Full Mold casting Services
Frigate uses Full Mold Casting with expanded polystyrene for complex geometries. We ensure precise mold burnout, achieving accurate tolerances and minimal thermal distortion.
Our Clients





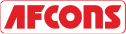

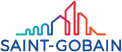


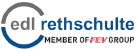

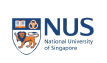
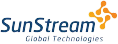

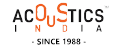




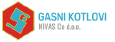
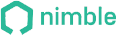
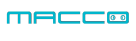












Advantages of Full Mold casting Services
Thermal Stability
The casting process minimizes thermal expansion, allowing consistent properties across the entire casting, which is crucial for high-performance applications.
No Draft Angles Required
Patterns can be made without draft angles, allowing for sharper details and reducing the complexity of the pattern-making process.
Fast Production Cycles
This method allows quick pattern production and streamlined casting, making it ideal for short lead times and rapid prototyping.
Lower Risk of Defects
By eliminating parting lines typical in traditional molds, Full Mold Casting reduces the occurrence of casting defects like flash or mismatches.
Advanced Solutions with Custom Full Mold Casting Services
Custom Full Mold Casting offers precise manufacturing for intricate and complex designs. This method utilizes expendable polystyrene patterns to achieve tight tolerances and sharp details. It reduces tooling costs and accelerates production timelines, making it ideal for high-precision applications. The process ensures minimal thermal distortion, resulting in consistent dimensional accuracy and superior surface finishes. Full Mold Casting is compatible with various alloys, accommodating diverse material requirements. The method eliminates parting lines, lowering the risk of casting defects and enhancing overall quality.

Get Your Quote Now
- Instant Quotation
- On-Time Delivery
- Affordable Cost
Our Full Mold casting Process






An expandable polystyrene foam pattern is precisely cut or molded to match the desired shape of the final casting.
The foam pattern is coated with a refractory material to create a heat-resistant barrier, enhancing the casting's surface finish.
The coated pattern is placed in a flask, and dry sand is compacted around it, providing support during the casting process.
When molten metal is poured directly upon it, the foam pattern is vaporized, and the cavity is filled with liquid metal.
The metal cools and solidifies within the sand mold, maintaining the exact shape and details of the original foam pattern.
The sand mold is broken apart, and the completed casting is removed once the metal has cooled, ready for any necessary post-processing.
Post-Processing Services in Full Mold Casting
Post-processing enhances the quality and precision of full mold casting components. Techniques like deburring, heat treatment, and polishing ensure optimal surface finishes and performance for industries such as aerospace, automotive, and electronics.
Surface roughness: Ra < 0.5 µm
Automotive (brake components), Aerospace (engine parts)
Surface profile: 3-4 mils
Cleaning efficiency: 95-98%
Electronics (housing), Machinery (gears)
Hardness: 40-50 HRC
Medical devices (implants), Aerospace (turbine blades)
Hardness: Rockwell C 40-60
Stress relieving time: 1-2 hours
Automotive (engine blocks), Aerospace (landing gears)
Burr removal efficiency: 95%
Automotive (metal housings), Electronics (connectors)
Duration: 2-5 hours
Surface finish: Ra 1-3 µm
Consumer goods (cosmetic parts), Aerospace (small parts)
Cutting speed: 150-300 m/min
Depth of cut: 0.5-2 mm
Aerospace (brackets), Automotive (suspension parts)
Hardness: 35-55 HRC
Corrosion resistance: 500-1000 hours (salt spray test)
Electronics (circuit boards), Automotive (corrosion-resistant parts)
Laser power: 10-100 W
Precision: ±0.01 mm
Aerospace (serial numbers), Medical devices (labels)
Tensile strength: 400-600 MPa
Heat affected zone: ≤0.5 mm
Automotive (exhaust systems), Construction (structural components)
Methoding in Full Mold Casting
Aerospace (engine casings), Automotive (brake calipers)
Automotive (engine blocks), Marine (propeller hubs)
Aerospace (turbine blades), Automotive (transmission parts)
Automotive (engine blocks), Industrial (machinery components)
Aerospace (lightweight parts), Automotive (high-performance parts)
Aerospace (turbine components), Oil & Gas (high-pressure valves)
Automotive (aluminum engine components), Industrial (gear parts)
Electronics (small components), Automotive (engine parts)
Aerospace (precise castings), Automotive (brackets, mounts)
Industrial (pressure valves), Aerospace (jet engine parts)
Automotive (cosmetic parts), Electronics (precise components)
Automotive (engine components), Industrial (pump casings)
Aerospace (large turbine casings), Automotive (frame parts)

Full Mold casting Materials
Full Mold Casting enables precise production of complex and intricate designs. It offers tight tolerances and excellent control over dimensional accuracy.
These alloys provide excellent strength-to-weight ratios with good fatigue resistance. They are ideal for aerospace frames and automotive parts requiring lightweight durability.
Known for high tensile strength and impact resistance, ductile iron retains flexibility, making it perfect for heavy machinery parts subject to dynamic loads.
These grades offer outstanding corrosion resistance and are highly stable under extreme temperatures. They are suitable for chemical processing equipment and marine applications.
Copper-nickel alloys combine excellent resistance to seawater corrosion with good thermal conductivity. They are commonly used in marine fittings and heat exchangers.
High-carbon steel delivers superior hardness and wear resistance, making it suitable for industrial tools, dies, and high-strength components.
Inconel alloys are known for their exceptional oxidation and creep resistance at high temperatures. They are used in aerospace turbines and power generation systems.
Ensuring Consistent Material Properties Across Large Batches
In Full Mold Casting, the solidification process is closely controlled to ensure uniformity in material properties. Utilizing a consistent cooling rate and minimizing thermal distortion promotes an even distribution of strength, density, and mechanical characteristics. The vaporization of the polystyrene pattern eliminates the risk of variation due to traditional mold setup. Frigate’s precise control over the process results in castings that maintain uniform properties across large batches, ensuring reliability and consistency in high-demand applications.

Compliance for Full Mold Casting Services
We are committed to upholding the highest standards in Full Mold Casting services. We comply with stringent industry regulations to ensure precision, reliability, and safety in every casting. Our services meet the specific needs of high-performance sectors such as aerospace, automotive, and electronics. We guarantee that all castings meet or exceed the required specifications by adhering to strict quality control measures.
Quality management system standard for consistent excellence in production (Certification No. 12345).
Restriction of hazardous substances in electronic and electrical equipment.
Standard specification for aluminum alloy castings used in industrial applications.
Compliance with European Union regulations on the safe use of chemicals in manufacturing.
Environmental management system to reduce environmental impact (Certification No. 67890).
Aerospace quality management standard (Certification No. 11223) for stringent aerospace component requirements.
Compliance with Federal Aviation Administration standards for aerospace castings and materials.
Tonnage / Capacity in Full Mold Casting
Tonnage and capacity are critical factors in full mold casting, defining the scale, pressure, and precision required for the casting process. These parameters determine the ability to produce parts with specific mechanical properties, dimensional tolerances, and material characteristics.
Automotive (engine blocks), Aerospace (aircraft components)
Automotive (transmission parts), Industrial (heavy-duty components)
Aerospace (turbine casings), Automotive (brake rotors)
Electronics (connectors), Automotive (small engine parts)
Aerospace (small parts), Automotive (lightweight components)
Automotive (suspension parts), Industrial (gearboxes)
Aerospace (structural components), Automotive (brackets)
Automotive (aluminum alloy parts), Electronics (zinc die castings)
Automotive (engine parts), Aerospace (turbine components)
Automotive (axles, wheels), Aerospace (frames, support structures)
Dimensions in Full Mold Casting
Dimensions are a critical aspect of full mold casting, determining the size, shape, and precision of the final components. These parameters ensure that cast parts meet the necessary specifications for performance, structural integrity, and fit.
Heavy machinery (large housings), Automotive (large brackets)
Aerospace (wing components), Automotive (radiator tanks)
Industrial (hydraulic cylinders), Aerospace (engine mounts)
Aerospace (thin-walled structural parts), Automotive (lightweight components)
Precision components (gears, housings)
Automotive (engine components), Industrial (pumps)
Heavy-duty components (structural parts), Aerospace (frames)
Aerospace (long parts), Automotive (frame structures)
Aerospace (turbine components), Automotive (precision parts)
Micro-components (electronic housings), Aerospace (brackets)

Tolerance for Full Mold Casting Services
Tolerance in the overall dimensions of cast parts, influenced by material, complexity, and mold design.
The roughness average (Ra) indicates surface texture, important for friction reduction and aesthetic purposes.
Tolerance for casting wall thickness, impacting mechanical strength, heat distribution, and product longevity.
Tolerance in the linear dimensions critical for assembly and precise fitting with mating parts.
Angular deviations, ensuring parts align correctly during assembly and fit into complex structures.
Variations in casting weight due to material consistency, process control, and design specifications.
Tolerance for holes or inner features to ensure tight tolerances for shafts, bolts, or other mating components.
Deviation from a flat surface, ensuring stability and effective assembly when parts must lie flush against each other.
Deviation from perfect circularity, critical for functional parts such as shafts or gears where rotational accuracy is essential.
Tolerance for depth in molds, critical for ensuring the correct material distribution and component fit.
Deviation in the position of internal cores during casting, affecting the final shape and fit of internal cavities.
Variation in the thickness of different sections of the casting, influencing cooling rates and mechanical properties.
Deviation from parallelism between two surfaces, ensuring proper alignment in assemblies requiring flatness.
The tolerance of how centered one feature is relative to another, crucial for parts with rotating or moving components.
Deviation in the angle of tapered surfaces, critical for parts that require accurate fits or efficient material flow during casting.
Variations in material composition, ensuring alloy purity and homogeneity for consistent mechanical properties across parts.
The required strength for bonding areas, ensuring the integrity of cast parts under stress.
Efficiency of the mold filling, ensuring that the cavity is completely filled with minimal porosity or defects.
Maximum allowable porosity in the final cast, critical for maintaining structural integrity and functionality.
Variability in dimensions due to material contraction during solidification, affecting the final size and fit of parts.

Quality Testing Standards for Full Mold Casting Services
Provides detailed, non-destructive internal analysis of wall thickness and material integrity, especially in complex geometries.
Advanced scanning technology for rapid and accurate dimensional measurement of complex parts.
Verifies critical geometric features like angle, flatness, and perpendicularity, ensuring compliance with design specifications.
Ensures that the final casting weight is within the specified tolerance for material consistency.
Measures internal diameters with high precision for ensuring accurate fit for mating components.
Detects any deviation from a flat plane, which is crucial for parts that must mate with other flat surfaces.
Ensures that rotating parts (like shafts) maintain precise circular geometry with minimal deviations.
Measures depth of mold cavities, ensuring uniform fill and minimal deviations in thickness, especially for deep or complex parts.
Non-destructive imaging technologies to detect shifts in core placement during solidification.
Ensures uniformity of thickness throughout complex castings to avoid weak spots and ensure load-bearing capacity.
Measures parallelism between two surfaces to ensure that components align accurately in final assembly.
Measures the alignment of concentric features, ensuring the precise fit of cylindrical or rotational parts.
Measures the taper angle of cast components to ensure proper fitting and material flow during casting.
Measures the chemical composition of alloys to ensure consistent material properties and purity.
Tests the tensile and bonding strength of cast materials to ensure that they meet mechanical performance standards.
Detects incomplete filling, voids, or cold shuts, ensuring that the mold cavity is fully filled and free from defects.
Non-destructive tests to identify internal voids and porosity, which can impact the part’s strength and durability.
Measures the final casting dimensions to ensure that shrinkage due to cooling is within specified limits.
Measures the material's resistance to fatigue under cyclic loading, important for components in dynamic environments.
Assesses the material's ability to absorb energy during impact, indicating toughness and resistance to brittle fracture.
Tests the hardness of cast materials, ensuring the final part meets the required wear resistance and durability.
Detects surface cracks, fissures, or other irregularities that may compromise the structural integrity of the cast part.
Measures material expansion or contraction during temperature changes, critical for ensuring dimensional stability in high-temperature applications.
Assesses the casting's ability to be welded effectively, ensuring proper integration with other components.
Inspection Techniques in Full Mold Casting
Value/Range - Surface Ra 0.8 µm to 3.2 µm, crack detection, defect spotting
Aerospace (turbine blades), Automotive (engine components)
Value/Range - ±0.05 mm to ±0.5 mm
Automotive (brackets, housings), Industrial (machine parts)
Value/Range - Void size detection from 0.1 mm, porosity % up to 10%
Aerospace (structural parts), Automotive (transmission parts)
Value/Range - Detection of flaws up to 50 mm depth
Aerospace (engine components), Marine (propellers, shafts)
Value/Range - Crack width detection down to 0.1 mm
Automotive (brake components), Defense (armor)
Value/Range - Detection of cracks and leaks down to 0.1 mm
Aerospace (landing gear), Oil & Gas (pressure vessels)
Value/Range - Detects cracks as small as 0.02 mm
Automotive (engine parts), Industrial (machine components)
Value/Range - 3D scan resolution up to 50 µm, porosity % detection
Aerospace (turbine blades), Automotive (engine blocks)
Value/Range - Vickers, Brinell, Rockwell hardness scales
Automotive (suspension parts), Industrial (gearboxes)
Value/Range - Tensile strength from 150 MPa to 800 MPa
Aerospace (frame components), Industrial (high-strength parts)
Value/Range - Ra 0.8 µm to 5 µm
Automotive (exterior parts), Electronics (precision components)
Value/Range - Charpy test values from 10 J to 100 J
Automotive (bumper systems), Defense (military equipment)


Industry Applications of Full Mold Casting
Turbine rotors, compressor blades, structural airframe components
Cylinder heads, crankshafts, brake discs, suspension arms
LED housings, connectors, circuit boards, motor housings
Gear racks, industrial valves, large machinery housings
Marine engine parts, rudder assemblies, propellers, hull fittings
Bone screws, implants, surgical devices, diagnostic tools
Armor plates, missile guidance systems, tanks, firearms components
Reinforced concrete molds, structural supports, bridge joints
Drilling tools, valve bodies, pipeline fittings, offshore equipment
Heat exchangers, turbine blades, reactor containment components
Wind turbine hubs, solar panel frames, geothermal equipment
Tractors, harvesters, plow blades, irrigation components
Drill rigs, mining tools, conveyor systems, crushers
Train wheels, tracks, coupling devices, braking systems
Excavator arms, bulldozer blades, crane parts
A Solution for Precision in Automotive Components
The need for high-precision and complex automotive parts often leads to difficulties in traditional casting methods. Full Mold Casting offers a more efficient solution, ensuring accurate dimensions and superior surface finishes with minimal porosity. Using vaporized foam patterns eliminates the risk of dimensional errors and allows for faster production cycles. This technique is ideal for manufacturing automotive components, including brake rotors, engine blocks, and structural parts, providing the necessary strength, durability, and accuracy for critical applications.






Industries We Serve
- Solid Progress
Our Manufacturing metrics
Frigate brings stability, control, and predictable performance to your sourcing operations through a structured multi-vendor system.
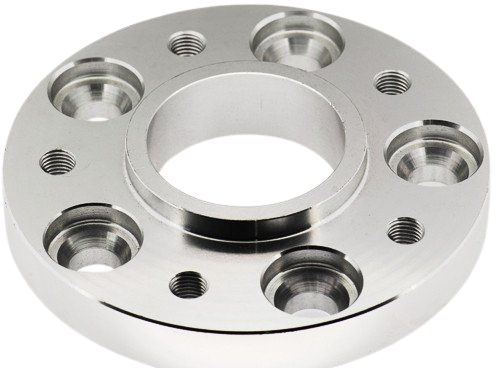
2.8X
Sourcing Cycle Speed
Frigate’s pre-qualified network shortens decision time between RFQ and PO placement.
94%
On-Time Delivery Rate
Structured planning windows and logistics-linked schedules improve project-level delivery reliability.
4X
Multi-Part Consolidation
We enable part family batching across suppliers to reduce fragmentation.
22%
Quality Rejection Rate
Multi-level quality checks and fixed inspection plans lower non-conformities.
30%
Procurement Costs
Optimized supplier negotiations and bulk order strategies reduce your overall sourcing expenses.
20%
Manual Processing Time
Automation of sourcing and supplier management significantly reduces time spent on manual tasks.
Reducing Lead Times for Faster Production
Full Mold Casting reduces lead times by streamlining mold preparation. Using expendable foam patterns eliminates the need for complex tooling, accelerating the mold creation. This method allows for faster cycle times, reducing overall production delays. Frigate’s efficient approach to Full Mold Casting ensures that parts can be produced quickly while maintaining high precision. This reduction in lead time is particularly beneficial for projects with tight deadlines, where quick turnaround without sacrificing quality is essential.

Get Clarity with our Manufacturing Insights
- Real Impact
Words from Clients
See how global OEMs and sourcing heads describe their experience with our scalable execution.
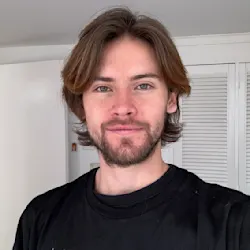
“Quick turnaround and solid quality.”
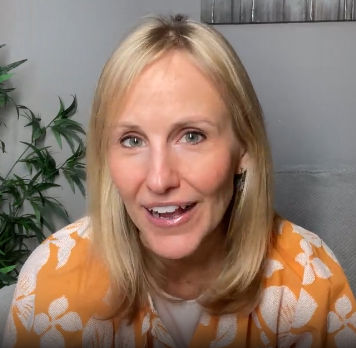
“The instant quote tool saved us time, and the parts were spot-on. Highly recommend Frigate!”
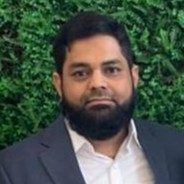
“I would strongly recommend Frigate to anyone who wants to do Rapid Prototyping, and take their ideas to manufacturing. One firm doing all kinds of Product Development!”
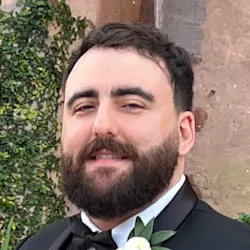
“Great service, fair price, and the parts worked perfectly in our assembly.”
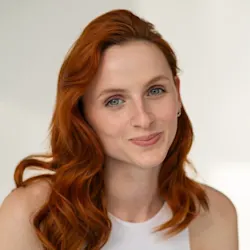
“Top-notch machining and fast shipping. Very satisfied with the results.”
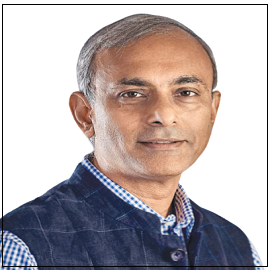
“The next disruption is happening in Prototyping & Manufacturing on-demand and Frigate is leading the way! I personally believe the Frigate's way of IIOT enabled cloud platform with Al.”
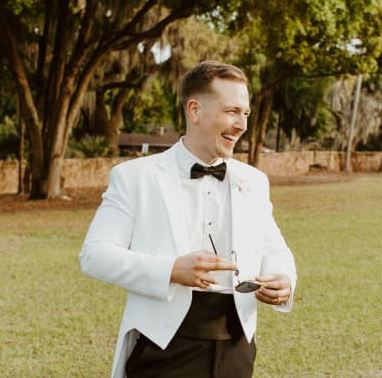
“Frigate delivered high-quality parts at a competitive price. The instant quote tool is a huge plus for us!”

“We appreciate the precision and quality of the machined components in the recent delivery—they meet our specifications perfectly and demonstrate Frigate’s capability for excellent workmanship.”
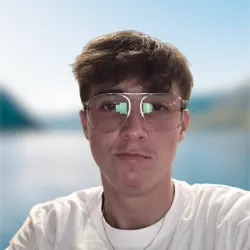
“Flawless execution from quote to delivery.”

“I am absolutely happy to work with supplier like Frigate who were quite proactive & result oriented . Frigate has high willingness team who has strong know how & their passion towards the products & process were absolutely thrilling.”
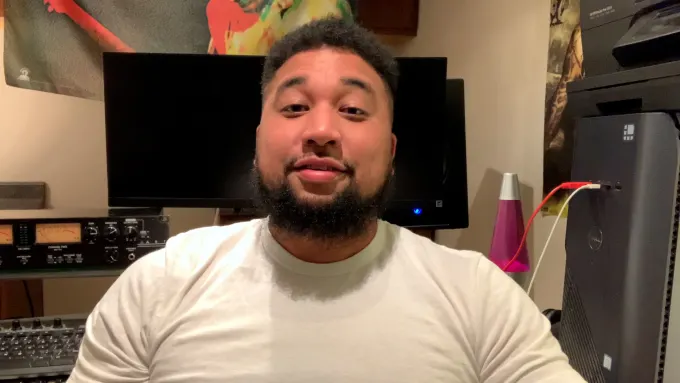
“The precision on these parts is impressive, and they arrived ahead of schedule. Frigate’s process really stands out!”
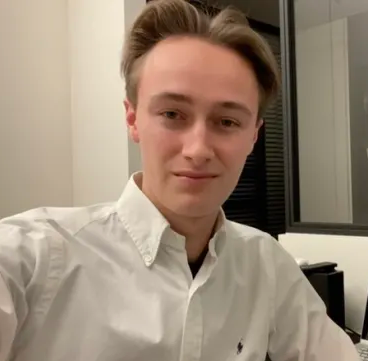
“Parts were exactly as spec’d, and the instant quote made budgeting a breeze.”
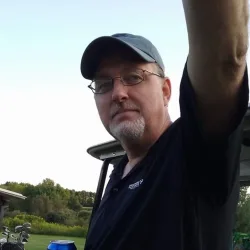
“Good value for the money.”
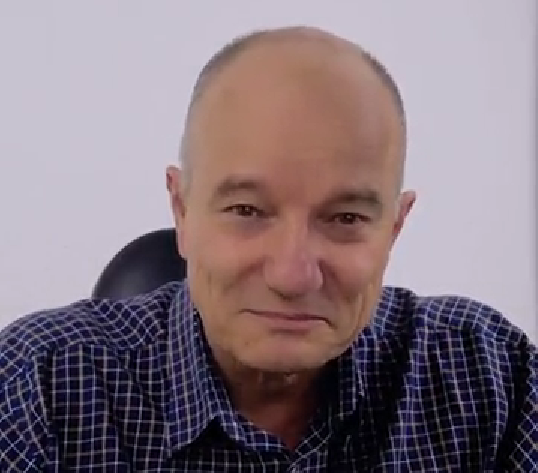
“The finish was perfect, and the team was easy to work with.”

“Working with Frigate has been great. Their proactive, results-driven approach and expertise shine through in every project. It's been a pleasure collaborating with them.”

"We are highly satisfied with the timely delivery and quality of the MIG Welding Cable from Frigate. Their attention to detail, secure packaging, and quick responsiveness stood out. We confidently recommend Frigate Engineering Services Pvt. Ltd. as a reliable manufacturing partner."
Having Doubts? Our FAQ
Check all our Frequently Asked Question
The mold coating provides a smooth, uniform surface that ensures the precise replication of intricate features and minimizes defects such as porosity or surface imperfections.
By carefully controlling the mold temperature and pouring speed, Full Mold Casting minimizes material flow issues and solidification anomalies, ensuring uniform density and strength across the casting.
The vaporization of the polystyrene pattern during pouring leaves an exceptionally precise cavity, enabling tight dimensional tolerances and reducing the need for secondary machining processes.
Proper sand compaction around the pattern ensures structural integrity during the casting process, preventing mold shifting or collapse and maintaining the accuracy of the final casting shape.
The foam patterns' expendable nature allows for quick and cost-effective mold creation, making Full Mold Casting suitable for high-volume production while maintaining high consistency and minimal scrap.
We'd love to Manufacture for you!
Submit the form below and our representative will be in touch shortly.
LOCATIONS
Global Sales Office
818, Preakness lane, Coppell, Texas, USA – 75019
Registered Office
10-A, First Floor, V.V Complex, Prakash Nagar, Thiruverumbur, Trichy-620013, Tamil Nadu, India.
Operations Office
9/1, Poonthottam Nagar, Ramanandha Nagar, Saravanampatti, Coimbatore-641035, Tamil Nadu, India. ㅤ
Other Locations
- Bhilai
- Chennai
- Texas, USA