- Cooling Extrusions
Automotive & Transportation Extrusions
Frigate designs precision extrusions with built-in thermal channels using high-conductivity alloys to manage heat loads in EV battery enclosures and power control systems. These extrusions help stabilize high-voltage components and mitigate thermal runaway risks.

Our Clients
Trusted by Engineers and Purchasing Leaders
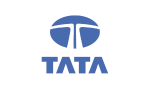
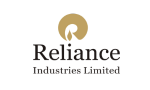


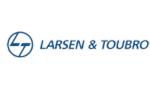
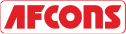


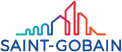

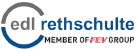

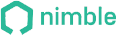
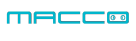









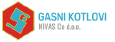
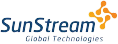

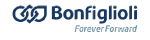


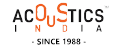
- Versatile Offerings
Our Automotive & Transportation Extrusions Products
Explore our range of high-quality Automotive & Transportation Extrusions today.
- Real Impact
Words from Clients
See how global OEMs and sourcing heads describe their experience with our scalable execution.
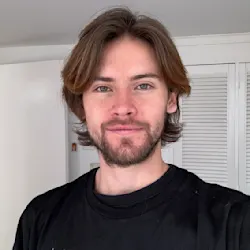
“Quick turnaround and solid quality.”
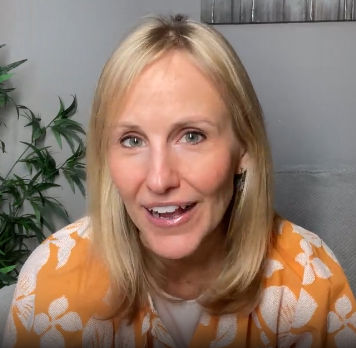
“The instant quote tool saved us time, and the parts were spot-on. Highly recommend Frigate!”
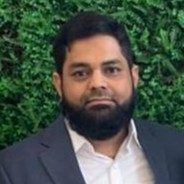
“I would strongly recommend Frigate to anyone who wants to do Rapid Prototyping, and take their ideas to manufacturing. One firm doing all kinds of Product Development!”
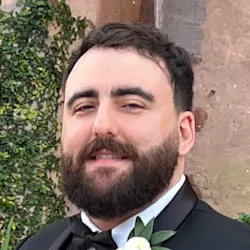
“Great service, fair price, and the parts worked perfectly in our assembly.”
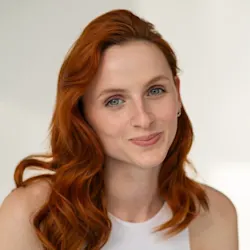
“Top-notch machining and fast shipping. Very satisfied with the results.”
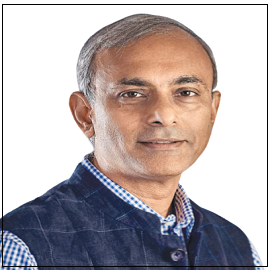
“The next disruption is happening in Prototyping & Manufacturing on-demand and Frigate is leading the way! I personally believe the Frigate's way of IIOT enabled cloud platform with Al.”
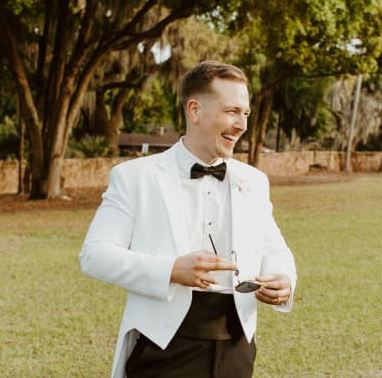
“Frigate delivered high-quality parts at a competitive price. The instant quote tool is a huge plus for us!”

“We appreciate the precision and quality of the machined components in the recent delivery—they meet our specifications perfectly and demonstrate Frigate’s capability for excellent workmanship.”
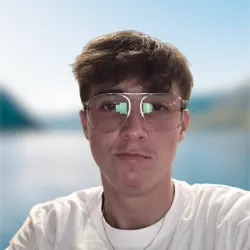
“Flawless execution from quote to delivery.”

“I am absolutely happy to work with supplier like Frigate who were quite proactive & result oriented . Frigate has high willingness team who has strong know how & their passion towards the products & process were absolutely thrilling.”
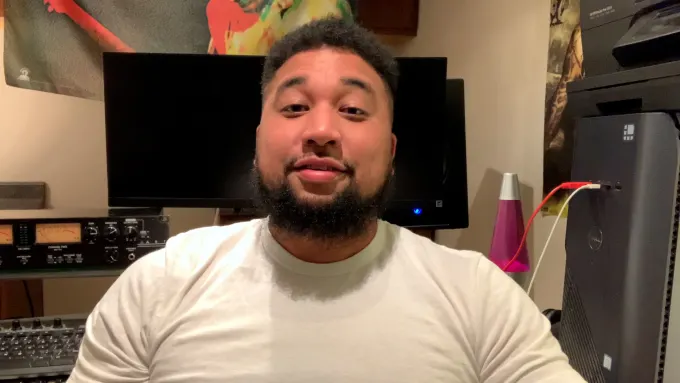
“The precision on these parts is impressive, and they arrived ahead of schedule. Frigate’s process really stands out!”
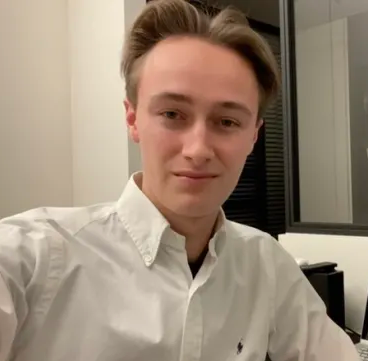
“Parts were exactly as spec’d, and the instant quote made budgeting a breeze.”
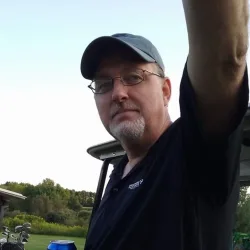
“Good value for the money.”
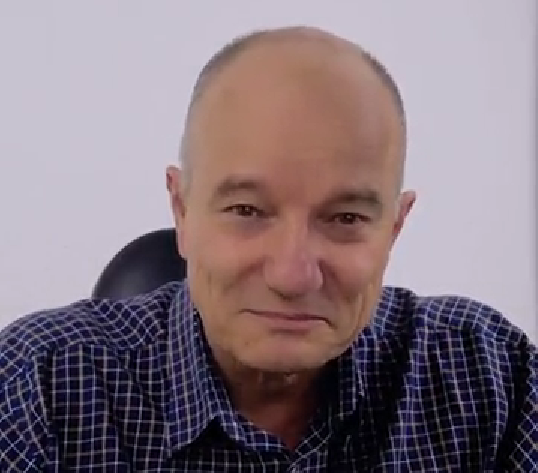
“The finish was perfect, and the team was easy to work with.”

“Working with Frigate has been great. Their proactive, results-driven approach and expertise shine through in every project. It's been a pleasure collaborating with them.”

"We are highly satisfied with the timely delivery and quality of the MIG Welding Cable from Frigate. Their attention to detail, secure packaging, and quick responsiveness stood out. We confidently recommend Frigate Engineering Services Pvt. Ltd. as a reliable manufacturing partner."
We export to 10+ countries
Frigate’s Global Presence
Frigate takes pride in facilitating “Make in India for the globe“. As our global network of Frigaters provides virtually limitless capacity, and through our IoT enabled platform your parts go directly into production. By digitally and technologically enabling “the silent pillars of the economy” MSME and SME manufacturing industries, we are able to tap the huge potential for manufacturing to bring the best results for our clients.

100,000+
Parts Manufactured
250+
Frigaters
2000+
Machines
450+
Materials
25+
Manufacturing Process
Industry Applications
Used in vehicle chassis and body frames to provide rigidity, crash resistance, and weight reduction through high-strength extruded profiles.
Form thermal and mechanical protective housings for electric vehicle battery packs, ensuring heat dissipation and structural containment.
Serve as energy-absorbing members in impact zones, manufactured with extruded aluminum for lightweight crash management.
Enable modular attachment systems for cargo, integrating aerodynamic profiles with corrosion-resistant extruded components.
Provide lightweight and strong structural bases for automotive seating, supporting precise mounting and alignment under dynamic loading.
Used in in-cabin climate control systems to route conditioned air through custom-shaped extruded pathways.




- Rapid Delivery
Accelerating Prototyping and Production
Rapid prototyping and agile tooling adjustments are crucial in the fast-moving EV sector to meet production deadlines. Frigate’s streamlined processes enable quick turnarounds and reduce lead times.
- Prototype extrusions delivered in 2-3 weeks, reducing cycle time by 30%
- Tooling adjustments completed in 24-48 hours, enabling rapid design changes
- Production schedules aligned in real-time to improve efficiency by 15-20%
- Scalable tooling for both low-volume prototypes and high-volume production
- Quick material sourcing and inventory management to minimize delays and ensure consistent production flow
- Seamless integration with OEM timelines to avoid bottlenecks and ensure on-time delivery
The right material, such as 6000 or 7000 series aluminum alloys, provides the necessary strength and flexibility to resist fatigue in high-cycle environments. These alloys undergo precise heat treatments to optimize microstructure, ensuring the extrusion maintains its performance in critical areas like suspension components and structural reinforcements.
To achieve tight tolerances, direct extrusion and pneumatic die systems are used. These methods ensure accurate profile geometry and reduce the risk of warping or deformation, especially in applications requiring precise fitments like trim parts, seals, or chassis components.
Multi-void profiles allow for lightweight, yet strong, structural solutions. By strategically placing voids within the extrusion, material usage is optimized without sacrificing strength, making them ideal for high-performance components such as bumpers, crash structures, and energy-absorbing elements.
Extrusions are often treated with anodizing, powder coating, or e-coating to enhance their resistance to corrosion. Anodizing creates a protective oxide layer, while powder coating and e-coating add a durable, smooth finish that resists environmental elements like salt, moisture, and road debris, particularly for underbody components.
The precision of extrusion dies is crucial in achieving complex geometries, like undercuts or intricate cross-sections, while maintaining uniform material flow. These dies are designed using advanced simulation techniques to ensure that the profile meets the specific strength, weight, and fitment requirements of automotive applications.
We'd love to Manufacture for you!
Submit the form below and our representative will be in touch shortly.
LOCATIONS
Registered Office
10-A, First Floor, V.V Complex, Prakash Nagar, Thiruverumbur, Trichy-620013, Tamil Nadu, India.
Operations Office
9/1, Poonthottam Nagar, Ramanandha Nagar, Saravanampatti, Coimbatore-641035, Tamil Nadu, India. ㅤ
Other Locations
- Bhilai
- Chennai
- USA
- Germany