- Precision Control
Industrial & Custom Extrusions
We deliver extrusions with precision-engineered dies and real-time dimensional control systems. This ensures tolerance consistency as tight as ±0.005″, supporting error-free integration into automated assemblies and eliminating costly downstream fitment issues.

Our Clients
Trusted by Engineers and Purchasing Leaders
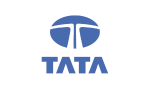
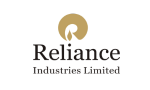


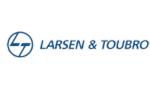
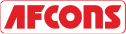


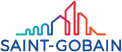

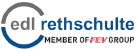

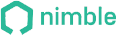
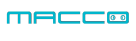









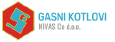
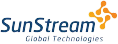

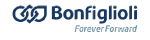


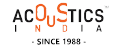
- Versatile Offerings
Our Industrial & Custom Extrusions Products
Explore our range of high-quality Industrial & Custom Extrusions today.
- Real Impact
Words from Clients
See how global OEMs and sourcing heads describe their experience with our scalable execution.
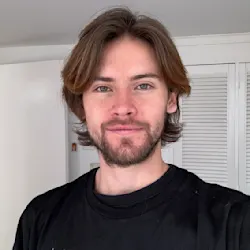
“Quick turnaround and solid quality.”
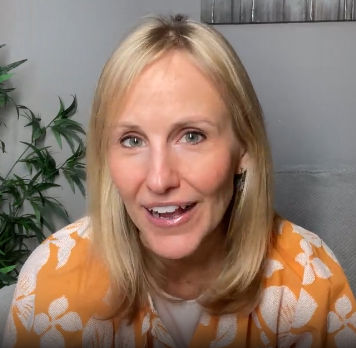
“The instant quote tool saved us time, and the parts were spot-on. Highly recommend Frigate!”
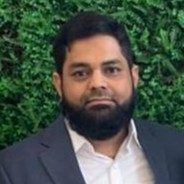
“I would strongly recommend Frigate to anyone who wants to do Rapid Prototyping, and take their ideas to manufacturing. One firm doing all kinds of Product Development!”
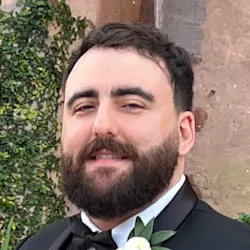
“Great service, fair price, and the parts worked perfectly in our assembly.”
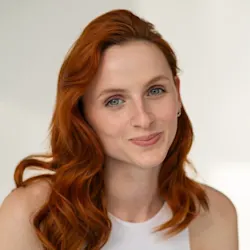
“Top-notch machining and fast shipping. Very satisfied with the results.”
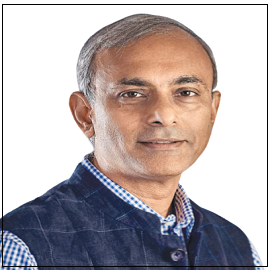
“The next disruption is happening in Prototyping & Manufacturing on-demand and Frigate is leading the way! I personally believe the Frigate's way of IIOT enabled cloud platform with Al.”
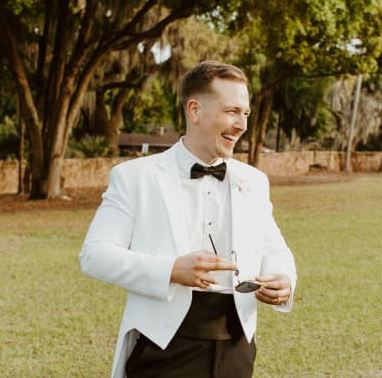
“Frigate delivered high-quality parts at a competitive price. The instant quote tool is a huge plus for us!”

“We appreciate the precision and quality of the machined components in the recent delivery—they meet our specifications perfectly and demonstrate Frigate’s capability for excellent workmanship.”
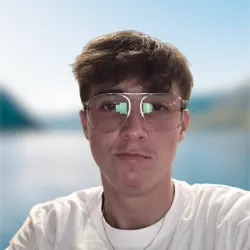
“Flawless execution from quote to delivery.”

“I am absolutely happy to work with supplier like Frigate who were quite proactive & result oriented . Frigate has high willingness team who has strong know how & their passion towards the products & process were absolutely thrilling.”
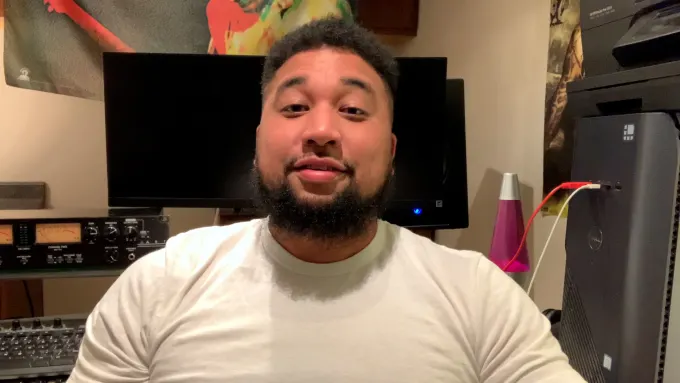
“The precision on these parts is impressive, and they arrived ahead of schedule. Frigate’s process really stands out!”
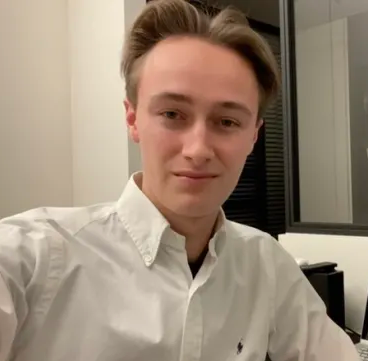
“Parts were exactly as spec’d, and the instant quote made budgeting a breeze.”
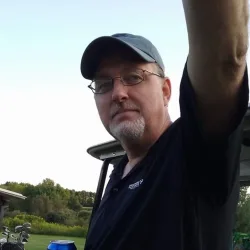
“Good value for the money.”
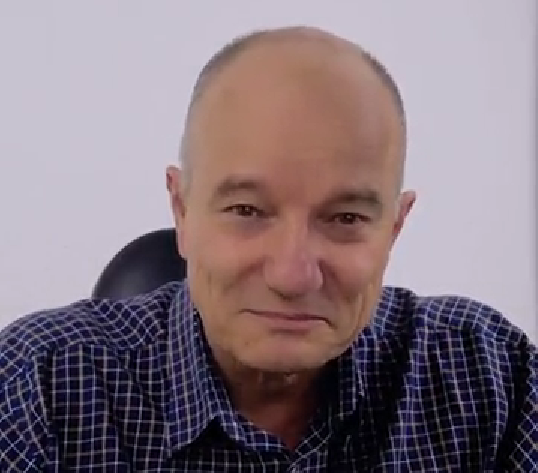
“The finish was perfect, and the team was easy to work with.”

“Working with Frigate has been great. Their proactive, results-driven approach and expertise shine through in every project. It's been a pleasure collaborating with them.”

"We are highly satisfied with the timely delivery and quality of the MIG Welding Cable from Frigate. Their attention to detail, secure packaging, and quick responsiveness stood out. We confidently recommend Frigate Engineering Services Pvt. Ltd. as a reliable manufacturing partner."
We export to 10+ countries
Frigate’s Global Presence
Frigate takes pride in facilitating “Make in India for the globe“. As our global network of Frigaters provides virtually limitless capacity, and through our IoT enabled platform your parts go directly into production. By digitally and technologically enabling “the silent pillars of the economy” MSME and SME manufacturing industries, we are able to tap the huge potential for manufacturing to bring the best results for our clients.

100,000+
Parts Manufactured
250+
Frigaters
2000+
Machines
450+
Materials
25+
Manufacturing Process
Industry Applications
Construct protective enclosures around moving equipment using rigid extruded profiles with standardized slots for modular assembly.
Serve as structural bases for rails and actuators, maintaining alignment and precision in automated motion control applications.
Provide customized frames for storage and transport systems, engineered for load-bearing strength and dimensional accuracy.
Form ergonomic industrial workbenches and fixtures with extrusions that integrate cable routing, tool mounts, and adjustable supports.
Used in side rails, guides, and frames for conveyors, supporting mechanical loads while allowing modular attachment.
Support photovoltaic modules with extruded brackets and rails engineered for environmental durability and precise alignment.




- Warp Control
Precision Cooling to Eliminate Twisting and Bowing
Twisting or bowing during cooling disrupts profile accuracy and causes misalignment in assemblies. We eliminate distortion through precise thermal control, optimized die flow, and real-time automated corrections.
- Multi-zone cooling with ±1°C control for uniform thermal gradients
- CAE-optimized die flow ensures symmetric material distribution
- Servo pullers maintain ±0.05 m/min speed consistency to prevent tension-induced warping
- Low-warp materials selected based on shrinkage data (e.g., polycarbonate 0.6%)
- Inline straightening keeps linearity within ±0.25 mm per meter
- Infrared thermal monitoring enables live cooling adjustments
We use advanced flow simulation software to optimize the die design for uniform material distribution across all channels. The die is engineered to ensure each channel has consistent flow, avoiding weak spots or thinning. Real-time sensors monitor pressure and temperature throughout the extrusion process to ensure accuracy. This results in wall thicknesses maintained within ±0.05 mm, even in complex multi-channel profiles.
We carefully select materials with compatible thermal expansion rates and melting temperatures. The extrusion process is adjusted to ensure that materials bond effectively during cooling, preventing delamination. We also apply specialized bonding agents and optimize the cooling rate to match the material characteristics. Extensive testing ensures the integrity of the bond remains intact, even under thermal cycling.
Long-length extrusions are monitored using laser measurement systems that provide real-time feedback. We use servo-driven pullers that adjust speed dynamically to ensure uniform tension and avoid warping. Additionally, our straightening process applies controlled pressure to correct any slight deviation in the profile. This approach keeps dimensional accuracy within ±0.25 mm over long lengths, even with tight tolerances.
Sharp transitions or thin sections are managed through careful die design and melt flow optimization. The extrusion speed and pressure are adjusted to maintain a consistent material flow, preventing defects like flow hesitation or tearing. In cases where the wall thickness is under 1.5 mm, additional cooling mechanisms are applied to avoid distortion. This ensures that thin or intricate sections maintain strength and integrity during extrusion.
We use high-quality resins with stable dielectric constants to maintain insulation properties. For added performance, we incorporate nano-fillers, ensuring the extrusion material can withstand high-voltage applications. The extrusion process is carefully controlled to avoid shear stress, which can degrade dielectric strength. After production, the material is tested to ensure it can handle up to 20 kV/mm without failure.
We'd love to Manufacture for you!
Submit the form below and our representative will be in touch shortly.
LOCATIONS
Registered Office
10-A, First Floor, V.V Complex, Prakash Nagar, Thiruverumbur, Trichy-620013, Tamil Nadu, India.
Operations Office
9/1, Poonthottam Nagar, Ramanandha Nagar, Saravanampatti, Coimbatore-641035, Tamil Nadu, India. ㅤ
Other Locations
- Bhilai
- Chennai
- USA
- Germany