Injection molding has long been a foundation of modern manufacturing, enabling the mass production of high-quality plastic parts. But the industry isn’t still. New injection molding technologies are constantly emerging, offering vast advantages for businesses across various sectors.
Whether you’re a seasoned manufacturer or just starting, incorporating these advancements can significantly improve your operations. Let’s explore how new injection molding technologies can benefit your business regarding manufacturing efficiency, design flexibility, production speed, and more.
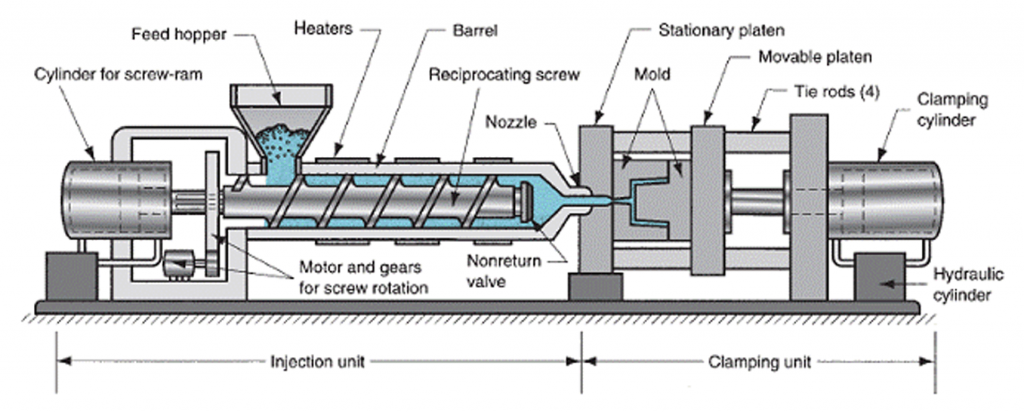
Optimizing Manufacturing via Injection Molding Technologies
One of the most significant benefits of new injection molding technologies is their ability to streamline manufacturing. Here’s how-
- Automation & Reduced Labor Costs- Advanced technologies like robotic part handling and automated process control significantly reduce the need for manual intervention. This transforms to lower labor costs and a safer work environment for your employees.
- Real-time Data & Process Optimization- Modern injection molding machines are equipped with sensors that collect real-time data on various process parameters. This data can be analyzed to identify areas for improvement and optimize settings for higher efficiency and reduced waste.
- Remote Monitoring & Reduced Downtime- With features like remote monitoring, you can keep an eye on your injection molding machines even from afar. This allows for early detection of potential issues and prompt intervention, minimizing downtime and ensuring smooth production runs.
Unlocking Design Flexibility
New injection molding technologies are pushing the boundaries of what’s possible in terms of design. Here’s how they empower you to create innovative products-
- Multi-material Molding- This technique allows you to combine different materials within a single mold, creating parts with unique properties like enhanced strength, conductivity, or aesthetics.
- Conformal Cooling Channels- Traditional cooling channels can limit design complexity. New technologies like conformal cooling offer more intricate channel designs, enabling the production of complex parts with consistent cooling throughout.
- Rapid Prototyping & Design Iteration- Advanced 3D printing techniques are often integrated with injection molding. This allows for faster and more cost-effective prototyping, facilitating rapid design iteration and quicker time-to-market.
Boosting Production Speed
New injection molding technologies can significantly accelerate your production process, giving you a competitive edge-
- Faster Cycle Times- Advancements in mold design and machine capabilities allow for faster material injection, cooling, and part ejection, leading to quicker cycle times and higher production output.
- Reduced Lead Times- With faster production speeds, you can fulfill customer orders more promptly, reducing lead times and improving customer satisfaction.
- Increased Responsiveness to Market Demands- The ability to speed up production quickly allows you to respond efficiently to changing market demands and capitalize on new business opportunities.
Four Advancements in Injection Molding Technologies
Let’s take a closer look at four specific advancements in injection molding technologies that offer exciting possibilities-
- Gas-assisted injection molding- This technology utilizes gas to improve the even distribution of molten material into complex molds, leading to parts with fewer defects, less material waste, and improved strength.
- Structural foam molding- This process creates lightweight parts with a low-density core and a high-density skin, making them ideal for applications where weight reduction and structural integrity are crucial.
- Injection over-molding- This technique allows for the creation of multi-material parts by injecting a new material over an existing base part. This can enhance grip, provide shock absorption, or create aesthetically pleasing two-tone designs.
- Software for injection molding- New software advancements like mold flow simulation and structural analysis tools empower designers and manufacturers to optimize mold designs, predict product behavior, and streamline the entire injection molding process.
Additional Benefits Beyond Efficiency, Design, and Speed
The advantages of new injection molding technologies extend far beyond just efficiency, design flexibility, and production speed. Here are some additional benefits to consider-
- Reduced Material Waste- Certain technologies like multi-shot molding and controlled material dosing minimize material waste during the production process, leading to cost savings and a more sustainable operation.
- High-Quality Products- Advanced process control ensures consistent part quality with minimal defects. This translates to fewer rejects and a higher overall yield, leading to improved product quality and customer satisfaction.
- Sustainability Considerations- Many new injection molding technologies prioritize sustainability. Some allow for the use of recycled materials or bioplastics, reducing your environmental consequences.

Frigate is your Partner in Innovation in Injection Molding Technologies
At Frigate, we’re more than just an injection molding service provider. We’re your innovation partner. We stay at the forefront of the industry, constantly investing in the injection molding technologies and training our team to be experts in their field.
Here’s what sets us apart
- Unparalleled Expertise- Our team of experienced engineers and technicians possesses a deep understanding of new injection molding technologies and their applications. They can help you determine the best approach for your specific needs and ensure a seamless integration into your existing processes.
- Cutting-Edge Equipment- We’re committed to providing our clients with access to the most advanced injection molding machinery available. This ensures you benefit from the latest advancements in speed, precision, and efficiency.
- Customized Solutions- We understand that every business has unique requirements. We take the time to understand your specific goals and challenges, and then develop a customized injection molding solution that perfectly aligns with your needs.
- Unwavering Support- Our commitment to your success doesn’t end after the initial project. We offer ongoing support throughout your journey, ensuring you have the resources and expertise to maximize the benefits of new injection molding technologies.
Investing in the future of your manufacturing starts with a conversation. Contact Frigate today to discuss your specific needs and explore how we can help you transform your operations with the power of new injection molding technologies. Let’s unlock a world of possibilities together.