, aluminum, titanium, and nickel-based alloys. These materials are chosen depending on the part's application and requirements, such as heat resistance, corrosion resistance, or mechanical strength. The flexibility in material choice is a major benefit of investment casting.
The ceramic shell used in investment casting forms a smooth inner surface, which transfers to the final cast part. This results in a smooth surface finish, often between 125 to 63 microinches (3.2 to 1.6 microns) without additional machining. This is particularly useful for components that need minimal post-production finishing or polishing.
Investment casting is well-suited for high-temperature applications because it can work with superalloys and other heat-resistant materials. These alloys retain their strength and integrity even at extreme temperatures, making investment casting ideal for aerospace components, gas turbines, and other demanding environments where high heat resistance is critical.
We'd love to Manufacture for you!
Submit the form below and our representative will be in touch shortly.
LOCATIONS
Global Sales Office
818, Preakness lane, Coppell, Texas, USA – 75019
Registered Office
10-A, First Floor, V.V Complex, Prakash Nagar, Thiruverumbur, Trichy-620013, Tamil Nadu, India.
Operations Office
9/1, Poonthottam Nagar, Ramanandha Nagar, Saravanampatti, Coimbatore-641035, Tamil Nadu, India. ㅤ
Other Locations
- Bhilai
- Chennai
- Texas, USA